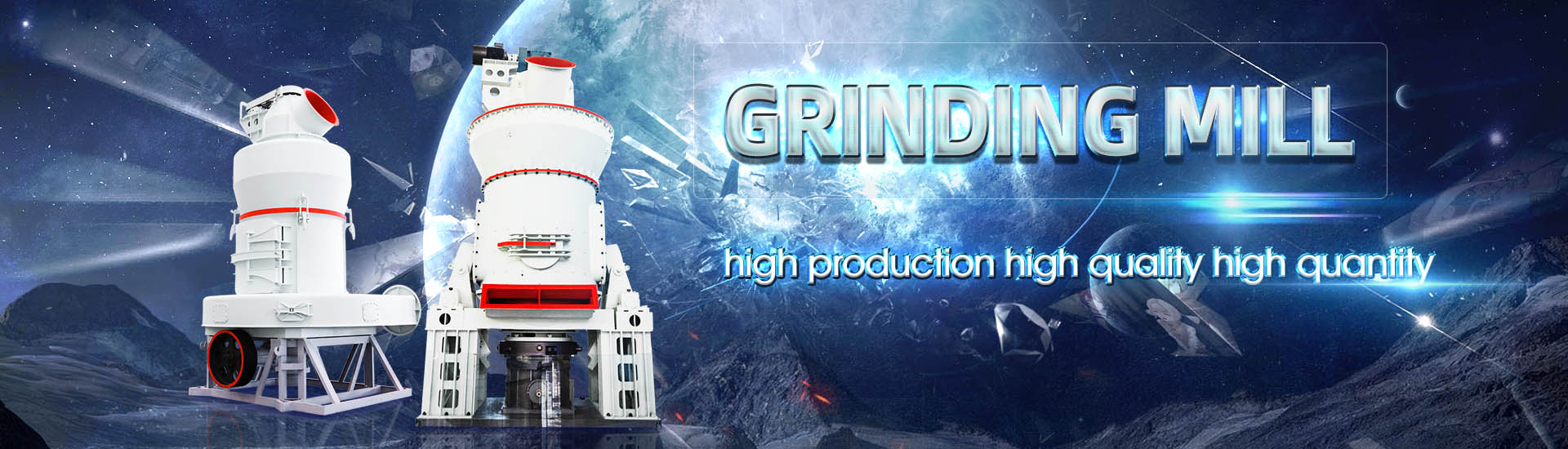
Grinding mill selectionGrinding mill selectionGrinding mill selection
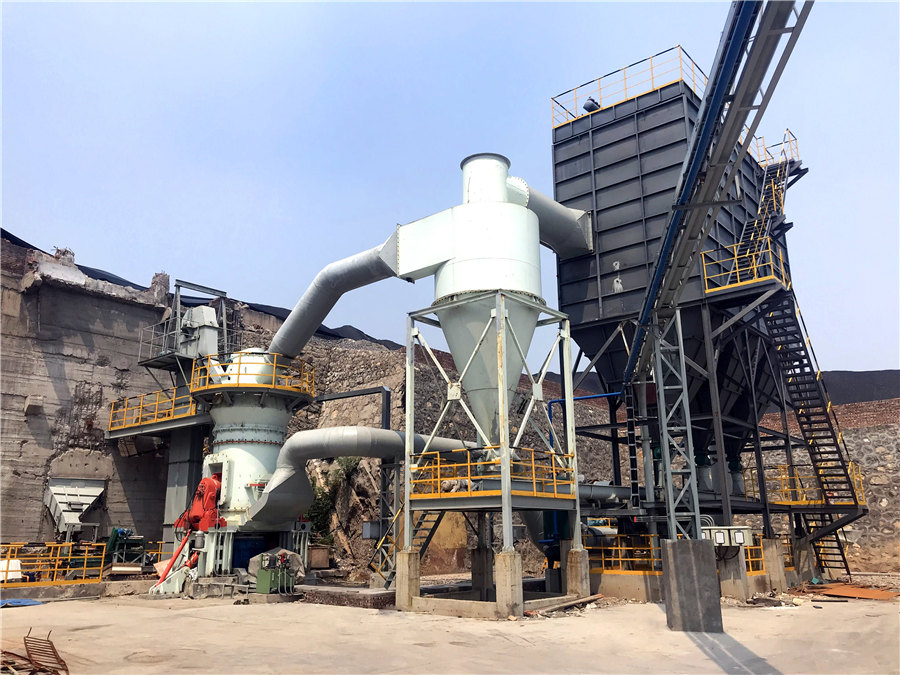
Primary Grinding Mills: Selection, Sizing And Current Practices
In the present state of technological development for primary grinding mills, there is a wide choice of acceptable options with respect to type and size, grinding flowsheet and grinding media2007年1月1日 The fine grinding mills are classified often into five major groups (i) impact mills, (ii) ball media mills, (iii) air jet mills, (iv) roller mills, and (v) shearing attrition mills from the Chapter 10 Selection of Fine Grinding Mills ScienceDirectSelecting the right grinding mills for your operation requires the serious consideration of a variety of factors, far beyond “what do I want to grind?” and “How fine do I want it?” Do you need lab Selection Tips for Grinding Mills Union Process2024年11月5日 Air classifier Mill (ACM) is an integrated grinding, classifying, conveying, and collecting operations for achieving ultrafine grinding (of up to 2 micron*) depending upon the Mill Selection Made Easy: Air Classifying and Hammer Mills
.jpg)
Chapter 10 Selection of Fine Grinding Mills ResearchGate
2007年12月31日 The fine grinding mills are classified often into five major groups: (1) impact mills, (2) ball media mills, (3) air jet mills, (4) roller mills, and (5) shearing attrition mills from2004年12月10日 By comparing the mill characteristics with the breakage characteristics of the feed material, the performance of different mills and different operating states can be Mill selection and process optimization using a physical grinding Combining impact and shearing actions enhances mill efficiency Proper selection of media milling equipment is vital for success in all three areas There are many different types of grinding mills (Table 1) Some devices, such as ball mills, Solids Choose the Right Grinding Mill Chemical Metso Select™ horizontal grinding mills provide classleading performance to grinding operations, while delivering reliability, availability and productivity Reliability: Dependable productivity from preengineered designSelect™ Horizontal Grinding Mills Metso
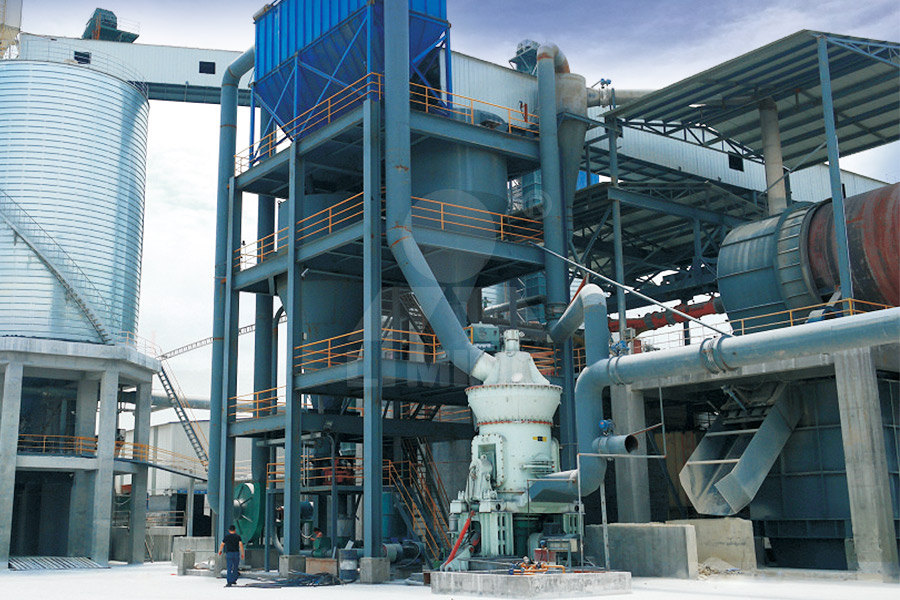
Mill Selection and Process Optimization using a Physical Grinding
2004年12月1日 By grinding γAl2O3 and Hunan coal separately in an impact mill, a grinding process model of two dimensionless groups and is developed using Buckingham Pi theorem Optimised liner design can be used to strike the best economic balance between liner life and mill grinding performance, thus enhancing the profitability of a mining operation Protection of the The selection and design of mill liners Semantic ScholarGrinding Mills: Ball Mill Rod Mill Design PartsCommon types of grinding mills include Ball Mills and Rod Mills This includes all rotating mills with heavy grinding media loads This article focuses on ball and rod mills excluding SAG and AG Grinding Mills 911MetallurgistA crushing plant delivered ore to a wet grinding mill for further size reduction The size of crushed ore (F 80) was 40 mm and the SG 28 t/m 3 The work index of the ore was determined as 122 kWh/t A wet ball mill 1 m × 1 m was chosen to grind the ore down to 200 micronsGrinding Mill an overview ScienceDirect Topics
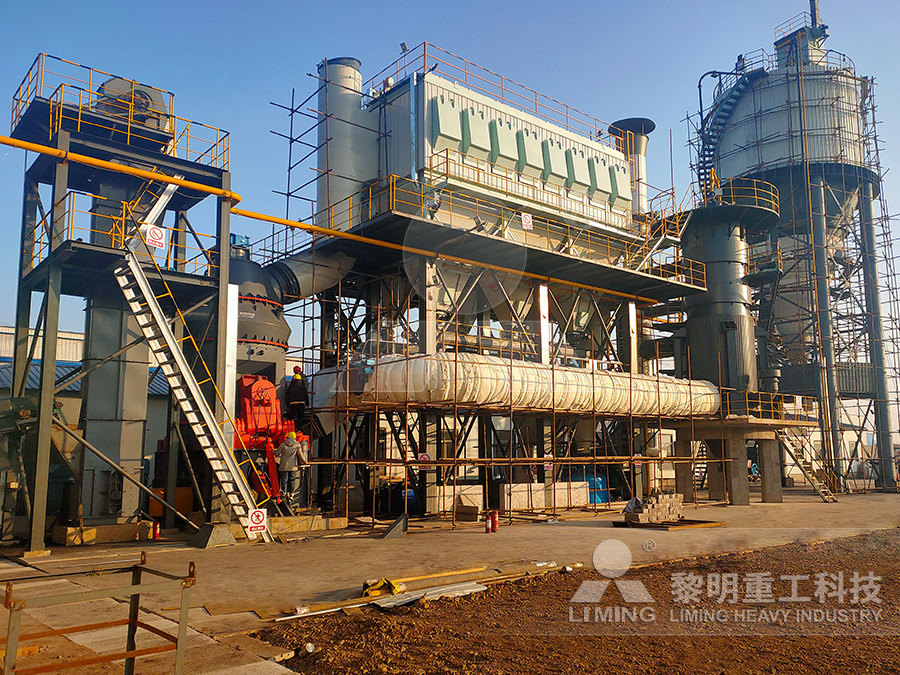
Batch Grinding in Laboratory Ball Mills: Selection Function
2009年10月1日 Request PDF Batch Grinding in Laboratory Ball Mills: Selection Function (hard ore or soft ore) to the mill varies continuously, leading to uncontrolled grinding in the mill2016年6月6日 Sufficient capacity (primarily a concern of large circuits where multiple pebble crushers are required to serve one grinding line); Design for bypassing crushers during maintenance, and; Evaluation of the where to reintroduce the crushed pebbles back to the grinding circuit SAG mill by feeding crushed pebblesSAG Mill Grinding Circuit Design 911Metallurgist2020年9月22日 Grinding machine has been widely used in gold mines in South Africa since 1905 At that time, the grinding machine used river pebble as the grinding medium, which was essentially a gravel mill Later, in order to improve the production capacity of the mill, cast iron balls were used as the medium, so normal gravel mills were evolved into ball mills and rod millsGrinding Machines: Types and Selection Principles Miningpedia2008年7月1日 Dry grinding experiments on cement clinker were carried out using a laboratory batch ball mill equipped with a torque measurement The influence of the ball size distribution on the specific The specific selection function effect on clinker grinding efficiency
.jpg)
The Selection Design and Application of Mill Liners for Large
The history of mill liners has evolved over time and this paper tracks the changes and development of liner technology It provides an overview of the primary types of liners, the design and the materials of construction The design of a mill liner is driven by application, materials of construction, casting technology and handling issues The choice of solid steel, grid liners, 2004年12月10日 Presently, the description, selection and design of comminution and dispersion processes are based mainly on practical experience and empirical relations For the determination of the optimum operation parameters of a grinding or dispersing process or mill, usually several grinding or dispersing tests have to be carried outMill selection and process optimization using a physical grinding Video credit: shsbjq / CC BYSA 40 Specifications Important specifications when selecting grinding mills and pulverizers include, The size of the mill can range from pilot/lab to production, eg, 35 to 1600 cu ft; Feed size, material, and hardness of feed must be considered; Output size ranges; Mills can handle dry or wet input, or both; Mills operate in batches or continuouslyGrinding Mills and Pulverizers Selection Guide: Types, Features This includes: Cost savings from investing in a preengineered solutions, time savings from our expedited selection, quotation process, and order execution, and faster delivery and startup of your Select™ horizontal grinding mill The Metso Select™ horizontal grinding mill is a robust mill for exceeding operational goals today and tomorrowSelect™ Horizontal Grinding Mills Metso
.jpg)
Equipment Sizing: Crusher or Grinding Mill
2016年7月8日 UNTIL THE THIRD THEORY OF COMMINUTION of "Work Index" method of determining crushing and grinding mill size was introduced, there was no way of accurately 911 Metallurgist is a trusted Following is a selection and delivery is reduced through the use of standardized equipment selection, quotation preparation, and order execution approach This will result in faster mill deliveries With a robust design, you will be up and running efficiently with high productivity Your Select™ horizontal grinding mill will help to exceed yourDesigned to perform Select™ Horizontal Grinding Mills Metso2018年4月5日 EF1 – Dry Grinding – for the same range of work, dry grinding requires 13 times as much power as wet grinding EF2 The preliminary rod mill selection would be a 366 meter (12 foot) inside shell 346 meter (1135 foot) Rod Mill Design Calculations 911MetallurgistThe Selection Design and Application of Mill Liners for Large Wet Grinding Mills Presented by Damian Connelly applications as ball mill liners and grinding balls Typical microstructure of class 1 type D nickelchromium white cast iron Source: Perez and Stameroff (2003)The Selection Design and Application of Mill Liners for Large Wet
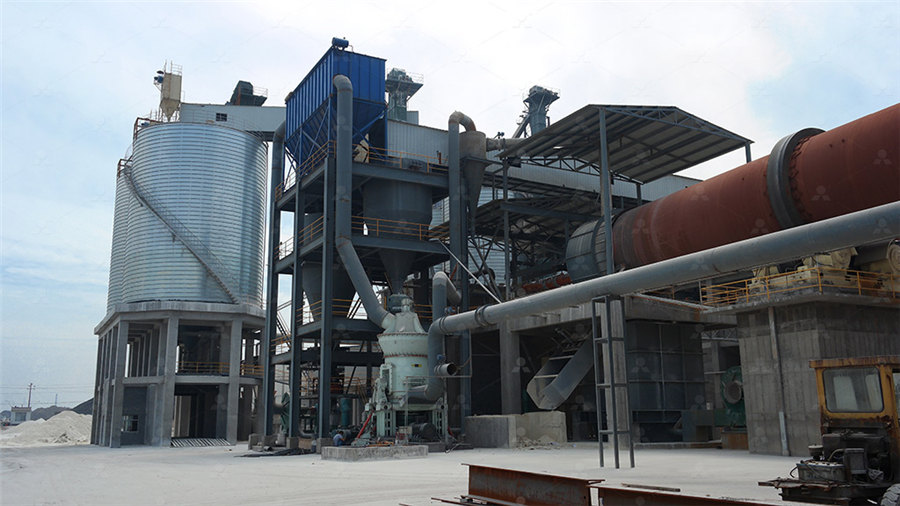
Ball Mill VS Rod Mill: Difference Selection JXSC Machine
2024年1月10日 Home » News » Ball Mill VS Rod Mill: Difference Selection Contact Now +86 Published time:10 January 2024 The grinding medium’s filling rate refers to the grinding medium’s percentage accounting for the grinding mill’s internal volume2006年1月1日 An overview of the selection and design of mill liners was published by Powell et al (2006), providing a reference source on mill liners, however no comprehensive technical manual or training is (PDF) Selection and design of mill liners ResearchGateand gearbox inefficiencies to develop a recommended mill motor size A graph shows the mill design relative to its minimum design A data base allows standard mill sizes to be picked for each manufacturer and the motor size that the manufacturer would put on each mill size MILLCALCv2a 4 19/02/2004Grinding Mill Computer Model AusIMMAfter the grinding, the state of the solid is changed: the grain size, the grain size disposition, and the grain shape There are essentially five different grinding mechanisms, and Retsch offers seven different types of mills that can be utilized The Grinding Mills for reliable size reduction tasks RETSCH
.jpg)
Mill Selection and Process Optimization using a Physical Grinding
2004年12月1日 This paper describes the microstructural properties and grinding behavior of γAl2O3 and coal particles in a batch impact mill By grinding γAl2O3 and Hunan coal separately in an impact mill, a 2012年6月1日 As the cylinder starts to rotate, the grinding balls inside the cylinder crush and grind the feed material, generating mechanical energy that aids in breaking bonds, activating the catalyst, and Grinding in Ball Mills: Modeling and Process ControlINTRODUCTION Primary grinding mills as defined in this paper, are autogenous or semiautogenous rotating, tumbling mills having a coarse feed with a top size usually varying from 150 to 300 mm (6 to 12 inches) Most frequently, the feed to these mills is the product of primary crushing plants but in some cases run of mine ore is used as feed such as at Benguet, Primary Grinding Mills: Selection, Sizing And Current Practices2017年2月20日 Grinding Mill Specifications Data According to formula 423/√d, where d is equal to internal shell diameter within new liners In this case the thickness used was 60 mm for small mill sizes up to and including 2940 and 80 mm for larger millsGrinding Mill Design Ball Mill Manufacturer 911Metallurgist
.jpg)
A guide to grinding mill installation: Ensuring efficient and
A guide to grinding mill installation: Ensuring efficient and troublefree operation Grinding mills are critical components in many industrial processes, responsible for reducing the size of materials and achieving desired particle sizes The successful installation of a grinding mill is essential for ensuring efficient and troublefree When grinding cement products, a grinding system composed of a roller press or an external circulation vertical mill + a powder concentrator + a tube mill is generally selected Taking grinding P o425 cement as an example, the pre grinding closedloop system composed of roller press or external circulation vertical mill and powder Cement Grinding Machine Selection: Vertical Roller Mill VS Roller Press2024年8月8日 The selection of grinding media is a critical decision in the ball milling process, Additionally, evaluate the milling conditions, including the type of mill, speed, duration, and whether the process is wet or dry These factors will influence the selection of the most suitable grinding media Step 2 Comparing Media Types:Ball Mill Success: A StepbyStep Guide to Choosing the Right Grinding interaction between grinding media and mineral in iii) The mill: Mill size and type, speed and discharge type are factors of the mill that need to be taken into consideration before choosing a specific media type since these factors contribute to the wear rate and failure of grinding media (Zheng and Yang, 1997)Selection of Grinding Media for Use in the Gold Processing
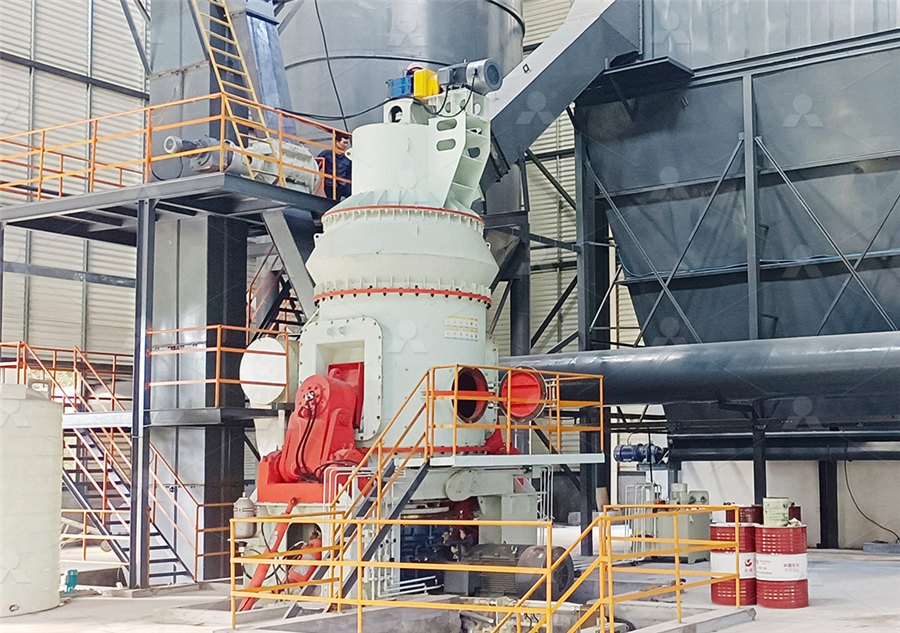
Solids Choose the Right Grinding Mill Chemical Processing
Combining impact and shearing actions enhances mill efficiency Proper selection of media milling equipment is vital for success in all three areas There are many different types of grinding mills (Table 1) Some devices, such as ball mills, are more suitable for coarse materials2017年10月26日 The following are factors that have been investigated and applied in conventional ball milling in order to maximize grinding efficiency: a) Mill Geometry and Speed – Bond (1954) observed grinding efficiency to be a function of ball mill diameter, and established empirical relationships for recommended media size and mill speed that take this factor into Factors Affecting Ball Mill Grinding EfficiencyThis review serves to highlight problems of mill liner designs and how they can be tackled in a logical and often inexpensive manner by considering charge trajectories and liner spacing criteria, in conjunction with liner wear monitoring Dramatic shortcomings of mill liner designs, especially of large SAG mills, such as rapid failure and even mill shell damage arising from impacting of the The selection and design of mill liners Semantic Scholar3 The maximum ball loading capacity of AG mill is calculated at 3% of effective mill volume, while the SAG mill with ball loading capacity at 15% of mill volume 4 The operating speed is usually 75% of critical speed of mill, the variable Grinding Mills Mineral Processing Equipment CITIC
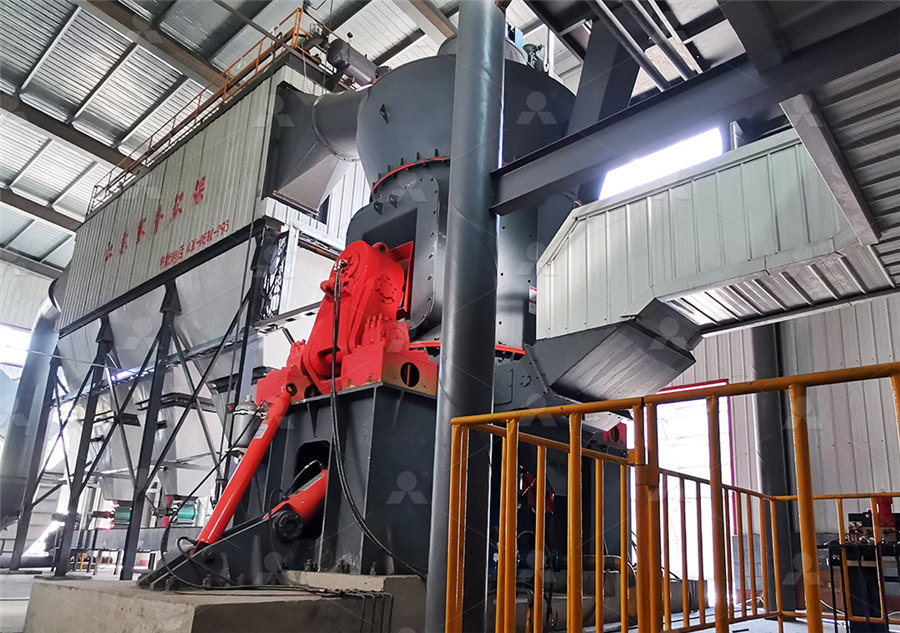
Calculation of Top Grinding Media Size Ball Sizing
2015年10月14日 The majority of grinding balls are forged carbon or alloy steels Generally, they are spherical, but other shapes have been used The choice of the top (or recharge) ball size can be made using empirical equations Discover our wide selection of grinding mill services and parts Why choose Metso as your partner? Circularity Extend component and equipment life to achieve sustainability targets Service footprint Over 1,500 field technicians Grinding mill services Metso2024年2月12日 Factor Description; Type of Mill: Manual: Requires handcranking, laborintensive, no power consumption Electric: Uses a motor, more convenient, faster grinding: Grinding Mechanism: Stone Grinding: Produces even, finetextured flour, ideal for bread making Impact Grinding: Fastmoving metal fins break grains into flour, quicker but possibly coarserHow to pick the best home grain mill: A buyer’s guide for easy selection1991年10月1日 When the mill is operated, a grinding zone is generated where both bails and powder violently alter their flow paths The state of the grinding zone is also described by eqns (3) and (4) in which J, Nb, Eb, Ob, f and U are replaced by those representing the grinding zone, denoted as Jo, Nbo, Ebo, Bbo, f~o and UoAn analysis of the selection function for mills using balls as grinding
.jpg)
What Ore Testing is Required For Mill Selection
2015年4月15日 Bond rod mill grindability tests at 10 or 14 mesh for Work Index For each ball mill grinding step, a Bond ball mill grindability test for Work Index at one mesh size coarser than the desired 80% passing size and at the mesh size of or just finer than the 80% passing sizeDIFFERENT MILLS REQUIRE DIFFERENT AMOUNTS OF MEDIA •BASED UPON WORKING VOLUME OR TOTAL VOLUME •Mills such as the Immersion Mill have a fixed amount determined by size of the basket •Steel Ball Mill 333% •Open Head Sand Mill 3545% •Ceramic Pebble Ball Mill 50% •Dry Grind Batch Attritor 4560% •Wet Grind Batch Attritor 3845% •Continuous How to Choose the Correct GRINDING MEDIA PCI Mag2019年8月30日 Forged steel balls; P=s=4548t/m3 cast steel balls P=4346t/m3; rolling steel balls P=6068t/m3; steel segments P=4346t/m3filling ratio of grinding medium, When wet grinding: lattice ball mill pi = 40% – 45%; overflow ball mill phi = 40%; rod mill phi = 35% Dry grinding: When material is mixed between grinding media, the grinding Ball Mill Parameter Selection Calculation JXSCThe Impact Mill Condux ® is a high speed fine impact mill for the dry grinding of various products up to a Mohs hardness of 3 3,5 The diversity of grinding tools allow the mill to be used universally depending on the application and area of operation This of course also applies later on, when circumstances such as product characteristics or requirements have changed, the Condux Impact Mill NETZSCH Grinding Dispersing
.jpg)
What is Limestone Grinding Mill SBM Mill Crusher
2023年5月15日 Proper equipment selection Make sure we have a grinding mill that is the appropriate size and type for processing limestone Mill type (such as a ball mill, vertical roller mill, or Raymond mill), capacity, power consumption, and overall efficiency are all important factors to take into account