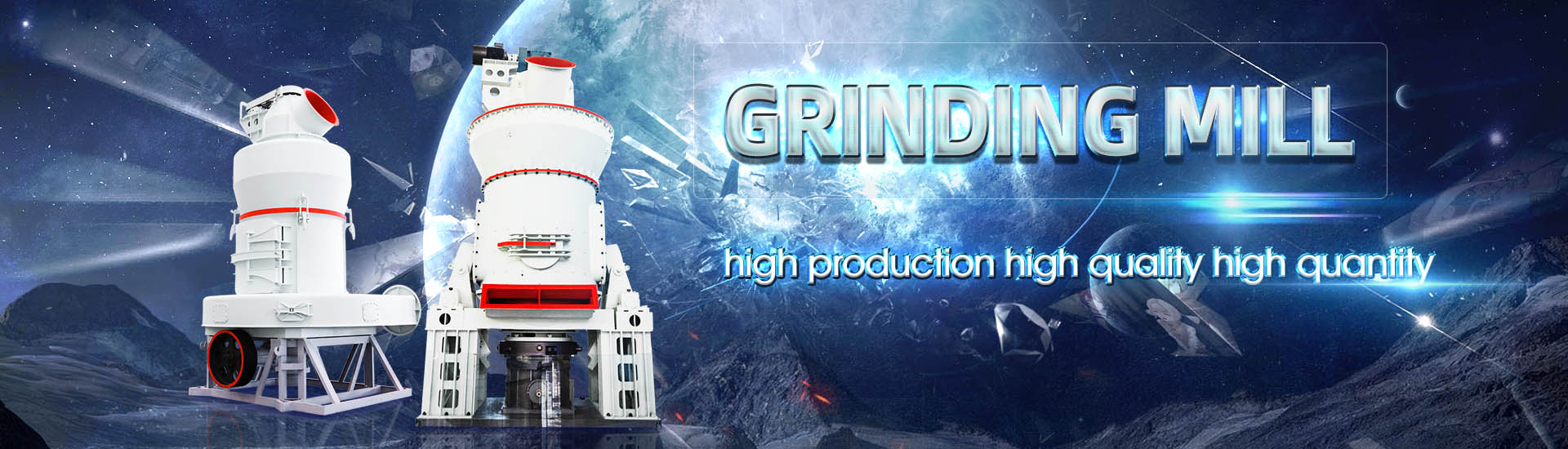
What is the particle size of Simon ore grinding machine
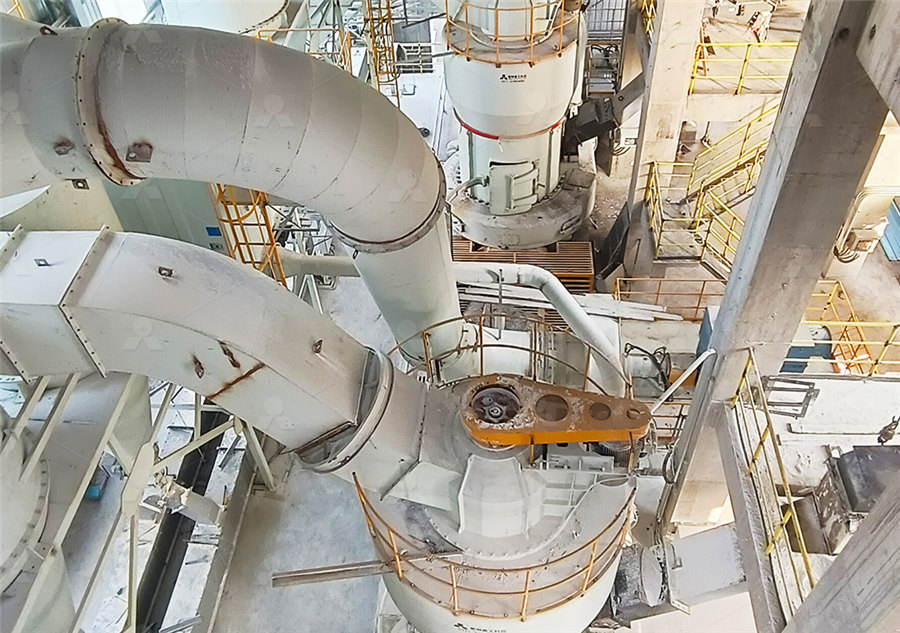
Ore Grinding SpringerLink
2023年7月20日 According to the particle sizes of grinding products, the grinding process is divided into coarse grinding, medium grinding, fine grinding, microfine grinding, and ultrafine grinding According to the material transmission methods, ore grinding is divided into dry The most efficient grinding system is a system that applies the minimum amount of energy to rupture the material without adding excess energy or heat Energy is required to reduce Principles of Sample Preparation by Grinding or Comminution2017年3月4日 Crushing involves reducing the ore size from various sizes ranging from particles as big as a human body, or just the size of your hea d or toe to an average 90 to 140mm for prim arySIZE REDUCTION BY GRINDING METHODSparticle size is small to improve dissolution rate, solubility, binding strength and dispersion properties Many solid materials exist/present in sizes that are too large to be used directly size reduction
.jpg)
Size Reduction and Energy Requirement ScienceDirect
2016年1月1日 The crushers are normally fed with rocks, up to about 1 m in size, while the grinders are usually fed with rocks crushed down to a maximum size of about 50 mm Larger 2015年2月2日 Calculating the energy required to reduce the feed ore size to the desired product size is the first step in selecting the appropriate size and installed power of equipment that Comminution SpringerLinkThe goal of the grinding circuit is twosided; to maximize the throughput of ore, and minimize the resulting particle size of the ground ore within some acceptable range In this work we study Reinforcement Learning for Grinding Circuit Control in Mineral events undergone by individual ore particles depend on particle properties such as size, shape, mineralogy, and texture For instance, the largest and smallest particles in a tumbling mill All About Particles: Modelling Ore Behaviour in Mineral Elements
.jpg)
Comminution Wikipedia
For comminution of finer particle size ranges (20mm > P 80 > 30 μm) machines like the ball mill, vertical roller mill, hammer mill, roller press or high compression roller mill, vibration mill, jet the gold deportment and particle size may provide additional information Mineralogical scans such as QEMScan and MLA are able to give good data as to the mineral liberation and particle size of gold down to about 5µm Below this size, an alternative method such as secondary ion mass spectrometry (SIMS) should be used Ultra Fine Grinding at KCGMUltra Fine Grinding A Practical Alternative to Oxidative 2016年6月8日 The conclusions that would be drawn from an inspection of the pneumatic machine tailing only, would indicate that finer grinding would be necessary to reduce the tailing losses Since this machine does not favor the Size by Size Particle Size Distribution Profile2020年1月3日 Iron ores obtained from different sources differ in their chemical and physical properties These variations make the process of grinding a difficult task The work carried out in this context focuses on three different samples of iron ore, viz, high silica high alumina, low silica high alumina, and low silica low alumina The grinding process for all the three iron ores is Estimation of Grinding Time for Desired Particle Size Distribution
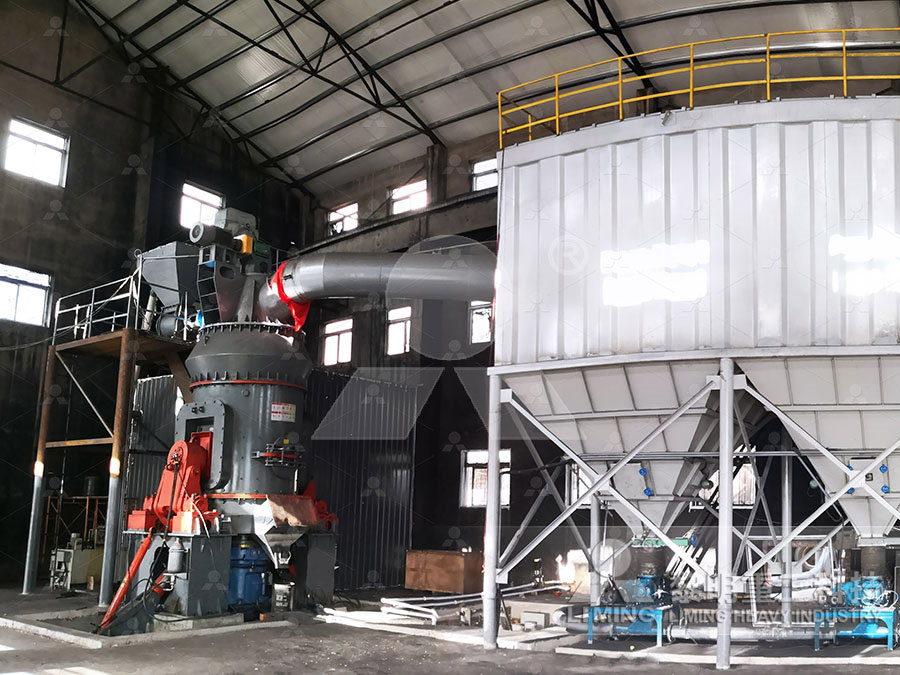
(PDF) Grinding Media in Ball MillsA Review ResearchGate
2023年4月23日 Grinding is the final stage of comminution, which reduces particle size to micron size level The size re duction is achieved by attrition, abrasion, and impact between the ore itself and between 2018年2月1日 In another study to investigate ball size distribution on ball mill efficiency by Hlabangana et al [50] using the attainable region technique on a silica ore by dry milling, a threeball mix of Effect of ball and feed particle size distribution on the milling 2016年7月7日 The recovery of gold by ore leaching is influenced by the size of the particles and the chemical environment The effect of particle size on the dissolution of gold is usually studied using mono Effect of Particle Size and Grinding Time on Gold Dissolution in 2019年10月31日 There are two types of particle destruction in the pulverization process, “surface grinding” and “volume grinding” In surface grinding, small pieces separate from a particle surface, gradually forming a large number of fine particles The particle sizes during grinding often follow a bimodal distributionPulverization 1: Definition and purpose THINKY MIXER
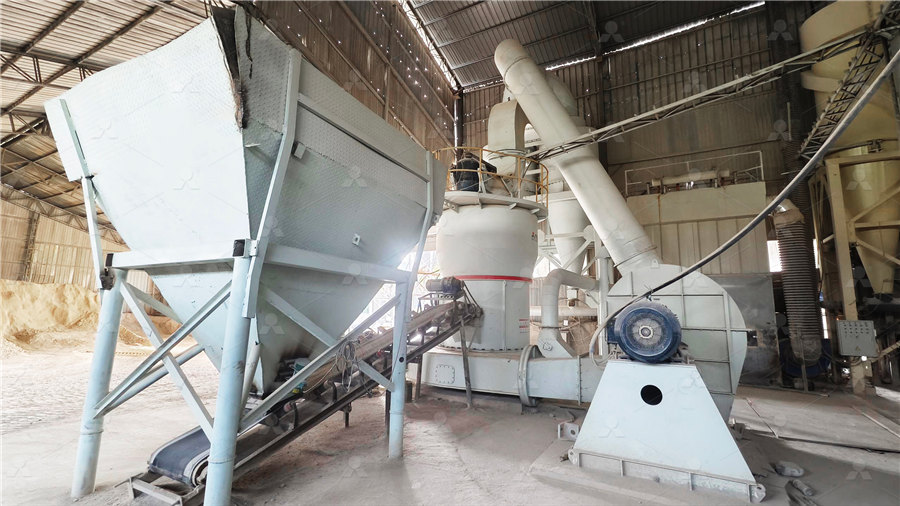
Types of Crushers: Choosing the Right One for Each Stage
2024年7月17日 They produce smaller particle sizes and can generate fine needlelike particles, but can only handle dry to slightly wet materials Sticky materials may cause machine blockages With a maximum capacity of up to 8,898 t/h, gyratory crushers are highly effective in medium to large mining operations and construction material production lines, though they are relatively 2024年4月19日 Atrition crushing is great for the production of very fine particle sizes and it is commonly used in mineral processing and mining for grinding ore Shear Crushing : Shear crushing takes a shearing force and applies it to the material, which results in the formation of cracks on the weak planesTypes of Crushers Explained: Everything You Need to Know JXSC5 Ball mills are used for wet grinding iron ore, gold/copper ore, nickel ore and other ores, as well as lime/limestone for flue gas desulphurisation systems, coal and other raw materialsSIZE REDUCTION BY GRINDING METHODS By ResearchGateBall mills are progressively used to grind the ores for particle size reduction and to liberate valuable minerals from the ores The grinding of ore is a highly energyintensive process [1–4] In this process, the size of the particle obtained depends on the energy consumption of the ball mill The major challenge encountered in theEstimation of Grinding Time for Desired Particle Size Distribution
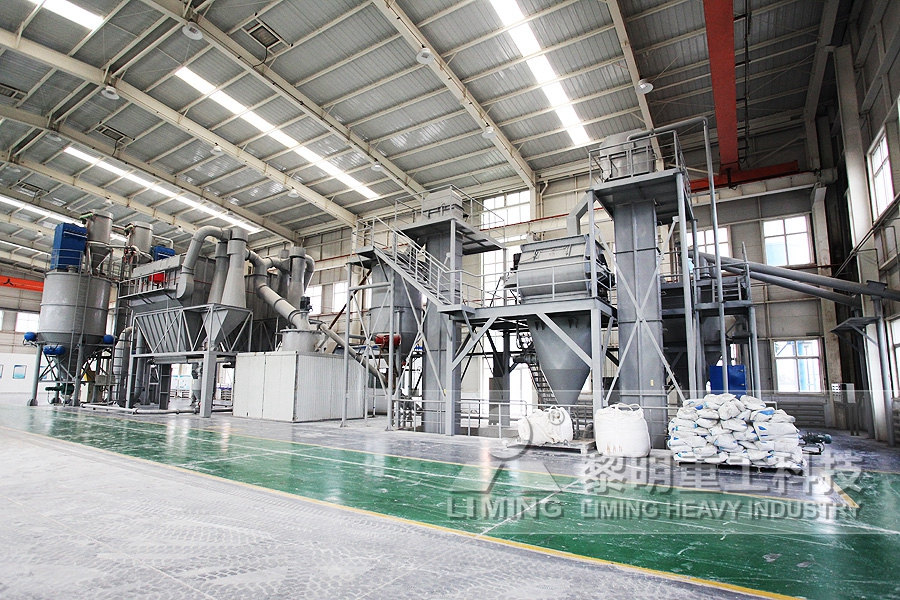
Research of Ore Particle Size Detection Based on Image Processing
2017年9月30日 The ore particle size distribution is an important basis for the evaluation of crushing effect The particle size parameters mainly include the particle area, perimeter, equivalent diameter, shape factor and so on In order to obtain the ore particle size distribution, we mainly study the following aspects: (1)2016年7月8日 UNTIL THE THIRD THEORY OF COMMINUTION of “Work Index” method of determining crushing and grinding mill size was introduced, there was no way of accurately figuring the most applicable, most economical Equipment Sizing: Crusher or Grinding MillHowever, despite its advantages in terms of particle size control and costeffectiveness, the VSI Mill is not commonly used in copper ore mining operations due to its limited capacity for handling large amounts of material SAG mills have proven to be efficient and reliable machines for grinding copper ore in the mining industryUnderstanding the SAG Mill in Copper Ore Mining Process2024年7月10日 Grinding Machines: These machines perform flat, cylindrical, or centerless grinding operations They feature motordriven wheels that remove material from surfaces Common types include bench grinders, hand grinders, pedestal grinders, portable grinders, flexible shaft grinders, and precision grinders, each suited for specific applications and What is Grinding: Definition, Types, Uses, and Working Process
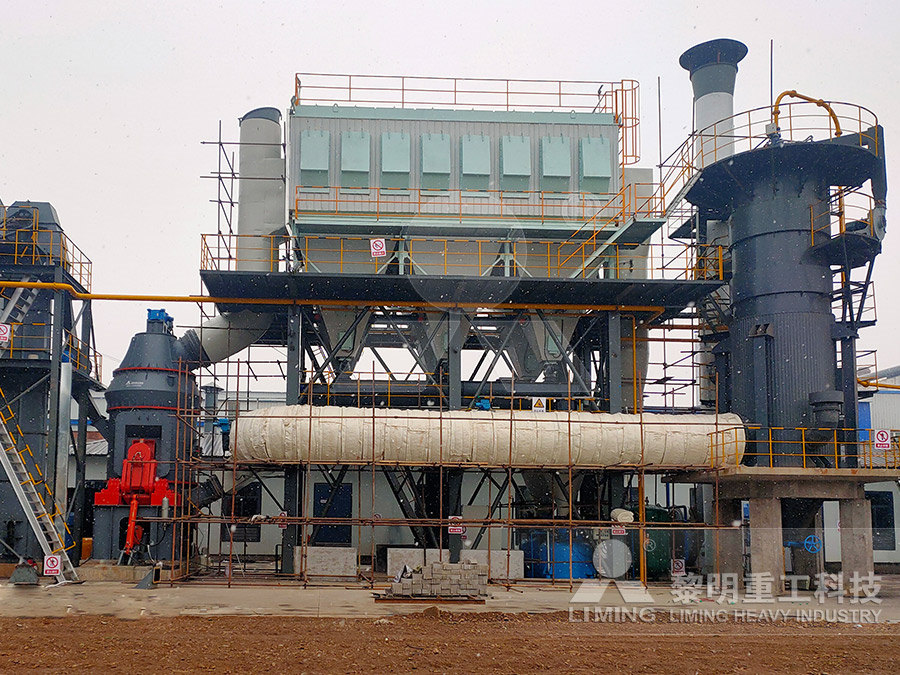
Pulverization 1: Definition and purpose | THINKY USA
2019年10月31日 “Crushing” refers to pulverization in the region where the particle size of the crushed material is relatively large (the maximum particle size is 1 mm or more) There is no clear boundary between grinding in a narrow sense and crushing, and the distinction remains vague2013年1月1日 Grinding performance was assessed by determining the throughput, specific rate of breakage, particle size distribution, power consumption, and energy required for grinding using a hammermill(PDF) The effect of moisture content on the grinding performance 2017年3月20日 An effect of a grinding method, that is ball mill and high pressure grinding rolls (HPGR), on the particle size, specific surface area and particle shape of an iron ore concentrate was studiedPhysicochemical Problems of Mineral Processing Investigation achieve the desired particle size, but jet milling is most often used to achieve particle sizes ranging from one to 10 microns Factors that affect the product’s fineness include: • Initial particle size • Feed and air flow rates • Nozzle pressure and angle • Chamber diameter and width • Product outlet diameterMILLING METHODS COMPARISON GUIDE Custom Processing
.jpg)
How to choose lead zinc ore grinding process and grinding
2023年7月30日 Preparation stage: CRUSHING AND SCREENING: Determine the particle size of lead zinc ore by crushing and screening choose the model of grinding equipment Strive to control the grinding size of leadzinc ore within a reasonable range, ; PhoneNo/WhatsApp:+06;2017年9月1日 With the continual depletion of high grade simple ore bodies, more complex, finely disseminated ore bodies are being processed, which has led to an increase in the prevalence of fine grinding (Sinnott et al, 2006)This has been evident in the platinum group element (PGE) industry in South Africa, where the Bushveld Complex hosts 70% of global Fine grinding: How mill type affects particle shape characteristics Keywords Particle size distribution (PSD) Retention time Comminution Characterization studies 1 Introduction Ball mills are progressively used to grind the ores for particle size reduction and to liberate valuable minerals from the ores The (PDF) Estimation of Grinding Time for Desired Particle Size These losses are due to a liberation mesh not absolutely achieved at 6 mm It should be possible to intensify the grinding of the feed product in order to obtain a 163 mm fraction in the jig However, due to commercially stipulated particle (PDF) Beneficiation of low grade manganese ore by
.jpg)
Grinding Modeling and Energy Efficiency in Ore/Raw Material
2022年8月31日 Dear Colleagues, The grinding process, as a primary stage of ore/raw material processing, is a necessary operation in beneficiation plants It not only provides the appropriate particle size for subsequent separation operations but also enables the liberation of valuable minerals from the gangue2017年10月2日 Figure 2 makes a simple but very important point that is often overlooked Even for the same ore at the same grind size (with all of the same simple grinding efficiency indices), the observed flotation recovery (and grade) in the plant can be strongly influenced by both the choice of the collector type as well as by that collector’s dosageEffect of P80 Grind Size on Flotation Collector 911Metallurgistparticle size is small to improve dissolution rate, solubility, binding strength and dispersion properties Many solid materials exist/present in sizes that are too large to be used directly Thus, such materials must be reduced in size before use Size reduction machines more commonly reduce the size of solids by (a) compression, (b) Âmpact,size reductionThe oldest and bestknown method is particle size determination by sieve analysis The particle size distribution is defined via the mass or volume Sieve analysis is used to divide the granular material into size fractions and then to determine the weight of these fractions In this way a relatively broad particle size spectrum can beThe Basic Principles of Sieve Analysis RETSCH
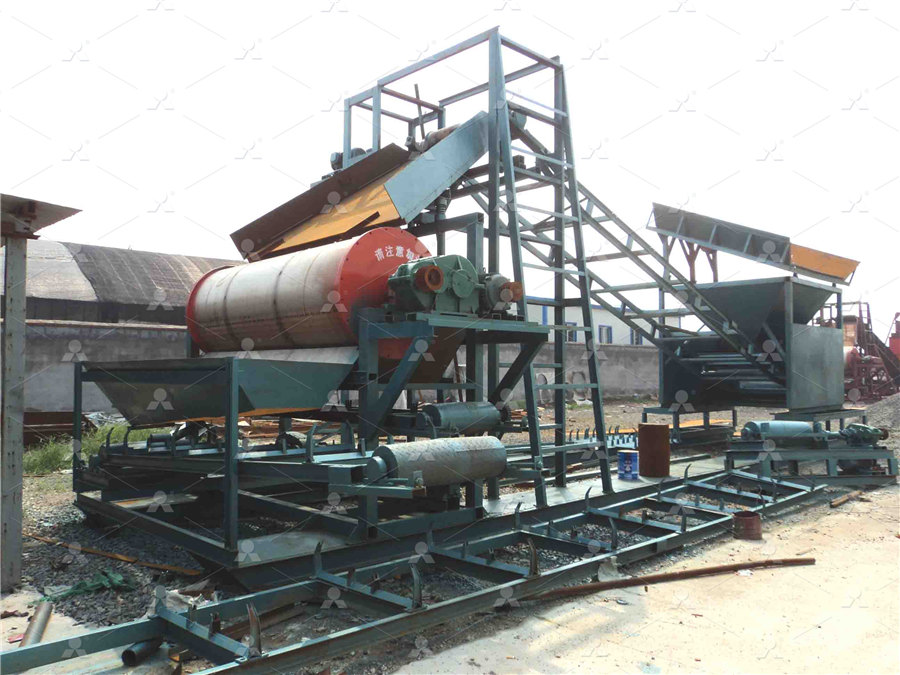
Investigation on Iron Ore Grinding based on Particle Size Distribution
2020年5月28日 The feed samples of X, Y, and Z iron ores were ground in the BBM (ball mill refers to a BBM of size 300 mm × 300 mm with smooth liners) to identify the PSD, BWI, and RT of each ore Grinding experiments were conducted according to Bond’s standard test procedure []For each iron ore sample, the RT taken to produce 250% circulating load in the BBM was 2022年1月23日 In the experience of the authors’ the following product particle size criteria are most common % passing 17 to 13 mm, 98% or greater % passing 45 µm P80, 250 to 700 µm In the experience of the authors’ typical feed size distribution specifications are Maximum particle size, 20–40 mm 80% passing, 8–20 mmPhysical Bauxite Processing: Crushing and Grinding of Bauxite2016年1月1日 For a particular operation where the ore size is known, it is necessary to estimate the diameter of rolls required for a specific degree of size reduction To estimate the roll diameter, it is convenient to assume that the particle to be crushed is spherical and roll surfaces are smoothRoll Crushers ScienceDirect2017年2月1日 The particle size of the hematite used in this study is close in size and surface area to an industrial iron ore concentrate Reduction Kinetics of Compact Hematite with Hydrogen from 600 to HPGR effect on the particle size and shape of iron ore
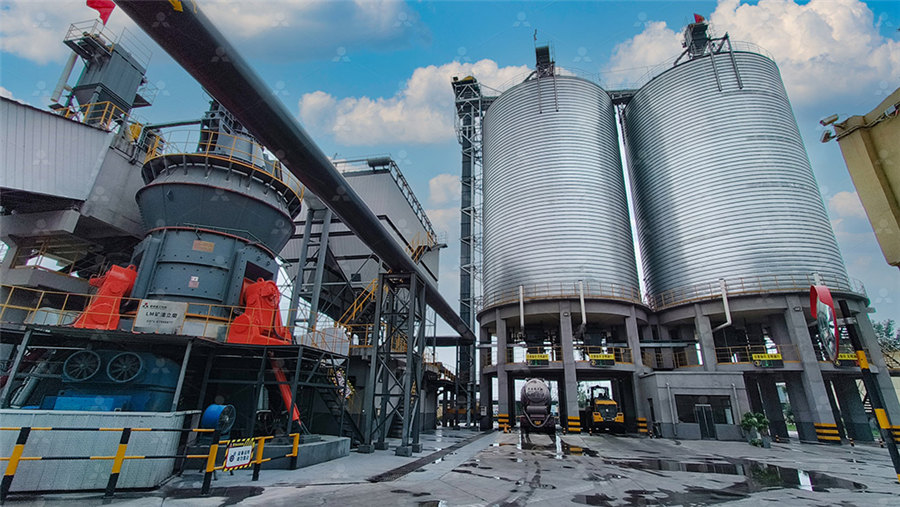
Predicting Particle Size of Copper Ore Grinding With Stochastic
2024年8月7日 This article presents a case study on predicting the particle size of copper ore grinding with stochastic configuration networks (SCNs) A set of temporal data was collected from the copper ore grinding process for building the predictive model The wellknown least absolute shrinkage and selection operator (LASSO) is employed for temporal feature selection Then, 2022年10月26日 The particle size composition of grinding products will significantly affect the technical and economic indexes of subsequent separation operations The polymetallic complex ores from Tongkeng and Gaofeng are Research on Grinding Characteristics and Comparison 2023年4月20日 For flotation concentrators, ore particle size (also known as grinding fineness) is an important factor affecting the final flotation index Practice has shown that the appropriate particle size generally means that more than 80% of the useful minerals have been dissociated from the monomersOre Particle Size Affects Flotation Index JXSC Mineral2022年2月28日 An investigation conducted on magnetite ore grinding with a dry HPGR machine to reduce the particle size from 50 mm to 90 µm has revealed that using two stages HPGR closed circuit with an air classifier can reduce energy consumption by 46% compared to a circuit in which there is a tertiary crushing with a wet ball millGrinding SpringerLink
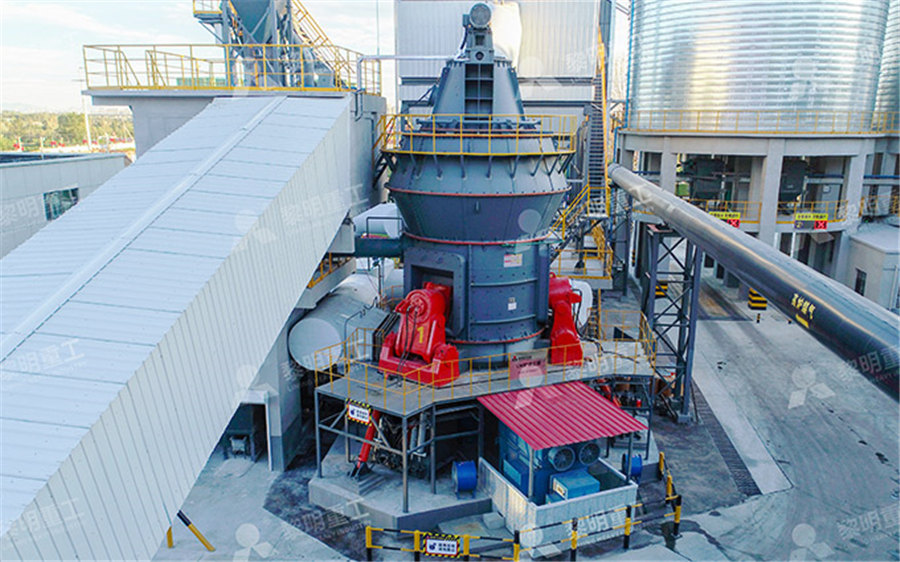
Particle size distribution (PSD) of the mill feed
The dosage of a collector is an important factor that determines the efficiency of a froth flotation process The representative sample of the carbonatitic Palabora copper ore ground 45 % passing 2015年6月19日 The basic parameters used in ball mill design (power calculations), rod mill or any tumbling mill sizing are; material to be ground, characteristics, Bond Work Index, bulk density, specific density, desired mill tonnage capacity DTPH, operating % solids or pulp density, feed size as F80 and maximum ‘chunk size’, product size as P80 and maximum and finally the type of Ball Mill Design/Power Calculation 911Metallurgist2024年6月11日 In this study, the evolution behavior of the particle size distribution during the grinding process was examined with fractal theory According to the distribution index k of the Rosin–Rammler–Benne model, the relationship between the fractal dimension D of the fractal theory and the distribution index k is discussed The fractal dimension D was used to evaluate Effect of Solid Concentration on Particle Size Distribution and 2019年3月28日 The prediction of grinding particle size is an effective measure to optimize the grinding process Cassiterite polymetallic sulfide ore and leadzinc ore, as the research object in this paper Research on prediction model of ore grinding particle size distribution
.jpg)
Research of iron ore grinding in a verticalrollermill
2015年3月15日 This mechanism is more energyefficient and usually produces a narrower particle size distribution than ball milling (Fandrich et al 2007) Also, bed breakage increases the liberation of the