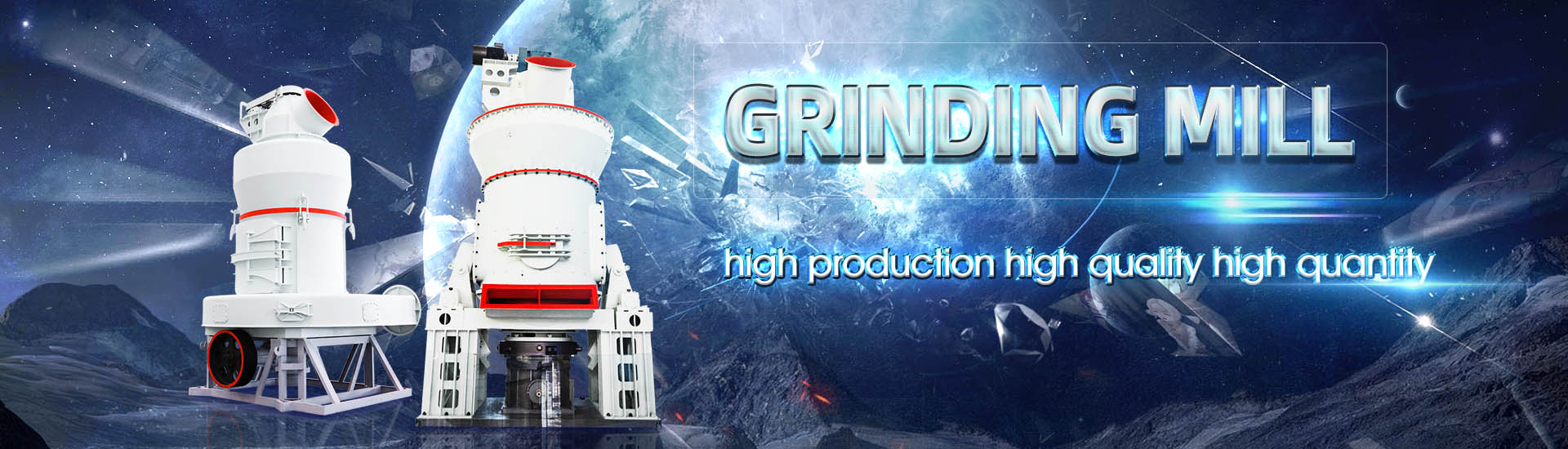
Failure analysis of industrial roller mill
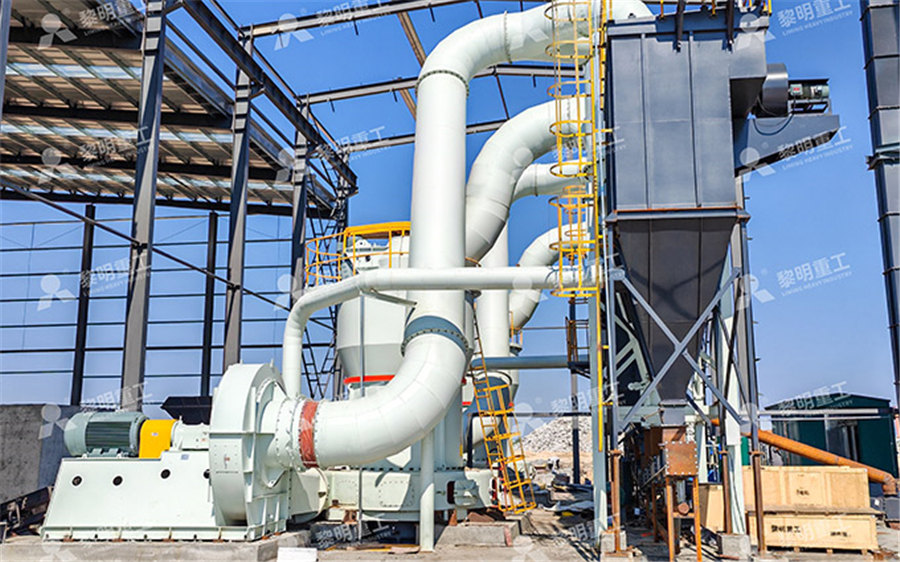
Failure mode Effect Analysis of Rollers in Mill Stand IJIRSET
The failure mode and effect analysis is used to identify and analyzed: (a) all failure mode of different parts of the system, (b) effects of these failure mode on the system and (c) how to 2014年7月30日 The objective of this study is to analyze different failures associated with rollers in the mill stand using Failure Mode Effect Analysis (FMEA) The values of severity, probability of occurrence and detection of Failure Analysis of Rollers in mill stand using Failure 2023年11月21日 Several reasons have been described in studies for the failure of vertical roller in grinding mill Unnatural vibration, short comings in maintenance, deviation in operating Operational Failure of Vertical Roller Attached to a Grinding Mill The samples of prematurely failed roll samples collected from steel plant were examined for their chemistry, inclusion content, microstructures, carbide characteristics, hardness and the Failure analysis of rolls of cold rolling mill in steel plant
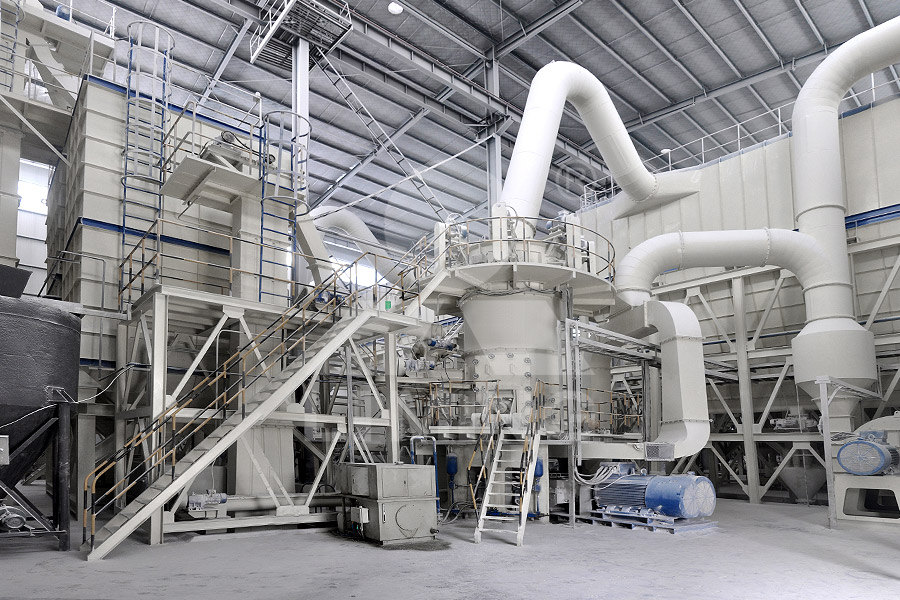
Fault Diagnosis and Root Cause Failure Analysis of Press Roller Mill
2019年7月31日 This case study is to identify and evaluate the root cause for failure of a roller press mill Cement plant has a heavy crushing operation the roller’s top surface is eroded, 2020年1月1日 The five steps of failure analysis assure failure validity, localize/characterize faults, sample preparation/defect tracing, physical/chemical characterization and root cause Fault Diagnosis and Root Cause Failure Analysis of Press Roller Mill 2024年3月22日 This study employed sound analysis using a smartphone, multiresolution analysis, and density of maxima to detect failure patterns in vertical roller mills It was Soundbased diagnosis of failure in a vertical roller mill2015年4月1日 In hot rolling mills, premature failure of rolls is a major concern This work describes two different types of roll failure Case I: enhanced ICDP Bottom roll of fifth stand Failure analysis of work rolls of a thin hot strip mill
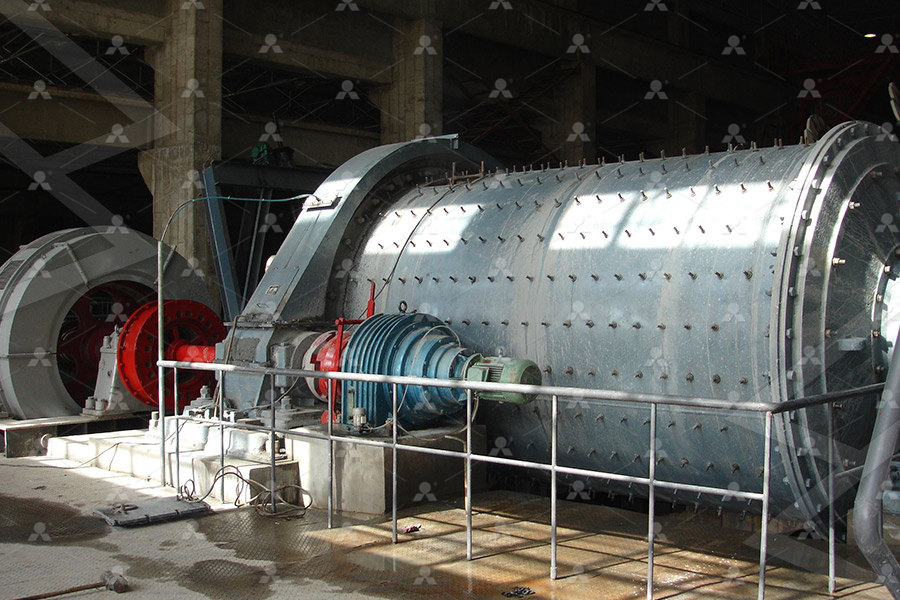
Intelligent fault diagnosis of rolling mills based on dual attention
2022年11月30日 Aiming at these problems, this paper proposes a new system for rolling mill fault detection based on time–frequency image and dualattention guided feature 2007年9月1日 A detailed analysis of all the elements which influenced failure was carried out, namely, the cause of all failures was determined and all fracture surfaces are described; the Failure analysis of rolls with grooves ScienceDirect2024年8月6日 Each grinding roller is borne by two roller bearings on the axle of the pressure yoke The bearings are oil lubricated, and oil level cannot be checked in running condition due to design constraints The bearing of new grinding roller assembly damaged within 1 service month Bearing mode of failure was seizure, and it happened due to lack of oilFailure Analysis of Pulverized Coal Injection (PCI) Mill Grinding 2022年5月31日 Analysis of vertical roller mill performance with changes in material properties and operating such as jaw crushers and cone crushers (Johansson et al, 2017, Wills and NapierMunn, 2007); where the material failure is mainly caused by compressive stress The vertical Due to the limitation of industrial experiments, Analysis of vertical roller mill performance with changes in
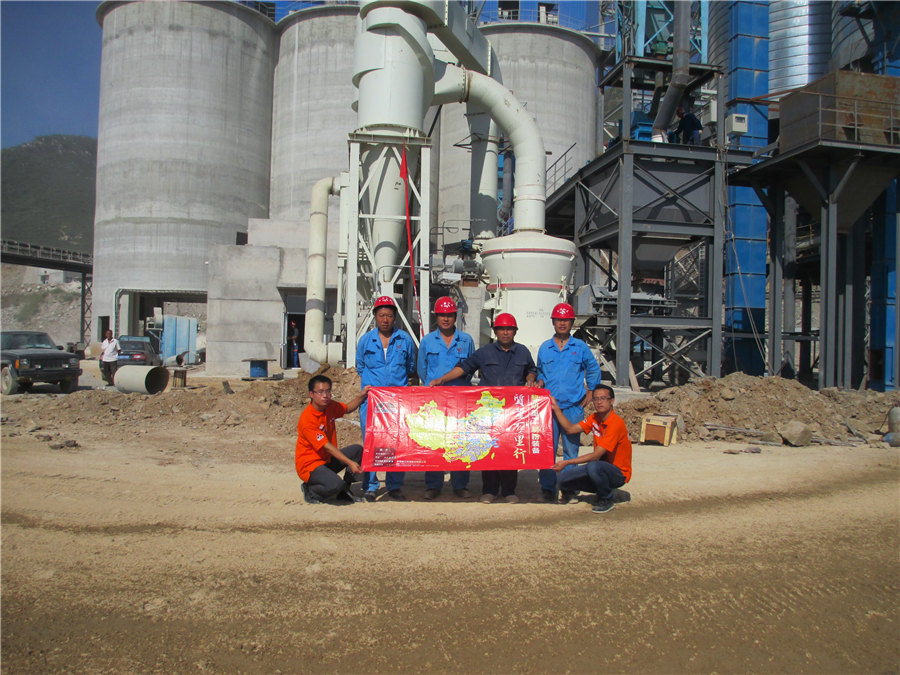
Application of Design Failure Modes and Effect
International Journal of Engineering Research Volume No4, Issue No12, pp : 663667 ISSN:23196890)(online),23475013(print) 01 Dec 2015 Application of Design Failure Modes and Effect Analysis (DFMEA) to Vertical Roller Mill Keywords Failure analysis Roller press mill Clinker SEM Fracture Case study S Babu () under an open environment or under the industrial fan This might have led to oxidation of the deposit as shown in Fig 2 It was found that the combination Fault Diagnosis and Root Cause Failure Analysis of Press Roller Mill 2019年8月19日 In hot rolling mills, premature failure of rolls is a major concern as it adversely affects the mill operation as well as production Analysis of failed roll materials and actual rolling conditions in service are therefore necessary to understand the roll failure mechanism and thereby improve the service life of rolls The hot strip mill referred here consists of two stands Analysis of a Progressive Failure of a Work Roll in Hot Strip Mill2015年4月1日 Chemical analysis was carried out using portable XRF alloy analyzer The chemical analysis of the defective location and its surroundings is given in Table 3 The chemical analysis report of the defective location revealed high niobium and iron content which indicates that the entrapment was basically ferroniobium (with ∼64%Nb)Failure analysis of work rolls of a thin hot strip mill
.jpg)
Failure Analysis of a Cylindrical Roller Bearing from a Rolling Mill
2011年3月23日 Premature failure of a cylindrical roller bearing of a gear box input shaft from a hot strip mill has been investigated The pins of the cylindrical rollers of the bearing broke from the welded joints at their ends on the cage ring Investigations were carried out on the failed roller pin and the welded joint The investigation consists of visual observation, chemical analysis 2023年11月21日 In the present incident, one of the rollers of grinding mill in cement plant failed during operation, exhibiting longitudinal cracking over inner surface Deposition welding was carried out just before the incident to match the wornout profile of the roller Investigation revealed that the subsurface of the cracked region contained discontinuities like blow holes Operational Failure of Vertical Roller Attached to a Grinding Mill 2015年1月1日 This paper presents a metallurgical failure analysis on failed material AISI 1020 bush used in industrial roller chains This failure analysis study is carried out using the methodologies of A review of failure analysis found in industrial roller chainsmaterials Article Internal Cracks and NonMetallic Inclusions as Root Causes of Casting Failure in Sugar Mill Roller Shafts Muhammad Jamil 1,2, Aqib Mashood Khan 1,2, Hussien Hegab 3, Shoaib Sarfraz 4, Neeraj Sharma 5, Mozammel Mia 6, Munish Kumar Gupta 7, GuLong Zhao 2, H Moustabchir 8 and Catalin I Pruncu 9,10,* 1 Department of Industrial Engineering, University Internal Cracks and NonMetallic Inclusions as Root Causes of
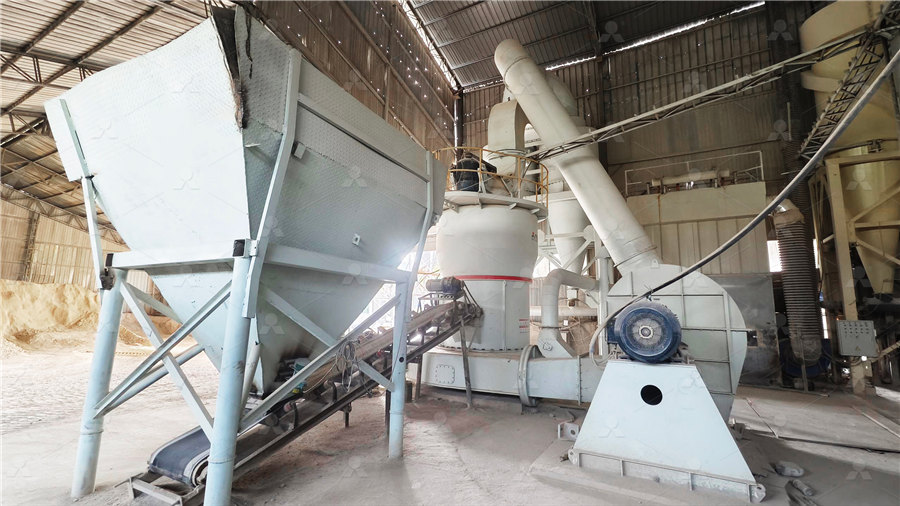
Major causes of roller bearing failure and
2019年6月14日 As many as 13% of industrial motor failures happen because of bearing failures Moreover, 60% of equipment breakdowns involve bearing wear Most defects result from a combination of failure modes, and each failure is 2019年8月3日 The results also found alumina and oxide type nonmetallic inclusions, which led to surface/subsurface cracks and ultimately the rejection of the mill roller shaft A root cause analysis (RCA (PDF) Internal Cracks and NonMetallic Inclusions as 2015年12月1日 DesignFailure mode and effect analysis (DFMEA) is very important tool used in industries to detect failure during design stage DFMEA is a technique to find out causes of failure and their Application of Design Failure Modes and Effect 2011年3月23日 Premature failure of a cylindrical roller bearing of a gear box input shaft from a hot strip mill has been investigated The pins of the cylindrical rollers of the bearing broke from the welded joints at their ends on the cage ring Investigations were carried out on the failed roller pin and the welded joint The investigation consists of visual observation, chemical analysis Failure Analysis of a Cylindrical Roller Bearing from a Rolling Mill
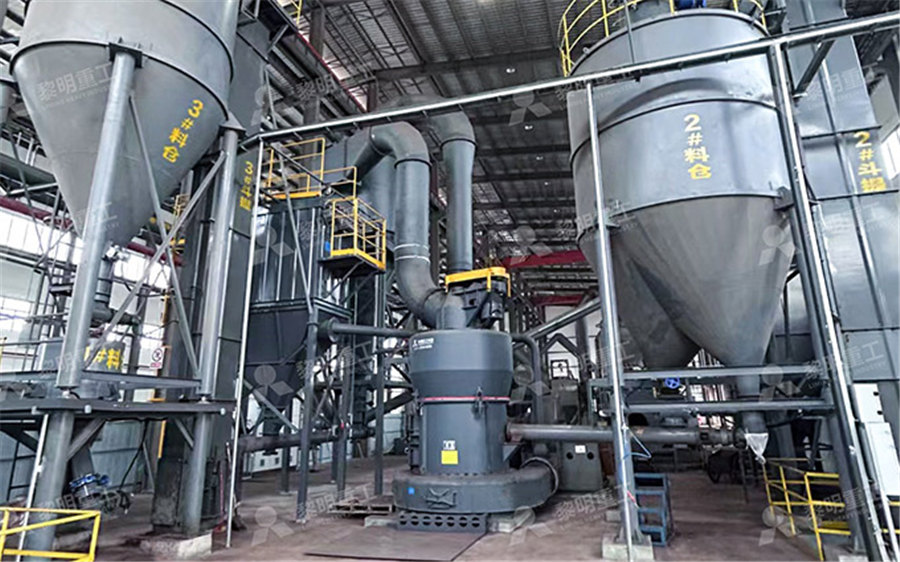
Application of Design Failure Modes and Effect Analysis (DFMEA)
2015年12月1日 Design FMEA is structured method of identifying potential failure modes and providing corrective actions before first production run occurs This paper aims to provide probable causes of failure, levels of effects of failure and corrective actions to be taken in the design phase for Bevel Planetary Vertical Roller Mill Gearbox Keywords—DFMEA, Bevel FAILURE ANALYSIS OF TIRE ROLLER IN VERTICAL ROLLER MILL AT FINISH MILL TUBAN 3 PT SEMEN INDONESIA Wikan Jatimurti, ST, MSc Department of Materials and Metallurgical Engineering Faculty Of Industrial Technology Sepuluh Nopember Institute of Technology Surabaya At Vertical Roller mill failure often occurs, especially onANALISA KEGAGALAN TIRE ROLLER PADA VERTICAL ROLLER MILL DI FINISH MILL FAILURE ANALYSIS OF ROCKER ARM IN VERTICAL ROLLER MILL AT COAL MILL PLANT TUBAN 1 PT Department of Materials and Metallurgical Engineering Faculty of Industrial Technology Sepuluh Nopember Institute of Technology Surabaya 2016 iv (Halaman ini sengaja dikosongkan) v vi Vertical Roller mill failure often occurs, ANALISA KEGAGALAN ROCKER ARM PADA VERTICAL ROLLER MILL DI COAL MILL 2014年7月25日 In this paper, vibration characteristics of a Vertical Roller Mill (VRM) are studied by using physical parameters of an operating VRM The mathematical model is derived and simulated for a set of Vibration Analysis of a Vertical Roller Mill: Modeling and Validation
.jpg)
Tribochemistry of Sugar Mill Roller Shaft Materials Academia
Three types of grooves are commonly manufactured into finished sugar mill roller shafts; • • • Fine grooves, containing 5–20 mm of pitch Medium grooves, containing 20–50 mm of pitch Coarse grooves, containing >50 mm of pitch Materials 2019, 12, 2474 3 of 22 Figure 1 Sugar mill roller shaft with final groove ready for shipment2015年12月1日 This paper presents a metallurgical failure analysis on failed material AISI 1020 bush used in industrial roller chains This failure analysis study is carried out using the methodologies of A Review of Failure analysis found in Industrial Roller ChainsDesign and Analysis of Roller for Hot Rolling Mill Mayur Kadu1, Prof S M Awatade2 1PG Student, industrial processes Rolling using grooved rolls (as a category different from grooveless rolling) is the most common practice in production of steel sections Key tools in Design and Analysis of Roller for Hot Rolling Mill2011年8月1日 The premature failure of a cylindrical roller bearing took place during service, with a total operation time of 100 h The failure cause was analyzed by macroscopic and microscopic observation Failure Analysis of a Cylindrical Roller Bearing from a Rolling Mill
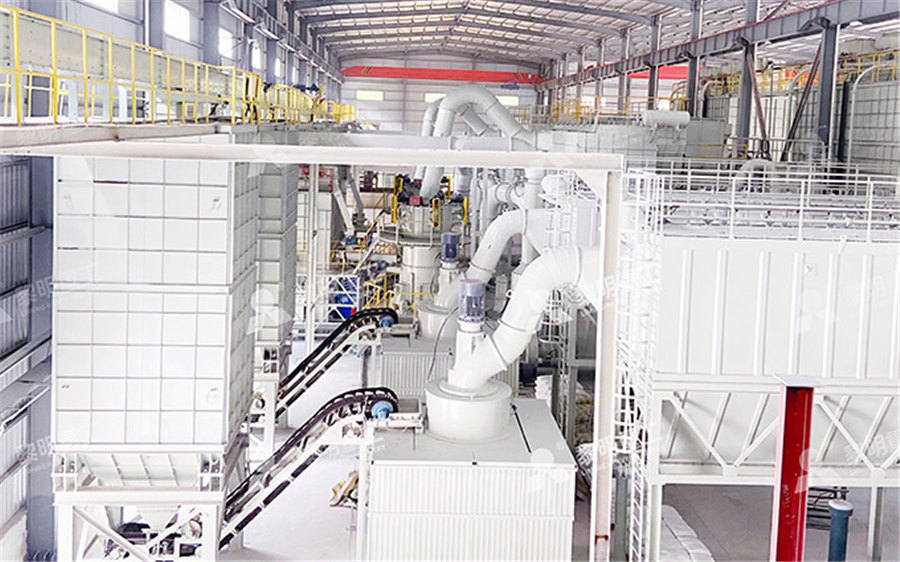
Analysis and Optimization of Grinding Performance of
2022年1月23日 This work concentrates on the energy consumption and grinding energy efficiency of a laboratory vertical roller mill (VRM) under various operating parameters For design of experiments (DOE), the response surface method 2012年9月8日 Failure analysis of a guide roller used in a bar mill of an integrated steel plant has been presented The guide rollers are positioned at the entry of rolling stands and act as guide in the multigrooved pass for aligning the hot bars and hold the twisted oval bar while it enters a round pass The hot bar is at a temperature of ≈1100°C, and the rollers are water cooled The Cracking of a Tool Steel Guide Roller in a Bar MillFailure Analysis of Rollers in mill stand using Failure mode Effect Analysis × IECON 2012 38th Annual Conference on IEEE Industrial Electronics Society, 2012 download Download free PDF View PDF chevronright The Paris System for Reporting Urinary Cytology: A MetaAnalysisFailure Analysis of Rollers in mill stand using Failure mode Effect The mill roll wear Roll wear is the most common failure mode for roll, which is rolled by the work roll and backup roll and work roll and the friction caused between In the production process, work roll for a long time in a hot environment, the roller surface produces a layer of dense, brittle but wear the oxide filmFailure mode and analysis of mill roll
.jpg)
Failure Analysis of Rollers in mill stand using Failure mode Effect
The research uses data collected from the industrial use at the as well as laboratory experiments carried out on a unique, Factor: 3449 (ISRA), Impact Factor: 1852 IJESRT INTERNATIONAL JOURNAL OF ENGINEERING SCIENCES RESEARCH TECHNOLOGY Failure Analysis of Rollers in mill stand using Failure mode Effect Analysis * Tadisetti Premsai, 2023年12月4日 An industrialscale vertical roller mill has been developed and successfully simulated employing the discrete element method Analysis of the VRM to many operational parameters shows trends that are in qualitative agreement with the industrial practiceNumerical Investigation of Vertical Roller Mill Operation Using Engineering Failure Analysis, 2011 download Download free PDF View PDF chevronright An analysis of forces August 2011 Walmiki SRathod, Chetan T Rathod (2012), Design and Analysis of Two Roller Sugar mill using FEA Technique, International Journal of Scientific Engineering and Technology, volume No 1, Issue No3, pg:148152 VB IJERTStatic Structural Analysis of Crushing Rollers of Three Roller 2019年10月1日 This paper presents a metallurgical failure analysis on failed material AISI 1020 bush used in industrial roller chains This failure analysis study is carried out using the methodologies of (PDF) Metallurgical investigation of failure analysis in industrial
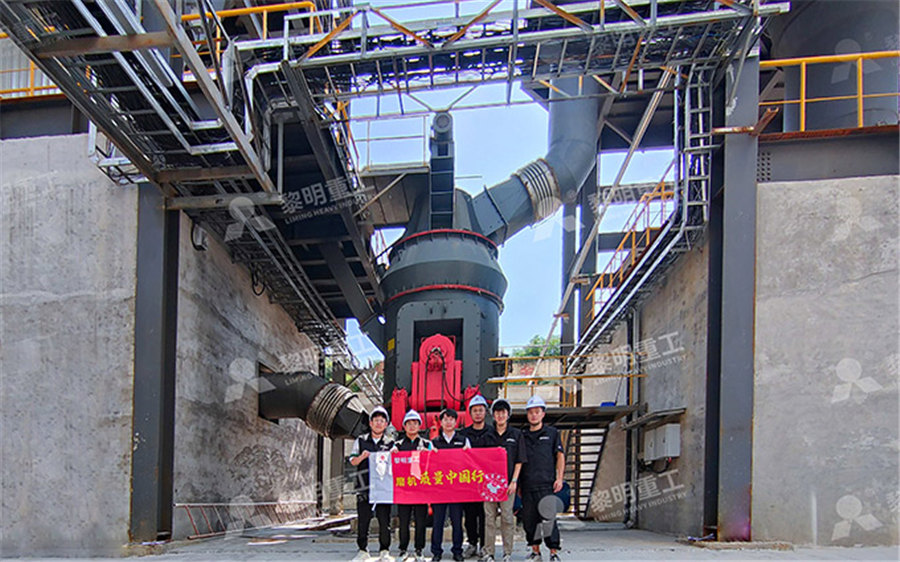
Failure Analysis of Rollers in mill stand using Failure mode Effect
The research uses data collected from the industrial use at the as well as laboratory experiments carried out on a unique, Factor: 3449 (ISRA), Impact Factor: 1852 IJESRT INTERNATIONAL JOURNAL OF ENGINEERING SCIENCES RESEARCH TECHNOLOGY Failure Analysis of Rollers in mill stand using Failure mode Effect Analysis * Tadisetti Premsai, FAILURE ANALYSIS OF TIRE ROLLER IN VERTICAL ROLLER MILL AT FINISH MILL TUBAN 3 PT SEMEN INDONESIA Wikan Jatimurti, ST, MSc Department of Materials and Metallurgical Engineering Faculty Of Industrial Technology Sepuluh Nopember Institute of Technology Surabaya At Vertical Roller mill failure often occurs, especially onANALISA KEGAGALAN TIRE ROLLER PADA VERTICAL ROLLER MILL DI FINISH MILL 2019年8月3日 materials Article Internal Cracks and NonMetallic Inclusions as Root Causes of Casting Failure in Sugar Mill Roller Shafts Muhammad Jamil 1,2, Aqib Mashood Khan 1,2, Hussien Hegab 3, Shoaib Sarfraz 4, Neeraj Sharma 5, Mozammel Mia 6, Munish Kumar Gupta 7, GuLong Zhao 2, H Moustabchir 8 and Catalin I Pruncu 9,10,* 1 Department of Industrial Internal Cracks and NonMetallic Inclusions as Root Causes of 2023年8月24日 Keywords: vertical roller mill, acoustic analy sis, vibration analysis, multiresolution analysis, SACDMSoundbased diagnosis of failure in a vertical roller mill
.jpg)
Analysis of mill rolls failure modes and causes
2024年9月26日 Any form of failure will directly shorten the service life of the roller Therefore, it is necessary to combine the failure form of the roll, explore the cause of its occurrence, and find an effective way to extend the service life of the mill rolls 1 Mill rolls peeling The peeling of mill rolls is the primary form of damageFailure analysis of a pull rod actuator of an ATOX raw Department of Mechanical and Industrial Engineering, Campus de Caparica, 2829526 Monte de Caparica, Portugal b SECIL The pull rod under study is one of the three rods that connect the three existing hydraulic cylinders to the roller mill and it is used to exert grinding (PDF) Failure analysis of a pull rod actuator of an ATOX raw mill Three types of grooves are commonly manufactured into finished sugar mill roller shafts; • • • Fine grooves, containing 5–20 mm of pitch Medium grooves, containing 20–50 mm of pitch Coarse grooves, containing >50 mm of pitch Materials 2019, 12, 2474 3 of 22 Figure 1 Sugar mill roller shaft with final groove ready for shipment(PDF) Internal Cracks and NonMetallic Inclusions as Root Causes 2017年3月24日 A worn backuproller in rolling mill was repaired by hardfacing technology The routine flaw detection after machining revealed that randomly distributed circumferential short cracks occurred on the surface of repaired roller Sectional observation throughout hardfacing region showed that intensively distributed transverse short cracks were also present inside the Cracking Failure of Hardfacing Layer of Repaired BackupRoller
.jpg)
Tribological Failure Analysis of Journal Bearings used in Sugar Mill
2023年1月1日 1 Introduction The sugar mills roller is used to take the juice from sugar cane The typical arrangement of the sugar roller is three roller mill arrangements so that maximum amount extraction of juice takes place [2], [8]The cane crushing can be done effectively by designing system in such way to have high coefficient of friction with lesser amount of speed 2021年6月1日 Download Citation Condition monitoring and fault detection in roller bearing used in rolling mill by acoustic emission and vibration analysis Bearings for rolling elements are essential Condition monitoring and fault detection in roller bearing used in