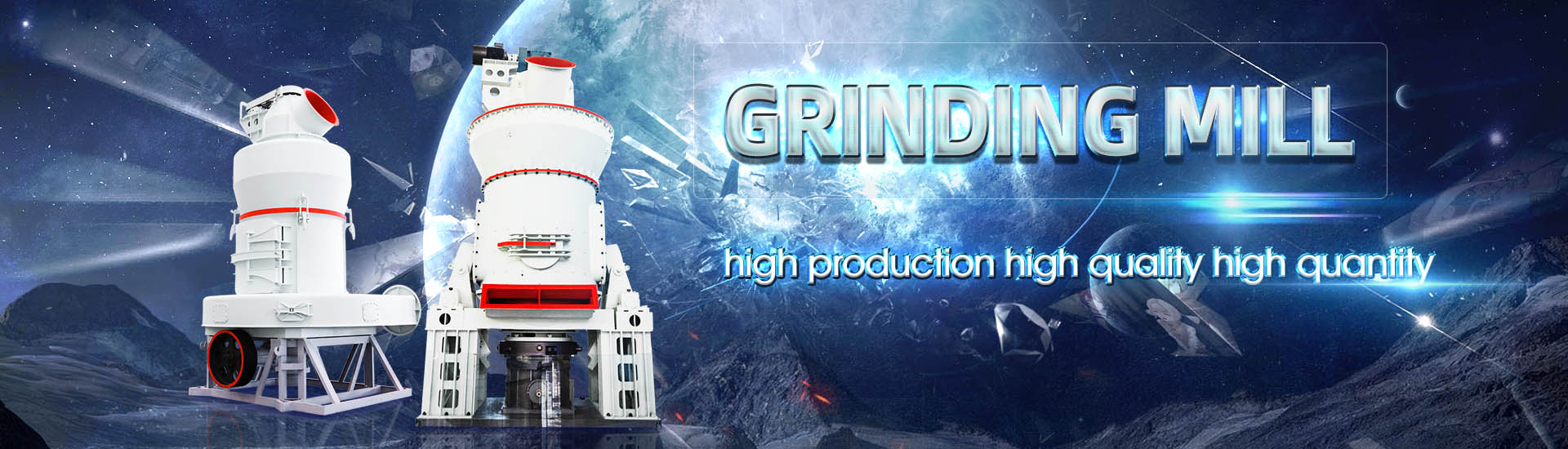
Selection of coal mill, coal
.jpg)
Coal Mill an overview ScienceDirect Topics
Mills are mechanical devices used to break different types of solid materials in small pieces by grinding, crushing or cutting In pulverised coalfired power plants, a pulveriser coal mill grinds 2009年1月1日 This paper aims at providing some guideline to plant engineers and consultants for selecting the Appropriate type of coal mill reject handing system for coal fired thermal Selection of coal mill reject handling system for ResearchGate2009年9月20日 This paper presents a novel coal mill modeling technique using genetic algorithms (GAs) based on routine operation data measured onsite at Modeling and Parameter Identification of Coal Mill2015年11月1日 Coal mills are bottleneck in coal–fired power generation process due to difficulty in developing efficient controls and faults occurring inside the mills In this paper, a dynamic A unified thermomechanical model for coal mill operation
.jpg)
(PDF) Modeling and Control of Coal Mill Academia
Coal mill is an important component of the thermal power plant It is used to grind and dry the moisturized raw coal and transport the pulverized coal – air mixture to the boiler Poor dynamic 2019年9月9日 This paper presents a fault early warning approach of coal mills based on the Thermodynamic Law and data mining The Thermodynamic Law is used to describe the Research on early fault warning system of coal mills based on the 2007年8月20日 This paper presents a multisegment coal mill model that covers the whole milling process from mill startup to shutdown This multisegment mathematical model is derived Development of a Multisegment Coal Mill Model Using an 2020年4月7日 The main task of a coal mill system is to provide qualified fuel for the pulverized coal boiler In the coal mill system, raw coal is firstly grinded into fine powder, and then dried and transmitted into the boiler by the primary airModeling of Coal Mill System Used for Fault Simulation
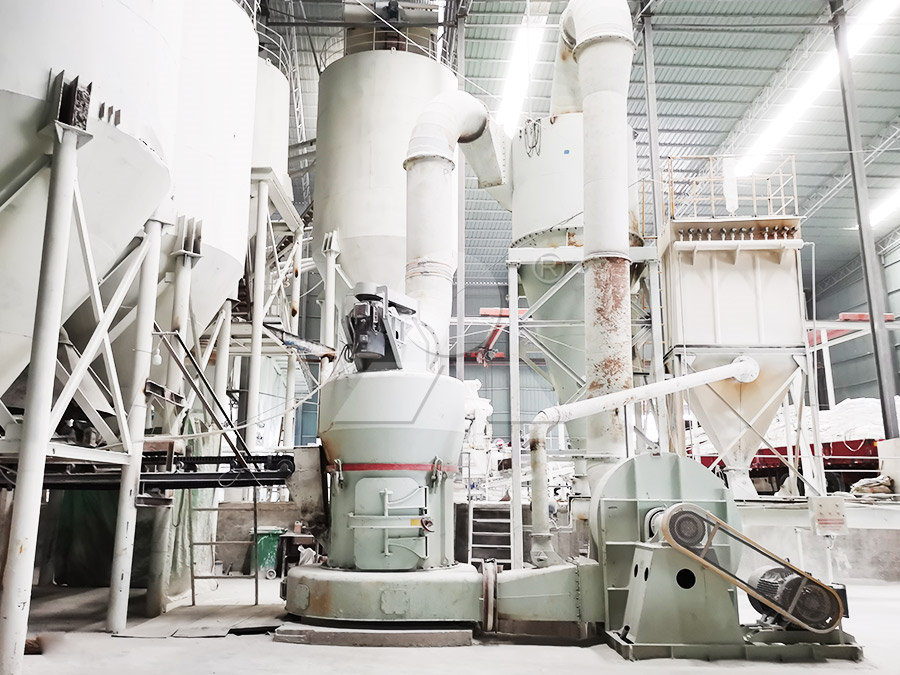
Coal Selection an overview ScienceDirect Topics
Various technologies to enhance coal preparation and selection have been used across the coal mines, increasing the competence of coal enterprises The coal chemical field is a big 2015年11月1日 As presented by Andersen et al (2009) and Odgaard, Stoustrup, and Mataji (2007), coal moisture imposes limit on the maximum load at which a coal mill can be operated and the load gradient (how fast the mill may change its operating point), if it is desired that the pulverized coal entering the furnace has moisture content less than or equal to a certain value A unified thermomechanical model for coal mill operation2020年4月2日 represent the temperature distribution in the boiler while PCs pipes at level 1 are not in service In the meanwhile, the others PC still in service and produced 700MWnettAnalysis of the Coal Milling Operations to the Boiler 2015年8月1日 Substantial savings, owing to reduced maintenance costs and production losses, can be achieved through fewer mill choking incidents, fewer mill runbacks, optimal mill operation, and rapid diagnoses of mill faults [5]Over the years, considerable research has been carried out for improving the operation of coal mills using better controls and diagnosing faults in mills at Review of control and fault diagnosis methods applied to coal
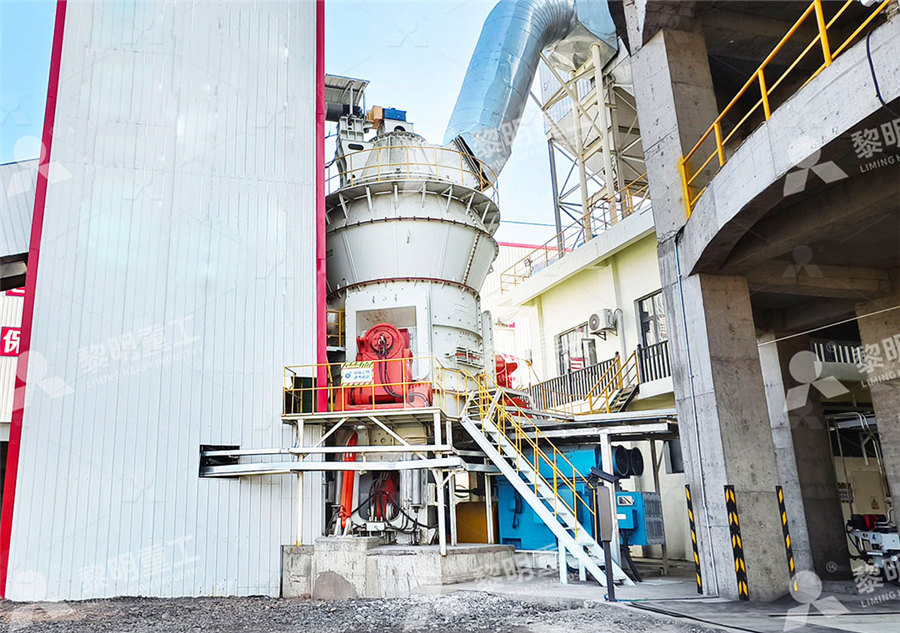
How to choose coal grinding equipment? What are the basis for coal mill
Coal mill is an important part of the pulverizing system and an important auxiliary power equipment in power plant Its main task is to break and grind coal into pulverized coal to provide boiler equipment, its configuration will directly affect Vertical Coal Mill (VCM) is equipment for grinding and pulverizing coal into micron size Rotary kilns then use the powders as fuel burners The VCM has a housing section equipped with a lining The layout of the coal mill with a rotary classifiermill modelling technique for Etype coal mill and dynamic behaviour are developed using genetic algorithms [3] Genetic Algorithms (GAs) have been successfully applied to problems in business, engineering, and science Gas are stochastic, populationbased search and optimization algorithms inspired by the process of natural selection and Measurement and Control of Coal Pipe Temperature of Coal Mills 2020年4月7日 Monitoring and diagnosis of coal mill systems are critical to the security operation of power plants The traditional datadriven fault diagnosis methods often result in low fault recognition rate or even misjudgment due to the imbalance between fault data samples and normal data samples In order to obtain massive fault sample data effectively, based on the Modeling of Coal Mill System Used for Fault Simulation MDPI
.jpg)
How to choose coal grinding equipment? What are the basis for coal mill
Coal mill equipment selection 1: lowspeed coal mill The typical representative of low speed coal mill is the ball mill The working principle is: the highpower motor through the gearbox to drive this heavy round plate rotation, the steel ball in the simple is rotated to a certain height and then falls down, through the impact of the steel ball on the coal and between the steel ball Vertical coal grinding mill integrates crushing, drying, grinding, powder selection and conveying; It has simple system and compact structure Vertical coal mill covers an floor area about 50% of the coal ball mill with the same specification; Coal vertical mills can work in openair environments, greatly reducing the cost of investment The design of the vertical coal mill system is simple Vertical Coal Mill for Coal Grinding in Cement Plant Power PlantFrom the coal yard, the coal is transfer to the mill bunkers through conveyor belt The bunkers are sized for an effective capacity of twelve (12) hours at BMCR with design coal Each mill bunker has one hopper, connected to the feeders Mills operate when the bunker coal gate valves are opened, coal is allowed to flow to the gravimetric feedersAnalysis of the Coal Milling Operations to the Boiler Parameters2024年5月1日 Dual fault warning method for coal mill based on Autoformer WaveBound Author links open overlay panel Congzhi Huang a b, Shuangyan Qu a, Zhiwu Ke c d, Wei Zheng c d The validity of the model is based on the quantity and quality of the data and the selection of algorithms Table 2 Parameters related to operation condition of Dual fault warning method for coal mill based on ScienceDirect
.jpg)
Sectional view of MBF coal mill Download Scientific
A control oriented model was then developed by Fan (1994) and Fan and Rees (1994) In 2009, coal flow and outlet temperature of mill were modelled using mass and heat balance equations for startup Abstract: The paper presents development and validation of coal mill model (including the action of classifier) to be used for improved coal mill control The model is developed by using the mass and heat balance equations of the coal mill Genetic Algorithm is used to estimate the unknown parameters that are used in the model validationModeling and Control of Coal MillCoal water slurry ball mill (CWS ball mill) is the key equipment for coal water slurry fuel production, which is commonly used in coal water slurry power plant Coal water slurry ball mill is grinding equipment specially used for coal water slurry production Its specifications, structure and working conditions must meet the requirements of coal water slurry production scale, Coal Water Slurry Ball MillThe ball mill is a traditional coal pulverizer machine, which has been widely used since it was invented In the cement plant, the new dry process cement manufacturing requires the moisture content of coal powder to be 05% ~ 15%, while that of raw coal is 15% ~ 40%Coal Mill in Cement Plant
.jpg)
A Fault Early Warning Method for Coal Mills Based on Causality
2024年9月4日 In this paper, seven different LSTM models are constructed based on different feature selection methods, including expert experience, correlation, and causality, and these models are used to analyze the realworld coal mill faults for early warning, and the results show that, i) compared with the feature selection methods based on expert 2021年10月28日 To ensure stable operation of the roller mill and an effective reduction in the size of the coal–TP blend, the selection and use of uniformly and sufficiently torrefied wood pellets are importantMilling Characteristics of Coal and Torrefied Biomass Blends in a 631 Thermal coal selection Power plants generally operate most efficiently when firing the coals for which they Over the last 25 years, many power plants designed for Eastern bituminous coals upgraded coal handling systems, installed mill inerting systems, and upgraded mill drying capacity to successfully fire lowcost PRB coals Read Coal Selection an overview ScienceDirect TopicsInerting steam for Coal mill firepdf Free download as PDF File (pdf), Text File (txt) or read online for free This document provides a draft design guide for inerting medium speed vertical spindle coal pulverizers It discusses inerting system design considerations such as inerting media selection, steam source considerations, and steam piping considerationsInerting Steam For Coal Mill Fire PDF PDF Combustion Scribd
46.jpg)
Coping With Coal Quality Impacts on Power Plant Coal
This paper was brief, but hopefully has shown the importance of one aspect, mill performance, on many coal quality related issues At first glance one might not consider the influence mill fineness has on mill capacity, slagging and opacity; this paper has shown that it does indeed, and mill performance is only one of many areas of consideration2023年12月16日 The characteristics of HGI fractions of the blend coal were investigated One rejected coal (A) with three imported coals, Indonesian coal (B), Russian coal (G) and Australian coal (H), and their blends were tested for their grindability indices as per standard ASTM D 409 The fractions obtained from HGI tests were further assessed for its quality using their Utilization of Rejected Coal Through Blending Techniques in 2023年6月12日 We source the best quality coal products from local coal mines in the Witbank, Emalahleni area, and the rest of South Africa For many year s, we have served consumers all around the country Our coal products include South African Coal Mining Techniquesfor controlling the coal flow at the discharge of a centrifugal classifier The model was based on an existing installation of a Riley Power standalone classifier, and included ductwork from the discharge of the ball tube mill up to the classifier and coal pipes The full length of the coal pipes was replaced by13045 Coal Distributor Paper:Layout 1 Babcock Power
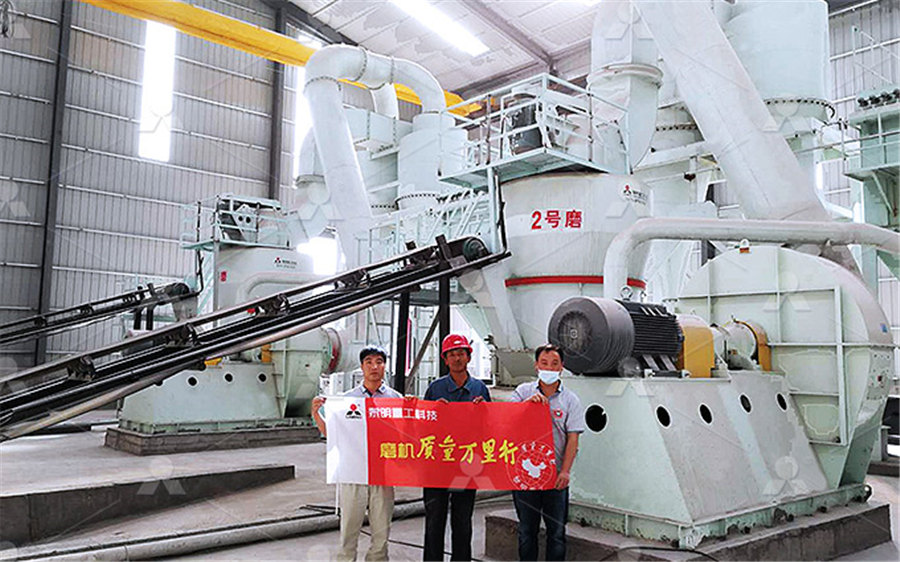
(PDF) Modeling and Control of Coal Mill Academia
Coal mill is an important component of the thermal power plant It is used to grind and dry the moisturized raw coal and transport the pulverized coal – air mixture to the boiler Poor dynamic performance of coal mill will lead to decrease in the overall efficiency of the power plant, The selection of mill system will depend mostly on the factors like initial capital cost, drying and grinding capacity required, cost of energy (power) etc Coal Mill Operational parameters: Mill Load (Kw or Amps) Mill sound/filling % (in ball mills) Mill Inlet Temperature (0 C)Coal Grinding Cement Plant Optimization4 Selection method The selection method of standard HP coal pulverizer can adopt computer software for accurate and detailed selection Users only need to provide raw coal data, boiler coal consumption, pulverized coal fineness and number of coal mills to the manufacturer, and the professional technical personnel of the manufacturer will feed back the selection results to the HP Bowl type millspower plant equipment2021年10月28日 CO2 emissions from coal power generation could be reduced by maximizing the amount of torrefied biomass that can be used in pulverizedcoalfired power plants In this study, to evaluate the milling performance of coal and torrefied wood pellets (TPs), various blend ratios were tested using a benchscale roller mill Neutral sugar analysis was performed to Milling Characteristics of Coal and Torrefied Biomass Blends in a
.jpg)
Industrial Coal Pulverizer Model Simulation and Parametric
2018年1月1日 A team from ABB designed a coal mill model for monitoring and control based on Fan and Rees principle using 3 particle size (Mercangoez et al 2011) A team of ABB Switzerland (Cortinovis et al 2013) designed a nonlinear coal mill model using former model given by the people from ABB considering 2 particle sizesThe Coal Striker Mill is a small Swing Hammer Crusher consisting of 8 rotary hammers passing over a perforated screen It is capable of sizing 6mm top size material to 212 micron in one operation and conforms to Australian Standard AS42641 The Coal Striker Mill is available in either a manual, automatic or the new cyclone modelCoal Striker Mill Wallerby Mining Products AustraliaA dynamic model of the coal mill system which has enough accuracy and adaptability for fault simulation, A datadriven modeling method with feature selection capability is proposed for the combustion process of a station boiler under multiworking conditions to derive a nonlinear optimization model for Optimization control of a pulverizing system on the basis of the 2007年8月20日 This paper presents a multisegment coal mill model that covers the whole milling process from mill startup to shutdown This multisegment mathematical model is derived through analysis of energy transferring, heat exchange, and mass flow balances The work presented in the paper focuses on modeling Etype vertical spindle coal mills that are widely used in coal Development of a Multisegment Coal Mill Model Using an
.jpg)
Coal Preparation Systems for Boilers Springer
Coal Preparation Systems for Boilers Coal can be burned in a number of ways Depending on the characteristics of Raw coal bunker Cutoff Coal feeder Coal mill Mill ventilator FIGURE 41 Coal storage system binandfeeder system, direct fired system, and semidirect system2020年9月1日 For modelbased fault diagnosis method, it first needs to establish a mathematical model of the coal mill Odgaard et al [2] used a simplified energy balance equation to monitor and diagnose abnormal energy flow in the coal mill Andersen et al [3] designed a Kalman filter to estimate the moisture entering and leaving the coal mill, thereby identifying whether the Research on fault diagnosis of coal mill system based on the 2023年10月8日 The selection of coal crushing equipment mainly depends on the input size of raw coal, the moisture of the coal, and the production scale (output) of the plant Of course, the output size and the final use of coal also need to be considered, such as 025 mm for gas furnaces, 825 mm for steam locomotives, 625 mm for industrial furnaces, and 025 mm for 6 Types of Coal Crusher: Which Is Best for Crushing My Coal?Introduction This article concerns itself with vertical grinding mills used for coal pulverization only (coal pulverizers), although vertical grinding mills can and are used for other purposes The 3D model in the saVRee database represents a vertical grinding bowl millOther grinding mill types include the ball tube mill, hammer mill, ball and race mill, and , roll and ring millVertical Grinding Mill (Coal Pulverizer) Explained saVRee
.jpg)
Modeling and control of ball mill system considering coal moisture
2016年8月1日 The established coal mill model is based on the following assumptions: (1) the process of coal grinding is simplified by disregarding the separation of coal particles; (2) the grinding and delivery of pulverized coal are divided into two stages in the mill; and (3) pulverized coal sizes at the outlet is neglected in the model, and only raw coal and pulverized coal exist in in coal, as a tracer in a roller mill20 In that study, the WPs were selectively accumulated inside the roller mill and discharged with a particle size larger than that of the coal particlesMilling Characteristics of Coal and Torrefied Biomass Blends in a mill modelling technique for Etype coal mill and dynamic behaviour are developed using genetic algorithms [3] Genetic Algorithms (GAs) have been successfully applied to problems in business, engineering, and science Gas are stochastic, populationbased search and optimization algorithms inspired by the process of natural selection and Measurement and Control of Coal Pipe Temperature of Coal Mills The production of 200 mesh coal powder requires the selection of an appropriate vertical mill that meets the specific requirements of the application The choice of vertical mill should be based on factors such as material properties, production capacity, Choosing the right vertical mill for 200 mesh coal powder