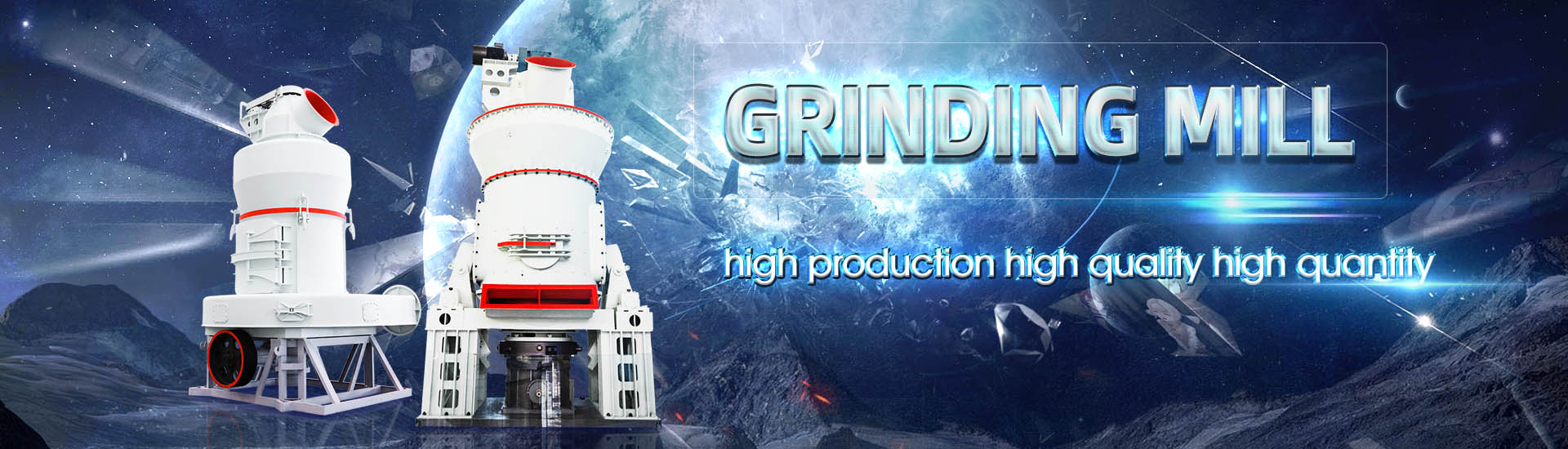
PF vertical grinding ore grinding mill design
.jpg)
(PDF) Operational parameters affecting the vertical roller mill
Grinding test results for zinc ore showed that it is possible to decrease the total grinding energy consumption from 2011 to 1140 kW h/t by using vertical roller mill instead of AG/SAGball mill Vertical stirred milling is a wellrecognized technology for the secondary, regrind and fine grinding applications and are increasingly replacing coarser ball mill applications in secondary and RECENT DEVELOPMENTS IN COARSE GRINDING USING VERTICAL 2015年3月15日 Two Swedish magnetite iron ores were comminuted with a pilot scale verticalrollermill In these experiments the mill parameters dam ring height, grinding pressure and Research of iron ore grinding in a verticalrollermill2017年4月1日 Vertical roller mills (VRM) have found applications mostly in cement grinding operations where they were used in raw meal and finish grinding stages and in power plants Operational parameters affecting the vertical roller mill
.jpg)
Latest Installations And Developments Of Loesche Vertical Roller
2012年9月1日 Mills (VRM) installations and summarises the main benefits of the dry compressive Loesche grinding technologies in Airflow and OverflowMode Some of these 2015年3月15日 The application of vertical roller mills (VRMs) for ore grinding is a part of the strategies against rising energy consumption (Reichert et al, 2015) Schematic operation Research of iron ore grinding in a verticalrollermill2015年3月15日 We investigated whether the vertical roller mill can be efficiently used in the beneficiation of lowgrade magnesite and whether it can improve upon the separation indices Research of iron ore grinding in a verticalrollermill2014年11月1日 In this study, a coarse sample of iron ore was tested in a pilot scale grinding circuit with a vertical mill Other three samples of pellet feed had already been tested with the methodologyVertical mill simulation applied to iron ores
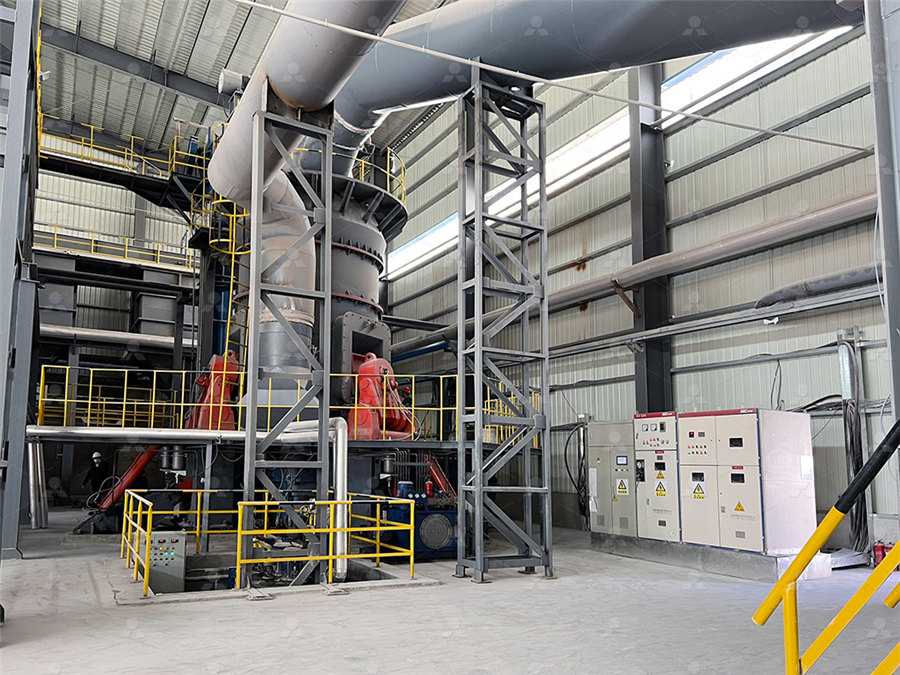
Predicting the effect of operating and design variables in grinding
2021年4月24日 Vertical stirred mills (VSM) are widely used for powder processing in many situations like mechanical alloying preparation and raw material crushing and shaping Many Overall, ball size and shape are important factors to consider when choosing a mill for ore grinding However, other factors such as mill design and the type of ore being processed also play a role in how well the ball milling process works Effect of media type on ore grinding performanceFactors affecting ores grinding performance in ball millsCompared with the ultrafine vertical grinding mill in the same industry, HCMilling(Guilin Hongcheng) HLMX nonmetallic ore ultrafine vertical grinding mill equipment has the following advantages: lower cutting point of the classifier; The median diameter is smaller; The content of fine powder is higher; Higher yield; Lower energy consumption; The floorstation structure is Application of HLMX Ultrafine Vertical Roller Mill for Nonmetallic Ore 2015年3月10日 DOI: 101016/JMINPRO201410002 Corpus ID: ; Copper ore grinding in a mobile vertical roller mill pilot plant @article{Altun2015CopperOG, title={Copper ore grinding in a mobile vertical roller mill pilot plant}, author={Deniz Altun and Carsten Gerold and Hakan Benzer and Okay Altun and Namık A Aydogan}, journal={International Journal of Copper ore grinding in a mobile vertical roller mill pilot plant
.jpg)
Research of iron ore grinding in a verticalrollermill
Request PDF On Mar 15, 2015, Mathis Reichert and others published Research of iron ore grinding in a verticalrollermill Find, read and cite all the research you need on ResearchGate2022年5月23日 Grinding experiments were conducted in a laboratoryscale stirred mill on a lowgrade PGE bearing chromite ore HighPressure Grinding Rolls (HPGR) product of −1 mm was used as feed material to Modeling and application of stirred mill for the coarse grinding 2014年1月1日 Vertical stirred mill is expected to upgrade the iron concentrate by further size reduced efficiently The tests for fine grinding of iron ores from Baiyun Boyu iron ore, Baogang Goup, iron Application of vertical stirred mill in iron ore fine grinding2015年7月16日 It can be concluded that the HPGRStirred mill combination was a more energyefficient grinding circuit than the HPGRBall mill combination for PGE bearing chromite ore View Show abstract(PDF) A Comparative study on a vertical stirred mill agitator design
.jpg)
Copper Ore Grinding in a Mobile Vertical Roller Mill Pilot Plant
2014年10月1日 In a test performed in the Loesche test center in Germany, copper slag grinding saved 229% energy in an airswept model and 344% energy in an overflow model [13,14]2015年3月10日 Within the scope of the study ore grinding performance of the vertical roller mill was investigated with mobile pilot plant In this context, chalcopyrite ore of a plant having rod and ball milling circuit was ground under different operating modes eg, air swept and overflow, and process conditions, then samples were collected around the systemCopper ore grinding in a mobile vertical roller mill pilot plant2017年2月20日 Grinding Mill Design Morgardshammar started to design and deliver grinding mills in the beginning of the century Today the mills are computer designed and manufactured in big plants with modern machinery In order to keep manufacturing costs at a minimum level, Morgardshammar has a series of standard mill diameters up to and including 65 mGrinding Mill Design Ball Mill Manufacturer 911Metallurgist2014年1月1日 Vertical Agitated Media Mill modeling has become subject of a research project due to its potential application as a secondary grinding mill as well as regrind and pellet feed preparation projectsPopulation balance model approach to ball mill
.jpg)
Vertical Stirred Mill Mineral Processing Equipment
Vertical stirred mills are a fine grinding equipment that covers advantages of low rotation speed, high reliability and long life cycle The significant advantages that the vertical stirred mills have over the ball mills are smaller size, less auxiliary 2019年8月1日 The flotation performance of the samples prepared either by dry grinding in Loesche vertical roller mill or by wet grinding in a rod mill are compared and the effects of dry and wet grinding are INVESTIGATION ON FLOTATION BEHAVIOR OF A COPPER SULFIDE ORE 2023年7月10日 The present literature review explores the energyefficient ultrafine grinding of particles using stirred mills The review provides an overview of the different techniques for size reduction and the impact of energy requirements on the choice of stirred mills It also discusses the factors, including the design, operating parameters, and feed material properties, EnergyEfficient Advanced Ultrafine Grinding of Particles UsingGrinding Mills: Ball Mill Rod Mill Design PartsCommon types of grinding mills include Ball Mills and Rod Mills This includes all rotating mills with heavy grinding media loads This article focuses on ball and rod mills excluding SAG and AG mills Although their concepts are very similar, they are not discussed herePhotographs of a glass ended laboratory ball mill show Grinding Mills 911Metallurgist
.jpg)
Cement Vertical Mill Vertical Grinding Mill Vertical Mill
What Is Cement Vertical Mill The cement vertical mill is a type of grinding equipment that merges fine crushing, drying, grinding, and powder separating into a single, which simplifies the production process and has many irreplaceable advantages, such as high grinding efficiency, large feeding size, low power consumption (2030% less power than a cement ball mill), large 2021年4月24日 The work uses the UFRJ mechanistic mill model and DEM to analyze the effect of several design and operating variables on the apparent breakage rates and breakage distribution function of a batch Predicting the effect of operating and design variables in grinding 2020年7月23日 (a) Isometric view of NETZSCH laboratory vertical stirred mill with disk type stirrer used in the fine grinding experiments (b) Top view of the CFD simulation snapshots at showing tangential Optimization of stirred mill parameters for fine grinding of PGE 2020年8月12日 Altun et al [15] explored the influence of the parameter settings of a vertical roller mill on grinding performance and demonstrated the influence of grinding pressure values on the size and mass An investigation of performance characteristics and energetic
.jpg)
Analysis and Optimization of Grinding Performance of
2022年1月23日 This work concentrates on the energy consumption and grinding energy efficiency of a laboratory vertical roller mill (VRM) under various operating parameters2015年3月15日 DOI: 101016/JMINENG201407021 Corpus ID: ; Research of iron ore grinding in a verticalrollermill @article{Reichert2015ResearchOI, title={Research of iron ore grinding in a verticalrollermill}, author={Mathis Reichert and Carsten Gerold and Andreas Fredriksson and G Adolfsson and Holger Lieberwirth}, journal={Minerals Engineering}, Research of iron ore grinding in a verticalrollermill2018年9月17日 The use of vertical stirred mills in the mining industry has increased remarkably over the past few decades, as a result of growing requirement for finer ore grindingDEVELOPMENT OF A LABORATORY TEST TO DESIGN 2017年9月11日 Due to the compact design and material transportation system of vertical roller mills (VRM), some important streams (total mill feed and discharge, dynamic separator feed and reject) remain in the (PDF) Performance Evaluation of Vertical Roller Mill in Cement Grinding
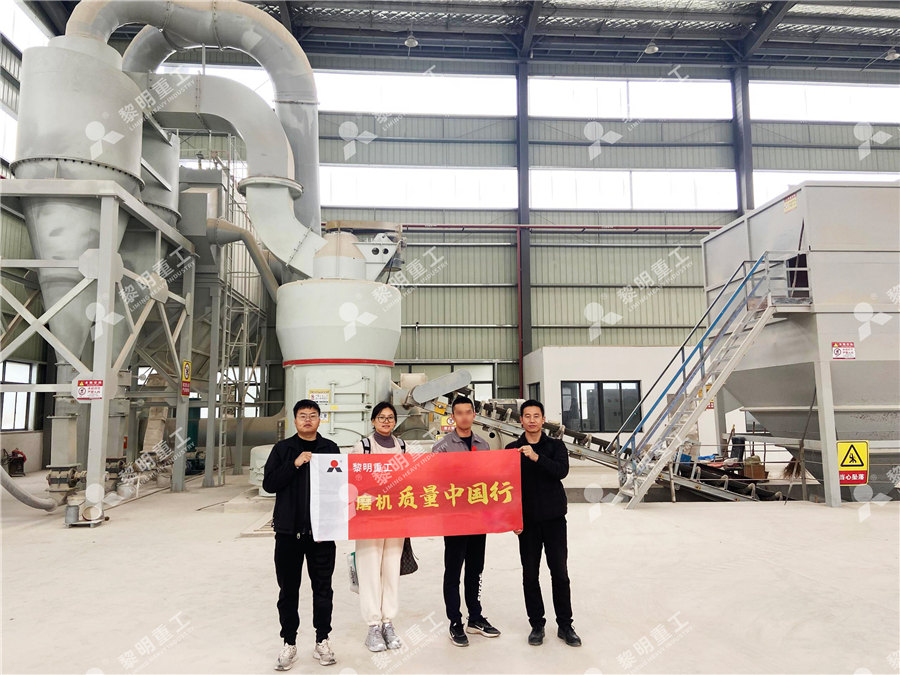
Vertical Roller Mills used for the comminution of mineral ores
Figure 1: Vertical roller mill operating principle (left: standard configuration, right: configuration with grit extraction) Pilot plant description and standard testing methods The grindability of a particular mill feed forms the basis for the design of an industrial grinding plantSBM ultrafine powder technology co,ltd Is China's excellent ore mill supplier Our main products include ultrafine vertical roller mill, ultrafine grinding mill, stone powder production equipment, Welcome to consult +17 [ protected] languageSBM Ultrafine Powder Technology Industrial Grinding Mill, 2021年7月1日 The work uses the UFRJ mechanistic mill model and DEM to analyze the effect of several design and operating variables on the apparent breakage rates and breakage distribution function of a batch gravityinduced stirred mill grinding copper oreIt shows that breakage rates increase significantly with stirrer speed; that increase in percent solids decreased breakage Predicting the effect of operating and design variables in grinding 1, Raymond Mill, HC series pendulum grinding mill: low investment costs, high capacity, low energy consumption, equipment stability, low noise; is the ideal equipment for wollastonite powder processing But the degree of largescale is relatively lower compared to vertical grinding mill 2, HLM vertical mill: largescale equipment, high capacity, to meet the largescale production Iron ore grinding mill Grinding plants for Iron Ore
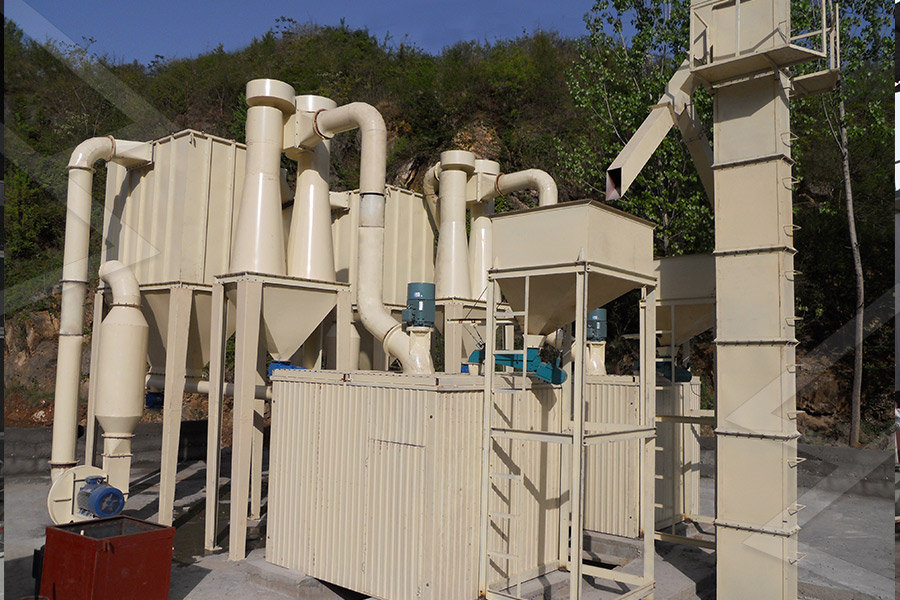
Analysis and Optimization of Grinding Performance of Vertical
2022年1月23日 This work concentrates on the energy consumption and grinding energy efficiency of a laboratory vertical roller mill (VRM) under various operating parameters For design of experiments (DOE), the response surface method (RSM) was employed with the VRM experiments to systematically investigate the influence of operating parameters on the energy VTM1500 vertical grinding mill Challenge Replacing the original tertiary ball mills with Metso’s Vertimill VTM1500 vertical grinding mill Solution Introduction of Metso’s Vertimill® VTM1500 vertical grinding mill at Miaogou Iron Mine to achieve Stirred mills MetsoFigure 3: Relationship between feed size (F80) and Bond efficiency factor (Huang et al, 2019) VERTICAL POWER MILL (VPM) – PRINCIPLE OF OPERATION Declining ore grades and more complex ore bodies, as well as waste management and global net zero initiatives, lead to a clear trend for high tonnage yet energy efficient grindingRECENT DEVELOPMENTS IN COARSE GRINDING USING VERTICAL 2018年8月8日 One of the most effective methods of grinding Portland cement is the use of an electromagnetic mill, which has proven its advantage in creating clinkerless binders [2], regulating the kinetics of (PDF) Grinding Kinetics Adjustment of Copper Ore
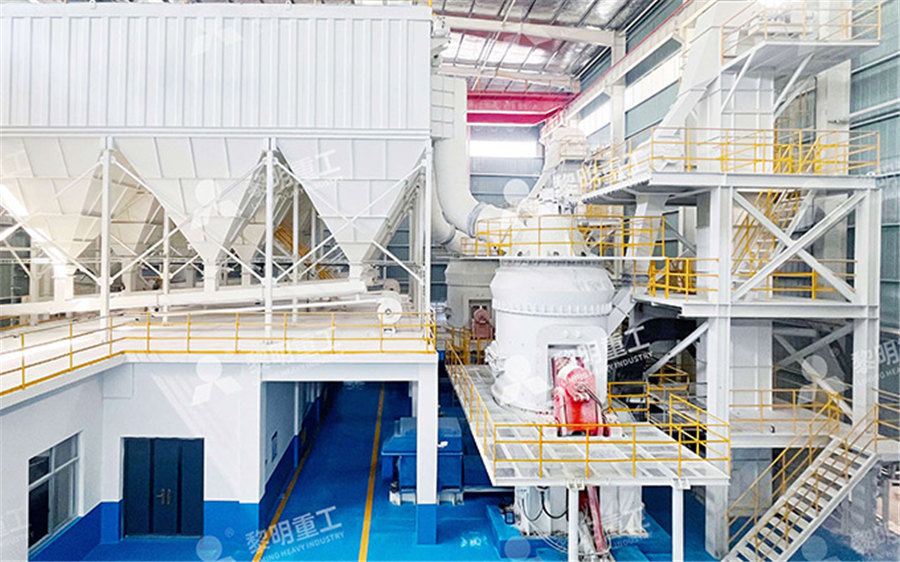
Ultrafine Grinding of Silver Plant Tailings of a Refractory Ore
2013年11月1日 Ultrafine grinding of the plant tailings of a refractory silver ore was studied using a laboratory type vertical stirred media mill Preliminary tests have confirmed that ultrafine grinding Grinding Mills Barry A Wills, James A Finch FRSC, FCIM, PEng, in Wills' Mineral Processing Technology (Eighth Edition), 2016 71 Introduction Grinding is the last stage in the comminution process where particles are reduced in size by a combination of impact and abrasion, either dry, or more commonly, in suspension in waterGrinding Mill an overview ScienceDirect Topics2015年7月16日 DOI: 101080/2015 Corpus ID: ; A Comparative Study on a Vertical Stirred Mill Agitator Design for Fine Grinding @article{Eswaraiah2015ACS, title={A Comparative Study on a Vertical Stirred Mill Agitator Design for Fine Grinding}, author={Chinna M Eswaraiah and N Venkat and Bijay K Mishra and Ralph Jerome Holmes}, A Comparative Study on a Vertical Stirred Mill Agitator Design 2023年12月4日 A vertical roller mill (VRM) is a grinding equipment used for the size reduction of minerals, and ceramics It is also used to grind slag and nonmetallic ores The VRM decreases the number of equipment in the grinding circuit by combining the drying, crushing, Grinding force is one of the critical design parameters of the VRMNumerical Investigation of Vertical Roller Mill Operation Using
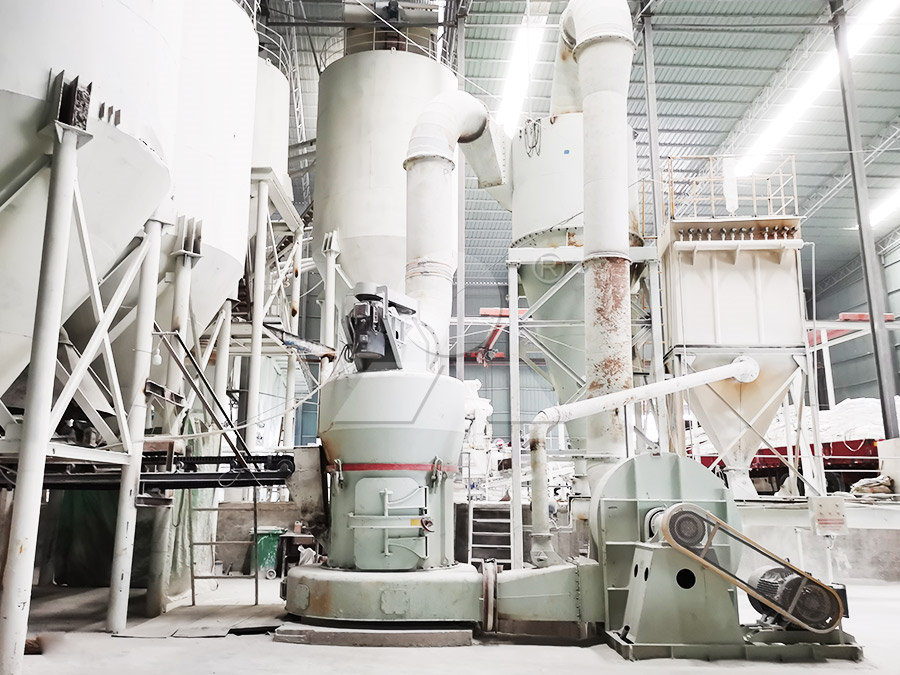
Mill (grinding) Wikipedia
A mill is a device, often a structure, machine or kitchen appliance, that breaks solid materials into smaller pieces by grinding, crushing, or cutting Such comminution is an important unit operation in many processesThere are many different types of mills and many types of materials processed in them Historically mills were powered by hand or by animals (eg, via a hand crank), 2013年11月1日 Ultra fine grinding of the plant tailings of a refractory silver ore was studied using a laboratory type vertical stirred media mill Preliminary tests confirmed that ultra fine grinding substantially improves the extraction of silver from the tailings in cyanide leaching (ie 36% Ag extraction rate from the asreceived tailings with d 80 of 100 μm, cf 84% extraction rate after Ultra fine grinding of silver plant tailings of refractory ore using 2023年7月10日 Metalliferous ore grinding is frequently the most energyintensive collection of activities and accounts for around a quarter of the 2% of the world’s energy that is used for mineral comminution [(PDF) EnergyEfficient Advanced Ultrafine Grinding of Particles 2022年1月23日 This work concentrates on the energy consumption and grinding energy efficiency of a laboratory vertical roller mill (VRM) under various operating parameters For design of experiments (DOE), the response surface method (RSM) was employed with the VRM experiments to systematically investigate the influence of operating parameters on the energy Analysis and Optimization of Grinding Performance of Vertical