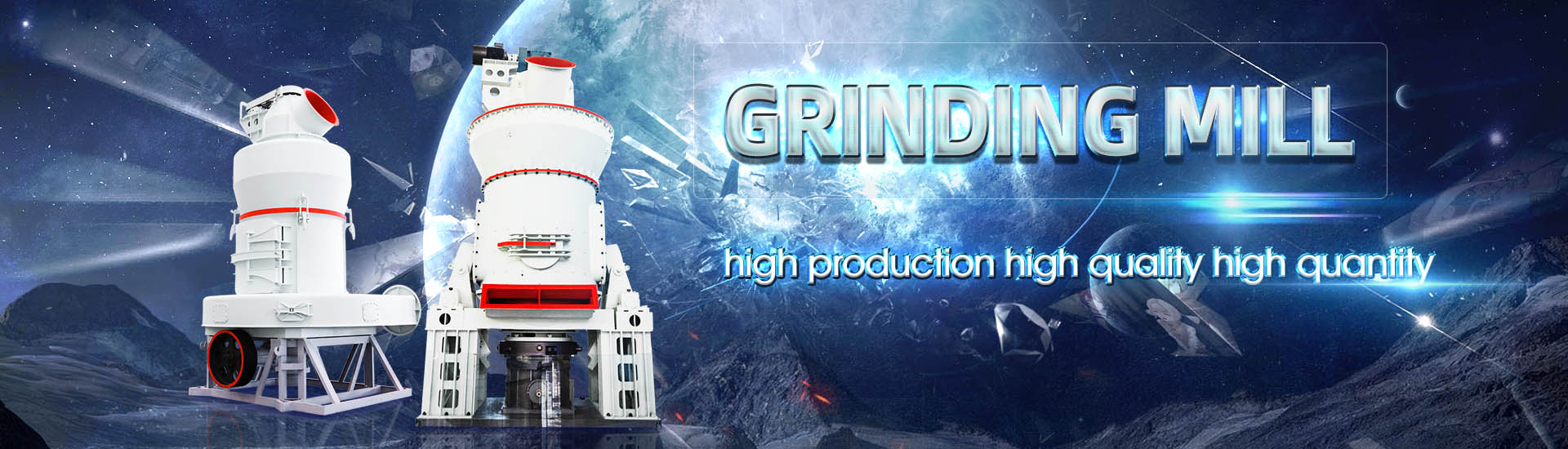
Energysaving and emission reduction measures for cement plants

Review on energy conservation and emission reduction
2022年12月1日 This review aims to help the cement industry to select the best method for improving energy efficiency and emission reduction Various energy conservation and 2020年3月1日 In the literature, technical characteristics like process specification, capacity enhancement, energy savings, CO2 emission reduction and quality enhancement have been A decision support tool for cement industry to select energy experience in the cement sector and focus on specific technical measures that could be implemented by cement plants to reduce their operating costs and improve their carbon IMPROVING THERMAL AND ELECTRIC ENERGY EFFICIENCY AT 2024年1月9日 The model considers energysaving and emission–reduction goals and incorporates five optimization scenarios: demand reduction, technological advancements, fuel Carbon emissions mitigation methods for cement industry
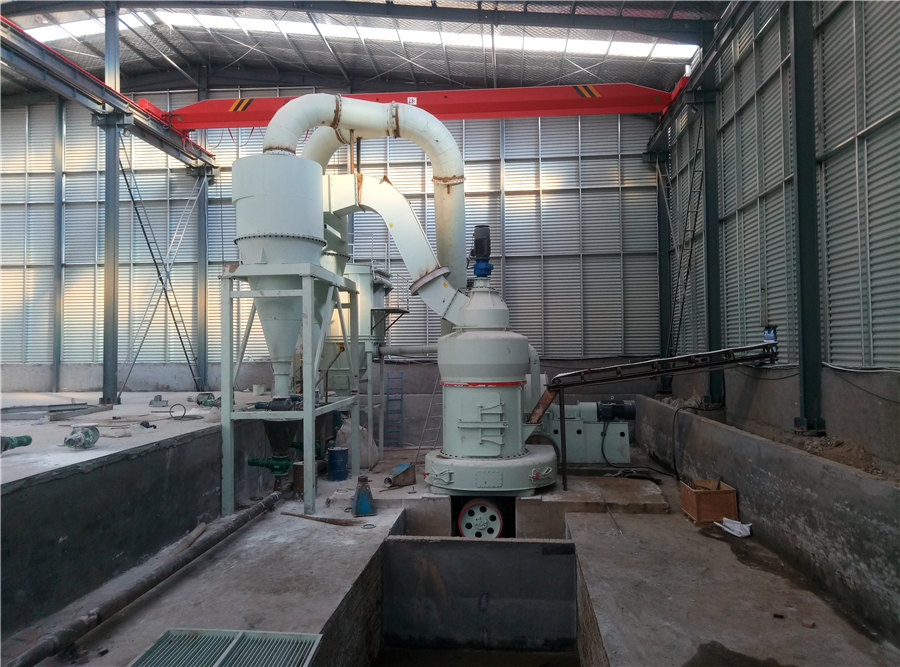
Energy and Emission Reduction Opportunities for the Cement
Concrete accounts for about 20% of the energy and 12% of the CO2 emissions associated with cement/concrete The cement/concrete industry operates at less than 40% thermal efficiency This report provides a summary of international best practice experience in the cement sector and focuses on specific technical measures that could be implemented by cement plants to reduce Improving thermal and electric energy efficiency at cement plants This document, prepared under the auspices of the SETPlan Information System (SETIS), aims to assess the current role of technological innovation in improving energy efficiency and ReqNo JRC59826 jrc2010energy efficiency and co2 emissions2024年2月2日 This study focuses on benchmarking the energy usage and carbon emissions of a UK cement plant to pinpoint opportunities for enhancing efficiency and reducing environmental Benchmarking of Energy Consumption and CO2 Emissions in
.jpg)
Impacts of energysaving and emissionreduction on sustainability
2024年3月1日 This study investigates effects of three representative energy saving and emission reduction measures (steam Rankine cycle power generation (SRC), organic Rankine technologies and measures and estimated energy savings, carbon dioxide emission savings, investment costs, and operation and maintenance costs for each of the measures The report describes the measures and experiences of cement plants around the world with these practices and technologiesEnergy Efficiency Improvement and Cost Saving Opportunities for Cement each technology or measure, costs and energy savings per tonne of cement produced are estimated and then carbon dioxide emissions reductions are calculated based on the fuels used at the process step to which the technology or measure is applied The analysis of cement kiln energyefficiency opportunities is divided into technologies and measuresEnergy Efficiency Improvement Opportunities for the Cement energy efficient technologies and measures and estimated energy savings, carbon dioxide savings, investment costs, and operation and maintenance costs for each of the measures The report describes the measures and experiences of cement plants around the wold with these practices and technologiesEnergy Efficiency Improvement and Cost Saving Opportunities for Cement
.jpg)
Potential energy savings and CO2 emissions reduction of China's cement
2012年6月1日 This study models output and efficiency improvements in Chinese cement industry from 2011–2030 Energy savings and CO 2 emission reductions estimated for 3 scenarios relative to frozen scenario Results reveal cumulative final energy savings potential of 271–375 EJ and 32–44 Gt CO 2 reductions Increasing efficiency is the most important 2024年5月1日 Waste heat recovery is the most studied of the technologies discussed in the literature The potential for electricity generation from an Indian cement plant is explored by Rajendran et al (2021), who found that significant power generation and emission reduction is possible from waste heat recoverySimilarly, Verma et al (2020) showed that a 9800 tpd Analysis of decarbonization measures for the Indian Cement Sector2022年8月27日 Besides CO 2 emission reduction due to energysaving or energy transformation measures, this work also takes CO 2 emission increase due to strengthening industrial emission standards into Cobenefits of CO2 emission reduction from China’s clean air 2024年7月11日 To bridge this knowledge gap, we present an annual intensity dataset of energy and CO2 emissions at plantlevel for Guizhou’s ordinary Portland cement industry, which involves the details of Plantlevel intensity of energy and CO2 emissions for Portland cement
.jpg)
Energy and Emission Reduction Opportunities for the Cement
for reducing energy usage and lowering emissions Immediate and nearterm improvements can be achieved by implementing demandside energy management measures to improve energy efficiency and reduce electricity and fuel use These improvements can come from utilizing free2021年12月15日 The cement industry is a key driver of urbanization and economic development as it supplies raw materials needed for infrastructure construction [1]Global cement output has increased significantly over the past years, with more than 200% increase between 2003 and 2015 [2]However, behind this tremendous output capacity, is a huge amount of energy Manyobjective optimization of energy conservation and emission 2011年5月1日 Energy saving measure Energy/Fuel saving Electric saving Cost Emission reduction (kgCO 2 /tonne) Payback period (years) Reference Remarks; Efficient Transport Systems for Raw Materials Preparation (Dry Process) 2 kWh/tonneInstallation cost US$ 3/tonne [70] 002 GJ/tonneRetrofit capital cost US$ 3/tonne: 053 [14] 34 kWh/tonneCapital cost US$ 3 A critical review on energy use and savings in the cement industrieseach technology or measure, costs and energy savings per tonne of cement produced are estimated and then carbon dioxide emissions reductions are calculated based on the fuels used at the process step to which the technology or measure is applied The analysis of cement kiln energyefficiency opportunities is divided into technologies and measuresEnergy Efficiency Improvement Opportunities for the Cement
.jpg)
Laying the foundation for zerocarbon cement
2020年5月14日 Cement acts as the binder between aggregates (fine and coarse rocks) in the formation of concrete While cement makes up only a small percentage of the mix (approximately 12 percent by volume), it is almost 2010年4月6日 The cement industry is one of the most energyconsuming industries in Thailand, with high associated carbon dioxide (CO2) emissions The cement sector accounted for about 206 million tonnes of CO2 emissions in 2005 The fuel intensity of the Thai cement industry was about 311 gigajoules (GJ)/tonne cement; the electricity intensity was about 943 kWh/tonne Technical and cost assessment of energy efficiency improvement 2024年2月1日 The International Energy Agency (IEA) estimated that the global CO 2 emissions from cement production will fall from 24 Gt in 2019 to 02 Gt in 2070 in the context of the sustainable development scenario (SDS) (IEA, 2020b), approximately 35% of CO 2 emissions will be reduced by cement avoided demand and 14% reductions from the clinkertocement ratio A review of lowcarbon technologies and projects for the global cement 2021年11月3日 Through routine energysaving monitoring, energy audit, energy efficiency benchmarking, internal audit, organizations’ energy consumption measurement, test and energy balance statistics, management review, selfevaluation, energysaving technical renovation, energysaving assessment, and other measures, we can improve the energy management Energy Conservation and Emission Reduction SpringerLink
.jpg)
Emission reduction through process integration and exploration
2023年1月7日 The cement industry is undeniably critical for the global economy However, they are also the largest energy consumers in the world The clinker manufacturing process causes gaseous emissions like nitrogen oxides, sulfur dioxide, carbon dioxide and particulate matter There is scope for various technologies to be used in the cement manufacturing process for vi Improving Thermal and Electric Energy Efficiency at Cement Plants: International Best Practice Cement is paramount for economic development and poverty reduction in emerging markets Along with aggregates and water, cement is the key ingredient in the production of concrete, and, as such, is an essential construction materialIMPROVING THERMAL AND ELECTRIC ENERGY EFFICIENCY AT CEMENT PLANTS 2013年6月1日 In this study, the energy conservation supply curves (ECSC) combined with the GAINS (Greenhouse Gas and Air Pollution Interactions and Synergies) was used to estimate the cobenefits of energy savings on CO 2 and air pollutants emission for implementing cocontrol options of energy efficiency measures and endofpipe options in the China’s cement industry Energy efficiency improvement and CO2 emission reduction energy efficient technologies and measures and estimated energy savings, carbon dioxide savings, investment costs, and operation and maintenance costs for each of the measures The report describes the measures and experiences of cement plants around the wold with these practices and technologiesEnergy Efficiency Improvement and Cost Saving Opportunities for Cement

Energy efficiency improvement and CO2 emission reduction
2013年6月1日 The fuel savings and CO 2 emission reduction achieved by each measure is also shown Increased production of blended cement (additives: fly ash, pozzolans, limestone or/and blast furnace slag) and kiln shell heat loss reduction (improved refractories) are the two most cost effective measures2024年10月1日 On the one hand, ECERFP commit to harmonizing energy conservation with economic growth, eliminate inefficient capacities through energysaving and emissionreduction measures, promote the adoption of advanced ecofriendly equipment and technologies, enhance the concentration of pivotal industries and the share of highend productivity, and further the Collaborative effect of the energy conservation and emission reduction Innovative emissions reduction strategies from the past few years include: Following the LEILAC2 (Low Emissions Intensity Lime and Cement) and Norcem Brevik CCS projects, Heidelberg Materials has announced plans to build a full Cement IEA International Energy AgencyThis study performs a benchmarking analysis of energy use and CO2 emissions for a UK cement plant as well as Best Available Techniques ( BAT) investigation to identify opportunities for performance improvement in crucial areas such as energy usage and environmental sustainabilityThe research utili ses industrial data from a 2850Benchmarking of Energy Consumption and CO2 Emissions in Cement
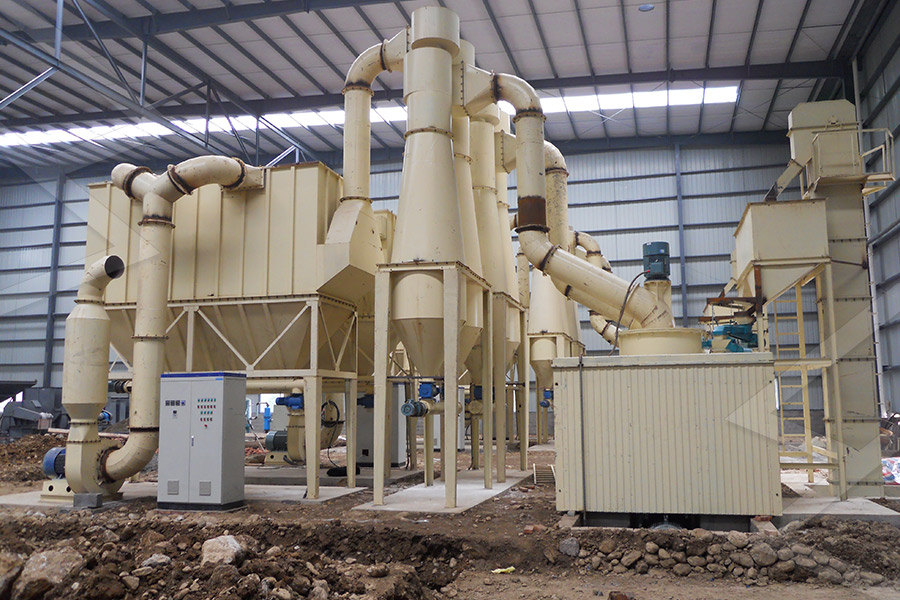
Bottomup analysis of energy efficiency improvement and CO2 emission
2021年5月10日 They also estimated the cumulative costeffective fuel savings at 1029 PJ with a corresponding decrease in CO 2 emission of 97 Mt Tesema and Worrell (2015) estimated that in the 8 cement plants operating in Ethiopia in 2010, the potential costeffective electricity savings could reach 11 GWh with fuel savings of 12 PJ, resulting in a 01 Mt reduction in CO 2 2010年8月1日 By converting the electricity saving potentials to primary energy using the conversion factors and taking into account the average efficiency of power generation and transmission, and distribution losses in China, Table 9 shows the total primary energy saving potentials as well as the total CO 2 emission reduction potential for the 16 studied cement Analysis of energyefficiency opportunities for the cement 2019年10月7日 In 2014 China proposed an ultralow emissions policy for coalfired power plants to reduce emissions Using comprehensive nationwide stack emissions monitoring data, Tang et al show reductions in Substantial emission reductions from Chinese power plants after 2023年9月13日 Urban green technology innovation (UGTI) is strongly tied to environmental regulations, which can successfully balance economic and environmental benefits Selecting the panel data for 280 Chinese The impact of China’s energy saving and emission reduction
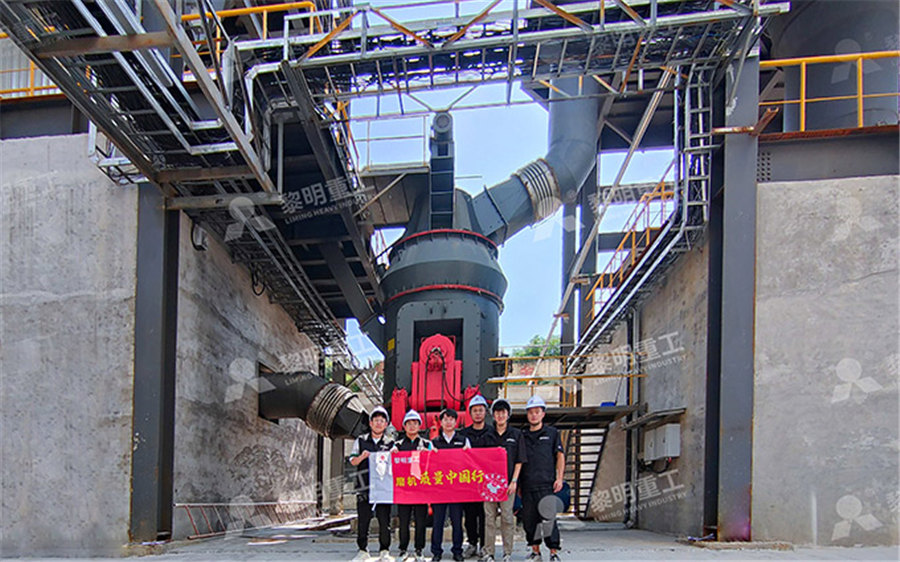
Bottomup analysis of energy efficiency improvement and CO2 emission
2021年5月10日 They also estimated the cumulative costeffective fuel savings at 1029 PJ with a corresponding decrease in CO 2 emission of 97 Mt Tesema and Worrell (2015) estimated that in the 8 cement plants operating in Ethiopia in 2010, the potential costeffective electricity savings could reach 11 GWh with fuel savings of 12 PJ, resulting in a 01 Mt reduction in CO 2 2015年12月15日 For the 8 operating plants in 2010, the costeffective energy savings equal 11 GWh electricity and 12 PJ fuel, resulting in 01 Mt CO 2 emissions reduction For the 20 cement plants expected to be in operation by 2020, the costeffective energy saving potentials is 159 GWh for electricity and 72 PJ for fuel, reducing CO 2 emissions by about 0 Energy efficiency improvement potentials for the cement 2 emission reduction opportunities in the US cement industry A guidebook on energyefficiency improvement technologies and measures commercially available for the cement industry includes the energy savings and CO 2 emission reduction potential, cost, brief explanations, and case studies of actual implementation for each technology (Worrell Technical and cost assessment of energy efficiency improvement 2016年11月8日 In the cement industry, from 1970 to 1999, carbon dioxide intensity due to fuel consumption and raw material calcination dropped 16 percent Despite the historic progress, there is considerable potential for energy efficiency improvement, when compared to other industrialized countries This guide examines more than 40 energy efficient technologies and Energy Efficiency Improvement and Cost Saving Opportunities for Cement
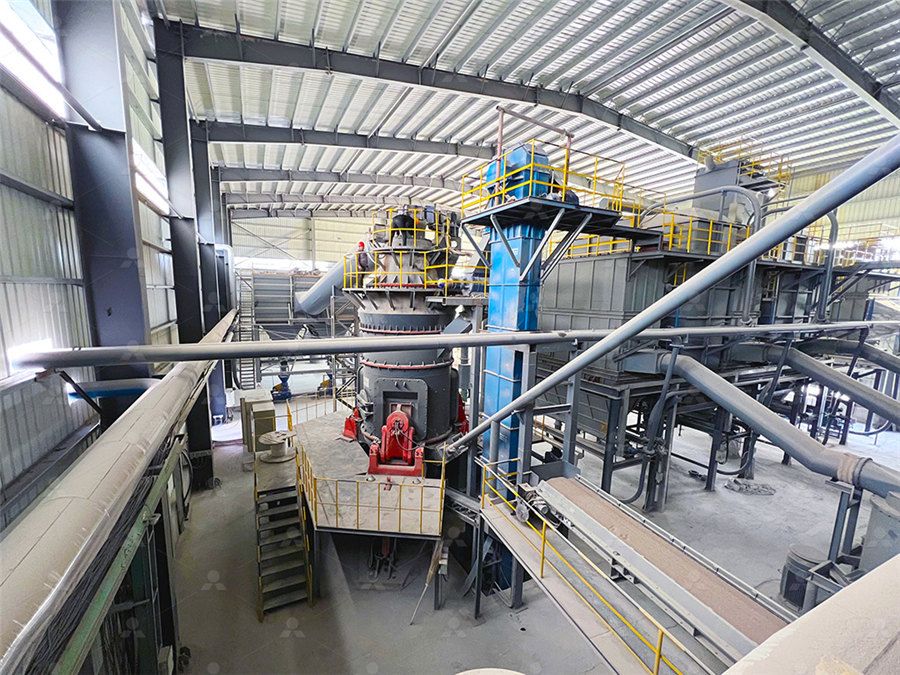
Historical trend and decarbonization pathway of China's cement
2023年9月15日 Cement manufacturing is one of the most energy and carbonintensive industries worldwide, accounting for 7 % of the global industrial energy use and 27 % of the global industrial carbon emissions (WBCSD and IEA, 2018)Cement, as a cementitious material of concrete, has been widely used in construction, transportation, water conservancy, and other 2012年10月1日 Globally, the cement industry accounts for approximately 5 percent of current anthropogenic carbon dioxide (CO 2) emissionsWorld cement demand and production are increasing significantly, leading to an increase in this industry’s absolute energy use and CO 2 emissions Development of new energyefficiency and CO 2 emissionreduction technologies Emerging energyefficiency and CO2 emissionreduction 2 天之前 Global emissions inventories and pathways, such as the community emissions data system (CEDS) (Hoesly et al, 2018) and CMIP6 Emissions (Gidden et al, 2019), oversimplify cementrelated emissions and fall short of capturing the spatial heterogeneity, by lacking sectoral reports and actual geographic locations of cement plants (Chen et al, 2022)Historical air pollutant emissions and future sustainable pathways Energy conservation at EREL Cement Plant in Mongolia will be achieved by introducing dry process production system and other energy saving countermeasures With the energy conservation, considerable amount of GHG emission can be reduced GHG emission reduction is estimated 156,939tCO2/year under the production volume ofEnergy Conservation in Cement Plant
.jpg)
Perform, Achieve and Trade (PAT) Bureau of Energy Efficiency
Perform, Achieve and Trade (PAT) Objective Perform, Achieve and Trade (PAT) is a regulatory instrument to reduce Specific Energy Consumption in energy intensive industries, with an associated market based mechanism to enhance the cost effectiveness through certification of excess energy saving which can be traded2022年7月1日 Due to this, cement plants located in regions without economic incentives have resorted to improving energy efficiency measures with conventional fuels These include upgrading kiln technologies [ 17 , 22 ], deploying multichannel burners [ 17 ], upgrading clinker coolers [ 11 , 17 ], increasing burnability of raw materials [ 17 ] and operating in oxygen Sustainable transition towards biomassbased cement industry: A 2023年11月23日 This paper develops a processlevel carbon emission calculation model for iron and steel enterprises through the carbon emission mechanism of the whole production process The relationship between material, energy and carbon flows is considered and combined The carbon emissions of enterprises are divided into industrial emissions and combustion CO2 emission accounting and emission reduction analysis of the 2017年1月20日 Regarding the energy saving and emission reduction effect of a single measure, improving energy efficiency (AT scenario) contributes the most energy saving (9 Mtce) and has a 304% emission reduction rate in 2050 Using calcium carbide as alternative raw materials has the lowest average abatement cost being 6303 CNY/tCO 2 in 2050Bottomup analysis of energy efficiency improvement and CO2 emission
.jpg)
China Emissions Reduction Energy Conservation Targets for
2024年6月17日 This is the first time China has provided specific energysaving and emissionsreduction goals for industries Reduce the comprehensive energy consumption per unit of cement clinker product by 37% compared with 2020 Regular internal audits of energy use and conservation measures will help prepare for official inspections