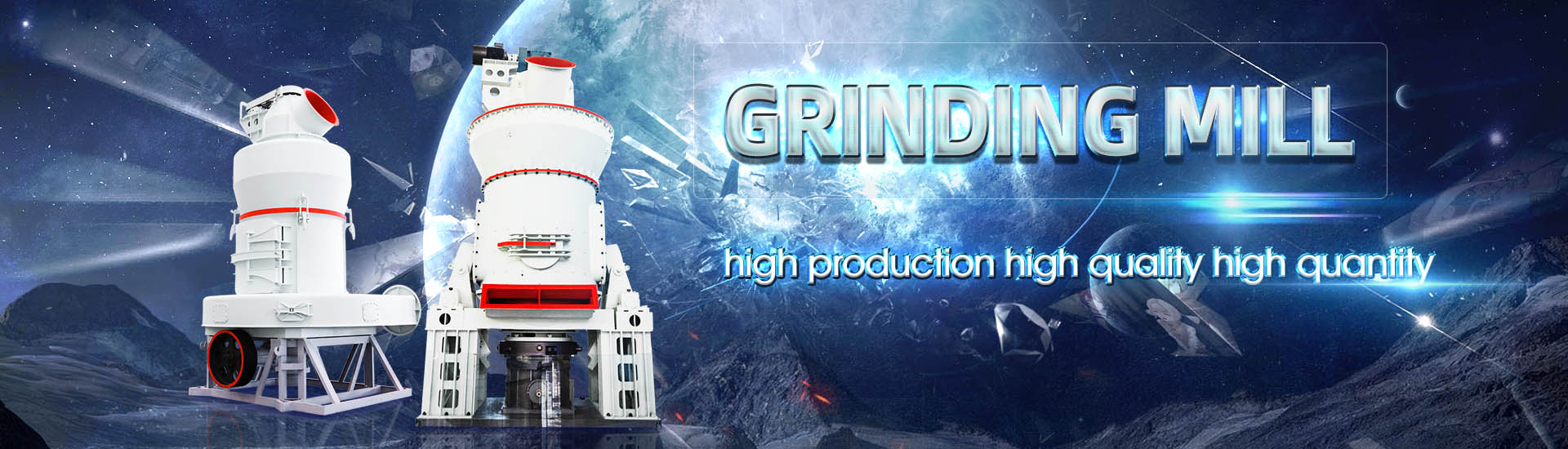
1 2 4 5. The weight of the ball mill
.jpg)
ball mill calculations, grinding media filling degree, ball size, mill
online live calculators for grinding calculations, Ball mill, tube mill, critical speed, Degree of filling balls, Arm of gravity, mill net and gross power Optimization; Online Training; Process and Ball mills are rated by power rather than capacity Today, the largest ball mill in operation is 853 m diameter and 1341 m long with a corresponding motor power of 22 MW (Toromocho, Ball Mill an overview ScienceDirect TopicsThe maximum rate of wear of steel balls, using very abrasive materials, is about 03 kg/Mg of material for dry grinding, and 1–15 kg/Mg for wet grinding The normal charge of balls is about Ball Mill an overview ScienceDirect Topics2015年6月19日 Use this online calculators for Motor Sizing and Mill sizing as well as mill capacity determinators In extracting from Nordberg Process Machinery Reference Manual I will also provide 2 Ball Mill Sizing (Design) Ball Mill Design/Power Calculation 911Metallurgist
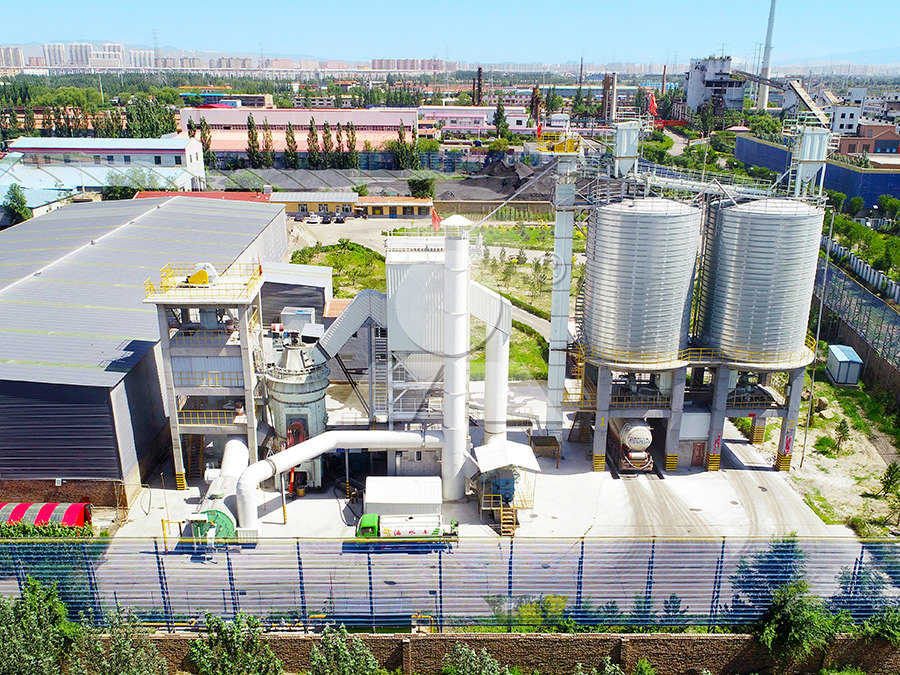
MODULE #5: FUNCTIONAL PERFOMANCE OF BALL MILLING
In this module, you will learn how to characterize the performance of ball mill circuits Specifically, after completing this module, you will be able to: List and describe the four elements of the Autogenous mills range up to 12 meters in diameter The lengthtodiameter ratios in the previous table are for normal applications For primary grinding, the ratio could vary between 1:1and 18:1 For fine regrinding in open circuit, the AMIT 135: Lesson 7 Ball Mills Circuits – Mining Mill 2021年1月1日 In this paper, the milling parameters of high energy ball mill (Fritsch Pulverisette 7) like vial geometry, number and size of balls and speed of the mill were modelled and discussedModelling of the HighEnergy Ball Milling Process2008年7月1日 In this paper, ball milling parameters: weight ratio of ball to powder, size of milling balls, type of medium, volume of milling medium and rotation speed in the planetary ball (PDF) Parameters optimization in the planetary ball milling of
.jpg)
Holdup weight in continuous wet ball milling: Relationship with
2023年2月1日 In the continuous mode of wet grinding operation, the amount of the particulate material present in the mill, commonly known as the holdup weight, varies with the mill 2023年4月30日 According to the ratio of cylinder length (L) to diameter (D), the ball mill can be divided into short cylinder ball mill, L/D ≤ 1; long barrel ball mill, L/D ≥ 1–15 or even 2–3; and Ball Mill SpringerLink2015年6月6日 Adjust the final weight up or down by substituting one Ball of one size with a new Ball of the same size, maintaining an exact count of 285 steel Balls 25 balls of 11/2″ 39 balls of 11/4″ 60 balls of 1″ 68 balls of 7/8″ 93 balls Bond Work Index Procedure and Method2017年2月13日 where an approximate figure for the constant is 35 for rod mills, 40 for overflow ball or pebble mills and 45 for grate discharge ball or pebble mills ç is specific gravity of grinding media (for rods or balls normally 785) q Ball Mills 911Metallurgist
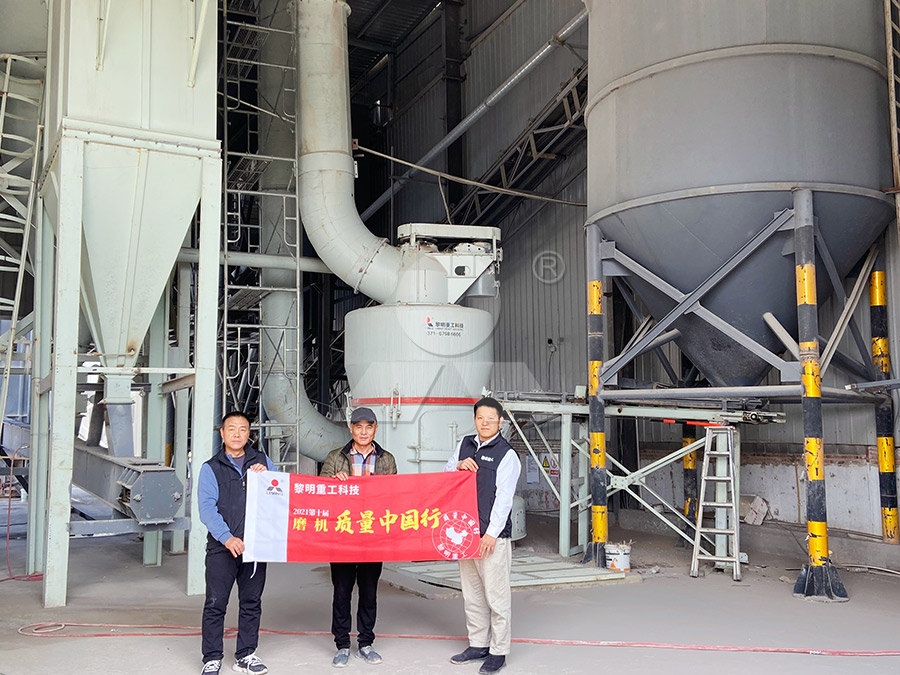
Ball mill PPT Free Download SlideShare
2015年4月24日 2 Ball mill consist of a hollow cylindrical shell rotating about its axis Axis of the shell horizontal or at small angle to the horizontal It is partially filled with balls made up of Steel,Stainless steel or rubber Inner surface of the 2016年1月1日 The wear of balls used during a grinding process is considered one of the losses that cause an increase in the operating cost allocated to the ball mill [21]A comparison of wear rates of ball mill grinding mediaWeight (exclude Jars, lbs) Dimension (in*in*in) XQM2L: 075: 4*(005~05L) 50~250mL vacuum jars : 70~670: 60: 9999: 205: 30*185*222: XQM4L: 075: Included in the package are a planetary ball mill, 4 pieces of jar clamper, 1 stainless steel sieve, 4 pieces of rubber jar cushion, a US standard power cord, Square Planetary Ball Mill (2L, 4L, 6L, 8L, 10L, 12L, 20L, 40L, 60L 2021年1月1日 The refractive index increased from 157 au to 265 au as the photon energy increased from about 138eV to 114eV The transmittance at the nearinfrared region was even up to 909% in some casesModelling of the HighEnergy Ball Milling Process
.jpg)
The formula for calculating the weight of grinding mill steel balls
2023年7月24日 Regarding the calculation of the weight of grinding mill steel balls, there are two different calculations due to the difference in steel ball density: Therefore, the weight of the steel ball G = 4/3π(L/2) × (L/2) × (L/2) × density = 4/3 2017年3月14日 The act introduces the average value of bulk weight by 3 weighing results The obtained result of bulk weight determination can be used in operational accounting, control of grinding process In our next articles we will consider the methodology for determining the bulk weight of grinding media in a working ball millTHE BULK WEIGHT OF GRINDING BALLS2017年1月1日 An increase of over 10% in mill throughput was achieved by removing the ball scats from a single stage SAG mill These scats are non spherical ball fragments resulting from uneven wear of balls (PDF) Performance optimization of an industrial ball mill for Total weight of ball = number of ball X weight of single ball Weight of single ball will depends the optimal mass ratio of ball to powder in ball mill is 75*24/(25*176)= 409 to 7 Best way to determine the balltopowder ratio in ballmilling?
.jpg)
Ball Mill (Ball Mills Explained) saVRee saVRee
If a ball mill uses water during grinding, it is a ‘wet’ mill A typical ball mill will have a drum length that is 1 or 15 times the drum diameter Ball mills with a drum length to diameter ratio greater than 15 are referred to as tube mills Ball mills The ball mill is a tumbling mill that uses steel balls as the grinding media The length of the cylindrical shell is usually 1–15 times the shell diameter (Figure 811)The feed can be dry, with less than 3% moisture to minimize ball coating, or slurry containing 20–40% water by weightBall Mill an overview ScienceDirect Topics2023年5月12日 In position a (Fig 1a) the length l 1 of the lower part of the chamber 1 is minimal, the grinding bodies 2 in it are located at the maximum level h 1Center of masses (CM 1) of grinding bodies (GB) in chamber 1 is located at the minimum distance a 1 from the filling bottom and at the distance b 1 from the crushing cylinder body The length l 2 of the lower part of the Power Calculation of BallTube Mill Drives in the Construction (2) The ball impact energy on grain is proportional to the ball diameter to the third power: 3 E K 1 d b (3) The coefficient of proportionality K 1 directly depends on the mill diameter, ball mill loading, milling rate and the type of grinding (wet/dry) None of the characteristics of the material being ground have any influence on K 1THE OPTIMAL BALL DIAMETER IN A MILL 911 Metallurgist
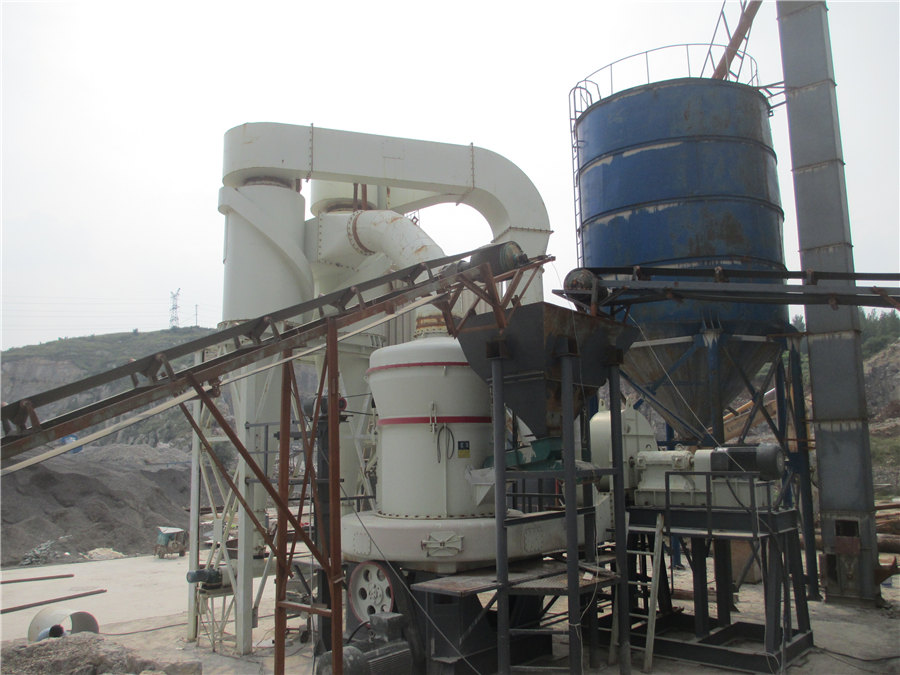
Method of Steel Grinding Ball Proportioning and Example
2023年2月15日 A beneficiation plant in Singapore loads balls into a ϕ 1500mm×3000mm wet grid type ball mill, determines the filling rate ϕ = 50%, and selects cast steel grinding balls δ = 45 t/m 3 The ball mill processes the mediumhard ore 1 See Table 1 for the sieving analysis results of all the ore samples from a ball mill Table 11 Cylinder: The cylinder is the main part of the ball mill It is a circular device made of welded steel plates of a certain thickness When working, it not only bears the static load of its own grinding medium, but also is affected by the alternating stress generated by the grinding medium impacting the rotation of the cylinderBall Mill SBM Ultrafine Powder TechnologyWeight 600 kg The MILL50 Ball Mill Refiner is used to produce/refine nut paste (hazelnut, almond, pistachio, macadamia nut, etc) extensive range of Bead Mill ( 14150 litres ), which is fabricated using high grade raw material to ensure optimum quality in the end productBall mill, Ball grinding mill All industrial manufacturersa ball mill circuit 4 Figure 2 The "effective mill power draw" 6 Figure 3 The ball mill "specific grinding rate" 8 Figure 4 The output of a ball mill circuit 9 Figure 5 The development of the functional performance equation 38 Table 1 Estimates of the MODULE #5: FUNCTIONAL PERFOMANCE OF BALL MILLING
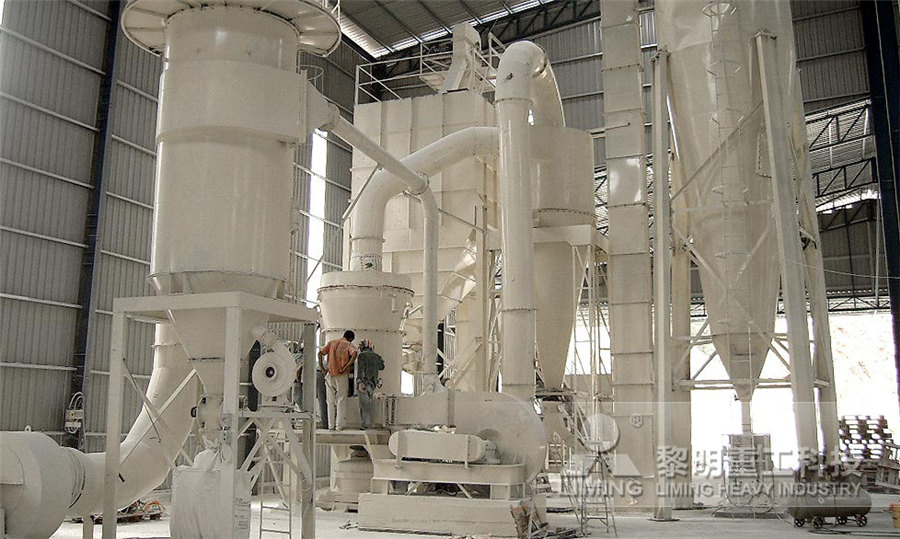
Effect of ball and feed particle size distribution on the milling
2018年2月1日 It was found that the ball mill consumed 5467 kWh/t energy to reduce the F 80 feed size of 7222 lm to P 80 product size of 2754 lm while stirred mill consumed 3245 kWh/t of energy to produce 2019年10月19日 Ball mills are extensively used in the size reduction process of different ores and minerals The fill level inside a ball mill is a crucial parameter which needs to be monitored regularly for optimal operation of the ball mill In this paper, a vibration monitoringbased method is proposed and tested for estimating the fill level inside a laboratoryscale ball mill A vibration Monitoring the fill level of a ball mill using vibration sensing and M Mhadhbi DOI: 104236/ampc2021 33 Advances in Materials Physics and Chemistry Figure 1 Photograph of the highenergy planetary ball millModelling of the HighEnergy Ball Milling Process ResearchGateModeling And Simulation Of A Closed Loop Ball Mill Grinding Circuit Proceedings of IRF International Conference, Chennai, India, 20th April 2014, ISBN: 978938 11 rate between 80 and 150 The input weights were set to 15 and 5 , output weights were set to 2 and 3 The weights restricts the deviation of the input and outputMODELING AND SIMULATION OF A CLOSED LOOP BALL MILL
.jpg)
[PDF] Study on the Performance of Ball Mill with Liner Structure
2018年6月29日 DOI: 105614/jengtechnolsci20185022 Corpus ID: ; Study on the Performance of Ball Mill with Liner Structure based on DEM @article{Li2018StudyOT, title={Study on the Performance of Ball Mill with Liner Structure based on DEM}, author={Zhanfu Li and Yao Kun Wang and Li Kunyuan and Wenyu Lin and Xin Tong}, journal={Journal of Engineering and The grinding jars are arranged eccentrically on the sun wheel of the planetary ball mill The direction of movement of the sun wheel is opposite to that of the grinding jars in the ratio 1:2 (or 1:25 or 1:3) The grinding balls in the grinding jars are subjected to superimposed rotational movements, the socalled Coriolis forcesPlanetary Ball Mill PM 400 RETSCH powerful and quick grinding14 Technical data 142 Weight PBM1 PLANETARY BALL MILL MANUAL 144 Power consumption The maximum power consumption is approx : • 175KW 145 Electrical fuses Automatic circuit breaker at the rear of the machine: 10 A 146 Material • Maximum feed size in the case of hard material approx 10 mmPBM 1 PLANETARY BALL MILL USER MANUAL2016年2月14日 Do you need a quick estimation of a ball mill's capacity or a simple method to estimate how much can a ball mill of a given size (diameter/lenght) grind for 911 Metallurgist is a trusted resource for practical insights, solutions, and support in mineral processing engineering, helping industry professionals succeed with proven expertise Small Ball Mill Capacity Small Ball Mill Capacity Sizing Table 911Metallurgist
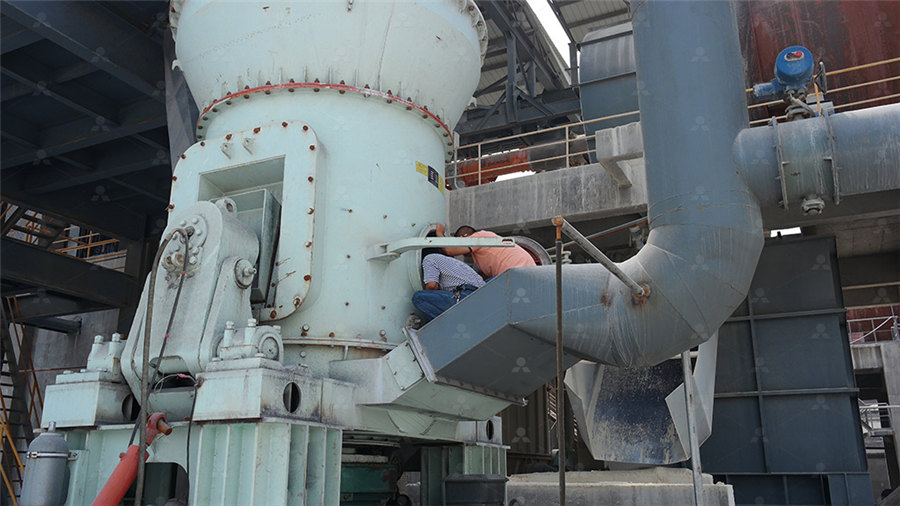
Planetary Ball Mill Process in Aspect of Milling Energy
PDF On Apr 28, 2014, Huynh Xuan Kho and others published Planetary Ball Mill Process in Aspect of Milling Energy Find, read and cite all the research you need on ResearchGateprocess Together with ball charge composition, both tools – liners and media – can be optimally adjusted for the application They can then fulfil the Figure 2: ball mill tools and comminution process Figure 1: ball mill communition process chain Ball charge management grinding Ventilation and cooling Operation and controlBALL MILLS Ball mill optimisation Holzinger Consulting2009年1月1日 A Bond Ball Mill Work Index test is a standard test for determining the ball mill work index of a sample of ore It was developed by Fred Bond in 1952 and modified in 1961 (JKMRC CO, 2006)This index is widely used in the mineral industry for comparing the resistance of different materials to ball milling, for estimating the energy required for grinding, and for ball Procedure for determination of ball Bond work index in the 2017年7月1日 51The effect of mill filling and ball size distribution on the mill power draw The weight percentage of each size (WPES) should be mentionedThe effect of ball size distribution on power draw, charge motion
.jpg)
AMIT 135: Lesson 7 Ball Mills Circuits – Mining
Autogenous Mill; Length: Diameter Ratio: 14 to 18: 05 to 35: 025 to 050: Feed Size: 25 cm maximum19 cm125 to 09cm: Coarse Ore Normal Ore: Reduction Ratio: 15:1 to 20:1: 20:1 to 200:1 Ball Mill Design A survey of Australian 2013年8月3日 In Grinding, selecting (calculate) the correct or optimum ball size that allows for the best and optimum/ideal or target grind size to be achieved by your ball mill is an important thing for a Mineral Processing Engineer AKA Calculate and Select Ball Mill Ball Size for Optimum 2013年12月28日 To grind the given material to a smaller size using a ball mill 2 To obtain the size distribution of the initial and the final mixture by sieving 3 Based on the results we obtained, set 1 (10 min, speed 5), the amount of Lab Report 1 and 2: PRACTICAL 1 : BALL MILLING2013年12月23日 Practical 1: Title: Ball Milling Objective: To grind the coarse salt to a smaller size by using a ball mill and to obtain the particle size distribution of the initial and the sieved final mixture Introduction: 'Ball milling is a method used to break down the solids to smaller sizes or into a powder APractical 1 : Ball Milling TF Lab 1
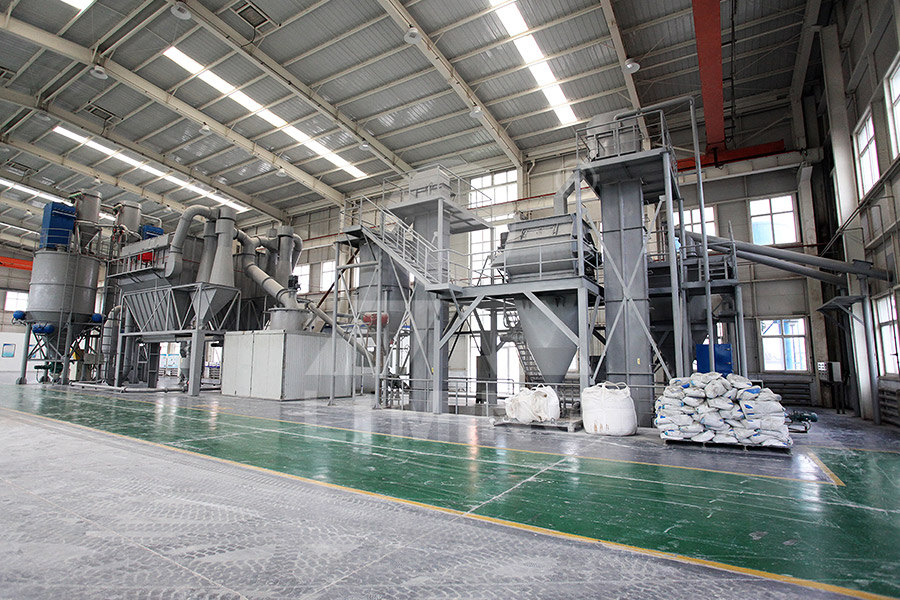
Kinetic grinding test approach to estimate the ball mill work
2015年7月31日 The Bond work index (BWI) is a wellknown method used when selecting comminution equipment, to evaluate the grinding efficiency and to calculate the required grinding power2018年5月1日 length of the ball mill [12] In the simulation, the axial length of the ball mill is taken as 500mm, the diameter of the grain ore is taken as φ10mm, and the effective volume is taken as 539 Study on the influence of liner parameters on the power of ball mill 2023年4月30日 Peripheral discharge ball mill, and the products are discharged through the discharge port around the cylinder According to the ratio of cylinder length (L) to diameter (D), the ball mill can be divided into short cylinder ball mill, L/D ≤ 1; long barrel ball mill, L/D ≥ 1–15 or even 2–3; and tube mill, L/D ≥ 3–5Ball Mill SpringerLink2021年2月19日 The optimum process parameters setting concluded that balls to powder weight ratio are 20:1, the optimum ball mill working capacity is 2 L while the optimum speed of the ball mill is 105 rpm Using SEM characterization, the improved particles of silica sand presented a spherical shape with a parative Study on Improving the Ball Mill Process Parameters
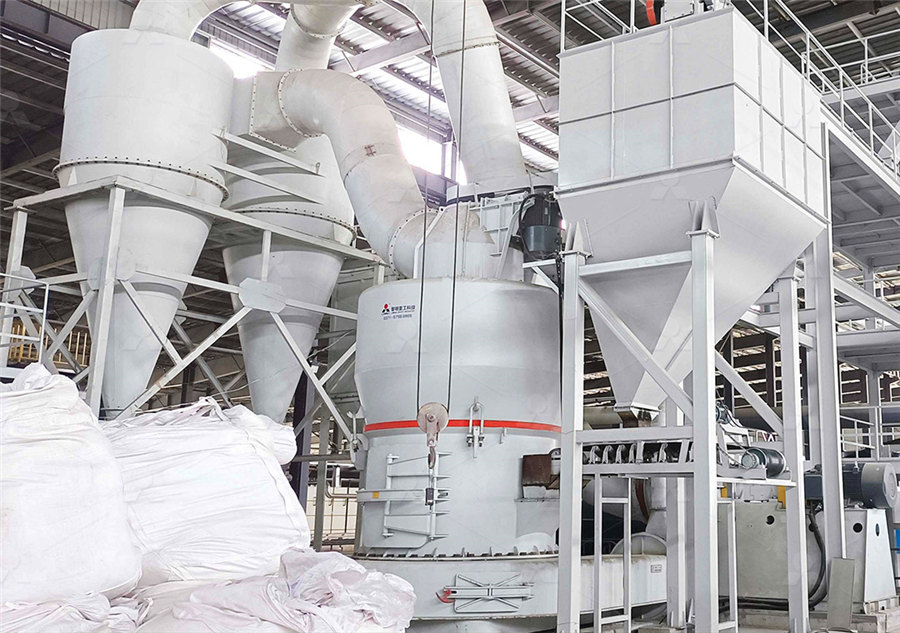
(PDF) Design of Threechamber Ball Mill ResearchGate
2021年1月1日 35 × 13m threechamber ball mill pitch diameter of the mill taken 4 times 𝑙 4D 14 m ( 2 ) The turning of the ball mill refers to the turning of the barrel of the ball mill when it 2014年3月1日 is net mill power input and H is the weight of particulate contents of the mill the test ball mill for a period of 12 min Pregrinding of the crushed material ensures that the (PDF) Analysis of ball mill grinding operation using mill power