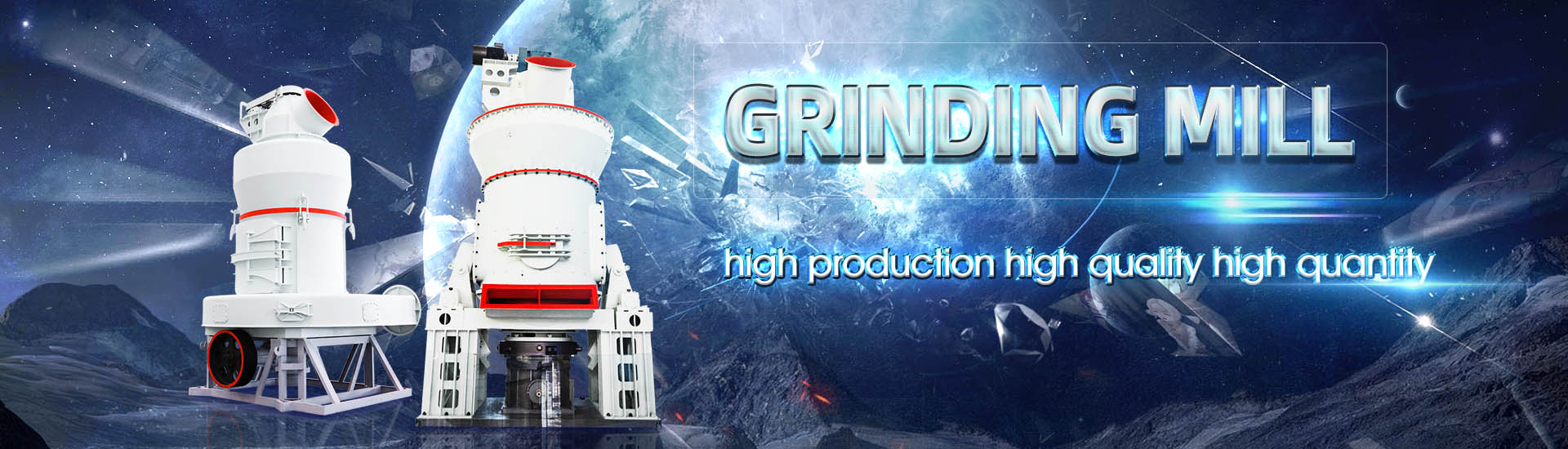
Fluorite reduces slag melting Mechanism of points
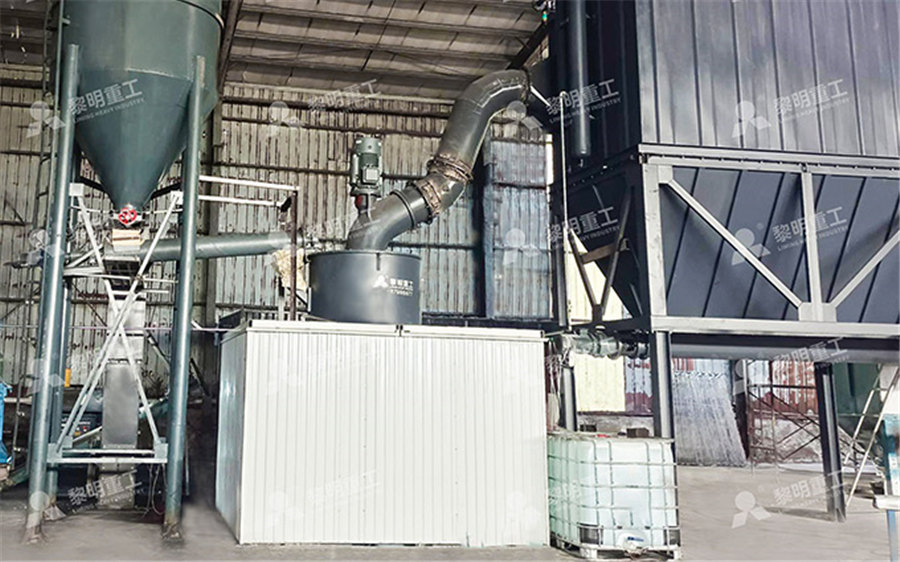
Effect of CaF2 and CaO/Al2O3 ratio on evaporation
2023年1月1日 The present study focuses on the evaporation of fluoride from lowfluoride CaF 2 –CaO–Al 2 O 3 –MgO–TiO 2 slag with varying CaF 2 content and CaO/Al 2 O 3 mass ratio and the melting characteristics of the slag2020年6月7日 The results show that the slag melting point decreases with an increase in the TiO2 content In addition, X‐ray diffraction analysis reveal that with an increase in the TiO2 Fluoride Evaporation and Melting Characteristics of 2021年7月28日 Since B 2 O 3 is a typical acid oxide with a low melting point (~ 450 °C) , the presence of B 2 O 3 is conducive to the fusing of CaO, Al 2 O 3, and other highmeltingpoint Effect of B2O3 on the Melting Temperature and Viscosity of The “hemisphere method” was used to detect the melting point, and the results showed that the measurements for the fluorinefree slag increased with increasing heating rate, and the Effect of the heating rate and premelting process on the melting
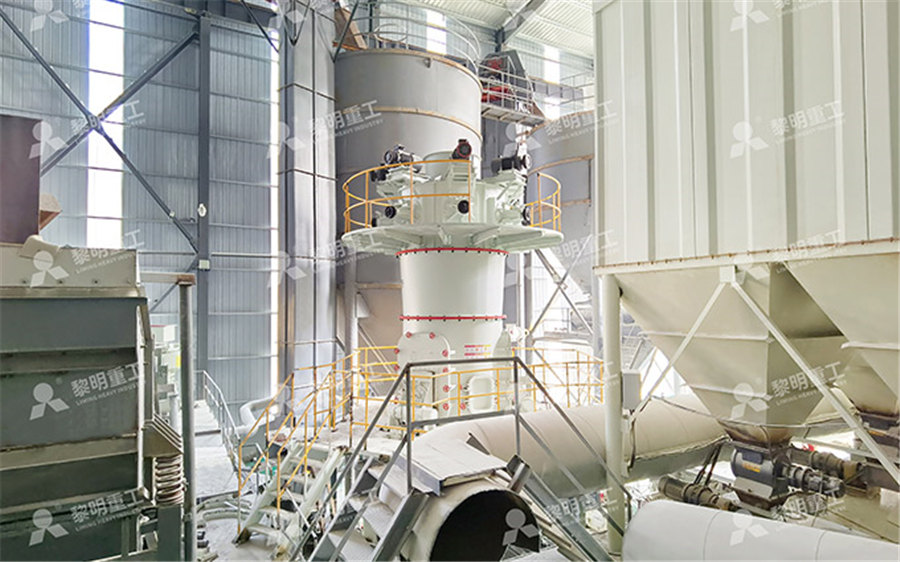
Investigation of fluoride evaporation from CaF2–CaO–Al2O3–MgO
2020年7月23日 Thermodynamic calculations and viscosity measurements were applied for studying the evaporation mechanism of fluoride The results showed that the evaporation ratio This study presents the evaporation mechanism of fluoride from CaF 2 –CaO–Al 2 O 3 –MgO–Li 2 O–(TiO 2) slag and their melting characteristics at different TiO 2 contents by Fluoride Evaporation and Melting Characteristics of 2023年5月4日 Studies have found that it is feasible to replace CaF 2 with alkaline oxide Na 2 O Na 2 O can reduce the melting point, viscosity, and surface tension, promote the crystallization Investigation of Fluoride Evaporation from CaF2CaOAl2O32012年7月1日 The reason why slag melting point for less slag smelting is lower than that for conventional smelting is that the quantity of added fluorite for less slag smelting is more than Slag Melting Characteristic of Slag Forming and Slag Splashing for
.jpg)
Determination of Fluorine Chemical Structure in Slag by Thermal
31P cross polarization/magic angle spinning (19F{31P}CP/MAS) method7can also be applied to analyze the chemical state of F; however, this is difficult since actual slag contains iron (Fe) 2014年5月14日 Many factors influence the nonmetallic inclusions in electroslag steel including furnace atmosphere and inclusions’ content in the consumable electrode, slag amount and its composition, power input, melting rate, filling Effect of Slag on Inclusions During Electroslag 2023年5月15日 According to the EDS analysis of points 5 and 6, the newly formed phases included C 2 S, MA, gehlenite (C 2 AS, melting point 1590 °C), and some glass phases Silicate increases the slag viscosity and reduces the penetration rate and depth of the refractorySlag resistance mechanism of MgO–Mg2SiO4–SiC–C refractories 2022年2月20日 The average hot metal dephosphorization rate of fluorite slagging is 777% The slag melting temperature during calcium ferrite slagging is 1137°C on average, which is lower than the melting (PDF) Hot metal dephosphorization process using
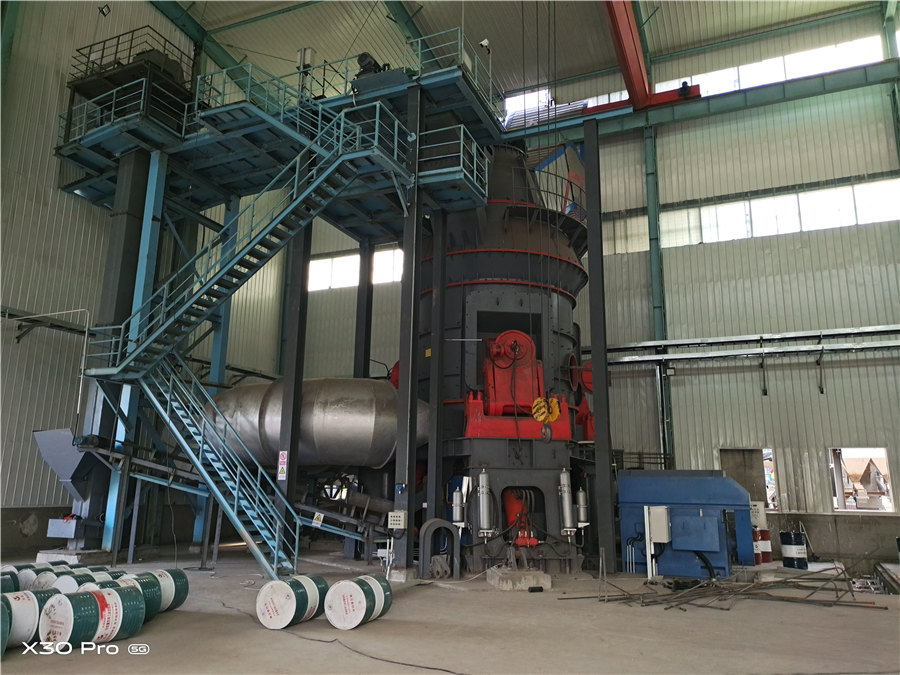
Effects and mechanisms of fluorite on the coreduction of
achieved with a small fluorite dosage (≤4wt%) in the process of coreduction In addition, F− was found to reduce the melting point and viscosity of the slag phase because of the high content of aluminate and silicate minerals in the blast furnace dust The low moisture content offoam slag by vortex stirring, which realizes the high efficiency and shortflow smelting of vanadium–titanium magnetite Previous work has investigated the reconstruction mechanism of the slag phase during the reduction process, but the kinetic control mechanism and the migration mechanism of the valuable components duringProcess mechanism research on direct vortex melting reduction Download scientific diagram Comparison of melting points between mixed slag and premelted slag: (a) Heats B1, B3, and B5, R = 10, w(Fe 2 O 3 ) initial = 10 pct; (b) Heats I1, I3, and I5, R = 2 Comparison of melting points between mixed slag and premelted slag 2021年4月6日 The melting behavior of BOF slag (CaOSiO2FeOx) is one of the key factors for dephosphorization during the converter process Laboratory experiments using mixed chemical reagents and premelted Effect of CaCl2 Addition on the Melting Behaviors of CaOSiO2
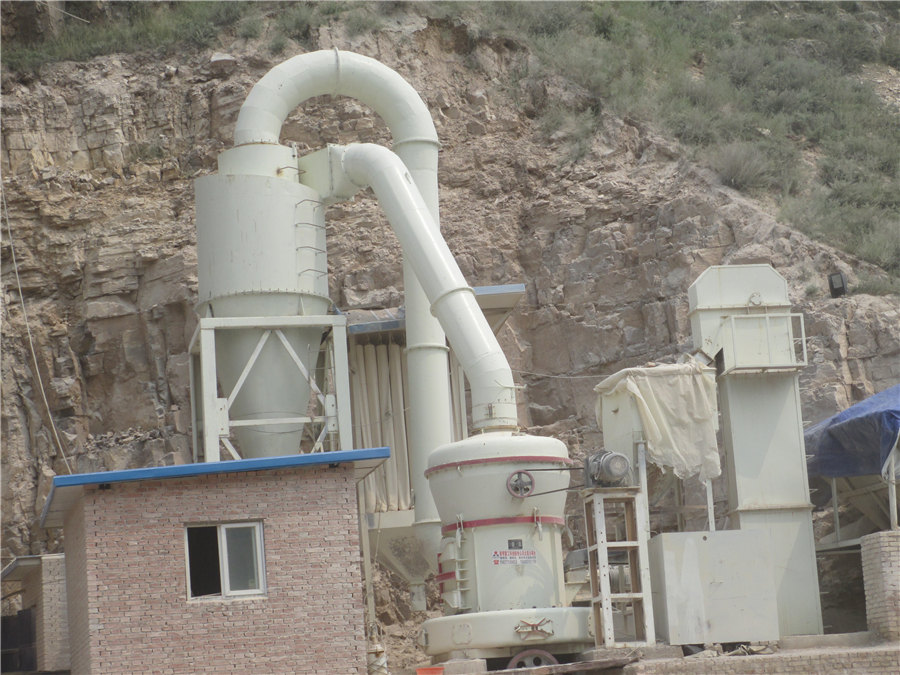
Study on a LimeFluorite Slag Melting Agent for Ladle Slag
2015年6月1日 The Al2O3MgOCr2O3 brick, which is used for wear lining in the ladle slag line, was selected, and the static crucible method was applied to perform a slag sticking test with the refining slag and then investigate the effect of the limefluorite slag melting agent with different recipes The slag corrosion and penetration rate of samples were measured, and the 2017年11月9日 Better results were achieved with a small fluorite dosage (≤4wt%) in the process of coreduction In addition, F− was found to reduce the melting point and viscosity of the slag phase because of the high content of aluminate and silicate minerals in the blast furnace dustEffects and mechanisms of fluorite on the coreduction of2023年5月30日 The reaction mechanisms during melting of hydrogen direct reduced iron pellets (HDRI) with different degrees of reduction were studied experimentally at 1773 K to 1873 K at different times (60 to (PDF) Reaction Mechanisms During Melting of HDRI Focusing on Slag 2004年1月1日 Ladle slag with added WM showed an overall mass transfer coefficient of sulfur ( k O ) equivalent to or higher than that of conventional 10 mass pct CaF 2 containing ladle slag In a slag melting Dissolution Mechanism of Fluorine in Aqueous Solution from
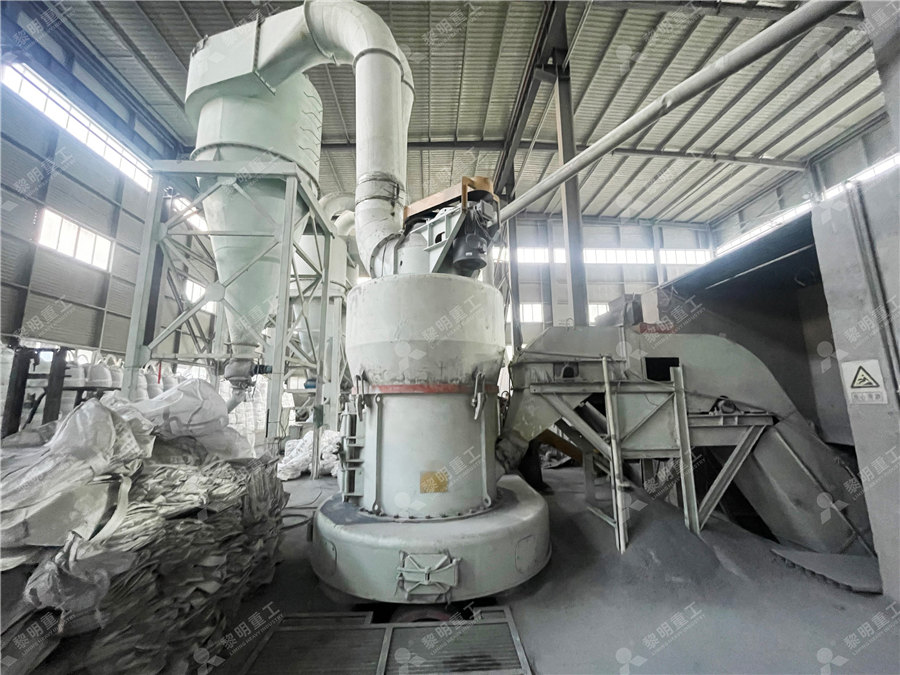
Corrosion behavior of Al2O3–C bricks in MnOcontaining mold slag
2023年8月16日 In order to explore the corrosion mechanism of Al2O3–C refractories in the mold flux bearing MnO, the immersion test of Al2O3–C refractories in CaO–SiO2–CaF2–MnO slag with different MnO contents was carried out at 1550 °C The results show that Mn particles were observed in the slag after experiment, due to the reduction of MnO by graphite in refractories 2024年11月15日 Effect of sintering behavior and phase evolution on glassceramics entirely derived from ferrochrome slag and fluorite tailing were mixed in the proportion of FsFt, 30–70 %, 35–65 %, and 40–60 % (in wt) In addition, in order to reduce the melting we explored the sintering and crystallization mechanism of Effect of sintering behavior and phase evolution on glassceramics 2024年8月19日 31 Migration mechanism of Fe and V during reduction process Figure 4 shows the variation of iron content in the slag with time, and Fig 5 shows the variation of V content in the metal with time As seen in Figs 4a and 5, the reduction rate of iron and vanadium rises as the vortex rate increases, but th reduction reaches its limitation at u = 100 r min −1 (T = 1550 °C)Process mechanism research on direct vortex melting reduction 2023年1月20日 Abstract Industrial production processes generate a large amount of secondary resources (copper slag and spent cathode carbon (SCC)) every year Reducing copper slag by fixed carbon from SCC would fully utilize the substance and the fluxing effect of fluoride In addition to effectively utilizing hazardous waste resources, the reduction of copper slag using Effect of Fluorine on Copper Slag Properties and Structure During
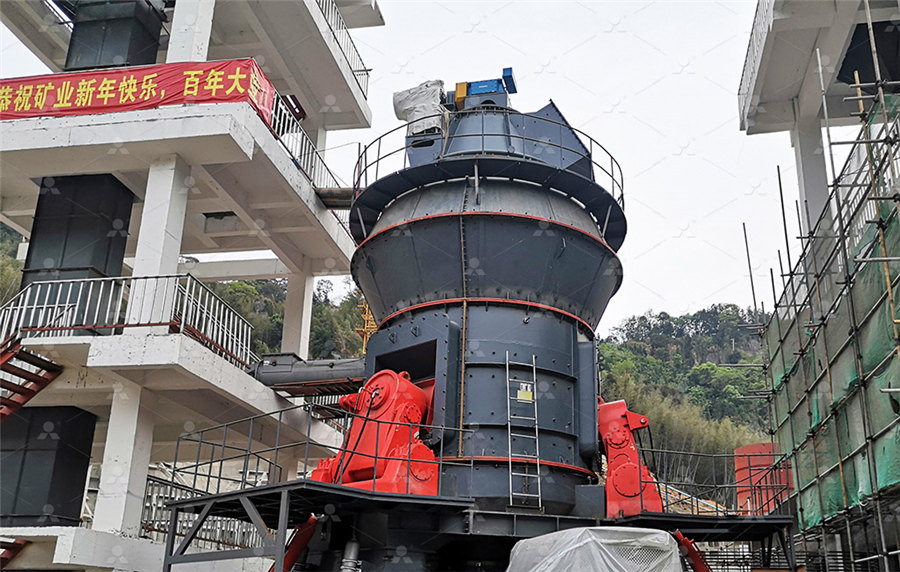
The Effect of Calcium Fluoride on Slag Viscosity
2011年7月6日 Some researchers have also investigated the mechanisms of the effects of calcium fluoride on slag viscosity[4–9] In addition, several models have been proposed to estimate viscosity of slags containing calcium fluoride[10–13] However, the viscosity data for multicomponent slags containing calcium fluoride are still scarce, especially for highbasicity 2021年10月9日 Diopsidebased glassceramics are successfully produced by recycling blast furnace slag and fluorite tailing with the addition of supplementary elements such as TiO2, Fe2O3 and Cr2O3 as nucleation agents, using a conventional melting method The effects of various nucleating agents on the phase components and structure of the prepared glassceramics Recycling of Blast Furnace Slag and Fluorite Tailings into 2019年5月23日 Steel slag is the waste generated in the steelmaking process and includes ferric oxide and the impurities of some infusible matters It is the byproduct when slagforming constituents (such as fluorite, lime, and deoxidant) are added for deoxidization, desulfurization, and dephosphorization in prehensive Utilization Technology of Steel Slag2007年1月1日 The composition of ferromanganese slag is very important as it determines the slag/metal equilibrium rela tions including MnO content of final slag, melting relations and slag viscosityThe effect of alumina in ferromanganese slag ResearchGate
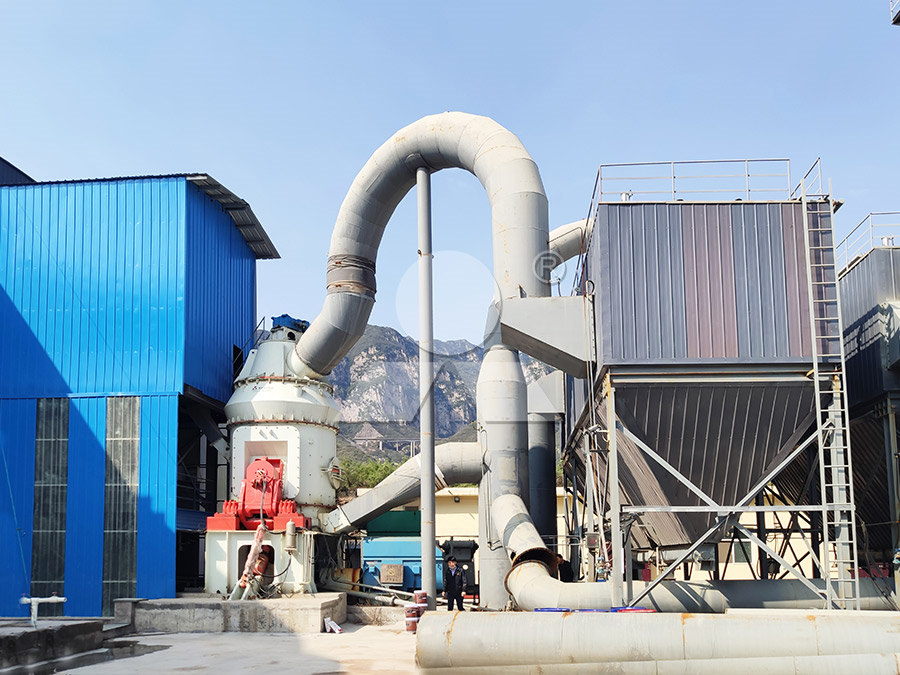
Melting Features and Viscosity of TiO2Containing Primary Slag
The performance of the primary slag in the cohesive zone of blast furnace is critical for smooth operation of blast furnace ironmaking process In the present work, the CaO–SiO 2 –MgO–TiO 2 –Al 2 O 3 –FeO slag system was studied to identify the influence of the FeO and the TiO 2 on the melting features and viscosity The temperatures of melting features are found to decrease 2024年2月19日 In the study, the ratecontrolling mechanism and the kinetic parameters of the reduction reaction of iron oxide in slag have been obtained Schematic diagram of the melting reduction experimental Kinetics analysis of iron oxide reduction by solid carbon in HIsmelt 2007年1月1日 The time for the dust component in the pellet to be melted completely is in the range of 20–45 s and increasing the preheating temperature, especially in the range of 600–800 °C, can Heating and melting mechanism of stainless steelmaking dust pellet in 2008年12月17日 An experimental study was conducted to understand the decarburization and melting behavior of directreduced iron (DRI) pellets in SiO2Al2O3CaOMgOFeO slags with various FeO concentrations (10 to 25 wt pct) and basicities (Bs), ranging from 15 to 25 The behavior of the pellet in slag was observed using the Xray fluoroscopy technique; the rate of Kinetics and Mechanism of Decarburization and Melting of
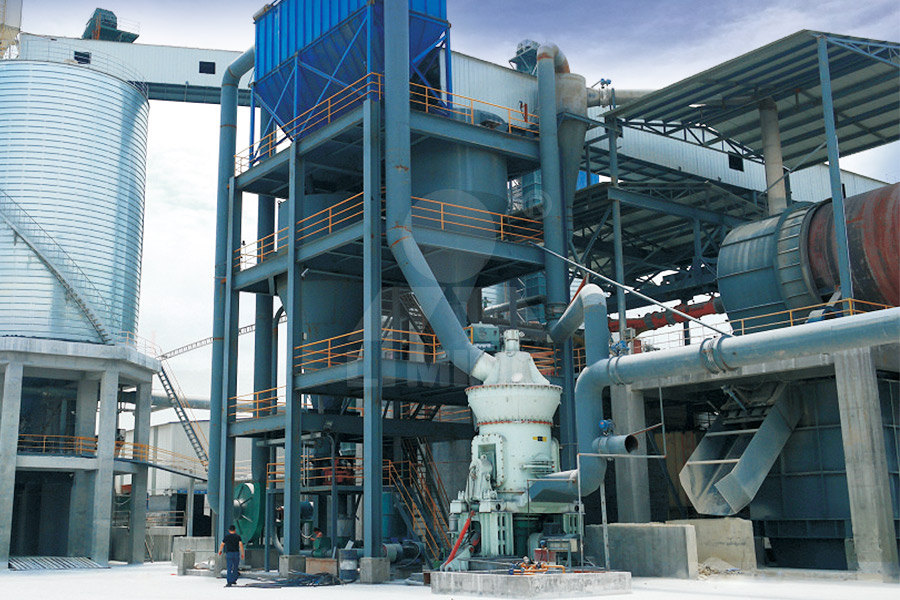
Kinetics and Mechanisms of Dolime Dissolution in Steelmaking Slag
2018年10月3日 mechanism where compounds with high melting points based on calcium and magnesium have a significant role A mathematical model for an unsteadystate diffusion regime has been applied in this work, for the determination of mass transfer and diffusion coefficients of the dolime dissolution process II EXPERIMENTAL PROCEDUREThe (100) plane is the most stable cleavage plane, where the coordination number of Ce atoms reduces from nine to five In contrast, fluorite crystals are attributed to a cubic crystal system Distribution of global fluorite reserves (data from the 2017 USGS calcium ferrite slag without fluorite Wei Wu, Bin Zhao, Bo Zhao, Wei Wu Huadong Meng To cite this article: Wei Wu, Bin Zhao, Bo Zhao, Wei Wu Huadong Meng (2022): Hot metalHot metal dephosphorization process using calcium ferrite slag 2020年7月9日 The melting point and volatilization characteristics of a fluorinecontaining slag were investigated under different heating rates and premelting processes The “hemisphere method” was used to Effect of the heating rate and premelting process on the melting
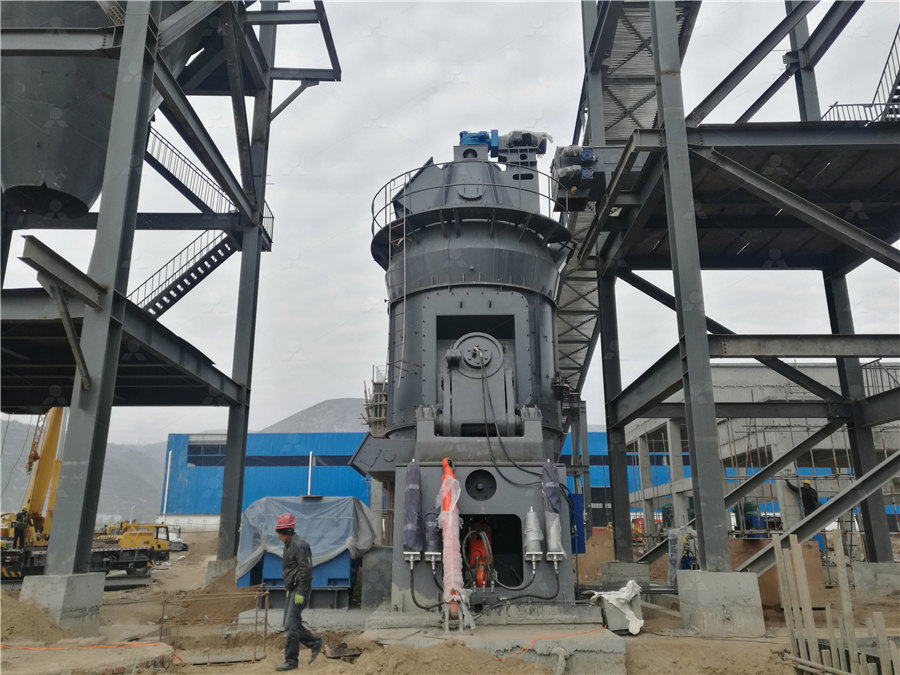
Effect of Fluorspar and Industrial Wastes (Red Mud and Springer
2020年6月23日 Fluorspar (CaF2) has been widely used to control the physicochemical properties of slag in steelmaking processes However, it is very important to reduce the CaF2 consumption because it causes various environmental problems In the current study, therefore, the effect of industrial waste materials such as red mud (RM) and ferromanganese slag (FMS) 2020年1月24日 To reduce environmental pollution caused by fluoride from conventional electroslag remelting (ESR)type slag and meet the requirements of vacuum ESR, it is strongly needed to develop lowfluoride Development of Lowfluoride Slag for Electroslag Remelting: 2 20 Abstract 21 In this paper, Softening Melting experiments with different charge ratios are 22 carried out and compared with typical slag phase properties The relationship between 23 the Relationship between slag phase and softening melting 2016年10月7日 Conventional commercial ESRtype slag contains a large amount of CaF 2 (typically 5070 mass pct), aiming to reduce melting temperature and viscosity of the slag Although CaF 2 plays an important role in ESR slag, the evaporation of fluoride from slag melts during ESR process has always been an extremely serious issue because it poses serious Development of LowFluoride Slag for Electroslag Remelting: Role
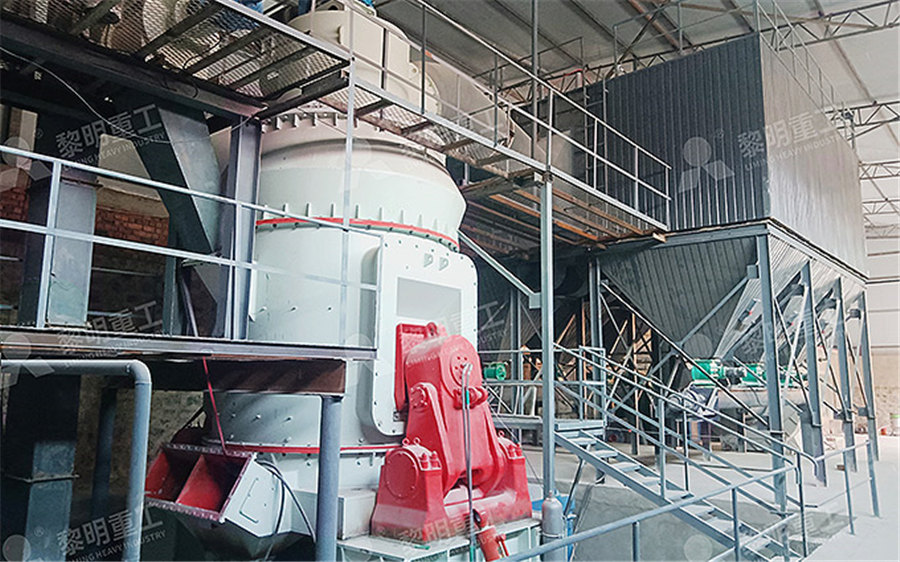
Study of Softening and Melting Behaviour of Iron
2012年6月7日 Softening and melting behaviour of the iron ore materials was studied towards understanding the mechanism of formation of liquid slag and metal phases in the prereduced sinter and pelletsblast furnace (BF) slag production ranges from about 300 to 540 kg per tonne of pig or crude iron produced, whereas 15 to 200 kg per tonne of slag is generated per tonne of liquid steel Lower grade ores yield much higher slag fractions, sometimes as high as one tonne of slag per tonne of pig iron produced Steel slag output is approximately 20 Slag Iron Steel 2015 IBM2014年1月14日 Also, the high melting point of coke ash leads to a decrease in the fluidity of slag, and the resulting small contact area between slag and iron hinders the absorption of sulphur from iron to slag Graphite has good reactivity under high temperature; reduction and carburisation rates in graphite pellets are so fast that they melt after just 4 minDesulphurisation mechanism of direct reduction and melting in 2021年10月9日 One of the stages of extracting gold and platinum from sulfide materials and circulating slags is the melting stage in orethermal and electric furnaces, where the melt is separated into matte and slag Gold, platinum, and nonferrous metals are concentrated in the matte However, a significant portion of them ends up in the slag, which reduces recovery and Transfer of Gold, Platinum and NonFerrous Metals from Matte to Slag
.jpg)
Effect of B2O3 on the Melting Characteristics and SlagMatte
2023年6月9日 This study aimed to increase the recovery efficiency of nickel metal and reduce smelting energy consumption by analyzing the effect of adding B2O3 on the melting characteristics of nickel flash melting slag and the separation of slag and matte In particular, thermodynamic analysis and hightemperature experimental investigations showed that adding 2024年9月16日 The melting and motion of ferroalloys play a crucial role in the mass transfer and homogenization of molten steel in ladles Heat transfer, melting, and solidification behavior of an alloy affect its size, thereby altering its motion within the gasstirring ladle This study established a heat transfer and solidificationmelting model for alloy particles in hightemperature metal Coupled CFDDEM with Flow and Heat Transfer to Investigate the Melting 2023年8月25日 The effect of the proportion of each component on the viscosity and melting temperature of fluorinefree CaOSiO2FeOB2O3MnO dephosphorization slag (DS) was simulated by FactSage software(PDF) Relationship between Slag Phase and Softening Melting converter slag and slag of suspended smelting furnaces Gold and platinum are concentrated in matte drops in the slag Thus, in order to reduce the loss of valuable components, it is necessary to increase the rates of coagulation and sedimentation of matte droplets in the slag, reducing its viscosity This is possible by adding fluxesINFLUENCE OF CaF2 AND CaCO3 FLUX ADDITIVES ON THE
.jpg)
Slag composition mechanism based reduction and smelting of
2015年2月1日 The smelting slag reaction mechanism was studied by thermodynamic analysis and coalbased direct reduction and smelting experiment The experiment result shows that the slag basicity has an