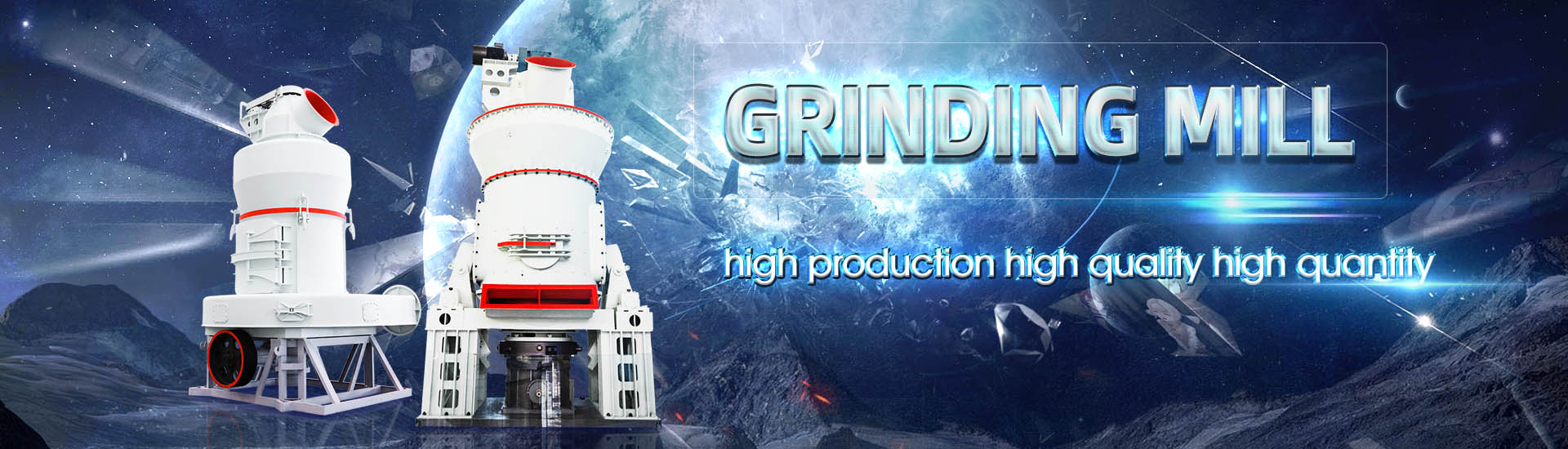
Ore mill price for coarse and fine separation
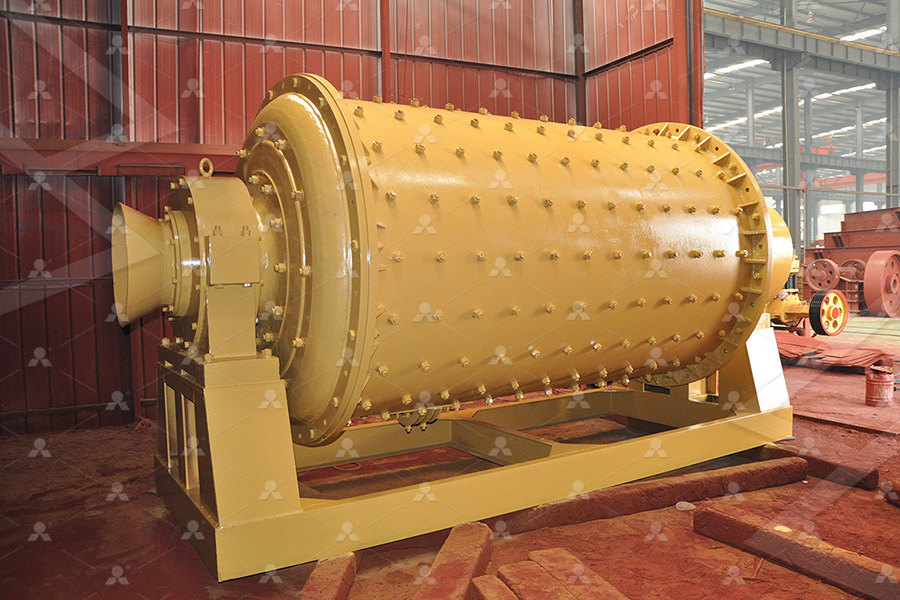
Ore mill, Ore grinding mill All industrial manufacturers
Find your ore mill easily amongst the 42 products from the leading brands (Fritsch GmbH, Retsch, Eriez, ) on DirectIndustry, the industry specialist for your professional purchases Exhibit with usRotational speed: 120 rpm 240 rpm Output: 400 kg/h 30,000 kg/h Machine Glass2009年1月1日 Historically, the lowest operating cost was achieved by multistage fully autogenous grinding with integrated magnetic separation steps between the stages The major benefit of fully autogenousProcessing of Magnetite Iron Ores–Comparing Airswept AG milling (for coarse grind) Historically, the lowest operating cost for finegrained ores was achieved by multistage, fully autogenous grinding (Koivistoinen et al, 1989) with integrated magnetic separation steps between Ecoefficient and costeffective process design for
.jpg)
Dense medium separation an effective and robust pre
Dense medium separation (DMS) is a robust process that can be conducted at particle sizes as coarse as 300 mm and as fine as 500 µm with high separation efficiency, depending on Our sorting equipment or mineral processing equipment, specially developed for mining applications, enables processes to be better controlled, and through ore sorting even ores that Mining separation and sorting equipment for processes in the New separation technologies for coarse particle recovey have begun to address this limitation, causing major mining companies to seriously evaluate the benefits of coarse grinding Coarser Grinding: Economic Benefits and Enabling CiDRAThis paper discusses such beneficiation techniques and advancement in technologies for the upgrading of coarse and fine iron ore utilising dense media separation (DMS), jigging, wet Fine and Coarse Iron Ore Beneficiation An Evaluation into Global
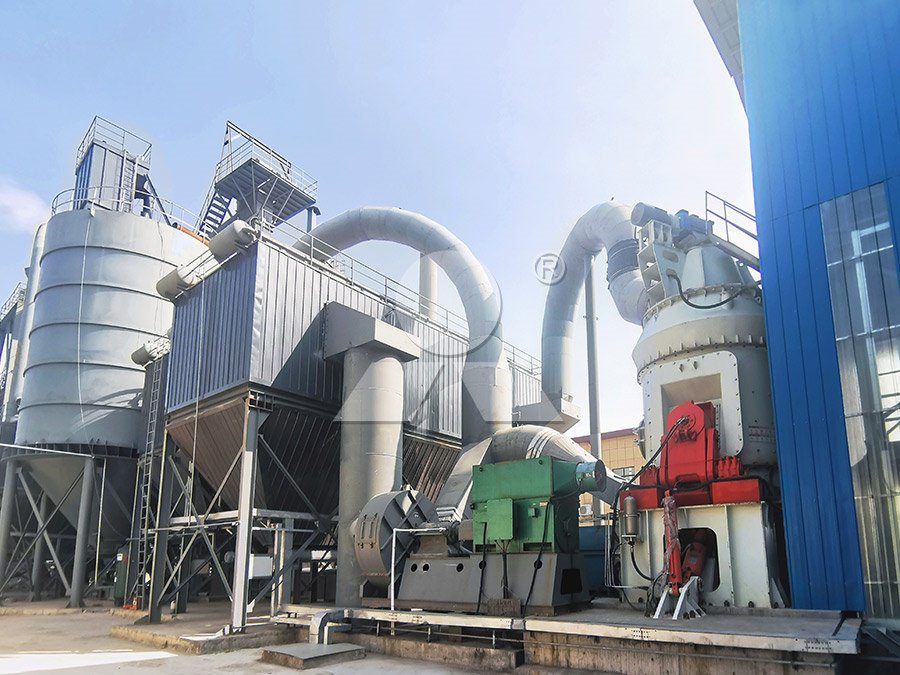
Mineral Processing SpringerLink
2017年8月24日 The price paid by the smelter depends primarily on the market process of the metal, but penalties are introduced in the prices for constituents in the ore or concentrate that 2014年10月15日 The greatest operating cost for a typical ore sorter is the compressed air used to separate stones after they have passed through the sensor (Fig 2) The cost associated Development of ore sorting and its impact on mineral processing 2021年3月1日 For this purpose, the design, operational features, types, and separation mechanism of enhanced gravity separators, such as Falcon concentrator, Knelson Application of Enhanced Gravity Separators for Fine Particle 2009年1月1日 The iron ore beneficiation plants normally include a series stages of size reduction (in order to achieve the desired liberation degree), increasing iron ore grade (magnetic separation), and Processing of Magnetite Iron Ores–Comparing
.jpg)
(PDF) Fine, Coarse and FineCoarse Particle Flotation
2021年3月19日 Fine, Coarse and FineCoarse Particle Flotation in Mineral Processing With A Particular Focus On The Technological Assessments March 2021 DOI: 103390/iecms2年4月1日 Zanin et al, (2021) developed a model to calculate bed porosity and apparent density for two feed specific gravities (porphyry copper ore: 27 kg/m 3 and hematite hosted copper ore: 38 kg/m 3) and particle size values (coarse: −600 + 150 µm and fine: −210 + 75 µm) through Richardson and Zaki models modified by introducing more suitable settling rate equationTechnological assessments on recent developments in fine and coarse 2024年1月17日 A Hasanzadeh, M Safari, DH Hoang, Fine, coarse and finecoarse particle flotation in mineral processing with a particular focus on the technological assessments, Paper presented at the 2nd international electronic conference on mineral science: part of the international electronic conference on mineral science series, 1–15 March 2021 (Online)Advanced Techniques on Fine and Coarse Particle Flotation2023年9月4日 Weakmagnetic separation machines combine with strongmagnetic separation machines First, select iron ore by a weakmagnetic separation machine, tailings scan through strong magnetism, and coarse and fine ores are separated through strong magnetism This process is mainly applicable to mixed ores of magnetism and iron oreIron Ore Beneficiation Plant Equipment For Mining Process
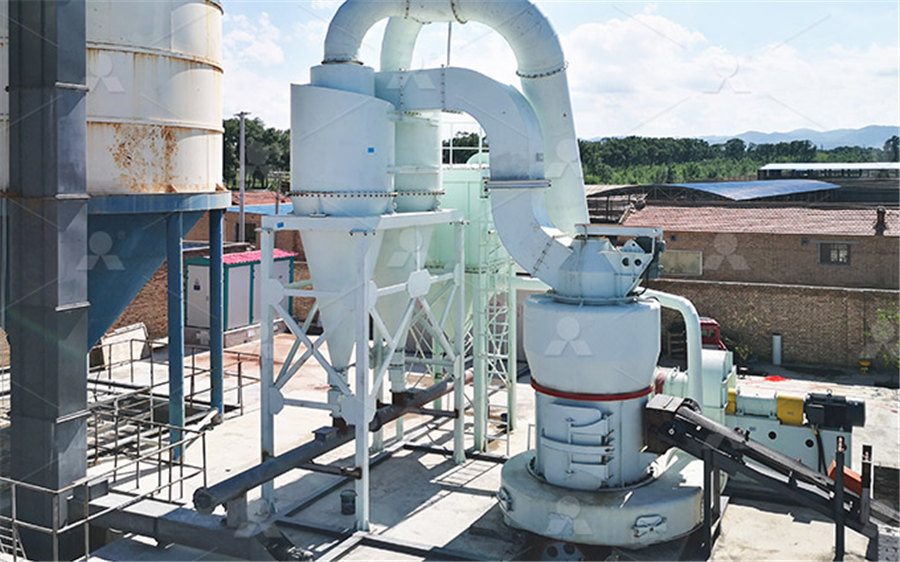
Modeling and application of stirred mill for the coarse grinding of
2022年5月23日 HighPressure Grinding Rolls (HPGR) product of −1 mm was used as feed material to the stirred mill experiments A fourfactor (stirrer speed, grinding time, pulp density, and media filling) and a fivelevel Central Composite Design matrix (CCD) was applied to investigate the stirred mill performance in coarse grindingzinc, copper and lithium based ores using DMS This paper reviews historical dense media systems, results from the pilot scale Condor DMS system as well as associated laboratory heavy liquid separation (HLS) test work KEYWORDS Preconcentration, dense media separation, heavy liquid separation, comminution, copper, lead, lithium, zincRECENT DEVELOPMENTS IN PRECONCENTRATION USING DENSE MEDIA SEPARATION2017年3月7日 ORE SEPARATION BY CLASSIFICATION It separates coarse and fine solids, to return coarse material back to the ball or ro d mill for further grinding(PDF) ORE SEPARATION BY CLASSIFICATION ResearchGate2017年3月3日 Particle impact noise detection (PIND) test is a kind of reliability screening technique which is used to detect free particle in hermetical components and is specified in MILSTD883E method 20207(PDF) ORE SEPARATION BY SCREENING ResearchGate
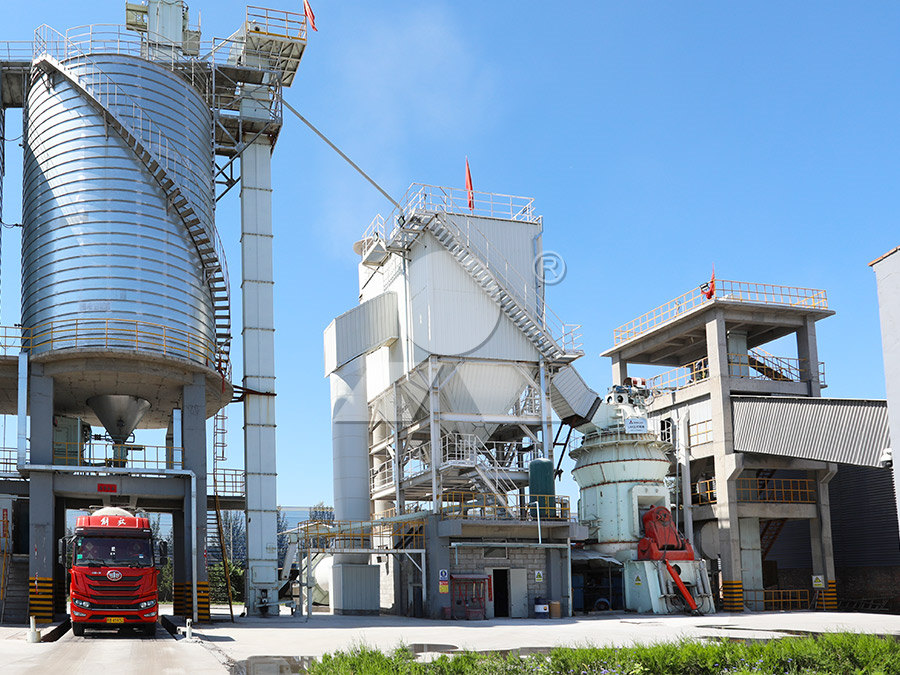
Ore, Rock Aggregate Screening (Complete Guide)
2016年6月20日 In a feed humidity is mainly fixed to the fine material The percentage of moisture, therefore, should always be measured in the finest fractions 911 Metallurgist is a trusted resource for practical insights, solutions, and support in mineral processing engineering, helping industry professionals succeed with proven expertise Ore, Rock Aggregate 2024年8月23日 Use of a ball mill is the best choice when long term, It handles fine gold ore and is simple to operate with low cost Spiral Concentrator: stable performance Jig: Used for coarse gold ore separation It has high processing How to Extract Gold from Oxidized Gold Ore: 3 Proven The vibrating table with a maximum feed particle size of 2 mm is used for coarse ore, 05 mm is used for fine ore, and 0074 mm is used for slime 3 The amount of feeding ore The amount of feeding ore is related to the granularity of the Shaking Table In Ore Processing Fote Machinery2018年10月12日 Fig 1 Effect of centrifugal force on gravity force Separation of the ore particle by gravity is dependent on two factors namely (i) settling rate of the particles, and (ii) difference in specific gravity when compared against the Gravity separation and Ore Beneficiation IspatGuru
.jpg)
Dense Medium Separation An Effective and Robust Pre
Dense medium separation (DMS) is a robust process that can be conducted at particle sizes as coarse as 300 mm and as fine as 500 µm with high separation efficiency, depending on liberation characteristics of the value minerals The DMS process involves three steps: feed preparation, dense medium separation, and ferrousbased media recoveryThe qualified mineral pulp will enter into two magnetic separators in order for the coarse and fine processing in order to realize the purpose of mineral separation 4 drying The fine ore pulp after classification will enter into the concentrator for the precipitation, and then entering into the dryer for the dehydration, and lastly the fine Magnetic Separation Process Hongxing Machinery2019年8月29日 Sensor‐based ore sorting can be used as a separation process for coarser grain sizes before the application of fine comminution and separation technologies and ughput of a gold ore mill(PDF) Sensor‐Based Ore Sorting Technology in Mining—Past, 2024年11月21日 Generally speaking, the grid type ball mill is suitable for coarse grinding, and the overflow type ball mill is suitable for fine grinding When it is necessary to grind to a uniform coarsegrained product of about 0208~0295mm (48~65 mesh), the grid type ball mill is better;Ball Mill Is Indispensable For Lithium Ore Processing
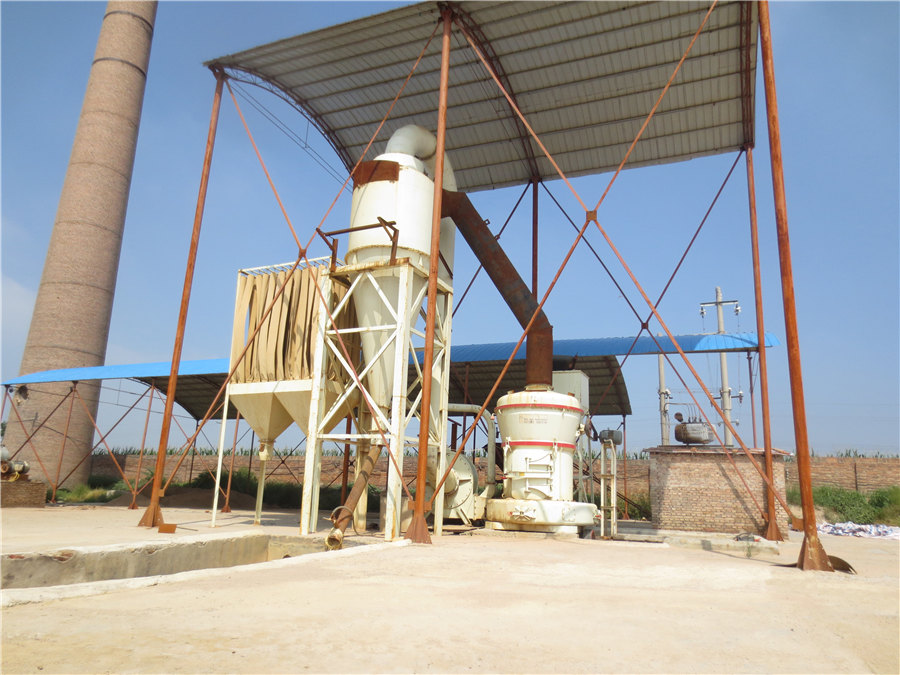
Recovery and separation of iron from iron ore using innovative
2017年1月1日 Finally, the magnetic component of the roasted ore can be recovered by magnetic separation after being liberated from gangue minerals Many pilotscale suspension magnetizing roasting and magnetic 2008年2月1日 The article makes an effort in consolidating the developments in the field of advanced gravity separation techniques for processing fine particles over the last few decades(PDF) Recovery of gold from a freemilling ore by ResearchGate2024年11月21日 In conventional better flotation indicators, it is necessary to control the particle size of mineral particles to 1010μm Coarse particle flotation generally refers to direct flotation recovery of ore particles with a particle size more than 150 μmHas the following advantages: (1) Carry out preselection and discarding of tailings on raw ore, reduce the amount of ore Causes And Measures Of Coarse And Fine Mineral Flotation 2020年4月1日 The decreasing grade of chromiumore bodies and difficulties in identifying new highgrade deposits highlight the significance of processing fine, lowgrade oresProcess optimization of a chrome ore gravity

Ore Grinding SpringerLink
2023年7月20日 Therefore, the rod mill is mostly used for coarse grinding of the previous period of ball mill, or grinding of brittle materials and materials against overcrushing, such as tungsten and tin ore before gravity separation; and (3) autogenous mill – it refers to the materials which themselves are collided and ground mutually to be crushed when the grinding mill rotates, and 2016年10月22日 At the same time, in order to eliminate the effect of fine slime, desliming of coarse slime should also be considered With high yield, Ran Jincai, et,al separation of coarse slime and its effect on coal preparation technique [J] Coal Preparation Technology, 2009(4):7174Problem Analysis and Optimization Test for Separation Process of 2019年12月15日 AMIRA 1993 An investigation of the Hilton Tower Mill Circuit Method and benefits of fine grinding ores Google Scholar Arvidson, BR, and D Norrgran 2014 In Magnetic separation in mineral processing and extractive metallurgy—100 years of innovation, ed CG Anderson, RC DunneBeneficiation of Gold and Silver Ores SpringerLinkChina Coarse Mill wholesale Select 2024 high quality Coarse Mill products in best price from certified Chinese Mill manufacturers, Grinder Machine suppliers, Wet Fine and Coarse Grinding Rod Mill / Rod Ball Mill with Good Prices US$ 700080000 / Piece 1 Piece (MOQ)Coarse Mill MadeinChina
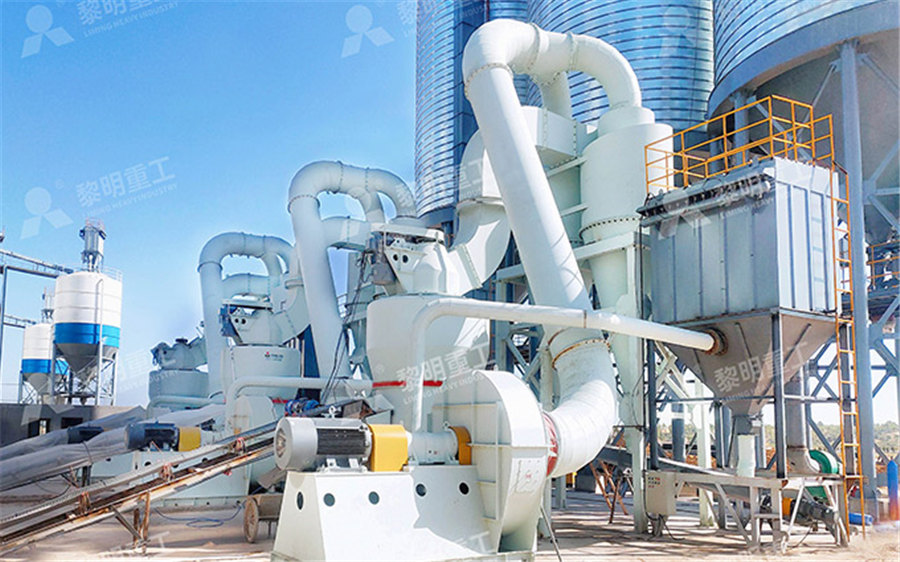
EcoEfficient and CostEffective Process Design for Magnetite Iron Ore
2013年9月16日 Although the majority of current steel production is supported by iron ore sourced from high0grade haemetite deposits, the longterm growing demand for steel has led to higher raw material prices ORE SEPARATION BY CLASSIFICATION By It separates coarse and fine solids, carried in liquids, with a high degree of accuracy and with lowest possible power and maintenance costsORE SEPARATION BY CLASSIFICATION By ResearchGate2023年4月25日 ② Use an overflowtype ball mill for fine grinding For the coppernickel ore with coarse particle size and not very size, grade, and concentration of the pulp meet the leaching requirements, so it is necessary to wash the laterite ore (separation of coarse and fine particles), remove impurities (mainly remove the 2 Types of Nickel Ore: Processing Methods and Equipment2024年5月6日 A crucial step in mineral processing – and in Minnesota’s iron ore processing – is comminution, a process of crushing and grinding Large rocks must first be crushed and then ground down to tiny particles to expose the valuable or desired minerals so they can be separated from the waste rock The prevalence of lowgrade and complex ores make fine and ultrafine NRRI advances efficient grinding technology on the Iron Range
.jpg)
Mineral Processing and Ore Dressing 911Metallurgist
2016年6月2日 A preliminary crushing to the necessary fineness is made, in some cases as coarse as 2″, and then the ore is subjected to a separation through a heavy mineral suspension The concentrated values are then further treated by finer grinding, flotation, or whatever indicated treatment is required to make a finished product2019年7月8日 While the deposit qualities for mineral raw materials are constantly decreasing, the challenges for sustainable raw material processing are increasing This applies not only to the demand for minimizing the SensorBased Ore Sorting Technology in Mining—Past, 2024年1月4日 Using coarsegrained jig machines for coarsegrained iron minerals, manganese ore, barite, celestite, etc, Using trapezoidal jigs and downmoving jigs for medium finegrained ore beneficiation For mineral Jig Separator Gravity Separation of Tin Ore JXSC 2024年7月11日 However, the magnetic separation method has limited processing capacity for nonmagnetic minerals in tin ore and has a poor separation effect on minerals with fine particle size and weak magnetism In Tin Ore Dressing: Gravity, Flotation And Magnetic
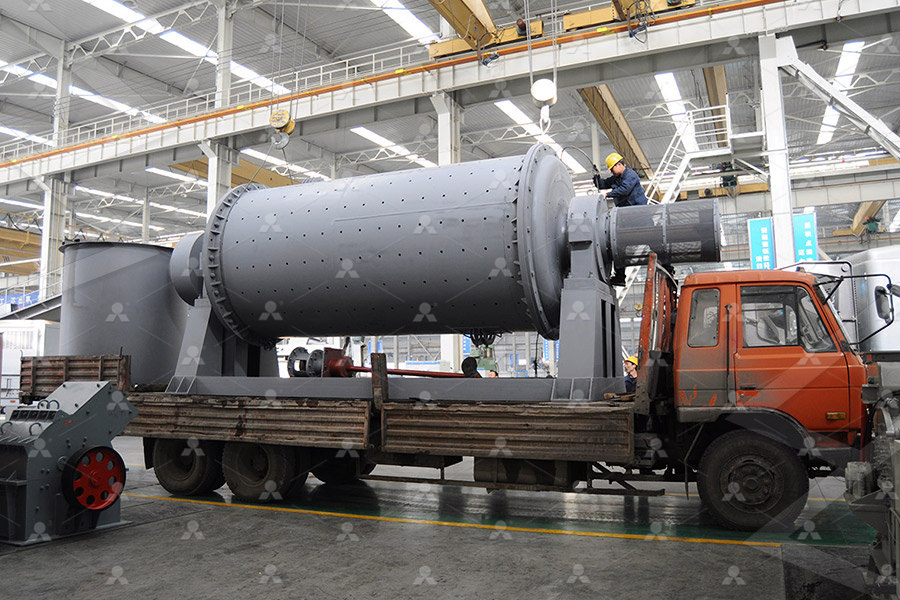
Types of Mining Magnetic Separators Mineral Processing
2024年11月21日 And magnetic separation is the main method of iron ore dressing Skip to content JXSC Machinery Us +86 It is suitable for the treatment of ore particles less than 05 mm of coarse and fine Please fill out the information below for the quotation price and engineer’s help We will reply ASAP! Your Name 2015年7月27日 Let’s begin with fine ore storage bin or stockpile, get it out of the way and then proceed to grinding You would think that there isn't that much to learn 911 Metallurgist is a trusted resource for practical insights, solutions, and support in mineral processing engineering, helping industry professionals succeed with proven expertise Fine Ore Storage Bin and Fine Ore Storage Bin and Stock Pile 911Metallurgist2016年2月29日 In this part, a reliable sampling representing the ore is a key aspect Separation, concentration and leaching processes involve several operations such as Jigs can receive coarse particles such as a ball mill discharge A finer size can be considered if the ore needs fine liberation The leach cycle is normally from 20 to 30 Gold Extraction Recovery Processes 911Metallurgist2024年4月26日 AG/SAG mills are typically used for coarse grinding, where large pieces of ore are efficiently broken down The grinding process reduces the ore size, which enhances the efficiency of subsequent beneficiation processes by increasing the surface area available for chemical reactions and physical separations 2 BeneficiationIron Ore Processing: From Extraction to Manufacturing
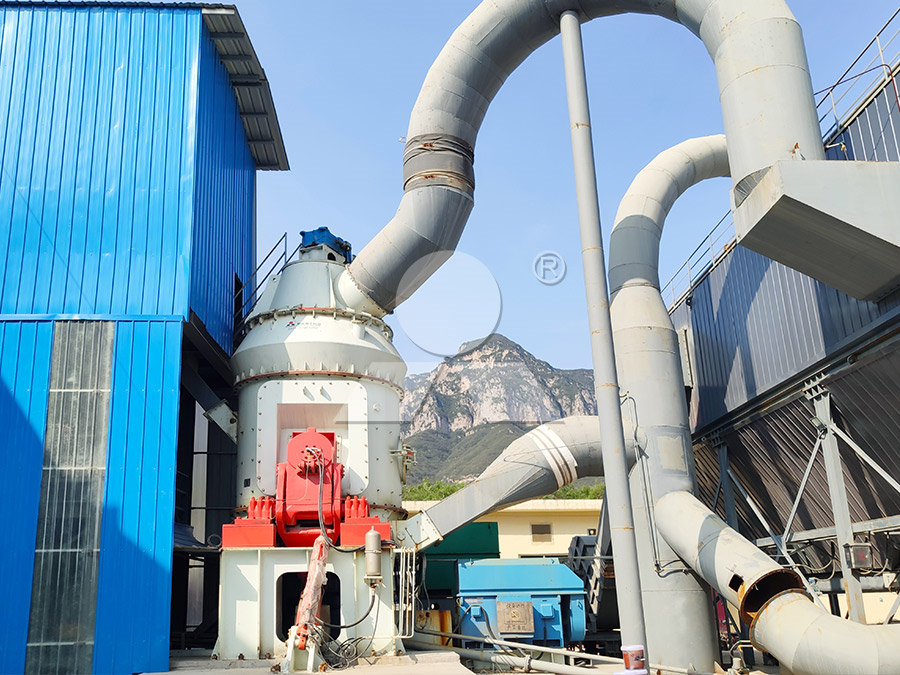
Optimization of stirred mill parameters for fine grinding of PGE
2020年7月23日 Abstract The depletion of highgrade ores has forced the utilization of lowgrade ores The small liberation sizes in the lowgrade ores require fine grinding which is an energy intensive operation In the present study, lowgrade chromite ore bearing platinum group of elements (PGE) was used as an experimental material The previous study concluded the 2022年1月1日 In Fig 914, the feed ore is first ground down to about 60% −75 micron particle size in the primary grinding stage of the flow sheet, and then classified into two size fractions, a coarse size fraction and a fine size fraction The coarse size fraction is treated with spiral separators to recover part of the final iron ore concentratePhysical separation of iron ore: magnetic separation2022年9月30日 Separation principle of CTFG dry magnetic separator for fine ore [41] 1—vib ration feeder; 2—ultrathin transport belt; 3—tail wheel; 4—concentrate scraper; 5—concentrate bucket; 6—Dry Permanent Magnetic Separator: Present Status and Future