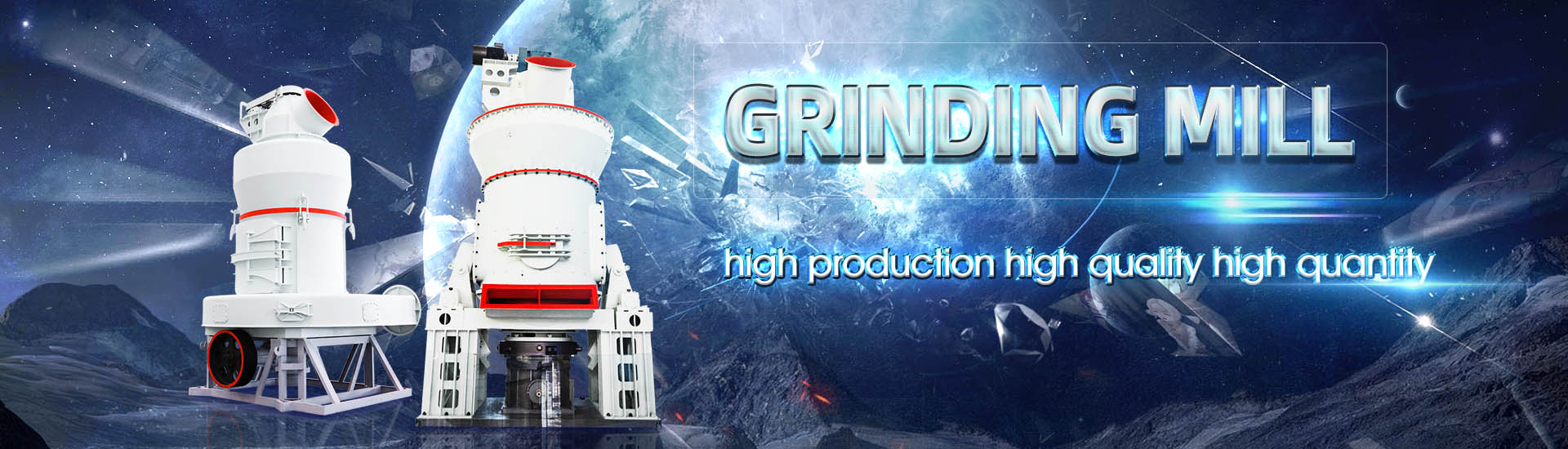
The output of ball milled high calcium powder
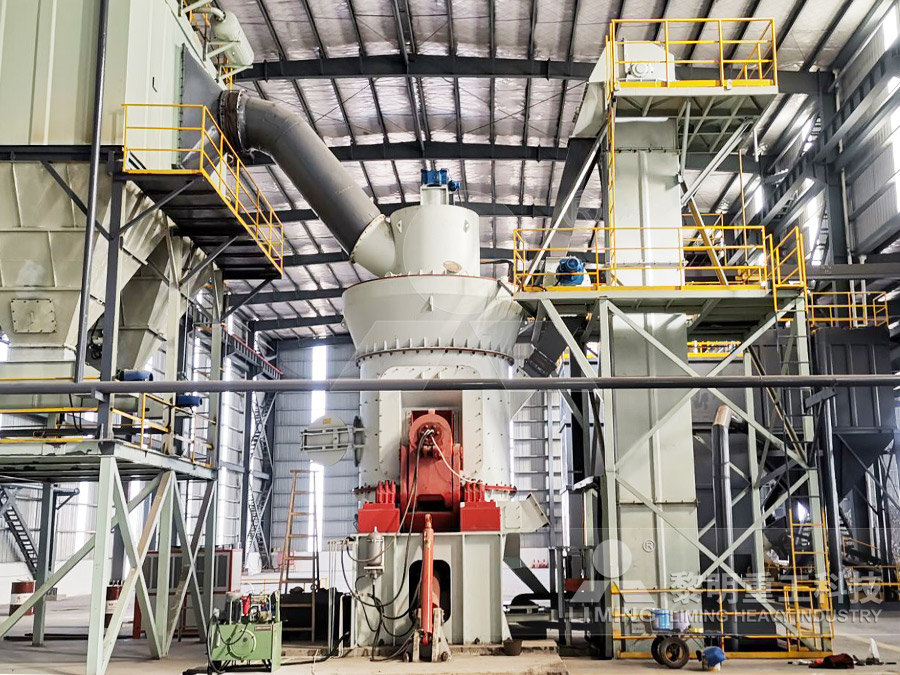
Use of Taguchi method for high energy ball milling of CaCO 3
2022年2月4日 Taguchi’s method was applied to investigate the effect of main high energy ball milling (HEBM) parameters: milling time (MT), ball to powder weight ratio (BPWR), and milling speed (MS) on the CaCO 3 crystallite size The settings of HEBM parameters were 2020年11月16日 The study showed that the combination of the BPR and powder type affects the particle size result The optimum of BPR at 12 with the number of balls is 60 pieces, and The design and optimization process of ball mill to reduce particle 2016年8月1日 As a significant case study in ceramic powder technology, the model is presented and validated for calcium fluoride (CaF 2), ground under different conditions in a planetary mill, Modeling of the planetary ballmilling process: The case study of 2014年1月1日 In this study, polycrystalline Ca3Co4O9+δ ceramics were prepared by a simple, thermal, hydrodecomposition method The influence of ballmilling time on particle size was Effect of Ballmilling Time on Particle Size of Ca3Co4O9+d
.jpg)
Effect of ball and feed particle size distribution on the milling
2018年6月1日 In this investigation, the input variables were the ball and particle size distributions while the output variables were the desired PSD The objective function was to 2014年1月1日 In the present work, CaAl 2 O 4 nanoceramic compound was produced by highenergy ball milling of the oxide powders followed by annealing The phase evolution and Synthesis of the CaAl2O4 nanoceramic compound using high 2019年6月26日 The variation of M2 powders shape during highenergy milling as the function of milling time up to 22 h was shown in figures 4(a)–(f) During the milling process, powders were Effect of ball milling on the powder characteristics and welding 2022年3月16日 Highenergy ball milling represents an efficient process for producing composite powders consisting of ceramic particles dispersed in a metallic matrix However, collision events, plastic deformations, and cold Influencing the Size and Shape of HighEnergy Ball
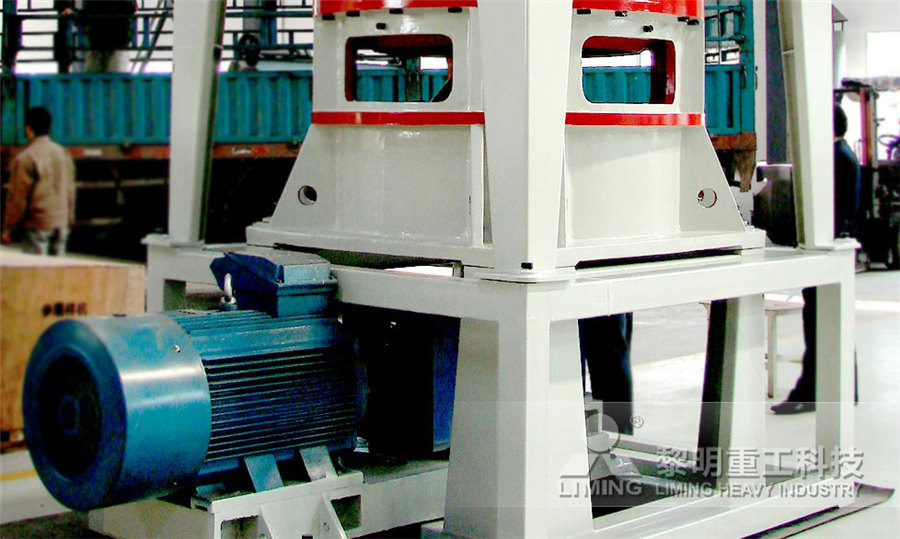
Effects of powdertoliquid ratio on properties of βtricalcium
ballmilling process (mβTCP) The resulting powder can be used in a calciumphosphatecement (CPC) In this study, the effects of the powdertoliquid ratio (P/L ratio) on the properties of the Download scientific diagram Phases and structural parameters of ballmilled (30 h) powder mixtures from publication: Synthesis and characterization of Mechanically alloyed Nanostructured Phases and structural parameters of ballmilled (30 2015年4月22日 SEM micrograph of the ballmilled mixture of boron carbide and graphite powders at milling time of 0 h (manual mixing) at magnification of (a) 500Â and (b) 2000Â, respectivelyOn the Use of Ball Milling for the Production of 2009年9月1日 The ball milling effect on the sorption properties of tribasic calcium phosphate (TCP) is presented The materials obtained were characterized by Xray diffraction, SEM, particle size and specific (PDF) The ball milling effect on tribasic calcium phosphate and its
.jpg)
Surface defect enhanced conductivity of calcium fluoride for
2019年2月12日 Nyquist plots of the CaF 2 pellets of pure CaF 2 ballmilled samples (RT to +100°C) are shown in A Similar results of the asprepared electrolyte (CaF 2 humidified and ball milled) for different 2017年8月24日 Preparation of TEM specimen of nanocrystalline Al10Ti alloy was possible by compaction of high energy ball milled powder under a pressure of 3 GPa Cold compaction followed by sintering is a simple and cost effective process and therefore has widely been used for consolidation of highenergy ball milled Al based alloys and several other alloys [ 37 , 38 , Consolidation of HighEnergy Ball Milled Nanocrystalline Al Powders2013年5月1日 A simple method of improving hydrogen generation from the reaction between highly activated Mg powder and water is established The Mg–H 2 O reaction is found to become faster and more intense when magnesium is mixed with salts and subjected to by highenergy ball milling Among the studied salts, AlCl 3 has the best performance The milling time and salt Hydrogen generation from the hydrolysis of Mg powder ballmilled 2015年7月1日 The milled Al–Sn–Zn–X (X: hydride or halide) mixtures had high reactivity and Al–Sn–Zn–MgH2 mixture produced 790 mL g−1 hydrogen in 5 min of the hydrolysis reaction with the Study on hydrogen generation from the hydrolysis of ball milled
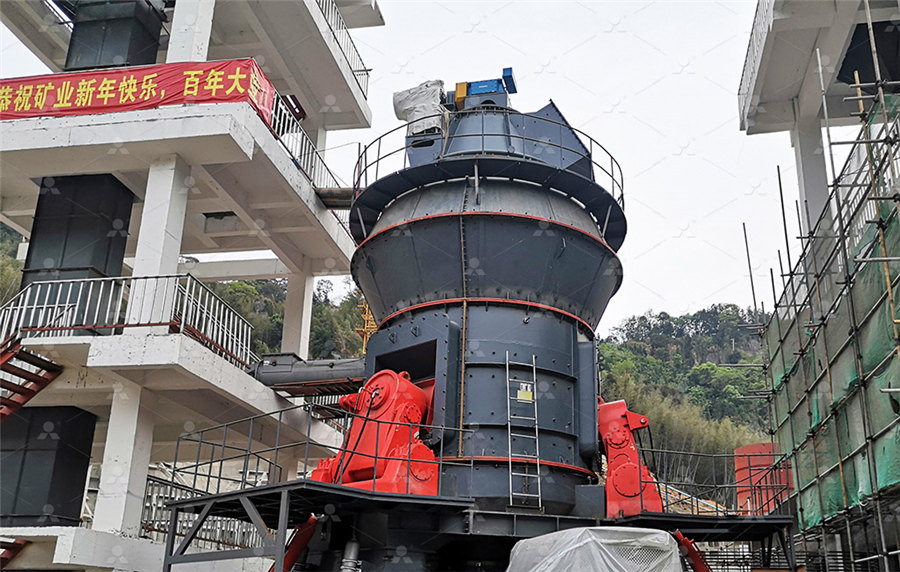
Comparative study on the characteristics of ballmilled coal fly
2015年12月10日 Highenergy mill (HEM) has a wide application in material preparation, activation and synthesis In the present study, fly ash was selected to be milled by HEM under the speed of 700 rpm and the balltopowder ratio of 10:1 by weight, but varied periods of milling time The changes in physical and morphology properties of the milled fly ash were determined 2016年11月1日 SEM micrographs of pristine powder (top) ballmilled with the cylindrical (CY, bottom left) and halfmoon (HM, bottom right) jars for 8 h and with velocity ratio of ω/Ω þ1¼ À10Homogeneity of ball milled ceramic powders: Effect of jar shape 2016年8月10日 Si powder was prepared as described above and its characteristics for reaction with water examined Fig 1 A shows typical results for the volume of produced H 2 and the temperature change of the reaction of ballmilled Si powder containing 70% Si, 20% KOH, and 10% sucrose with distilled water without stirring under the anaerobic atmosphere at the initial Ballmilled Si powder for the production of H ScienceDirect2013年7月4日 The paper is focused on the processing of aluminum alloy chips using powder metallurgy Chips obtained from recycled AlSi5Cu2 alloy were ball milled with the addition of silicon carbide powder Structure Investigation of Ball Milled Composite
.jpg)
Hydrogen generation from the hydrolysis of Mg powder ballmi
Downloadable (with restrictions)! A simple method of improving hydrogen generation from the reaction between highly activated Mg powder and water is established The Mg–H2O reaction is found to become faster and more intense when magnesium is mixed with salts and subjected to by highenergy ball milling Among the studied salts, AlCl3 has the best performanceM Mhadhbi DOI: 104236/ampc2021 33 Advances in Materials Physics and Chemistry Figure 1 Photograph of the highenergy planetary ball millModelling of the HighEnergy Ball Milling Process ResearchGate2002年2月1日 52 The reaction rate (or the rate constant of the transformation process for the starting powder) [k] during dry grinding by ball milling is a strong function of the rotation rate (), the total Effect of ball milling on the processing of bone substitutes with 2018年5月25日 The optimum pH for Cd(II) adsorption was 5 for ballmilled biochar entrapped in Caalginate beads The maximum Cd(II) adsorption capacity estimated with Langmuir isotherm modeling was 2271 mg g −1 for ballmilled biochar entrapped in Caalginate beads, much larger than that of ballmilled biochar alone (400 mg g −1) The ballmilledEntrapment of ballmilled biochar in Caalginate beads for the
.jpg)
Influence of oxygen induced during highenergy ball milling
2021年3月5日 Starting from micrometric pure nickel powder, highenergy ball milling process allows to produce nanostructured agglomerate powders associated with For both micrometric powder and milled powder, the amount of Ni2O3 oxides is similar However, with regard to NiO, the milled powder reveals a larger amount of oxides that the 2005年4月1日 A ZrO2–TiO2 solid solution is obtained by high energy ball milling of equimolar mixture of monoclinic (m) ZrO2 and anatase (a) TiO2 Nanocrystalline orthorhombic ZrTiO4 compound is initiated Xray Microstructure Characterisation of BallMilled Nanocrystalline 2022年4月21日 was milled with a ball to powder ratio of 5:1 with the mentioned lower milling speed aiming to break up the lamellar towards more homogeneous particle size and more r oundness In(PDF) Influencing the Size and Shape of HighEnergy Ball Milled 2022年6月25日 This work made an attempt to optimize the powder metallurgy (PM) process parameters of ballmilled AA8079B4C composites via Taguchi grey relational analysis to attain better mechanical propertiesEvaluation on Powder Metallurgy Process Parameters of BallMilled
.jpg)
(PDF) Dilatometry of ball milled nickel nano powder during
2007年1月1日 This work attempts to evaluate the sintering mechanisms of ball milled nanocrystalline nickel during nonisothermal heating Samples showed a sintered density of 912% (theoretical) and grain from balls to the powder particles during milling The energy transfer depends on such parameters: type of ball mill, milling speed, powder mass to ball mass ratio, lubricant presence, ball filling rate of milling container, milling speed, time and temperature of process [3, 4]THE EFFECT OF POWDER BALL MILLING ON THE 2018年11月1日 As a typical MA, high energy ball milling process is a very complex dynamic process that possesses a lot of variables, such as the ball to powder ratio (BPR), milling speed, number and type of milling ball, the amount of process control agent, etc High energy ball milling is a mechanical alloying process that can be used to fabricate nanocrystalline powder and The ball to powder ratio (BPR) dependent morphology and microstructure 2022年6月25日 This work made an attempt to optimize the powder metallurgy (PM) process parameters of ballmilled AA8079B 4 C composites via Taguchi grey relational analysis to attain better mechanical properties The process parameters are reinforcement weight percentage, compaction pressure, sintering temperature, and sintering time, and the output responses are Evaluation on Powder Metallurgy Process Parameters of Ball‐Milled
.jpg)
synthesis and characrerisation of advanced ballmilled AlAl2O3
2016年4月13日 The nano Al 2 O 3 reinforcements were observed to be dispersed uniformly after 20 h of milling, and the measured Carr index of 132% indicated that the ballmilled powder offered good flowabilityFig 1: Xray pattern of tribasic calcium phosphate: a) without ball mill (TCP), b) ball milling 5 h (TCP5), c) ball milling 10 h (TCP10) and d) ball milling 15 h (TCP15) Scanning electron microscopy (SEM) The size and shape of the grains of the nonmilled TCP sample and ball milled TCP samples as determined by SEM are very different (Fig THE BALL MILLING EFFECT ON TRIBASIC CALCIUM PHOSPHATE 2013年12月1日 Percent passing of milled Al 2 O 3 powder as a function of particle size for varying ball diameter Rotation speeds are (a) 50 rpm, 100 rpm, and (c) 153 rpmEffect of ball size and powder loading on the milling efficiency 2016年10月26日 As amorphous AT solid is known to be transformed into the stable crystalline form in an aqueous solution, [] the intrinsic solubility of amorphous form was evaluated based on initial dissolution profiles using a dissolution kinetic model Equation (1) involving phase transformation proposed by Nogami et al [29, 30] The dissolution tests were repeated three Effect of ball milling on the physicochemical properties of
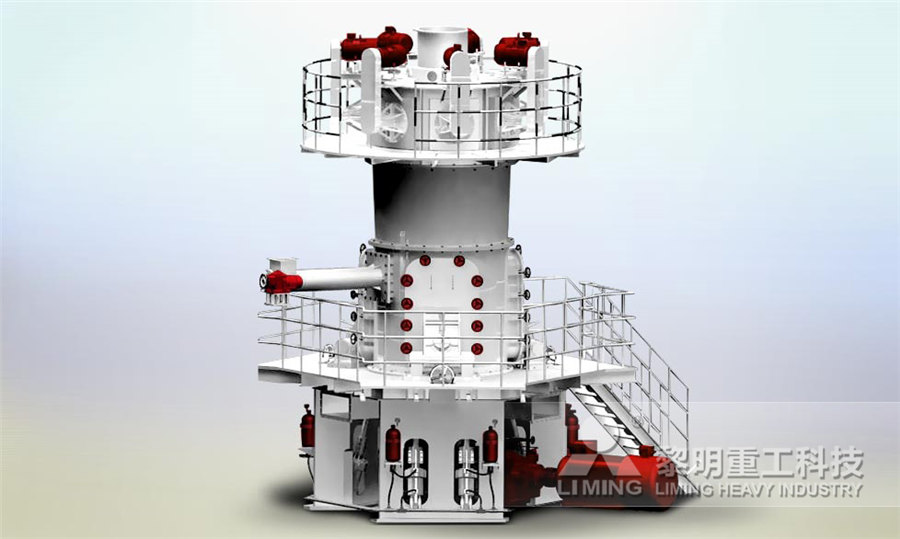
Effect of ball and feed particle size distribution on the milling
2018年6月1日 A number of researchers (Deniz, 2012; Bwalya et al, 2014; Petrakis et al, 2016) carried out studies about the effect of feed particle size and grinding media size on the grinding kinetics of different oresKhumalo et al, 2006 postulated that generally larger sized grinding media would break larger particles quicker but a finer product would be obtained by use of 2022年5月15日 First, the raw materials of mold powder were weighed (Table 1)In sequence, the mixtures were ballmilled, with a Zirconia (ZrO 2) ball as the media (d = 35 mm) and a balltomaterial mass ratio of 1:1, at the speed of 900 rpm for 60 min in the tank of the ball mill (Changsha Tianchuang Powder Technology Co, Ltd, China)Finally, dispersed and stable Effect of ballmilling parameters on the rheological properties of 2020年11月16日 By 10 h of ball milling with the optimized milling parameters, D50 and WC grain size of the ball milled WC–Co powder were about 400 nm and 10 nm, respectively View Show abstractThe design and optimization process of ball mill to reduce particle 2021年12月2日 This research work aims to investigate the mechanical alloying of Fe15Co2P3 powder mixture in terms of phases’ formation, microstructural parameters, and magnetic properties as function of milling time Parametric Rietveld refinement method, of the obtained Xray patterns, was performed for qualitative and quantitative phase analysis alongside the Dependence of magnetic properties with
43.jpg)
Effect of HighEnergy Ball Milling on Mechanical Properties of the
two methods: 1) ball milling: Mg and Nb powders were mixed together using high energy ball milling machine The ball milled (BM) mixture powder and composites fabricated with this powder are entitled as BM Mg–Nb powder and composites, and 2) manual mixing: the pure Mg powder was ball milled, and then manually mixed with unmilled Nb particles The2024年10月17日 The content of calcium feldspar and βTCP phases in HBC samples calcined at 1245 °C was higher than owing to the effect of highenergy ball milling, the powder particles gradually hardened, leading to a decrease in The particles of the HBC milled by highenergy ball milling were much smaller than those of the low The effect of highenergy ball milling on enhancing the 2013年12月1日 For instance, Yamamoto et al [1] reported a trapped field of 4 T at 10 K in an in situ sintered bulk MgB 2 and Naito et al [19] observed 46 T at 14 K in a Tidoped bulk MgB 2 High trapped fields in bulk MgB2 prepared by hotpressing of ball 2004年7月29日 In the present study, no stabilizing compound was required to obtain the cubic phase The finegrain powder was milled in a planetary ball mill for up to several hours at different BPMRs (ball to powder mass ratios): 10:1, 20:1, 35:1 and 40:1 During the process of ball milling, the monoclinic phase is gradually transformed to the cubic phasePreparation and microstructure characterization of ball‐milled
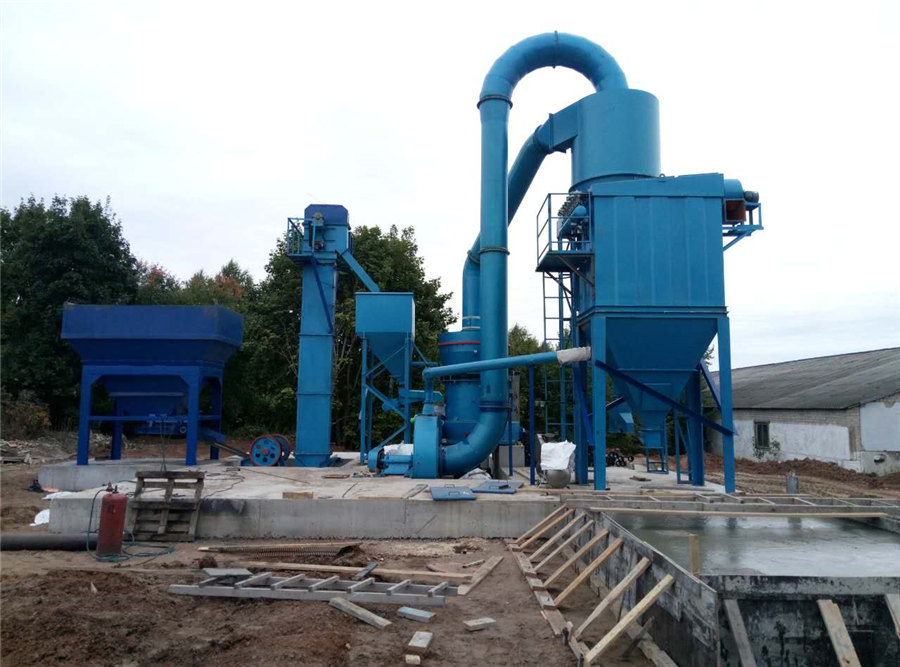
Use of Taguchi method for high energy ball milling of CaCO 3
2022年2月4日 Taguchi’s method was applied to investigate the effect of main high energy ball milling (HEBM) parameters: milling time (MT), ball to powder weight ratio (BPWR), and milling speed (MS) on the CaCO3 crystallite size The settings of HEBM parameters were determined by using the L9 (33) orthogonal experiments array (OA) The asreceived and milled powders 2020年12月1日 The milling environment plays a quite vital role in ball milling Wang et al [17] found that the Ni60Ti40 amorphous powders crystallized and demixed after milling in oxygen gas because of the exothermic oxidation reactionThe grain size of NiZn ferrite nanocrystalline milled in oxygen was larger than that in argon gas according to Abdollah et al [18]Effect of the environment on the morphology of Ni powder during high 2017年5月17日 The surface morphology of unmilled powder reveals the different size and barshaped V2O5 grains, whereas the asmilled (5 20 h) powders significantly affected by high energy ball milling, which Structural Characterization of High Energy Ball Milled 2012年1月1日 This study investigates the effect of incorporating banana stem powder, surface modified with 2% of sodium hypochlorite solution, as a reinforcing filler on the properties of natural rubber latex Excellent elasticity Reinforcement of Prevulcanised Natural Rubber
.jpg)
Ball milling as a mechanochemical technology for fabrication of
2020年9月1日 It showed that the CO 2 adsorption capacities (525 and 492 mg g −1) of BMHC600N (ballmilled, Ndoped hickory chips prepared at 600 °C) and BMHC450N (ballmilled, Ndoped hickory chips prepared at 450 °C) were 122% and 316% more than those of BMHC600 (ballmilled hickory chips prepared at 600 °C) and BMHC450 (ballmilled hickory