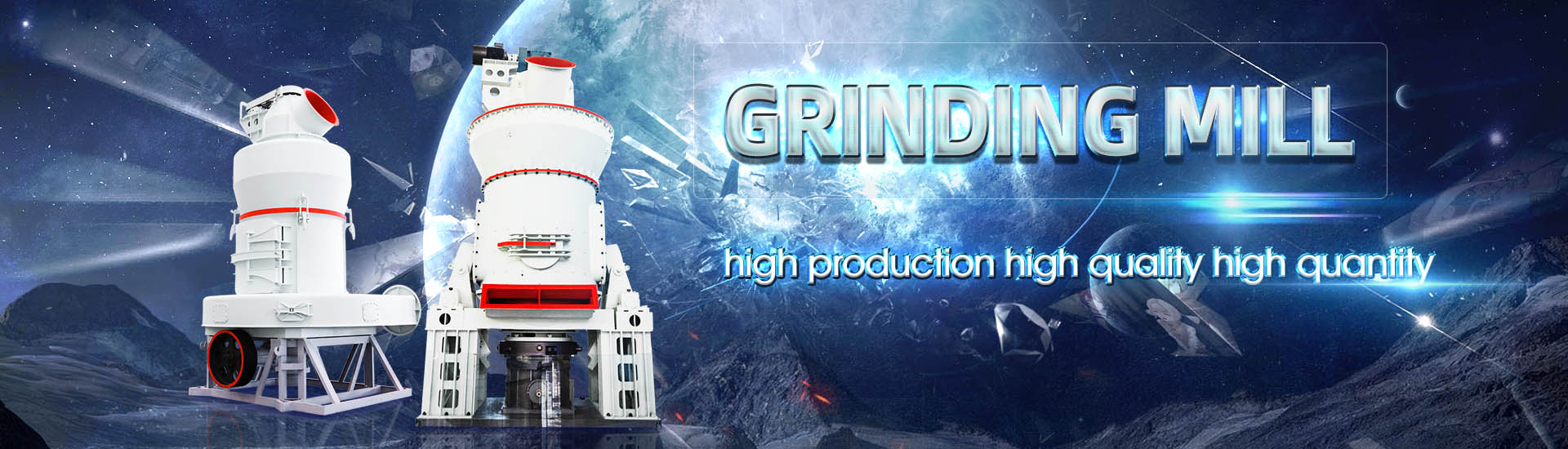
Putian limestone crusher smelting waste slag
.jpg)
Characteristics and environmental aspects of slag: A review
2015年6月1日 The results impact how slag waste is disposed, how slag waste piles are treated, and if and how slag is used as a resource for construction or environmental applications In 2018年2月5日 Piles of steel slag, a solid waste generated from the iron and steel industry, could be seen due to no utility found for the past century Steel slag has now gained much attention Review on the innovative uses of steel slag for waste minimization2019年7月1日 During the blast furnace process limestone (CaCO 3) flux is added, to collect the waste products produced: silica (SiO 2), phosphorus pentoxide (P 2 O 5), calcium sulfide The recycling and reuse of steelmaking slags — A review2016年5月16日 Integrated steel industries are generating huge amounts of steel slag as waste through the blast furnace and Linz–Donawitz (LD) process Presently, these wastes are disposed by dumping in an unplanned manner, Sustainable Approaches for LD Slag Waste
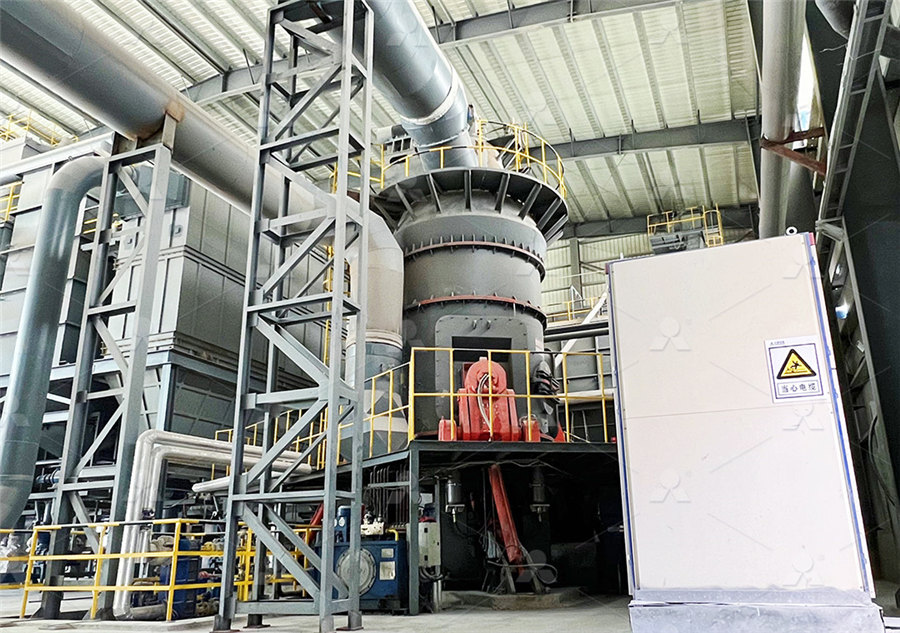
(PDF) Recycling and environmental issues of
2004年1月1日 Using slag as a recycling or renewable resource rather than a waste product has environmental and economic benefits Recycled smelter slags can be used in both in situ and ex situ treatment2019年12月9日 In this paper, the slag granulation and heat recovery options are reviewed and given a critical evaluation, aiming to provide a basis for future directions in slag handling The Granulation and Heat Recovery from Metallurgical Slags2018年9月1日 Based on thermal simulation experiment, SEM analysis and mathematical simulation, limestone dissolution and decomposition mechanism in steelmaking slag were studied The results showed that limestone Limestone dissolution and decomposition in 2019年3月21日 In the present study, waste foundry sand from Ordnance Factory, Medak, India, and blast furnace (BF) steel slag from Tata Steel, Jamshedpur, India, are tested for basic Evaluation of Waste Foundry Sand and Blast Furnace Steel Slag as
.jpg)
Comprehensive utilization of steel slag: A review ScienceDirect
2023年5月15日 To reduce the production of steel slag and increase the resource utilization process of steel slag, the Iron and Steel Institute of Japan (ISIJ) has been researching new 2019年9月3日 limestone, and blast enrichment Ferronickel smelting generates too much slag More than 95% of the charge material to furnaces report to the slag phase, which is regarded as waste(PDF) Nickel Laterite Smelting Processes and Some2023年1月1日 Although considerable effort has been done over a long period of time in the exploitation of industrial waste, ferrochrome slag has received surprisingly less investigationUtilization of steel slag waste as construction material: 2018年2月5日 Piles of steel slag, a solid waste generated from the iron and steel industry, could be seen due to no utility found for the past century Steel slag has now gained much attention because of its new applications The properties of slag greatly influence its use and thus had got varied applications The chemical composition of steel slag varies as the mineral composition Review on the innovative uses of steel slag for waste minimization
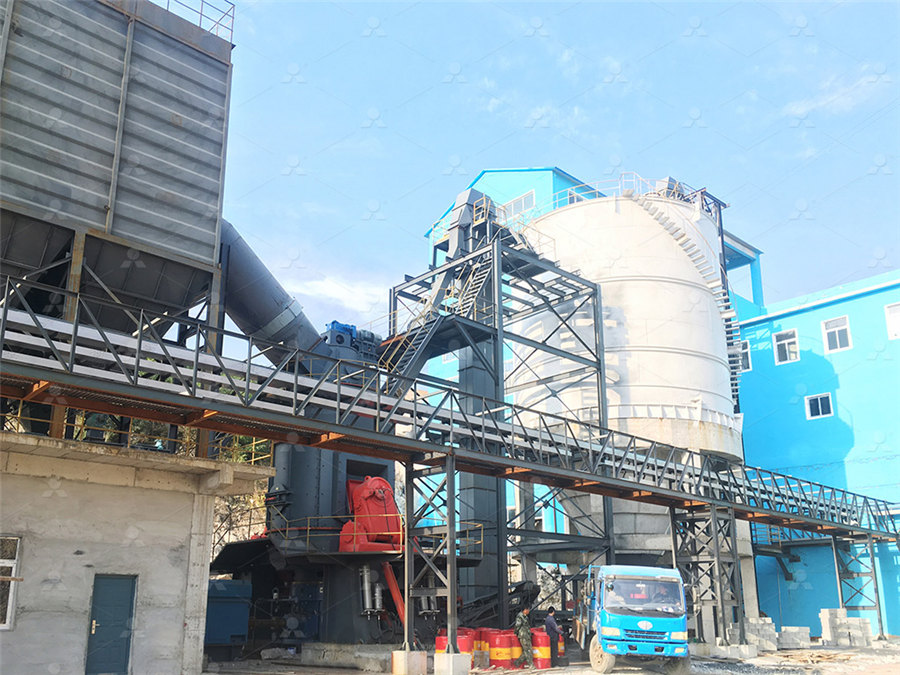
The potential for copper slag waste as a resource for a circular
2022年4月1日 Circular economy is an emerging subject area which has widely been recognised to have immense potential for resource circularity and sustainable development (Velenturf et al, 2019, Lanau and Liu, 2020)It comprises sustainable resource processing strategies that focus on a ‘produce, use and recycle’ paradigm (Nikoloski, 2020)The concept integrates economic 2023年1月15日 Ferrochrome slag (FCS) is a byproduct of ferrochrome industries and is produced during the extraction of ferrochrome from chromite ore The chemical composition of FCS comprises of 27–33% SiO 2, 15–25% Al 2 O 3, 20–35% MgO, and 10–15% ironchromium compoundsThe high chromium content of FCS and the possibility of its leaching into the Ferrochrome slag: A critical review of its properties, environmental 2021年4月30日 As seen from the test results shown in Table 35, the fluorine in magnesium slag that is generated via the Pidgeon process seriously exceeds the standard limitThus, the slag cannot be landfilled directly because it will cause serious consequences Similarly, with reference to HJ/T2992007 “Solid wasteExtraction procedure for Leaching ToxicitySulfuric acid and Magnesium Slag Generated by Reduction Smelting Using Pidgeon ProcessSteelmaking slag, or steel slag, is a byproduct from the production of steel during the conversion of hot metal to crude steel in a basic oxygen furnace, or during the melting of scrap in an EAFThe slag is generated as a melt and is a complex solution of silicates and oxides that solidify upon cooling 11 Depending on the specific steel production process, three different types of steel Steelmaking Slag an overview ScienceDirect Topics
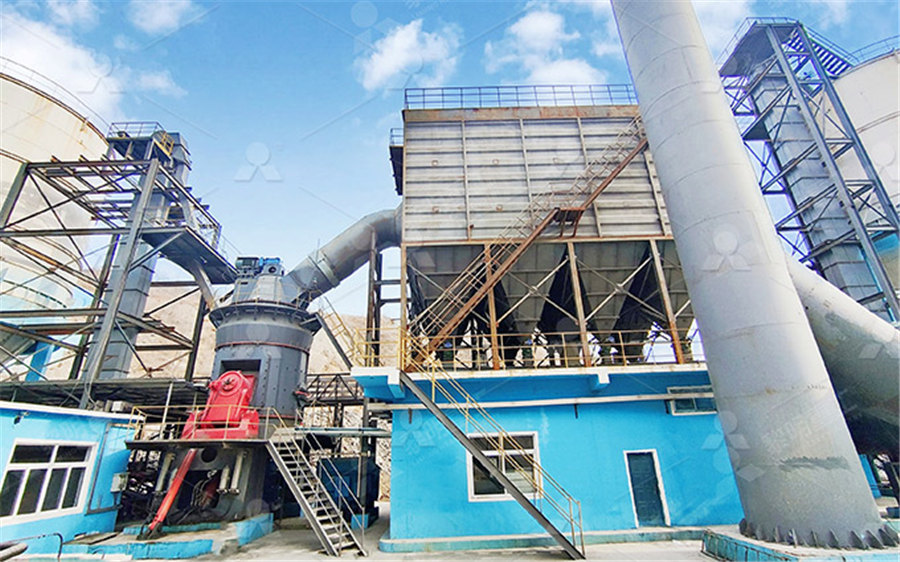
Mineralogy of Metallurgical Slags SpringerLink
2023年3月16日 The term “slag” is used for different materials which result from solidification of a meltSometimes it refers to pyroclastic rocks [], sometimes to ashes, eg from waste incineration, which have undergone sintering due to partial melting [], but mostly for pyrometallurgical residues which result from the reaction of slagforming agents with gangue or impurities in the metal in 2022年2月26日 Blast furnace slag can be processed into the following materials by various processes In China, blast furnace slag is usually processed into water slag, slag gravel, expanded slag and slag beadsWater slag is the process of putting the hotmelt blast furnace slag into water for rapid cooling, which mainly includes slag pool water quenching or furnace front What is Blast Furnace Slag and How to Process It?2016年1月1日 However, the process is only effective for recovering metallic copper and sulphide minerals, and cobalt remains in the slag or flotation tailings and eventually gets disposed of in waste dumps Recovery of copper from smelting slag by sulphation2024年7月5日 Using smelting technology to recover metals from slag is economically justified if the value of recovered metals exceeds a certain threshold per ton of slag treated (Mitrašinović Wolf, 2015) Various studies have shown that recovering metals from copper slag is economically feasible, with high iron recovery percentages and potential economic benefitsCopper Slag as a Source of Iron: An Overview SpringerLink
.jpg)
Resource Utilization of Copper Slag with a Focus on Springer
2024年2月7日 Reduction The reduction process for copper slag is typically followed by magnetic separation []Depending on the temperature and intensity of reduction, it can be classified as direct reduction, deep reduction, and smelting reduction []Commonly used reducing agents include coke, biomass carbon, and natural gas [31, 32]The reduction process converts 2022年3月31日 Inordinate levels of heavy metals in water sources have long been a matter of concern, posing serious environmental and public health risks Adsorption, on the other hand, is a viable technique for removing heavy metals from water due to its high efficiency, low cost, and ease of operation Blast furnace slag (BFS) is considered a cheap sorbent for the get rid of From waste to waste: iron blast furnace slag for heavy metal ions 2023年5月14日 Reusing slag and heat waste from hot slag contributes to green economy Using appropriate mixing composition, BFS and limestone mixture can be used for green cement production This works explores the potential to convert slag waste into cement clinker using heat recovered from blast furnace of iron productionBlast Furnace Slag Cement Clinker Production Using Limestone Steel Slag Processing line adopts jaw crusher for primary crushing, and uses hydraulic cone crusher for secondary and tertiary crushing, offering high crushing efficiency, low wear, energy saving and environmental protection, it has the features of high automation, low operation cost and reasonable allocation of equipmentSteel Slag Processing Gongyi Jingying Machinery
.jpg)
Utilization and detoxification of gypsum sludge by replacing limestone
2023年5月26日 Gypsum sludge refers to a hazardous solid waste produced by the nonferrous smelting industry, and its disposal and utilization are environmentally challenging To investigate the feasibility of replacing limestone with gypsum sludge for smelting slagging, the effect of gypsum sludge and smelting conditions on high lead slag reduction smelting was studied 2021年8月4日 Iron blast furnaces (BF) generate approximately 025 to 030 t of slag per t of crude iron for typical ore grades, with higher amounts generated for low ore grades (up to 10 to 12 t of slag per t of crude iron) 1 Steel furnaces commonly produce approximately 02 t of slag per t of steel, with some being returned to the furnace to recover entrained metal 1 Based on Introduction: Metallurgical Slags – Environmental Liability or 2020年9月24日 Ladle furnaces at Evraz Nizhnii Tagil Iron and Steel Works OJSC produce over 90,000 metric tons of slag per year As this slag cools, it turns into a finegrained powder; if the powder cannot be sold, it is temporarily stored until it can be disposed of [1] We have considered producing easily used flux sinter from the slag generated during ladle processing of steel LadleFurnaceSlag Reprocessing at Evraz Nizhnii Tagil Iron and 2023年2月22日 Sulfidation treatment of copper smelting slag In the sulfidation experiment, the particle size of the synthesized slag was controlled below 80 mesh (178 µm)The mixture of CaSO 4 and anthracite was pelletized at a pressure of 10 MPa in a Ø 4 mm pressing tool, and the weight of every pellet was roughly controlled to be 004 g Then the smelting slag and CaSO 4 The Phase Transition and Element Distribution of Copper Smelting Slag
.jpg)
Advances in recovery of valuable metals and waste heat from copper slag
2022年10月1日 Copper smelting slag usually contains 1–6 wt% copper, which can be recovered by pyrometallurgical and flotation processes However, the tailing slags still consist of 03–07 wt% Cu and 35 2020年10月16日 In view of the nonrenewable reductant resources and carbon neutralization in the process of copper slag cleaning in an electric furnace, this study proposed to use waste cooking oil as reductant to replace fossil energy Combined with the phase equilibrium theory and experimental results, the harm of excessive magnetite in the copper smelting slag to the Copper Smelting Slag Cleaning in an Electric Furnace by Using Waste 2017年12月8日 Scientific Reports CO2 Mineralization and Utilization using Steel Slag for Establishing a WastetoResource Supply Chain Skip to main content Thank you for visiting natureCO2 Mineralization and Utilization using Steel Slag 2022年9月25日 Iron in CSS mainly exists in the form of complex iron oxides such as iron olivine rather than magnetite or hematite, which is difficult to be recovered efficiently by traditional beneficiation methods (Li et al, 2021)In order to separate iron from CSS, it is necessary to convert the complex iron oxide into metal iron or ferric oxide, and then recover it through Extraction and separation of copper and iron from copper smelting slag

Utilization and detoxification of gypsum sludge by replacing limestone
reductions smelting of high lead slag Herein, toxicity leaching experiment of sulfuric acid and nitric acid method was used to evaluate the safety of the cosmelting slag to provide a basis for the cosmelting of high lead slag with gypsum sludge 2 Experimental 21 Materials and reagents In this study, high lead slag as the experimental2022年5月11日 Concrete is a composite material widely used in construction Waste slag smelting (pyrometallurgical) (steel slag (SS)) is a molten liquid melt of silicates and oxides created as a byproduct of steel production It is a complex solution of silicates and oxides Steel slag recovery conserves natural resources and frees up landfill space Steel slag has been used in Electrical conductivity, microstructures, chemical compositions, 2017年1月1日 The mineral composition of slags from the refining process is varied and the most common phase constituents are oxides and hydroxides (zincite ZnO, wustite FeO, hematite Fe2O3, goethite FeO(OH Slags of the Imperial Smelting Process for Zn and Pb Productionbecause when it ends up in the slag it can lead to failure of the TCLP Barium produces a deep green flame over the slag and matte, a stony appearance, and a large amount of matte Too much alkaline earths or too much zinc can “freeze” a blast furnace [2] A low silica highlime slag is a dangerous sign that the furnace is about to freezeA REVIEW OF SLAG CHEMISTRY IN LEAD RECYCLING
.jpg)
Steel Slag–Red MudBased Multisolid Waste Pavement Base
2022年1月21日 Steel slag (SS) and red mud (RM) are hazardous solid wastes that require disposal In this work, SS–RMbased multisolid waste composite pavement base material (PBM) was proposed based on different Ca/(Si + Al) ratios Its performance, structure and toxicity leaching have been studied The microstructure was characterized by XRD, SEMEDS, 29Si 2020年6月3日 Introduction Smelting slag is a typical hazardous waste generated in the smelting and metallurgy industry 1, 2Slag contains high concentrations of heavy metals, such as Cu, Zn, Cr and Ni, which are harmful if released into the environment 3In China, smelting slag is disposed of as an environmental priority pollutant, wherein the slag is generally stabilized with cement Highpurity recycling of hematite and Zn/Cu mixture from waste smelting 2019年12月9日 Metallurgical slags are produced at a massive rate of over 750 Mt/year, and carry a thermal energy equivalent to 40 Mt/year of coal The potential mineral and thermal energy values of slags are in the order of $22 b and $3–6 b per year Such attractive figures, together with tightening legislation on disposal of slag and the carbon footprint associated with the loss Granulation and Heat Recovery from Metallurgical Slags2003年3月1日 Up to now, the main methods of using steel slag were used as sinter material, hot metal dephosphorizing agent, waste water treatment materials, reclamation of waste steel, concrete admixtures, CO2 Comparison of properties of steel slag and crushed limestone aggregate
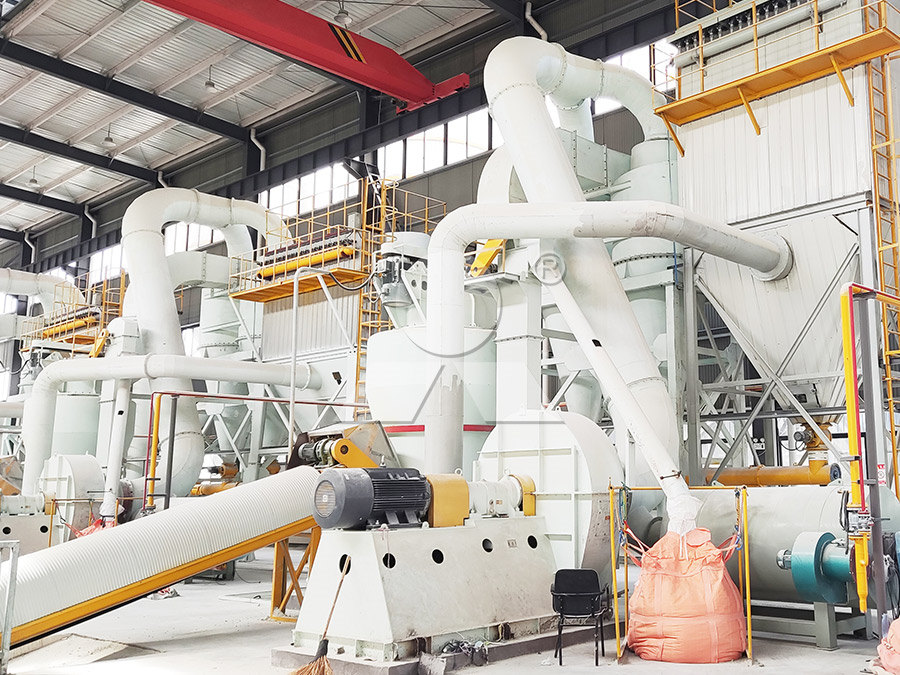
Use of waste ferrochromium slag as aggregate in concrete
2020年8月2日 Large amount of slag is obtained during the production of ferrochromium This byproduct has properties comparable to natural aggregates However, almost all of the ferrochromium slag is landfilled The main objective of this study was to investigate the effects of ferrochromium slag aggregate on the mechanical properties and permeability of concrete For 2022年4月4日 Slag analyses from archaeological iron smelting sites are common Rigorous analyses of iron and slag from successful experimental smelting, however, are still rare Furthermore, thorough analyses from a series of smelts, and of the slag produced in different phases of the smelt, are exceedingly rare The present study investigates the effect of an iron By the hand of the smelter: tracing the impact of decisionmaking 2017年2月8日 Materials The smelting slag used in this study was obtained from a copper plant in China Mineralogical analysis, performed using scanning electron microscope (SEM) and energy dispersive Xray spectroscope (EDS), polarizing microscope and Xray diffraction (XRD), indicated that fayalite (Fe 2 SiO 4) and magnetite (Fe 3 O 4) phases were major components The Recovery of Copper from Smelting Slag by Flotation Processcessing of manmade raw materials such as metallurgical slag Metallurgical slag is a major byproduct of ferrous metals production, making up approximately 70–85% of all castiron and steel smelting waste [2] Slag has an iron content of 25–30%, with some in bead form (11–15%) Slag recycling is a requisite for wastefree operLADLEFURNACESLAG REPROCESSING AT EVRAZ NIZHNII TAGIL
.jpg)
Limestone impact on properties, microstructure and CO
2024年10月10日 Utilizing industrial and urban solid wastes is crucial for developing lowcarbon cements This study proposes a novel method to integrate recycled glass and blast furnace slag (BFS) into alkaliactivated cements It also investigates the influence of pulverized limestone (LSP), as a readily available costefficient partial replacement for BFS The activators were 2021年5月27日 Blast Oxygen Furnace (BOF) slag represents one of the largest waste fractions from steelmaking Therefore, slag valorisation technologies are of high importance regarding the use of slag as a secondary resource, both in the steel sector and in other sectors, such as the construction or cement industries The main issue regarding the use of BOF slag is its Comprehensive Analysis of Steel Slag as Aggregate for Road2023年5月26日 Gypsum sludge refers to a hazardous solid waste produced by the nonferrous smelting industry, and its disposal and utilization are environmentally challengingUtilization and detoxification of gypsum sludge by replacing limestone 2009年2月1日 Smelting activity by its very nature produces large amounts of metalbearing waste, often called metallurgical slag(s) In the past, industry used to dispose of these waste products at dumping The bioleaching feasibility for Pb/Zn smelting slag and
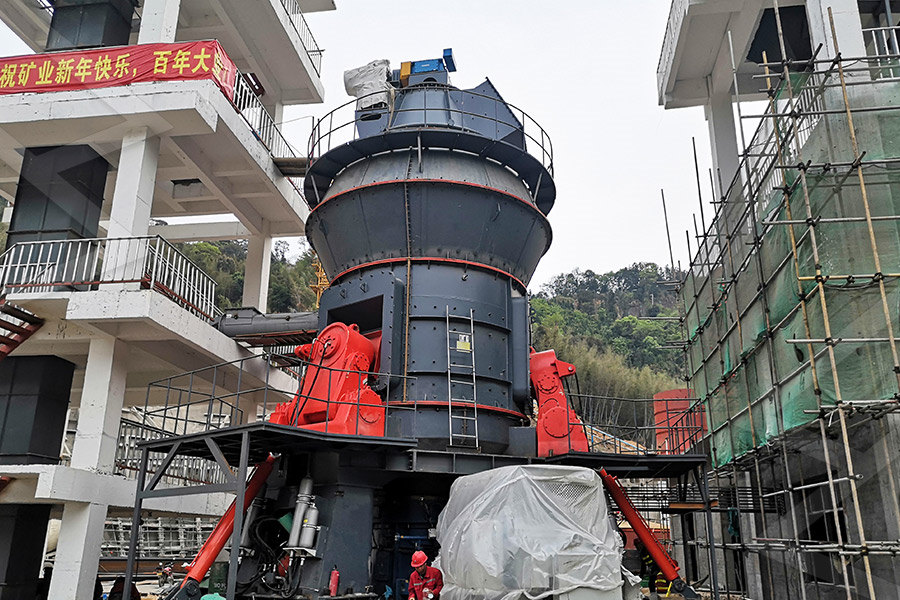
Innovation and performance of lead smelting slagbased multi
2024年1月12日 LSS is a byproduct resulting from the smelting process of metallic lead, which involves hightemperature melt quenching in water, similar to other materials such as fly ash [9], steel slag [10], and GGBFS [11]The material under consideration comprises a certain quantity of amorphous calciumaluminumsilicate glassy phase, which exhibits cementitious behavior