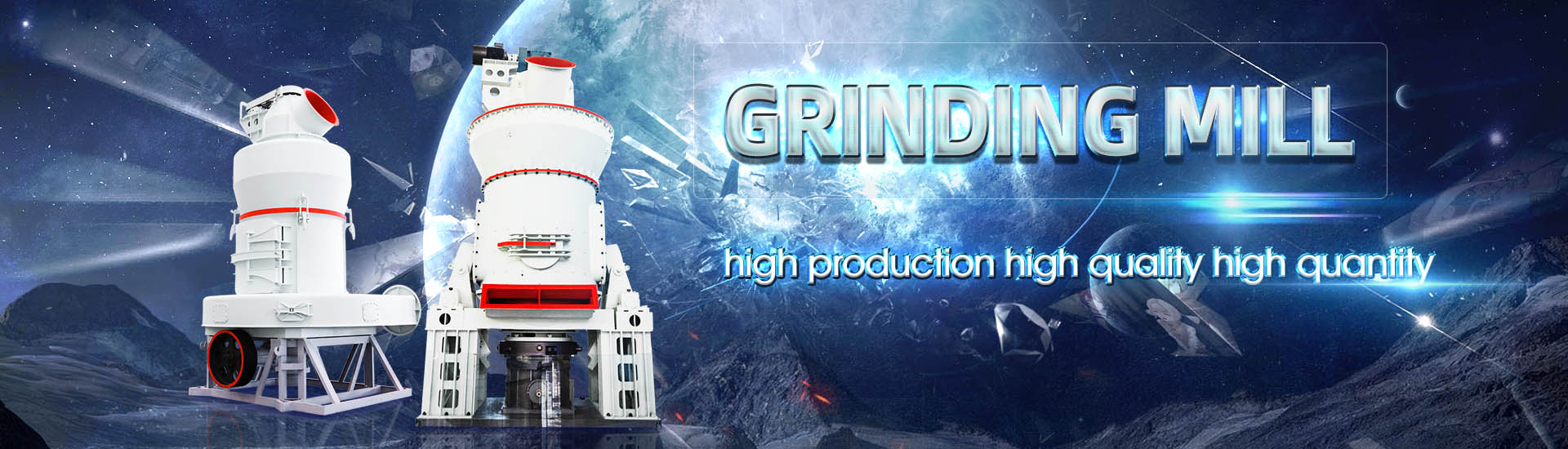
Cement grinding system diagram
.jpg)
CEMENT GRINDING SYSTEMS INFINITY FOR CEMENT EQUIPMENT
2017年4月21日 The common cement grinding systems are summarized in Figure 1 and can be divided into three main groups: Tube Mill Only All grinding work is done in the tube mill and The paper analyzes key findings and proposes a plan–do–check–act (PDCA) framework for I40 implementation based on a system thinking approach to guide cement companies to strategically Sankey diagram of cement grinding systemIn order to realize the target tracking control of cement strength, a selflearning fuzzy predictive control algorithm is proposed to calculate the adjustment variables of cement grindingA schematic of a closedloop cement grinding control Closed circuit grinding system Based on a dynamical model of the grinding process in closed circuit mills, efficient efforts have been made to optimize PID controllers of cement milling TheClosed circuit grinding system Download Scientific
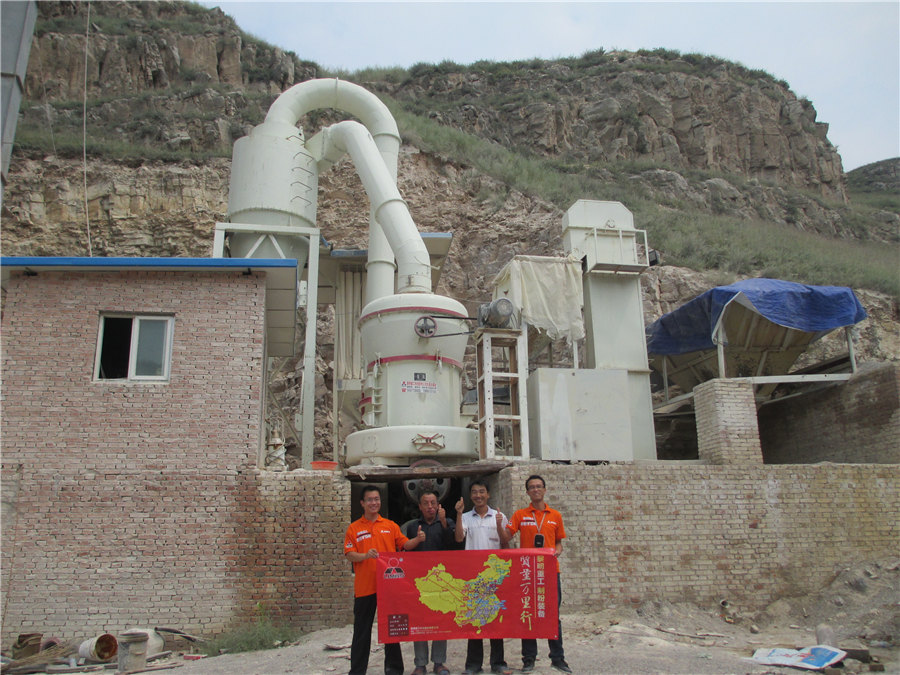
“Holderbank” Cement Seminar , 2000 HOLDERBANK Internet
The requirements on a cement grinding system are manifold and a profound investigation and valuation of all criteria is necessary in order to find the appropriate solution (technically and Closedcircuit Grinding System The closedcircuit grinding system of the ball mill is shown as follows: materials mixed in a certain proportion will firstly enter the cement ball mill for grinding and then be sent to the powder concentrator by Ball Mill In Cement Plant Cement Ball Mill AGICO Abstract Based on a dynamical model of the grinding process in closed circuit mills, efficient efforts have been made to optimize PID controllers of cement milling The process simulation OPTIMIZING THE CONTROL SYSTEM OF CEMENT MILLING: An evaluation of the grinding system and operation includes meaningful and critical inspection of all equipment, components and the process parameters by experts PEC Consulting can help OPTIMIZATION OF CEMENT GRINDING OPERATION IN BALL MILLS
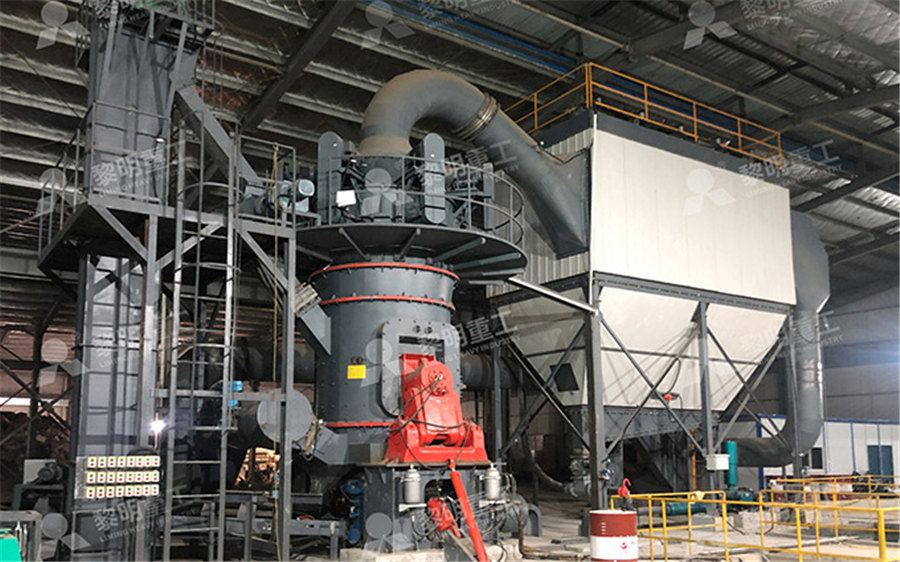
BALL MILLS Ball mill optimisation Holzinger Consulting
Ball mills and grinding tools Cement ball mills are typically twochamber mills (Figure 2), where the first chamber has larger media with lifting liners installed, providing the coarse grinding Closed circuit grinding system The main purpose of the present article is to develop mathematical models predicting cement strength at 28 days based on early strength as well as onClosed circuit grinding system Download Scientific Download scientific diagram Closed circuit grinding system from publication: Dynamic behavior of closed grinding systems and effective PID parameterization The object of the present study is Closed circuit grinding system Download Scientific DiagramProcess Technology Cement Grinding Systems 1 OVERVIEW GRINDING SYSTEMS The common cement grinding systems are summarized in Figure 1 and can be divided up into three main groups: Tube Mill only All grinding work is done in the tube mill and the setup is: @ Tube mill in open circuit @ Tube mill in closed circuit with“Holderbank” Cement Seminar , 2000 HOLDERBANK Internet

BALL MILLS Ball mill optimisation Holzinger Consulting
As grinding accounts for a sizeable share in a cement plant’s power consumption, optimisation of grinding equipment such as ball mills can provide significant cost and CO 2 emission benefits to the cement producer n by Thomas Holzinger, Holzinger Consulting, Switzerland BALL MILLS 1 FEBRUARY 2021 INTERNATIONAL CEMENT REVIEW TThe cement pregrinding system The most noticeable feature of the roller press cement pregrinding system is that the fine material power ground at the middle part of the roller will be sent to the ball mill for further grinding The cement grinding process in this system is rather simple with less equipment requiredBall Mill Roller Press for Cement Grinding ProcessDownload scientific diagram Flow chart of the grinding and blending process from publication: Effective Optimization of the Control System for the Cement Raw Meal Mixing Process: I PID Tuning Flow chart of the grinding and blending processDownload scientific diagram Closed circuit grinding system from publication: Prediction of cement strength: analysis and implementation in process quality control The main purpose of the Closed circuit grinding system Download Scientific Diagram
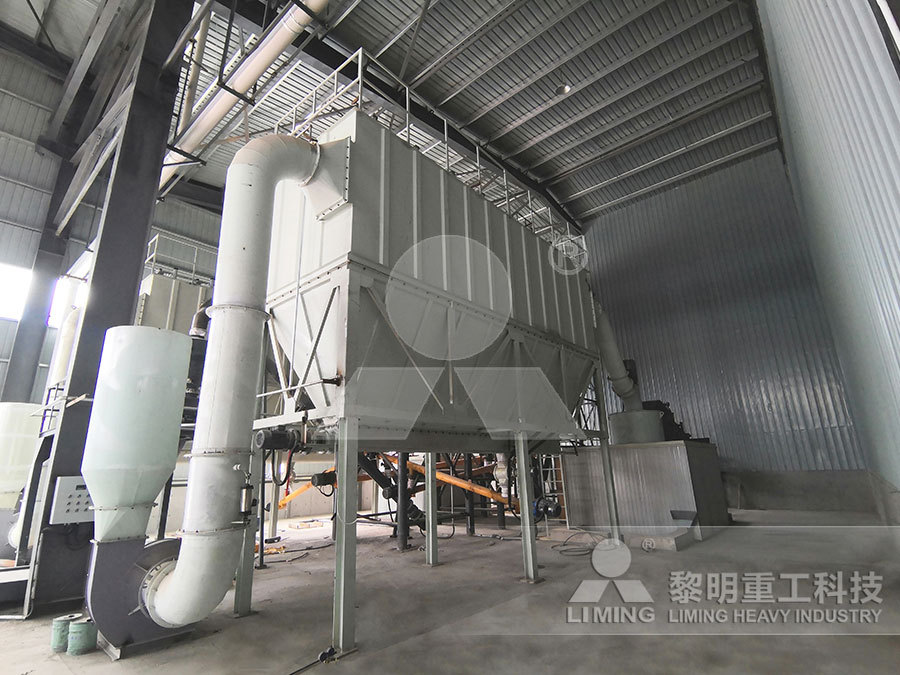
116 Portland Cement Manufacturing US EPA
1971年8月17日 States The balance of domestic cement production is primarily masonry cement Both of these materials are produced in portland cement manufacturing plants A diagram of the process, which encompasses production of both portland and masonry cement, is shown in Figure 1161 As shownIn Germany, the following grinding aids are employed in the grinding of finished cements: Amine acetate Ethylene glycol Propylene glycol Grinding with propylene glycol generates approxi mately 800 cm2/gram cement more surface than grinding without Finish grinding INFINITY FOR CEMENT EQUIPMENT2023年10月19日 Therefore, efficient grinding techniques and technologies are employed to minimize energy use and reduce production costs, contributing to the sustainability of the cement industry Types of Clinker Grinding Techniques used in cement manufacturing process Clinker grinders are an important part of the cement manufacturing processClinker Grinding Techniques in Cement Manufacturing JM Today, cement producers have the option of using a wide variety of different systems for cement grinding A complete list of all available options would undoubtedly include traditional ball mill systems, highpressure grinding rollers in all types of design and their various combinations with ball mills and, of course, VRM vertical roller millsAn Introduction to Clinker Grinding and Cement Storage
.jpg)
OK™ Raw and Cement Mill
Our bestinclass OK™ Mill is a globally successful vertical roller mill solution for grinding raw material, cement and slag Its cuttingedge design features consistently deliver the highest quality products with the greatest efficiency It vertical roller grinding mills for grinding: • Coal • Cement raw material • Clinker / granulated slag • Industrial minerals, and • Ores grinding systems and to implement solutions such as LMmaster RelauchLMmaster 2 250814 11:47 3 The “Stand Alone” real PROCESS OPTIMISATION FOR LOESCHE GRINDING PLANTSThe largest planetary gears for ball mill drives in the cement industry supplied at this writing by the Maag Gear Wheel Co, have a transfer capacity of 8 MW Since 1967 to 1982, about 70 planetary gears for central drive for the cement Mill drives INFINITY FOR CEMENT EQUIPMENTTo Download this post + all manuals and books and Excel sheets and all notes I collected over my 23 years of experience in Cement industry click here now INTRODUCTION Comminution is a major unit operation in a cement plant, accounting for about 50 75 % of the total plant energy consumption Fine grinding in general is extremely inefficientProcess Training Ball Mill INFINITY FOR CEMENT EQUIPMENT
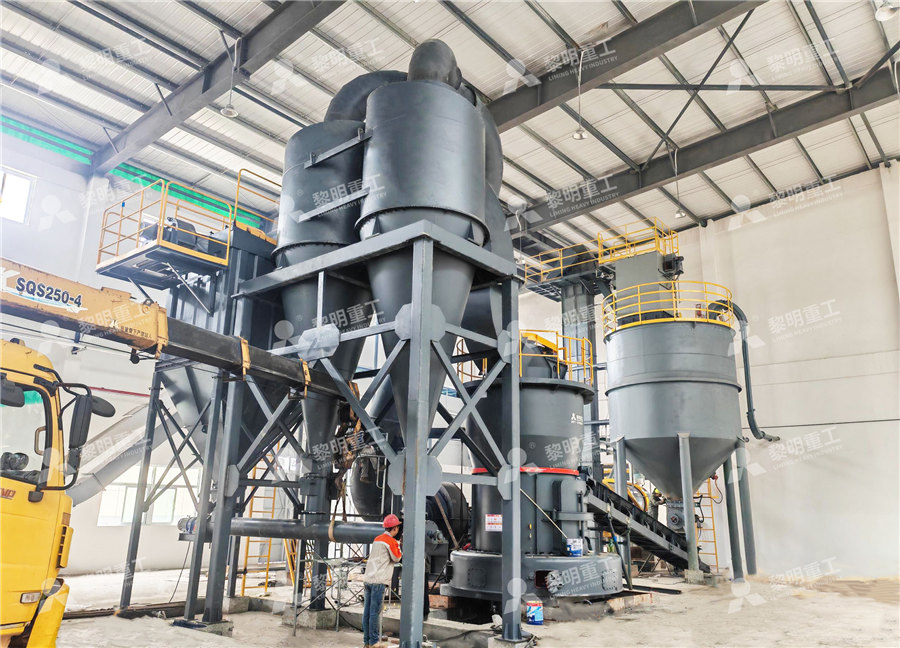
PROCESS ENGINEERING FOR THE CEMENT LIME INDUSTRIES
GRINDING SYSTEMS) IN ENGINEERING, WE OFFER KEY DISCIPLINES FOR PLANT DESIGN PROCESS CALCULATIONS AND FLOW DIAGRAMS PROCESS SELECTION AND EQUIPMENT SIZING St Mary´s Cement Water System – Plant Layout info@saxuming saxumus saxuming PROJECTSDownload scientific diagram The cement raw material blending process and its control system from publication: Modeling and Optimization of Cement Raw Materials Blending Process This paper The cement raw material blending process and its control system Grinding: the material is ground between rollers and grinding table while passing from the center of the table to the nozzle ring The commnation method belongs to the most efficient grinding processes applied in the cement manufacturing Separation: the ground and dried material is lifted up with the drying gasesCement Manufacturing Process INFINITY FOR CEMENT EQUIPMENT2024年11月23日 Cement Extraction, Processing, Manufacturing: Raw materials employed in the manufacture of cement are extracted by quarrying in the case of hard rocks such as limestones, slates, and some shales, with the aid of blasting when necessary Some deposits are mined by underground methods Softer rocks such as chalk and clay can be dug directly by Cement Extraction, Processing, Manufacturing Britannica
.jpg)
EVERY COMPONENT OF BALL MILL DETAILED EXPLAINED INFINITY FOR CEMENT
The grinding is not any more done by balls against material but by material against material SOLUTION Adapted mill cooling, playing with:Clinker temperatureMill ventilationWater injection Use of grinding aid (temporary solution because expensive) Water Injection SystemsMonitoring and control of burning and cooling systems Stable clinker burning with maximum combustion effi ciency for energysaving operation of facilities Control of cement grinding systems Stable quality of cement product with cement grinding at maximum effi ciency for energysaving operationMonitoring Control Systems for Cement Plants Fuji Electric GlobalThey come in various sizes and materials such as steel, ceramic, and porcelain The choice of grinding media depends on the material being ground and the desired final product Drive system: The drive system is responsible for The Ultimate Guide to Understanding Ball Mill Download scientific diagram Closed loop for grinding circuit from publication: Control System Architecture for a Cement Mill Based on Fuzzy Logic This paper describes a control system Closed loop for grinding circuit Download Scientific
.jpg)
CEMENT PRODUCTION AND QUALITY CONTROL
CEMENT PRODUCTION AND QUALITY CONTROL A Cement manufacturing Process Source:civilengineeringforumme The whole process of cement manufacturing in Messebo Cement plant which consists of two separate Cement Production lines can be summarized into the following processes ;as can be seen in the process and Quality flow diagram below; 1Download scientific diagram Cement clinker sintering system schematic diagram from publication: Multivariable nonlinear predictive control of a clinker sintering system at different working Cement clinker sintering system schematic diagramDownload scientific diagram Design of clinker grinding system; mill and separator from publication: Radiotracer Investigation of Clinker Grinding Mills for Cement Production at Ghacem Design of clinker grinding system; mill and separator2006年11月1日 Cement production is an energy intensive process Grinding is a highcost operation consuming approximately 60% of the total electrical energy expenditure in a typical cement plant(PDF) Pregrinding technology ResearchGate
.jpg)
Ball Mill In Cement Plant Cement Ball Mill AGICO Cement
Closedcircuit Grinding System The closedcircuit grinding system of the ball mill is shown as follows: materials mixed in a certain proportion will firstly enter the cement ball mill for grinding and then be sent to the powder concentrator by bucket elevator The powder concentrator divides the materials into coarse and fine materials2021年3月9日 In this study the process flow diagram for the cement production was simulated using Aspen HYSYS 88 software to achieve high energy optimization and optimum cement flow rate by varying the flow rate of calcium oxide and silica in the clinker feed Central composite Design (CCD) of Response Surface Methodology was used to design the ten experiments for Simulation and Optimization of an Integrated Process Flow Sheet Early hydraulic cements, such as those of James Parker, James Frost and Joseph Aspdin were relatively soft and readily ground by the primitive technology of the day, using flat millstonesThe emergence of Portland cement in the 1840s made grinding considerably more difficult, because the clinker produced by the kiln is often as hard as the millstone materialCement mill WikipediaPredictive Control of a Closed Grinding Circuit System in Cement Industry Luis I Minchala1;3, Member, IEEE, Youmin Zhang2, Senior Member, IEEE, Luis E GarzaCastan˜on´ 3, Member, IEEE Abstract—This paper presents the development of a nonlinear model predictive controller (NMPC) applied to a closed grinding circuit system in the cement Predictive Control of a Closed Grinding Circuit System in Cement
.jpg)
Grinding in closed circuit INFINITY FOR CEMENT
For fine grinding in open circuit, the F L Smidth Co, developed a grinding system consisting of two tube mills The principle of this grinding system, also called Minipebssystem, is shown in Fig 124 Pregrinding to a fineness of 2500 Land cement grinding The cement grinding and drying system be dovetail of a large array of obsolete incompetent equipment and was completely replaced by a single VRM, it improves the fineness and diminish the maintenance and power consumption [1, 34, 36] Optimization of cement grinding using standard bond grinding calculations basedPROCESS CONTROL FOR CEMENT GRINDING IN VERTICAL Download scientific diagram Stages in cement production flow chart [43] from publication: A review on kiln system modeling The purpose of this study is to evaluate performance cement of Stages in cement production flow chart [43] ResearchGateCement Vertical Mill Diagram Cement Vertical Mill Specifications Model: Grinding Disc Diameter(mm) Grinding Roller Median Diameter(mm) Grinding Roller Quantity: Power(kW) Capacity(t/h) The power consumption of its grinding system is about 20%30% lower than that of the ball mill, Cement Vertical Mill Vertical Grinding Mill Vertical Mill AGICO
.jpg)
The cement grinding process Download Scientific Diagram
Download scientific diagram The cement grinding process from publication: Modeling and Sliding Mode Control for Cement Particle Size Considering the characteristics of large time delay and CHAPTER I: DETAILED DESCRIPTION OF MILL SYSTEMS This discussion deals with detailed description of a raw grinding system of a cement plant The grinding sys tem is concerned with the grinding of limestone, shale or clay, and pyrite or iron ore to produce raw meal A ball mill or a roller mill is employed for this purpose OperaSimulation of raw grinding system of a cement plant CORECement from the mill will be transported by a system comprising air slides and a belt/chain bucket elevator to two storage silos each having a capacity of 5000 MT, and made of reinforced concrete They will be equipped with aeration and extraction systems for EVERYTHING YOU NEED TO KNOW ABOUT ESTABLISHING CEMENT GRINDING PLANT GRINDING CIRCUIT 1SKISHORE SUBRAMANIAM, 2VENKATAESHS, 3RAMKUMAR KANNAN, 4JAYALALITHAS, 5GURU PRASAT 1,2,3,4Sastra University,Thanjavur, 5FLSmidth PvtLtd Abstract The concept of modeling and simulation in a ball mill grinding process have grown exponentially in recent past owing to the competition in the cement industryMODELING AND SIMULATION OF A CLOSED LOOP BALL MILL GRINDING
.jpg)
Process and instrument diagram for the twostage grinding
Download scientific diagram Process and instrument diagram for the twostage grinding process from publication: Modeling and Simulation of Whole Ball Mill Grinding Plant for Integrated Control 2016年10月12日 Closed circuit grinding system See the advantages of closed circuit grinding The method of installing a bowl classifier to overcome the difficulty is shown in Fig 27 This circuit is usually adopted in modern practice, but with a bowl instead of a straight classifier, Closed Circuit Grinding VS Open Circuit Grinding