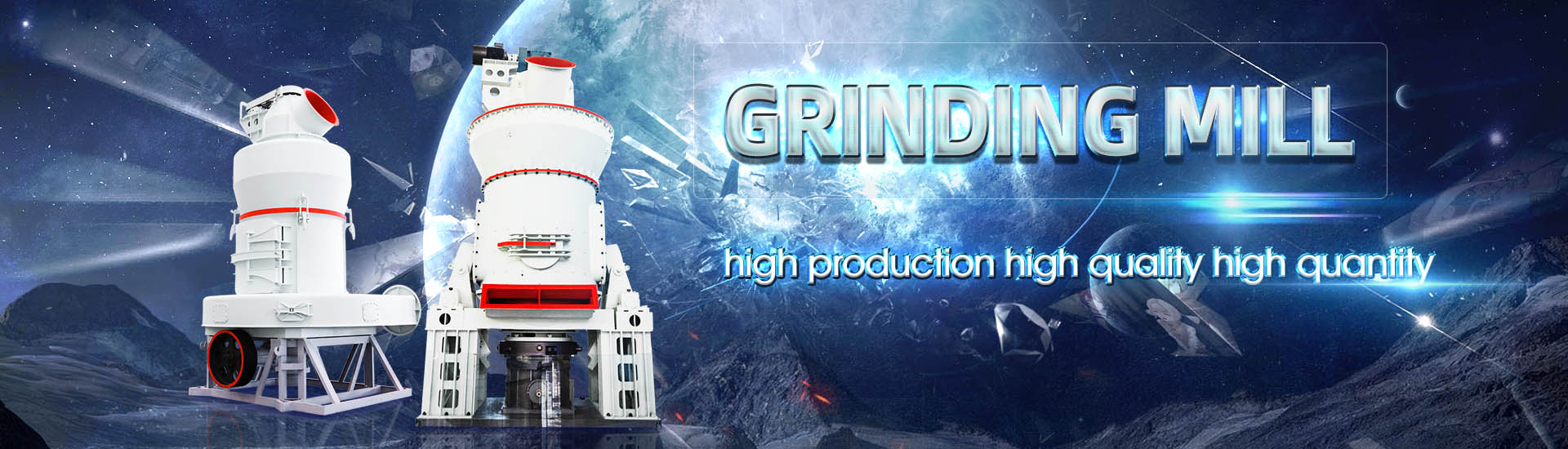
Process design of 250T clinker production line per day
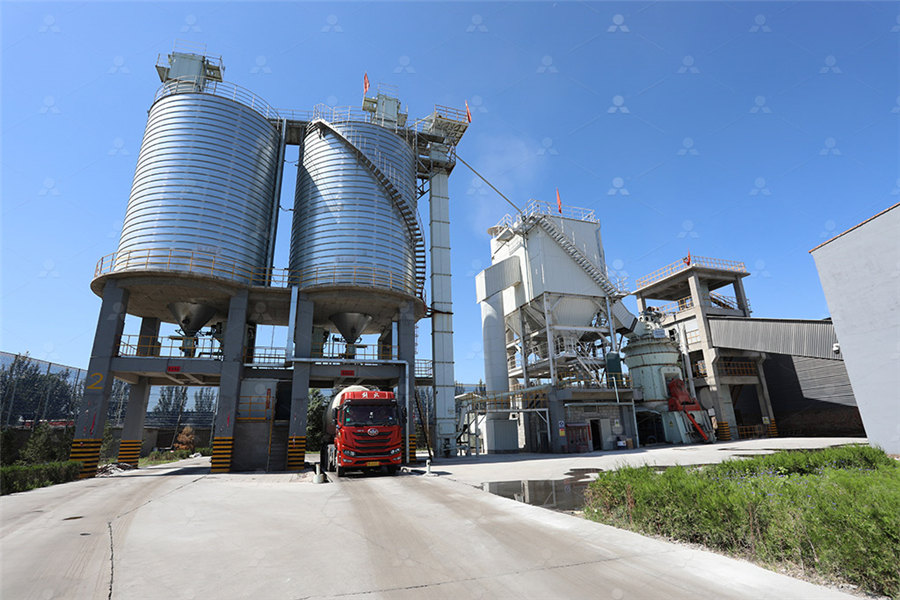
Optimization of the Clinker Production Phase in a Cement Plant
2020年9月9日 In this paper, an APC architecture based on a twolayer linear MPC strategy is designed for the clinker production phase control and optimization The approach described in Clinker production is the most energyintensive stage in cement production, accounting for more than 90% of total industry energy use and virtually all the fuel use The main kiln type used Clinker Production an overview ScienceDirect Topics2024年3月1日 By using these tools to guide the selection of raw materials, process parameters, and production pathways, it is possible to produce sustainable clinkers that meet highquality Toward smart and sustainable cement manufacturing process: • A reference cement clinker production line • Specs for standard process units • Utilities description, cost and climate impact • Extent of capture and CO 2 specs • Economic Process characteristics of clinker and cement production SINTEF
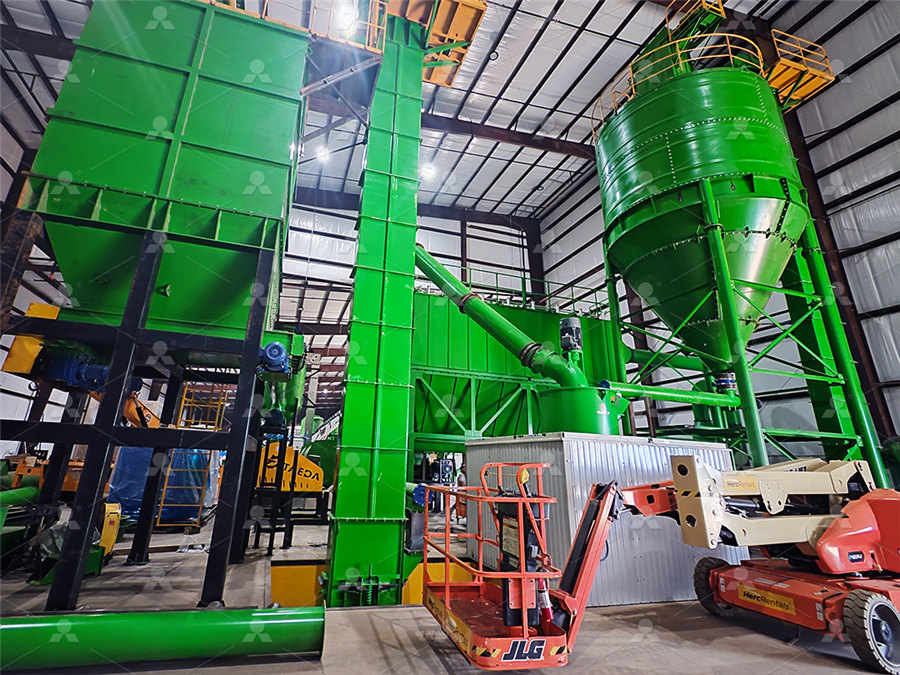
Optimization of the Clinker Production Phase in a Cement Plant
In this paper, an APC architecture based on a twolayer linear MPC strategy is designed for the clinker production phase control and optimization The approach described in [7] is further 2023年10月16日 This study proposes a raw meal proportioning methodology for optimising coprocessing of natural feedstocks with alternative raw materials in clinker production, intending Thermodynamic modelling of cements clinkering process as a tool 2021年8月19日 This paper aims to present efficient efforts to optimize the proportionalintegraldifferential (PID) controller of clinker cooling in grate coolers, which have a fixed grate and at (PDF) Optimizing the Control System of Clinker Cooling: Process 2024年8月1日 The processes involved in clinker production were summarized into five steps: evaporation, clay dehydration, calcination, clinkerization, and cooling Air Circulation : The Efficiency enhancement and cost reduction in cement clinker
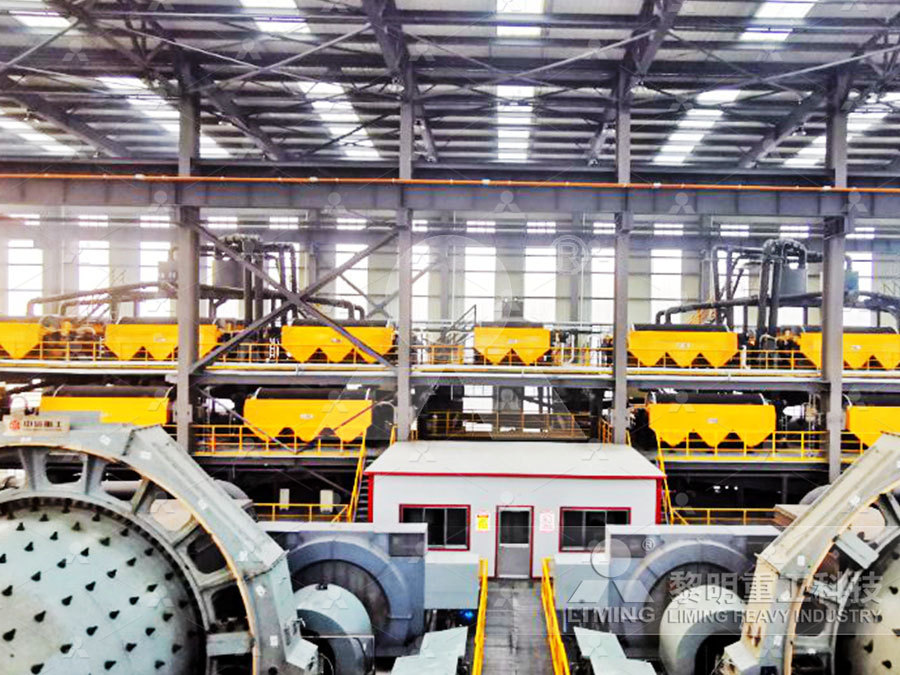
Optimisation and stabilisation of clinker production ResearchGate
2005年12月1日 PDF stanislav chromy, Brno, czech Republic, and pavelMarlrauz, cement plant Republic, describe the optimisation and stabilisation of actual clinker Find, read and cite all 2023年1月7日 During the clinker manufacturing process, large amounts of nitrogen oxides (NO x), sulfur oxides (SO x), particulate matter (PM) and carbon dioxide (CO 2) are emitted in the Emission reduction through process integration and exploration of The impact of coating layers on the clinker production process within a rotary kiln burning both coal and Refuse Derived Fuel (RDF) was investigated in one study [7], showing that a thin coating Clinker formation process in a modern plant rotary kilnThe overall process of conversion from raw meal to clinker being endothermic demands a theoretical heat of about 380420 kcal/kgclinker However, the rest of the specific heat consumption as tabulated above constitutes heat losses from Clinkerization Cement Plant Optimization
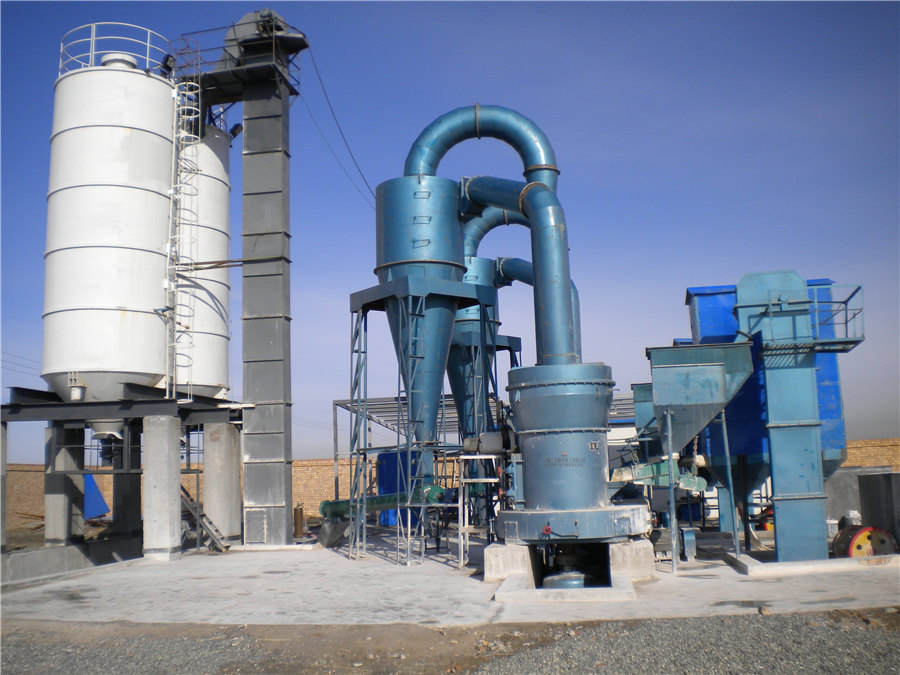
Cement Clinker Manufacturing Process with Reactions
The powdery or granular mixture quickly solidifies into spherical nodules of clinker Cooling and storing The mixture inside the slightly inclined kiln is rapidly cooled from 2000°C to 100°C200°C Thus, the final product, clinker, is produced, and then stored, ready for the production of cementClinker Output Fuel Input Gas Output Raw Meal Input Air Input Fig 1: Simplied Clinker Production Line: preheating Cyclones (P), Calciner (Ca), Rotary Kiln (K), and Cooler (Co) The production of clinker comprises several process equipment: a preheating tower (with a set of cyclones), a calciner, a rotary kiln, and a cooler, see Fig 1A Dynamical Simulation Model of a Cement Clinker Rotary Kiln2024年9月15日 At present, the new dry process is the mainstream technology for cement production lines and consumes only 60 %–74 % of the previous energy consumption [[10], [11], [12]]It is mainly composed of raw meal preparation, clinker calcination and cement grindingOperation optimization of cement clinker production line based 2020年1月9日 In this study, first the function unit and the system boundary were defined, on the basis of which the resource consumption inventory of cement clinker production was compiled, and then, the resource consumption intensity of cement clinker production in China and the resource benefit brought by the utilization of CCS in cement kiln (eg, the relationship between Exergybased resource consumption analysis of cement clinker production
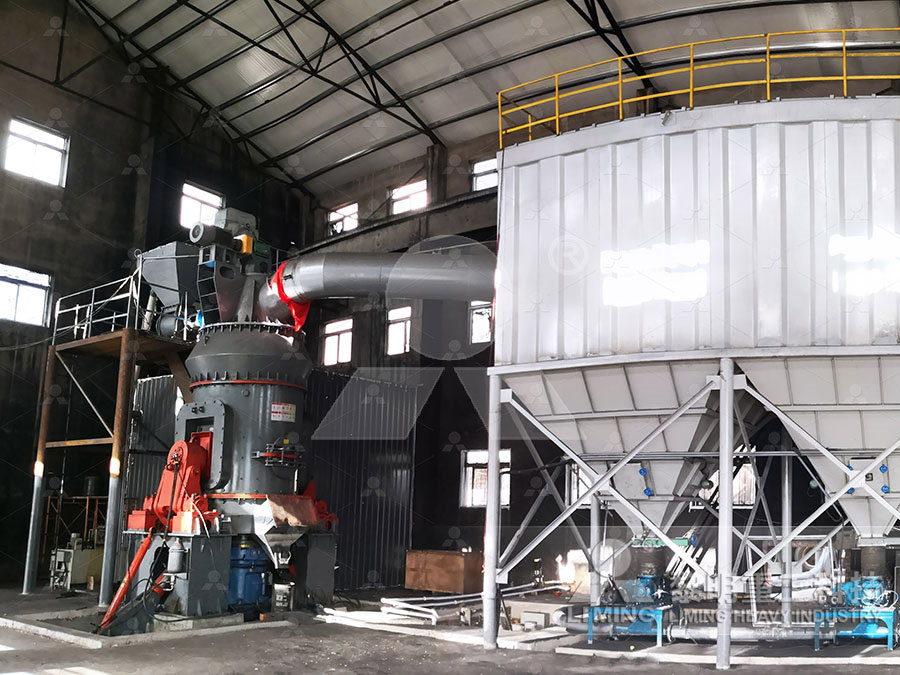
Conceptual design and lifecycle environmental and economic
2024年9月15日 This study provides a comprehensive analysis for lowcarbon cement process design to achieve CO 2 emissions reduction Graphical abstract Download: but the production line is only 1k to 10k t/d and scattered worldwide, The production capacity of the cement process is 4000 tons of clinker per day3000tpd cement production line; 2500TPD new type dry process cement clinker pr; Cement production line with annual output of 1; 1000tpd cement production line; 1500t / d cement production line; Mainly technological process of 1000t/d cement; Mainly technological process of 5000t/d cement; 100,000 Tons/Year Small Concrete Processing Pl3000tpd cement production lineJiangsu Pengfei Group Co,LtdConsidering the clinker production capacity of new line (4100 t clinker per day) and considering the global warning potential (GWP) reduction estimated by the IPCC method, it is possible to System boundaries of the cradletogate for clinker production 2005年12月1日 stanislav chromy, Brno, czech Republic, and pavelMarlrauz, cement plant Republic, describe the optimisation and stabilisation of actual clinker pnase and the adaptable control of its burninoOptimisation and stabilisation of clinker production
.jpg)
Improving the sustainability of cement clinker calcination process
2019年7月1日 While the amount of heat loss through kiln shell for each specific cement clinker production line is not accurately assessed and monitored during the cement clinker production process Due to lack of measuring technique, the heat loss has been mostly estimated by assuming that the shell temperature is constant ( Atmaca and Yumrutaş, 2014a , Engin and J o u r n a l P r e p r o o f in line with the ones reported by Schakel et al (2018) and Cavalett et al (2022), where the authors find that the use of biogenic fuels combined with capture and Kiln fuel mix of the clinker production process under Description: The 2500t / d cement clinker production line adopts a new dry process, with an annual output of 775,000 tons of cement clinker and a total cement output of 105 million tons / yearA cement production line and auxiliary facilities from limestone crushing to cement packaging are constructed Specialties include raw materials, production technology, electrical and 2500TPD new type dry process cement clinker production lineDownload scientific diagram Clinker and cement production process from publication: Specific energy consumption of cement in Thailand According to the 2015 Thai Energy Conservation Plan, the Clinker and cement production process ResearchGate
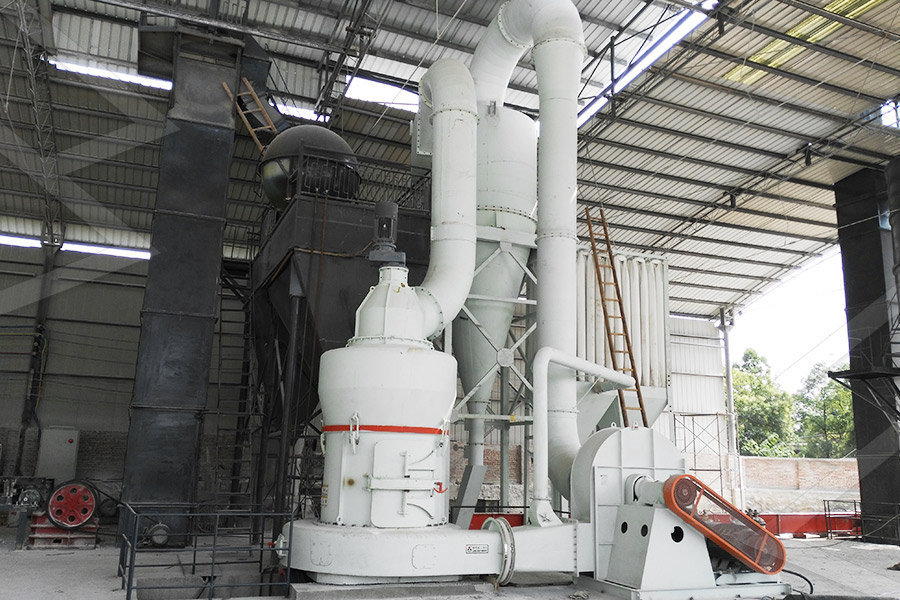
Clinkerization an overview ScienceDirect Topics
The major developments in cement chemistry in general and clinker manufacturing chemistry in particular over three decades from 1964 to 1989 can be perused in [1]More specific manufacture related issues pertaining to raw materials preparation and clinkerization have been dealt with in fair details in [2–7]Notwithstanding the widening knowledge base of materials chemistry from The 2500t / d cement clinker production line adopts a new dry process, with an annual output of 775,000 tons of cement clinker and a total cement output of 105 million tons / year Tel:+86513 Email: Home ; clinker 28 day strength (6) 2500TPD new type dry process cement clinker production lineFor the base case, the optimal cost for clinker production is USD 9021/t clinker while CO2 emissions generated from both calcination of raw materials and fuels combustion is 53168 kg CO2/t Stages of the Portland cement process productionFigure 3: Overview of the clinker production process Waste heat recovery technologies Generally, there are two sources of waste heat available in a clinker production line: i) waste heat recovery from hot gases and ii) radiant heat loss from the kiln surface One of Waste heat recovery from cement production for faecal sludge drying
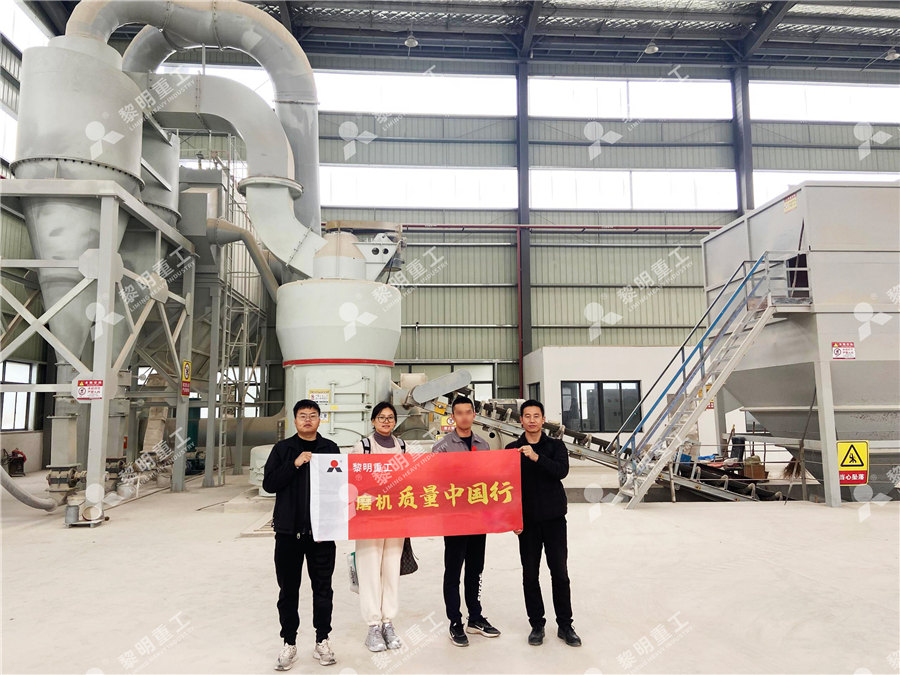
(PDF) Energy and Exergy Analysis of Clinker Cooler in
2018年12月31日 Energy recovery and exergy recovery in a clinker cooler was a major factor in optimizing clinker production and cement grinding process, the running clinker cooler has an energy recovery was 4831 2021年2月24日 Report on the achievement of clinker production quality at XYZ company from 2017 2019 Optimizing the clinker production by using an automation 2018年7月31日 Today any design project would include some of the following provisions which conducts the design and selection of a clinker cooler: low capital cost, optimum cooling rate for good quality of clinker, low clinker outlet temperature, minimum possible impact upon the environment, high heat recovery, low power consumption, low wear and maintenance cost, Development of Cooling Performance of Clinker Cooler Process 2012年1月1日 Energy efficiency measures for clinker production e qual to10000 ton per day preheaters and clinker coolers this allowed the throughput of each kiln line to be increased from 1500 Energy Savings Measures for Clinker Production in Cement Industry
.jpg)
Calculation of the formation process of clinker
2018年4月19日 The found average difference in Heat required for clinker formation between temperature 1338 °C and 1450 °C is 8226 kJ/kgclinker representing 223% of Total heat input are 3686 kJ/kgclinker2020年10月15日 This research focused the role to study the effects and ways to control the chemical composition of clinker for better cement production Cement is a substance produced by grinding a mixture of a Effects and Control of Chemical Composition of Clinker for Step 3: clinker cooling Clinker cooling is the final step in clinker production This process aims to recycle heat, preheat the secondary air, and improve the quality and grindability of the clinker Besides, the rapid cooling of the clinker in this process is convenient for cement storage and transportation Clinker CoolerClinker Production Clinker Manufacturing Cement 2014年1月1日 As a result, the φDC and φP of the production line were increased from 3003% and 6461% to 3069% and 6569%, respectively; the φQY increased from 6170% to 6255%; the clinker output of the Thermal efficiency modelling of the cement clinker manufacturing process
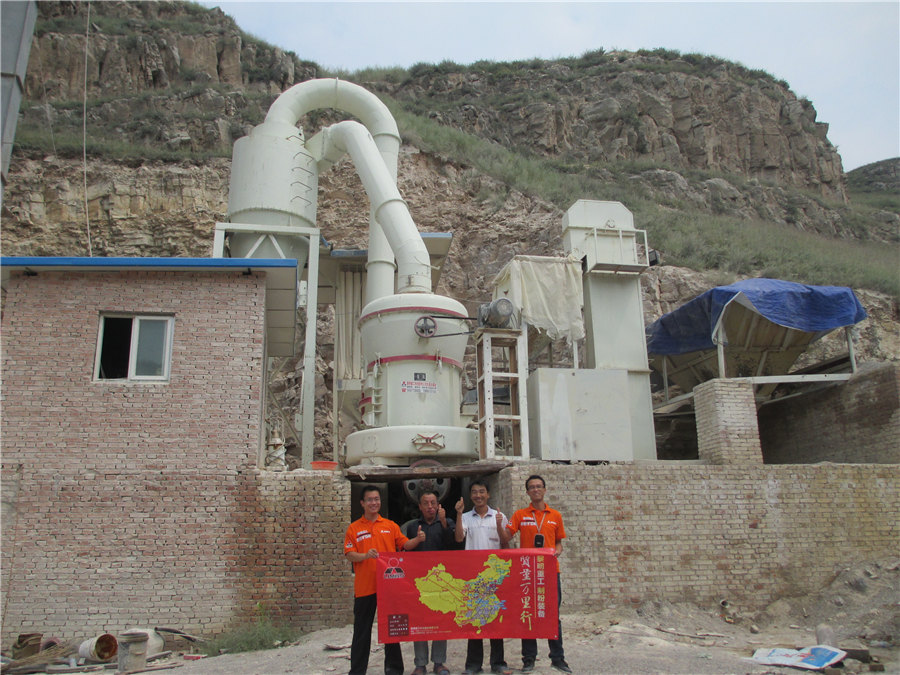
Thermal energy consumption and its conservation for a cement production
2020年6月24日 Previously, the kiln used to be operated for 9,700 tons per day with the consideration of 330 days running It means that it is capable of producing 320 million tons of clinker per annum Further, the kiln throughput has been increased to a value of 11,400 tons per day, to enhance the clinker capacity2020年10月10日 As a result, the φDC and φP of the production line were increased from 3003% and 6461% to 3069% and 6569%, respectively; the φQY increased from 6170% to 6255%; the clinker output of the production line increased from 5799 MT/D to 5968 MT/D; the heat consumption of clinker was reduced from 328698 kJ/kgcl to 325241 kJ/kgclModeling of the Thermal Efficiency of a Whole Cement Clinker Cement production process has been highly energy and cost intensive The cement plant requires 8784 h per year of the total operating hours to produce 640,809 tonnes of clinkerKiln feed and clinker composition Download Table ResearchGateEnergy recovery and exergy recovery in a clinker cooler was a major factor in optimizing clinker production and cement grinding process, the running clinker cooler has an energy recovery was 4831 Crosssectional view of clinker cooling process inside a grate
.jpg)
(PDF) Neural Network Soft Sensor Application in Cement Industry
2011年7月1日 10000 tons of clinker production per day Some of the soft sensors developed here are implemented online at graduate students and industrial process technologists – through the design 2005年6月1日 Energy recovery and exergy recovery in a clinker cooler was a major factor in optimizing clinker production and cement grinding process, the running clinker cooler has an energy recovery was 4831 Heat Exchange Modeling of a Grate Clinker Cooler 2023年1月7日 Thus, for 220 ton/day clinker production, Indian coal requirement is 220 *12/100 ton/day Therefore, total coal conserved is 264 ton/day As per the current study, for one ton of clinker production, 096 kg of NO x gets emitted during the clinker manufacturing processEmission reduction through process integration and exploration 2019年12月1日 The required electrical energy input for calcination in a kiln system producing 1 Mt of clinker per year, is about 85 MW An earlyphase cost estimate was conducted resulting in total annualized Combined calcination and CO2 capture in cement clinker production
G[R.jpg)
Utilization of Biomass as an Alternative Fuel in Cement Industry
2017年9月15日 The utilization of multiple biomass fuels is studied on an industrial production line with a productivity of 6000 tons per day of the clinker production process 250 t/h of clinker 2007年9月18日 The Project is undertaken by EKON, a part of PROKONEKON Group of Companies, as an EPC Contract covering the engineering, procurement, construction (civil, mechanical, electrical and automation works), commissioning and start up of 2500 tons/day a new greenfield clinker burning line, cement additives and cement grinding facilities projectHasanoğlan Cement Factory 2500 Ton/Day Capacity Clinker Production 2024年10月1日 Currently, the hightemperature heat source (550–1450 °C) during the decomposition and sintering process of Portland cement clinker is mainly provided by coal, the standard coal consumption in cement clinker production is between 92 kg/t and 128 kg/t [2, 8], and the average thermal energy intensity is 36GJ/t clinker in 2022, of which approximately Technology verification of Portland cement clinker production 2012年4月1日 Considering the clinker production capacity of new line (4100 t clinker per day) and considering the global warning potential (GWP) reduction estimated by the IPCC method, it is possible to determine a daily GWP reduction of 200 t of CO 2eq was achieved and additionally, if the design goal is achieved at end of 2011 the reduction can be around of 331 t of CO 2eq Journal of Cleaner Production ScienceDirect
.jpg)
Optimizing the Control System of Clinker Cooling: Process
2023年6月14日 𝑎 = = =2024年1月15日 In the conventional cement production process, CO 2 emissions primarily result from the production of clinker, the main component of Portland cement [3]Specifically, two main sources of CO 2 emissions exist: (1) process emissions from the calcination process, where limestone (CaCO 3), a key component in the raw meal for clinker production, decomposes into Decarbonisation pathways of the cement production process via