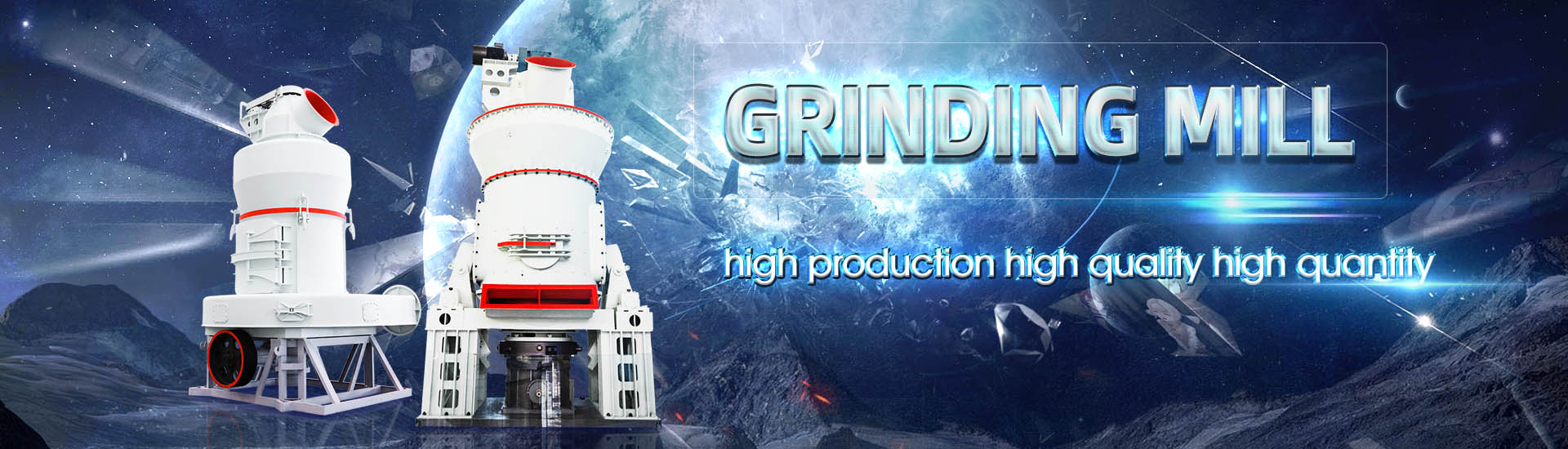
Inertial vertical mill ore mill installation size

The Grinding Efficiency of the Currently Largest Vertimill
The MinasRio regrinding circuit is currently the largest Vertimill installation in the world, consisting of sixteen VTM1500 Vertimills, in closed circuit with hydrocyclones The objective of this study The achievable product size from a VRM is in the range between P80 of 1 mm down to P99 of 20 μm Comminution is achieved by compressive and shear stress on the particle bed; the Vertical Roller Mills used for the comminution of mineral oresEIRICH’s largest TowerMill, the ETM1500, can be mechanically installed within 5 days Comminution, or the process of size reduction, takes place in agitated media mills when the EIRICH TowerMill Vertical agitated media mill2017年4月1日 Simulation of the currently largest vertical mill installation in the world Industrial vertical mill scaleup and simulation using Population Balance Model Breakage parameters Vertical stirred mill scaleup and simulation: Model validation by
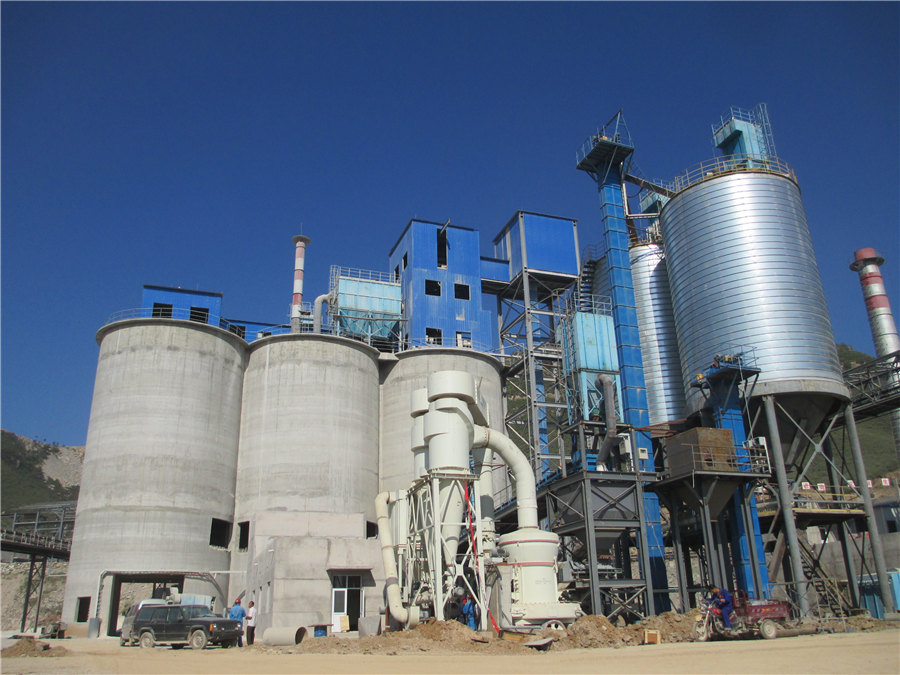
CLUM Series Ultrafine Vertical Roller Mill
3 Double PositionLimiting Technology Makes Operation More Stable In the CLUM series ultrafine vertical roller mill, the contact point between roller shell and millstone liner plate adopts electronic limiting technology and mechanical 2015年3月15日 It was found that the ball mill consumed 5467 kWh/t energy to reduce the F 80 feed size of 7222 lm to P 80 product size of 2754 lm while stirred mill consumed 3245 kWh/t of energy to produce Vertical Agitated Media Mill scaleup and simulation Fresh feed size: 3,000 microns (hard rock ores) 10,000 microns (soft ores eg limestone) n The energy distribution within the vertical mill is constant for any given height and radius TowerMill Installation: Karara Iron Ore Project slurry pump hydrocyclone horizontal ball mill hydrocyclone magnetic separatorEIRICH TowerMill Vertical agitated media mill2019年4月16日 Conference: Applying a Successful Technology from the Cement Industry: Advantages of Grinding Ore in a VerticalRollerMill; At: Antalya, Türkey(PDF) LEARNING FROM OTHER INDUSTRIES; WHY THE VRM
.jpg)
Comparing ball and vertical mills performance: An industrial case study
vertical mill performance and to compare the operational data of the three mills The industrial data was also compared to jar mill tests results, which are monthly conducted in Samarco labs in order to predict the specific energy consumption required by the ore fed to In the present study, size reduction experiments were performed on HighPressure Grinding Rolls (HPGR), ball mill and stirred mill of PGE bearing chromite oreParticle size distributions of the pilot vertical mill circuit feeds VANCOUVER 2015 THE GRINDING EFFICIENCY OF THE CURRENTLY LARGEST VERTIMILL INSTALLATION IN THE WORLD *DB Mazzinghy1, JFC Russo1, J Lichter2, CL Schneider3, J Sepúlveda4, and AVidela5 1 Anglo American Iron Ore Brazil Conceição do Mato Dentro Minas Gerais, Brazil (*Corresponding author: douglasmazzinghy@angloamerican) 2 The Grinding Efficiency of the Currently Largest Vertimill Installation 2014年10月1日 In a test performed in the Loesche test center in Germany, copper slag grinding saved 229% energy in an airswept model and 344% energy in an overflow model [13,14]Copper Ore Grinding in a Mobile Vertical Roller Mill Pilot Plant
.jpg)
RECENT DEVELOPMENTS IN COARSE GRINDING USING VERTICAL
Figure 3: Relationship between feed size (F80) and Bond efficiency factor (Huang et al, 2019) VERTICAL POWER MILL (VPM) – PRINCIPLE OF OPERATION Declining ore grades and more complex ore bodies, as well as waste management and global net zero initiatives, lead to a clear trend for high tonnage yet energy efficient grindingVertical stirred mills are a fine grinding equipment that covers advantages of low rotation speed, high reliability and long life cycle The significant advantages that the vertical stirred mills have over the ball mills are smaller size, less auxiliary equipment required, more simple system and more options of processing methodsVertical Stirred Mill Mineral Processing Equipment CITIC HIC2018年9月17日 The paper describes the development and validation with six different ore samples of a simplified laboratory jar mill test using a 6"×8" jar, which is smaller than the 8"×10" size, the latter DEVELOPMENT OF A LABORATORY TEST TO DESIGN Figure 37 Size analysis for a repeat experiment performed in a vertical mill shown as a function of grinding time for a single 595 +420μm feed size 71 Figure 38 Vertical mill geometry (left) and RockyDEM simulation of the vertical millPREDICTING THE PRODUCT PARTICLE SIZE DISTRIBUTION FROM A VERTICAL

INVESTIGATION ON FLOTATION BEHAVIOR OF A COPPER SULFIDE ORE
2019年8月1日 investigation on flotation behavior of a copper sulfide ore after dry grinding by loesche vertical roller mill August 2019 Conference: 58th Annual Conference of Metallurgists (COM 2019)2014年10月20日 Rio Paracatu regrind circuit Santos Júnior et al (2011) presented some data on the Paracatu Vertical Mill circuit process, as well as its comparison to the plant's conventional ball millRegrind of metallic ores with vertical mills: An overview of the 2018年4月16日 This paper brings together two separate studies, in which the vertical roller mill was used to grind two different precious metal ores, an epithermal gold deposit hosted in quartz vein from Turkey Comparing Vertical Roller Mill Performance on Two Different Precious VTM1500 vertical grinding mill Challenge Replacing the original tertiary ball mills with Metso’s Vertimill VTM1500 vertical grinding mill Solution Introduction of Metso’s Vertimill® VTM1500 vertical grinding mill at Miaogou Iron Mine to achieve Stirred mills Metso
.jpg)
Vertical Roller Mill SBM Ultrafine Powder Technology
Vertical roller mill is an efficient industrial milling equipment, Feed size: 20 mm Output: 120 T/H Product features: High grinding efficiency; Strong drying capacity; Low noises and little dust; 86 Uses of vertical roller mill – in ore field960284D Installation 1 aa Aain n 1 VERTICAL MILL INSTALLATION INSTRUCTIONS Machine RequiReMents Machine footprints and operating dimensions are available in the brochure and the anchoring addendum GeneRal RequiReMents Operating Temperature Range 41°F to 104°F (5 to 40°C) Storage Temperature Range 4°F to 158°F (20 to 70°C)VERTICAL MILL INSTALLATION INSTRUCTIONS Haas AutomationThe samples collected after the test works and size distributions were in the OGP mobile constructed by Loesche for ore grinding The installation of the OGP in a gold processing plant is illustrated in Picture 1 3 (2), 54–63 Reichert, M, 2015 Research of iron ore grinding in a verticalrollermill Miner Eng 73, 109 (PDF) Operational parameters affecting the vertical roller mill Our wear parts for vertical mill grinding circuit are designed to minimize environmental impact through reduced energy consumption and waste generation, our wear parts for vertical mills are designed to process various types of ore, delivering consistent particle size reduction and enabling efficient extraction processes for many different Vertical Mill Mining Magotteaux
.jpg)
Vertical Roller Mills used for the comminution of mineral ores
energyefficient size reduction compared to tumbling mills Figure 1: Vertical roller mill operating principle (left: standard configuration, right: configuration with grit extraction) Pilot plant description and standard testing methods The grindability of a particular mill feed forms the basis for the design of an industrial grinding plant2012年9月24日 Interior of the Vertical Mill (Pena, 1990) Construction started in 2002 including an 80 km road between the city of Parauapebas and the mine, infrastructure for the city of Canaã dos Carajás, in Copper concentrate regrind at Sossego plant using Vertical mill merges fine crushing, drying, grinding and powder selecting into a single, which simplifies the production process It has the advantages of high grinding efficiency, low power consumption, large feed particle size, easy Vertical Mill In Cement Plant Cement Vertical Mill2017年4月1日 The vertical stirred mills have a screw agitator centrally located in the mill chamber, which promotes the grinding action by stirring the media and circulating it throughout the mill (Morrison et al, 2009)Stirred mills can be divided into two classes: those with low agitator speeds, that also use gravity to promote media movement and apply forces, and those with Vertical stirred mill scaleup and simulation: Model validation by
.jpg)
THE GRINDING EFFICIENCY OF THE CURRENTLY LARGEST VERTIMILL INSTALLATION
Figure 6 shows the particle size distributions obtained from as jar mill thetests performed with the hematite concentrate Figure 6 – Jar test particle size distributions (Metso, 2011)2015年3月10日 Comparison of the vertical roller mill and rodball mill circuit on the gold extraction; C Gerold et al Recent installations and developments of loesche vertical roller mills in the ore industry; M Ito et al Productivity increase of the vertical roller mill for cement grinding; SW JørgensenCopper ore grinding in a mobile vertical roller mill pilot plantFresh feed size: 3,000 microns (hard rock ores) 10,000 microns (soft ores eg limestone) n The energy distribution within the vertical mill is constant for any given height and radius TowerMill Installation: Karara Iron Ore Project slurry pump hydrocyclone horizontal ball mill hydrocyclone magnetic separatorEIRICH TowerMill Vertical agitated media millGrinding % % % % % %INVESTIGATION ON FLOTATION BEHAVIOR OF A COPPER SULFIDE ORE
.jpg)
Tower Mill Operating Work Index 911Metallurgist
2016年6月3日 Talc from 9 microns average to 19 microns average particle size Silica from 37 microns average to 17 microns average particle size Barite from 28 microns average to 155 microns average particle size Limestone from minus 74 microns to 31 microns average particle size Limestone from minus 4000 microns to 24 microns average particle sizeDOI: 101016/JMINENG201809016 Corpus ID: ; Predicting the product particle size distribution from a laboratory vertical stirred mill @article{Rocha2018PredictingTP, title={Predicting the product particle size distribution from a laboratory vertical stirred mill}, author={Danielle Campos Rocha and Erik Spiller and Patrick R Taylor and Hugh B Miller}, Predicting the product particle size distribution from a laboratory The vertical roller mill integrates crushing, drying, grinding, and conveying +17 [ protected] Feed size: 20 mm there is professional service personnel to connect with you We provide free installation instructions and train operators for you free of charge Share this article Product Specifications Model: CLUM Dolomite Ultrafine Vertical Roller MillFind out all of the information about the FLSmidth DorrOliver Eimco product: mill with rods VXPmill Contact a supplier or the parent company directly to get a quote or to find out a price or your closest point of saleMill with rods VXPmill FLSmidth DorrOliver Eimco

Population balance model approach to ball mill
2014年1月1日 A test campaign with a pilot scale vertical mill was carried out with five different ore samples to elaborate a simple and robust methodology to scaleup vertical mills and perform simulations SBM Ore Ultrafine Grinding Mill Discharge fineness: 1503000 mesh Feed size: 20 mm Output: 120 T/H Product features: Models: HGM ultrafine grinding mill, CLUM vertical roller mill, LXMC ultrafine wet stirring mill etc Send us an Inquiry If SBM Ore Ultrafine Grinding Mill2017年9月11日 PDF In this study, an extensive sampling study was carried out at vertical roller mill of ESCH Cement Plant in Luxemburg Samples were collected from Find, read and cite all the research (PDF) Performance Evaluation of Vertical Roller Mill in2016年12月1日 It was found that the ball mill consumed 5467 kWh/t energy to reduce the F 80 feed size of 7222 lm to P 80 product size of 2754 lm while stirred mill consumed 3245 kWh/t of energy to produce Vertical stirred mill scaleup and simulation: Model validation by
.jpg)
Ok Vertical Mill PDF Mill (Grinding) Scribd
OK VERTICAL MILL Free download as PDF File (pdf), Text File (txt) or read online for free The OK vertical roller mill is a compact and energyefficient mill for grinding cement, slag, and blended cements It uses 3050% less energy than ball mill systems and allows for a more simplified plant layout The OK mill combines drying, grinding, and separation into a single unit2023年2月23日 It explains the higher efficiency of vertical orientation at coarser grind size and reduced efficiency towards the finer producti on Finally, the mill perfor mances were compared according to the (PDF) Performance Comparison of the Vertical and ResearchGate2018年9月29日 Enter the vertical mill A vertical mill is essentially a lathe stood on end with a large milling the head itself up and down on a column Socalled column mills are less rigid, but compact and versatile for their size 13 thoughts on “ Vertical Mill – Installation ” Dominic Tramonte says: September 30, 2018 at 2:37 amVertical Mill – Installation – BlondihacksMaterial circulation inside the mill FSmidth Cement flsmidthcement 3 ATOX coal mill Proven technology Today the airswept vertical roller mill is the standard solution for coal grinding installations And thanks to our continuous refinement of the ATOX coal mill over the years, today’s leading airswept vertical roller mill is the ATOX COAL MILL