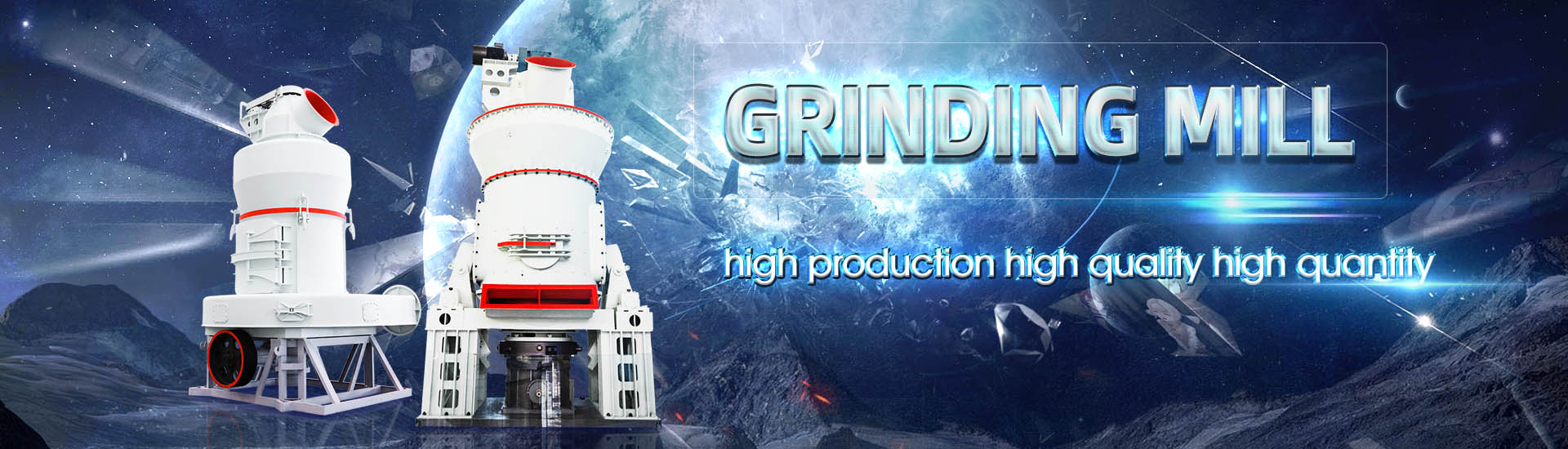
Discharge port of anthracite lignite grinding mill
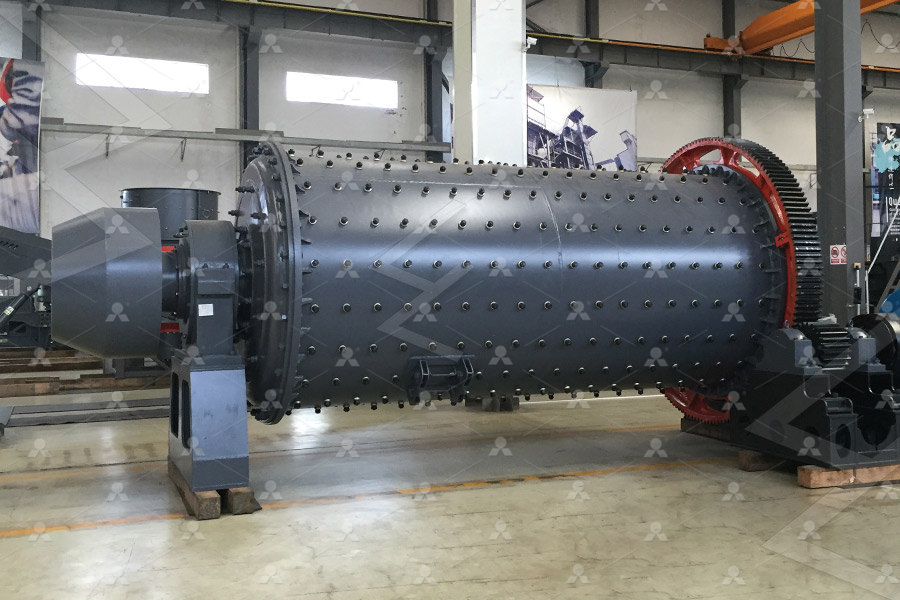
Reprint from ZKG 3 Gebr Pfeiffer
Thus, the MPS coal grinding mill with a high drying capacity is very suitable for grinding lignite with feed moistures of as much as 45 % Depending on this high feed moisture the mill rating Vertical roller mills are not only used for grinding cement raw materials but also find an application in grinding a wide variety of coal types in cement and power plants Gebr Pfeiffer SE (GPSE) COAL GRINDING IMPS: more than meets the eye Gebr PfeifferThe main motor drives the grinding table to rotate through the reducer, and at the same time, the wind enters the mill from the air inlet The material falls through the screw feeder's discharge LM Vertical Coal Mill, coal mill, coal mill price, vertical coal mill The Loesche coal grinding mill range is divided into two serial types: Small twin mills constructed to individual specifications (LM 122 D to LM 202 D), with table diameters from 1,200 to 2,000 LOESCHEMILLS
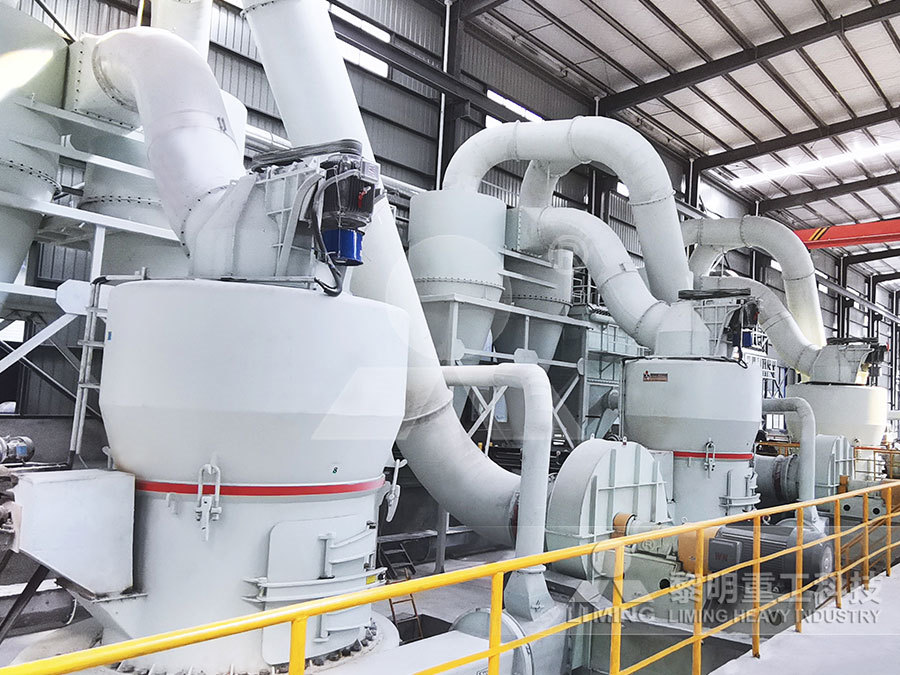
SLURRY FLOW IN MILLS : GRATEONLY DISCHARGE MECHANISM
Discharge grates play an important role in determining the performance of autogenous (AG), semiautogenous (SAG) and grate discharge ball mills The flow capacity (grinding capacity) of 2007年3月21日 The commercially viable and industry accepted alternate is a grate discharge trunnion supported mill or a grate discharge shell supported mill using pulp lifters The only Optimizing your SAG mill operation International Mining2020年6月25日 The Outotec ® Open Ended Discharge Grinding Mill (OED Mill) enables innovative and efficient highcapacity circuit designs through the removal of pulp lifters from Outotec launches new openended discharge grinding mill1996年4月1日 The mill discharge model for the observer is adapted from the model presented in Morrell and Stephenson (1996), where the discharge of charge from the mill through the end Slurry discharge capacity of autogenous and semiautogenous
.jpg)
Operation Analysis of a SAG Mill under Different
2020年10月9日 the qualified particle size at the discharge port of the semi autogenous mill, and the qualified particle size is defined as no more than 25 mm The simulation process is shown in Figure 5 2014年12月1日 The discharge behaviour of different port configurations in a HICOM mill is investigated using DEM simulation The charge in the mill is strongly sheared and circulates rapidly but has a free Effect of port configuration on discharge from a HICOM® millThe MPS coal grinding mill with a high drying capacity is very suitable for grinding lignites with feed moistures of as much as 45 per cent Depending on this high feed moisture, the mill rating is determined by drying whereas for anthracite, hard coal and petcoke the rating of the mill is determined by grinding The greatCOAL GRINDING IMPS: more than meets the eye Gebr Pfeiffer2023年1月16日 The objective of this research is to design and construct a hammer mill for grinding leonardite charcoal (Lignite, class J) The conditions for the design and construction of the grinder are Optimum Design of Hammer Mill for Grinding Leonardite
.jpg)
Simulation of overflow ball mill discharge and trommel flow using
2015年9月1日 Discharge of pebbles, finer rock, ball scats and slurry from mills and its flow through trommels, and into other processing operations has strong impacts on overflow ball mill performance2023年7月18日 1 Cleaning equipment Cleaning the ball mill is one of the important tasks of daily maintenance When cleaning, first turn off the power, remove the components such as the feed port, discharge port, and slag discharge port of the ball mill, and clean each part with clean water and detergent, being careful not to get the electrical parts wetBall Mill Maintenance Process and Methods MiningpediaThis document discusses beater wheel mills used in lignitefired boilers It includes: 1 An overview of beater wheel mills, including their components, typical sizes and capacities, and the comminution process within the mill 2 Diagrams of beater wheel mills with different configurations, such as with or without a separating classifier or with a precrusher 3 Photos of Beater Wheel Mill PDF Lignite Mill (Grinding)2002年6月1日 The kinetics of dry versus wet grinding of several feed size fractions of lignite in a laboratory size porcelain mill are reported here using feed fractions prepared to 600+425, 425+300 and 300 Kinetics of wet versus dry grinding of lignite by a porcelain mill
.jpg)
Overflow VS Grate Discharge Ball or Mill – Why Retrofit
2015年6月25日 Compare Type of Mill Discharge Grate Discharge Ball Mill Capacities The above tables list some of the most common Grate Discharge Ball Mill sizes Capacities are based on medium hard ore with mill operating in closed circuit under wet grinding conditions at speeds indicated For dry grinding, speeds are reduced and capacities drop between 30% 2015年8月13日 A grate discharge mill that is “groundout” would show the desired near zero blinding The slots in the early grates were designed around the traditional types found in proven concepts of metal grates The size and location of this support frame is very specific to the grinding applicationHow a Grate Discharge Ball Mill Works 911Metallurgist2015年12月15日 DOI: 101016/JFUEL201509028 Corpus ID: ; Effects of different drying methods on the grinding characteristics of Ximeng lignite @article{Zhu2015EffectsOD, title={Effects of different drying methods on the grinding characteristics of Ximeng lignite}, author={JieFeng Zhu and Jianzhong Liu and Junhong Wu and Jun Cheng and Zhihua Wang Effects of different drying methods on the grinding characteristics 2023年1月5日 The charcoal briquettes extruder machine is widely used for the molding of charcoal powder, coal foam, coal gangue, lignite, anthracite, iron powder, aluminum powder, and other raw materials And it is often used with Charcoal briquette machine Shuliy Machinery
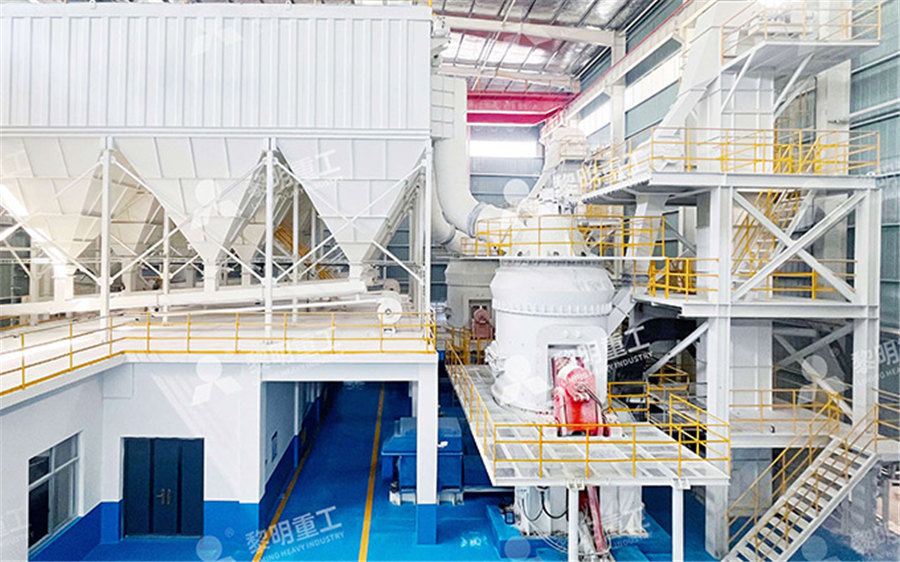
Grinding Mill Design Ball Mill Manufacturer 911Metallurgist
2017年2月20日 All Grinding Mill Ball Mill Manufacturers understand the object of the grinding process is a mechanical reduction in size of crushable material 911 Metallurgist is a trusted resource for practical insights, solutions, and support in mineral processing engineering, helping industry professionals succeed with proven expertise Grinding Mill Design Ball Mill Anthracite Lignite Petroleum coke Bituminous coal Applications: The material falls through the screw feeder's discharge port and falls in the center of the grinding table When grinding the roller table area, Thank you for your interest in Our Industrial Grinding Mill If you want to get help immediately, please chat online nowLM Vertical Coal Mill, coal mill, coal mill price, vertical coal mill 2020年6月25日 “The Outotec Open Ended Discharge Grinding Mill takes high capacity discharge systems to the next level, enabling novel circuit designs with reduced CAPEX and OPEX The completely open discharge end results in the lowest possible slurry pool level while simultaneously optimizing serviceability and maximizing availability,” says Damon Bordi, Outotec launches new openended discharge grinding millR Roller Mill Xiao Xiao1, Huang Lilong2 and Xu Kuangdi3 1Changsha Research Institute of Mining and Metallurgy, Changsha, China 2Changsha Research Institute of Mining and Metallurgy, Changsha, China 3Chinese Academy of Engineering, Beijing, China Roller mill is a type of grinding equipment for crushing materials by pressure between two orRoller Mill Springer
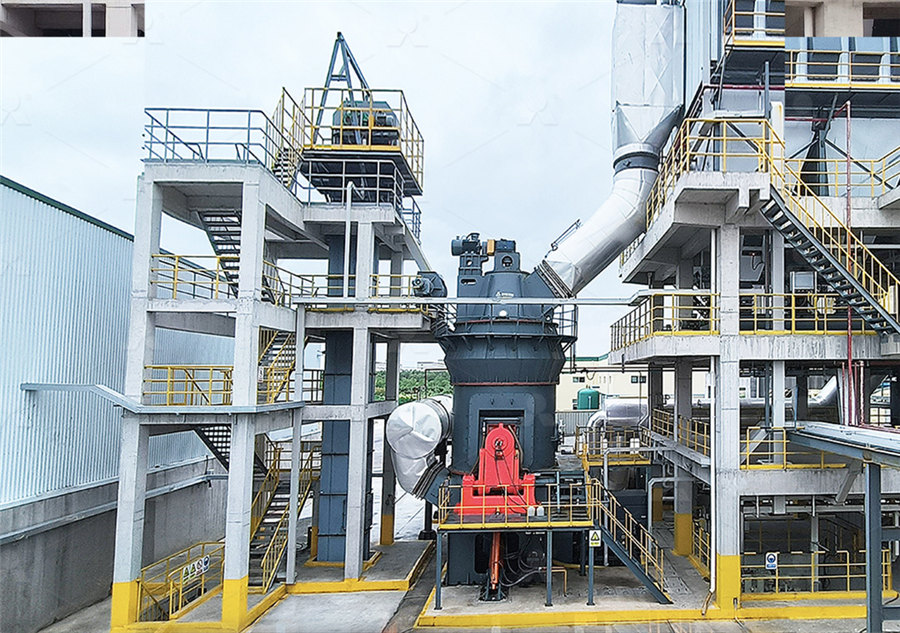
Research on the grinding characteristics of lignite based on grinding
2022年9月30日 Mark Duffy produced a complete set of grinding data on a pilotscale tower mill Here these data are analyzed in terms of grinding kinetics The results show that the data can be fitted with a Omega Global Journal of Engineering and Technology volume 1 issue 1, Aug 2019 Reserved Copy Rights 2019 36Design and Modify of Mill Discharge Valve Using in2018年6月8日 Properties of coal surface and pore structure are important aspects to be investigated in coal preparation and utilization In order to investigate the limits of different probe methods, a Surface Properties and Pore Structure of Anthracite, Bituminous Coal E Discharge to the mill A Discharge of coal from the bunker B Conveyance of coal (particularly lowvolatile coals such as lean coal and anthracite) This mill type can deal with approx 150 t /h of coal Depending on size and space, Pulverisers for Lignite The grinding system –Hitachi Power Europe Service GmbH PDF4PRO
.jpg)
Ball Rod Mill Density – How Water Impacts Grinding
2015年8月6日 The % solids by volume of the rod mill discharge Rod mill grinding efficiencies have been shown to increase in the range of 5 to 15% with more dilute discharge slurry (ie, increased feed water) at least down to the range of 45 to 50% solids by volume2015年7月29日 As you increase the volume of the through put, the time that the ore has to react to the grinding media is lessened As you add ore to the mill you are also adding WATER and changing density which affects the slurry rheology and workings of the grinding action inside that mill This water is one of the main controls that you have over your grindEffect of Water Density on Grinding Mill 911MetallurgistSo far, the biggest mill for lignite coal grinding will be delivered to Cemindo’s Bayah plant in Indonesia This MPS 4500 BK has been ordered for grinding lignite with a maximum moisture of 37% and it is able to produce a throughput rate of minimum 100 t/h at a residue of 15% R009 mm The installed power for the mill main drive is 1300 kWReprint from ZKG 3 Gebr Pfeiffer2022年6月1日 In this study, the particle size distribution, fractal dimension, specific energy consumption, and grinding kinetics of chalcopyrite ore under high voltage pulse discharge were systematically Characterization of chalcopyrite ore under high voltage pulse discharge
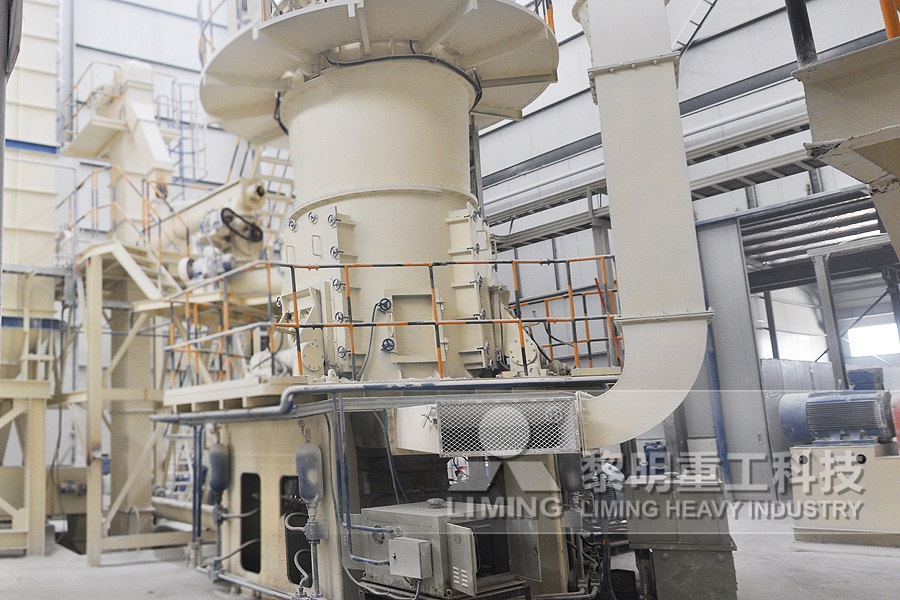
SAG Mill Grinding Circuit Design 911Metallurgist
2016年6月6日 For circuits classifying mill discharge at a coarse size (coarser than approximately 10 mm), trommels can also be considered to classify mill discharge Trommels are less favorable in applications requiring high classification efficiencies and can be constrained by available surface area for highthroughput millsIt could be used to grind bituminite, meagre coal, and anthracite lignite with high moisture under some conditions Vertical mill adopts low speed, big roller diameter, high loading force design It has the widest adaptability to coal types and variation in coal properties, big grinding surface ability, low rolling resistance, low energy consumption, stable output, etcVertical mill for coal pulverizing in power plant Geckointech2016年6月6日 Discharge End Designs Historically the grate discharge has been a design option in grinding mills With the introduction of wet autogenous and semiautogenous mills, this type design is used exclusively The discharge end of this mill must incorporate some method of conveying the pulp to the outside of the millSAG Mill Liner Design 911Metallurgist2016年3月14日 Without any reference to dry grinding, the first successful ballmill for wet crushing, which is still in operation, was built 10 years ago The peripheraldischarge mill differs from a trunnion discharge mill, in the character of its Peripheral Discharge Ball Mills Theory and Practice
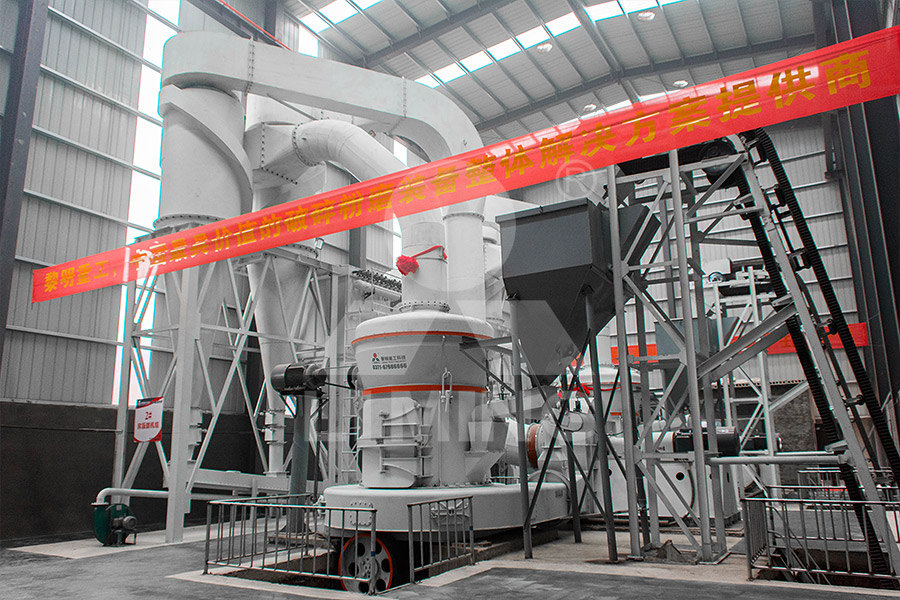
Slurry flow in mills: grateonly discharge mechanism (Part1)
2003年7月1日 If the grate provides a high resistance to flow of slurry, then the mill will fill with an excessive amount of slurry to a level past where efficient grinding occurs, and the mill will “go off the grind” (Austin et al, 1984)Moys (1986) supported this view and stated that an excessive buildup of slurry would seriously affect autogenous mills as a large volume of dense slurry Abstract: The particle size distribution of ball mill grinding products is an important production index of the grinding operation, and due to its multivariate strong coupling and nonlinearity in the operation process, it leads to difficulties in achieving optimal control of the discharge particle size distribution To this end, a reinforcement learningbased optimal control method is proposed Reinforcement learning based ball mill discharge size distribution A vertical roller mill, also known as a vertical grinding mill or vertical mill, is a comprehensive grinding equipment integrating crushing, drying, grinding, grading, and conveying Vertical grinding mills can be widely used in electric power, Energysaving and Efficient Vertical Roller Mill Fote 2018年1月1日 Batch dry grinding of –335+17 mm and –17+06 mm feed fractions of anthracite and lignite was studied in order to Fine grinding of lignite in a ball mill was shown to be nonlinear in Kinetics and sub sieve morphology of ball mill grinding for
.jpg)
Flotation of Base Metals from Grinding Mill Discharges
More recently, a Reichert cone has been used to recover sulphide and oxide base metal minerals from screened rod mill discharge 1To the authors' knowledge, the first application of flotation of base metal minerals from the discharge of a production plant grinding mill was at the Lake Dufault concentrator of Corpor'1tion Falcon bridge Copper17 Lignite Combustion – US Environmental Protection Agency In a pulverized lignitefired boiler, SCCs = pulverized coalfired boilers, 10100301, Boiler Design And Operating Variables Affecting Uncontrolled » More detailed! Coal Firing Systems – Hitachi w Polsce Designed as coal bunker dischargers, the mill feeders supply the pulverizers with In hard coal boiler units layout of coal mill /bunker for lignite fired boilers – Grinding Mill Therefore, the Rod Mill causes no excessive grinding, enabling you to produce products of relatively sharp particle size distribution curve Features The Rod Mill is a grinding mill used for coarse grinding or fine grinding, which offers the following types and uses 1) Peripheral Discharge Type 1 Wet grinding type (EPD type and CPD type)Horizontal Coarse Grinding Mill Rod Mill [KURIMOTO, LTD]Request PDF On Jun 25, 2023, Hongwang Liang and others published Effect of ultrafine grinding on biomethanation of lignite Find, read and cite all the research you need on ResearchGateEffect of ultrafine grinding on biomethanation of lignite
.jpg)
Comparison of measured and predicted PSD of mill discharge
Three series of grinding tests were performed using a laboratoryscale ball mill (Sepor, Los Angeles, CA, USA) with a volume of 5423 cm 3 operating at 66 rpm, which corresponds to 70% of its 2016年6月1日 Dry ROD MILL Grinding No other type of mill is so well adapted to dry grinding materials to 4 or 8 mesh in single pass with the production of a minimum amount of fines A major factor in dry grinding is the rapid removal of finished material to prevent cushioning of the rods This is accomplished in the End Peripheral Discharge Rod MillRod Mills: Efficient Grinding Solutions for Mining2020年3月15日 This paper selects anthracite coal and coking coal as experimental materials to conduct heterogeneous grinding in the Hardgrove mill Energy consumption and product t 10 of single coal and mixtures at various grinding time are measured, and effects of mixed ratio on energysize reduction process are discussed T 10 values of component after the mixture Energysize reduction of mixtures of anthracite and coking 2011年2月1日 A comparison of the results obtained from grinding in a stirred media mill lignite coal samples treated with microwave and untreated samples February 2011; Fuel 90(2):659664;A comparison of the results obtained from grinding in a stirred