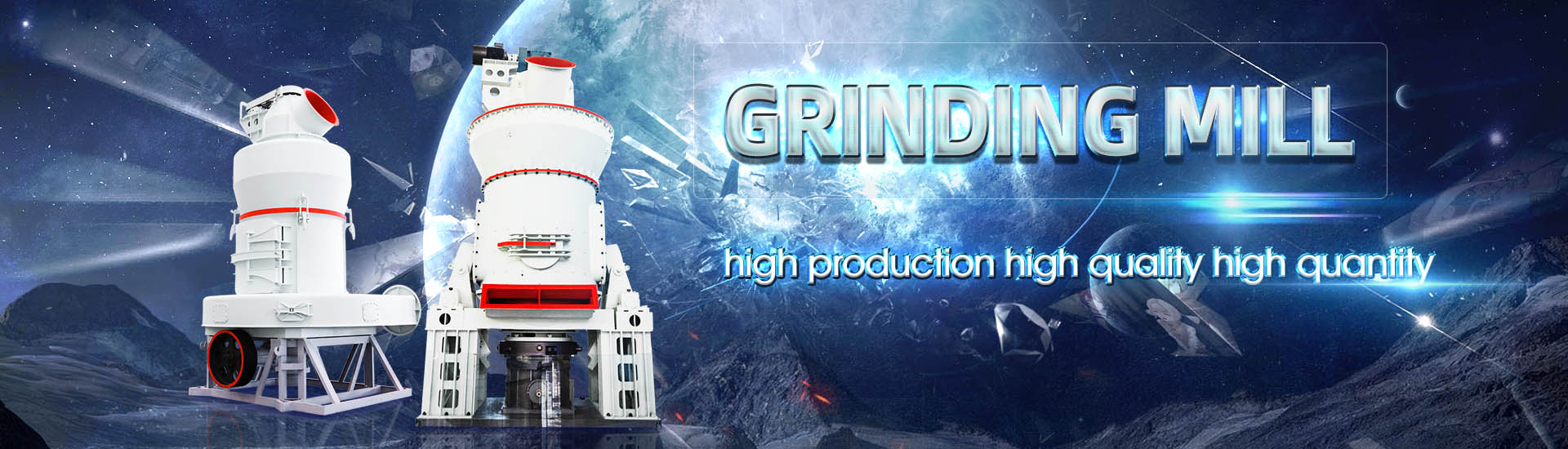
How to reduce the production cost of slag micron powder
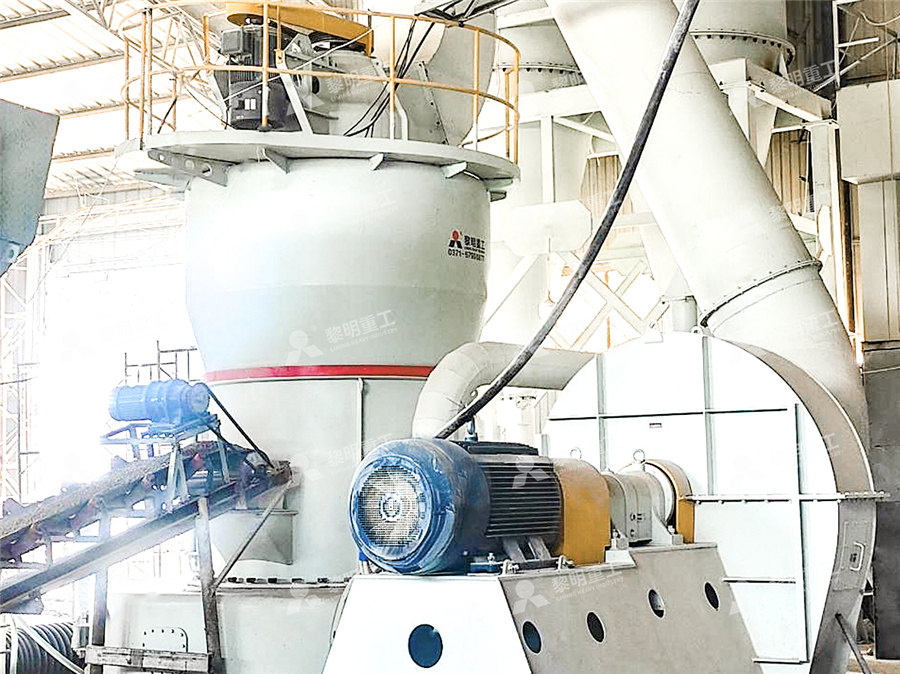
Analysis and multiobjective optimization of slag powder process
2020年11月1日 Optimal solution for slag powder production process is determined by proposed CTNSGAII algorithm Slag powder is a process with characters of multivariables, strongly coupling and nonlinearity The material layer thickness plays an important role in the processrent RD efforts focus on reducing its production cost and increasing the longterm stability of cells and stacks by lowering its operation temperature without losing power density Smart Powder Processing for Advanced Materials JSTAGE2021年10月5日 Large iron and steel enterprises in the US, Japan, Europe, Germany, and China have adopted ways to recycle waste steel from steel slag for reducing the cost of the raw Production, characterisation, utilisation, and beneficial soil 2020年7月1日 For slag powder process, operational stability of the vertical mill (indexed by the material layer thickness) is the primary concern for production safety and longterm benefitsAnalysis and multiobjective optimization of slag powder process
.jpg)
SIZE REDUCTION BY GRINDING METHODS ResearchGate
The process "Comminution" involves size reduction and sizewise classification called as screening or separation The objective of this report is to provide the details 4 天之前 The utilization of silicomanganese slag (SiMnS) as a precursor for alkaliactivated materials (AAMs) is considered as an efficient approach for sustainable and ecofriendly large Preparation of Low Carbon Silicomanganese SlagBased AlkaliTo increase output with efficient milling practices, your need to ensure you find the optimum balance between milling size reduction and heat generation An increase in temperature can Particle Size Reduction Milling EquipmentFrom lab/pilot to production requirements, Hosokawa Micron Powder Systems offers a complete line of size reduction technologies Whether you call it size reduction, micronization, milling, Size Reduction Milling Hosokawa Micron Powder Systems
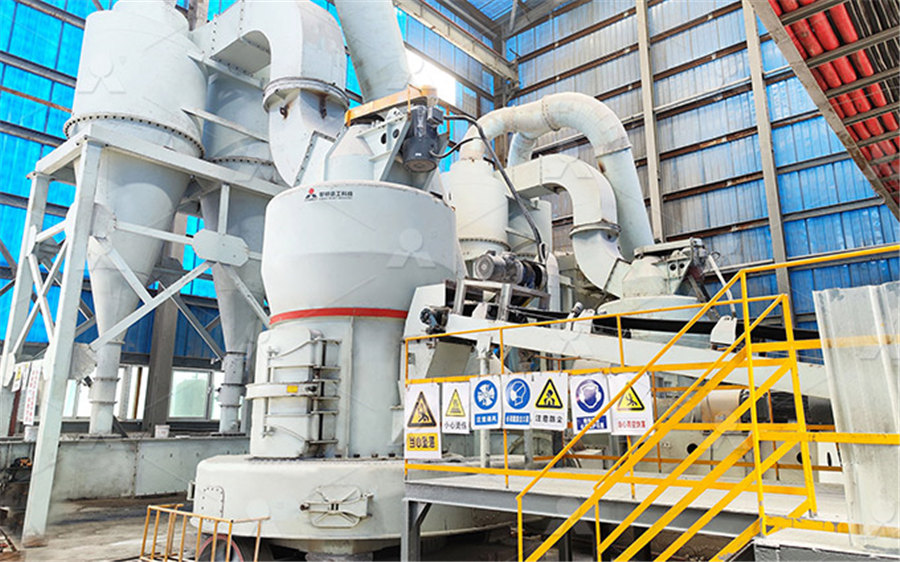
A Review on Stabilization of Ladle Furnace SlagPowdering Issue
2022年9月30日 According to Zhao et al , stabilization of AODbased slag can be done through the addition of quartz sand to the slag that will reduce the slag basicity from 2 to 15 at a lower 2021年1月5日 This paper deals with the procedure tried out at TATA STEEL to prevent the disintegration of LF slag generated during the production of siliconkilled steel grades The Prevention of Ladle Furnace Slag Disintegration Through Different 2016年2月5日 The quality of raw materials (iron ore, coal, and coke) has a clear impact on the carbon emissions of the hot metal production in steel making So far, very little work has been done to measure and quantify this impact Yet for benchmarking, technology choice and general carbon optimization are important elements The total slag production of a blast furnace gives The Carbon Cost of Slag Production in the Blast Furnace: A2020年5月21日 Iron ore pellets are largely characterized by inherent physical and chemical properties of the ore Alumina and silica play important roles in determining the productivity of a Blast Furnace On average, one percent increase in iron content improves productivity by 2% and reduces coke consumption by 1% Therefore higher iron ore feed content to blast furnace is A Study on HighGrade Iron ore Beneficiation to Reduce
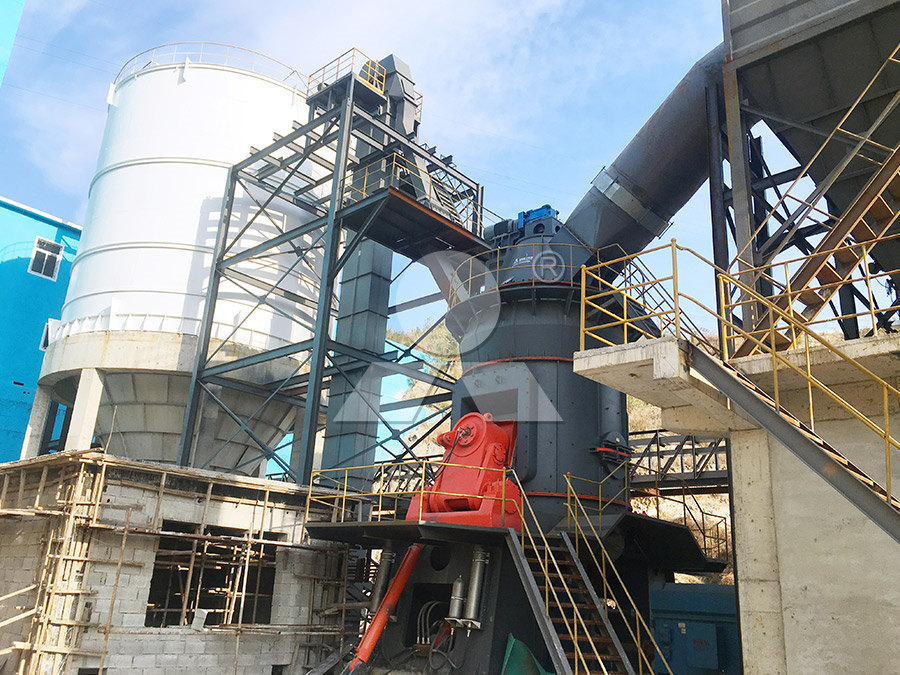
Slag Powder: A Sustainable and Valuable Resource
Slag powder is a finegrained byproduct produced during the separation of metal from its ore in various hightemperature metallurgical processes, such as smelting and refining It is composed of various minerals and compounds, and its specific composition depends on the type of ore being processed and the production methods employed Types of Slag Powder Ground []2015年11月3日 Increasing urban development has increased the demand for cement and cement production significantly contributes to CO2 emissions These emissions are reduced when high volumes of cement are REVIEW ON PARTIAL REPLACEMENT OF CEMENT IN CONCRETE 2009年11月1日 In a pioneering study by Parker and Ryder, published in 1942, the stability field of C 2 S, adjusted on the sulfide content of the slag, was defined from CaOMgOSiO 2 Al 2 O 3 and expressed in EqsA way to reduce environmental impact of ladle furnace slag1 Introduction The basic oxygen steelmaking (BOS) process produced over 70% of the global crude steel in 2018, [] generating 100 to 150 kg of slag (“BOS slag”) for every tonne of crude steel produced BOS slag, a product of hot metal element (eg, Si, Mn, Fe, P) oxidation and flux (eg, lime, dolomite) dissolution, plays a critical role in the production of highquality crude steelBasic Oxygen Steelmaking Slag: Formation, Reaction, and Energy
.jpg)
Basics of Size ReductionCoarse to Medium Grinding – Hosokawa Micron
Hosokawa Micron Powder Systems designs and manufactures size reduction systems and powder processing solutions for the Chemical, Pharmaceutical, Food, Mineral, Cosmetic and Plastic industries Call us at 1800526年12月15日 Food manufacturers and ingredient suppliers have access to a wide range of hightech milling methods Each one offers advantages for achieving product characteristics such as particle size and moisture content, along with other considerations such as cost, footprint and the need for ancillary equipmentSize reduction: How to select the proper milling equipment2021年1月5日 Ladle furnace (LF) slag plays an important role in modern steel making in terms of quality and productivity The major challenge of using LF slag is its dusting problemPrevention of Ladle Furnace Slag Disintegration Through Different Slag 2023年11月20日 In the twentyfirst century, steel has become one of the most utilized engineering materials, from house utensils to the automotive sector According to the World Steel Organization, the world produced a total of 1951 A Review on Environmental Concerns and
.jpg)
Basics Size Reduction – Fine Ultrafine Size Reduction
Hosokawa Micron Powder Systems designs and manufactures size reduction systems and powder processing solutions for the Chemical, Pharmaceutical, Food, Mineral, Cosmetic and Plastic industries Call us at 1800526年7月10日 The present literature review explores the energyefficient ultrafine grinding of particles using stirred mills The review provides an overview of the different techniques for size reduction and the impact of energy EnergyEfficient Advanced Ultrafine Grinding of Download Citation On Nov 1, 2024, Zhong Yin and others published Improvement of the resistance to carbon dioxide corrosion of oil well cement by micron diabase powder in hightemperature Improvement of the resistance to carbon dioxide corrosion of oil 2024年9月23日 SS production has increased from 3535 million tons (out of 1014 million tons of steel production) in 2017–2018 to 53 million tons (out of 150 million tons of steel production) in 2019–2020, which tends to strengthen the effective and economically viable utilization of Enhancing concrete properties with steel waste: a comprehensive
.jpg)
Preparation of LiFePO using iron(II) sulfate as product from
To further reduce the production cost of LiFePO 4 cathode material and promote the resource utilization of titanium dioxide slag solid waste, this paper chose titanium dioxide slag rich in iron(II) sulfate as raw material After purification, it prepared Redesigning processes and products while reducing waste can save on overall material costs 11 Reduce Packaging Costs More companies are using less packaging in order to save not just costs but also the environment Excess packaging doesn’t just cost more in raw materials but also increases weight, adding to shipping costs15 Ways To Reduce Costs In Manufacturing TWI2009年1月1日 Valorization of LF slag helps in sustainable steelmaking and also reduces steel production cost In spite of beneficial composition, valorization of LF slag is difficult due to its disintegration A way to reduce the environmental impact of LF slagUp to one third of the production cost of an AM component is the cost of the powder used, with commercial viability resting on establishing a robust supply chain and effective powder recycling strategies Identifying analytical tools that can be used to reliably set specifications for AM metal powders to validate quality and manage their use is manufacturing Optimizing metal powders for additive ATA
.jpg)
(PDF) FactSage Studies to Identify the Optimum Slag
2020年11月29日 Decreasing the slag rate can lead to a lower fuel rate and higher productivity in the blast furnace (BF) Indian iron ore is known to have adverse alumina–silica ratio2017年3月4日 purpose is to reduce the size of the ore (rock) pa rticle before subjecting it to reagents (chemical reactions) Crushing involves reducing the ore size from various sizes ranging from particles SIZE REDUCTION BY GRINDING METHODS2022年7月18日 Building manufacturing has played a significant part in the urbanization and industrialization that has occurred in recent decades Approximately 5–10% of global employment is provided by the construction A Comprehensive Review on the Ground Granulated 2024年9月27日 Hosokawa Micron Powder Systems designs and manufactures size reduction systems and powder processing solutions for the chemical, mineral, pharmaceutical, cosmetic, food and plastic industries Hosokawa Home Hosokawa Micron Powder Systems
.jpg)
Review of the Methods for Production of Spherical Ti and Ti Alloy Powder
2017年8月15日 Spherical titanium alloy powder is an important raw material for nearnetshape fabrication via a powder metallurgy (PM) manufacturing route, as well as feedstock for powder injection molding, and additive manufacturing (AM) Nevertheless, the cost of Ti powder including spherical Ti alloy has been a major hurdle that prevented PM Ti from being adopted for a wide 2024年2月14日 With the rising costs of highactivity materials like slag (Han et al 2017), the focus has shifted to economically viable alternatives such as steel slag (SS) and ceramic powder (CP) SS, a byproduct of the iron and steel industry, contributes significantly to China's annual production (Francisca and Glatstein 2020 ; Cui et al 2021 ), offering a sustainable resourceSustainable assessment and synergism of ceramic powder and steel slag 2024年4月22日 This is helpful to improve the utilization efficiency of energy in steel slag and reduce the demand for energy such as Sun et al used steel slag to fix carbon, fully mixed steel slag powder with water at a mass ratio of 1 it is expected to achieve efficient carbon capture while reducing the cost of hydrogen productionResearch progress of hydrogen production and CO2 fixation in 2017年8月1日 Powder cost per pound = $350 ; A pound of powder with a specific gravity of 10 at 100percent utilization will cover 1923 ft 2 at a thickness of 1 mil That is the starting point for calculating the powder costCalculating the Cost of Powder Coating Products Finishing
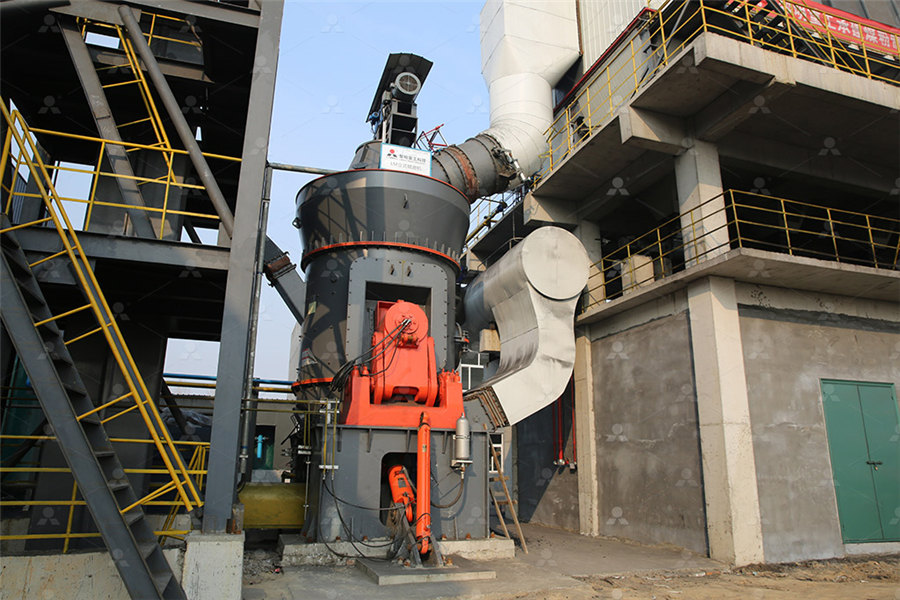
Alumina Production an overview ScienceDirect Topics
Production of alumina J Metson, in Fundamentals of Aluminium Metallurgy, 2011 27 Production of speciality aluminas Although around 93% of alumina production is subsequently used as the feedstock in the smelting of the metal, there is a significant market for specialty aluminas These markets lie in ceramics, particularly insulators and refractories, abrasives, catalysts, catalyst 2020年9月24日 With the rapid development of China’s steel industry, rising rates of steel production have led to the increase of steel slag emissions Steel slag is a kind of industrial solid waste produced in the process of iron and steel smelting, and its emission is about 15 wt%–20 wt% of crude steel output []According to the data released by the World Iron and Steel Sustainable Utilization of Steel Slag from Traditional Industry and 2019年1月1日 Global slag production exceeds 400 million tons recycled materials in order to reduce their reliance on natural Due to its high disposal cost and the positive features of steel slag, Recent trends in slag management utilization in the steel In this research work, EAF slag was used as raw materials in the production of ceramic tiles The EAF slag was crushed and ground into micron size powder before wetmixed and milled with ball clay Recycling of Malaysia's EAF steel slag waste as novel
.jpg)
Experiment on micronsized particle production of iron ore by
2018年3月1日 Conventional techniques used for the production of micronsized particles of iron ore are mostly based on mechanical shells, and chalk or marl combined with shale, clay, slate, blast furnace slag, silica sand, and iron ore Optimization of the powdering process is likely to reduce the cost of iron ore powder production 72022年1月12日 Figure 1 shows the Ellingham diagram for different oxides It can be seen that thermodynamically, molecular hydrogen can be used to reduce a number of metal oxides, namely ZnO, CoO, NiO, PbO, Cu 2 O, and Fe 2 O 3Hydrogen in atomic and plasma states, however, is found to be a more powerful reductant, where the ΔG° of atomic and plasma hydrogen are 3 Metals Production and Metal Oxides Reduction Using Hydrogen: 2021年12月3日 Copper slag is generated when copper and nickel ores are recovered from their parent ores using a pyrometallurgical process, and these ores usually contain other elements which include iron Environmental and Socioeconomic Impact of Copper SlagA Steel production has been targeted to be higher than as of now in future and the generation of slag will also be high Steel slag is presently used in various fields such as in construction (Lam Particle size distribution of steel slag powder
.jpg)
Powder Processing of Bulk Components in Manufacturing
2014年1月1日 Thus, the heating operation is developed in an easily deformable and thermally stable powder material in two ways: (a) the degassed green compact of particles, poured into a steel can, is heated up at T [°C] and then the compaction pressure acts on the can by the means of a hydraulic press in low thermal conductivity powder, eg, talcum (Fig 61a and b) the semi 2023年7月23日 making slag at 70 C and the calcium leaching rate was over 85% Sun et al [17] used NH4Cl as a solvent to leach steelmaking slag at 60 C and initial CO2 pressure of 10 bar for 60 min, 211 kg CO2 could be fixed per ton of steelmaking slag To further reduce energy consumption, Ji et al [18,19] proposed the integrated technology of CO2 Conversion of Activated Calcium in Industrial Water to Micron 2021年3月3日 In this case, powder coating process parameters were optimized to improve the dry film thickness of powder coating on mild steel using RAL 7040 epoxypolyester at coating thickness in the range 70 Optimization of powder coating process parameters in mild Production of Silicon Carbide Micron Powder in particulate filters present in diesel and as an additive in oils to reduce friction 5 the silicon carbide micron powder results in significant cost savings due to its properties as a slag reducer, energy supply and improved characteristics of the metal obtained 11Silicon Carbide (SiC) Micron and Nano Powder Nanografi
.jpg)
Prevention of Ladle Furnace Slag Disintegration Through Different Slag
2021年1月5日 Abstract Ladle refining is a popular secondary metallurgy process and plays a vital role in achieving the desired chemistry and temperature during steelmaking The slag produced after ladle refining mostly contains dicalcium silicate (C2S) The presence of high C2S in slag leads to the disintegration of slag into fine powder during cooling due to phase