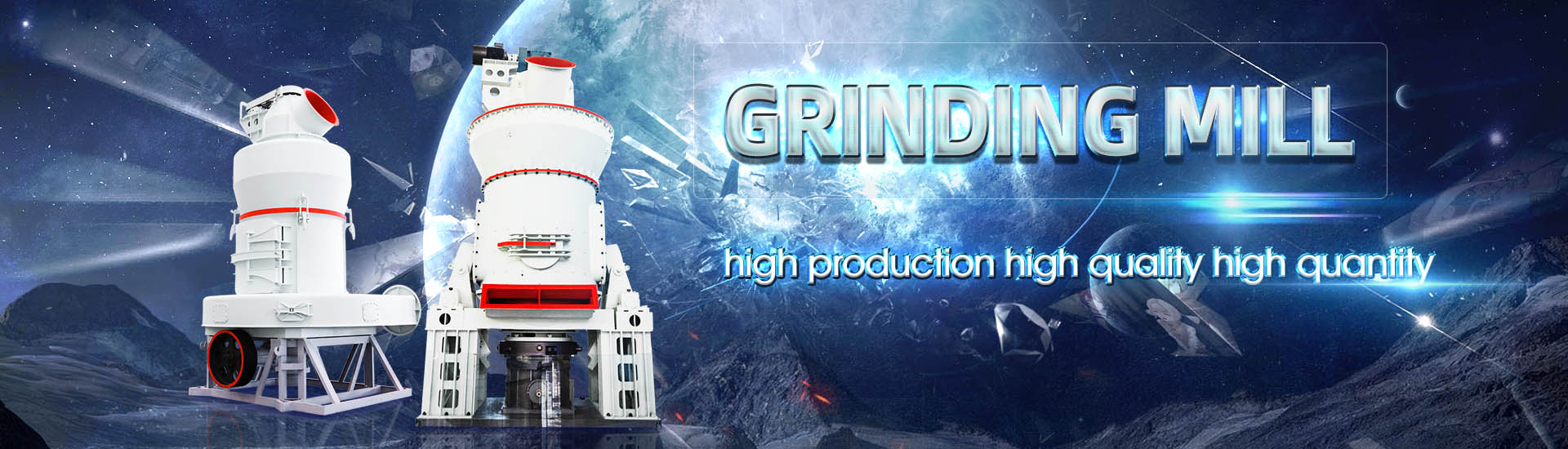
Coal mill pressure difference control
.jpg)
Modeling and Control of Coal Mill
The pressure drop, across the mill depends on the mill differential pressure of the primary air, and the amount of coal suspended in the air During normal operation, the mill pressure drop is predominately proportional to the primary air differential pressure and a small change in coal 2015年8月1日 The variations in the coal flow and air flow are directly related to changes in the fuel demand; mill outlet temperature is strongly influenced by the coal flow, air flow, mixed Review of control and fault diagnosis methods applied to coal Coal mill is an important component of the thermal power plant It is used to grind and dry the moisturized raw coal and transport the pulverized coal – air mixture to the boiler Poor dynamic (PDF) Modeling and Control of Coal Mill Academia2012年5月1日 The paper presents development and validation of a coal mill model to be used for improved mill control, which may lead to a better load following capability of power plants Derivation and validation of a coal mill model for control
.jpg)
Derivation and validation of a coal mill model for
2012年1月1日 In typical coal fired power plants, there are 4–8 coal mills providing fuel to each boiler unit (Fig 1) The control problems arise from the lack of good sensors for measuring the output of pulverized fuel from each mill2018年5月2日 Three system output parameters of vertical roller coal mill (the pressure drop over the mill, power consumed by the mill and outlet temperature) models have been developed and used in nonlinear model predictive control Detection of Malfunctions and Abnormal Working 2012年5月1日 The paper presents development and validation of a coal mill model to be used for improved mill control, which may lead to a better load following capability of power plants Derivation and validation of a coal mill model for control2016年1月18日 This paper presents the shortcomings of traditional PID method in coal mill control, such as multivariable coupling, nonlinearity and largetime delay, and giveThe Inferential predictive control method of coal mill IEEE
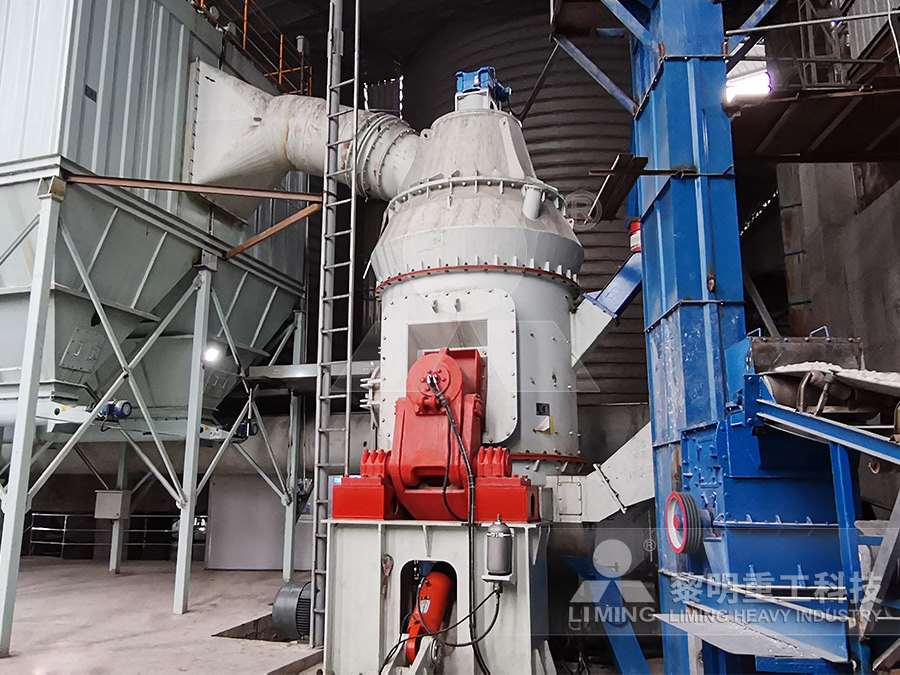
Modeling and outlet temperature control of coal mill using Model
Poor dynamic performance of coal mill causes difficulties in maintaining the frequency, boiler pressure and temperature of the plant This paper presents development and validation of coal Instrumentation and control is an integral part of a coalfired power station A modern, advanced IC system plays a major role in the profitable operation of a plant by achieving maximum Instrumentation and control in coalfired power plant ICSCCONTROL OF COAL MILL In general the control systems, of mills have two components: coal air mixture temperature control and the coal feeder control Control scheme for outlet temperature is essential since improper control may lead to chances of explosion In the thermal power plant, the outlet temperature is maintained at 70 C (PDF) Modeling and Control of Coal Mill AcademiaAbstract: The paper presents development and validation of coal mill model (including the action of classifier) to be used for improved coal mill control The model is developed by using the mass and heat balance equations of the coal mill Genetic Algorithm is used to estimate the unknown parameters that are used in the model validationModeling and Control of Coal Mill
.jpg)
Derivation and validation of a coal mill model for
520 P Niemczyk et al / Control Engineering Practice 20 (2012) 519–530 Nomenclature Dpmill mc mpc mcair mass of unground coal on the table (kg) mass of pulverized coal on the table (kg) mass of pulverized coal carried by The counter pressure reduces the noise generated by the mill and is adjustable depending on the coal properties and required coal fineness During operation, both pressures are adjusted proportionately to the feeder speed by means of pressure control valves to achieve an optimized grinding force characteristic throughout the mill load rangeCOAL PULVERIZER DESIGN UPGRADES TO MEET THE DEMANDS 2011年8月1日 Pulverizers prepare raw fuel by grinding it to a desired fineness and mixing it with the just the right amount of air before sending the mixture to boiler burners for combustion In Part I of Pulverizers 101: Part I POWER Magazine2006年6月25日 due to small driving pressure difference, and leakage pressure control loop when the coal mill dynamics vary It should be noticed that a prefilter is added in theObserverBased Coal Mill Control Using Oxygen Measurements
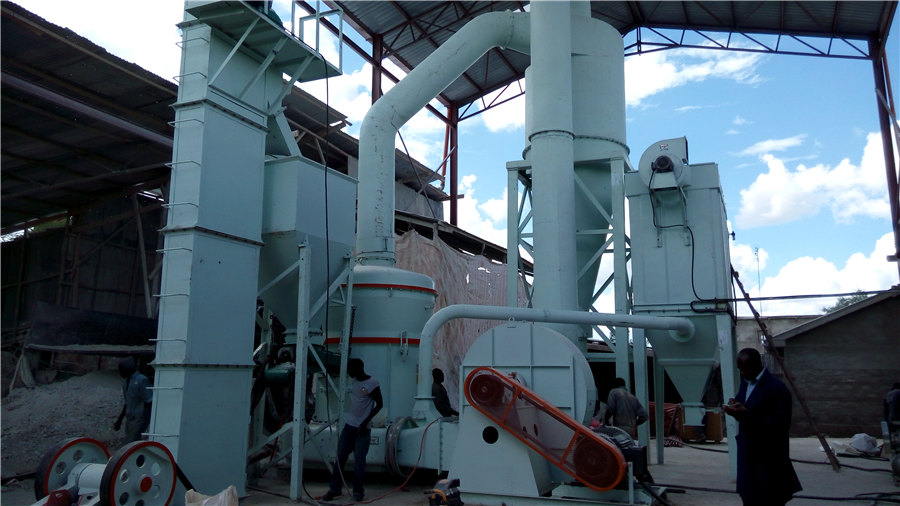
Derivation and validation of a coal mill model for control
520 P Niemczyk et al / Control Engineering Practice 20 (2012) 519–530 Nomenclature Dpmill mc mpc mcair mass of unground coal on the table (kg) mass of pulverized coal on the table (kg) mass of pulverized coal carried by primary air (kg) wc wpc wout wret mass mass mass mass flow flow flow flow of of of of the dry raw coal to the mill (kg/s) pulverized coal (kg/s) pulverized coal coal grinding applications in the cement industry, where normally a twomillsystem is used 1 Introduction Two mill systems are employed for most coal grinding applications in the cement industry These are, on the one hand, vertical roller mills (VRM) that have achieved a share of almost 90 % and, on the other hand, ball mills whose share de Reprint from ZKG 3 Gebr Pfeiffer2020年3月2日 Instead of dividing the total reference amount of coal into four equal parts and forwarding the information to the algorithm to determine the optimal distribution within each pair, first 1/7 of the total quantity was allocated to the mill coupled with the inactive mill (eg if mill M3 is inactive, mill M7 gets 1/7 of the total load), while the remainder of the total demand was Full article: One approach to temperature distribution control 2013年3月1日 In order to improve the quality of the coal mill control, plenty of advanced techniques are used nowadays, such as decoupling control, predictive control, fuzzy control or adaptation of different Nonlinear coal mill modeling and its application to model predictive
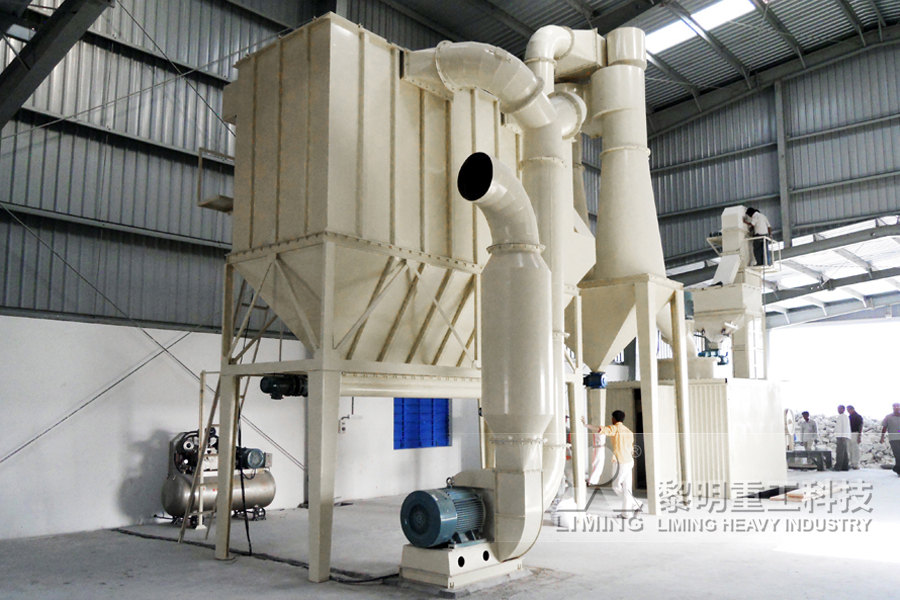
Modeling and Parameter Identification of Coal Mill
2009年9月20日 A control oriented model was then developed by Fan (1994) and Fan and Rees (1994) In 2009, coal flow and outlet temperature of mill were modelled using mass and heat balance equations for startup boiler pressure, and temperature Control performance can be improved by modeling the coal mill properly for control purpose It is necessary to model the coal flow andModeling and Parameter Identification of Coal Mill ResearchGate2024年5月1日 In summary, the application of the proposed dual warning method is able to monitor the fault information and localize the abnormal variables in advance The proposed Autoformer WaveBound coal mill early warning approach aggregates the characteristics of different components of the coal mill and the trends over a longer period of timeDual fault warning method for coal mill based on ScienceDirectAbstract: The paper presents development and validation of coal mill model (including the action of classifier) to be used for improved coal mill control The model is developed by using the mass and heat balance equations of the coal mill Genetic Algorithm is used to estimate the unknown parameters that are used in the model validationModeling and Control of Coal Mill
.jpg)
Modelling and control of pulverizing system considering coal moisture
2015年2月1日 Considering the effect of coal moisture on the energy balance of the coal mill, Zeng [5] et al established a dynamic model of a coal mill and designed an optimized control scheme for the coal be improved by modeling the coal mill properly for control purpose It is necessary to model the coal flow and the pulverized coal temperature [3], [4] Several coal mill models have been developed in the literature The transfer functions of coal mill are experimentally measured in [5, 6] The authors assumeModeling and Parameter Identification of Coal Mill2013年12月18日 Download Citation Modeling and Control of Coal Mill [Show full abstract] temperature of mill, as well as the difference between inlet and outlet pressure, Modeling and Control of Coal Mill ResearchGate2012年5月1日 Niemczyk et al constructed and validated a dynamic pulverizing system model for different coal mill types the conventional automatic control of boiler outlet steam pressure by means of the Derivation and validation of a coal mill model for control
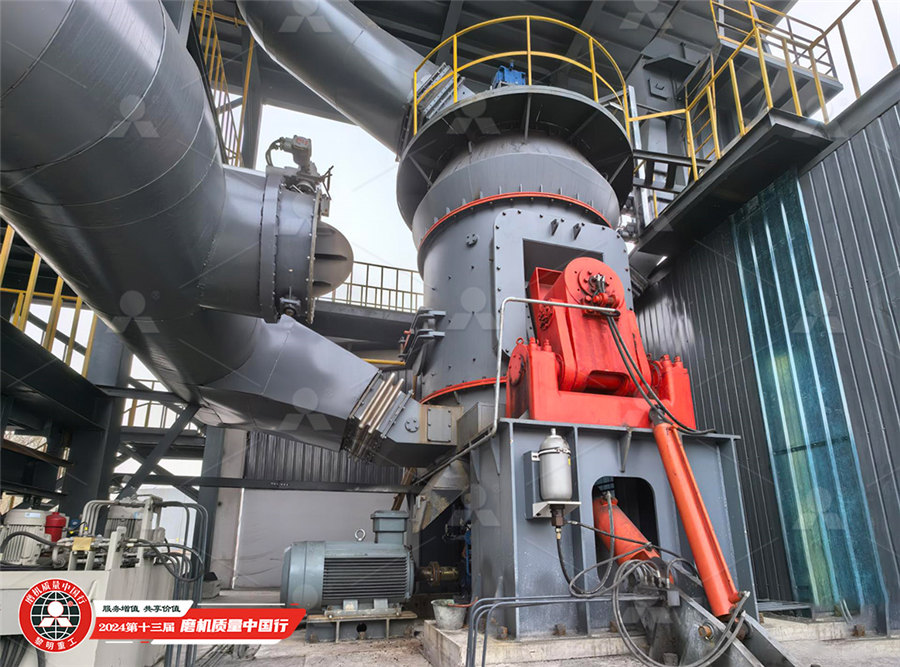
ONLINE COAL FLOW MEASURING AND BALANCING (CONTROL) AND ONLINE COAL
ONLINE COAL FLOW MEASURING AND BALANCING (CONTROL) AND ONLINE COAL FINENESS MEASURING SYSTEM FOR COMBUSTION OPTIMISATION IN A THERMAL BOILER Suresh G Chandwani1, Dr Francesco Turoni2, Reinhardt Kock2, Dr Michael Haug2, Dr Michael Schreiber2 1NSGuzder Company Pty Ltd, Neville House, Currimbhoy Road, 2021年8月1日 Yukio et al [7] proposed a model consisting of blending, grinding and classifying processes for pulverizer control Agarawal et al [8] differentiated coal powder into ten size groups, divided the bowl mill into four zones, and developed a unified model Palizban et al [9] derived nonlinear differential mass equations of raw coal, recirculation coal and suspension coal in Coal mill model considering heat transfer effect on mass Multiobjective Optimization of Coal Mill Outlet Temperature Control Using MPC Zengji Zhang1, Yicheng Zhang2, Wei Shen2, BOE Xukang Lyu3,∗ 1Sinoma International Engineering Co, Ltd, Nanjing, Jiangsu, China 2College of Computer Science and Technology, Zhejiang SciTech University, Hangzhou, Zhejiang, China 3Zhejiang New Rise Digital Technology Co, Ltd, MultiObjective Optimization of Coal Mill Outlet Temperature Control As a consequence of these problems, coal mill control and fault detection have been the main focus in many research activities DELTAPAmbar Pressure difference between mill inlet and primary air collector 10 ðÞMPPPINAVG kPa PPPINAVGkPa FUEL2POWER Proportion FUELDMD/MW, possible estimation of fuel qualityDetection of Malfunctions and Abnormal Working Conditions of a Coal Mill
.jpg)
Hequ Power Plant Coal Mill Differential Pressure Level Meter
Hequ Power Plant Coal Mill Differential Pressure Level Meter Xiaodong Gao Shenhua Guoneng Power Hequ Power Generation Co Ltd, Hequ Shanxi Received: Feb 7th, 2017; accepted: Feb 20th, 2017; published: Feb 23rd, 2017 Abstract This paper introduces the working principle of the coal mill differential pressure level DifferenThe counter pressure reduces the noise generated by the mill and is adjustable depending on the coal properties and required coal fineness During operation, both pressures are adjusted proportionately to the feeder speed by means of pressure control valves to achieve an optimized grinding force characteristic throughout the mill load rangeCoal Pulverizer Design Upgrades to Meet the Demands of Low 2016年8月1日 The output of the power control strategy is then combined with the primary air pressure setting of the original control circuit to obtain a new and the respective openings of each group will be different during operation due to the different coal feeding rate of each mill Therefore, x 2 and x 1 are expressed as the largest hot A powersaving control strategy for reducing the total pressure 2016年4月1日 Wang et al 1 applied principal component analysis and support vector machine to analyze the spectrum of 199 different types of coal samples, proposed a high accuracy and speed coal sample Modeling and control of ball mill system considering coal moisture
.jpg)
COAL GRINDING IMPS: more than meets the eye Gebr Pfeiffer
difference between an MPS mill for solid fuels and other MPS mills lies in its pressureshock resistance Mill and classifier housing, feed unit and expansion joints are designed pressureshock resistant To avoid accumulations of coal dust as a source of spontaneous combustion, all surfaces in the grinding and classifying• Coal characteristics profoundly influence risk – Lower rank coals are generally more easily ignited inside the coal mill – High volatile matter and highly reactive coals encourage preignition inside the mill – Higher moisture content requires temperature extremes inside the millMill Inerting and Pulverizer/Mill Explosion Mitigation2013年3月1日 This is in contrast to the SISO controller design, which is not straightforward and the interaction between control loops have to be considered Therefore, for coal mill control the application of NMPC is a recommended solution 8 Conclusions In the present paper, the modeling of a vertical roller pressure coal mill was addressedNonlinear coal mill modeling and its application to model 2022年12月3日 Coal seams are often affected by gas effects in addition to static and dynamic superimposed loads in the process of coal mining Understanding the mechanical properties and energy dissipation of impacted coal under different initial gas pressures is extremely important Therefore, dynamic compression experimentation of coal samples was conducted using a self Dynamic Compression Behavior of Coal Under Different Initial
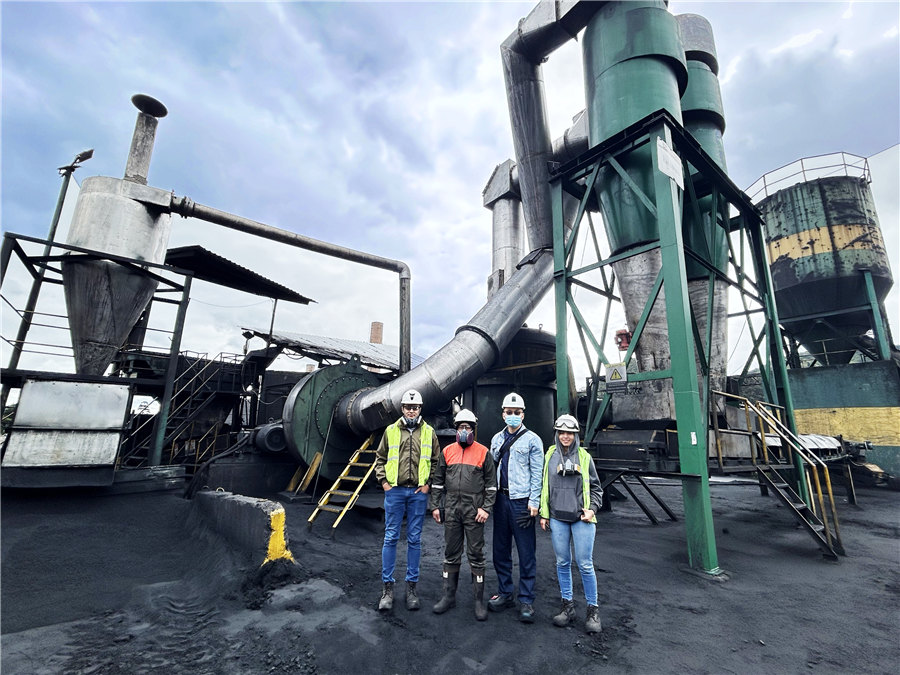
Detection of Malfunctions and Abnormal Working Conditions of a Coal Mill
2018年5月2日 As a conseque nce of these prob lems, coal mi ll control an d fault detec tion have be en the main focus in many rese arch activi ties DELTAPAmbar Pressure difference between mill inlet and2022年7月26日 diagnosis of the major faults in the coal mill system [4] Fan et al, designed a knowledgebased finegrained coal mill operator support/control system for coal plants The system is composed of mathematical coal mill model and expert knowledge database and has the ability of parameter estimation, coal mill performance monitoring, fault diagnosisFault Diagnosis of Coal Mill Based on Kernel Extreme Learning 2013年3月1日 Coal mills play an important role in the overall dynamic response of coal fired power plants and there is significant potential to improve the load ramp rates of coal fired power plants through improvements of coal mill control strategies This potential can be employed to compensate for the power fluctuations generated by renewable but intermittent energy Nonlinear coal mill modeling and its application to model predictive 2013年12月1日 The paper presents development and validation of coal mill model (including the action of classifier) to be used for improved coal mill control The model is developed by using the mass and heat balance equations of the coal mill Genetic Algorithm is used to estimate the unknown parameters that are used in the model validationModeling and Control of Coal Mill ScienceDirect
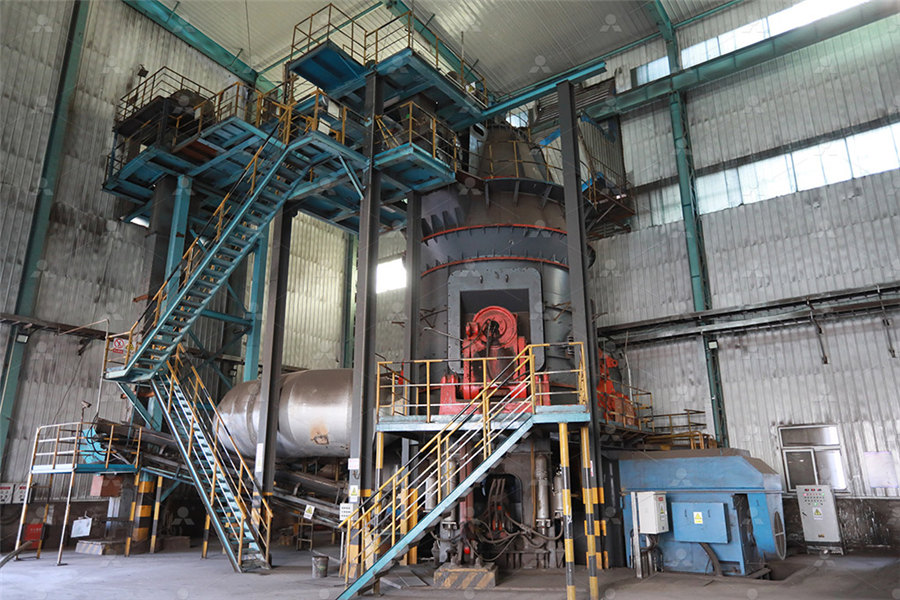
A unified thermomechanical model for coal mill operation
2015年11月1日 From Fig 3, Fig 4, Fig 5, Fig 6 and Table 5, it can be seen that the measured outputs of the proposed model (mill differential pressure, current, outlet temperature) approach the onsite values very well and unmeasured outputs (pulverized fuel flow, mass accumulated inside the mill, outlet moisture content, moisture in accumulated coal inside the mill, mill 2024年2月1日 Fig 20 shows the difference in Δb s between adopting the revised control schemes and the typical CCS control method with different throttling schemes when V e is 20 % Pe min −1 The difference in Δb s ranges from 038 to 157 g kW −1 h −1 When selecting the throttling scheme Ⅲ, the minimum of ΔΔb can be obtainedEnhancing the flexibility and stability of coalfired power plants by Our ATOX® Coal Mill has large rollers with great grinding capability of virtually all types of raw coal The rollers work harmoniously with a highlyefficient separator and feed sluice to consistently and reliably deliver coal meal to your desired fineness and moisture levelATOX® Coal Mill FLSmidth Cementet al 2017) In a coalfired power plant, one of the main equipment is the coal mill, whose effectiveness influences mainly the whole power plant performance (Shah, Vuthaluru, andAn investigation of performance characteristics and energetic
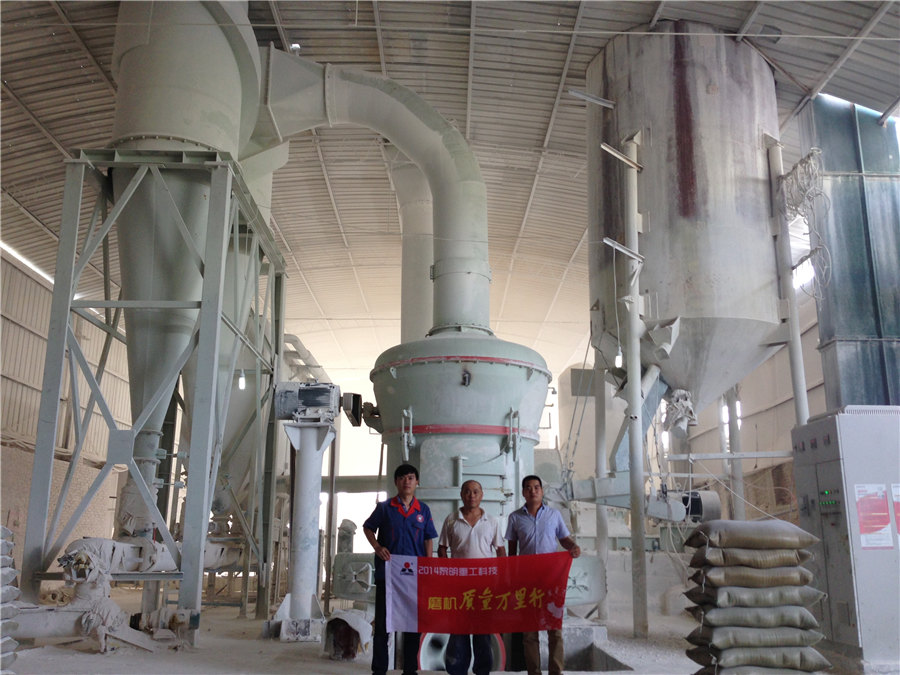
Coal Mill Modeling for Monitoring and Control
motor p ow er consumption, and the mill pressure drop Fig 2 sho ws an example of measured mill pressure drop and unit load, compared to mo del results F urthermore the mo del is capable of pro viding estimates for unmeasured coal mill outputs suc h as the pulv erized fuel o w and neness and the amoun t of pulv erized fuel stored inside the mill