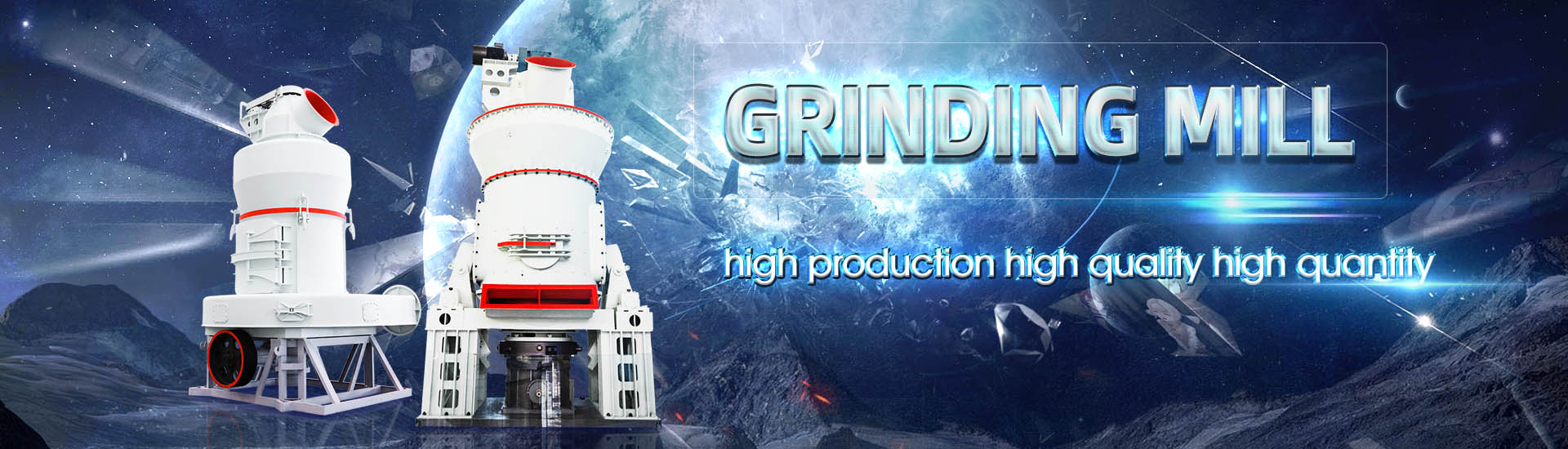
Refined iron oxide processing technology
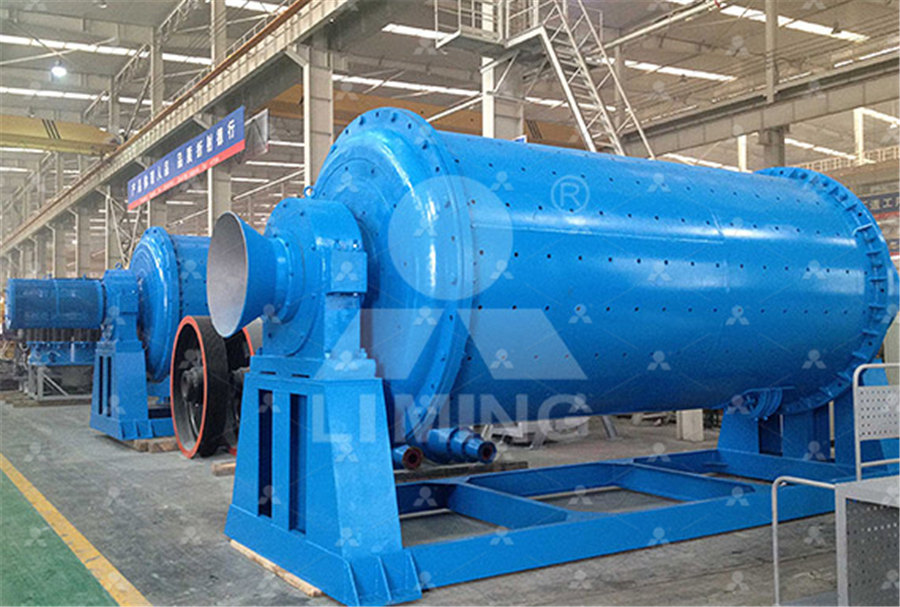
From Ore to Iron with Smelting and Direct Iron
2017年10月17日 The Hismelt process employs a single smelt reduction vessel (SRV) where iron oxide fines are injected deep into hot metal melt, which 2024年3月20日 Electrochemical production of iron metal can support a decarbonized process for steelmaking Here, we report a lowtemperature, electrochemical cell that consumes lowcost and abundant iron oxide, salt, Electrochemical chloriron process for iron production 2023年2月9日 The process is designed to work with lowcost intermittent renewable electricity and cheaper, lowgrade iron ores to produce lowtemperature iron (LTI) Electra CoFounder Producing green iron with a zeroCarbon electrochemical Process S2024年2月8日 Extracting iron from iron oxide ores— one of the first steps in steelmaking —typically involves roasting a mixture of the crushed ore and coke in a blast furnace at temperatures of up to 1,200 °C Both the burning of coal to Producing iron from salt water and iron oxide
.jpg)
New Processing Route for Production of Fine Spherical Iron Powder
In this paper the powder properties and sintering results of a fine spherical iron powder which is produced by using iron oxide as a byproduct of steelmakers and a patented hydrogen 2023年3月14日 Zou et al electrochemically reduced iron oxide to iron in strong alkaline solutions at a low temperature and studied the influence of experimental parameters, such as Research progress in the preparation of iron by electrochemical 2024年2月15日 Iron ore, refined through orebeneficiation techniques, yields ironore concentrate powder, which is directly utilized as the raw material in fluidizedbed reactors To Direct reduction of iron to facilitate net zero emissions in the steel 2023年12月11日 Direct reduction ironmaking is a process that involves reducing iron ore to obtain metallic iron in a reaction vessel using gas or solid reducing agents at a temperature HydrogenBased Reduction Technologies in LowCarbon
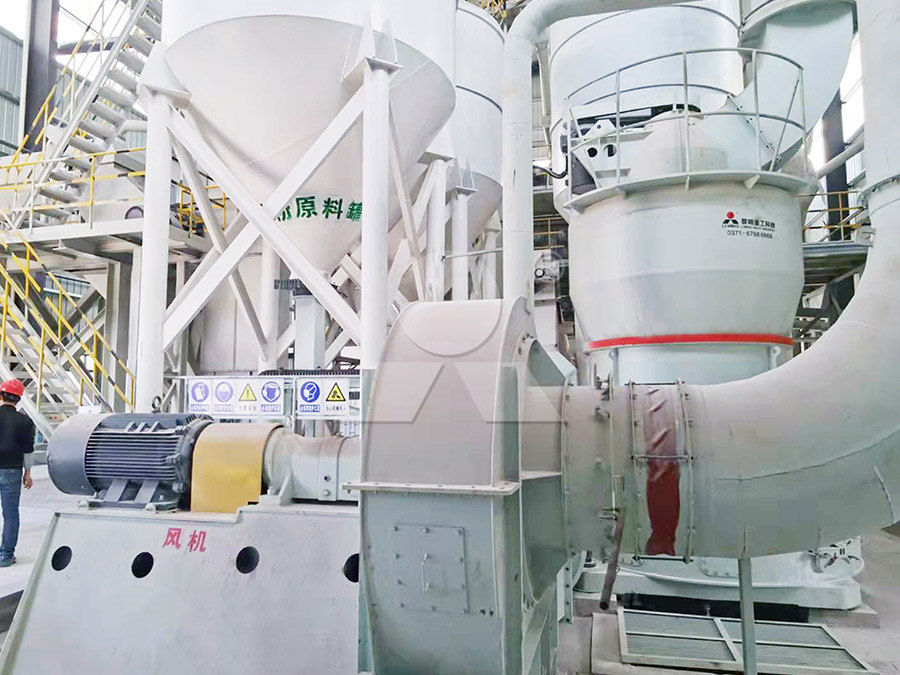
ROSIE—Revolutionizing Ore to Steel to Impact Emissions
that would eliminate carbon dioxide emissions from the ironmaking process The proposed technology eliminates the coke used in traditional b ast furnaces and removes the energy 2024年1月1日 Ironmaking is the process of refining iron oxides in iron ores into metallic iron The earth’s crust is rich in iron, accounting for 42% of the total elements, ranking fourth With no Ironmaking SpringerLink2023年4月5日 The blast furnace and direct reduction processes have been the major iron production routes for various iron ores (ie goethite, hematite, magnetite, maghemite, siderite, etc) in the past few decades, but the Recent Trends in the Technologies of the Direct titanium processing, the extraction of titanium from its ores and the preparation of titanium alloys or compounds for use in various products Titanium (Ti) is a soft, ductile, silvery gray metal with a melting point of 1,675 °C (3,047 °F) Owing to Titanium processing Technology, Methods, Facts
.jpg)
From Ore to Iron with Smelting and Direct Iron
2017年10月17日 Smelting Reduction Figure 2: The smelt reduction vessel (SRV) is the core technology component of the Hismelt process Source: RioTinto While years of ironmaking technology innovations have optimized blast vanadium processing, preparation of the metal for use in various products Vanadium (V) is a grayish silver metal whose crystal structure is a bodycentred cubic (bcc) lattice, with a melting point of 1,926° C (3,499° F) The metal is used principally as an alloying addition to highstrength lowalloy (HSLA) steels and, to a lesser extent, in tool steels and iron and steel castingsVanadium processing Extraction, Uses Applications BritannicaThe iron separated from the surrounding rock but never quite melted Instead, it formed a crusty slag which was removed by hammering This repeated heating and hammering process mixed oxygen with the iron oxide to produce iron, and removed the carbon from the metalHow iron is made material, manufacture, making, history, used 2020年12月15日 Based on the technical conditions of the ancient times, there were two common ways to reduce iron ore to iron One is lowtemperature solid reduction, which uses wood or charcoal as fuel and reducing agent to reduce iron oxide to loose sponge iron at a lower temperature (about 1,000 degrees Celsius) in a bowl furnace or a lower shaft furnacePig IronBased Steel Smelting Technology SpringerLink
.jpg)
New Sustainable, Scalable and OneStep Synthesis of Iron Oxide
2021年3月20日 This work introduces an innovative, sustainable, and scalable synthesis of iron oxides nanoparticles (NPs) in aqueous suspension The method, based on ion exchange process, consists of a onestep procedure, time and energy saving, operating in water and at room temperature, by cheap and renewable reagents The influence of both oxidation state of the 2016年3月30日 In book: Encyclopedia of Iron, Steel, and Their Alloys (pppp 10821108) Chapter: i) Direct Reduced Iron: Production; Publisher: CRC Press, Taylor and Francis Group, New York(PDF) i) Direct Reduced Iron: Production ResearchGate2024年2月15日 Graded pelletization effectively addresses issues such as low quality in the production of iron oxide pellets This technology is achieved through a twostage process using a highspeed agitator in the initial granulation phase and a drum mixer In the first stage, the fine material is pelletized with water and lime in the form of microparticlesDirect reduction of iron to facilitate net zero emissions in the steel 2023年6月8日 Copper metallurgy is the process in which copper metal is extracted from copper ore and a little over 10 of them are of industrial mining value, which are classified into three types: copper sulfide, copper oxide, Its main components are copper, iron, and sulfur The sum of the content of the three components accounts Copper Metallurgy SpringerLink
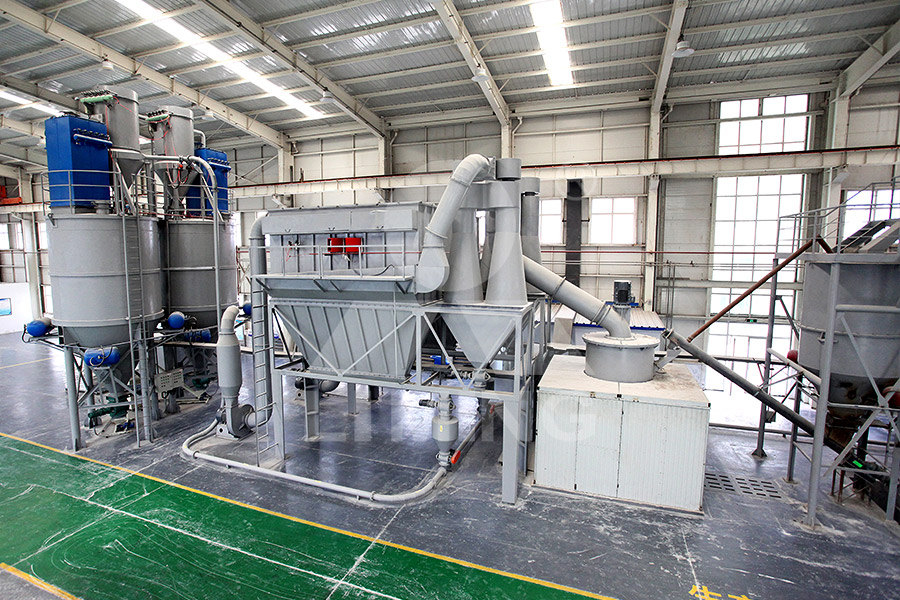
A Review on Processing of Electric Arc Furnace Dust
2022年1月14日 The iron oxides are reduced to direct reduced iron under a strong reducing atmosphere, and the per cent of metallization goes up to 90% in 15–20 min of time [ 25 ]2015年7月1日 Aggregation behaviour was observed within pH 3–45 for synthetic iron oxide NPs with a maximum particle size reading of 1398 ± 1173 dnm, while for natural iron oxide nano colloids, the Synthesis, Characterization and Applications of Iron 2021年12月16日 For several decades, the metallurgical industry and the research community worldwide have been challenged to develop energyefficient and lowcost titanium production processes The expensive and energy Titanium: An Overview of Resources and 2022年8月23日 Iron oxide nanoparticles (IONPs) are found within the size range of 1–100 nm in nanomaterials and have a diverse range of applications in fields such as biomedicine, wastewater purification, and (PDF) An Overview of the ReductionSmelting Process of Iron
.jpg)
Nickel processing Extraction, Refining, Alloying Britannica
Nickel processing Extraction, Refining, Alloying: The extraction of nickel from ore follows much the same route as copper, and indeed, in a number of cases, similar processes and equipment are used The major differences in equipment are the use of highertemperature refractories and the increased cooling required to accommodate the higher operating temperatures in nickel During the process, carbon restores iron oxide The relatively low temperature of the process and the high content of iron slag prevented the carbonization of the metal, resulting in the production of lowcarbon iron The resulting iron accumulates at the bottom of the furnace and is called "kritsa" Once extractedModern and New Technologies in Copper ProductionCopper processing is a complicated process that begins with mining of the ore (less than 1% copper) and ends with sheets of 9999% pure copper called cathodes, which will ultimately be made into products for everyday useThe most common types of ore, copper oxide and copper sulfide, undergo two different processes, hydrometallurgy and pyrometallurgy, respectively, Copper Mining and Processing: Processing Copper Ores2020年6月10日 224 Direct Reduction of Iron Oxide by Solid Carbon The direct reduction process of iron oxide by solid carbon is highly endothermic in nature and occurs when the molten slag flows over incandescent coke in the bosh region at a temperature above 1000 °C Therefore, the corresponding reaction can be written as follows:Iron and SteelMaking Process SpringerLink
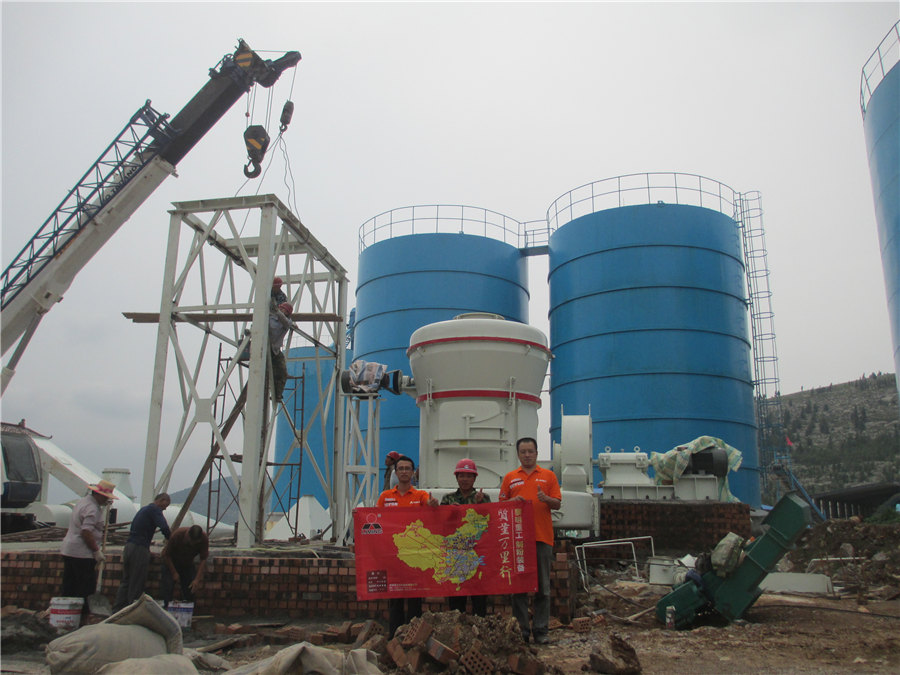
Removal of Iron from Hard Zinc for Production of Refined Zinc
As the primary South African metallurgical technology provider, Mintek became involved in the evaluation of a pyrometallurgical process for the recovery of zinc from the Gamsberg deposit This includes the patented Enviroplas® process for the treatment of zinc bearing waste materials [25] New Jersey process is a pyrometallurgical technologySteel mill with two arc furnaces Steelmaking is the process of producing steel from iron ore and/or scrapIn steelmaking, impurities such as nitrogen, silicon, phosphorus, sulfur, and excess carbon (the most important impurity) are removed from the sourced iron, and alloying elements such as manganese, nickel, chromium, carbon, and vanadium are added to produce different Steelmaking Wikipedia2021年3月8日 BFBOF route employs a blast furnace (BF) to reduce the iron ore to molten iron and subsequently refined to steel in a basic oxygen furnace (BOF) As the dominant technology for primary steelmaking, BFBOF route LowCarbon Production of Iron Steel: Technology 2019年3月15日 In the paper are shown the history, processing and applications of hematite Hematite is an oxide of iron having the composition Fe2O3 Pure hematite, also called “red ore” contains 70% Fe(PDF) Hematite Processing and Applications
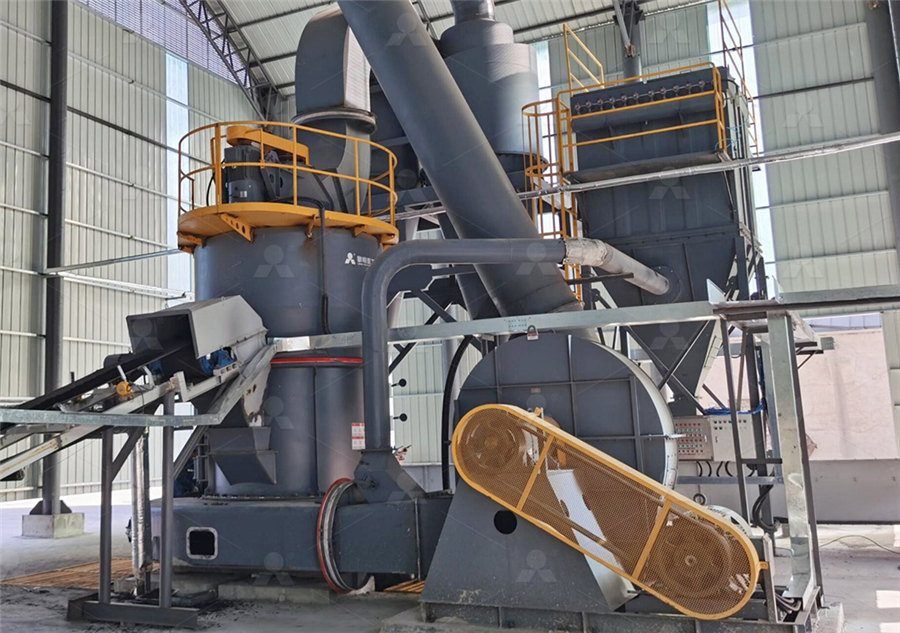
Molybdenum processing Extraction, Applications Uses
molybdenum processing, preparation of the ore for use in various products Molybdenum (Mo) is a white platinumlike metal with a melting point of 2,610 °C (4,730 °F) In its pure state, it is tough and ductile and is characterized by moderate hardness, high thermal conductivity, high resistance to corrosion, and a low expansion coefficientWhen alloyed with other metals, molybdenum cobalt processing, preparation of the metal for use in various products Below 417 °C (783 °F), cobalt (Co) has a stable hexagonal closepacked crystal structureAt higher temperatures up to the melting point of 1,495 °C (2,723 °F), the stable form is facecentred cubic The metal has 12 radioactive isotopes, none of which occurs naturallyCobalt processing Uses, Supply, Facts Britannica2023年2月9日 reactant for reducing iron oxide to iron metal Approximately 90% of the steel technology 60°C Processing Temperature Commercial and LowGrade Iron Ore Intermittent Renewable Electricity Grid Balancing CoRefined Minerals (Primary Iron Ore Impurities) EAF Steelmaking (Existing Infrastructure) >999% Iron Plates Oxygen Created Producing green iron with a zeroCarbon electrochemical Process S2008年1月1日 Finally, potential applications of supercritical fluid technology for the processing of iron oxide nanoparticles are presented Physical and Chemical Properties of Hematite, Processing of iron oxide nanoparticles by supercritical fluids
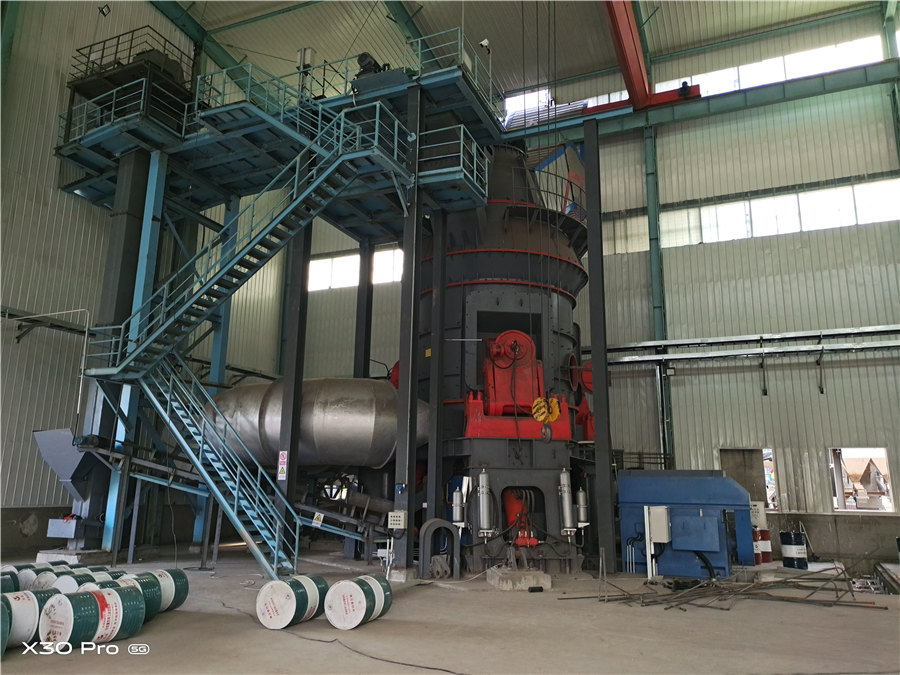
A study of selective precipitation techniques used to recover refined
2017年4月1日 Resulting iron oxide pigment powders were analyzed with Xray diffraction (XRD) and energy dispersive spectroscopy (EDS), and visually evaluated for color and coating ability Drying duration resulted in increased redness in paint streaks and enhanced crystallinity, as amorphous phases of iron oxide transformed into hematite2023年12月19日 Researchers of Karlsruhe Institute of Technology (KIT) and the SMS group have developed a new process to reduce CO2 emission of worldwide steel production by several hundred million tons per year It is based on modernizing blast furnace technology with moderate investments and has already been demonstrated successfully in a pilot plant The researchers New process enhances sustainability of pig iron productionFind Iron Oxide Processing stock images in HD and millions of other royaltyfree stock photos, illustrations and vectors in the Shutterstock collection Thousands of new, highquality pictures added every dayIron Oxide Processing photos Shutterstock2023年2月23日 The carbon both acts as fuel to heat the furnace, and as a chemical reactant: the oxygen in the air reacts with carbon in the coke to form carbon dioxide, which in the heat of the furnace quickly becomes carbon monoxide The carbon monoxide, in turn, reacts with the iron oxide to form iron and CO2 (called “ reduction ” of the oreThe Blast Furnace: 800 Years of Technology Improvement
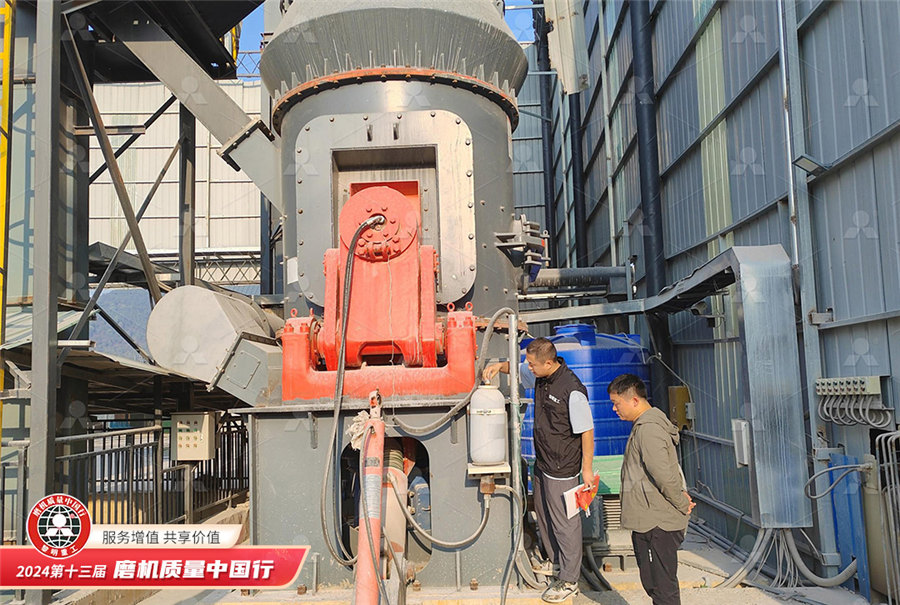
DEVELOPMENTS IN HYDROMET PROCESSING OF NICKEL LATERITES
manganese and iron with magnesia, and evaporative crystallization of magnesium sulphate which is thermally decomposed The resulting sulphur dioxide is utilized for acid production and in the first leaching stage, while magnesia is used in the process and can be a possible byproduct Iron oxide is also a possible byproductCast iron has already been mentioned above This section deals with the types of iron and steel which are produced as a result of the steelmaking process Wrought iron: If all the carbon is removed from the iron to give high purity iron, 233: Metallurgy of Iron and Steel Chemistry A New Refining Process for Iron Oxide Using Iron Ore and Its Application to Hard Ferrites S Nakashima, Y Ikeda, S Hirose, H Nakamura manufacturing technology of refined iron ore and the features of the hard ferrite produced with it are described 100 90 A new refining process for iron oxide using iron ore and its 2021年1月4日 Until the late 19th century iron oxide pigments were obtained wholly from natural materials, generally with little alteration other than physical purification In some cases roasting or calcination was also carried out However, beginning in the first part of the 20th century, chemical methods were developed for synthetic production of commercial iron oxidesIron Oxide Pigments 911Metallurgist
.jpg)
Iron Separation from Bauxite Through SmeltingReduction Process
2017年2月12日 The products of the digestion step are separated in a clarification process where undissolved impurities such as silica and iron settles as mud, which is called red mud residue []Red mud is one of the largest industrial byproducts today (3 billion tons in 2010) []As it does not have a commercial value, several different methods is used for its deposition, including 2024年8月5日 The transition to green steel production is pivotal for reducing global carbon emissions This study presents a comprehensive technoeconomic analysis of various green steel production methods, including hydrogen reduction and three different electrolysis techniques: aqueous hydroxide electrolysis (AHE), molten salt electrolysis, and molten oxide electrolysis Economics of Electrowinning Iron from Ore for Green Steel aluminum processing, preparation of the ore for use in various products Aluminum, or aluminium (Al), is a silvery white metal with a melting point of 660 °C (1,220 °F) and a density of 27 grams per cubic cm The most abundant metallic element, it constitutes 81 percent of Earth’s crust In nature it occurs chemically combined with oxygen and other elementsAluminum processing History, Mining, Refining, Facts2021年7月2日 The epsilon phase of iron(III) oxide exhibits many desirable properties for application in 6G technology, but synthesizing the material is complex Researchers in Russia refined a silicabased synthesis method that is reproducible, cheap, easily implemented, and only takes a day to performMaterials for 6G technology: Scientists refine synthesis of rare iron
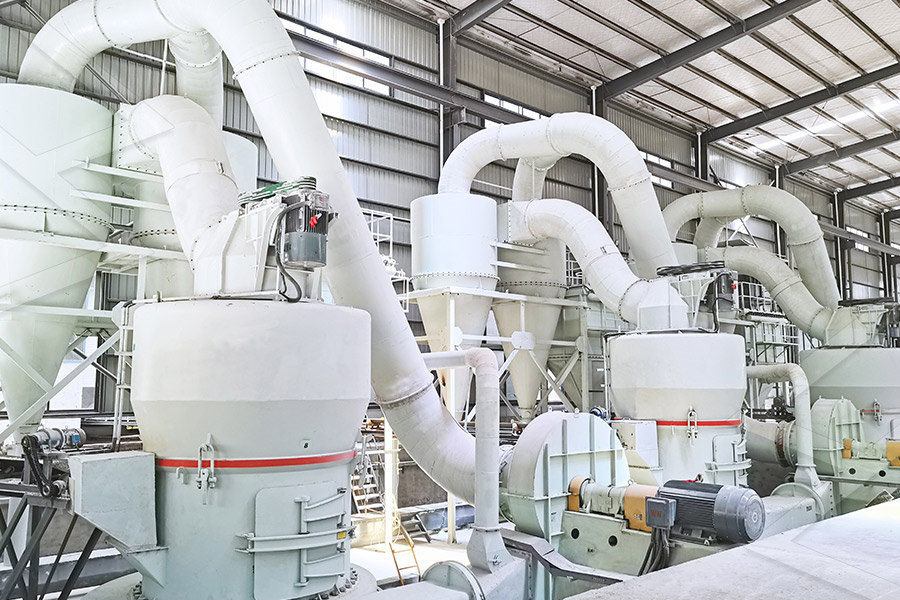
Chromium processing Extraction, Uses Applications Britannica
Chromium processing, preparation of the ore for use in various products Chromium (Cr) is a brilliant, hard, refractory metal that melts at 1,857 °C (3,375 °F) and boils at 2,672 °C (4,842 °F) In the pure state it is resistant to ordinary corrosion, resulting in its application as an electroplated12 The Open Mineral Processing Journal, 2009, 2, 1216 18748414/09 2009 Bentham Open Open Access Removal of Iron from Hard Zinc for Production of Refined Zinc MA Barakat* Central Metallurgical R D Institute, PO Box 87 Helwan 11421, Cairo, EgyptRemoval of Iron from Hard Zinc for Production of Refined Zinc