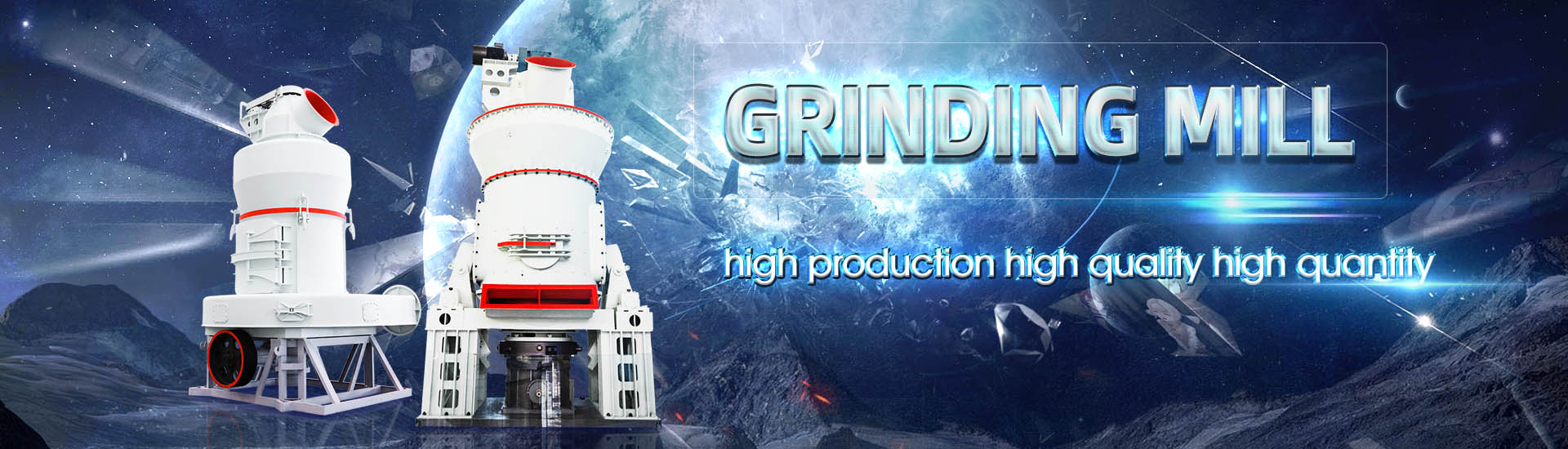
Cement products grinding and deep processing equipment
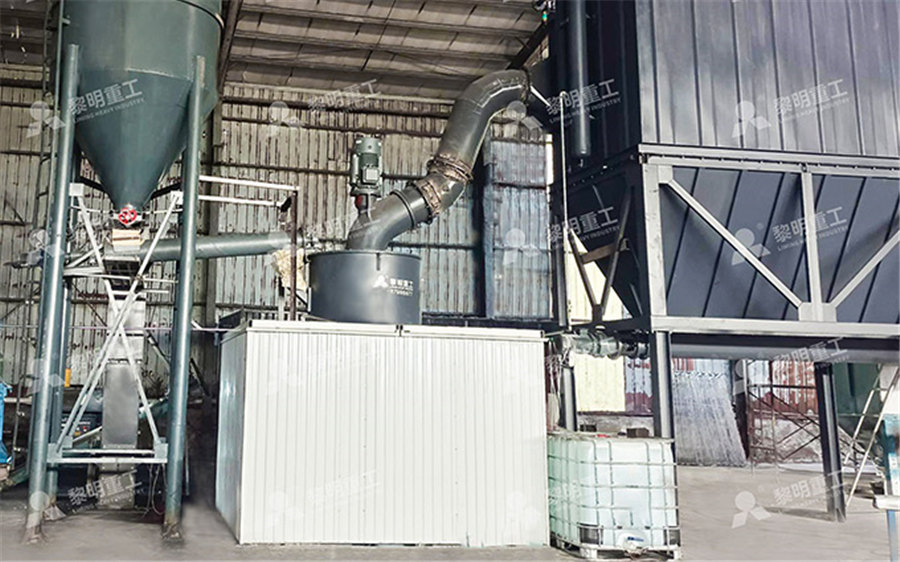
polycom® HPGR cuttingedge technology in the cement industry
Modern polysius® grinding systems for cement applications are often designed as combi grinding systems consisting of a polycom® HPGR, a staticdynamic sepol® separator, and a ball mill The cement plant of the future will have various touchpoints for predictive How to create the cement plWith our marketleading MULTICOR cement processing solutions, we help you meet the defining challenges in today’s marketplace, by dramatically reducing your CO2 emissions in line with new regulations – and ensuring the quality Cement processing equipment QlarThe cement industry uses a wide range of different systems in raw material, coal, and cement grinding While new plants mainly focus on highly energy‑efficient systems, using roller Thomas Holzinger, Holzinger Consulting, grinding system
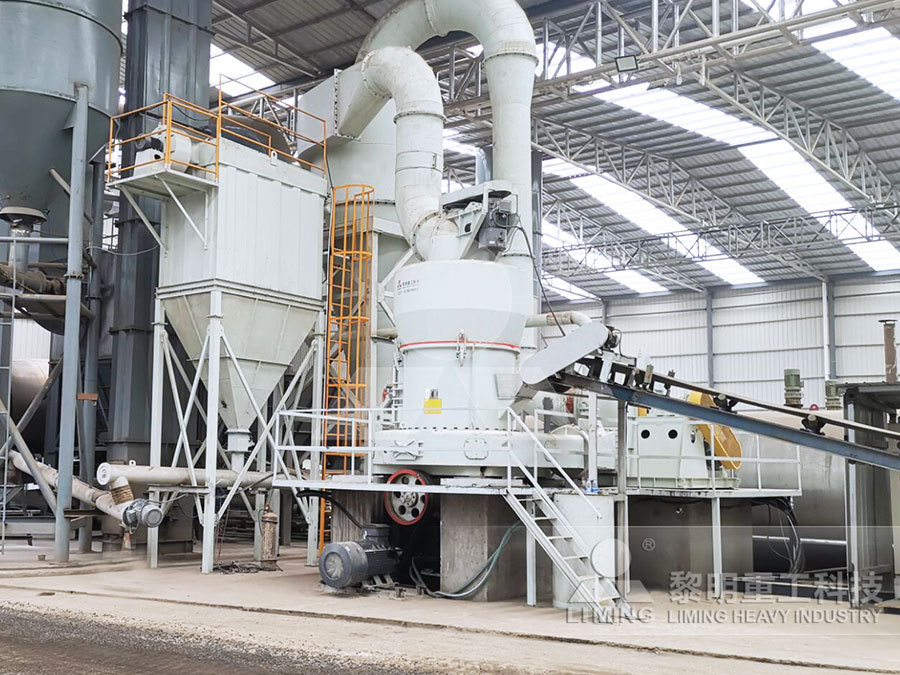
CEMENT GRINDING SYSTEMS INFINITY FOR CEMENT EQUIPMENT
2017年4月21日 Grinding with propylene glycol generates approximately 800 Cm 2 /gram cement more surface than grinding without an aid, given the same energy consumption the most Highcapacity cement grinding solutions are essential for meeting today’s production demands while optimizing energy use and maintaining product quality Technologies like vertical roller HighCapacity Cement Grinding Solutions: Enhancing Efficiency Grinding cement clinker (and gelling agent, performance tuning materials, etc) is used to grind the cement to the appropriate size (in fineness, specific surface area, etc), optimize cement grain grading, increase the hydration area and Cement Production Line CHAENGProviding a comprehensive guide to the entire cement production process from raw material extraction to the finished product, the industry’s favourite technical reference book is now fully The Cement Plant Operations Handbook International Cement
-2.jpg)
EnergyEfficient Technologies in Cement Grinding
2016年10月5日 In this chapter an introduction of widely applied energyefficient grinding technologies in cement grinding and description of the operating principles of the related equip‐ ments and comparisons over each other in 2017年5月19日 Sustainability of cement products is increased by reducing grinding energy and limiting CO2 emissions Cement additives permit to reach bothe the targetsOverview of cement grinding: fundamentals, additives, What Is Ultra Fine Grinding Mill The ultrafine powder grinding system is a new product independently developed by our company, mainly used to grind and classify various nonmetallic ores in cement plants, such as the grinding of Ultra Fine Grinding Mill Ultra Fine Powder GrinderStage 2: Grinding, Proportioning, and Blending The crushed raw ingredients are made ready for the cementmaking process in the kiln by combining them with additives and grinding them to ensure a fine homogenous mixture The composition of cement is proportioned here depending on the desired properties of the cement Generally, limestone is 80%, and the remaining 20% How Cement is Made Cement Manufacturing Process
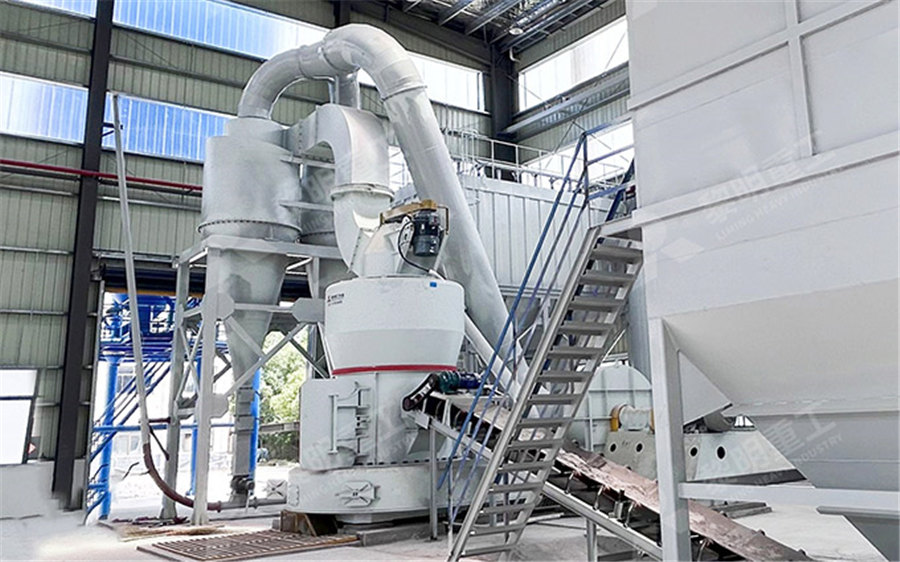
Cement Production Seminar: Grinding
Products Products Crushing Emission control Gas analysis cement plants Work sessions are scheduled to allow for an interactive study of the design, function, and evaluation of grinding systems in a cement plant Cement Production Seminar Ball vertical mill systems and equipment components; Process design basic parameters; Control An Asian cement manufacturer integrated highpressure grinding rolls (HPGRs) into its existing grinding circuit, resulting in a 30% increase in grinding capacity The addition of HPGRs allowed the plant to process harder materials while improving energy efficiency and HighCapacity Cement Grinding Solutions: Enhancing Efficiency 5 Methods, Processes and Equipment Involved in Manufacturing Cement Free download as Powerpoint Presentation (ppt / pptx), PDF File (pdf), Text File (txt) or view presentation slides onlineMethods, Processes and Equipment Involved in Manufacturing CementThe ultrafine grinding system manufactured by AGICO is mainly used for grinding pulverized coal and cement To meet the need for further grinding and 3D printing, in 2015, our company built an ultrafine powder grinding production line of 12t/d — 20t/d The ultrafine grinding mill is the important equipment in this production lineGrinding Mill Grinding Equipment Cement Mill AGICO
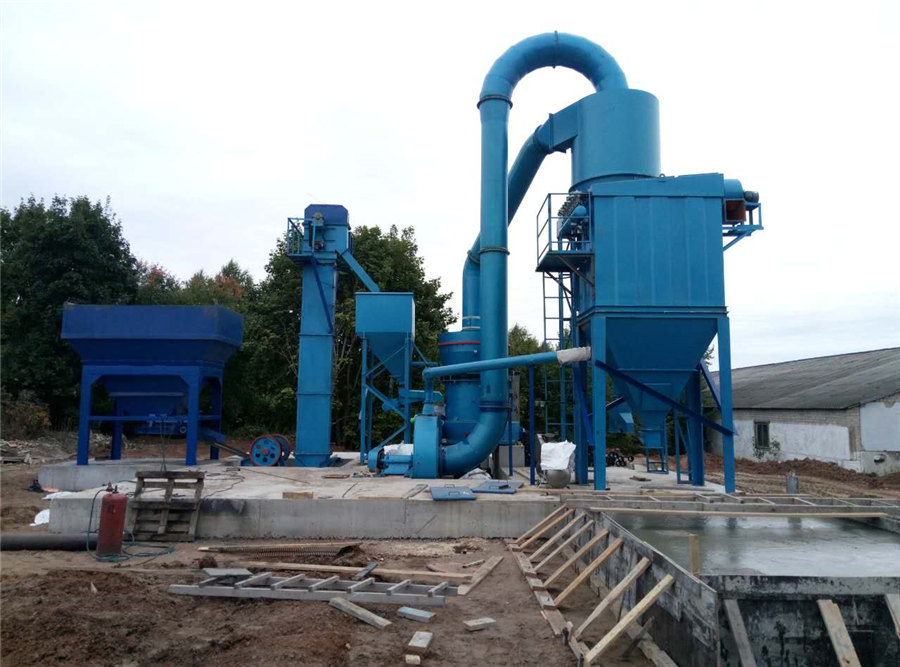
(PDF) A comprehensive review on the grinding process:
June 2022; ARCHIVE Proceedings of the Institution of Mechanical Engineers Part C Journal of Mechanical Engineering Science 19891996 (vols 203210) 236(2):年3月1日 We use deep learning models as extractors to identify cement processing equipment from HR image chips Admittedly, confusion exists between cement processing equipment and other substrates or industries We note that the performance of the deep learning models is very satisfactory (>95%) in the closedset testingMonitoring global cement plants from space ScienceDirectProducts As a leading global manufacturer of crushing, grinding and mining equipment, ZENITH can offer advanced, reasonable solutions for any sizereduction requirements including crushing or grinding of quarry stone, aggregate and different kinds of minerals ZENITH can provide you the complete stone crushing and beneficiation plantsCrusher, Grinding Mills, Crushing and Grinding Equipment2020年8月25日 Before you send inquiry Please provide us with project information as much as possible: For a complete project: the material availability, the required output capacity, the process technology, your budgetary and financing status, the estimated starting time, etc For singular machinery: the model, the capacity, your budgetary information, other requirements, etcCement Production Process Cement Manufacturing Process AGICO CEMENT
.jpg)
Innovation in Action – Cement Products
2017年6月7日 Typical vibration monitoring solutions for cement plant equipment that’s used for grinding, crushing, materialtransport systems, ball and roller mills, and material separators include: Air compressors Belt drives Fans and blowers Kiln rollers Motor bearings wilcoxon 12 Storage Systems2014年6月10日 Evolution of the cement Process • Wet process easiest to control chemistry better for moist raw materials • Wet process high fuel requirements fuel needed to evaporate 30+% slurry water • Dry process Cement manufacturing process PPT Free DownloadSINOMA Zibo provides not only technical solutions but also cement grinding equipment to help customers build their cement grinding units such as cement mills, cement mill separators, bucket elevators, cement silos, conveyors, Cement Grinding Equipment Cement Mills2019年1月3日 Clinker grinding technology is the most energyintensive process in cement manufacturing Traditionally, it was treated as "low on technology" and "high on energy" as grinding circuits use more than 60 per cent of total energy consumed and account for most of the manufacturing cost Since the increasing energy cost started burning the benefits significantly, Clinker grinding technology in cement manufacturing
.jpg)
Concrete Grinding, Honing and Polishing The Basics
2021年4月19日 Understand the processes, the variables, and the differences between each category of a processed concrete floor Let's go over what a concrete contractor needs to know about grinding, honing, and 2024年1月17日 For nonmetallic mineral grinding, the choice of processing equipment is very important Different types of grinding equipment are suitable for minerals of different attributes, and have specific correspondences to hardness, raw material size, humidity, output, etc, and understanding the working principle, performance characteristics and scope of application of 11 types of grinding equipment commonly used in the nonThe final manufacturing stage at a cement plant is the grinding of cement clinker from the kiln, mixed with 45% gypsum and possible additives, into the final product, cement In a modern cement plant the total consumption of electrical energy is about 100 kWh/t The cement grinding process accounts for approx 40% if this energy consumptionCEMENT GRINDING SYSTEMS INFINITY FOR CEMENT EQUIPMENT2021年8月10日 The grinding process is a dry one and gypsum (a setting retarder) in about 3–6% (wt) is added to the clinker and ground together Compartment mills are used for grinding and the process may be either open or closed circuit The energy requirement for this operation is the highest of all the unit operations used in the manufacture of cementCement and Clay Products Technology SpringerLink
.jpg)
EnergyEfficient Technologies in Cement Grinding
2016年10月5日 In this chapter an introduction of widely applied energyefficient grinding technologies in cement grinding and description of the operating principles of the related equip‐ ments and comparisons over each other in terms of grinding efficiency, specific energy consumption, production capacity and cement quality are given A case study per‐ formed on a FIGURE 43 Interface between the waste management and recycling industry and the cement plants (Reproduced from Cement International, Storing, metering and conveying solid secondary fuel—Design basis and equipment, Cement International, Vol 5, 6/2007 43–53 With permission from Cement International and Schenck Process GmbH)Alternative fuels and raw materials INFINITY FOR CEMENT EQUIPMENTHowever, with the continuous improvement of equipment and technology in recent years, this system has also been applied to the cement grinding process This system not only has higher requirements for equipment but also requires Cement Grinding Plant Expert Cement Grinding 2023年12月17日 Technologies for multistage processing in the agrotechnical industry are actively developing today, allowing us to offer a highquality product to the end consumer In Russia, such areas are still being formed, but there Deep processing of grain: technologies, equipment
.jpg)
Modern Processing Techniques to minimize cost in Cement
The power used for the actual grinding process while grinding raw materials, depends mainly on the hardness of raw materials and the type of mill used, ie ball mill or vertical roller mill Typically, the motor of the ball mill consumes about 14 – 15 kWh/ ton of raw mix whereas the VRM motor uses 7 – 8 kWh/ ton2019年9月27日 Cement equipment refers to the cement making machines that are applied to the cement manufacturing plant Before learning the cement equipment, we learn the process of cement manufacturing process first Cement manufacturing process In general, we can divide the cement production line into three main steps: raw material preparation of cement Cement Euipment Overview Cement Making Machines Cement Cemtech Live Webinar: Advances in cement plant maintenance, 06 November 2024; Cemtech MEA 2025, Dubai, UAE, 0912 February 2025; Cemtech Live Webinar Series 2024; Diary Dates; Conference Event Photos; Conference Archives; Online Training Calcined Clay Cement; Cement Manufacturing Technology; Grinding Milling Systems; Cement Kiln Process 2019 International Lime and Deep Processing Technology Equipment The production and processing of cement has also become a large project that many Limestone deep processing products include calcium oxide, calcium carbonate, etc, among which calcium oxide Shanghai Clirik focuses on the grinding industry and has developed various types of ore grinding equipment and a complete set of grinding How does a limestone grinding mill process cement
.jpg)
Cement Extraction, Processing, Manufacturing Britannica
2024年11月23日 Cement Extraction, Processing, Manufacturing: Raw materials employed in the manufacture of cement are extracted by quarrying in the case of hard rocks such as limestones, slates, and some shales, with the aid of blasting when necessary Some deposits are mined by underground methods Softer rocks such as chalk and clay can be dug directly by Products Products Crushing Emission control Gas analysis and emissions monitoring Ball mill for cement grinding Gear Pinions Girth Gear STANEX Diaphragm for Ball Mill Roller presses Pyroprocess systems and equipment components; Equipment and process design basic parameters; Key process concerns, Cement Production Seminar: PyroprocessGrinding Process: From Rough to Polished – Transforming Concrete Surfaces Transforming a concrete surface from rough and uneven to smooth and polished is an art that involves a meticulous grinding process This transformation not only enhances the aesthetic appeal of the concrete but also extends its durability and functionalityGrinding Process: From Rough to Polished Transforming With 65 years of dedicated experience in cement equipment and fertilizer research, development, and manufacturing, we are your expert and reliable partner for cement plant technology, and equipment, continually striving to enhance production processes and precision Our focus spans metal casting to riveting, welding, machining, and heat treatmentCement Fertilizer Equipment Manufacturer 65+ years Experience
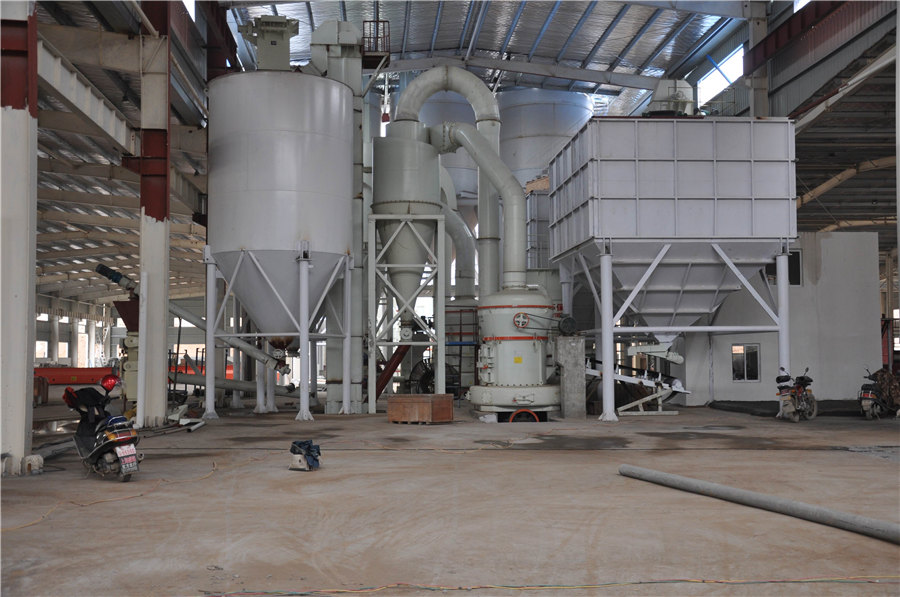
Cement Grinding Plant Manufacturers NT Engitech
Cement Grinding plant The cement grinding unit manufactured by our company combines drying, grinding, powder classification, dust collection and cement packing It can grind cement clinker and process cement mixtures such as The cement plant designed and built according to the new dry process cement production technology has features of highquality, highyield, energysaving, environmental protection, largescale, and automation at the same time Cement Plant for Sale Cement Plant Equipment Calcining and burning or clinkering — the conversion process that takes place within the cement kiln and associated equipment Finish milling — the grinding of clinker to produce cement Raw Materials The main raw material for the manufacture of clinker is a limebearing materialThe Cement Production Process2023年8月21日 ICR looks at the inner workings of grinding mills in the cement industry to understand the technological advancements that are reshaping the landscape against the foreground of sustainability Innovations to enhance the grinding processes are aimed at minimising their environmental footprint while increasing efficiency and performance In CuttingEdge Grinding Solutions Indian Cement Review
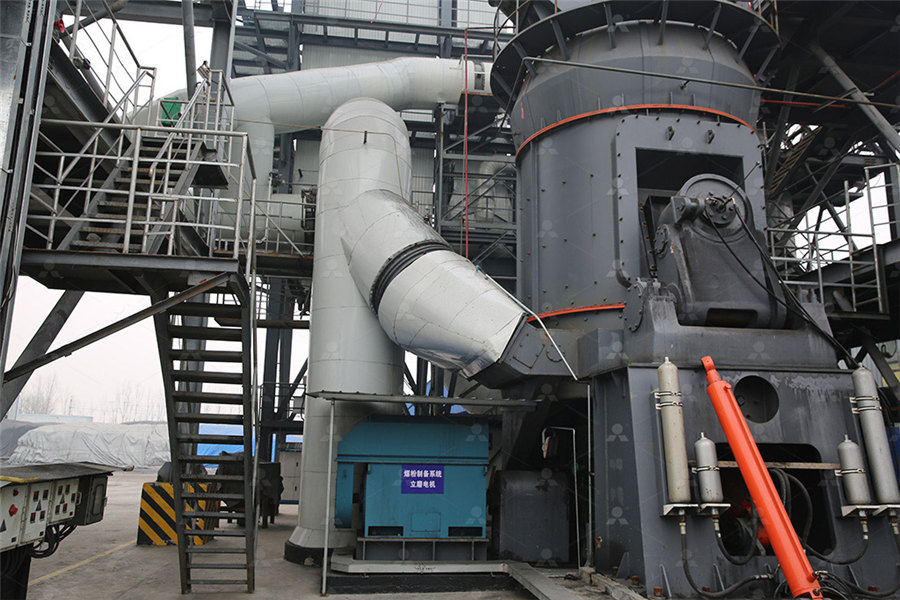
The Cement Plant Operations Handbook International Cement
passivation – 13 Cement quality – 14 Setting time – 15 ASTM cement types and specifications – 16 European EN 197 cement specification – 17 Composite cements (intergrinds and blends) – 18 Supersulphated cement – 19 Calcium aluminate cement (CAC) – 20 Shrinkagecompensating cements (SCC) – 21 ISO 9001:2000 Quality 82015年9月16日 Grinding Aids reduce particle reagglomeration during and after the milling process so improving the yield Strength enhancers push clinker reactivity increasing the use of SCM in blended cements(PDF) Clinker grinding process and cement propertiesWith years of experience in the cement and over 3000 mills sold worldwide, FLSmidth Cement continues to develop its range of efficient milling and grinding solutions This experience and knowhow, as well as close collaboration with our customers, means we Milling and grinding FLSmidth CementGrinding media are used to crush and grind materials in the cement production process, ensuring efficient and smooth operation How often should grinding media be changed? The changing intervals for grinding media typically range from 7,000 to 8,000 hours, depending on the manufacturer and usage prehensive Guide to Grinding Media in Cement Factories
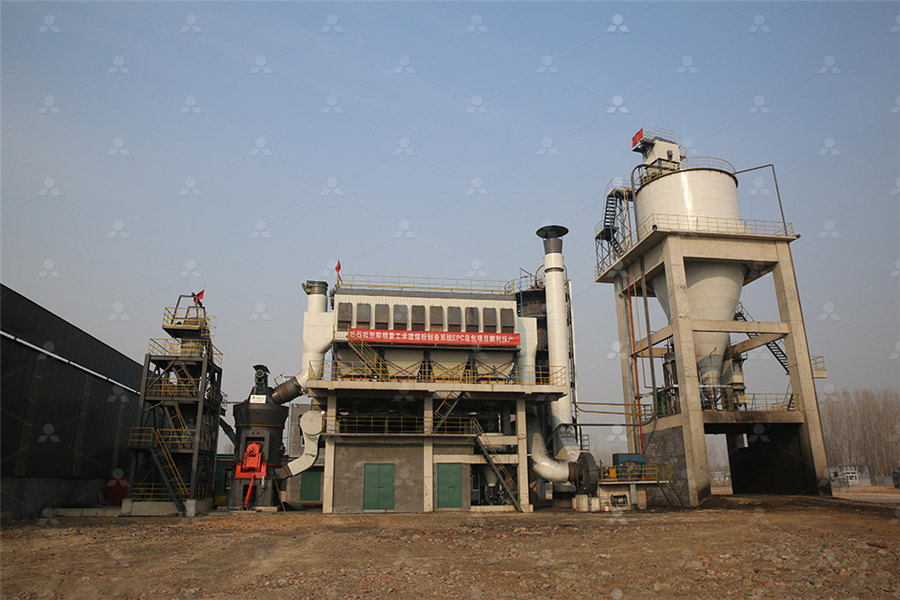
Comprehensive Guide to Cement Kilns: Processes, Types,
Raw Material Proportioning and Grinding Techniques for proportioning and grinding raw materials Equipment used in this stage Word count: 1000; Section 2: Types of Cement Kilns Wet Process Kilns Description and operation Advantages and disadvantages Word count: 1000; Dry Process Kilns Description and operation Advantages and