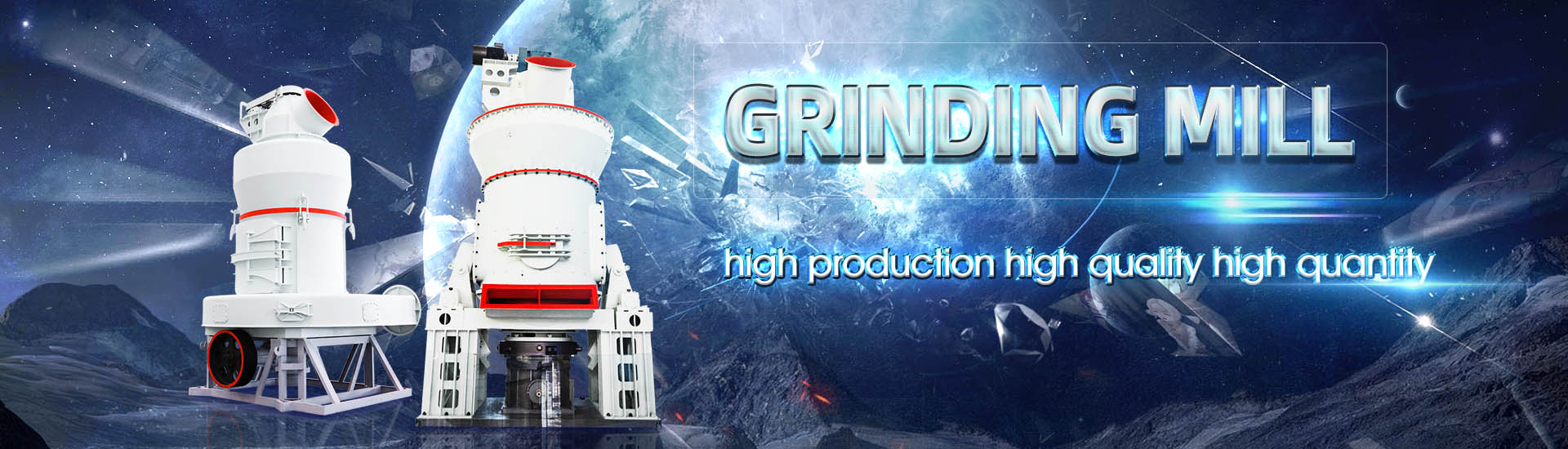
Ore mill shell lining
.jpg)
Mill liners Metso
Optimal mill lining solution for your specific mill Promote safety, improve grinding efficiency, reduce downtime and enhance profitability Metallic, PolyMet™, Megaliner™, Rubber and Orebed™ mill liners for all mill typesdesign to maximize mill availability The shell lining has a major influence on grinding efficiency It transforms the mill rotation into charge motion, and both profile and spacing must be selected Mill lining solutions for horizontal MillProtection of the mill shell from the aggressive impacting and abrasive environment inside a mill is well known as the primary purpose of mill liners Generally the liners fell under the The Selection and Design of Mill Liners 911 Metallurgistmill is equal to twice the number of the feet in the mill shell diameter (eg, a 34ftdiameter mill shell would have 68 shell lifters) This is also called a 2D shell lining Eliminating some shell Semiautogenous grinding (SAG) mill liner design and development
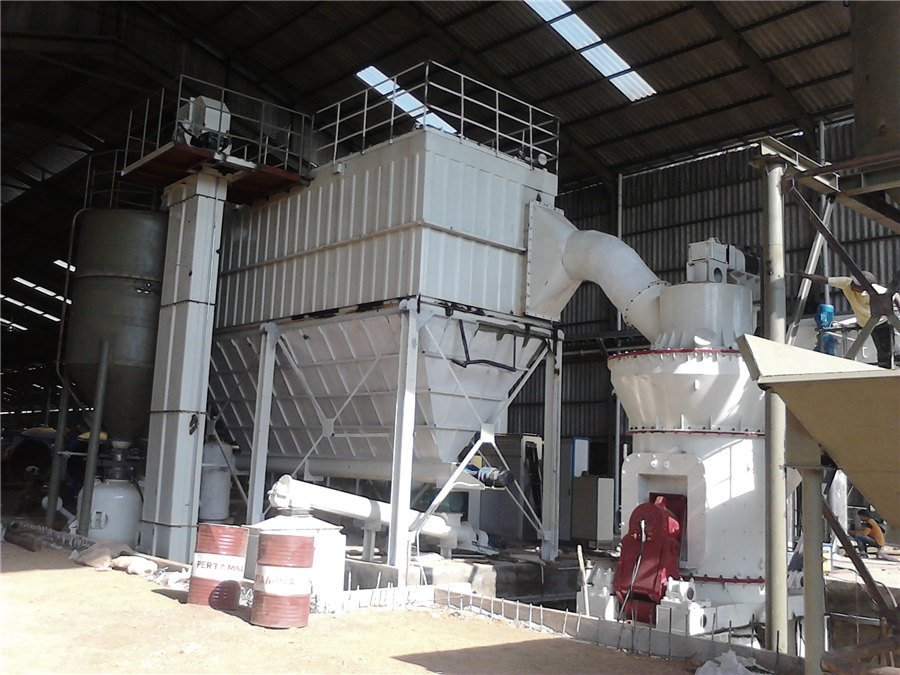
(PDF) Selection and design of mill liners ResearchGate
2006年1月1日 Protection of the mill shell and the end walls from the aggressive impacting and abrasive environment inside a mill is well known as the primary purpose of mill liners (Powell et al,Mill liners protect the mill shell from wear and transfer energy to the grinding charge Careful balance is needed to optimise these differing requirements, as poor liner design has Mill Liners Multotec2020年1月27日 A mill lining system serves two purposes: to protect the mill shell from wear caused by the impact and abrasion of the mill charge, and to elevate and tumble the mill contents in the necessary manner to create a grinding actionKey considerations when selecting a mill lining system2017年2月27日 In the present research, the wear behavior of SAG mill shell liners of Iran Chadormalu iron ore complex has been investigated to obtain the proper solutions to improve Wear and Failure Analysis of SemiAutogenous Grinding Mill Liners
.jpg)
Tega DynaWear Rubber Mill Liner Manufacturer and
The Tega DynaWear® rubber lining system is the preferred lining system for secondary ball mills, regrind mills and scrubbers DynaWear® rubber mill linings are individually designed for your particular working conditions and goals, with Rod Mill The rod mill is loaded with steel bars as grinding media and comprises five parts: cylinder shell, feeding system, discharge system, main bearing, and transmission system It is suitable for both dry and wet grinding to meet customer needs Materials with a Moh's Hardness of 5512 can all be handled by our millOre Grinding Millmill grinds the largesized ore and then a secondary mill grinds the ore from a small size to the desired size The breakage mechanisms that mills use are impact (for coarse grinding), and attrition and abrasion (for finer sizes) These forces not only grind the rock, but they also subject the mill to substantial wear and tear Applying theseThree factors that determine the wear life and performance of mill 2015年8月6日 The amount of unground material will slowly increase until the mill can no longer grind the bigger ore Instead, three design concepts based on rubber as a lining material will be discussed These are combination liners, Grinding Mill Liners 911Metallurgist
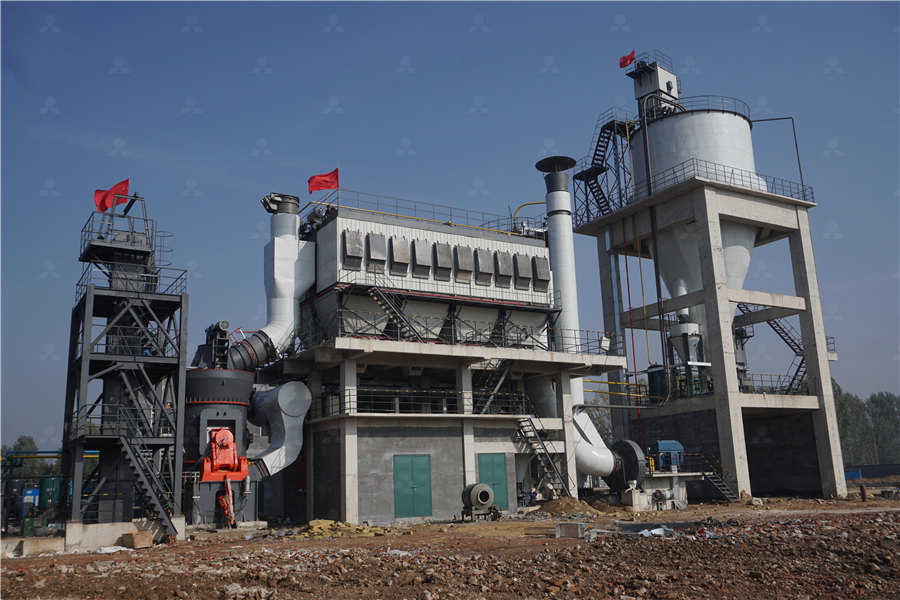
Rubber mill liners Pioneering rubber mill linings Metso
The Mill lining protects the equipment and has a large impact on mill performance Grinding is a tough process, especially when grinding abrasive ores, and the mill liners plays a crutial role Skega Life rubber will give you up to 25 % longer wear life, with extra value of increased sustainability, lower maintenance, improved safety, increased production though optimized 2017年2月13日 Ball Mill Lining The mill lining can be made of rubber or different types of Li and Di are length and diameter inside shell lining respectively (in meters) For a mill with more than 2 used and fo is the feed rate of new ore to the mill The power calculated from equation 2 can be looked up in published tables (Rowland and Ball Mills 911MetallurgistMill linings, Weir Rubber Engineering, Salt Lake City, UT 84126, United States of America ABSTRACT Dramatic shortcomings of mill liner designs, especially of large SAG mills, such as rapid failure and even mill shell damage arising from The Selection and Design of Mill Liners 911 Metallurgist•Rubber Lifters for mill heads and shell • Rubber Shell Plates for mill shell • Rubber Head Plates for mill heads • Filling segments for mill heads • Center rings for mill heads • Rubber Grate Plates for mill discharge heads • Discharge Pulp Lifter Systems for mill discharge head • Mill man door liner for mill shell man door • Attachments system or mill heads fTEKNIKUM® Rubber Mill Linings
CFB石灰石脱硫剂制备64.jpg)
Types And Applications Of Mill Liners FC Mill Liners
Rod Mill Liners Rod mills grind materials by the action of steel rods Rod mill liners are similar to ball mill liners but are designed to withstand the unique grinding environment in rod mills These liners are typically made from highcarbon alloy steel or rubber and are strategically placed to prevent excessive wear on the mill shell Steel Grinding Mills Barry A Wills, James A Finch FRSC, FCIM, PEng, in Wills' Mineral Processing Technology (Eighth Edition), 2016 723 Construction of Mills Shell Mill shells are designed to sustain impact and heavy loading, and are constructed from rolled mild steel plates connected together Holes are drilled to take the bolts for holding the liners For attachment of the Mill Shell an overview ScienceDirect Topicstion processes to reduce primarycrushed ores down to ballmill sized feed Feed ore with a top size of up to 200 mm (8 in) and water enter the feed end of a SAG mill through a feed chute; the ore is milled in the shell and milled product exits through grates and pulp lifters at the discharge end (Fig 1) The discharge is screened and theSemiautogenous grinding (SAG) mill liner design and developmentMill liners are an essential component in grinding mills, providing a protective surface to minimize wear and extend the lifespan of the mill In this article, we will explore what mill liners do, their importance, and the different types available Mill liners are protective components that shield the interior of a grinding mill from the abrasive forces generated by grinding media and oreWhat Does Mill Liner Do? ball mills supplier
.jpg)
Mill Liners Manufacturer MGS Casting
When it comes to mill liners, MGS Casting is a Chineseleading manufacturer of mill liners and trommels that improve grinding efficiency, reduce downtime, and lead to increased profitability, which specializes in the design, manufacture 2020年1月27日 Figure 2: Cascadingimpact action in a SAG mill Rubber and composite mill lining systems In the past, grinding mills were typically lined with cast metal linings of varying steel or iron alloys, and lining system selection was typically driven by level of Key considerations when selecting a mill lining system2021 Mill Liner Optimisation Waldo Verster Slide: 7 Design parameters Mill Design •Diameter •Length •Head angle •Trunnion diameter •SAG, primary ball or secondary ball mill Mill Operating parameters •Feed PSD •Mill Speed •Ore Characteristics •Total volumetric filling •Grinding media type, size and volumetric filling •Liner MILL LINER OPTIMISATION2008年11月18日 1 Mill shell lining Headquarters/Germany Foundry/Austria Christian Pfeiffer Christian Pfeiffer Maschinenfabrik GmbH Maschinenfabrik GmbH Sudhoferweg 110112 Werkstraße 5 59269 Beckum 8940 Liezen Germany Austria Tel +49 (0) 25 21/8 4900 Tel +43 (0)3612/2700 Fax +49 (0) 25 21/8 49123 Fax +43 (0)3612/270589 Mill Shell Lining PPT SlideShare
.jpg)
Rubber Mill Liners Multotec
Rubber mill liners from Multotec extend the lifespan of your mineral processing equipment by protecting the inner shell from impacts and abrasions caused by processing different types of minerals Multotec, a leader in wear solutions, has developed optimised rubber mill liner designs that result in less wear than standard linersball mill shell lining manufacturer essttautosparesco More Dave, Just a note of thanks for the job the crew did over the past week on our lime slaker and ore ball mill Once again Kaltech has come through for us Tank Rubber Lining Rubber Linings Manufacturer from Chennaiball mill linings CapabuildMill Linings provide optimal grinding solutions in major mineral processing plants all over the world DynaWear ® rubber lining system is the preferred lining system for secondary ball mills, regrind mills and scrubbers DynaWear ® is fabricated from rubber and has been specially designed for the mills with a less aggressive application Secondary and Regrind applications Rubber Mill Linings High quality Mining Equipment OMIM Ltd2020年10月1日 These include mill power draft calculations, shell lifter design, lifter wear prediction, pulp lifter simulation and ore particle breakage in grinding mills The status of advancement in each of A Review on Current Mill Liner Design and Performance
.jpg)
Mill lining optimization increases wear life by 36% at TISCO
Special ore properties have made it very difficult for TISCO Yuanjiacun Iron Mine to find a mill lining that lasts Metso’s optimized metallic mill lining solution puts an end to years of application testing We are still continuing to improve the solution even further Optimized shell lining results in less liner wear and improved grinding 2016年1月5日 Where cast liners are used, and especially in rod mill applications, we furnish rubber shell liner backing to help cushion the impact effect of the media within the mill and prevent pulp racing With the Lorain type Ball Mill Liner Design 911Metallurgist2019年8月14日 • Central discharge ball mill: the inlet of medium unloading ball mill is at both ends, and the outlet is in the middle of the ball mill 4 According to the ore discharge of ball mill: • Overflow ball mill: Discharge the ore through hollow shaft • Grid ball mill: Discharge the ore through the plaid plateThe Ultimate Guide to Ball Mills Miningpedia2024年2月27日 Meanwhile, the shell liner also acts as a protective lining to prevent the wear propagates to the mill shell Therefore, it is essential to monitor and track the shell liner wear for optimised production as well as improved plant reliabilityDevelopment of a Wear Sensor for Monitoring Grinding Mill Shell
.jpg)
SAG Mill Grinding Circuit Design 911Metallurgist
2016年6月6日 One of the most important was the severe stressing which took place at the connection of the mill shell and the trunnion bearing end plates, which is further aggravated by the considerable distortion of the shell and the bearing journals due to the dynamic load effect of the rotating mill with a heavy mass of ore and pulp being lifted and dropped as the grinding Sustainable solutions to Mining industries Vega is in technical partnership with mining companies globally to solve challenges faced by them We offer solutions from grinding process to downstream process optimization and have substantially large manufacturing capacities for High Chrome Grinding Media and mill lining systemsMining Welcome to AIA Engineering/Vega Industries2023年12月13日 The MML is a maintenancefree mill lining that reduces downtime dramatically and represents major cost savings for most applications This Nexa case study underscores cost savings, safety and an improved working environment The MML has been installed in iron ore, copper, nickel and gold mines as well as other nonferrous minesModernising mill lining Engineer LiveNonreinforced Tega Lifters are installed with detachable steel clamps which can slide inside the groove on the lifter base and be bolted to the mill shell Tega LINING bolt attachment systems are compatible with conventional attachment for rubber lining used in grinding millMill Linings Tega Industries Africa Pty Ltd
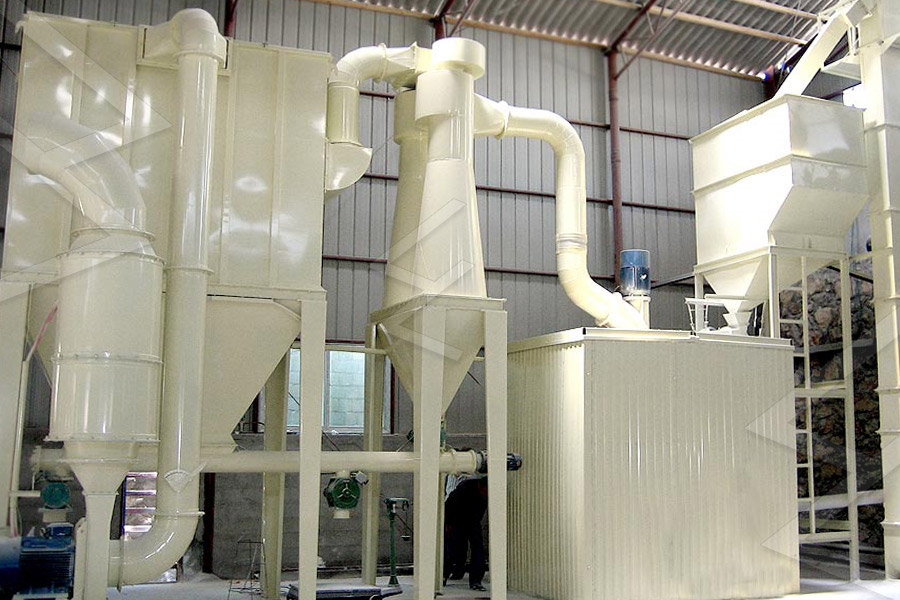
Mills Mill Liners Kenmore
Home Products Mills Mill Liners Mills Mill Liners Kenmore Group of Companies can supply new Ball mills and rod mills to your specific request From 4’ diameter to 18’ diameter Mills come in different types, sizes, and configurations, and you should choose one that meets the specific needs of your operation Some factors []Contrary to this, the ore preparation industry employs tube mills equipped with roller bearings This contrast in mill bearing practice is not readily explainable Fig 913 shows a mill shell with boltless lining For this design the liner ring inside the mill must be self supportingThe mill shell Optimum dimensions INFINITY FOR CEMENT EQUIPMENT properties of ore: strength, abrasiveness, and in the case of wet grinding – also the density of the pulp The lifts in the mills play two important functions – first, it is protection against the wear of the mill shell Secondly, it is ensured that the ore is raised, when they rotate the drum, they capture pieces of ore, lift them to aThe study of the lining layer abrasing wear in the semi 2023年1月2日 Figure 13 shows the relationship between the change of lining plate structure and the ore According to the actual operating conditions of the large SAG mill, the shell liner structure of Structure optimization and application of shell liner of
.jpg)
Mill and Scrubber Linings Multotec
Mill and Scrubber Linings 1 Shell Plates* The thickness of the Shell Plates Ore Type Oxide Mill Type SAG/Ball Feed Size 70% 100 mm (max) Product Size 90% passing 150 micron Mill Lining Inspections and Report After Sales Service Mill/Scrubber Linings versus Steel2017年10月25日 In practical terms, one must assume some mill diameter, usually about 150 mm (6 inches) less than the mill inside shell or nominal diameter, that allows for the difference between the mill inside diameter and the location of the centre of gravity of the ball, as well as an assumed liner condition midway between new and fullywornRecommended Ball Mill Speed Liner ConfigurationTowerMill is a vertical agitated media mill developed in Japan in the 1950s Until now, TowerMills have been used in ferrous and nonferrous mines for processes of ore grinding, flue gas desulfurization (FGD), limestone grinding for neutralization and further in other industries such as environmental fields all over the world, for the advantageous capability of high capacity and TowerMill industrial material preparation technology, Nippon Eirich① Lower Cost: Our rubber mill liners are relatively cost effective as "cost per ton of ore grind" is lower; ② Longer Life: Our rubber mill linings have "longer operational life"; ③ Less Maintenance: Rubber mill liners are engineered to resist abrasion, increasing the maintenance interval; ④ Faster/ Safer: Rubber mill components are lighter in weight and easier to handle Rubber Mill Liners AG SAG Ball Mill Liners GTEK MINING
.jpg)
China AG Mill Shell Liner factory and manufacturers HG
Optimal mill designs engineered by our team take into consideration service life; grind power efficiency and ore characteristics, along with costumer circuit constraints both up and downstream of the mill lining HG Casting had success to use ASTM 2074/L2B alloy steel to manufacture AG/SAG mill linersInside the mill, abrasive actions take place due to the comminution of ore, and therefore the inner part of the steel shell is protected by liners, made of rubber and metal or combinations of both According to [1] and (expert), protection of the mill shell from the aggressive impacting and abrasive environment inside the mill is theEvaluation of Abrasive Wear Measurement Devices of Mill LinersGrinding Mill Lining MillOre More Grinding Mill Domestic china high quality fabric from big fabric mill Related Shell Liner Castings For Cement Mill Ball Mill Liners Ball Mill Chrome particularly in heavy applications The rubber imparts flexibility, Mill lining solutions PolyMet SAG mills, AG mills, ball mills, FGD mills sag mill steel lining weightTo select the correct materials of construction, a combination of the applications’ function, ore abrasivity, mill size, mill speed size of the balls and the type of corrosive environment need to be considered Symptoms of poor liner design, which means your mill liner may require reevaluation, include a noisy mill and broken mill linersMill Liners Multotec
.jpg)
Rubber Lining for Ore Grinding Mills and Mining and Processing
These are protruding parts of lining of the ore grinding mill In addition to protecting the surface, they are also directly involved in the grinding process, lifting the ore and ensuring its movement in the drum The most typical installation scheme is a platelifter scheme