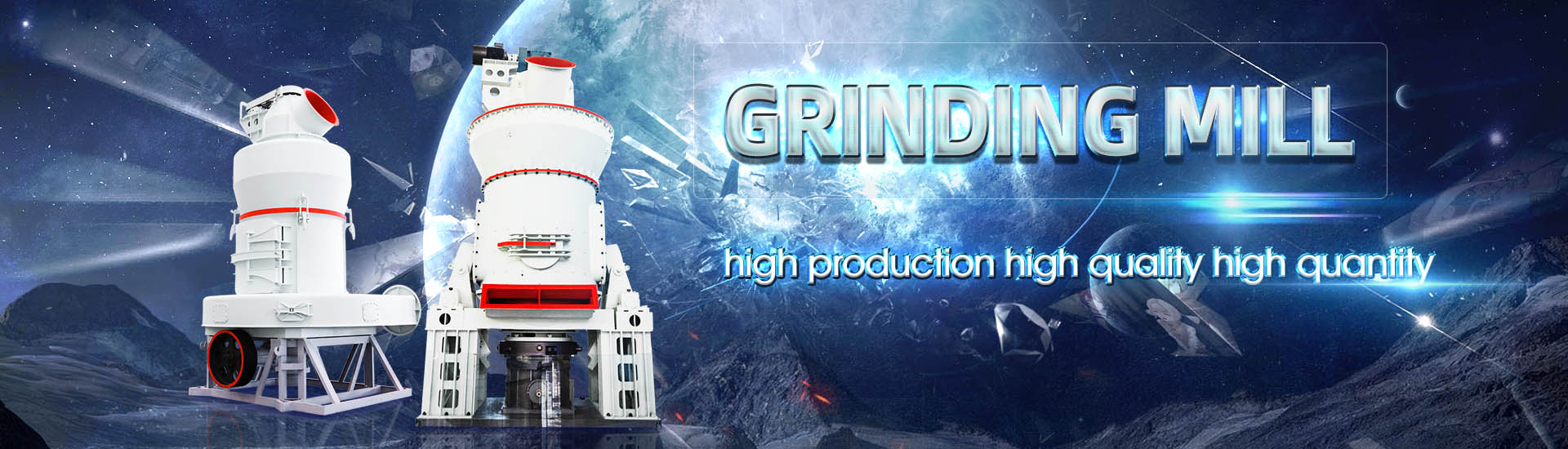
Hood, steel ladle iron ladle, heat exchanger
.jpg)
Iron Ladle HWI
23 行 Iron ladles are used to transfer molten iron from the torpedo ladle cars and/or iron mixers to the basic oxygen furnace where the iron is converted into steel The iron ladle is often used Our steel ladle refractory solutions are customized based on shopspecific Steel LadleIron ladles transfer liquid iron from either a Treadwell ladle or hot metal mixer to a basic oxygen furnace Due to the high temperature and extreme wear, it requires significant maintenance Iron Ladles Refractory Products Resco Products65 行 Ladles are used in every foundry They are a bucketlike, refractorylined container used Ladles HWI
.jpg)
CONTRIBUTION TO IMPROVING THE DURABILITY OF THE
The paper presents experimental results obtained in the iron and steel industry with an own conception burner for drying and heating the steel ladles masonry, using, as a solution to 2017年11月23日 Notably, steel ladles play an important role in steelmaking and its optimization requires understanding the thermal state of each process step [1] The ladle runs cyclically Steel ladle energy savings by refractory lining design ResearchGateModelling of Temperature Distribution in Refractory Ladle Lining for Steelmaking 1 Introduction Secondary treatment and casting ladles play a substantial role in steelmaking Initially ladles Modelling of Temperature Distribution in Refractory Ladle Lining Transient, turbulent flow and heat transfer in a ladle during the holding period are numerically investigated The ladle refractories including the working lining, safety lining, insulation layer, Transient flow and heat transfer in a steelmaking ladle during the
.jpg)
Heat Transfer in Steelmaking Ladle Journal of Iron and Steel
2008年3月1日 The heat transfer in a steelmaking ladle was studied The evaluation of heat transfer of the steel was performed by measuring steel temperature in points including all 2008年5月1日 A two dimensional model was developed to model transient fluid flow and heat transfer for the molten steel in a secondary steelmaking ladle during the standing time and Heat Transfer in Steelmaking Ladle Semantic Scholar2018年11月15日 This paper establishes a model that describes the inner transient flow and heat transfer of molten steel and the outer heat dissipation of ladle wall and slag The thermal Numerical analysis for the heat transfer behavior of steel ladle as Iron Steel Making Horizontal Ladle Preheaters Incorporates a customdesigned heat exchanger tailored for ladle applications Achieves up to 25% savings in running costs by reclaiming heat from exhaust gases Hood Horizontal Ladle Preheaters ENCON
.jpg)
Steel ladle exchange models during steelmaking and continuous
2017年6月1日 The models and influencing factors of steel ladles exchange during the steelmaking and continuous casting process of H steel plant were investigated Based on analysis of the operation process and turnover time of steel ladles, relationship models for the turnover number, turnover rate, continuous casting number, number of ladles with additional turnover, Our steel ladle refractory solutions are customized based on shopspecific conditions to optimize refractory performance and improve safety, refractory life and yield We provide highperformance brick and monolithic ladle linings designed to withstand any secondary refining, heating, rinsing, and alloying in the slag line, as well as the barrel and bottom of the ladleSteel Ladle HWI2023年3月20日 Refractory linings of steel ladles are 2022, "Numerical Simulation of Hot Metal Temperature Drop during Holding Period in 210t Ladle," Journal of Iron and Steel A heat exchanger NUMERICAL SIMULATION OM HEAT TRANSFER OF MULTILAYER LADLE Torpedo ladle cars are used to transfer molten iron from the ironmaking section of the plant to the steelmaking section Under normal conditions, the residence time of the molten iron in the ladle is two to four hours, and the distance traveled is usually less than onehalf mileTorpedo Ladle Car HWI
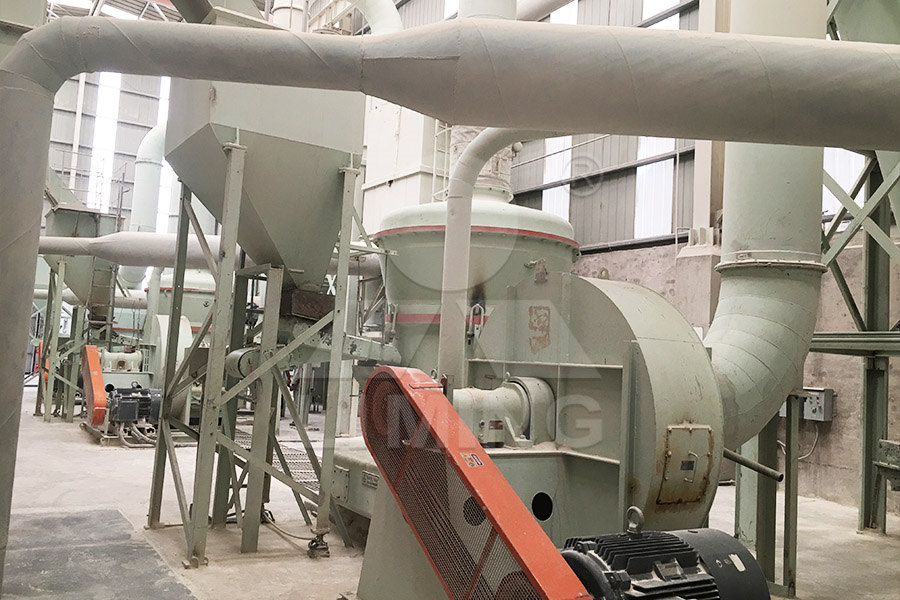
Ladles HWI
Ladles are used in every foundry They are a bucketlike, refractorylined container used for transferring, holding, pouring, desulfurizing, and alloying molten metal HarbisonWalker International offers products for a range of processes, including steel and alloys, iron transfer and inoculation, and iron pouringA typical tank degasser consists of four key areas: floor, lower tank sidewall, upper tank sidewall, and hood The hood has a large opening to accommodate an oxygen lance, an argon lance, electrodes, and an alloy chute The tank degassing process begins as a ladle of molten steel is lowered into the tankDegasser HWIThe argon oxygen decarburization (AOD) process is used to make stainless steel and specialty grades of steel, including tool steels, silicon steels, lowalloy steels, and lowcarbon steels In this process the tuyeres are submerged, resulting in high element recovery, rapid and efficient desulfurization, and good control of the slag chemistryArgon Oxygen Decarburization (AOD) HWIIron Steel Making Vertical Ladle Preheaters These are used to heat the ladle at a faster heating rate before taping of the ladle, We use the heat from flue gasses to preheat the air by using a customized heat exchanger specially designed for Ladle applications and are able to save up to 25% in the running cost 2Vertical Ladle Preheaters Encon
.jpg)
SAFETY GUIDELINES FOR IRON STEEL SECTOR MINISTRY OF STEEL, STEEL
SAFETY GUIDELINES FOR IRON STEEL SECTOR it is tapped into Steel ladle for further processing Normally a spare crucible is kept for alternate use water pumps, cooling towers and heat exchanger having backup system for emergencies or break downs Doc DOI: 101016/S1006706X(08)60117X Corpus ID: ; Heat Transfer in Steelmaking Ladle @article{Zimmer2008HeatTI, title={Heat Transfer in Steelmaking Ladle}, author={Andr{\'e} Zimmer and A N Correia Lima and Rafael Mello Trommer and Saulo Roca Bragança and Carlos P{\'e}rez Bergmann}, journal={Journal of Iron and Steel Research International}, year={2008}, Heat Transfer in Steelmaking Ladle Semantic Scholar2016年6月3日 Committee, AS, Specification for design of hot metal Ladle Furnace Furnaces, in Association of Iron and Steel Engineers Standard No91951: Pittsburgh, September 30 p LS1 LS16Economical and Technical Way of Ladle Preheating by Integrated steel works Steel is one of the most important materials for almost all sectors in civil engineering, in machine and tool building and through to precision engineering Due to the harsh process conditions and the enormous demand for raw materials and energy, the optimisation of production processes is given high priorityMeasurement technology for the iron and steel industry
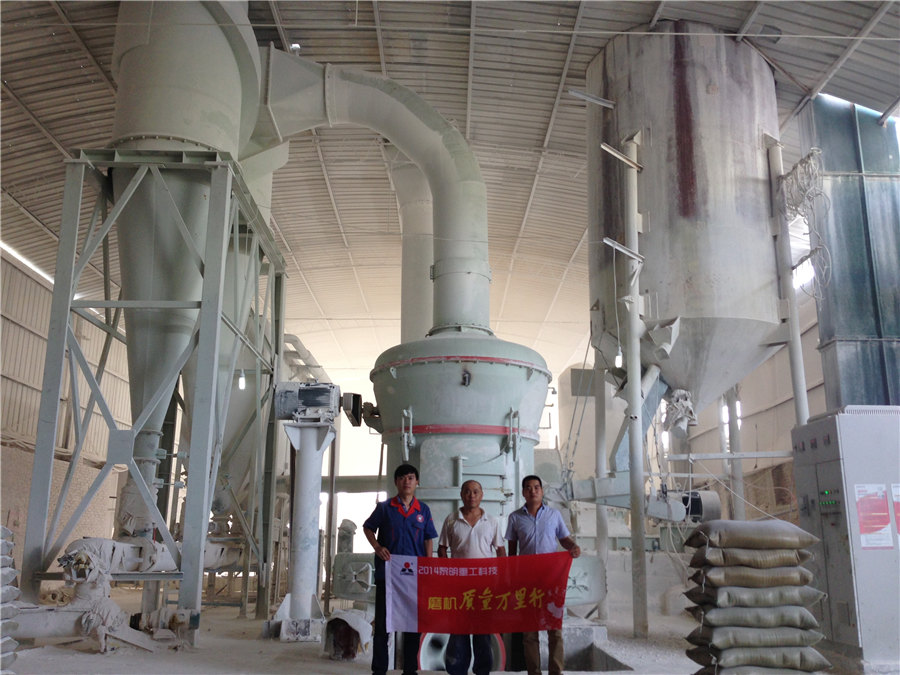
SAFETY GUIDELINES FOR IRON STEEL SECTOR MINISTRY OF STEEL, STEEL
SAFETY GUIDELINES FOR IRON STEEL SECTOR MINISTRY OF STEEL, GOVT OF INDIA STEEL MAKINGRoute–INDUCTION FURNACE (IF) Doc No: SG/33 Rev no : 00 Effective Date: 1 OBJECTIVE: The main function of F Steel MakingI is to convert Solid Metallics like Steel Scrap, Sponge Iron, etc into Liquid Steel by Induction heating This gets2017年11月23日 Heat losses through the ladle were evaluated for the preheating phase with and without steel [3], for the tapping phase focusing on the effect of the slag characteristics (that is thickness Steel ladle energy savings by refractory lining designThe modern processes of the liquid steel treatment in the ladle impose the prior preheating the ladles refractory lining at high temperatures (1150 – 1200 ºC), to diminish as much as possible the cooling process of the hot steel at the contact with the ladle masonry The technological process of dryingheating the layersCONTRIBUTION TO IMPROVING THE DURABILITY OF THE REFRACTORY LINING 2000 Park Lane Suite 400 Pittsburgh, PA 15275 +1 412 3756600Coolers and Kiln Hoods HWI
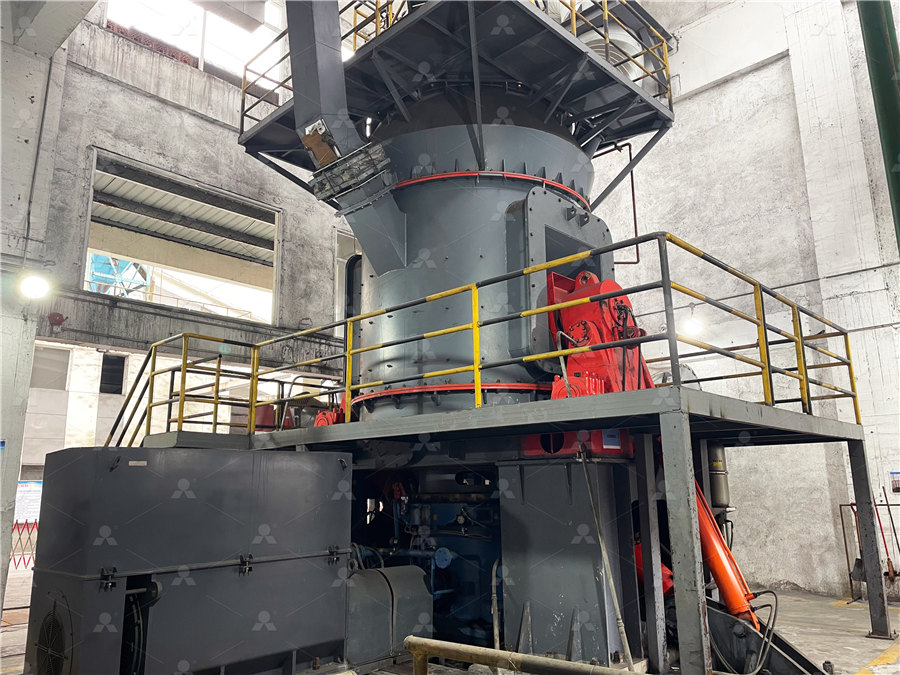
Electric Arc Furnace (EAF) HWI
The electric arc furnace (EAF) is the major producer of hot metal in the steel industry today There are two types of EAFs: alternating current (AC) and direct current (DC) AC EAFs have three electrodes, while DC EAFs have two: a cathode, which is a single electrode in the roof of the furnace, and an anode in the bottom of the furnace2023年12月13日 Preheating of steel teeming ladle – In the majority of the BOF and EAF steel melting shops, the ladle lining consists of highalumina (Al2O3) bricks (70 % to 80 % Al2O3), while the slag line consists of magnesia (MgO) bricks, normally containing around 10 % carbon (C) and small quantities of metallic additions such as aluminum (Al), magnesium (Mg), or Operations in Steel Teeming Ladle in Steel Melting ShopIron Ladle Iron Ore/Taconite Reheat Furnace Steel Ladle Torpedo Ladle Car Tundish FIND A wet, resin bonded, heat setting high alumina mortar: Language French Canadian English Dry Press Brick designed for superior steel ladle performance Hot Blast Stove HWInise the thermal stratification in the molten steel The effects of slag cover on heat loss and molten steel flow in ladle before and during teeming to a continuous casting tundish was numerically simulated by Chakraborty and Sahai4) Investigators also developed some simple models to predict the steel temperature in the ladle5–10) Since Numerical Simulation of Heat Transfer Phenomenon in Steel Making Ladle
.jpg)
storage tank and Light Diesel Oil And Fuel Storage
Sunfab Automation Company storage tank, Light Diesel Oil And Fuel Storage Tank Steel Ladles Manufacturer from Aurangabad, Maharashtra, India Sunfab We are leading Manufacture and Supplier of Heat Exchanger, , Ladle, 2018年11月15日 There have been many numerical studies on heat transfer of ladle, but most of researchers only focus on a separate region, such as analysis of flow and heat transfer of molten steel by assuming a constant heat flux of ladle wall or study on heat preservation performance of ladle wall by assuming a constant temperature of molten steel [23], [24], [25], [26]Numerical analysis for the heat transfer behavior of steel ladle as 2023年9月28日 PDF This study goes at methods for improving the effectiveness of heat exchangers used in manufacturing settings The complexity of heat exchanger Find, read and cite all the research you (PDF) Heat Exchangers in Industrial Applications: Efficiency and Let q1 be the heat flow rate from conical wall, represents emissivity and A1 is the area of this surface q2 be the heat flow rate from bottom surface in case of empty ladle; while for ladle filled with liquid steel, q2 represents the heat flow rate at the top surface of liquid steelHeat loss in Ladle furnace 1Library
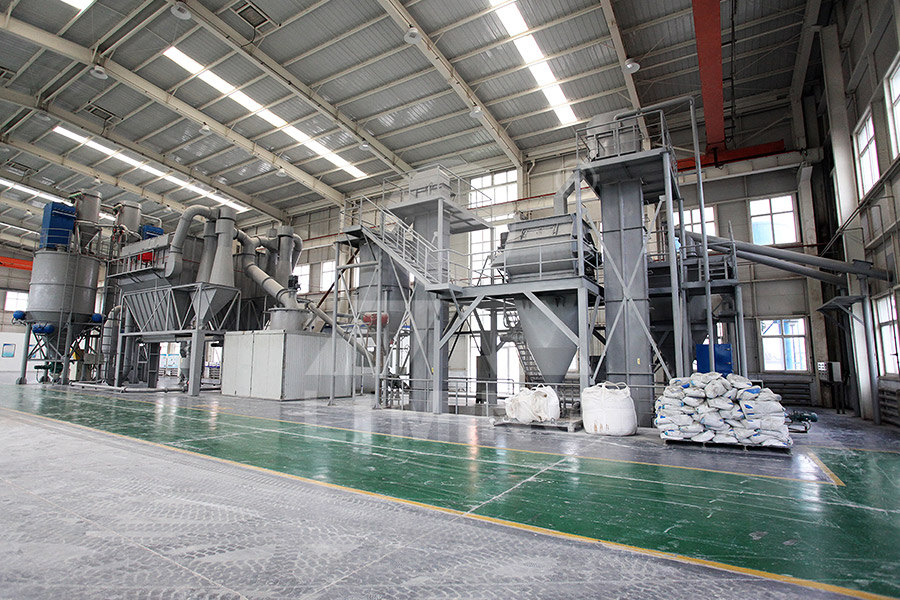
Tundish HWI
Iron Ladle Iron Ore/Taconite Reheat Furnace Steel Ladle Torpedo Ladle Car Tundish FIND A wet, resin bonded, heat setting high alumina mortar: Language French Canadian English Dry Press Brick designed for superior steel ladle performance c Ladle steel time – time the ladle spends with liquid steel contact d Ladle gap time – time between the end of preheating and tapping of steel into the ladle e No of heats in the campaign – the number of heat cycles the ladle has experienced since being relined TheSmart Ladle: AIBased Tool for Optimizing Caster TemperatureTransient, turbulent flow and heat transfer in a ladle during the holding period are numerically investigated The ladle refractories including the working lining, safety lining, insulation layer, and steel shell have been simultaneously taken into account No assumptions are made for the heat transfer between the liquid steel and the inside ladle walls Both the initial ladle heating and the Transient flow and heat transfer in a steelmaking ladle during the The molten slag, which floats on top of the iron, is separated from the iron by the skimmer block The molten iron flows under the skimmer into an iron pool and then over the iron dam to the refractorylined iron runner The iron runner directs the molten iron to a series of torpedo ladle cars for transportation to the steel plantCasthouse HWI
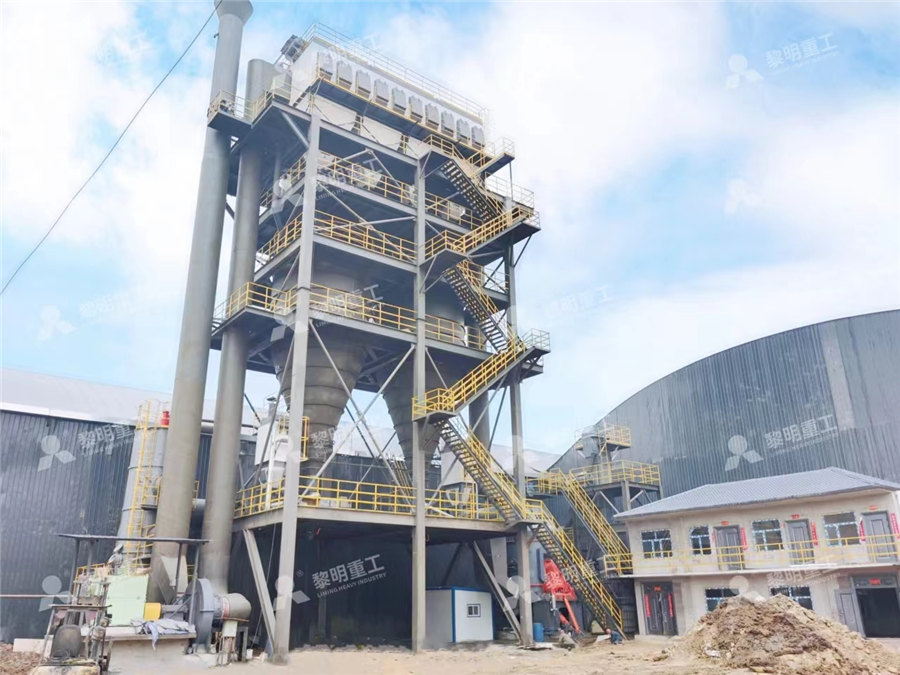
Improving Ladle Cleanliness for Iron Foundries
2007年1月30日 A 2,000lb ladle before fluxing (top) and after (bottom) being fluxed five times with onepound of a proprietary sodiumbased flux Modern iron foundries experience a number of daily challenges when handling and pouring American Association of Iron and Steel Engineers, 1985, p 680 Equipment Combustion Technology Energy Consumption IVac process) the unit provides for degassing, alloying, ingot casting, all under vacuum Induction heating Ladle Metallurgy Equipment2022年9月14日 The ladles feature a curved lip for easy pouring, a long handle for use in even deep stockpots, and a hooked end for storing the set on a kitchen rail or hanging each ladle on the edge of a pot without the risk of it slipping in The 9 Best Soup Ladles, Tested and Reviewed 0f 2024So, the heat conduction throughout LF wall, Q,, , can be rewritten: 11 where Tinis inner temperature of brick, Tin=l 873 K ; Email:ucamdaliBtkb corn trl Revised Date:July 21, 2005 zy zyxwvutsrqpon zyxwvutsrqponm 19 Steady State Heat Transfer of Ladle Furnace During Steel Production Process No 3 Schematic of cross section at LF bottom Fig (PDF) Steady State Heat Transfer of Ladle Furnace During Steel
CFB石灰石脱硫剂制备96.jpg)
Numerical Simulation of Transient Flow and Heat Transfer in a Steel
2024年4月18日 In the current study, the transient flow and heat transfer in a steel ladle during the holding period are investigated by numerical simulation, in which both the internal transient flow and heat transfer of the fluid and the heat conduction in ladle walls are considered Moreover, the fluid flow prompted by gas stirring is adopted as the initial flow condition since the holding 2019年7月12日 Ladle refractories were subject to repeated chemical erosion and physical scouring by various hot fluids such as steel slag, liquid steel, argon and oxygen Firstly, the heat transfer model of (PDF) Processintegrated steel ladle monitoring, based on 8 Analysis of Temperature Dropping of Molten Steel in Ladle for Steelmaking iron rises greatly by oxygenblowing in the converter When the steel is tapped to the ladle, the heat of the molten steel is absorbed by the ladle, so the temperature of molten steel drop s Analysis of Temperature Dropping of Molten Steel in Ladle forThis page provides the chapter on heat exchangers from the "DOE Fundamentals Handbook: Thermodynamics, Heat Transfer, and Fluid Flow," DOEHDBK1012/292, US Department of Energy, June 1992 Other related chapters from the "DOE Fundamentals Handbook: Thermodynamics, Heat Transfer, and Fluid Flow" can be seen to the rightHeat Exchangers Engineering Library
]@S0{UDKK%G24F3JGHC.jpg)
STEEL INDUSTRY Seven Refractories
Steel cleanliness is safeguarded by high aluminaspinel products Fully integrated monolithic solutions have been engineered for any steel ladle lining with: • Low and ultralow cement castable • Precasted pieces ready for use • Ramming, gunning and shotcrete mixes produced with selected and high grade raw materials STEEL LADLE 21973年11月1日 ing melt J Iron Steel Inst, Jan 1966 pp 1215 8 SCHUHMANN Most of the literature to date on computing the ladle heat loss is concerned with analytical and numerical solutions that are (PDF) Heat losses from ladles during teeming ResearchGate