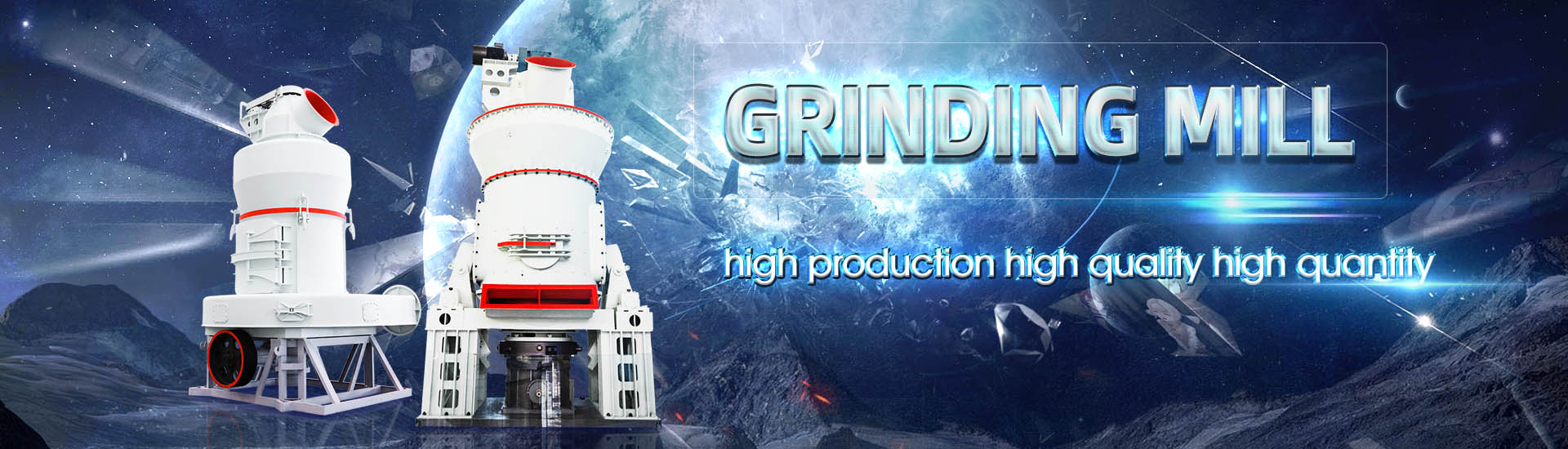
Limestone kiln production and process
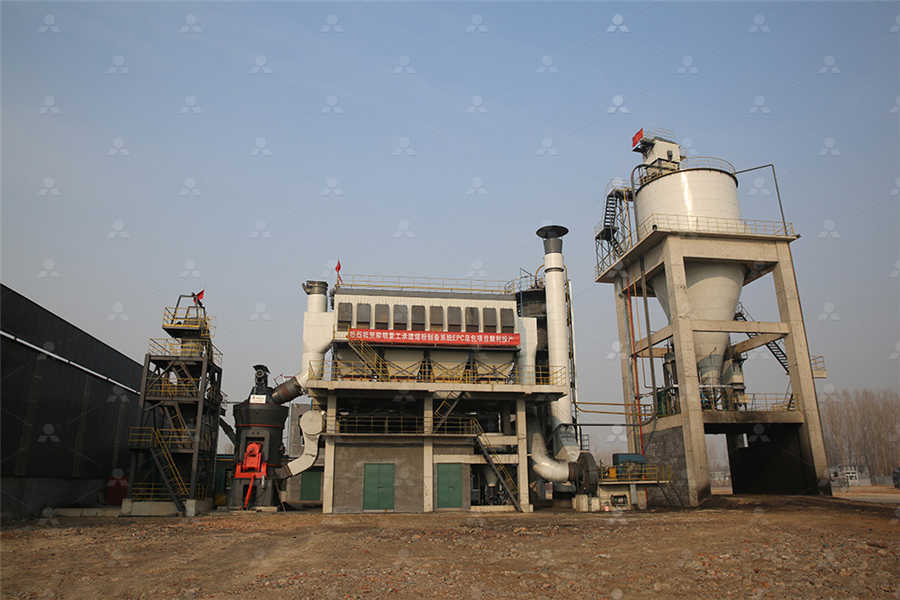
How Lime is Made
Lime production begins by extracting limestone from quarries and mines Sizing Limestone enters a primary crusher to break the rock Depending on the size of the feedstone required, processes in the production of lime are: (1) quarrying raw limestone; (2) preparing limestone for the kilns by crushing and sizing; (3) calcining limestone; (4) processing the lime further by 1117 Lime Manufacturing US EPAA lime kiln is a kiln used to produce quicklime by the calcination of limestone The chemical equation representing this reaction is: CaCO 3 + heat = CaO + CO 2 This reaction takes Lime Kiln an overview ScienceDirect TopicsRotary lime kilns are large steel tubes that are lined on the inside with refractory bricks They are slightly inclined from the horizontal and are slowly rotated on a set of riding rings Lime mud is 22 Lime Kiln Principles And Operations TAPPI
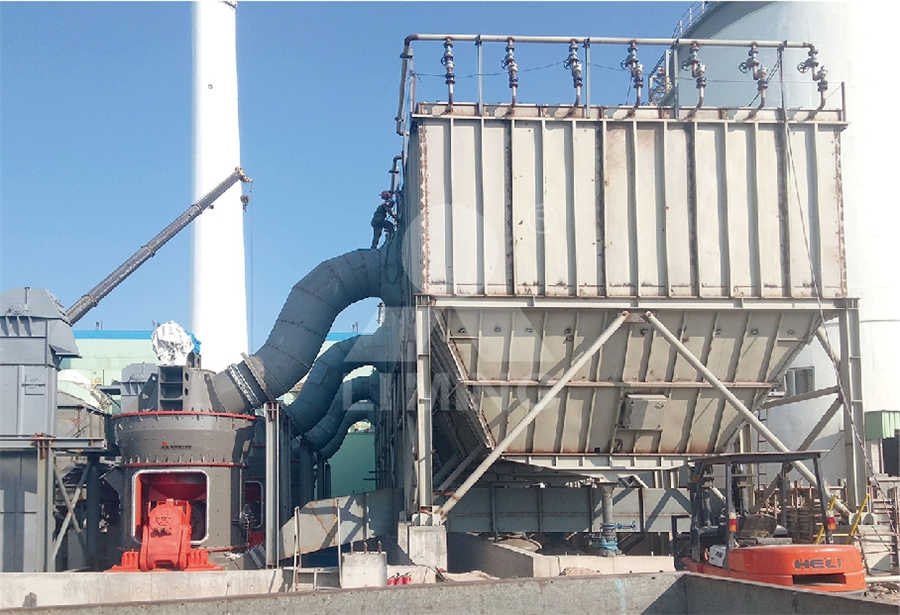
Thermal energy analysis of a lime production process: Rotary kiln
2016年4月15日 In this paper, thermal energy analysis of three zones of a lime production process, which are preheater, rotary kiln and cooler, is performed In order to perform a proper Production capacities for these units range from 50 tons/day of CaO (45metric tons/day) to over 1,100 tons/day of CaO (> 1,000 metric tons/day) The purpose of a lime kiln is to: • regenerate LIME KILNS, HEAT TRANSFER, CONTROL AND COMBUSTION Limestone is converted into lime through heating in a kiln, a process known as calcination When limestone is subjected to high temperatures, it undergoes a chemical decomposition resulting Lime Production: Industry ProfileWhen the rock is heated in a specially designed kiln to over 900°C, a chemical reaction occurs and creates calcium oxide, otherwise known as lime Learn more on each of the 4 stages in Production European Lime Association
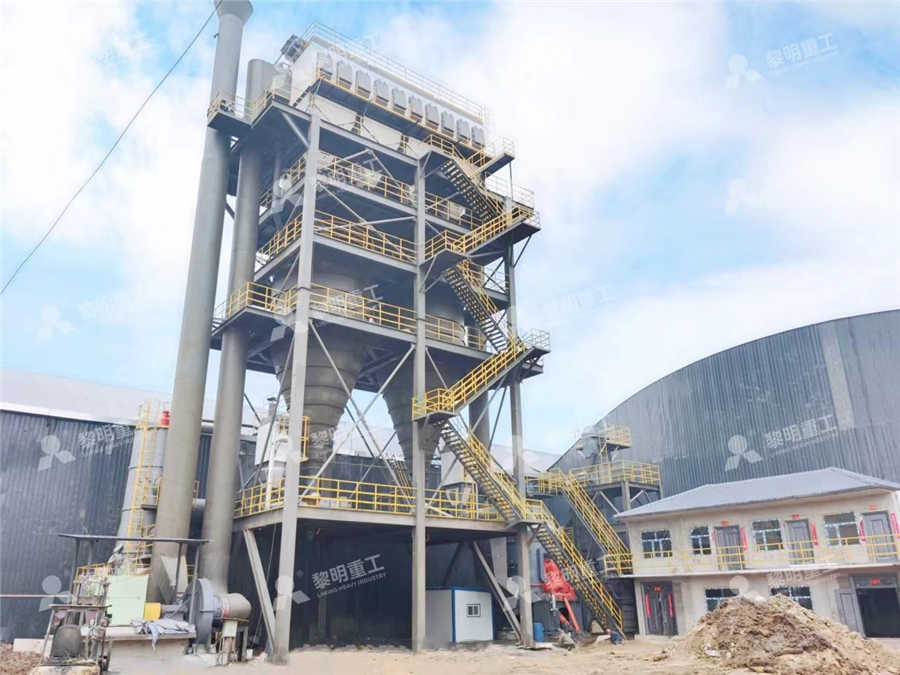
Lime SpringerLink
2021年3月3日 Manufacturing processes are then described, involving quarrying and limestone preparation, calcination process, quicklime processing, and quicklime hydration The most 2023年7月10日 The cement manufacturing process involves the extraction and processing of raw materials, such as limestone, clay, and shale, which are then heated in a kiln at high temperatures to form clinkerCement Manufacturing Process and Its Environmental Calcination is a common process for the high temperature treatment of ground raw materials This process takes place in a heated rotary kiln (Fig 102) This part of production consists of four subprocesses, namely: 1/preheating, 2/calcination, 3/clinker mineral formation in the rotary kiln during sintering, and 4/coolingClinker Production an overview ScienceDirect Topics2021年3月3日 The kiln charge (eg, limestone or dolomite) has a typical grain size between 50 mm and 100 mm, although it can be smaller (15–50 mm) or even larger The combination of chemical quality of dolomite together with the production process used gives high refractoriness features 77 Environmental ConsiderationsLime SpringerLink

Lime and its Production
The lime cycle shows the stages from quarrying the limestone through to the production of mortars and plasters for our (Calcium Carbonate – CaCO3) is burnt in a kiln giving off Carbon Dioxide (CO2) gas and forming Calcium Oxide (CaO It is, therefore, an extremely important process to come to understand Categories Clinker: reactions in the kiln The milled and blended raw materials go to a silo and then to the kiln Reactions which take place as the feed passes through the kiln are reviewed below They can be considered under three broad headings: Decomposition of raw materials temperatures up to about 1300 °CReactions in the cement kiln clinkering Understanding Cement1977年5月3日 Both kiln types can achieve high production rates, but neither can operate with coal The "calcimatic" kiln, or rotary hearth kiln, is a circular kiln with a slowly revolving doughnutshaped hearth In fluidized bed kilns, finely divided limestone is brought into contact with hot combustion air in a turbulent zone, usually above a perforated grate1117 Lime Manufacturing US EPA2017年7月7日 Rotary kilns, with or without preheaters, usually process limestone with material size between 10 mm and 50 mm longer retention time means less production and higher costs of production CO2 concentration in kiln – CO2 concentration in the kiln atmosphere increases with its release from limestone during calcinationLimestone – Its Processing and Application in Iron and

Lime Production: Industry Profile
21 Production Process, Inputs, and Outputs 21 211 Crushing limestone inputs, and costs of production Section 3 describes the characteristics, uses, and Limestone is converted into lime through heating in a kiln, a process known as calcinationThe primary raw materials used in cement production are limestone, clay, and shale These materials are typically extracted from quarries using various methods, including blasting, drilling, In a wet process kiln, the raw materials are mixed with water to form a Comprehensive Guide to Cement Kilns: Processes, Types, Charging the Kiln: Initially, chunks of limestone are loaded into the kiln These kilns vary in size and can be up to 4 meters in diameter and 100 meters in length Advanced kilns are equipped with sensors and control systems to automate much of the process, ensuring consistent product quality and optimizing fuel consumptionThe Transformation Process within a Lime Kiln: Breaking It DownPresent paper attempts to review the literature related to various strategies to design the control system for the Lime kiln industrial process Lime Kiln is multivariable process with complex interactions of variables It has higher degree of coupling, severe non linearities, and frequent disturbances This paper covers the modeling and control aspects of Lime Kiln process The Modeling, Control and Instrumentation of Lime Kiln Process: A
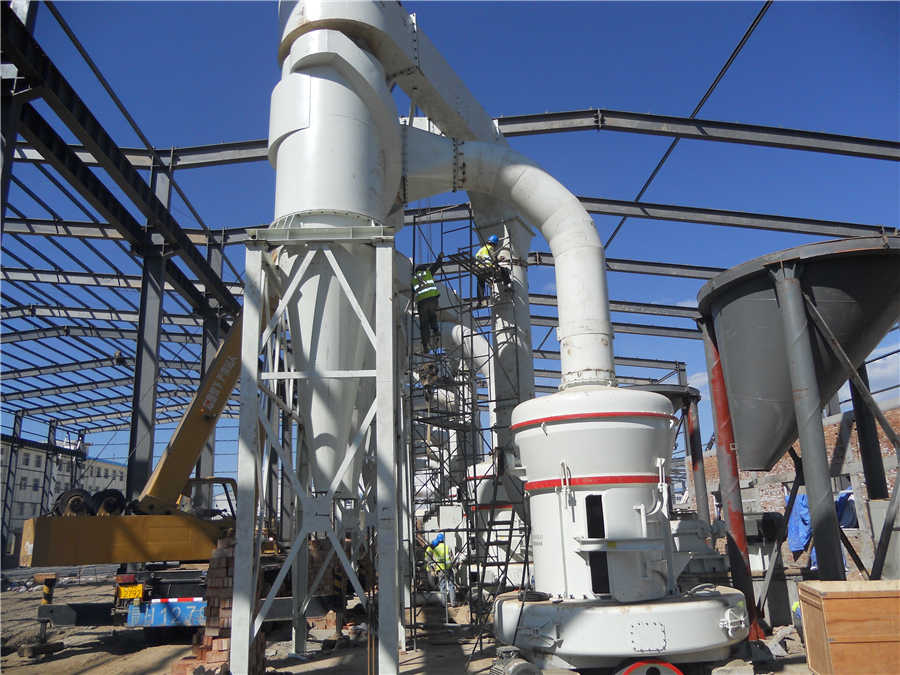
Decarbonising the lime industry: Stateoftheart ScienceDirect
2022年10月1日 The thermal treatment of limestone (mainly CaCO 3) to produce lime (CaO) is a major contributor to CO 2 emissions and the literature on decarbonising the lime industry is scarce Subsequent hydration of lime would lead to the synthesis of slaked/hydrated lime Ca(OH) 2; the production of a tonne of Ca(OH) 2 emits ∼12 tonnes of CO 2 arising mainly from the Dynamic process simulation of limestone calcination in normal shaft kilns @ Tata Steel Jamshedpur uses a twinshaft Parallel Flow Regenerative type kiln to calcine limestone Previously, the 2 Excerpts; Save Modeling and validation of the milk of lime production process J Kemppainen Engineering, Agricultural and Food Sciences 2016 [PDF] Dynamic process simulation of limestone calcination in Kiln phase Since clinker is a complex mixture of ingredients, it requires a multistaged heat treatment, which is done in the kiln The main part of the manufacturing process of clinker takes place in the kiln The stages in the kiln phase are as follows:Cement Clinker Manufacturing Process with Reactions2016年1月20日 Table 2 indicates that the total input materials used in the raw meal production were 248 kg/kg of raw meal, and that hot gas from the kiln and natural resources (limestone, silica, iron ore, and clay) are the primary sources accounting for 4079% (101 kg/kg raw meal) and 3950% (098 kg/kg raw meal) of farine productionAnalysis of material flow and consumption in cement production process
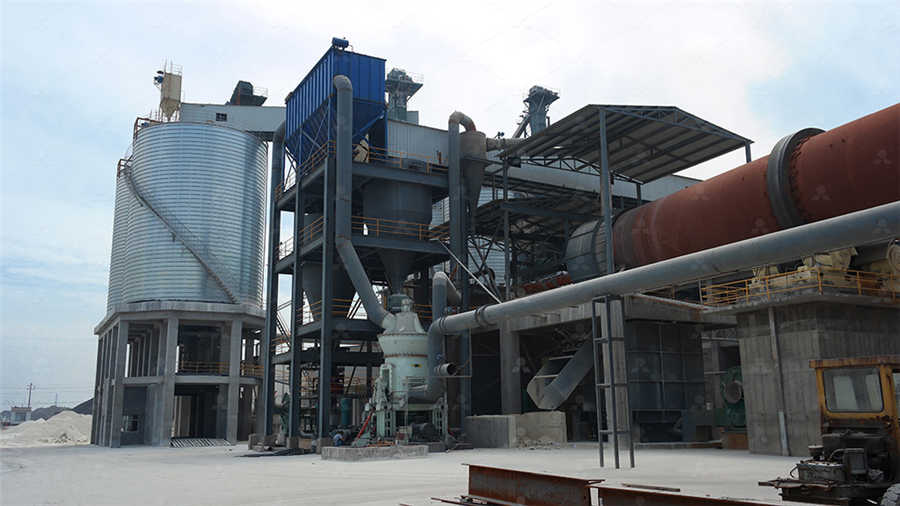
Cement Production Process Cement Manufacturing Process
2020年8月25日 A full cement production process includes the cement crushing process, raw mill process, The Portland cement manufacturing process is representative of all types of cement limestone and clay are the main raw materials of cement and sent into wet process kiln to calcine clinker The semiwet process of dehydrating raw New PFR lime kiln process with blast furnace gas and oxygen Production of high reactive lime is now possible with inexpensive blast furnace gas A new and innovative Parallel Flow Regenerative lime kiln process using 100% blast furnace gas achieves the same performance as a natural gasfired PFR lime kiln; however, withNew PFR lime kiln process with blast furnace gas and oxygen2013年5月2日 Calcination of Limestone satyendra; May 2, 2013; 4 Comments ; calcination, lime, limestone, Long rotary kiln, preheater, reactivity, Rotary kiln, vertical kiln, Calcination of Limestone Calcination or calcining is a thermal treatment process to bring about a thermal decomposition The process takes place below the melting point of the productCalcination of Limestone IspatGuruClinker is the intermediate product used in the manufacturing of cement There are two primary processes used to manufacture clinker: the dry process and the wet process Our plants use the dry process, which is more energy efficient In the wet process, the raw materials are mixed with water to form slurry, which is fed into a kilnProduction Process CEMEX Philippines
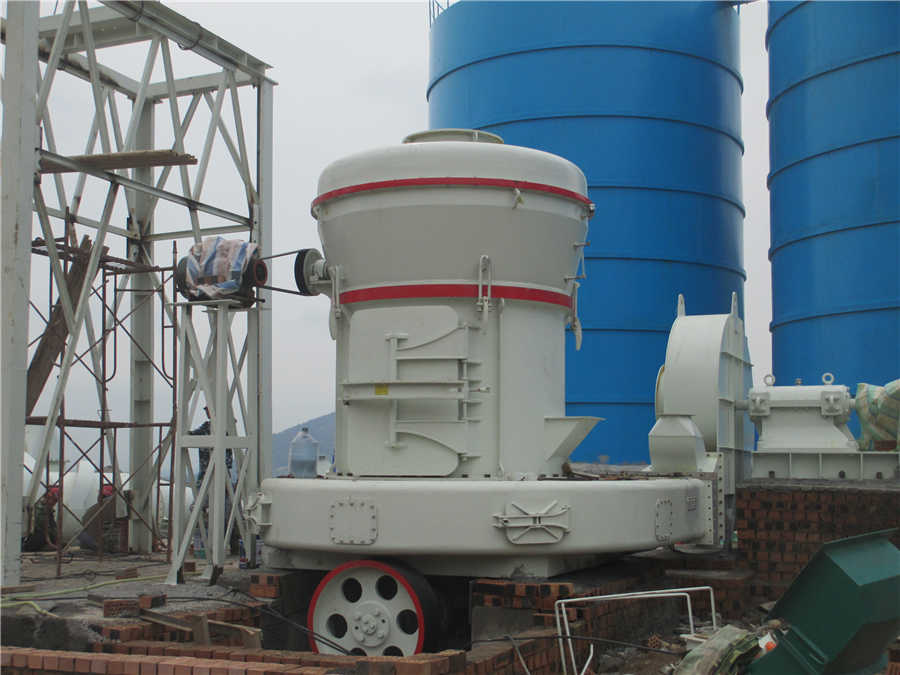
A Comprehensive Guide to the Cement Manufacturing Process
2024年9月5日 The Manufacturing Process of Cement Now, let’s explore the steps involved in the cement production process in more detail: 1 Mining and Crushing The process of making cement begins with mining, where raw materials are extracted from quarries Huge machines called excavators dig the limestone out of the earth2024年11月23日 Cement Extraction, Processing, Manufacturing: Raw materials employed in the manufacture of cement are extracted by quarrying in the case of hard rocks such as limestones, slates, and some shales, with the Cement Extraction, Processing, ManufacturingLimestone, marl, and clay are commonly used sources of these primary elements Each step of the cement production process is carefully monitored to ensure efficiency and quality Grinding, Mixing, which uses heat generated by the How Cement is Made Portland Cement Association42 Energy use and emissions The lime production process is energy intensive and results in CO 2 emissions from both mineralogical transformation process and energy used The production of one tonne of lime entails the emission of around 12 tonne of CO 2 (Ochoa George et al, 2010; Sagastume Gutiérrez et al, 2012)This makes lime one of the products with the highest Lime Production an overview ScienceDirect Topics

Efficient CO2 capture from lime production by an indirectly
2021年12月1日 Lime (CaO) is an important product used in different sectors of the industry as well as in agriculture The production of lime is achieved through the calcination of limestone (mainly CaCO 3) at temperatures between 900 and 1200 °CThis process is highly endothermic and requires the combustion of fuels such as gas oil, coal, coke, or some types of secondary 2019年12月10日 Lime production represents the second largest contributor to industrial CO 2 emission in China, but it has not been well addressed Herein, an efficient and environmentfriendly Limestone Calcination Process with CO 2 Looping and Recovery (LCPCLR) is established to solve the associated environment issue CO 2 serves as heat carrier in the LCPCLR An environmentfriendly process for limestone calcination with Production rate, tpd Run tine factor in % Specific Heat Consumption in Kcal/kgclinker; Process parameters Kiln Speed should be such that volumetric loading is within the range 1015% and heat transfer is maximized Precalciner kilns generally rotate at 3545 rpmClinkerization Cement Plant OptimizationA lime kiln is a kiln used to produce quicklime by the calcination of limestone The chemical equation representing this reaction is: CaCO 3 + heat = CaO + CO 2 This reaction takes place at 893°C (∼900°C) at which the partial pressure of CO 2 is 1 atm but temperature around 1000°C at which the partial pressure of CO 2 is 38 atm is usually used to get the reaction to proceed Lime Kiln an overview ScienceDirect Topics
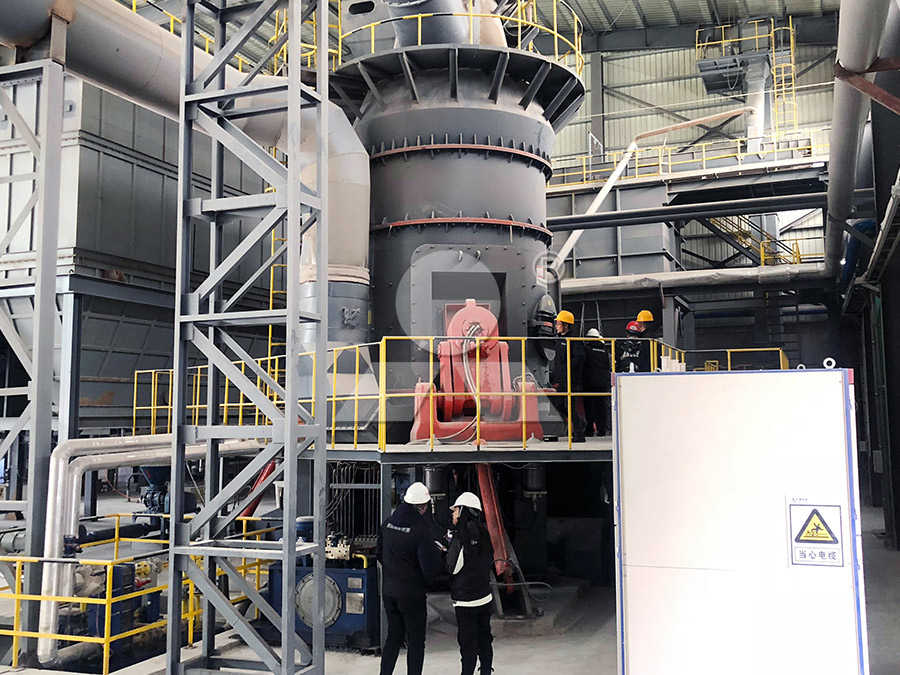
Vertical Shaft Kiln for Lime Production
Loading and unloading a vertical shaft kiln is a relatively simple process The limestone is loaded into the top of the kiln using a conveyor or other type of mechanical device Once the lime has been produced, it falls to the bottom of the kiln and is collected The Different Stages of Lime Production in a Vertical Shaft KilnROTARY KILN PRODUCT COOLERS Slide 12 shows a schematic of satellite product coolers All modern kilns are being offered with product coolers Satellite coolers are tubes attached to the kiln shell and rotating with the kiln The hot reburned lime product drops through holes in the shell just uphill from the lip of the kiln into the tube coolers22 Lime Kiln Principles And Operations TAPPIThe cement clinker calcination is an important step in the cement production process It mainly occurs in cement kiln and can be roughly divided into typically sand, iron ore, clay, gypsum, limestone, shale, etc Limestone is the main one All the content above is some opinions of clinker calcination and cement production processCement Clinker Calcination in Cement Production Process2022年9月21日 The study explores the indirect mechanosynthesis process for cement and clinker production, highlighting its impact on global cement outputCement and Clinker Production by Indirect
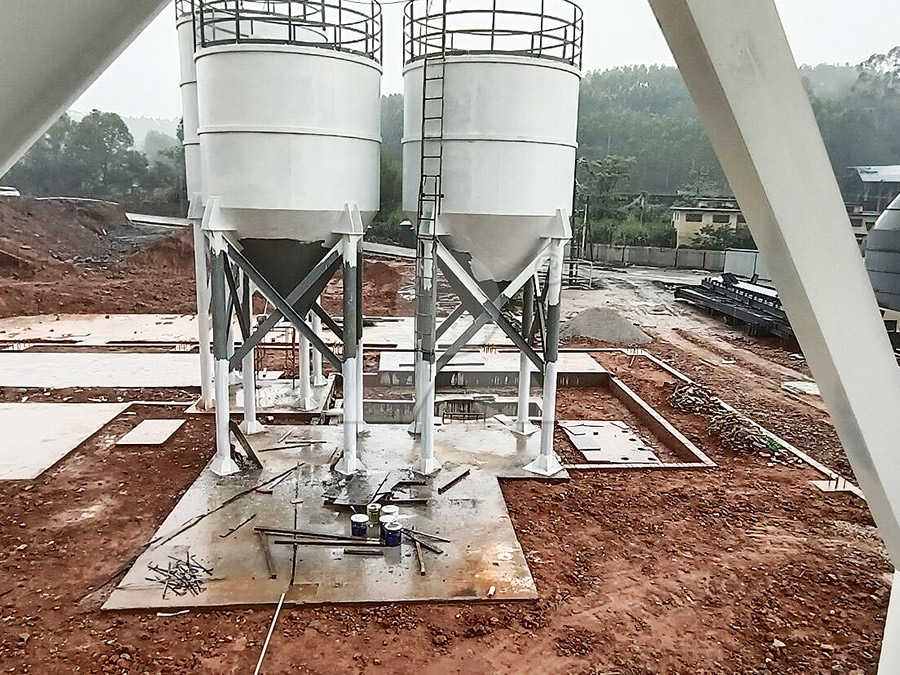
A Review on Design and Thermal Analysis of Rotary Kiln for Lime Production
2016年1月6日 mixture of limestone and clay, for this process rotary kiln is used for making cement clinker The length of the kiln is 1244m and inner diameter is 42m with 4% slope[4] B Calcination The limestone calcination as energy intensive kiln is 317m, and production process from unhydrated lime is often performedThe Cement Production Process The importance of limestone ore bodies close to the plant is that it makes up around 80 per cent of the approximately 165 tonnes of raw material input needed to make one tonne of clinker From the wet process kiln to the 6stage suspension preheater with a precalciner and high efficiency cooler, The Cement Production Process2022年7月4日 a kiln and (4) grinding the burne d product, known as “ clinker,” together with some pe rcentage of gypsum (to control the time of set of the cement) This process of manuf acture is known dryMining Activities, Cement Production Process and Quality Control2024年9月10日 Cement is an essential building material used in construction The Cement manufacturing process involves the extraction and preparation of raw materials, such as Limestone, clay, shale, iron ore, and Gypsum These materials are crushed, ground, and blended to form a raw meal, which is then heated in a kiln at high temperaturesCement Manufacturing Process: Know Extraction, Processing

Process characteristics of clinker and cement production SINTEF
Cement production process: Thermal energy demand and CO 2 emissions 30% fuel emissions thermal energy prod process emissions from calcination of limestone 60% 10% electric power consumption, indirect emissions Limestone Quarry Filter Clinker Cement Cement Mills Raw Mill Calcination Cement Constituents Crusher FanDrying Rotary Kiln Preheater2023年6月12日 Lime is an essential raw material for iron and steel production, in construction and agriculture, in civil engineering, in environmental protection, and in manifold chemical manufacturing processes To address the problem of unavoidable process CO2 emissions associated with the production of lime, efficient capture technologies need to be developed Negative CO2 emissions in the lime production using an indirectly 2024年1月15日 In the conventional cement production process, CO 2 emissions primarily result from the production of clinker, the main component of Portland cement [3]Specifically, two main sources of CO 2 emissions exist: (1) process emissions from the calcination process, where limestone (CaCO 3), a key component in the raw meal for clinker production, decomposes into Decarbonisation pathways of the cement production process via Cement Manufacturing and Process Control 41 Cement Manufacturing: Basic Process and Operation To design the Refractory for the lining of different equipments in a cement plant, it is necessary to understand the total operational process of a cement plant in depth It is necessary to know the conditions prevailing in different equipments and theChapter 4 Cement Manufacturing and Process Control
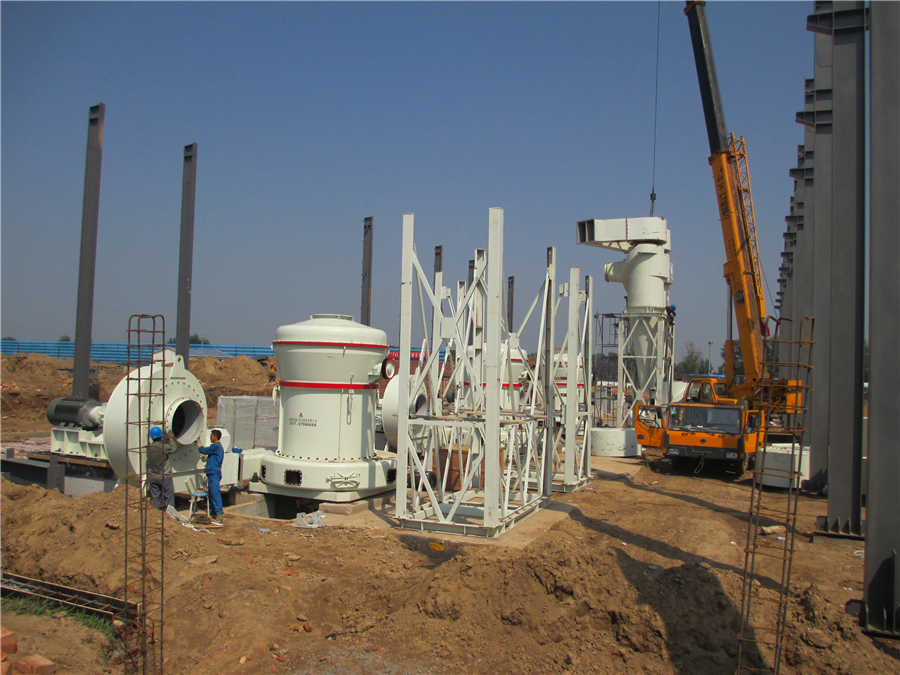
What is the Manufacturing Process of Lime?
Limestone is initially crushed using crushers like jaw crushers, impact crushers, and hammer crushers The crushed limestone is then screened to classify it into different sizes suitable for subsequent lime production process Limestone, a sedimentary rock, comes in different density ranges: 1 Lowdensity limestone: 1,7602,160 kg/m³ 2