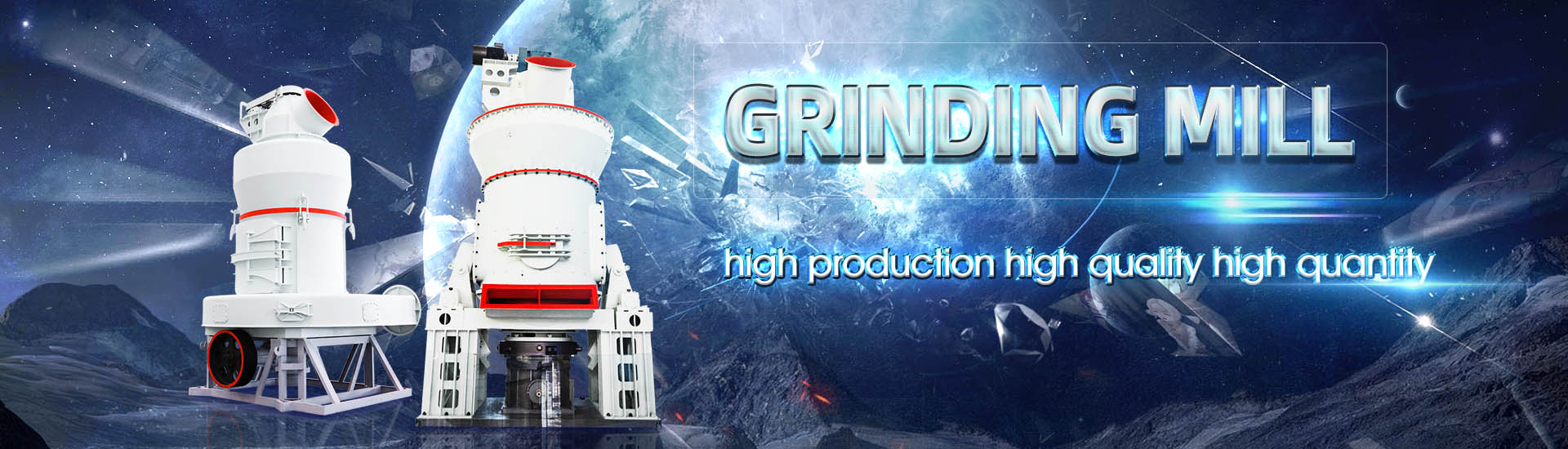
Dry process production of silicon micro powder equipment
.jpg)
Production Technology and Application of Silicon Micropowder
2021年8月23日 The production processes of spherical silicon micropowder abroad include hightemperature melting spray method, gas flame method, hydrolysis method of silicon tetroxide, 2024年5月28日 The drying procedure is an important consideration for the silicon powder processing Herein, a comparative investigation of the drying efficiency, drying performance, Study on efficient drying process of industrial silicon powderHerein, a comparative investigation of the drying efficiency, drying performance, and energy consumption of silicon powder after separation and purification of monocrystal silicon cutting Study on efficient drying process of industrial silicon powderThe DRIE process is a highly anisotropic dry etching process for the production of silicon microstructures The method is iterative and based on the use of a passivation layer which, in conjunction with a superimposed DC voltage, Deep Reactive Ion Etch (DRIE) Fraunhofer Institute for
.jpg)
Silicon Powder Properties Produced in a Planetary Ball Mill as a
2020年1月15日 Silicon Mechanical milling is a promising route for production of submicron and nano sized silicon powders, but it is challenging to predict and control the product properties 2022年5月23日 Surface modification process; Because the dry process is relatively simple and the production cost is relatively low, at present, the surface modification of silicon micropowder in China basically adopts the dry processSurface Modifiers, Processes and Equipment For Silicon Fraunhofer ISIT has developed a dry coating process, which works completely without solvents The drying of the coated electrode slurry is an energy intensive process It also requires a Dry Coating Fraunhofer Institute for Silicon Technology2022年7月18日 The spray granulation process is adopted to carry out the atomization process of a silicon dioxide and carbon source mixed slurry to produce a dry spherical powder This method has the advantage of directly Granulation of Silicon Nitride Powders by Spray Drying:
.jpg)
Review of Silicon Recovery and Purification from Saw Silicon Powder
2020年5月4日 Processing silicon powder from a diluted slurry is an indispensable prerequisite To effectively recover silicon, the oil or liquid should first be screened out from the slurry Powder microdosing system Large volume manufacturers demand the most out of their production process, including powder millin The techniques here are primarily mechanical, using dry milling equipment like jet mills or roll mills Powder Manufacturing Equipment Making2022年8月1日 Technologies and applications of siliconbased microoptical electromechanical systems: A brief It mainly includes wet and dry etching of Si Bettman B et al 2004 Thermally tuned external cavity laser with micromachined silicon etalons: Design, process and reliability 54th Electronic Components and Technology Conference 818 Technologies and applications of siliconbased microoptical 2020年4月11日 Crystalline metallurgical silicon nanopowder was successfully produced from Tunisian silica sand by magnesiothermic reduction Silica sand was first transformed into silica powder via a specific chemical process The produced silica powder was reduced by magnesium granules at a temperature range of 500–800 °C Thermal analysis shows that a low High Purity Porous Silicon Powder Synthesis by Magnesiothermic
.jpg)
Understanding the Polycrystalline Silicon Manufacturing Process
2024年3月26日 Polycrystalline silicon, also known as polysilicon or multicrystalline silicon, is a vital raw material used in the solar photovoltaic and electronics industries As the demand for renewable energy and advanced electronic devices continues to grow, understanding the polysilicon manufacturing process is crucial for appreciating the properties, cost, and 2013年9月1日 The exergetic efficiency for an industrial silicon production process the overall process resource utilization Today, several plants have installed some sort of thermal energy recovery equipment exergies Song and coworkers [15] derived an expression for specific chemical exergies of solid and liquid fuels with a dry Energy and exergy analysis of the silicon production processAtlantic Equipment Engineers has been a trusted supplier of highpurity metal powders for almost 60 years We always prioritize quality and specialize in packing and shipping orders of any size With AEE, you’ll always get highpurity silicon powder that meets all your specifications at a competitive priceSilicon Powder Supplier AEE Atlantic Equipment Engineers2020年8月3日 Experimental process of scallop smoothing of DRIE trench by RIEbased SF 6 plasmas This process flow represents a single trench of 64 × 8 arrays a Patterning the photoresist with a circular Lowtemperature smoothing method of scalloped DRIE trench by postdry
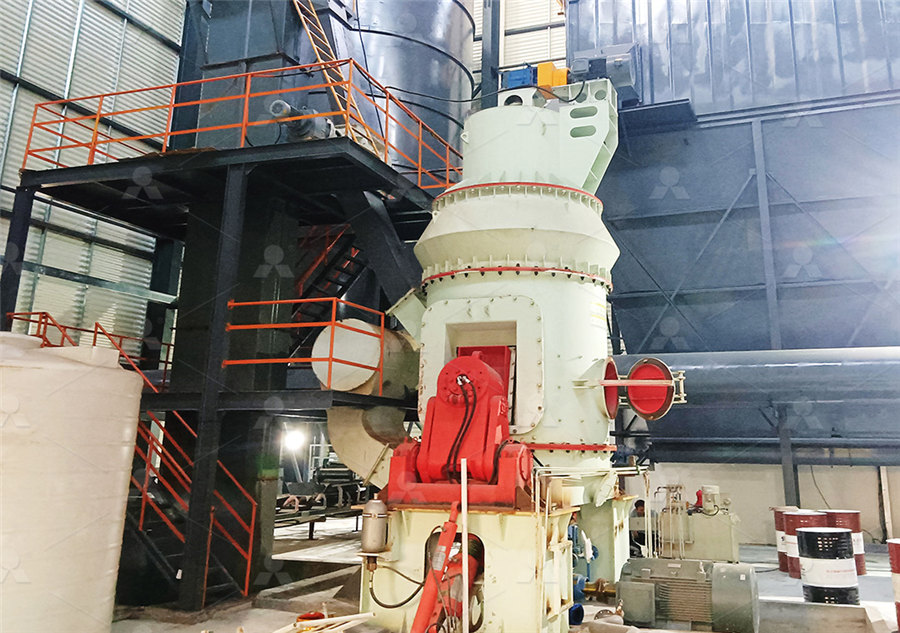
Surface Modifiers, Processes and Equipment For Silicon ALPA Powder
2022年5月23日 Silicon micro powder is a silica powder material made of natural Because the dry process is relatively simple and the production after comprehensive consideration, select a reasonable modifier, and on this basis, determine the surface modification process and equipment What nonmetallic mineral powders are contained in If you want to know more about silicon powder production equipment and the process information of silicon grinding mill, please contact mkt@hcmilling or call at +86773, HCM will tailor for you the most suitable grinding mill program based on your needs, more details please check https://hongchengmillNews How To Produce Silicon Powder? Introduction Of Silicon All dry powder materials were mixed using Maxwell’s proprietary dry coating process to yield a final powder mixture consisting of active material, binder and conductive additive as shown in Fig 1 (top) This powder mixture was calendered to form a continuous selfsupporting dry coated electrode film that is wound in roll form (Fig 1, bottom)Dry Electrode Coating Technology POWER SOURCES CONFERENCEProcess Solutions Dry Grinding; Classifying The production line of silicon micropowder ball milling and grading with annual output of 10,000 tons of a Address:Chongqing Jiangsu a new material company production 100kg per The production line of silicon micropowder ball
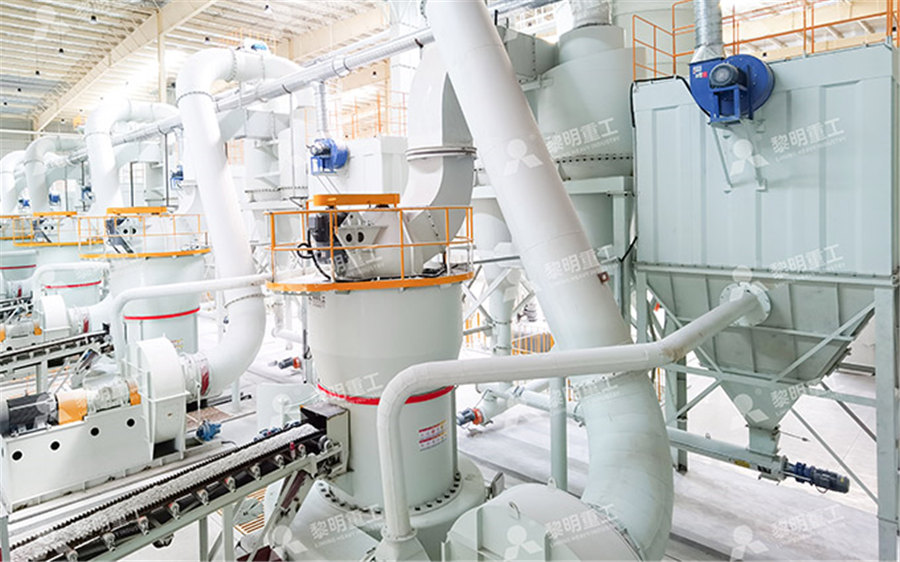
Shallow and deep dry etching of silicon using ICP cryogenic reactive
2010年2月5日 We achieved to etch nanostructures as well as structures with high aspect ratios in silicon using an inductively coupled plasma cryogenic deep reactive ion etching process We etched cantilevers, submicron diameter pillars, membranes and deep structures in silicon with etch rates between 13 nm/min and 4 μm/min These structures find applications as templates 2023年6月3日 Different types of silicon micro powder modification effects are also different Among them, spherical silicon micro powder has good liquidity It is easy to combine with the modifier during the modification process And the Surface modification method of silicon micro powderProcess Integration and Pilot Production Poly Silicon Process Platform Inertial Sensors; PostCMOS Integration; Pilot Development and production of innovative active and passive power semiconductor devices based on silicon and gallium nitride Power Electronics Micro Manufacturing Processes Industrialization, quality and reliability of Fraunhofer ISIT2023年11月13日 SIMOX Fabrication method and history The Separation by IMplantation of OXygen (SIMOX) method, developed in the 1970s, introduced an approach for the fabrication of SOI wafers without bonding []In the SIMOX process, a high dose of oxygen ions is implanted into a silicon wafer (Fig 2a) This implantation stage is succeeded by a hightemperature Fabrication and characterization of silicononinsulator wafers Micro
.jpg)
Novel drysuspension granulation process for preparing pressed
2021年1月2日 Owing to the advantages of drygranulation technology in terms of environmental protection and energy savings, some European companies and technicians have developed the dry granulation process to produce ceramic pressed powders since the early 80s [4]Furthermore, in the field of academia, Zhu [1, 5, 6] created a half dry droplet granulation process for 2001年6月1日 The process of plasma dry etching is quite simple straightforward and can be considered as the key technology in the micromachining of silicon The most important motivation for this work is Dry etchingbased silicon micromachining for MEMS2010年6月24日 2) We will introduce Micro Powder Dry system at ULVAC booth (No 2224) of Interphex JAPAN at "TOKYO BIG SIGHT" from Jun 30(Wed) to July 2 Technical seminar will be also held at 16:2017:20 on Jun 30(Wed), Conference room EXP1 For further information ULVAC, IncIndustrial Equipment Division indinfoMicro Powder Dry system for powder process: ULVAC has The organic binder was admixed in an amount of 4 to 25 parts by weight per 100 by weight of a mixture of silicon nitride powder, silicon powder and additive powder parts by weight of a mixture of silicon nitride powder, silicon powder and additive powWu et al [36] used a binder, which was a mixture of polyvinyl alcohol, dextrin, der methylcellulose, and glucoseGranulation of Silicon Nitride Powders by Spray Drying: A Review
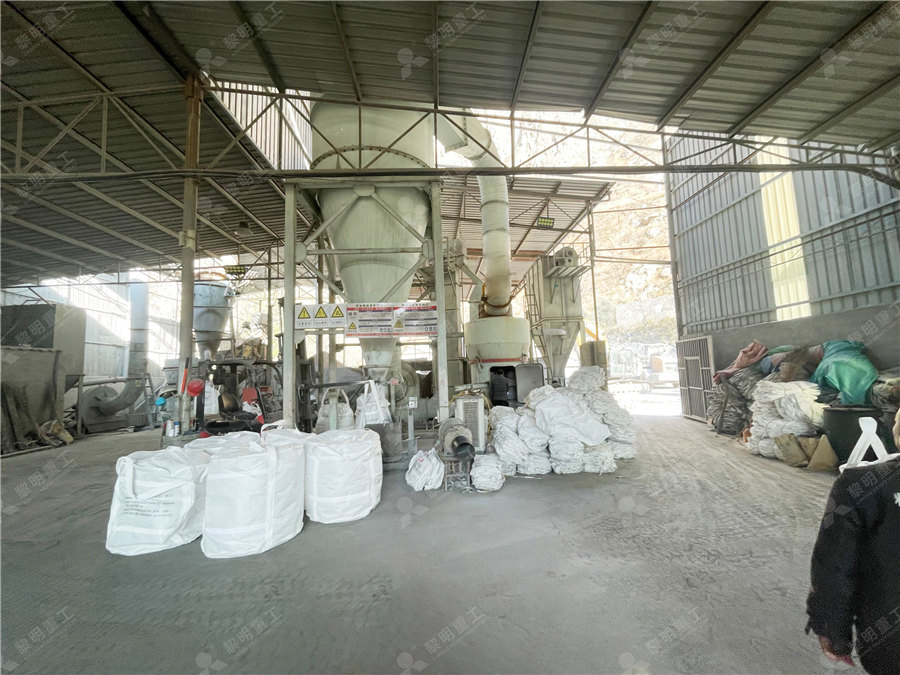
(PDF) Dry etching of monocrystalline silicon using a laserinduced
2021年12月1日 In contrast to electrically generated plasmas, laserinduced micro plasmas are controllable sources of reactive species in gases at atmospheric pressure that can be used for dry etching of materials2001年6月15日 The knowledge on dry etching technology seems to be of a great potential enabling us to revolutionise the stateoftheart of MEMS devices by achieving high vertical aspect ratios and extending the limits of deep etching down to the 40–300 μm rangeIn this article, attention is given to some promising applications and technological processes for the Dry etchingbased silicon micromachining for MEMSNew Dry Process Concepts †P77 Akihiro Shimizu Effects of Vacuum Ultraviolet Irradiation and Oxygen Plasma Treatment as Pretreatment on Interface Structure between Copper Seed Layer and Cycloolefin Polymer Film ‡P78 Koshi Kato Suitability evaluation of DC arc plasma treated WCCo granulated powder for laser based additive manufacturingTOP DPS 2024 45th International Symposium on Dry Process2021年12月1日 In the present study, we have demonstrated the laserinduced plasma etching of monocrystalline silicon A Ti:Sapphire laser has been used for igniting an optically pumped plasma in a CF 4 /O 2 gas mixture near atmospheric pressure The influence of process parameters, like substrate temperature, O 2 concentration, plasmasurface distance, etching Dry etching of monocrystalline silicon using a laserinduced
.jpg)
Inductively Coupled Plasma Dry Etching of Silicon Deep Trenches
2023年4月14日 Microoptical gyroscopes (MOGs) place a range of components of the fiberoptic gyroscope (FOG) onto a silicon substrate, enabling miniaturization, low cost, and batch processing2024年9月20日 The manuscript introduces an innovative dry electrode processing technique for negative electrodes It combines simulation analysis and experimental studies to optimize particle evolution and rolling parameters The composite powder consists of silicon oxide (SiO) and polytetrafluoroethylene (PTFE) within the dry electrode process •Construction and verification of simulation model for multiroll 2021年6月30日 Siemens process shows the lowest TAC ($050 M/y), but this does not mean that it is the process with the highest potential, since it has the lowest silicon production rate, 047 kt/yMethods of trichlorosilane synthesis for polycrystalline silicon 2021年12月11日 Silicon micropowder is made of natural quartz (SiO 2) or fused quartz (amorphous SiO 2 after high temperature melting and cooling of natural quartz) after crushing, ball milling (or vibration, jet milling), flotation, pickling purification, highpurity water treatment, etc The micro powder processed by this technology Silica powder is a nontoxic, odorless, non Features and application of silicon powder ALPA Powder Equipment
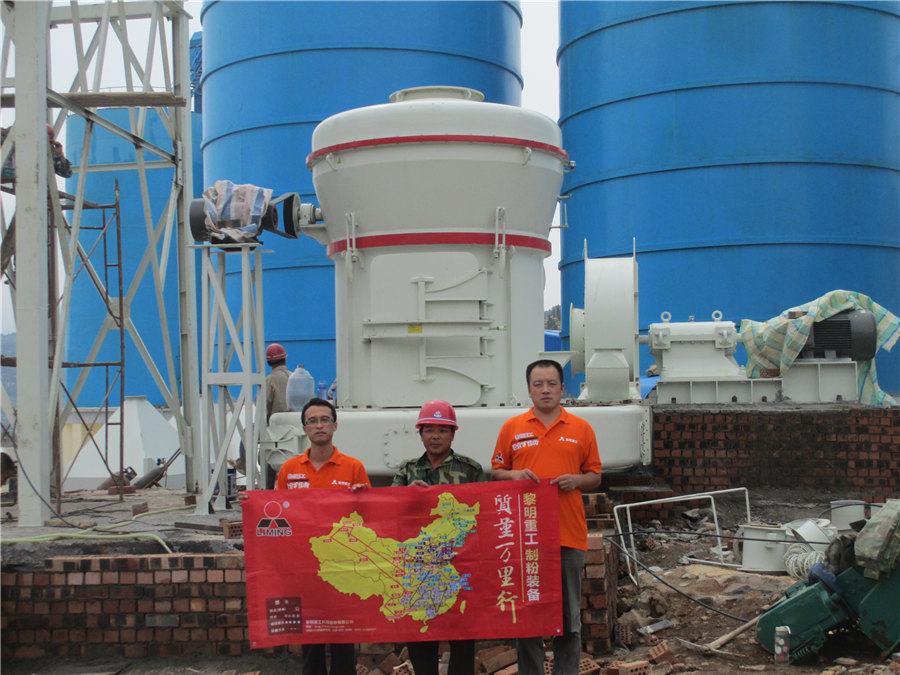
Capabilities of ICPRIE cryogenic dry etching of silicon IOPscience
The cryogenic dry etching process was first introduced by Tachi et al [6] Among the dry etching processes for silicon, the cryogenic dry etching process allows for both micro and nanomachining of silicon The cryogenic dry etching process uses two gases, ie SF 6 and O 2, at the same time in order to etch cryogenically cooled silicon wafers Perhaps this is due to the unpredictable behavior of bulk solids Also in this process, determination of the required product properties is of highest importance Find manufacturers of size reduction and size enlargement equipment to assist you when handling dry bulk materials in our Equipment GuidePowder and Bulk Handling Equipment Dry material handling Silicon micropowder is made of natural quartz (SiO 2) or fused quartz (amorphous SiO 2 after high temperature melting and cooling of natural quartz) after crushing, ball milling (or vibration, jet milling), flotation, pickling purification, highpurity water treatment, etc The micro powder processed by this technology Silicon micropowder is a nonmetallic material that is odorless, Application, processing technology and development trend of silicon powder2020年8月3日 Deep reactiveion etching (DRIE) is the most popular dry etching process used to create deep trenches and holes for various applications such as micromachining of microelectromechanical systems (MEMS) and through Lowtemperature smoothing method of scalloped DRIE
.jpg)
Dry Etching and Ashing Fraunhofer Institute for
The DRIE process is a highly anisotropic dry etching process for the production of silicon microstructures The method is iterative and based on the use of a passivation layer which, in conjunction with a superimposed DC voltage, 2021年8月20日 This paper reviews the recent advances in reactionion etching (RIE) for application in highaspectratio microfabrication Highaspectratio etching of materials used in micro and nanofabrication has become a very Recent Advances in Reactive Ion Etching and 2017年6月1日 Request PDF Solventfree dry powder coating process for lowcost manufacturing of LiNi 1/3 Mn 1/3 Co 1/3 O 2 cathodes in lithiumion batteries We report a solventfree dry powder coating Solventfree dry powder coating process for lowcost 2024年5月10日 Silicon carbide (SiC) is a promising semiconductor material as well as a challenging material to machine, owing to its unique characteristics including high hardness, superior thermal conductivity, and chemical inertness The ultrafast nature of femtosecond lasers enables precise and controlled material removal and modification, making them ideal for SiC A Review of Femtosecond Laser Processing of Silicon Carbide
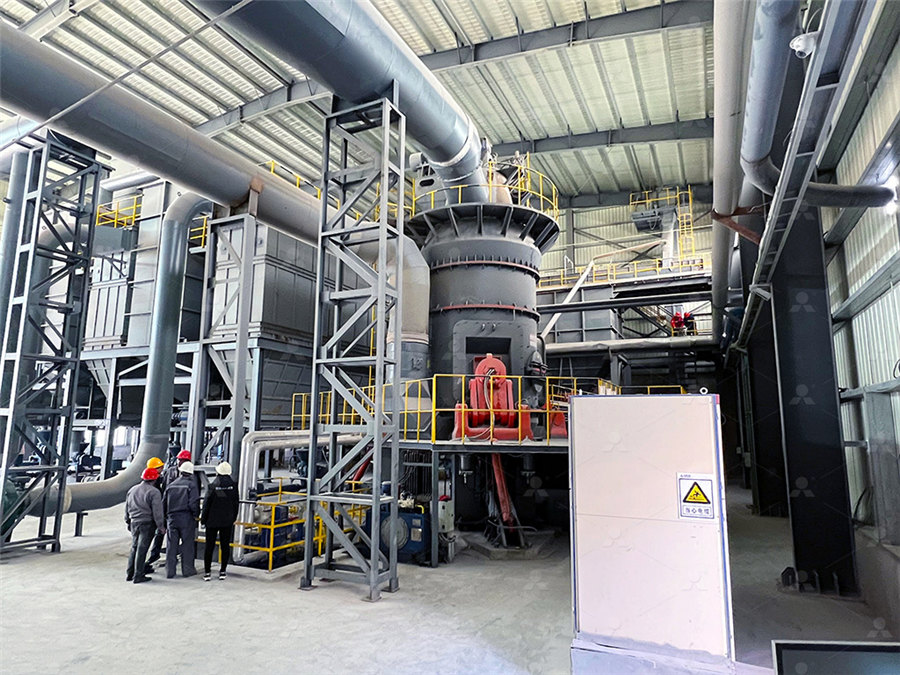
Dry Coating Fraunhofer Institute for Silicon Technology
Dry coating technology without solvent consumption implies significant material savings in the electrodes production; Drastic reduction of the mixing time thanks to adapted dry mixing processes; Accelerated production process; Less than a third of the equipment space required compared to conventional solution2021年9月20日 The basic principle of the preparation of silicon nitride powder is to produce silicon nitride powder with high purity and specific Advantages: Low raw materials, simple process, continuous production Disadvantages: Product purity is not Complex equipment and process, difficult to mass production Sol gel method Using Comparison of Six Methods for Making Silicon Nitride Powder2005年5月1日 Then, the fibrous fumed silica porous compact was formed by dry pressing of the powder mixture and exhibited fracture strength of 158 MPa at room temperature and thermal conductivity of 00282 W Dry Powder Processing of Fibrous Fumed Silica Compacts for The main method of production of fumed silica is chemical vapour deposition This process is also known as the pyrolysis, dry or combustion method Its main raw material is siloxane, mainly hexaethylsiloxane, silicon tetrachloride and methyltrichlorosilaneThe production process of fumed silica is to send the raw materialAnalysis of silica production and drying processes IOSR Journals

(PDF) Microfabrication of bulk PZT transducers by dry film
2012年8月1日 A facile fabrication process for bulk PZT microsystems using dry film photoresist and micro powder blasting is presented Bulk PZT and dry film photoresist etching characteristics are evaluated as