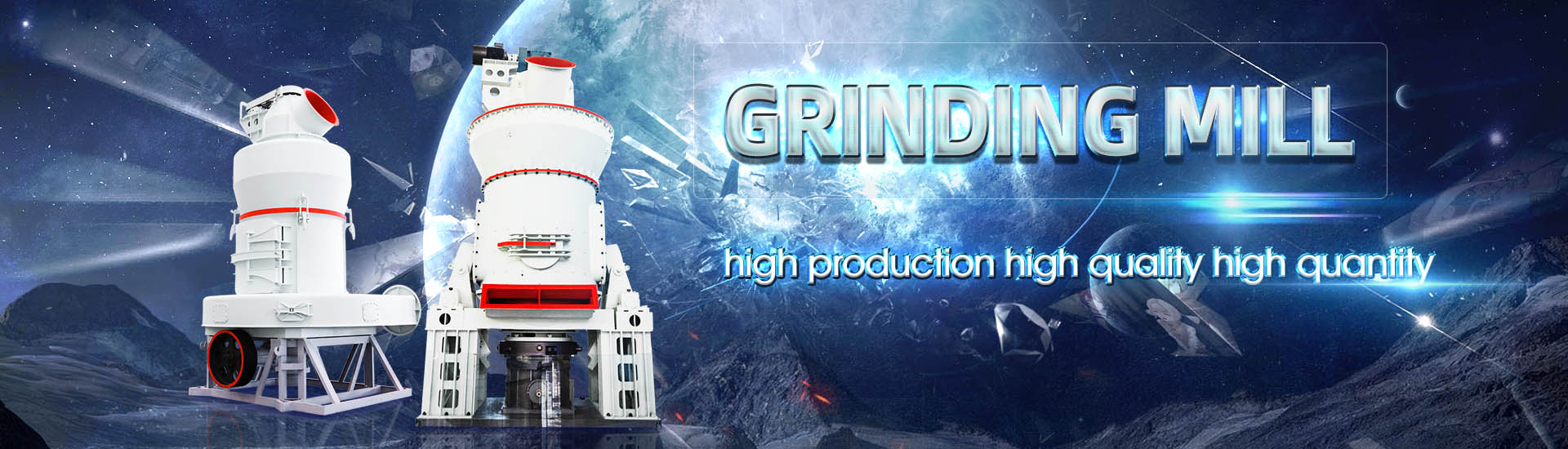
How many tons can a cement mill grind in one hour
制粉-10.25公众号.jpg)
Cement Grinding Cement Plant Optimization
Closed circuit ball mill with two compartments for coarse and fine grinding are generally found in cement plants for cement grinding Compartments (filled with grinding media) are divided by a optimization of cement grinding operation in ball mills Several energy efficient options for cement grinding are available today such as vertical roller mills, roller presses (typically in combination OPTIMIZATION OF CEMENT GRINDING OPERATION IN BALL MILLSA mill of this type would be driven by a 1200 hp motor, but the mills can vary in size from 500 hp to 6000 hp with cement outlets that can vary from 10 to 140 tons per hour As with the grinding of raw materials, both the open circuit mill and An Introduction to Clinker Grinding and Cement StorageEach running mill would make 1316 t/h, so they might typically make 52 tonnes in a shift a labour usage rate for finish milling of 046 manhours per tonne A large plant with 35 kilns, making 1000 t of clinker per week, would need 13 Cement Kilns: Size Reduction and Grinding

Roller mills INFINITY FOR CEMENT EQUIPMENT
Roller mills are now operated with throughput capacities of more than 500 tons per hour of cement raw mix (Loeschemill, Polysius double roller mill, Pfeif ferMPSmill, SKET/ZABroller mill)online live calculators for grinding calculations, Ball mill, tube mill, critical speed, Degree of filling balls, Arm of gravity, mill net and gross powerball mill calculations, grinding media filling degree, ball size, mill 2004年11月1日 Approximately 15 tonnes of raw materials are required to produce 1 tonne of finished cement The electrical energy consumed in the cement making process is in order of Cement grinding optimisation ScienceDirectAs grinding accounts for a sizeable share in a cement plant’s power consumption, optimisation of grinding equipment such as ball mills can provide significant cost and CO 2BALL MILLS Ball mill optimisation Holzinger Consulting
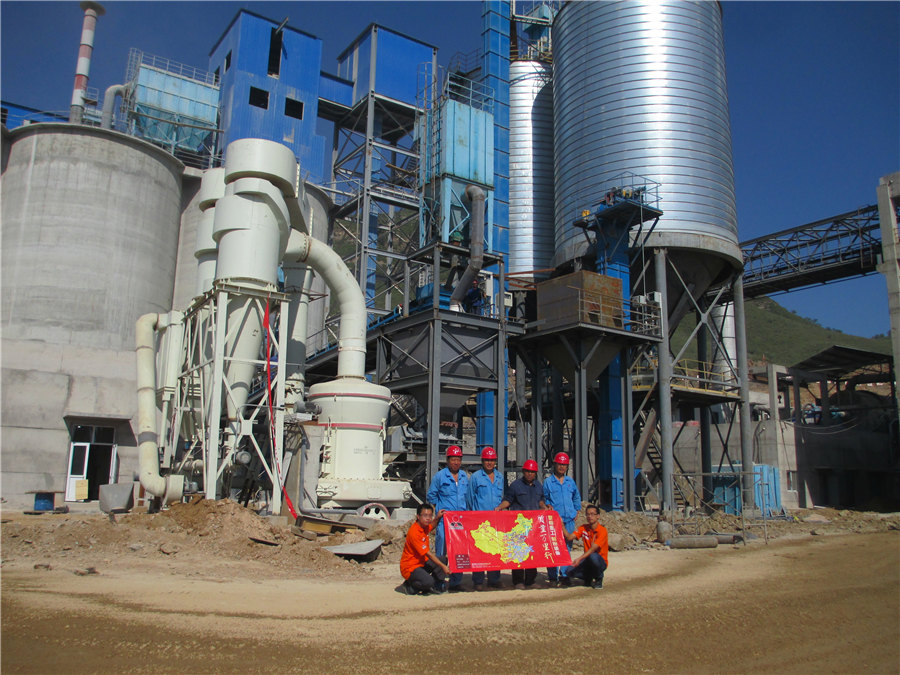
Optimization of Cement Grinding Operation in Ball
The consumption of energy by the cement grinding operation amounts to one third of the total electrical energy used for the production of cement The optimization of this process would yield substantial benefits in terms of energy Alternative cementitious materials: Researchers are also exploring the use of alternative cementitious materials, such as fly ash, slag, or pozzolanic materials, which can be used as a partial replacement for clinker in cement production (reduced the clinker to cement ratio) This can help to reduce the amount of energy and emissions associated Cement Production Demystified: StepbyStep Process and 2020年7月12日 Concrete work productivity rate are the average output per hour of the activity Each activity has a recommended list of teams for labor and equipment Skip to content Elevated one way beam, Suspended, @ 600 Concrete Work Productivity Rate2015年12月17日 With a typical 6:1 reduction ratio, the power consumption of a large jaw crusher (48 by 60) is approximately 18 tons per horsepowerhour (22 t/kWh) Source: Arthur Taggart; The power consumption of a 42inch gyratory crusher is approximately 24 tons per horsepowerhour (29 t/kWh) Source: Arthur TaggartRock Crushing Rule of Thumb 911Metallurgist
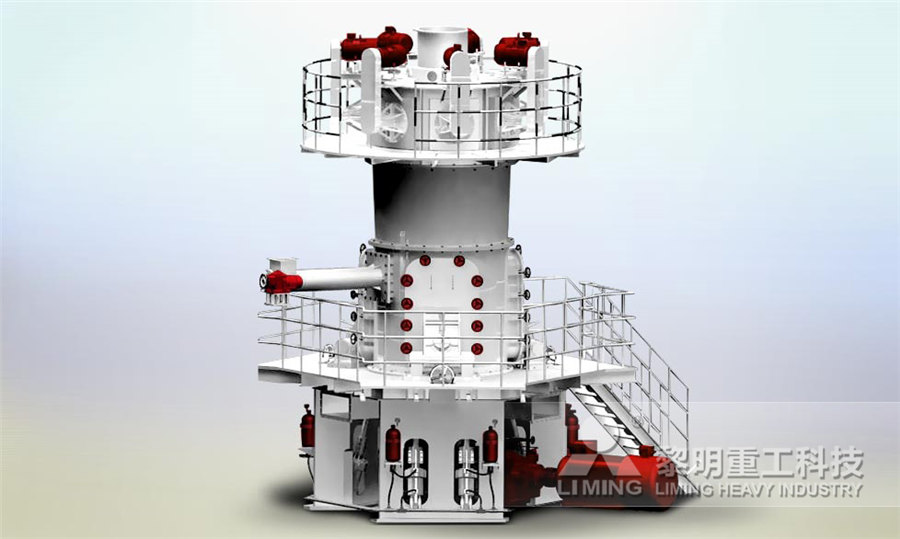
Calculate and Select Ball Mill Ball Size for Optimum Grinding
2013年8月3日 In Grinding, selecting (calculate) the correct or optimum ball size that allows for the best and optimum/ideal or target grind size to be achieved by your ball mill is an important thing for a Mineral Processing Engineer AKA Metallurgist to do Often, the ball used in ball mills is oversize “just in case” Well, this safety factor can cost you much in recovery and/or mill liner Raw mill is generally called cement raw mill, raw mill in cement plant, it refers to a common type of cement equipment in the cement plantIn the cement manufacturing process, raw mill in cement plant grind cement raw materials into the raw mix, and the raw mix is sent to the cement kiln to make cement clinker, next, clinker and other admixtures will be ground into finished cement by Raw mill Cement Plant2016年10月5日 In this chapter an introduction of widely applied energyefficient grinding technologies in cement grinding and description of the operating principles of the related equip‐ ments and comparisons over each other in terms of grinding efficiency, specific energy consumption, production capacity and cement quality are given A case study per‐ formed on a EnergyEfficient Technologies in Cement Grindingonline live calculators for grinding calculations, Ball mill, tube mill, critical speed, Degree of filling balls, Arm of gravity, mill net and gross powerball mill calculations, grinding media filling degree, ball size, mill

Ball Mill Design/Power Calculation 911Metallurgist
2015年6月19日 The ball mill motor power requirement calculated above as 1400 HP is the power that must be applied at the mill drive in order to grind the tonnage of feed from one size distribution The following shows how the size or select the matching mill required to draw this power is calculated from known tables ‘the old fashion way’Roller mills are now operated with throughput capacities of more than 500 tons per hour of cement raw mix (Loeschemill, Polysius double roller mill, Pfeif ferMPSmill, SKET/ZABroller mill) The working principle of roller mills is based on two to four grinding rollers with shafts carried on hinged arms and riding on a horizontal grinding table or grinding bowlRoller mills INFINITY FOR CEMENT EQUIPMENTThis is done by a mixture of both aircooling and watercooling, including spraying water inside the mill Cement milling and gypsum dehydration Because the cement gets hot due to the heat generated by grinding, gypsum can be partly dehydrated, forming hemihydrate, or plaster of Paris 2CaSO 4H 2 OCement Milling2020年8月25日 Cement equipment refers to all equipment in the cement plant, such as cement mill, cement crusher, cement kiln, cement silo, cement preheater, etc There are two methods to choose, drying and grinding the cement raw Cement Production Process Cement Manufacturing
.jpg)
How Much Concrete Is Used In A Wind Turbine? UtilitySmarts
The resources required for the production of cement, steel, and polymers are transported by freight trains and cargo ships Steel alone accounts for 150 metric tons for reinforced concrete foundations, 250 metric tons for rotor hubs and nacelles (which house the gearbox and generator), and 500 metric tons for the towers in a 5megawatt turbine2023年1月29日 Raw Mill is mainly used to grind raw materials into fine powder, whereas Cement Mill is used for grinding clinker and other additives to form the final cement product The main difference between the two lies in their respective input materials; Raw mill mainly accepts raw materials from the kiln whereas Cement Mill mainly accepts precrushed material from a What Is Cement Milling? Difference Between Raw Mill And Cement Mill2023年11月30日 How many tons of ore can a Raymond mill grind in one hour? In fact, the production capacity of early Raymond mills was not high Early Raymond machines named after the R series, such as 4R3220 and other common models, are all relatively small Raymond mills, with an hourly output of about 5 tons Because the demand for grinding is not high in How many tons of ore can a Raymond mill grind in one hour?2003年6月5日 Required water:cement ratio to achieve a slump of 60 to 70 mm in concretes made with different cements Cement E contained a limestone not conforming to the EN 1971 criteriaThe Use of Limestone in Portland Cement: A StateoftheArt
.jpg)
An Introduction to Clinker Grinding and Cement Storage
A mill of this type would be driven by a 1200 hp motor, but the mills can vary in size from 500 hp to 6000 hp with cement outlets that can vary from 10 to 140 tons per hour As with the grinding of raw materials, both the open circuit mill and the closedcircuit mill are used for clinker grinding2020年3月13日 What is cement vertical mill? As one of the necessary cement equipment, because the cement vertical mill has a large production capacity up to 100 tons, which can meet the need of largescale production of enterprises The cement vertical mill can quickly grind different raw materials into the required finenessWhy Choose Cement Vertical Mill?The mill produces two different size products from the same raw material Regular Grind can be produced at a rate of 10,000 pounds per hour and has a demand of 400 tons per week with a price per ton of $900 Super Grind can be produced at a rate of 6,000 pounds per hour and has a demand of 200 tons per week with a price of $1,900 per tonSOLVED: Mason Milling grinds calcined alumina to a standardMilling quickly can also put an unnecessary amount of wear on the machine “These machines are beating themselves to death and we’re trying to put one foot in the grave by running them that hard,” Chastain said Lastly, milling at high speeds can cause issues with sizing material “We’re trying to use that RAP material,” Chastain saidMaximize Milling with these Best Practices AsphaltPro Magazine
.jpg)
How to Grind Concrete Three Ways Angi
2023年6月22日 However, avoid them if you can because they can break down the concrete over time Apply a Sealer You don’t have to apply a concrete sealer, but a sealer can reduce the amount of moisture the concrete absorbs and prevent stains For newly poured concrete, you should wait 28 days before applying the sealer so it can fully hardenThe installation of liners Length Diameter Ratio The lengthdiameter ratio of the cement ball mill is relatively large For mills of opencircuit grinding system, the lengthdiameter ratio is usually between 35 and 6 to ensure that the product Cement Ball Mill Cost Effective Cement Grinding Mill 2017年7月26日 Total volume of 35 blocks required = 0502 m 3 Let the number of wheel barrow trips of sand be x Hence, (volume of 1 bag of cement) + (Total volume of sand) = Volume of 35 blocks Hence, 003472 + x(0065) = 0502 m How to Estimate the Quantity of Sand and Cement o For ball mills, only 3 – 6% of absorbed energy is utilized in surface production, the heat generated can increase mill temperature to > 120⁰ C causes excessive gypsum dehydration media coating if mill ventilation is poor Types of Improvements in New Existing Cement Grinding
.jpg)
How to Grind Concrete: A StepbyStep Guide to Concrete Grinding
2023年11月28日 Avoid excessive grinding in one spot, as it may lead to uneven results or surface damage Switch to Finer Grit: Once you have removed the desired amount of material or achieved a level surface, switch to a finergrit diamond grinding disc Continue grinding with finer grits to achieve a smooth and polished finish Clean the Surface:2019年1月3日 Clinker grinding technology is the most energyintensive process in cement manufacturing Traditionally, it was treated as "low on technology" and "high on energy" as grinding circuits use more than 60 per cent of total energy consumed and account for most of the manufacturing cost Since the increasing energy cost started burning the benefits significantly, Clinker grinding technology in cement manufacturing2024年2月23日 The operation of the cement raw mill is a critical step in cement production By grinding the raw materials into a fine powder, these powders can be more easily mixed with other cement ingredients and burn more evenly during the cement clinker process Therefore, the efficient operation of the cement raw mill directly impacts the production efficiency and quality How Does a Raw Mill Work in a Cement IndustryCement manufacturing brief description of a cement mill Cement clinker is usually ground using a ball mill This is essentially a large rotating drum containing grinding media normally steel balls As the drum rotates, the motion of the balls crushes the clinker The drum rotates approximately once every couple of secondsThe cement mill
.jpg)
How does a raw mill work in a cement plant? LinkedIn
2022年12月19日 A raw mill is a type of grinding machine used to crush material into a fine powder It is an essential component in cement plants because it is used to grind down raw materials such as limestone 2018年11月1日 Figure 31: Changing seal of cement mill • B all mill are used to grind the crushed mate rial 80100 mm and 100 tons per hour Figure 9: (PDF) A REPORT ON ONE WEEK Internship IN SHIVAM CEMENT 2020年2月1日 Nowadays, ball mills are used widely in cement plants to grind clinker and gypsum to produce cement In this work, the energy and exergy analyses of a cement ball mill (CBM) were performed and Energy and exergy analyses for a cement ball mill of a new A standard cement truck can typically hold between 8 to 14 cubic yards, so such a truck could handle this project’s need in one trip However, if the project size was larger and I calculated a need of, say, 20 cubic yards, I would need to How Much Concrete Does a Cement Truck Hold:
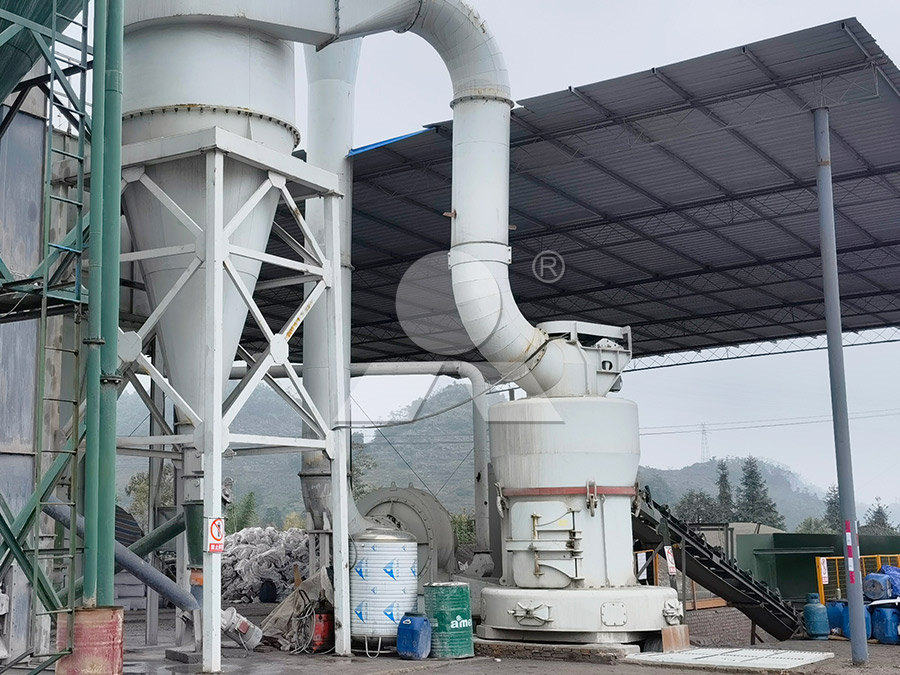
How Much Does It Cost To Start A Cement Plant?
2020年5月14日 How many factors involved in cement plant cost? cement equipment? cement manufacturer? or raw materials cost? the total cost of a cement plant is estimated to be US$ 17,000 to US$ 20,000 per ton One thing The vertical cement mill is largescale cement grinding machine With advantages of energyefficient and stable quality, vertical roller mill is widely applied to many industries, such as cement, power, metallurgy, chemical and nonmetallic Vertical Cement Mill2019年9月27日 There are various types of cement crusher on the market, including jaw crusher, cone crusher, hammer crusher, impact crusher, and etc AGICO Cement can provide all types of cement crusher Our cement crusher can fully crush the raw material, reduce feed size into the mill, and increase the reaction of raw material in the following cement manufacturing process, Cement Euipment Overview Cement Making Machines Cement 2023年4月23日 Jankovic et al [74] observed that the wear rate was higher for onehour tests than for threehour tests The authors suggest that the wear ra te of the grinding med ia varied inversely with (PDF) Grinding Media in Ball MillsA Review ResearchGate
.jpg)
BALL MILLS Ball mill optimisation Holzinger Consulting
Ball mill optimisation As grinding accounts for a sizeable share in a cement plant’s power consumption, optimisation of grinding equipment such as ball mills can provide significant cost and CO 2 emission benefits to the cement producer n by Thomas Holzinger, Holzinger Consulting, Switzerland BALL MILLS 1 FEBRUARY 2021 INTERNATIONAL CEMENT The ground material, known as mill feed, is discharged from the mill and sent to the next stage of the cement production process Importance of Cement Ball Mill Cement ball mills are essential in the cement production process for several reasons: 1 Grinding of Raw Materials: Cement ball mills are used to grind raw materials into fine powdersCement ball mill: A key component in cement production2022年9月14日 Use a milling machine to grind up the top layer of asphalt, adjusting to the depth you need, depending on your project and how damaged the asphalt is Put asphalt millings into a dump truck to be reused The crushed asphalt can be as useful of an aggregate as concrete, gravel, or fresh asphalt in resurfacingWhat is Asphalt Milling and When Should You Use It?2018年4月16日 So, if you grind 5,000 square feet in 7 hours, you would have a production rate of 714 square feet per hour Write down the date, location, job, tool, grinder, and floor condition next to the production rate so you have a complete picture This information should be kept in a log book that you bring to all your jobsConcrete Grinding Tools 101 Concrete Construction Magazine
.jpg)
Coal utilization in the cement and concrete industries
2023年1月1日 Joseph Aspdin was a bricklayer from Leeds, United Kingdom However, Aspdin’s cement was too lightly burnt (temperature≈1400°C) to be a true Portland Cement and the real prototype may have been produced in 1850 by Isaac Charles Johnson who took the temperature up to between 1400°C and 1500°C