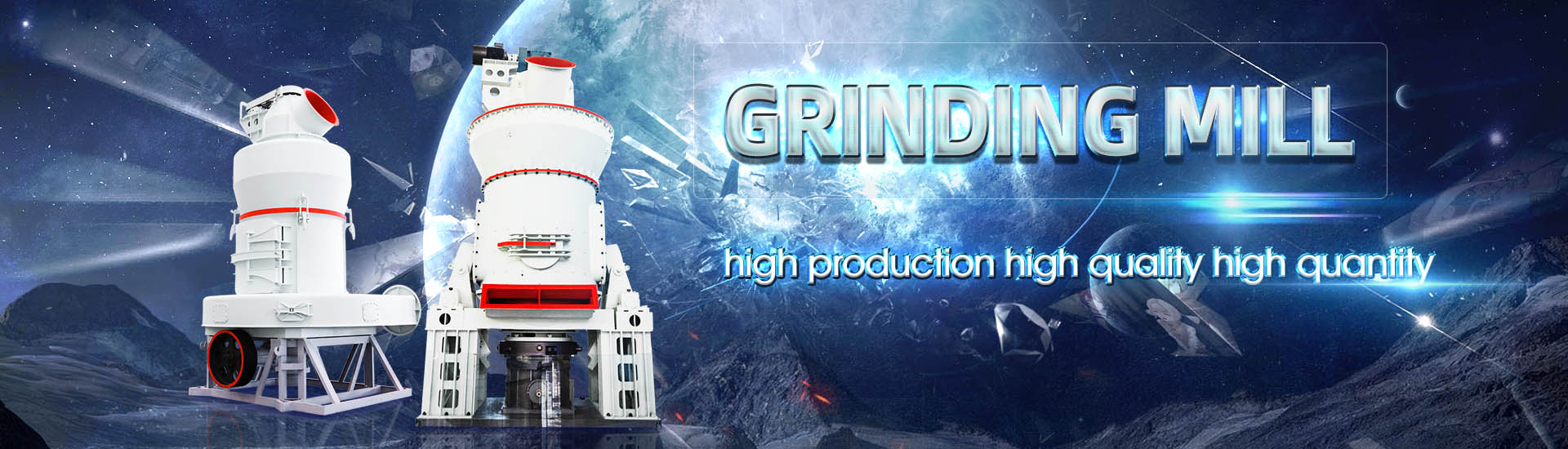
Learn the principle and process of grinding coal mill operation
.jpg)
Coal Mill an overview ScienceDirect Topics
Coal mills grind the coal into fine powder, and the primary air entering the mill dries and drives the coal into the power plant furnace for combustion Mills can be a bottleneck for the power generation process2018年8月17日 Extreme temperatures, impact velocity, mill load, grinding media, ore types, and applications are some of the factors to be considered while installing new linersGrinding Mills — Types, Working Principle Applications2013年1月1日 Principles of Modern Grinding Technology explains the principles that led to rapid improvements in modern grinding technology over recent decades Removal rates andPrinciples of Modern Grinding TechnologyThe proper functioning of grinding mills is essential for the efficiency of mining and mineral processing operations Understanding the operational principles and factors that influence mill Understanding the operation of grinding mills in the mining and
.jpg)
Grinding Mill an overview ScienceDirect Topics
Grinding can be achieved by several mechanisms, including: impact or compression due to sudden forces applied almost normally to the particle surface; chipping or attrition due to The working principle of vertical mill is as follows: the material is fed into the mill through the inlet on the top center of the mill and falls on the grinding plate, and the grinding rollers which are driven by the rotation of the grinding plate will Coal Mill in Cement PlantThe modular structure of larger roller grinding mills enables utilisation of the same components in different mill sizes Module components include grinding rollers, rocker arms, pedestals and LOESCHEMILLSprocessoptimised operation of Loesche grinding systems with the main focus on efficient performance, throughput, product consistency and availability Failsafe PLC for hot gas PROCESS OPTIMISATION FOR LOESCHE GRINDING PLANTS
.jpg)
COAL GRINDING IMPS: more than meets the eye Gebr Pfeiffer
ows the MPS series for coal grinding mills Depending on the fuel to be ground throughput rates of h feed moistures of as much as 45 per cent Depending on this high feed moisture, the mill Learn about the Vertical Grinding Mill (Coal Pulverizer)! How it works, its components, design, advantages, disadvantages and applicationsVertical Grinding Mill (Coal Pulverizer) Explained saVReeWorking Principle During the operation of the ball mill, the raw coal first enters the drying chamber through the feed inlet for drying, and the dried raw coal enters the grinding chamber for grinding and second drying The pulverized coal is Coal Mill in Cement PlantMill Feeders: Feeders for coal mill are generally installed directly under hoppers with rod gate in between The feeders are generally 2 to 3 m long and discharge on to conveyor or feeding chute to mill For coal mill feeding, table feeders, belt feeders, Coal Grinding Cement Plant Optimization

Modeling and Parameter Identification of Coal Mill
2009年9月20日 A control oriented model was then developed by Fan (1994) and Fan and Rees (1994) In 2009, coal flow and outlet temperature of mill were modelled using mass and heat balance equations for startup The raw material of coal powder is coal with various hardness, and it drying in the coal mill grinding process to obtain finished coal powder which can be efficiently burned Coal ball mills are widely used in the cement industry and thermal power generation industry, and are also suitable for metallurgical industry, chemical industry, sugar industry and other fieldsCoal Ball Mill Grinding for Different Kinds of Pulverized CoalSafe operation of coal grinding systems: Raw coal silo protection against fire and explosions Safe operation of coal grinding systems: Raw coal yard management The purchasing process for coal grinding systems needs changes Talk at a virtual seminar, November 2023 Accept the probability that the fire and explosion safety of your coal grinding system is nothing more than a mirageFire and explosion protection of coal grinding systems Where are 2014年1月1日 Two mill systems are employed for most coal grinding applications in the cement industry These are, on the one hand, vertical roller mills (VRM) that have achieved a share of almost 90% and, on (PDF) MPS mills for coal grinding ResearchGate
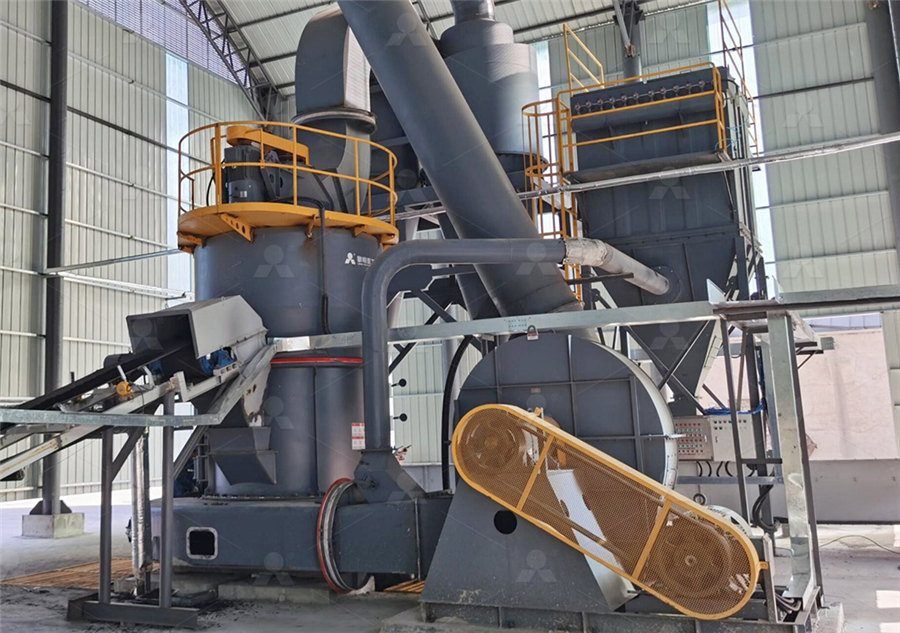
Grinding Mills — Types, Working Principle Applications
2018年8月17日 A rock cutting process, drilling sets the stage for the next steps in the mineral processing operation Be it surface or underground deposits, we are mining our way to the next stage! Stage 2 Coal grinding is a critical process in the production of energy and industrial products like cement It comes with inherent risks Ensuring the safety of workers and equipment in coal grinding operations is paramount This article outlines key safety measures and best practices to mitigate the hazards associated with coal grindingEnsuring Safety in Coal Grinding Operations Coal Mill Safety Ball mills are used for many applications in cement production: raw meal grinding, coal and petcoke grinding as well as finish cement grinding Each of these systems have their similarities and differences This ball mill training course is designed to train each participant on the overall technology, operation and maintenance of the ball mill ME068: Ball Mill Operations and MaintenanceUnderstanding the operational principles and factors that influence mill performance is crucial for optimizing mill operations and achieving the desired particle size for downstream processes By considering these factors, mining companies can enhance the productivity and costeffectiveness of their grinding mill operationsUnderstanding the operation of grinding mills in the mining and
.jpg)
Size Reduction1: Grinding – Unit Operations in Food
In the process of crushing and grinding operation, The principles of operation are compression, impact, and shear, not by compression alone, In the mill the grinding chamber is an oval loop of pipe 25 to 200 mm in diameter and 12 to The PALLA Vibrating Mill is used in a wide range of applications for process engineering duties Due to its easy operation, versatility and operation efficiency the PALLA Vibrating Mill gains in importance in the mineral processing industry This PALLAbrochure focusses on the technology and the principle of ultrafine grindingpalla VIBRATING MILL mbecoalandminera'@'lAbstract: The paper presents development and validation of coal mill model (including the action of classifier) to be used for improved coal mill control The model is developed by using the mass and heat balance equations of the coal mill Genetic Algorithm is used to estimate the unknown parameters that are used in the model validationModeling and Control of Coal MillThe coal mill is illustrated in principle in Fig 1 The coal is fed to the coal mill through the central inlet pipe The coal is pulverized on the rotating grinding table by the rollers Operation of coal mills is affected by both the moisture content and volatiles content of Coal Mill an overview ScienceDirect Topics
CFB石灰石脱硫剂制备——磨机公众号12.8 推送案例(8)53.jpg)
Grinding Process Optimization Featuring Case Studies and
The modular design of the vertical roller mill comprising 4 to 6 grinding rollers allows the continuation of mill operation even if one roller module is not availablePDF On May 1, 2017, Caroline Woywadt published Grinding process optimization — Featuring case studies and operating results of the modular vertical roller mill Find, read and cite all the (PDF) Grinding process optimization — Featuring case studies 2022年2月24日 The current work focuses on the process of grinding coals in ball drum mills for further pulverized combustion a waterfall mill operation mode was described in detail in [31]Improving the efficiency of the coal grinding process in ball drum Safe operation of coal grinding systems: Raw coal silo protection against fire and explosions Safe operation of coal grinding systems: Raw coal yard management The purchasing process for coal grinding systems needs changes Talk at a virtual seminar, November 2023 Accept the probability that the fire and explosion safety of your coal grinding system is nothing more than a mirageSafety Aspects of Coal Grinding Coal Mill Safety, Explosion and
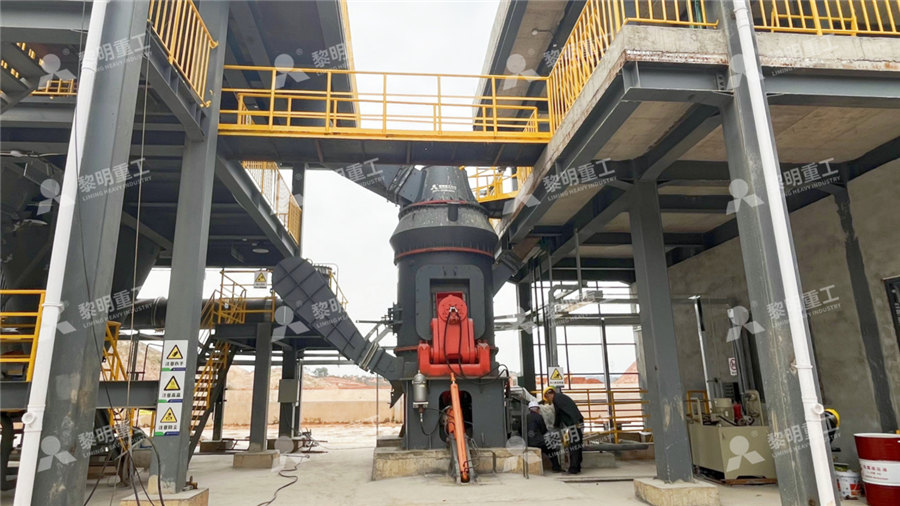
VRM Operation and Optimization PDF Mill (Grinding)
VRM operation and optimizationppt Free download as Powerpoint Presentation (ppt / pptx), PDF File (pdf), Text File (txt) or view presentation slides online The document discusses vertical mills used for grinding clinker, raw materials, coal, and cement Vertical mills can be used for both pregrinding and finish grinding They comprise rollers that are hydraulically pressed onto a vertical roller grinding mills for grinding: • Coal • Cement raw material • Clinker / granulated slag • Industrial minerals, and • Ores The core elements of these plants are the Loesche vertical mills for drygrinding the abovementioned grinding stock Loesche has PROCESS OPTIMISATION FOR LOESCHE GRINDING PLANTSThe principle of grinding precision machining: Grinding is an abrasive precision machining method that uses a lapping tool and abrasive to grind off a thin layer of metal from the surface of the workpiece based on fine machining Define The Working Principle and Types of Grinding RevealedVertical coal grinding mill integrates crushing, drying, grinding, powder selection and conveying; It has simple system and compact structure Vertical coal mill covers an floor area about 50% of the coal ball mill with the same Vertical Coal Mill for Coal Grinding in Cement Plant

Rolling operation in metal forming: Process and
2020年6月17日 A brief study on rolling operation in metal forming and equipment has been conducted The manufacturing disposition, whether in small, and large scale, contributes tremendously to national Safe operation of coal grinding systems: Raw coal silo protection against fire and explosions Safe operation of coal grinding systems: Raw coal yard management The purchasing process for coal grinding systems needs changes Talk at a virtual seminar, November 2023 Accept the probability that the fire and explosion safety of your coal grinding Coal Mill Safety: A Critical Aspect of Power Plant Operations Coal 2024年3月17日 Milling is a popular machining process Milling is a machining operation in which a revolving cutter removes material from a workpiece in a controlled manner This method of subtractive manufacturing seeks to give the workpiece the desired shape In milling operations, rotary cutting tools, typically equipped with multiple teeth or edges, are employed to precisely 16 Types of Milling Operations Explained [with PDF] The 2022年1月23日 This work concentrates on the energy consumption and grinding energy efficiency of a laboratory vertical roller mill (VRM) under various operating parametersAnalysis and Optimization of Grinding Performance of Vertical

Grinding Machine: Learn its working, types, and applications
Operations on Grinding Machine After gaining knowledge of the parts and the definition of the machine, it is easier to understand the common grinding machine operations or processes Let’s study more Surface Grinding Process One of the most frequent grinding process is the surface grinding Process2020年10月5日 Advantages of the ball mill Ball milling boasts several advantages over other systems: • the cost of installation and grinding medium is low; • it is suitable for both batch and continuous operation, • similarly it is suitable for open as well as closed circuit grinding • It is applicable for materials of all degrees of hardnessCement industry : grinding process of ball mill PPT SlideShareSafe operation of coal grinding systems: Raw coal silo protection against fire and explosions Safe operation of coal grinding systems: Raw coal yard management The purchasing process for coal grinding systems needs changes Talk at a virtual seminar, November 2023 Accept the probability that the fire and explosion safety of your coal grinding system is nothing more than a mirageIndirect Firing Coal Grinding Systems: Enhancing Efficiency and 2024年6月17日 Continuous operation: A welldesigned hammer mill system can run continuously, so you do not need to wait to receive crushed materials Continuous operation can increase output and improve productivity Easy maintenance: Removeable door covers and accessible parts make cleaning and repairing custom hammer mills simple and easyUnderstanding Hammer Mill Operation Pulva
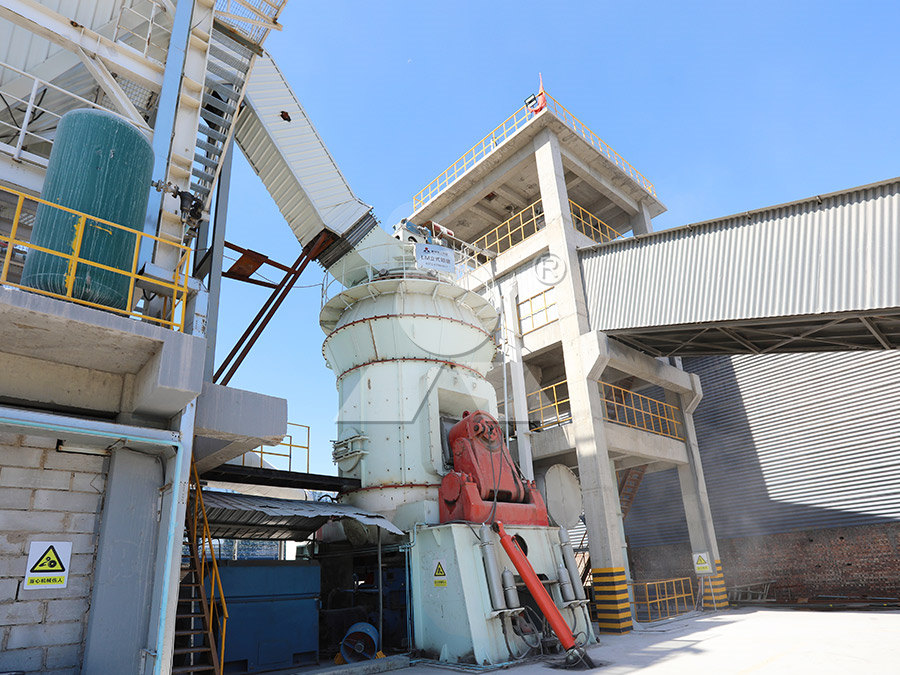
Coal mill, gypsum mill, clay mill, etc Pfeiffer MPS mills
Grinding of coal, petcoke, clay, limestone, quicklime, The grinding principle and the high efficiency classifier ensure the reduction of electric energy consumption by up to 40% as compared and remote control of grinding pressure and 2022年11月28日 Grinding is a type of finishing process in mechanical processing, with less machining and high precision It is widely used in the machinery manufacturing industry The heattreated and quenched carbon What is Grinding Process How It Works Different 2020年10月9日 In order to obtain the optimal operation parameters of a SAG mill, in this paper, the discrete element method (DEM) is used to simulate the breakage process of the particles by controlling three Operation Analysis of a SAG Mill under Different The grinding process of the ball mill is an essential operation in metallurgical concentration plants Generally, the model of the process is established as a multivariable system characterized Flow diagram of the ball mill grinding process

LOESCHEMILLS
1927 First Loesche coal mill delivered for the Klingenberg power station in Berlin 1953 500th coal mill plant sold worldwide 1961 Introduction of hydraulic spring assembly system 1965 Construction of first pressure mill (LM 122 D) 1980 Delivery of first modular coal mill (LM 263 D) 1985 Delivery of first selfinerting coal grinding plant (LM 212 D) for the steel industry (PCI Coal grinding is a critical process in various industries, particularly in power generation and cement production However, the process involves significant safety risks due to the combustible nature of coal dust and the mechanical hazards posed by the operation of the mill Ensuring safety during coal grinding is essential to prevent accidents, exAspects of Coal Mill Safety Coal Mill Safety, Explosion and Fire 2024年1月11日 The 5step process to pulverize coal efficiently The coal pulverization process involves a precise sequence of steps Each is systematically designed to convert raw coal into a fine, efficient powder But you have to start by prepping up the coal rock before the grinding process Step 1: Crush the coal rock The coal pulverization steps begin How to Process Coal into Pulverized Coal in 5 Steps?Safe operation of coal grinding systems: Raw coal silo protection against fire and explosions Safe operation of coal grinding systems: Raw coal yard management The purchasing process for coal grinding systems needs changes Talk at a virtual seminar, November 2023 Accept the probability that the fire and explosion safety of your coal grinding system is nothing more than a mirageIn discussion: Coal Mill Safety Coal Mill Safety, Explosion and

Derivation and validation of a coal mill model for control
Detailed models of the coal pulverization process in a mill have been presented by Austin, Shah, Wang, Gallagher, and Luckie (1981), According to the basic principle ‘‘Nature is simple’’, The equations have been derived for nominal grinding operation of a mill, but they also capture the start up and shut down dynamics well55 known as the distribution function [45, 46]) describes the distribution of fragment sizes obtained after a breakage of particles of size xjThus, b1j, b2j, , bnj are the mass fractions of particles in size classes 1, 2, , n after a breakage of particles in size class j The mechanism of breakage is illustrated in [23] by a diagram shown in Fig 3Grinding in Ball Mills: Modeling and Process Control Sciendo