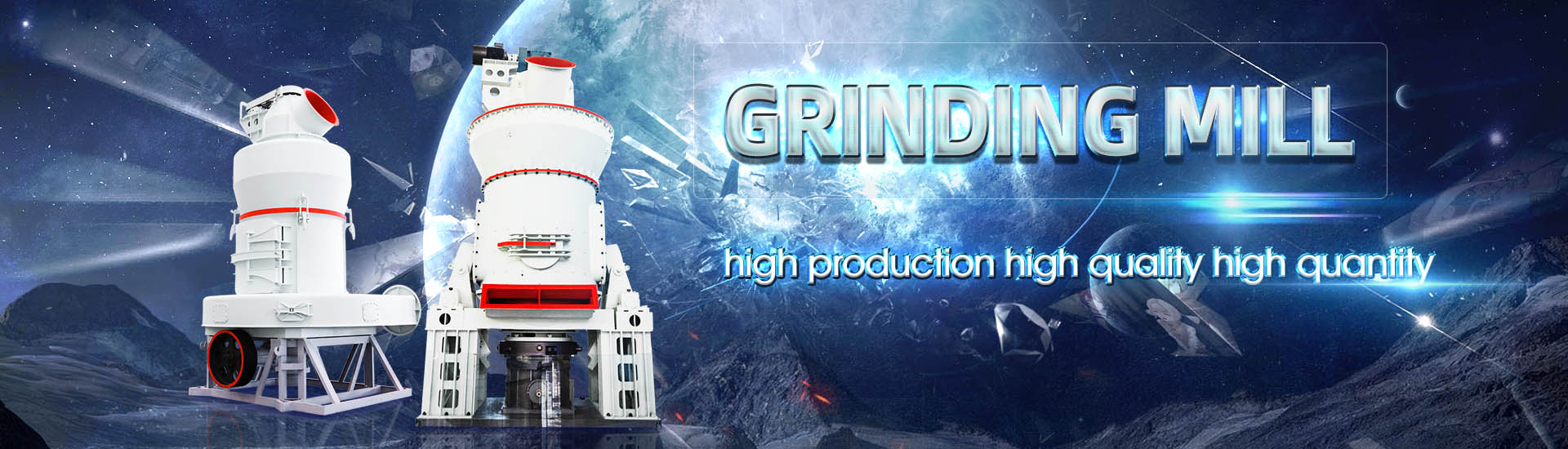
What are the characteristics of automatic feeding coal mill
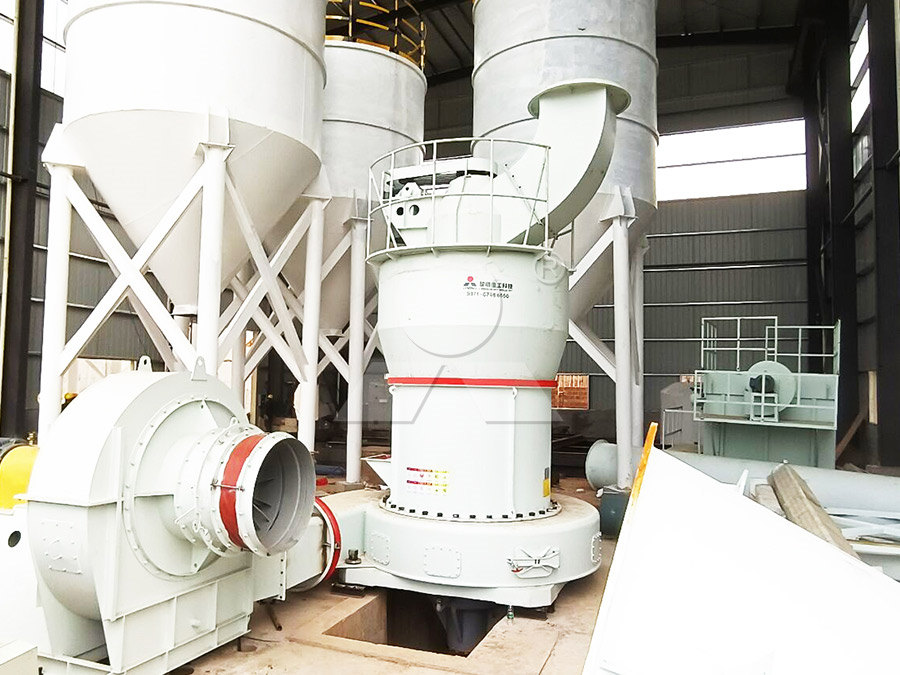
AUTOMATION AND OPTIMIZATION OF COAL GRINDING BY
automatic control mode “Automatic” The coal is fed into the mill by means of a raw coal feeder (RCF) controlled directly by the controlleroptimizer The controlling action of the controlleroptimizer is performed by regulating the rotation frequency of the RCF drive The system is Mills are mechanical devices used to break different types of solid materials in small pieces by grinding, crushing or cutting In pulverised coalfired power plants, a pulveriser coal mill grinds Coal Mill an overview ScienceDirect Topics1997年8月1日 This paper describes the analysis results of the dynamic characteristics of coal grinding mills used in a large coalfired power generation unit The aim of the work is to Analysis of coal Mill Dynamic Characteristics Under Normal and 2015年11月1日 Coal mills are bottleneck in coal–fired power generation process due to difficulty in developing efficient controls and faults occurring inside the mills In this paper, a dynamic A unified thermomechanical model for coal mill operation
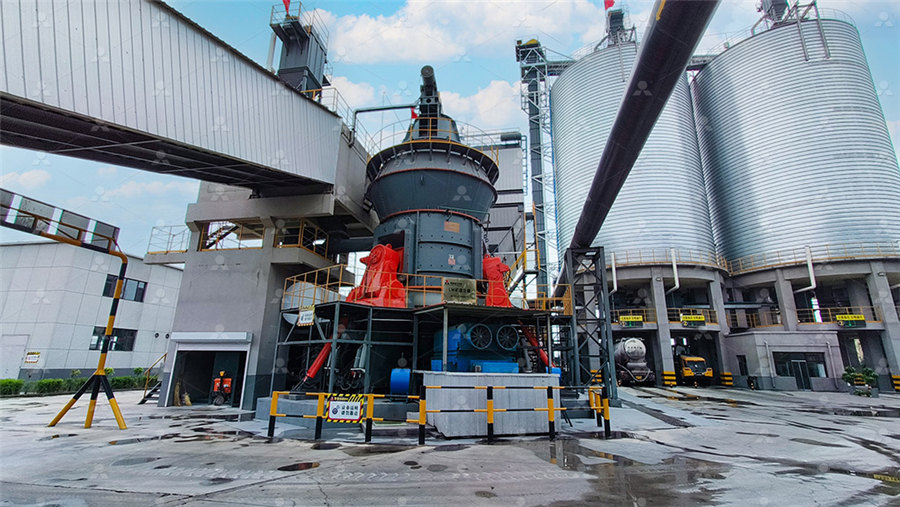
An investigation of performance characteristics and
2020年8月12日 Obtained results indicate that grinding pressure, primary air (PA) temperature and mill motor current have a tendency to rise by increasing coal feeding mass flow rates for all used coalTypical Stock Feeder Accuracy Accurate fuel delivery ensures stable combustion control and rapid response to changes in boiler load The STOCK ® gravimetric feeder is designed to provide uninterrupted fuel delivery with a feed rate Coal Feed Systems For Boiler and Coal Milling Plant 2020年8月12日 In a power plant, the coal mill is the critical equipment, whose effectiveness impacts the overall power plant efficiency Uniform coal feeding mass flow rate and required An investigation of performance characteristics and energetic Feed mill automation can help to substantially increase production, reduce costs, reduce error, increase safety, and generally increase efficiency at your facility In this guide, we’ll discuss Copy of APEC Complete Guide to Feed Mill Automation
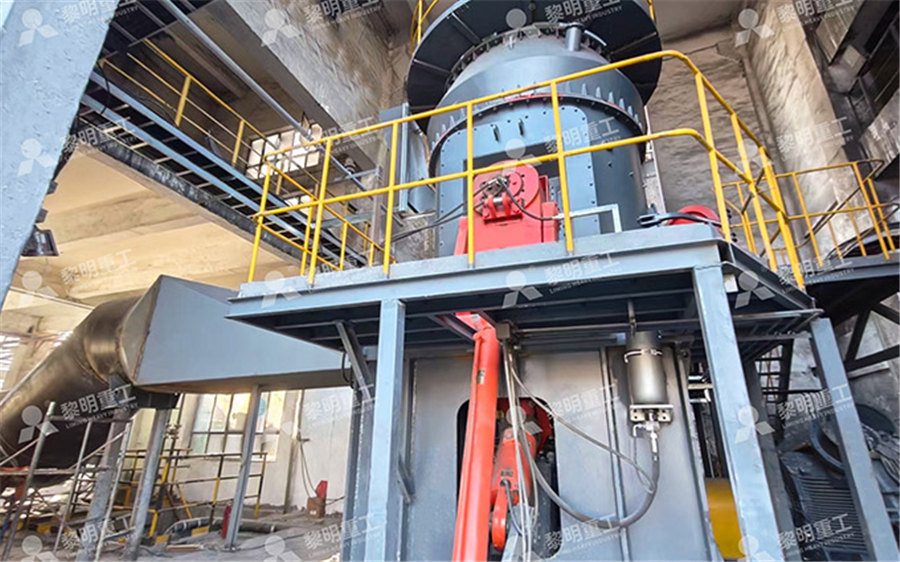
COAL GRINDING IMPS: more than meets the eye Gebr Pfeiffer
The MPS coal grinding mill with a high drying capacity is very suitable for grinding lignites with feed moistures of as much as 45 per cent Depending on this high feed moisture, the mill 2021年7月7日 It integrates crushing, grinding, dust removal, and packaging Its integrated function can greatly reduce labor for enterprises It is an industrial grinding mill with extremely highcost performance for enterprises such as ore What are the types of industrial grinding mills?A simple energy balance model of the coal mill is derived in (Odgaard and Mataji 2006), this model is based on a more detailed model found in (Rees and Fan 2003)In this model the coal mill is seen as one body with the mass m mThe following variables are defined: T(t) is the temperature in the coal dust flow in the mill, ṁ PA (t) is the primary air mass flow, T PA (t) is Coal Mill an overview ScienceDirect Topics2014年1月1日 Two mill systems are employed for most coal grinding applications in the cement industry These are, on the one hand, vertical roller mills (VRM) that have achieved a share of almost 90% and, on (PDF) MPS mills for coal grinding ResearchGate
.jpg)
Optimization and transformation of 300MV units steel ball coal mill
Coal quality characteristics and pulverized coal fineness during the test Because of the change of coal market, the coal quality deviates from the original designed coal quality,the operatingDownload scientific diagram Effect of mill outlet temperature on the coal volatile matter from publication: An investigation of performance characteristics and energetic efficiency of vertical Effect of mill outlet temperature on the coal volatile matter2019年11月7日 Comprehensive treatment,we should have a test on the 300 MV unit steel ball coal mill pulverizing systemAt the same time,analyze the main operating parameters before modificationTransform the Optimization and transformation of 300MV units steel ball coal mill 2015年12月12日 In industrial production, material level control of ball mill are normal operation of ball mill is of great significance In view of the ball mill run time nonlinear, big inertia and strong coupling characteristic, studied a kind of fuzzy PID based on PLC 300 ball mill feeding control algorithm, based on fuzzy reasoning to selftuning of PID parameters, realized the automatic Ball mill feeding based on fuzzy adaptive control system
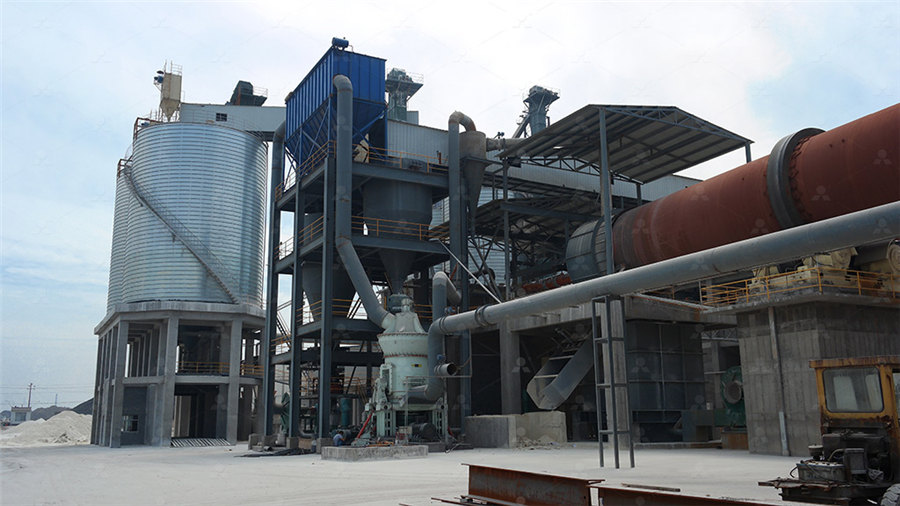
Effect of mill outlet temperature on the coal moisture content
Download scientific diagram Effect of mill outlet temperature on the coal moisture content from publication: An investigation of performance characteristics and energetic efficiency of vertical 2012年11月17日 20 131Fineness Fineness is an indicator of the quality of the pulverizer action Specifically, fineness is a measurement of the percentage of a coal sample that passes through a set of test sieves usually designated at 50, 100, and 200 mesh A 70% coal sample passing through a 200 mesh screen indicates optimum mill performance The mill wear and Coal mill pulverizer in thermal power plants PPT SlideShareDownload scientific diagram Technical specifications of vertical roller coal mill from publication: An investigation of performance characteristics and energetic efficiency of vertical roller Technical specifications of vertical roller coal millMill Type Overview Three types of mill design are common The Overflow Discharge mill is best suited for fine grinding to 75 – 106 microns; The Diaphram or Grate Discharge mill keeps coarse particles within the mill for additional AMIT 135: Lesson 7 Ball Mills Circuits – Mining
.jpg)
Five essentials for optimizing hammermill operations
Controlling the feed rate and ensuring massflow characteristics to the direct mill feeding device is critical to success Most systems use pocket rotary feeders and custom rotary valves The pocket rotary feeder is designed for this application automatic control mode “Automatic” The coal is fed into the mill by means of a raw coal feeder (RCF) controlled directly by the controlleroptimizer The controlling action of the controlleroptimizer is performed by regulating the rotation frequency of the RCF drive The system is equipped with a controlling relayAUTOMATION AND OPTIMIZATION OF COAL GRINDING BY The Raymond® Bowl Mill is considered the finest vertical rollermill available for pulverizing coal Each bowl mill system is designed to achieve thebest solution forthe processing application The mill, feeder, classifier, fan, cyclone,dust collector and other system components are selected to meet the requirementsand characteristics of the material processedRaymond® Bowl Mill Coperion2011年12月31日 The intrinsic safety characteristics of combustion and explosion in coal dust were studied using the minimum ignition energy (MIE) test, minimum ignition temperature (MIT) of cloud apparatus, and (PDF) Operation and Maintenance of Coal Handling System in
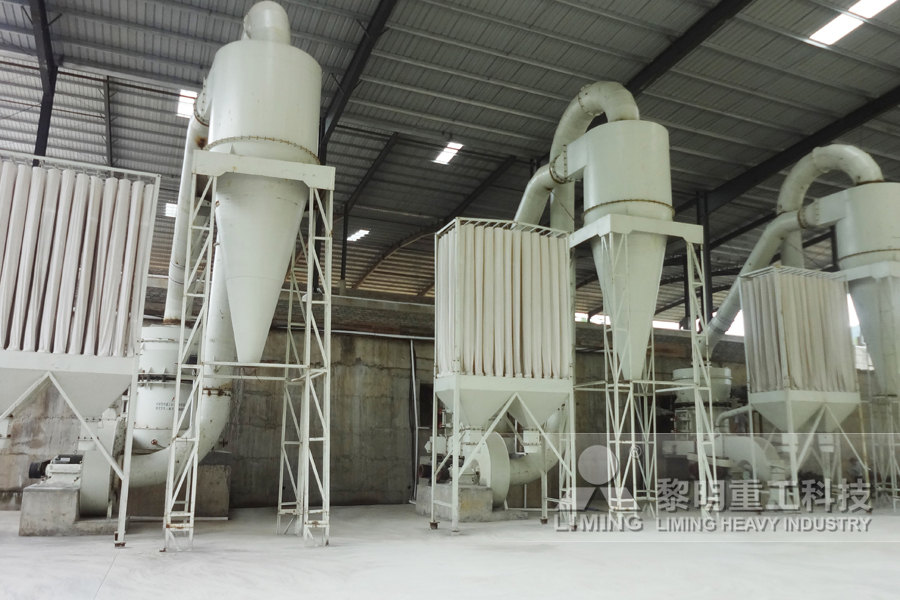
MultiObjective Optimization of Coal Mill Outlet Temperature
Multiobjective Optimization of Coal Mill Outlet Temperature Control Using MPC Zengji Zhang1, Yicheng Zhang2, Wei Shen2, BOE Xukang Lyu3,∗ 1Sinoma International Engineering Co, Ltd, Nanjing, Jiangsu, China 2College of Computer Science and Technology, Zhejiang SciTech University, Hangzhou, Zhejiang, China 3Zhejiang New Rise Digital Technology Co, Ltd, 2023年5月17日 This can entail employing a crusher or other coal preparation machinery to reduce the size of the coal A sufficient feed size for the hammer mill is the goal Feeding: The feeding machine then supplies the hammer mill with prepared coal It usually enters the hammer mill’s grinding chamber by gravity from a hopper or a conveyor beltWhat Is Coal Hammer Mill? SBM Mill Crusher2015年8月1日 Mill problems originate mainly due to poor controls or faults occurring within the milling system As discussed by GQ Fan and NW Rees [3], the control of mills remains very simple in most of the power plants due to the fact that the mill system is highly nonlinear with strong coupling among the variables and it is very difficult to measure some important Review of control and fault diagnosis methods applied to coal 2015年2月1日 A nonlinear coal mill model with three inputs and three outputs is established in this study The dynamic characteristics of coal moisture, pulverized coal moisture, and outlet temperature of the coal mill are considered in the model The parameters of the model are identified by the genetic algorithm and verified by online measurement dataModelling and control of pulverizing system considering coal moisture
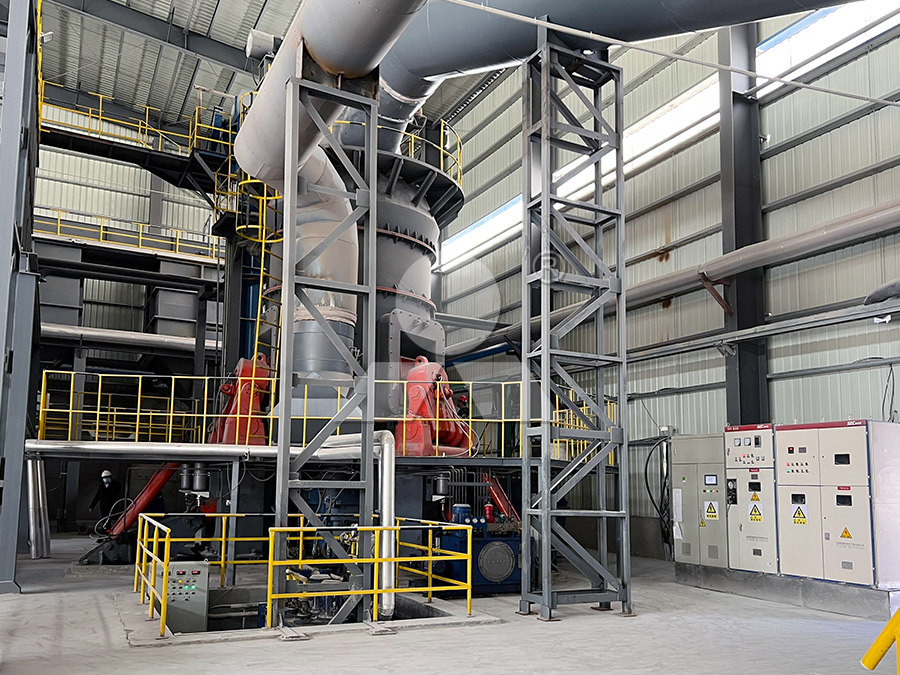
Investigation of the Performance of a 660MW Supercritical
2022年6月18日 This paper presents an indepth experimental evaluation conducted on a 660MW supercritical boiler having a steam generation of 1917 tonnes and a steam pressure of 242 kg/cm2 Significant parameters affecting the performance of boilers are analyzed, viz size of coal, various air distribution nozzles through primary air (PA) nozzles with coal flow, concentric firing 2019年1月1日 A grain size reduction hammer mill for crushing corn (Zea mays L) was designed depending on variety characteristics and by using computer aided design “ANSYS” softwareDesign and Evaluation of Crushing Hammer mill2023年7月4日 It was successfully designed in 1984, the first high pressure roller mill was applied in the cement industry in 1985, and by 2015 it had been widely used in various metal and nonmetallic minerals such as iron ore, manganese ore, cement raw clinker, limestone, blast furnace slag, and coal The highpressure roller mill mainly consists of the Roller Mill SpringerLink2020年4月7日 characteristics of a coal mill system in the fault state, and it is i mpossible to be used for fault simulation Therefore, on the basis of pr evious work, in order Modeling of Coal Mill System Used for Fault
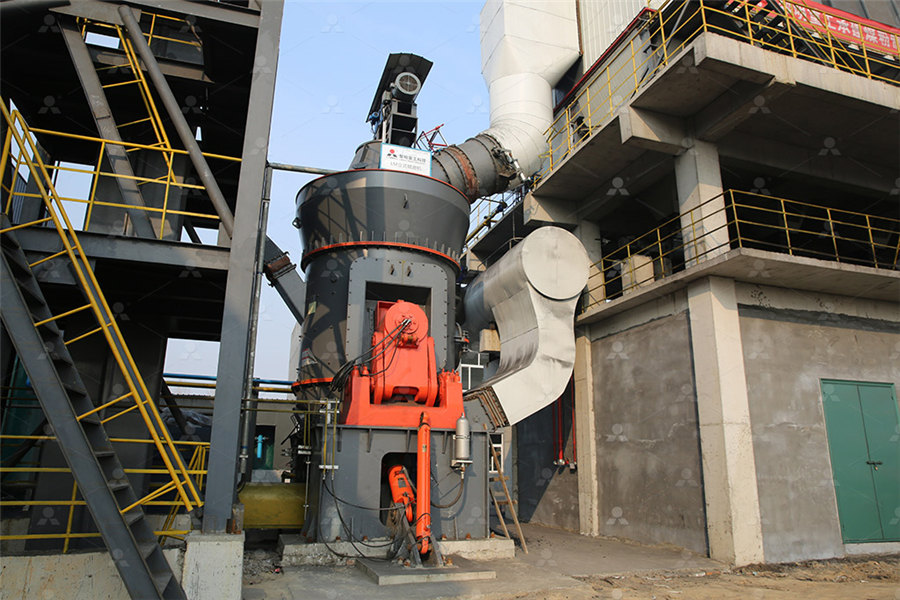
Coal Mill in Cement Plant
A coal mill is also called a coal pulverizer or coal grinder It is a mechanical device used to grind raw coal into pulverized coal powders The most used coal mills in cement plants are airswept ball mills and vertical roller mills At present, most cement plants use coal as the main fuel in the clinker production process31 The feeding device of the coal mill The feeding device adopts the louver structure that can feed air and materials at an inclined angle, which makes the feeding smoother A sealing device is provided at the contact point between the feeding device and the rotating part to prevent cold wind from entering from hereAirSwept Coal Mill of High Quality Fote Machinery2021年7月1日 And the mixing combustion needs to increase auxiliary equipment, thus increasing the operating cost According to these characteristics of coal gasification slag, the properties of carbon residue (discussed in Section 221), the quality improvement of carbon residue (discussed in the fourth section) and cyclic mixing sintering have been studiedReview of the characteristics and graded utilisation of coal 2023年1月9日 Automatic detection of material supply interruption; Accurate dosing cylinder; Stepper motor speed starting from 01 up to 200 rpm; Disadvantages Relatively more expensive than a volumetric feeder, but short ROI Volumetric feeder Advantages Relatively low priced dosing system; Accurate dosing cylinder; Stepper motor speed starting from 01 Gravimetric feeder versus volumetric feeder Movacolor
.jpg)
Modeling of Coal Mill System Used for Fault Simulation MDPI
2020年4月7日 Monitoring and diagnosis of coal mill systems are critical to the security operation of power plants The traditional datadriven fault diagnosis methods often result in low fault recognition rate or even misjudgment due to the imbalance between fault data samples and normal data samples In order to obtain massive fault sample data effectively, based on the • Coal characteristics profoundly influence risk – Lower rank coals are generally more easily ignited inside the coal mill – High volatile matter and highly reactive coals encourage preignition inside the mill – Higher moisture content requires temperature extremes inside the millMill Inerting and Pulverizer/Mill Explosion MitigationThis arrangement suits applications for retrofitting that are being encountered Bunker Gates Q Custom designed to suit wide range of bunker sizes Q Designed to close through a standing column of coal Q Manual or Power operation Typical Feeder Arrangements The Standard Gravimetric Coal Feeder Q Designed to withstand 35 bar g explosion pressure per NFPA Coal Feed Systems For Boiler and Coal Milling Plant Gravimetric 2015年2月1日 Considering the effect of coal moisture on the energy balance of the coal mill, Zeng [5] et al established a dynamic model of a coal mill and designed an optimized control scheme for the coal Modelling and control of pulverizing system considering coal moisture
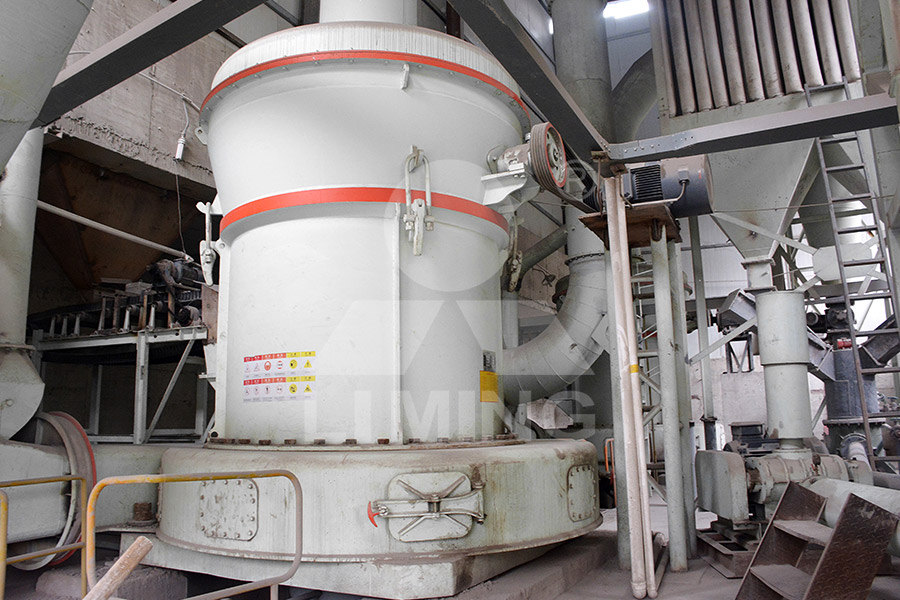
Coal Pulverizers an overview ScienceDirect Topics
Similarly, material level estimation of the coal in the mill can be used for designing better controls [37] There are a number of researchers who have worked on determining the level of coal mass inside the ball mill by developing models using various soft computing techniques (like neural network, fuzzy logic and genetic algorithm) [38–41]Analysis of Coal Mill Operation Free download as PDF File (pdf), Text File (txt) or read online for free This document analyzes the comilling of coal and wood biomass in a ringball mill It describes tests conducted pulverizing hard coal Analysis of Coal Mill Operation PDF Mill (Grinding) 1997年8月1日 This is because the mill coal transportation capability and size distribution of both mill suspended coal and coal on the grindi ng table are functions of mill air flow When the air flow is changed, the size distribution of the coal in the mill, coal on the grinding table and coal suspended in air/coal mixture stream, is changedAnalysis of coal Mill Dynamic Characteristics Under Normal and 2018年12月1日 Furthermore, the regular geometry and standard size allow compact storage, convenient handling, and automatic feeding in large scale unit operations Among various types of pellets, wood pellets are commonly used biomass for modern bioenergy In 2016, 165 million tons (~03 EJ) of wood pellets were traded internationally [17]Production and utilization of fuel pellets from biomass: A review
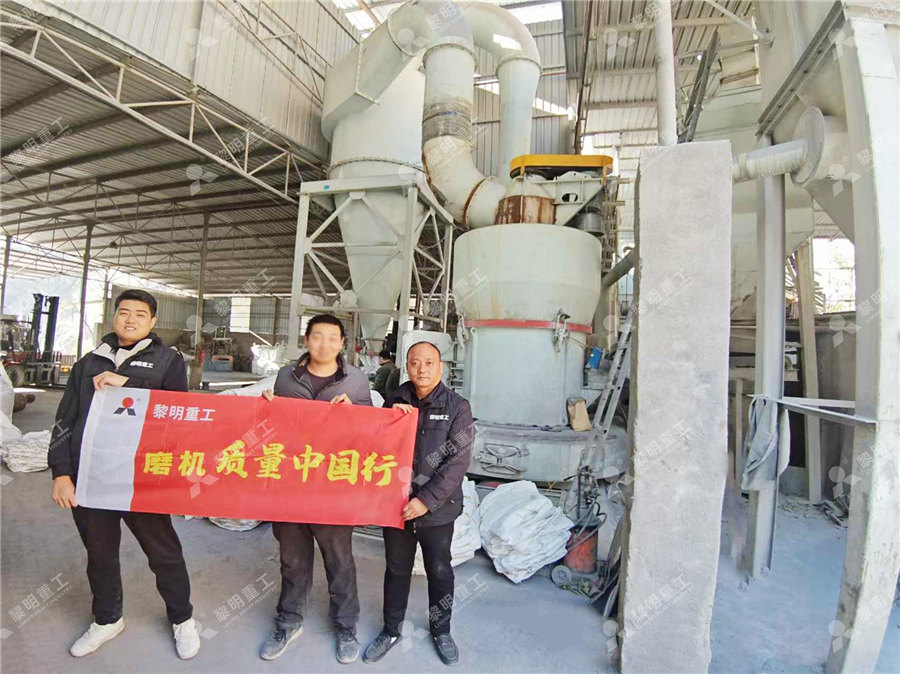
28 SOP of Coal Mill Coal Feeder
This standard operating procedure outlines the steps for starting up and shutting down the coal mill and coal feeder system at the Singareni Thermal Power Plant's 2x600 MW power plant The procedure describes the line up process, startup, shutdown, isolation, and routine checks for the coal mill It provides responsibilities and ensures proper operation to safely deliver pulverized Air Swept Coal Mill Working Principle First, the raw coal is fed into the feed chute by the feeding device Then, the hot air with a temperature of about 300 ℃ enters through the air intake pipe and begins to dry the raw coal while they are falling After Air Swept Coal Mill Coal Mill In Cement Plant AGICO GROUP2020年4月2日 The need to operate a boiler efficiently in today's environment is at the top of many plant owners and operators lists Unfortunately, operating a boiler efficiently and meeting local emission Analysis of the Coal Milling Operations to the Boiler Parameters2021年8月1日 A root cause failure analysis of coal mill vertical shaft used in thermal power plant has been carried out The failed parts of the shaft showed the signature of fatigue failures(PDF) Fault analysis and optimization technology of HP
.jpg)
Grinding in Ball Mills: Modeling and Process Control
2012年6月1日 As the cylinder starts to rotate, the grinding balls inside the cylinder crush and grind the feed material, generating mechanical energy that aids in breaking bonds, activating the catalyst, and