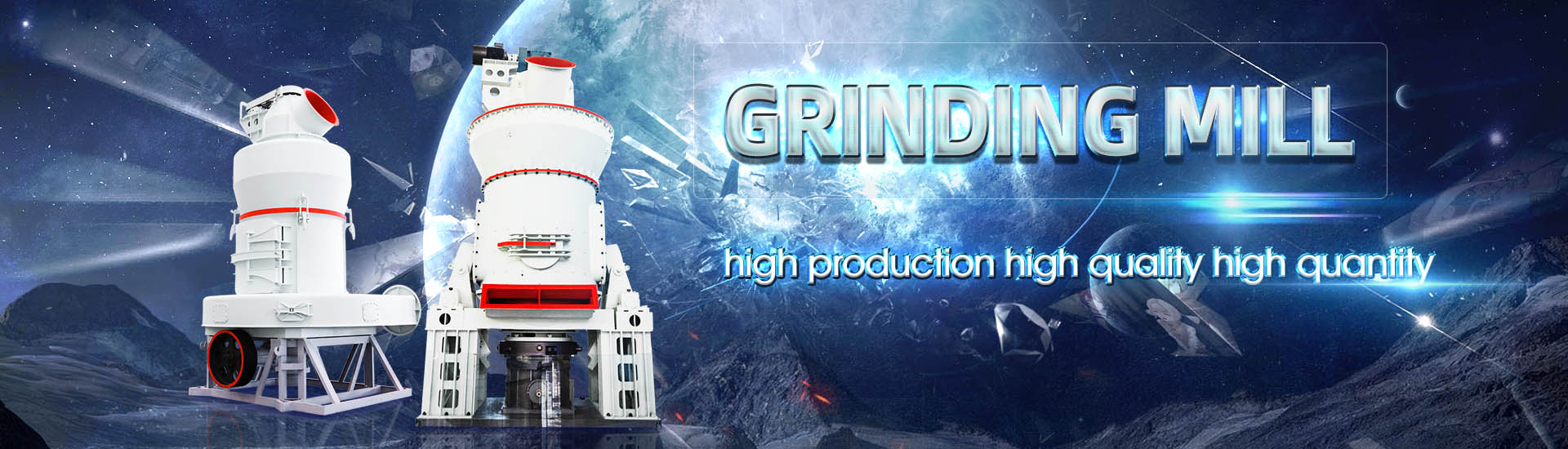
Power consumption of 35x13m cement openflow mill
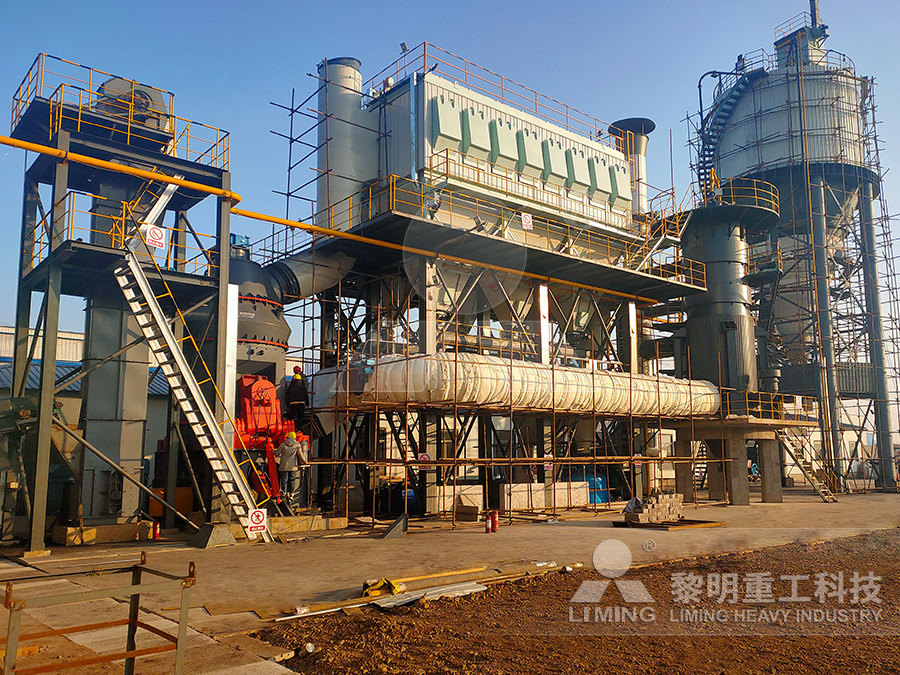
Modeling of energy consumption factors for an industrial cement
2022年5月9日 By initiating a CL for an industrial cement vertical roller mill (VRM), this study conducted a novel strategy to explore relationships between VRM monitored operational variables and theirFull Size Image Modeling of energy consumption factors for an industrial Full Size ImageIn cement plant about 75% electric power is consumed by comminution equipment such as crushers and ball mills and theoretically only 2% of the whole power is used by comminution, Optimizing Electrical Energy Consumption In Cement Process 2012年6月1日 The specific energy consumption for farine production is determined to be 2475 kWh/ton farine The use of an external hot gas supply provides 67% reduction in energy Reducing energy consumption of a raw mill in cement industry
.jpg)
Optimization of Energy Consumption in ElectricPowered Modular
By leveraging AI, modular cement plants can optimize their energy consumption, minimize waste, and enhance overall operational efficiency This paper investigates the role of AI in driving 2011年5月1日 The typical electrical energy consumption of a modern cement plant is about 110–120 kWh per tonne of cement [19] The main thermal energy is used during the burning A critical review on energy use and savings in the cement industriesBy initiating a CL for an industrial cement vertical roller mill (VRM), this study conducted a novel strategy to explore relationships between VRM monitored operational variables and theirModeling of energy consumption factors for an industrial cement 2022年5月9日 By initiating a CL for an industrial cement vertical roller mill (VRM), this study conducted a novel strategy to explore relationships between VRM monitored operational Modeling of energy consumption factors for an industrial cement
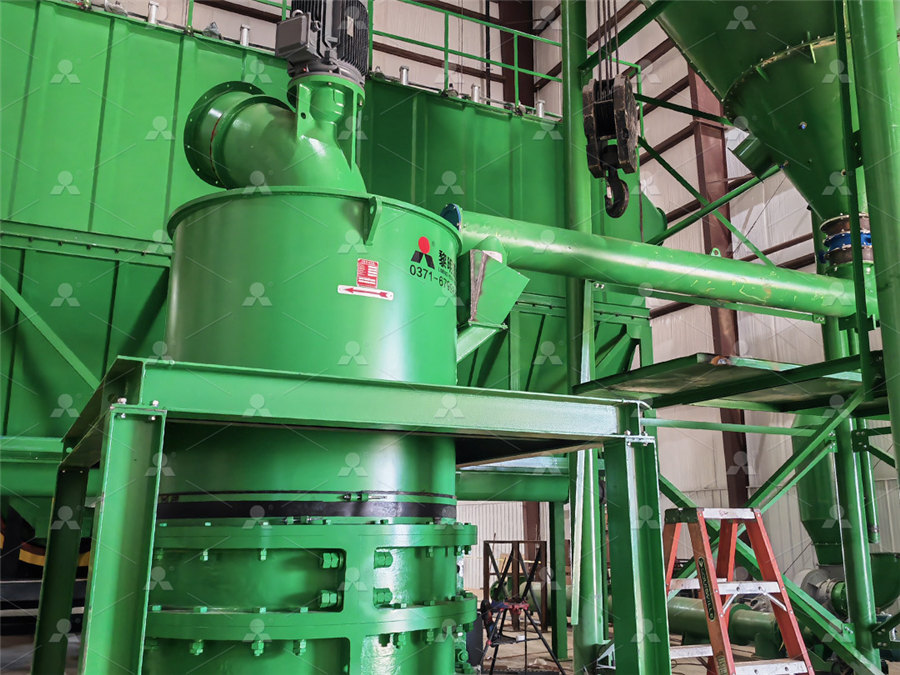
A decision support tool for cement industry to select energy
2020年3月1日 Cement accounts for 83% of total energy use in the production of nonmetallic minerals and 94% of CO2 emissions Both financial and technical aspects need to be taken For the cement industry, the international BPT for total energy consumption is 302 GJ/t cement, which is lower than the national BPT value of 361 GJ/t cement In Chapter 46, energy saving Benchmarking Report for the Cement Sector UNIDOThe optimal configuration to minimize the workshop's specific power consumption was obtained for a maximum mill outlet temperature of 1125°C, a maximum capacity of mill feed throughput Specific Electricity Consumption optimization of Raw Grinding power consumption at mill shaft with this charge as 4110 kW • Process measurements were conducted The details and observations on process measurements are given below: Mill vent flow : 972 m 3/min Separation air at separator outlet : 5599 m 3/min Separator vent air at bag filter outlet : 210 m 3/minPROCESS DIAGNOSTIC STUDIES FOR CEMENT MILL
.jpg)
Ball motion, axial segregation and power consumption in a full
2009年8月1日 The power draw is the energy consumed by the mill in setting up and maintaining the steady circulating flow of charge The power draw consumed by the first chamber is 8234 kW and by the second chamber is 1495 MW for a total power draw for the mill of 232 MW This prediction is within the expected range for such a mill2021年1月1日 India is the world's second largest producer of cement and produces more than 8 per cent of global capacity Due to the rapidly growing demand in various sectors such as defense, housing, commercial and industrial construction, government initiative such as smart cities PMAY, cement production in India is expected to touch 550–600 million tones per Review on vertical roller mill in cement industry its performance 2024年1月5日 Closedcircuit ball mill grinding plant Advantage: Lower power consumption than an open circuit ball mill High cement fineness achievable Cement fineness can be controlled with separator adjustment Disadvantage: Closedcircuit mills are more sophisticated and can have more technical problems Larger space requirement Higher investment cost (+ 25 Cement ball mill process calculation pdf PPT SlideShare2016年4月25日 In this study, certain measures are implemented in an existing raw mill in a cement factory and the specific energy consumption of the unit is calculated to be 2552 kWh/ton farineDetermination of correlation between specific energy consumption

Charge behaviour and power consumption in ball mills:
2001年8月1日 Decreasing the fill level to 30% again increases the specific power consumption, (but by a smaller percentage than that of the last increase) The peak specific power consumption remains around 105% but continues to broaden For the 25% fill level the power curve is again translated higher by a smaller increment and again the peak broadensEnergy, , Modeling of energy consumption factors for an industrial cement 2021年6月29日 This article deals with the preparation and laboratory milling of βdicalcium silicate Dicalcium silicate is the second most important calcium silicate of Portland clinker βC 2 S is usually Effects of Mill Speed and Air Classifier Speed on Performance of 2023年3月27日 Power consumption characteristics of cement industry and This is an open access article distributed under the terms of the Creative main equipment includes raw meal mill, cement mill, ball (PDF) Power consumption characteristics of cement industry and
.jpg)
OPTIMIZATION OF CEMENT GRINDING OPERATION IN BALL MILLS
Optimization of the Cement Ball Mill Operation Optimization addresses the grinding process, maintenance and product quality The objective is to achieve a more efficient operation and increase the production rate as well as improve the run factor Consistent quality and maximum output with lower specific power consumptionEvery 100 cm²/g increase in cement fineness increases the mill power consumption by 12 kWh/t for a closed circuit mill 23 kWh/t for an open circuit mill, a sheer waste if this is not required by the market! flyash pozzolana Improvements in New Existing Cement Grinding In addition, the large throughflow areas enable the mill to operate with large volumes of venting air and a low pressure drop across the mill This reduces the energy consumption of the mill ventilation fan and keeps your energy costs down Cement grinding – taking on the tough tasks Cement ball mills have to achieve the desired grinding BALL MILL FLSmidth Cement2022年5月9日 Apart from linear assessment (Fig 5), gas flow also influences energy consumption factors, as SHAP illustrated (Fig 4) Gas flow through the mill helps ensure constant lift for the internal circulating material and keeps separator performance constant to ensure a consistent product size distribution 6,76Modeling of energy consumption factors for an industrial cement
.jpg)
Ball charge optimization INFINITY FOR CEMENT EQUIPMENT
Previous Post Next Post Contents1 Ball charge optimization2 1 How to use the BP21 2 Description of the main indicators used in this BP2101 The residue on 2mm/4mm before partition wall2102 Material filling level and ball charge expansion211 Cement mill specific power 1st compartment 212 Raw mill specific power 1st compartment Ball charge 2009年8月1日 For instance, the power consumption of a two chamber cement ball mill is predicted to be 23 MW [15] Therefore, improving the energy efficiency could result in significant economic and Ball motion, axial segregation and power consumption in a full 2024年1月26日 Approximately 65–75 % of the total power consumption is used in grinding process Generally, ball mills are utilized for grinding the raw material into finished product (cement) in grinding unit of cement plants As the cement manufacturing is the continuous process, it is necessary to properly maintain the ball mill for the efficient putation of charging media for a double compartment cement ball mill Total power consumption for grinding circuit as a whole is also less by about 30% compared to closed circuit ball mill in spite of higher fan power Feed size can be as large as 75 to 100 mm Feed size can be as large as 5% of roller diameterRaw Material DryingGrinding Cement Plant Optimization
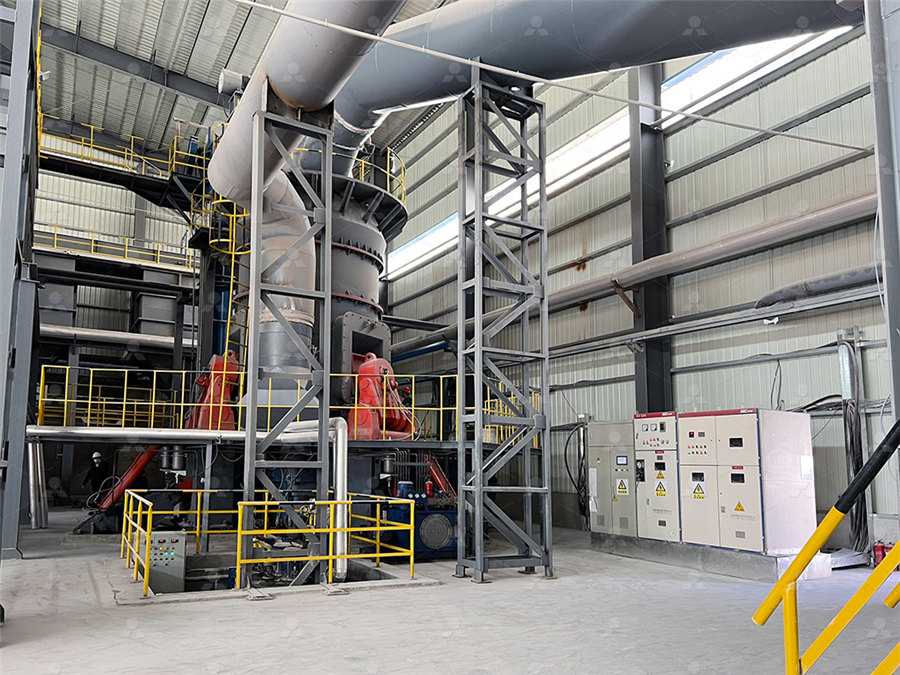
Everything you need to know about clinker/cement Grinding
For the RM it is considered to have 40% – 45% of the total mill power consumption in the first compartment For raw mills it is most common to use a ball charge with the coarse grading (up to 50% of 90 mm balls) – see table below for “coarse” grading Cement Mill2023年5月12日 In position a (Fig 1a) the length l 1 of the lower part of the chamber 1 is minimal, the grinding bodies 2 in it are located at the maximum level h 1Center of masses (CM 1) of grinding bodies (GB) in chamber 1 is located at the minimum distance a 1 from the filling bottom and at the distance b 1 from the crushing cylinder body The length l 2 of the lower part of the Power Calculation of BallTube Mill Drives in the Construction LOESCHE has supplied more than 365 mills worldwide for producing various types of cement such as OPC, PPC, composite cement, as per international standards The LOESCHE cement mill LM 352 +2 S is successfully operating Sri Balaha Chemicals Pvt Ltd, Hindupur, produces Granulated Ground Blast Furnace Slag (GGBFS) of 4,000cm²/gm at 50t/hHigher Feed Rate, Reduced Power Consumption with LM 352+2 CS Mill2021年6月10日 Under these conditions, the power consumption of the mill was found to be 422861 kW Also, optimal conditions were established in industrial grinding processesVentilation Prediction for an Industrial Cement Raw
.jpg)
Analysis of Material Flow and Consumption in
This document summarizes a research article that analyzed material flows and consumption in the cement production process The researchers established material flow routes for cement manufacturing and built mass balances for the 2020年9月14日 Power consumption per ton of clinker with a conversion ratio for consumption 155 : 1 = 174 x 155 = 27 kWh/ton; Using 4% gypsum – 1 ton clinker = 104 tons of cement; Therefore power consumption per ton of cement The essentials of electrical systems in cement plants EEP2018年9月10日 Furthermore, the power consumption of the raw mill grinding process was reduced by 67 percent by using exterior hot gas, as suggested in an energy and exergy analysis of the mill by Atmaca (PDF) Thermodynamic Analysis of Raw Mill in CementIn cement industry about 110 kWh of electrical energy is consumed to produce one ton of cement and about 26% of the total electrical power is used during farine productionThe use of electrical energy in cement production
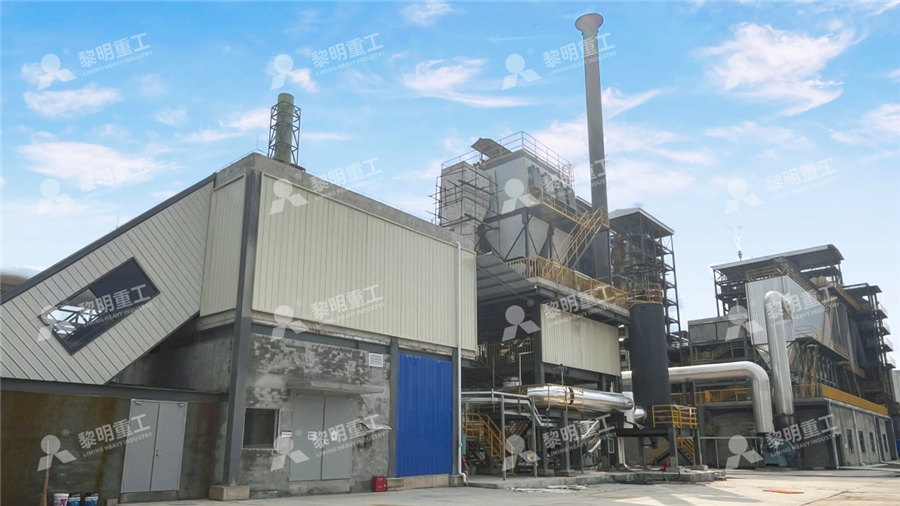
Reducing energy consumption of a raw mill in cement industry
2012年6月1日 Several grinding methods are available in cement industry depending upon the material to be ground In cement production process, about 26% of the total electrical power is used in grinding the raw materials During grinding process, the energy obtained from the rotary burner is consumed In this study, the first and second law analysis of a raw mill is performed 2016年10月12日 The simplest grinding circuit consists of a ball or rod mill in closed circuit with a classifier; the flow sheet is shown in Fig 25 and the actual layout in Fig 9Closed Circuit Grinding VS Open Circuit Grinding2019年6月13日 It is shown that the modification can reduce the total water consumption by about 20 % and the specific power consumption by about 05 kWh/ton of Raw Mill product(PDF) Water and power consumption reduction by gasTypical power consumption per tonne of cement in different unit operations is given below Cement Mill 33% Raw Mill 24% Kiln 23% Losses and crane High pressure grinding rolls can be used as premill in open circuit or as a finish mill in a close circuit modeOptimizing Electrical Energy Consumption In Cement Process
.jpg)
Heat Integration in a Cement Production IntechOpen
2017年10月20日 1 Introduction Nowadays, cement manufacturing is an energyintensive industry The energy costs of cement industry are about 40% of the product cost that indicates that this sector is one of the biggest CO 2 emitter The global anthropogenic CO 2 emission of cement industry is approximately 5% []The International Energy Agency reported in 2011 that 2006年5月9日 Download Citation Ball charge loading Impact of specific power consumption and capacity In determining the proper mill size required to meet a targeted production rate, many factors are Impact of specific power consumption and capacity2020年3月28日 PAPER OPEN ACCESS Water and power consumption reduction by gas conditioning tower system modification in cement industry To cite this article: C W Purnomo et al 2019 IOP Conf Ser: Mater Sci Eng 543 View the article online for updates and enhancements This content was downloaded from IP address 157553962 on 28/03/2020 at PAPER OPEN ACCESS Water and power consumption reduction online live calculators for grinding calculations, Ball mill, tube mill, critical speed, Degree of filling balls, Arm of gravity, mill net and gross power Optimization Online Trainingball mill calculations, grinding media filling degree, ball size, mill
.jpg)
The Decision Algorithm of Cement Mill Operation Index Based
2023年1月25日 Abstract An improved differential evolutionary cement mill operation index decision algorithm based on constraint control and selection strategy is proposed to address the problem that the operation index is usually decided by manual experience in the cement mill operation process, which causes unqualified cement specific surface area and excessive # differential pressure of mill #power consumption of mill main drive #air flow through mill #power consumption of mill fan # temperature at mill outlet # grinding bed thickness and its fluctuation The operator influences the process by adjusting the following parameters: # fan damper and other damper positionsPROCESS TRAINING for operators of Vertical RAW Mills2021年2月1日 The total electrical energy that is consumed in cement companies is about 100 kWh per 1000 kg of cement, and twothird of this amount just consumes in raw material and cement mill units [3] Today, one of the most important goals of cement industries is to reduce their power consumption by increasing their energy efficiency [4], [5]A case study on energy and exergy analyses for an industrialscale 2017年3月1日 This results to a net potential to generate 289 MWh of electrical power after factoring in the auxiliary power consumption by Waste heat recovery plant system at 15%(PDF) The generation of power from a cement kiln waste gases
.jpg)
Cement Grinding Cement Plant Optimization
Primary Ball mill controls are: Mill drive power or mill differential pressure to control mill feed rate Mill Sound level to control filling level inside mill with feed rate Mill outlet gas temperature Mill outlet material temperature Cement temperature Outlet gas flow determined from mill inlet and outlet drafts or flow meters installed2019年4月17日 Experimental investigation on power consumption of an industrial fan with different flow control methods April 2019 Environmental Progress Sustainable Energy 39(4):e13237Experimental investigation on power consumption of an Cement Separator Ball Mill Optimization Air speed in mill – Open circuit : 08 to 12 m/sec – Closed circuit : Power consumption of mill went down Improvement Tromp curve 2 Improve production rate: Reduce %bypassImprove separator feed distributionCement Separator Ball Mill Optimization