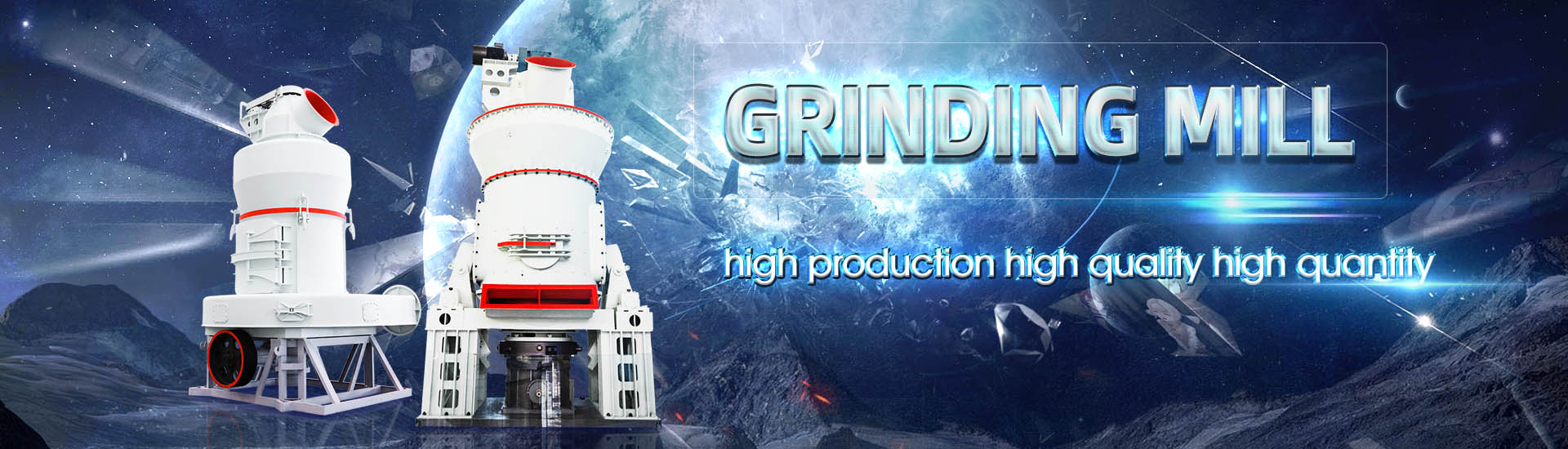
Ball mill speed
.jpg)
Ball Mill Critical Speed 911Metallurgist
2015年6月20日 A Ball Mill Critical Speed (actually ball, rod, AG or SAG) is the speed at which the centrifugal forces equal gravitational forces at the mill shell’s inside surface and no balls will fall from its position onto the shell2015年6月19日 Learn about Ball Mill Critical Speed and its effect on inner charge movements The effect of Ball Mill RPM speed going from subcritical to supercritical helps understand the BallBall Mill Critical Speed Working Principle YouTube2017年10月25日 For coarse grinding, a mill speed of 75 to 78 percent of critical is recommended, depending on the initial lifter face angleRecommended Ball Mill Speed Liner Configuration2020年7月2日 When the mills charge comprising 60% of small balls and 40% of big balls, mill speed has the greatest influence on power consumption When the mill charge is more (PDF) Effects of Ball Size Distribution and Mill Speed and Their
.jpg)
Ball Mill (Ball Mills Explained) saVRee saVRee
Most ball mills operate at approximately 75% critical speed, as this is determined to be the optimum speed The true optimum speed depends upon the drum diameter Larger drum diameters operate at lower than 75% critical speed The theoretical critical speed of a ball mill is the speed at which the centrifugal force is sufficiently large to cause a small particle to adhere to the shell interior for a full revolution of the mill The ATTRITORS AND BALL MILLS HOW THEY WORK Union Process2020年7月2日 A comprehensive investigation was conducted to delineate the effect of ball size distribution, mill speed, and their interactions on power draw, charge motion, and balls Effects of Ball Size Distribution and Mill Speed and Their 1999年8月3日 Critical rotation speed of dry ballmill was studied by experiments and by numerical simulation using Discrete Element Method (DEM) The results carried out by both Critical rotation speed for ballmilling ScienceDirect
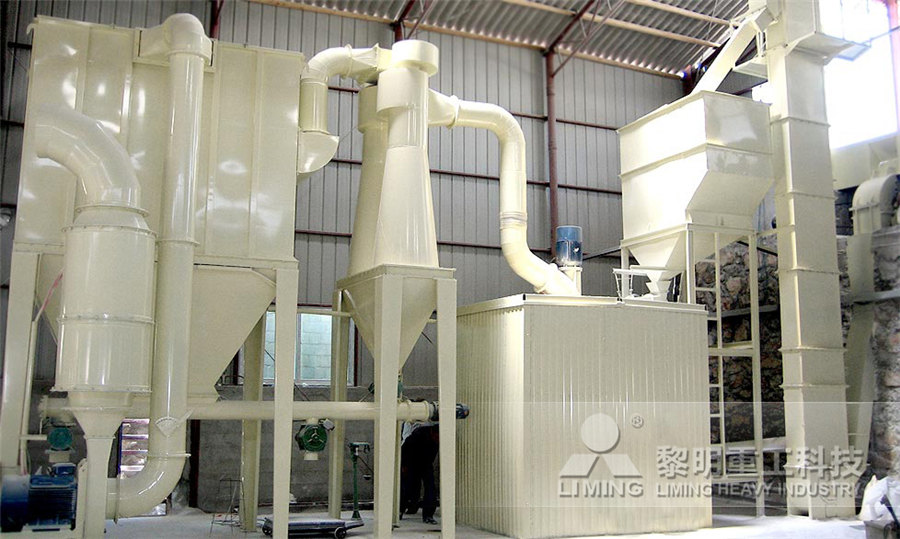
TUMBLING MILL MECHANICS
As is well known this is the usual operational speed of ball mills Fig 12/3 Outer and inner parabolic trajectories In the most inner trajectory the spiral and this trajectory have a common 2021年6月29日 Nowadays, ball mills are widely used in cement plants to grind clinker and gypsum to produce cement The research focuses on the mill speed as well as air classifier speed effect on the two Effects of Mill Speed and Air Classifier Speed on In a planetary ball mill, each jar represents a “planet” This planet is located on a circular platform, the socalled sun wheel As the vials are made of glass, the speed of the mill should be selected carefully, we recommend a maximum of Planetary Ball Mills RETSCH fine grinding of materials2011年8月1日 In 1999, ElEskandarany et al [21] investigated the effect of milling speed on crystalline solidstate cyclic phase transformations on Al–Zr binary system upon ball milling their elemental powders with a nominal composition of Al 50 Z 50, using planetary ball mill (Fritsch P5) operated at different milling speed of 90, 180, 270, and 360 rpmMill Speed an overview ScienceDirect Topics
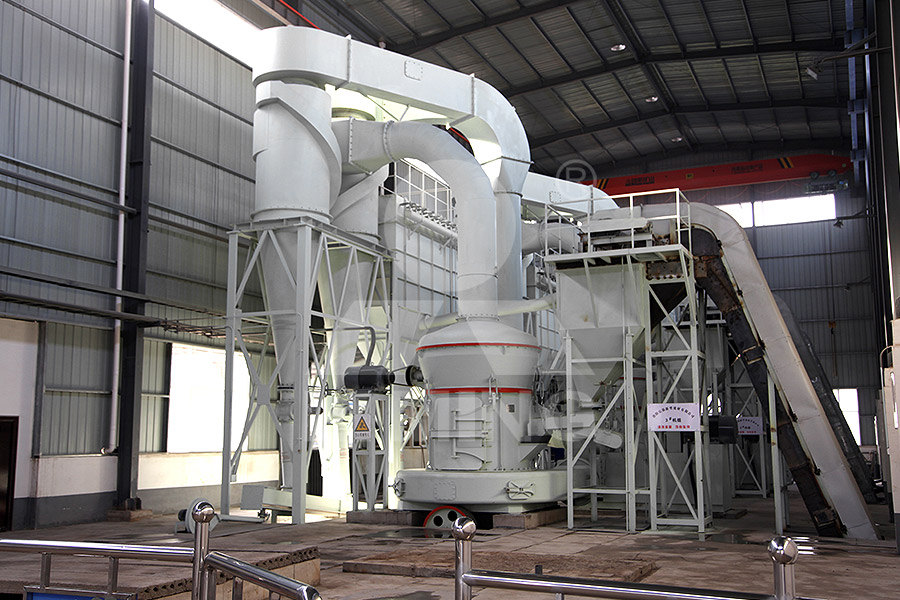
Ball Mill Design/Power Calculation 911Metallurgist
2015年6月19日 The basic parameters used in ball mill design (power calculations), rod mill or any tumbling mill sizing are; material to be ground, characteristics, Bond Work Index, bulk density, specific density, desired mill tonnage capacity DTPH, operating % solids or pulp density, feed size as F80 and maximum ‘chunk size’, product size as P80 and maximum and finally the type of 1983年1月1日 Afton claims that the variable mill speed has been useful for preventing liner wear while processing soft ore (Pazour, 1978) Sydvaranger processes iron ore through a 21 by 33foot variable speed ball mill The speed range of this mill is from 62 to 82 percent of critical, with normal operating speed at 78 percentMill Speed as a Manipulated Variable for Ball Mill Grinding ControlExplain the role of ball mill in mineral industry and why it is extensively used Describe different types (F↓80) ↑029 (W↓i) ↑04 / (νD) ↑025Where ν = the rotational speed of the mill Ball Bulk Density Low density media can be used for soft and brittle materials Hard materials required high AMIT 135: Lesson 7 Ball Mills Circuits – Mining Mill Operator 2017年2月13日 Center peripheral discharge Rod Mill for minimal slimes in final product CERAMIC LINED BALL MILL Ball Mills can be supplied with either ceramic or rubber linings for wet or dry grinding, for continuous or batch type operation, in sizes from 15″ x 21″ to 8′ x 12′Ball Mills 911Metallurgist
.jpg)
Planetary Ball Mill PM 100 RETSCH highest fineness
The Planetary Ball Mill PM 100 is a powerful benchtop model with a single grinding station and an easytouse counterweight which compensates masses up to 8 kg It allows for grinding up to 220 ml sample material per batch even at maximum speed of 800 rpm, wet grinding, The ball mill is a tumbling mill that uses steel balls as the grinding media The length of the cylindrical shell is usually 1–15 times the shell diameter (Figure 811)The feed can be dry, with less than 3% moisture to minimize ball coating, or slurry containing 20–40% water by weightBall Mill an overview ScienceDirect Topics2024年7月31日 The production of cement, an essential material in civil engineering, requires a substantial energy input, with a significant portion of this energy consumed during the grinding stage This study addresses the gap in the literature concerning the collective impact of key parameters, including ball size, feed rate, and mill speed, on grinding efficiency Nine spherical Effect of Grinding Conditions on Clinker Grinding Efficiency: Ball 2017年6月26日 Ball Nose Milling Without a Tilt Angle Ball nose end mills are ideal for machining 3dimensional contour shapes typically found in the mold and die industry, the manufacturing of turbine blades, and fulfilling general part Ball Nose Milling Strategy Guide In The Loupe
.jpg)
Ball Mill SpringerLink
2023年4月30日 When the ball mill rotates at a certain speed, the grinding medium such as steel ball (rod) or gravel in the cylinder rises to a certain height with the rotation of the cylinder under the action of its own gravity, the friction between the cylinder liner and the centrifugal force generated by the rotation of the ball mill2012年6月1日 u 2 − fresh ore feed rate, u 3 − mill critical speed fraction, efficiency of the ball mill and the economic assessment of the process control R e f e r e n c e s 1Grinding in Ball Mills: Modeling and Process ControlThe critical speed of a ball mill is the speed at which the centrifugal force is equal to the gravitational force acting on the balls At this critical speed, the balls are held against the inner wall of the mill and do not fall to the bottom where they would be more effective at Ball Mill Principle, Application, Uses, Critical Speed, Diagram The E max is an entirely new type of ball mill for high energy milling The unique combination of high friction and impact results in extremely fine particles within the shortest amount of time faster and finer grinding than any other ball mill; speed of 2000 min1 Emax High Energy Ball Mill Retsch
.jpg)
Ball Mill; Principle, Working, and Construction » Pharmaguddu
2022年10月17日 Ball mill Speed Impact on Size Reduction Low speed: At low speed, the mass of balls will slide or roll up one over another and will not produce a significant amount of size reduction High Speed: At highspeed balls are thrown to the cylinder wall due to centrifugal force and no grinding will occur2024年1月1日 When the ball mill rotates at a certain speed, the grinding medium such as steel ball (rod) or gravel in the cylinder rises to a certain height with the rotation of the cylinder under the action of its own gravity, the friction between the cylinder liner and the centrifugal force generated by the rotation of the ball millBall Mill SpringerLinkMax speed 400 rpm, large sun wheel ; Up to 10 mm feed size and 01 µm final fineness ; 4 grinding stations for jars from 12 ml up to 500 ml, jars of 12 – 80 ml can be stacked With a special adapter, cocrystal screening can be carried out in a planetary ball mill, Planetary Ball Mill PM 400 RETSCH powerful and quick grindingThe mill critical speed will be calculated based on the diameter (above) less twice this shell liner width Mill Actual RPM: Enter the measured mill rotation in revolutions per minute Result #1: This mill would need to spin at RPM to be at 100% critical speedMill Critical Speed Determination
.jpg)
Effect of lifters and mill speed on particle behaviour, torque, and
2017年5月1日 When a ball mill works at a relatively high speed, its net power consumption can be determined, as indicated in Table 1, where m is the mass of the charge, φ is the fill level, ψ is the rotation rate (constant fraction of the critical speed), ρ is the density of the granular pile, V is the internal volume of the ball mill, D is the internal diameter of the ball mill, and d j is the Ball Mill Grinding Process Handbook Free download as PDF File (pdf), Text File (txt) or read online for free This document provides guidance on ball mill grinding processes It covers topics such as ball mill design including length to Ball Mill Grinding Process Handbook PDF Mill 2021年2月19日 The ball mill process parameters discussed in this study are ball to powder weight ratio, ball mill working capacity and ball mill speed As Taguchi array, also known as orthogonal array design, adds a new dimension to conventional experimental design, therefore, Orthogonal array (L9) was carefully chosen for experimental design to understand the effects Comparative Study on Improving the Ball Mill Process Parameters 2024年6月27日 A new planetary ball mill device with adjustable speed ratio for enhanced mechanochemical processes† Frank Yntema ab, Cameron Webster a and Emmanouil Broumidis * ab a Pluto Mills Ltd, Michelin Scotland Innovation Parc, Baldovie Rd, Dundee, DD4 8UQ, UKA new planetary ball mill device with adjustable speed ratio for
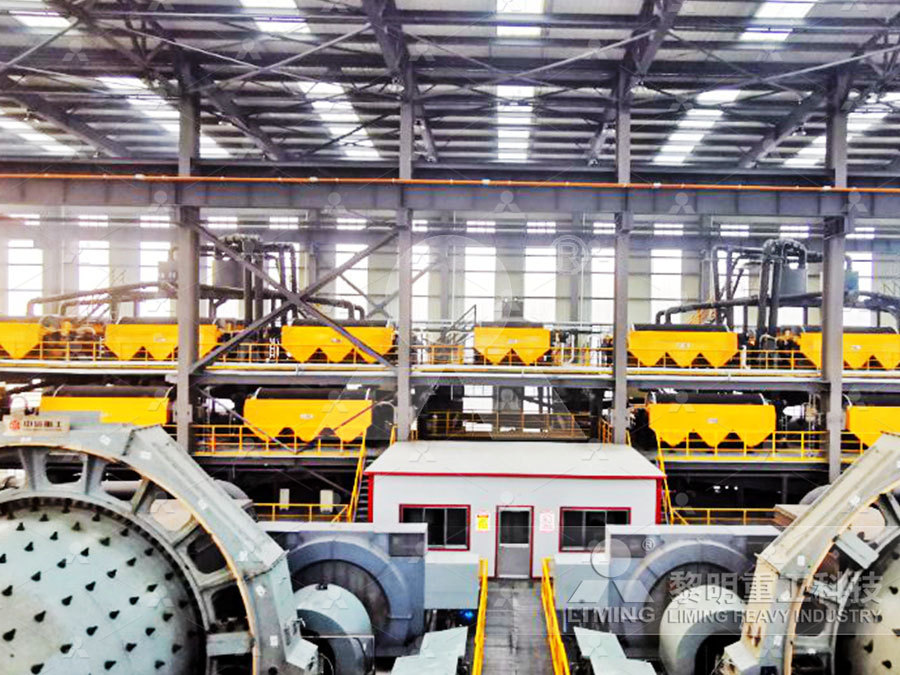
FCMO: Ball Mill Operating Speed MSubbu Academy
2024年8月8日 In a ball mill of diameter 2000 mm, 100 mm dia steel balls are being used for grinding Presently, for the material being ground, the mill is run at 15 rpm At what speed will the mill have to be run if the 100 mm balls are replaced by 50 mm balls, all the other conditions remaining the same? Calculations: The critical speed of ball mill is Ball milling is a mechanical process that involves the rotation of a drum containing grinding media, typically steel balls, at a high speed The materials to be milled are loaded into the drum, and as the drum rotates, the grinding media collide with the materials, causing them to Exploring ball milling theory: A comprehensive guide2022年11月30日 A ball mill also known as pebble mill or tumbling mill is a milling machine that consists of a hallow cylinder containing balls; mounted on a metallic frame such that it can be rotated along its longitudinal axis The balls which could be of different diameter occupy 30 – 50 % of the mill volume and its size depends on the feed and mill sizeBall Mill: Operating principles, components, Uses, Advantages andThe Speeds and Feeds Calculator may be employed for calculations of estimated speeds and feeds (RPM and IPM) values on the basis of the parameters you have currently set based on your tools and stock materialSpeeds and Feeds Calculator Good Calculators
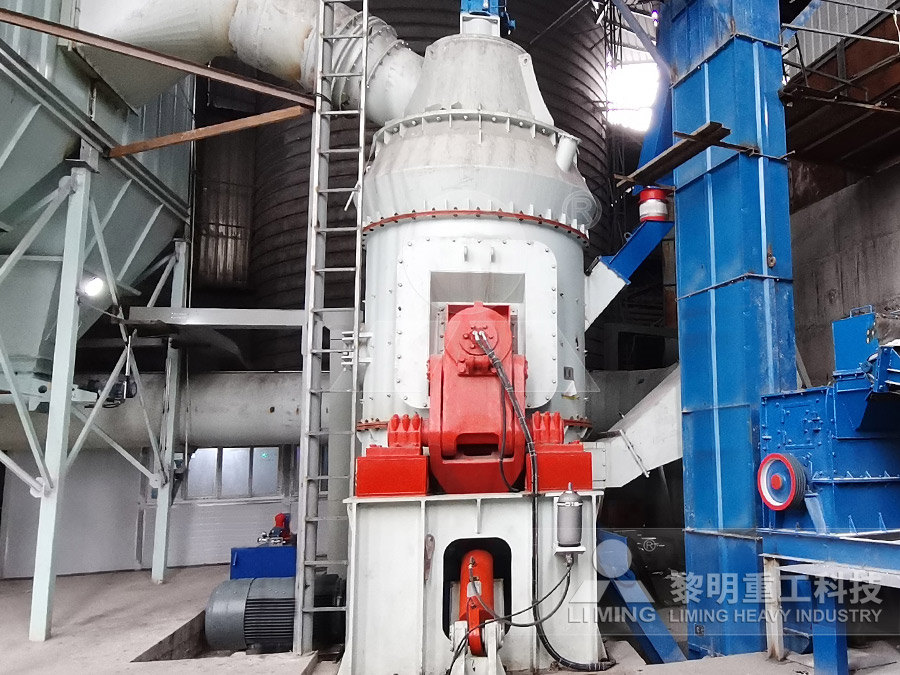
A new planetary ball mill device with adjustable speed ratio for
2024年6月27日 A new planetary ball mill device with adjustable speed ratio for enhanced mechanochemical processes† Frank Yntema ab, Cameron Webster a and Emmanouil Broumidis * ab a Pluto Mills Ltd, Michelin Scotland Innovation Parc, Baldovie Rd, Dundee, DD4 8UQ, UK2024年10月12日 Ball Nose End Mill Feed and Speed Calculator Tool Diameter (in inches): Cutting Speed (SFM Surface Feet per Minute): Number of Flutes: Chip Load per Tooth (in inches): Calculate Ball Nose End Mill Feeds and Speeds: The Ultimate Guide Ball nose end mills are versatile cutting tools used extensively in 3D machining, profiling, andBall Nose End Mill Feed and Speed Calculator calculattorTalk with the Experts at Paul O Abbe® about your process requirements and Ball Mill Loading, Wet Milling, Size Reduction and Mill Speed Critical Speed needs About Section 179 6303503012Mill Speed Critical Speed Paul O AbbeEnd Mill Feeds and Speeds The most important aspect of milling with end mills is to run the tool at the proper RPM (revolutions per minute or spindle speed) and IPM (inches per minute or feed rate) We have broken these recommendations down into material categories so you can make better decisions with how to productively run your end millsMilling Speeds And Feeds: Charts Data 6gTools
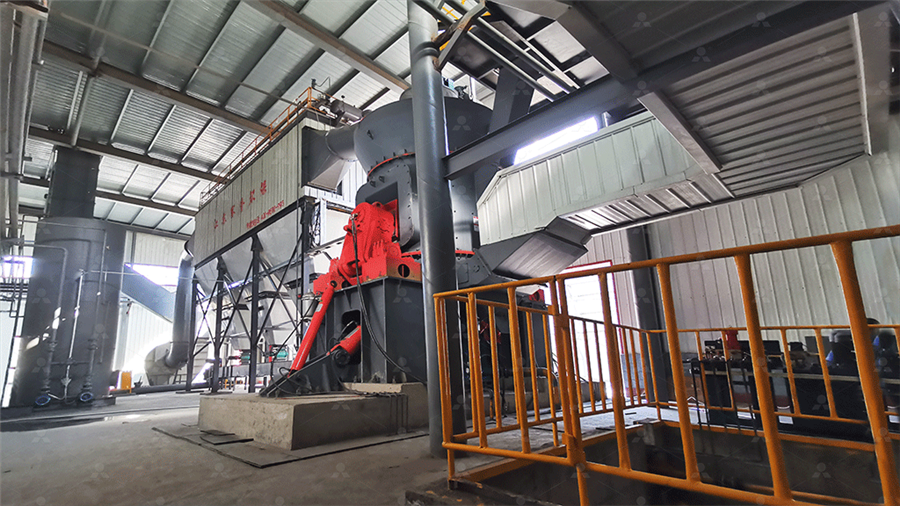
Effect of mill speed and slurry filling on the charge dynamics by
2019年8月1日 As the mill speed increases from φ = 60% to φ = 80%, the ball mill provides more energy to grinding ball, so the average rotational kinetic energy increased As the slurry filling increases from U = 0 to U = 15, the slurry reduced the friction between the grinding ballsBall Mills Steel Ball Mill Lined Ball Mill Since the late 1800s, the ball mill has revolutionized industrial grinding processes, establishing itself as the gold standard in particle size reduction The basic construction of a ball mill is a Orbis Machinery Ball Mills Ball Mill Drive2024年4月30日 In a ball mill of diameter 2000 mm, 100 mm dia steel balls are being used for grinding Presently, for the material being ground, the mill is run at 15 rpm At what speed will the mill have to be run if the 100 mm balls are replaced by 50 mm balls, all the other conditions remaining the same? Calculations: The critical speed of ball mill is Ball Mill Operating Speed MSubbu Academy950 rpm Blaine is the important characteristic of ball mill which is influenced by the mill speed and separator speed Ball mill is grinding equipment which is used to reduce the size of clinker into cement It uses grinding media in the form of balls Clinker coming from the silo is sent into hopper and mill for impact action Clinker is Effects of Mill Speed and Air Classifier Speed on Performance of
.jpg)
Critical Speed of a Ball Mill Calculator – Derivation and Working
2024年8月29日 The critical speed of a ball mill is the rotational speed at which the centrifugal forces acting on the ball are equal to the gravitational force At this speed the outermost balls loose the contact with the wall of the mill and ready to fall The critical speed can be calculated using the formula: \[Nc = \frac{1} 2019年8月14日 D—the inner diameter of the ball mill, M; N0 critical speed of revolutions, r /min When the nonsmooth ball mill liner is used, the grinding ball filling ratio is 4050%, and the grinding concentration is relatively large, the calculation result The Ultimate Guide to Ball Mills MiningpediaRotation speed of the cylinder Working of Ball Mill: Several types of ball mills exist They differ to an extent in their operating principle They also differ in their maximum capacity of the milling shell, ranging from 0010 liters for planetary ball mill, mixer mill, or vibration ball mill to several 100 liters for horizontal rolling ball Ball Mill Principle, Construction, Working, and More Soln Pharma2015年4月24日 10 • Weight of the balls: With a heavy discharge of balls,we get a fine productWe can increase the weight of the charge by increasing the number of balls or by using a ball material of high density • Speed rotation of Ball mill: low speeds,the balls simply roll over one another and little grinding is obtained while at very high speeds the balls are carried along Ball mill PPT Free Download SlideShare
.jpg)
Ball Nose vs Flat End Mill Ball Nose End Mill Speeds and Feeds
2023年2月28日 For example, if you are machining aluminum with a 1/4″ ball nose end mill and a cutting speed of 250 SFM, the spindle speed would be 2,000 RPM – Determine the feed rate (IPM) based on the depth of cut and the width of the tool For example,