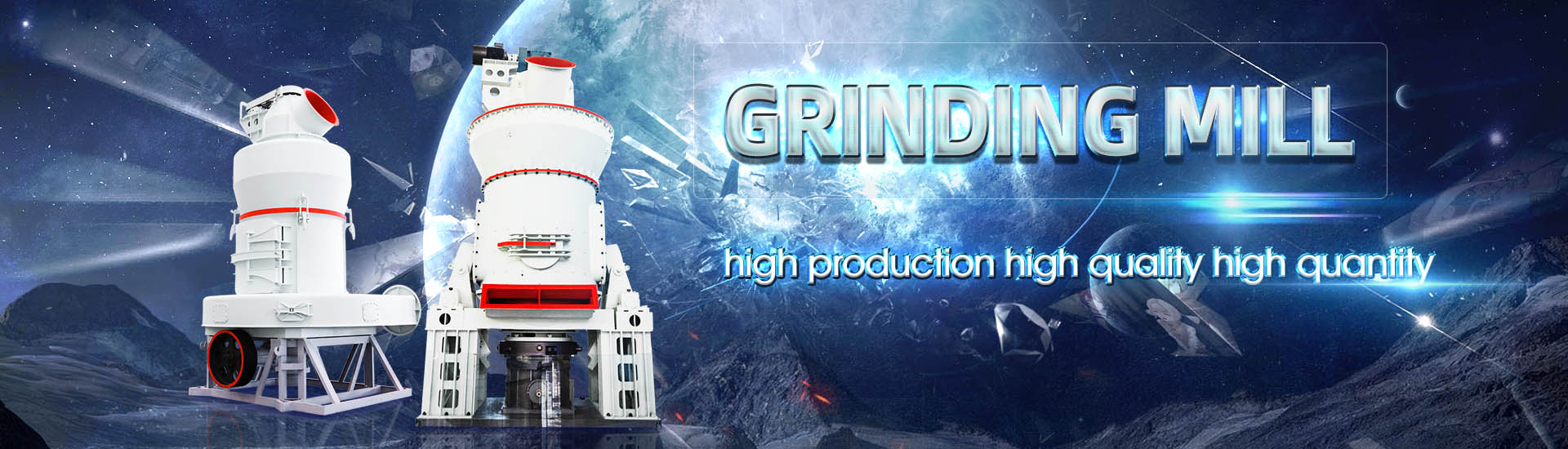
The internal structure of the hp803 coal mill
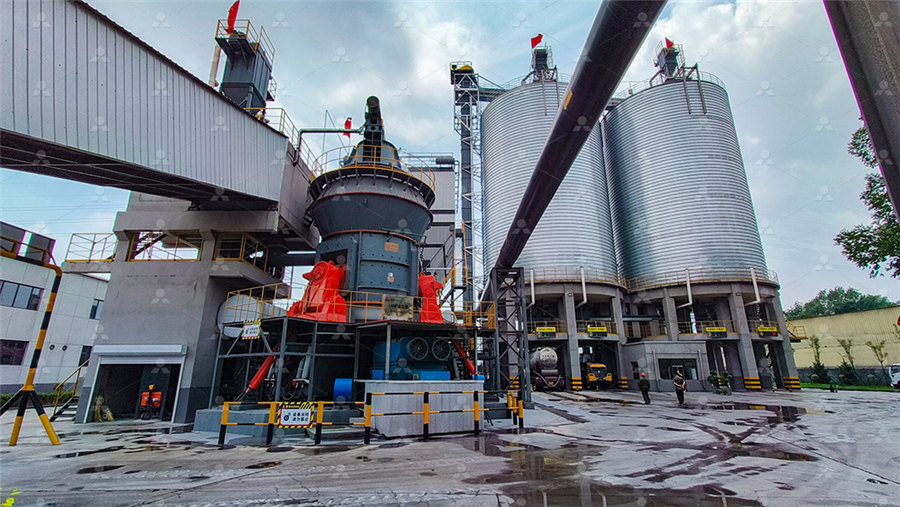
en/168/internal structure of hp803 coal millmd at main
Contribute to lbsid/en development by creating an account on GitHubThe structure of HP bowl type coal mill is bowl shaped grinding plate, three grinding rollers and spring variable loadingHP Bowl type millspower plant equipment2009年9月20日 In this model, the internal structure of a pulverizer is divided into five zones The grinding, pneumatic transport, and classification processes are considered in corresponding zones CoalModeling and Parameter Identification of Coal MillCoal Bowl Mill, for guaranteed performance at a 500 MW capacity NTPC thermal power plant The study was conducted to assess the effective performance of the pulverizers of this 500 A Study on 500 MW Coal Fired Boiler Unit’s Bowl Mill Performance
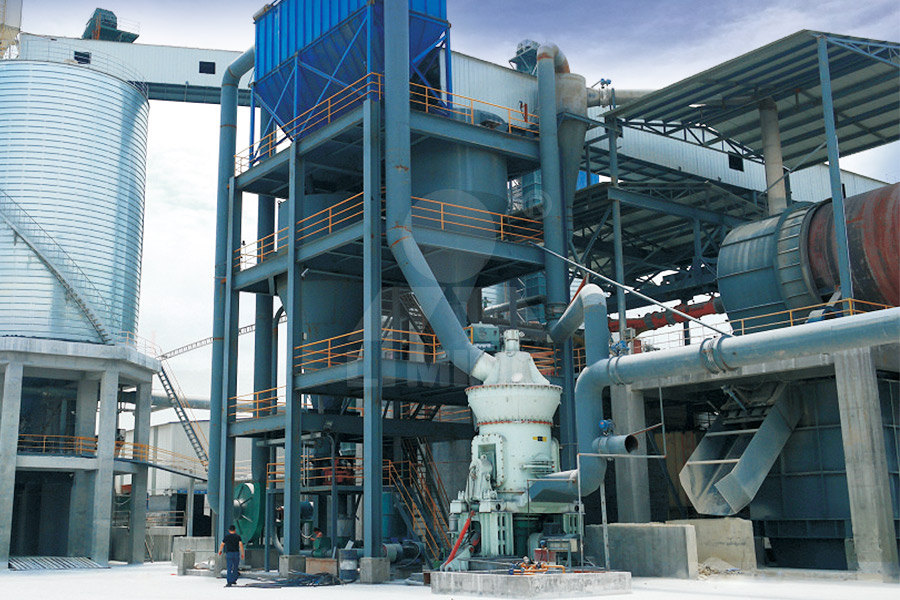
SHPHGLXP VSHHGFRDOPLOO ResearchGate
Taking hp1103 medium speed roller disc coal mill as the carrier, this paper mainly describes the common faults in the normal operation of this type of coal mill, and analyzes and judges2013年6月9日 GRINDING PROCESS OF MILLS Coal are fed from Raw coal feeder ( situated just above the mill on concrete floor) One end of the Raw coal feeder is attached with Coal MILLS IN A THERMAL POWER STATION PART I2013年3月1日 In this paper a three state coal mill model based on heat and mass balances as well as a single step coarse to fine particle grinding relationship is presented with the purpose Nonlinear coal mill modeling and its application to model HP Series Medium Speed Bowl Mill is used to grind, dry and separate raw coal into qualified fineness for combustion in steam boilers It consists of a grinding bowl, grinding rollers, spring loading device and other components The coal HP Series Medium Speed Bowl Mill
.jpg)
PRODUCT STANDARD Product Bharat Heavy Electricals Limited
(Raymond Mill) coal mills for power plant applications with typical high ash Indian coal as given in Annexure I 211 Bidder should have supplied minimum of 13 sets of Grinding rolls Bull ring 2014年10月1日 Milanović, in his PhD dissertation, [4] investigates turbulent multiphase flow in the straight channels of noncircular section Živković et al in their paper [5] and S Atas et al in [6 Numerical and experimental analysis of pulverized coal mill 2016年1月18日 Next, the paper estimates the coal outlet mass flow of the coal mill by using extended Kalman filter (EKF), and the result is compared with the coal flow instruction Finally, we take the estimation of coal outlet mass flow as the new controlled variable and use inferential predictive control method to solve the coal mill control problemsThe Inferential predictive control method of coal mill IEEE Download scientific diagram Effect of mill outlet temperature on the coal volatile matter from publication: An investigation of performance characteristics and energetic efficiency of vertical Effect of mill outlet temperature on the coal volatile matter
.jpg)
HP Bowl type millspower plant equipment
Due to the improvement of the roller structure of HP coal mill, the roller replacement can be carried the internal circulation load of the dynamic separator is smaller under the same output condition The maximum internal circulation load of the coal mill can be achieved by HP803/Dyn: 393: 59: 400: HP823/Dyn: 2200: 1300: 418: 627: 38 2009年1月1日 This book details advances in the production of steam and the utilization of all types of fuels Section 1 covers Steam Fundamentals including thermodynamics, fluid mechanics, heat transfer CFD Modeling of MPS Coal Mill for Improved Performance and SafetyMill performance not only influences its own internal operation and but also affects the combustion performance of the furnace Indicators of combustion performance, NOx, CO, unburnt carbon CFD Modeling of MPS Coal Mill for Improved Performance and The article presents an identification method of the model of the ballandrace coal mill motor power signal with the use of machine learning techniques The stages of preparing training data for model parameters identification purposes are described, as well as these aimed atThe identification method of the coal mill motor power model
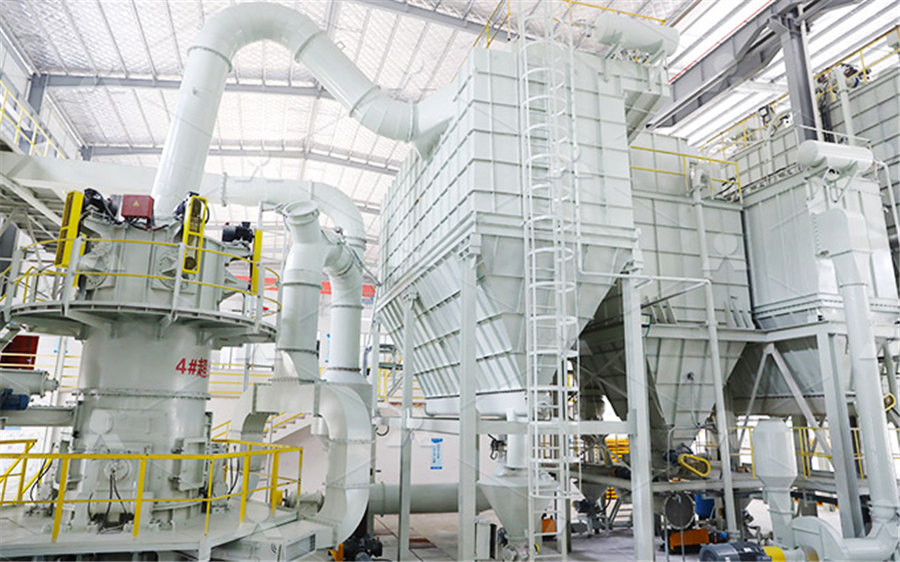
Effects of steam treatment on the internal moisture and
2023年5月1日 Ultimately, the variation in coal internal moisture was also related to the coal internal structure, coal rank, duration and temperature of steam As demonstrated in Fig 3 (a2)∼(a4), (b2)∼(b4), steam treatment at 200–400 °C (superheated steam) had an excellent drying effect on coal and could remove almost all the water in the coal (including irreducible 2023年5月23日 Goossens et al 1 combined the values of 60 sensors to construct a global damage index for the structure and implemented the security alert by setting the damage monitoring threshold Lei et al 2 reviewed the four processes of remaining useful life (RUL) prediction for mechanical devices: data acquisition, HI construction, health stage division, and Health indicator construction and application of coal mill based 2017年6月1日 However, the coal mill must be sealed to prevent coal powder leakage because the internal pressure of the coal mill is higher than the atmospheric pressure The structure of a typical positivepressure, directfired pulverizing system is shown in Fig 1 Download: Download highres image (229KB)Optimization control of a pulverizing system on the basis of the 2012年11月17日 20 131Fineness Fineness is an indicator of the quality of the pulverizer action Specifically, fineness is a measurement of the percentage of a coal sample that passes through a set of test sieves usually designated at 50, Coal mill pulverizer in thermal power plants PPT
.jpg)
The Physical Structure of Coal ScienceDirect
1982年1月1日 Changes in the internal structure of coal during carbonization have been studied extensively though less so than changes with coal rank The several studies, collectively, have used essentially all the techniques mentioned above, and, in a qualitative sense, seem to be in general agreement2012年5月1日 Coal fired power plants are heavily used due to large and long lasting coal resources compared with oil or natural gas An important bottleneck in the operation of this particular kind of plants, however, is the coal pulverization process, which gives rise to slow takeup rates and frequent plant shutdowns (Rees Fan, 2003)In typical coal fired power plants, Derivation and validation of a coal mill model for control2020年6月15日 Industrial hammer mills are employed in particle reduction applications for processing material Though machine designs vary, the basic hammer mill working principle remains the same—uniform size reduction of aggregate raw material is achieved by repeated blows with hammers mounted to a rotating shaftUnderstanding the Working Principle of Hammer Mills Prater2019年10月19日 Ball mills are extensively used in the size reduction process of different ores and minerals The fill level inside a ball mill is a crucial parameter which needs to be monitored regularly for optimal operation of the ball mill In this paper, a vibration monitoringbased method is proposed and tested for estimating the fill level inside a laboratoryscale ball mill A vibration Monitoring the fill level of a ball mill using vibration sensing and
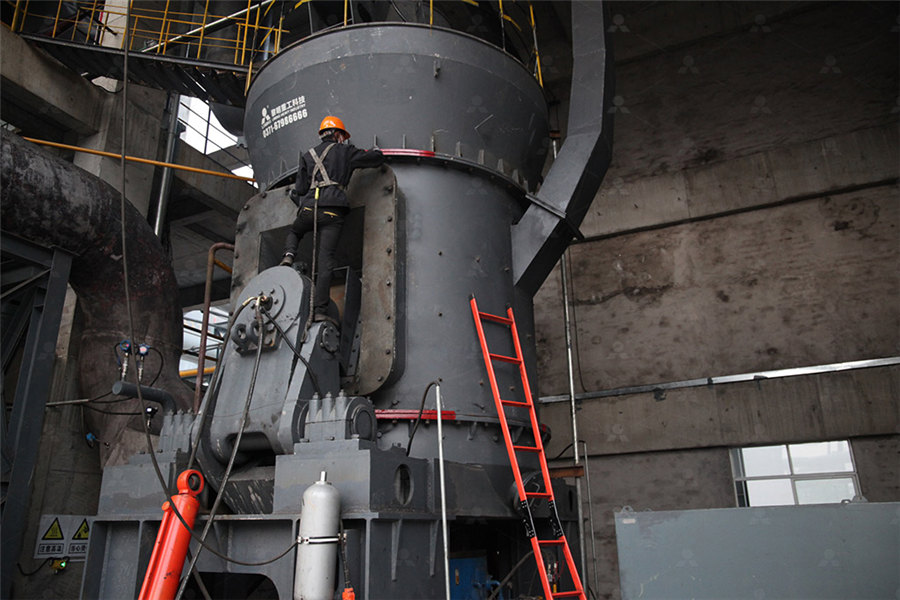
Schematic structure of the MPS mediumspeed mill
Download scientific diagram Schematic structure of the MPS mediumspeed mill from publication: Application of ModelBased Deep Learning Algorithm in Fault Diagnosis of Coal Mills The coal 2021年8月1日 Studies have shown that the higher the moisture content in coal, the stronger the wettability of the coal dust [36] The ash content of coal refers to the residue left after the complete Coal mill model considering heat transfer effect on mass Core At the planet’s center lies a dense metallic core Scientists know that the core is metal for a few reasons The density of Earth’s surface layers is much less than the overall density of the planet, as calculated from the planet’s rotation53: The Composition and Structure of EarthDownload scientific diagram Technical specifications of vertical roller coal mill from publication: An investigation of performance characteristics and energetic efficiency of vertical roller Technical specifications of vertical roller coal mill

Coal mill model considering heat transfer effect on mass
2021年8月1日 Yukio et al [7] proposed a model consisting of blending, grinding and classifying processes for pulverizer control Agarawal et al [8] differentiated coal powder into ten size groups, divided the bowl mill into four zones, and developed a unified model Palizban et al [9] derived nonlinear differential mass equations of raw coal, recirculation coal and suspension coal in 2016年9月1日 Furthermore, VRM separator speed (rpm) is one of the key operational parameters that determines product particle size Increasing the classi er rotor speed from 60 to 80 rpm decreases the particle Operational parameters affecting the vertical roller mill Finally, the temperature equation is based on heat balance equation of the coal millThe significant heat contribution comes from the primary air flow , moisture of the incoming coal particles, coal flow into the mill (1) and from grinding the moisture coal particles and temperature depends on the The mass of pulverised coal on the table grinding rate and the amount of coal (PDF) Modeling and Control of Coal Mill Academia2022年12月1日 Schematic drawing of the MWk 12 mill (FPM SA Mikołów, Poland) Download : Download highres image (138KB) Download : Download fullsize image; Fig 2 Plates of highmanganese cast steel used for mill lining and beaters of a coal grinding mill: a) inner (IP) and middle plates (MP), b) outer plates (OP) Download : Download highres image The wear mechanism of mill beaters for coal grinding madeup
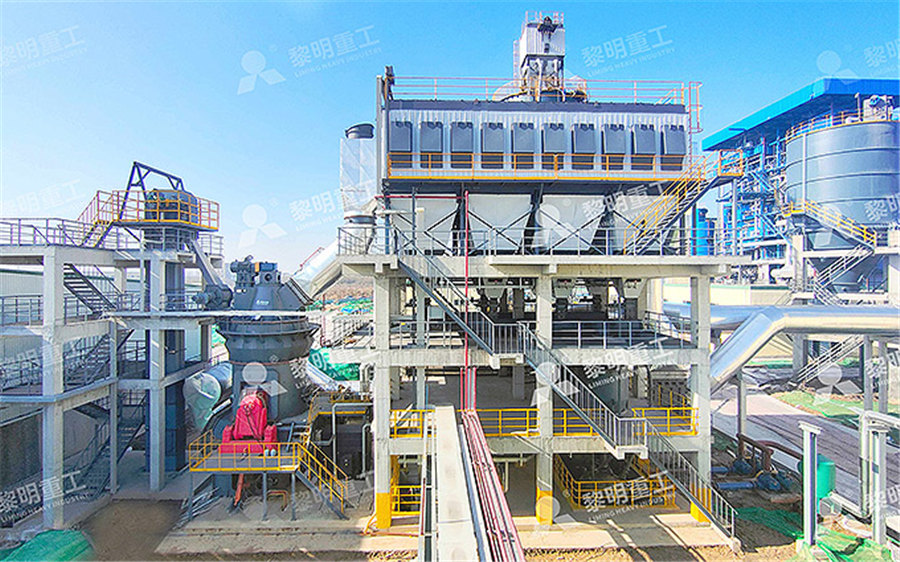
Classification performance of model coal mill classifiers with
2019年12月1日 The classification performance of model coal mill classifiers with different bottom incoming flow inlets was experimentally and numerically studied2017年6月1日 However, the coal mill must be sealed to prevent coal powder leakage because the internal pressure of the coal mill is higher than the atmospheric pressure The structure of a typical positivepressure, directfired pulverizing system is shown in Fig 1Optimization control of a pulverizing system on the basis of the Vertical coal grinding mill integrates crushing, drying, grinding, powder selection and conveying; It has simple system and compact structure Vertical coal mill covers an floor area about 50% of the coal ball mill with the same specification; Coal vertical mills can work in openair environments, greatly reducing the cost of investment The design of the vertical coal mill system is simple Vertical Coal Mill for Coal Grinding in Cement Plant Power Plant2023年5月23日 Choosing (an) adequate model structure(s) for a given purpose, catchment, An extended Kalman filter was designed to estimate and verify the internal states of the coal millHealth indicator construction and application of coal mill based
.jpg)
Modelling and control of pulverizing system considering coal
2015年2月1日 Wei and Wang established a simple model for the mill Genetic algorithm was used to optimize the parameters of the model, and the multistage modelling method was proposed to match the conditions during start up and shut down [1]Shin and Li presented a model with two particle sizes and pressure drop dynamics [2]However, the effect of coal A simple energy balance model of the coal mill is derived in (Odgaard and Mataji 2006), this model is based on a more detailed model found in (Rees and Fan 2003)In this model the coal mill is seen as one body with the mass m mThe following variables are defined: T(t) is the temperature in the coal dust flow in the mill, ṁ PA (t) is the primary air mass flow, T PA (t) is Coal Mill an overview ScienceDirect Topics2024年11月1日 However, all of these investigations have revealed an enormous vortex inside the VRMs that could not be eliminated The internal flow field of VRMs is determined by their structure, and the large vortices cannot be completely eliminated Moreover, the vortex area can be reduced by improving the internal structure of the millNumerical Study of Flow Field and Particle Motion Characteristics 2020年4月1日 Coal mills are important equipment of the coal pulverizing system The structure of the MPS mediumspeed coal mill is shown in Figure 1 [1]As can be seen from Figure 1, the raw coal entering the Research on Fault Diagnosis of Coal Mill System Based on the
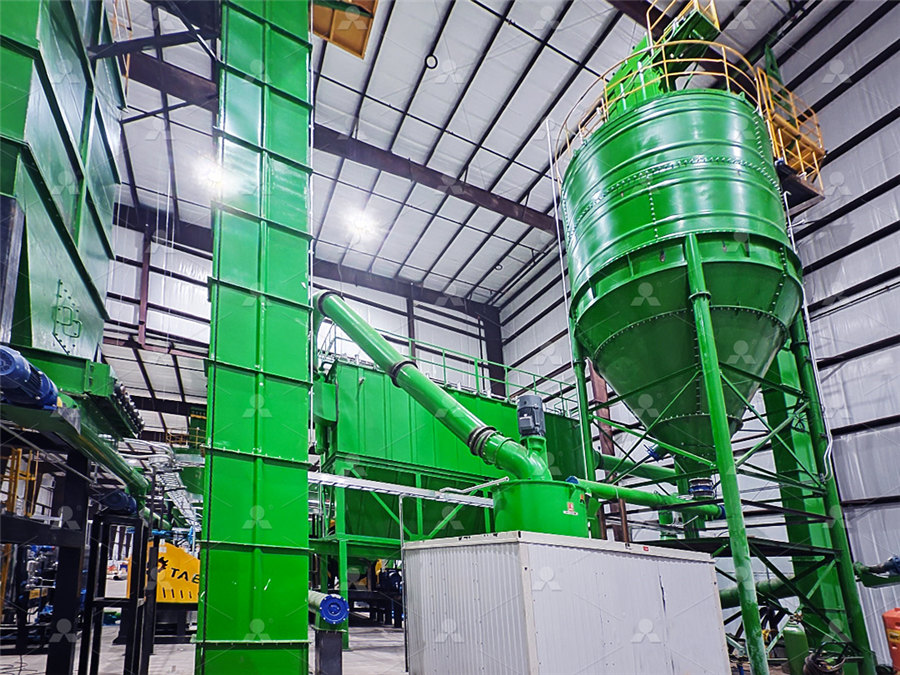
A review of coal permeability models including the internal
2024年6月20日 Coal bed methane (CBM), the highquality and efficient fuel, has caught the interest of many nations as they strive for environmentally friendly development Therefore, the efficient exploitation and utilization of CBM has become one of the international focal research problems A significant factor affecting the mining of CBM is coal permeability To better 2019年6月1日 Coal is the world’s largest and most widely distributed conventional energy However, it is mainly categorized as lowranked lignite and subbituminous coals [1], which have low commercial and heating values [2]Moreover, the traditional way of coal combustion caused the release of toxic and harmful substances, which brought great negative impact on human Effect of chemical structure of lignite and highvolatile bituminous 2020年8月12日 In a power plant, the coal mill is the critical equipment, whose effectiveness impacts the overall power plant efficiency Uniform coal feeding mass flow rate and required particle size and temperature at the outlet channel throughout with better classifier performance are crucial indicators that characterize the coal mill performanceAn investigation of performance characteristics and energetic also find an application in grinding a wide variety of coal types in cement and power plants Gebr Pfeiffer SE (GPSE) describes its vertical roller mills for coal grinding and provides a case study of an MPS225BK installed at CBR’s Lixhe cement works in Belgium COAL GRINDING Figure 1: MPS coal grinding mill with SLS highefficiency classifierCOAL GRINDING IMPS: more than meets the eye Gebr Pfeiffer
.jpg)
On the structure and mechanism of the gastric mill in
A brief description of the foregut inPenœus indicus and a comparative account of the same in the remaining types of Penæidea and Stenopidea examined by me has been givenThe structure of the gastric mill in the Decapoda conforms to a typical plan common to all species, the variations being due to the coalescence, reduction or disappearance of one or more ossicles; in those • Smoldering coal inside an idle mill can evolve into a big problem when the mill is started, agitating these accumulation combined with a high air to fuel ratio environment • PRB is one of the most difficult coals with respect to mill fires and explosions • Mill internal temperatures are generally high enough somewhere to ignite any type ofMill Inerting and Pulverizer/Mill Explosion Mitigation2020年1月1日 An extended Kalman filter was designed to estimate and verify the internal states of the coal mill Based on the dynamic mathematical model of coal mill, (PDF) Modelling and multiloop selective control of industrial coal NomenclatureBowl Mills 583 XRS / 803 XRP Bowl mills 58,80 stands for bowl diameter in inches If the number is even then its shallow bowl mill If the number is odd then its deep bowl mill 3 number of rollers three nos X frequency of power supply 50 cyclesIn USA ’x’ means 60 cycles R Raymond, name of the inventorPulverizer Plant OM Aspects
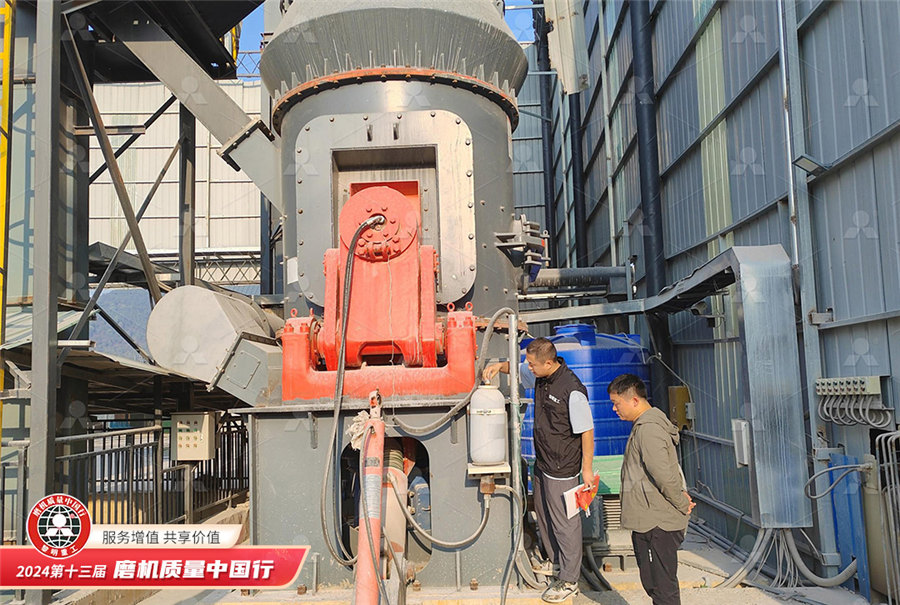
CFD modeling of MPS coal mill with moisture evaporation
2010年5月1日 Mill performance not only influences its own internal operation and but also affects the combustion performance of the furnace Indicators of combustion performance, NO x, CO, unburned carbon, slagging, fouling, flame stability and boiler capacity are directly altered by mill outputBurners and other allied combustion equipments are designed with the assumption