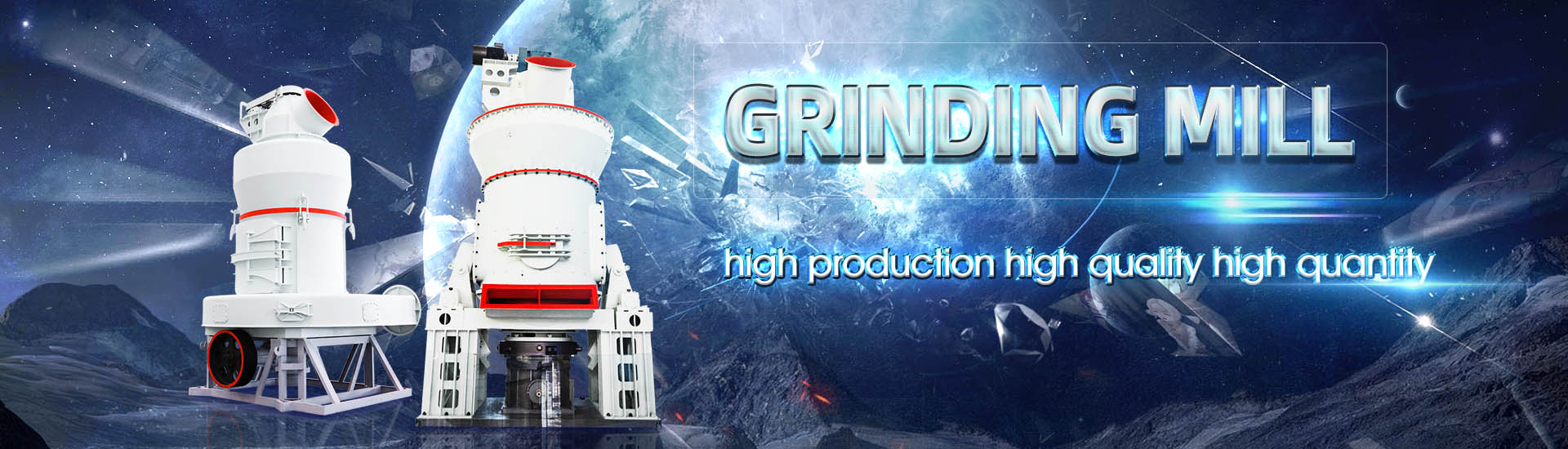
How to save energy in mediumspeed mill
.jpg)
3 ways to improve feed mill energy efficiency
2023年2月23日 Below are three actions feed millers can take to improve energy efficiency and lower carbon emissions Replacing outdated motors on feed processing equipment with highefficiency motors and variable speed drives 2020年1月7日 The MultiImpact Hammer Mill improves energy efficiency while giving you more control over the size and shape of your particles Reducing How to Improve Energy Efficiency in the Milling 2020年2月1日 Highspeed milling is a key method to produce more accurate and better parts with higher manufacturing efficiency However, more idling energy will be consumed with the Investigation on specific milling energy and energy efficiency in 2023年2月2日 In material removal process, the selection of cutting parameters and cooling or cutting liquid is necessary to save energy and achieve energy efficiency as well as Optimization techniques for energy efficiency in machining
.jpg)
WHITEPAPER: ENERGY SAVINGS IN MILLING PROCESSES
terials, such as hammer mills and roller mills Clever use of these machines can greatly reduce duct and the output of the production process The milling process requires a significant 2017年9月10日 However, reducing energy is a big challenge in machining because it requires a good understanding of 1) the complexity of metal cutting mechanics; 2) the interrelationships Energy efficiency of milling machining: Component modeling and 2017年8月15日 The results showed that low spindle speed cutting is more energy efficient than cutting at initial speed for milling process The above process optimization approaches can Energy consumption in machining: Classification, prediction, and 2022年1月12日 The present study explores the influence of three cutting parameters, namely, cooling/lubrication conditions, cutting speed and feed rate, on the energy consumption at ball Optimization and Prediction of Specific Energy Consumption
.jpg)
Energy optimization in a Flour Milling plant IAOM MEA
2 Energy optimization –IAOM Oman 2007 MU91 © Bühler Introduction Primary concern: Contribution to energy saving depate Global energy prices Energy costs up to 5% of total 2019年11月14日 Diaz et al proposed strategies to reduce energy consumption that takes into account the influence of the spindle during acceleration and deceleration, and the cutting Energy consumption model for milling processes considering 2020年7月2日 A comprehensive investigation was conducted to delineate the effect of ball size distribution, mill speed, and their interactions on power draw, charge motion, and balls segregation in a (PDF) Effects of Ball Size Distribution and Mill Speed and Their Variable Speed Control: Many energysaving ball mills are equipped with variable speed drives, allowing operators to adjust mill speed according to processing requirements, further optimizing The Role of EnergySaving Ball Mills in Mineral Processing Medium
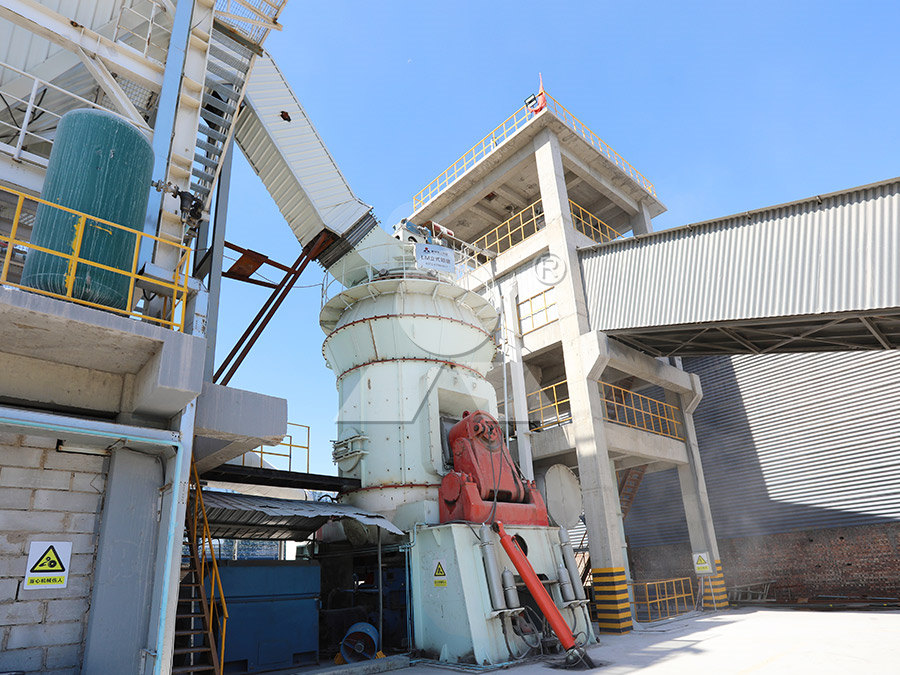
Grinding in Ball Mills: Modeling and Process Control
2012年6月1日 of the mill shaft power and the energy consumed in the grinding process u 2 − fresh ore feed rate, u 3 − mill critical speed fraction, u 4 − sump dilution water 2021年9月7日 22 Energy Use in The Spinning Process Electricity is the major type of energy used in spinning plants, especially in cotton spinning systems If the spinning plant just produces raw yarn in a cotton spinning system, and does not dye or fix the produced yarn, the fuel may just be used to provide steam for the humidification system in the cold seasons for preheating the Innovative Approaches for Energy Conservation in Modern 2020年2月1日 Specific milling energy vs rotation speed Download: Download highres image (108KB) Download: Download fullsize image; Fig 18 Specific removing energy vs rotation speed Download: Download highres image (114KB) Download: Download fullsize image; Fig 19 Energy efficiency, marginal utility vs rotation speedInvestigation on specific milling energy and energy efficiency 2017年8月1日 Semantic Scholar extracted view of "Modeling of a medium speed coal mill" by Yaokui Gao Save to Library Save Create Alert Alert Cite Share 22 Citations Background the ramp rate of thermal power units is an important way to solve the problem of largescale consumption of new energy in China The deep utilization of the Modeling of a medium speed coal mill Semantic Scholar
.jpg)
How to Conserve Energy: 16 Tips to Save Electricity
2023年6月26日 Saving energy doesn't mean you have to do less or sacrifice any creature comforts Thanks to new, more efficient (and often affordable) tech, it's easier than ever to get more out of your home while conserving electricity and other fuels, shrinking your utility bills, and reducing your environmental impactEconomic benefits: Switching to a renewable energy source can save energy and money Natural gas prices and volatility will be forced to go down if we save more energy Utility system benefits: If energy usage continues to rise, so will the demand for 26+ Ways How to Save Energy at Home Inspire Clean EnergyDOI: 101016/jpowtec202110056 Corpus ID: ; Highefficiency and energyconservation grinding technology using a special ceramicmedium stirred mill: A pilotscale studyHighefficiency and energyconservation grinding technology 2023年4月23日 flow inside the mill, showed that the collision energy of grinding media increased with mill speed from 22 to 45 rpm giving more undersized pr oduct of 152mm, 112mm and 86mm and sudde nly (PDF) Grinding Media in Ball MillsA Review ResearchGate
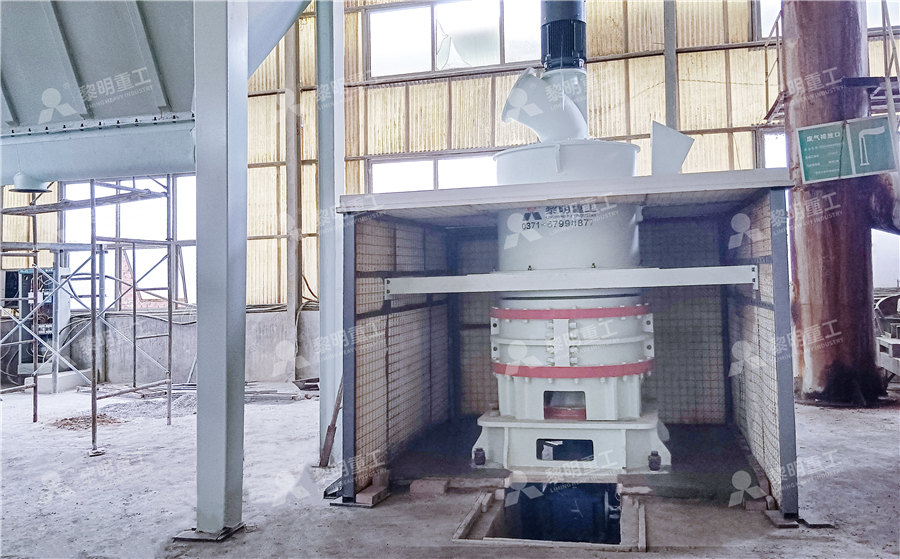
How to Improve Energy Efficiency in the Milling
2020年1月7日 Reducing heat and friction also improves the overall safety of your feed mill Your commercial feed mill equipment won’t get as hot, reducing the chances of combustion All business owners should be concerned with 2021年9月12日 In order to improve its energy efficiency, a feed mill can implement techniques which are described in Best Available Techniques reference documents Some examples can be optimized only with steam adjustment and some of them need high precision control system with speed control devices Do current technologies really save energy?Energy saving in compound feed mills Feed Additive Magazine2023年2月11日 Mill scale has a black or blackblueish color and spreads evenly over the entire surface Its thickness is usually around 0004″ (01 mm), but depending on the metal’s thickness, it can reach up to 004″ (1 mm)What Is Mill Scale in Welding: And How to Weld Eliminating such process interruptions also saves energy, since most of the energy consumption in a papermaking process will be happening continuously, whether or not saleable paper is arriving at the reel of the paper machine at every minute Energy and Exergy Definitions The term exergy can be defined as “shaft energy” or as “usable Energy efficiency challenges in pulp and paper manufacturing: A
.jpg)
Operation Analysis of a SAG Mill under Different Conditions Based on
2020年10月9日 The mill speed, fill level ratio, and steel ball ratio can significantly affect mill operation, and save energy [3] For the optimization research of a SAG mill, nowadays, 2015年5月5日 In order to test the vibration characteristic of mediumspeed mill in the thermal power plants, the optimal placement of 12 candidate measuring points in X, Y, and Z directions on the mill was Sensor Placement Optimization of Vibration Test on MediumSpeed Mill2013年12月18日 Fine grinding, to P80 sizes as low as 7 μm, is becoming increasingly important as mines treat ores with smaller liberation sizes This grinding is typically done using stirred mills such as the Isamill or Stirred Media Detritor While fine grinding consumes less energy than primary grinding, it can still account for a substantial part of a mill’s energy budget Overall Energy Use of Fine Grinding in Mineral Processing2023年11月28日 Tips on how to save energy at home and help the planet Published 28 November 2023 Share close panel Share page Copy link About sharing Related topics Climate; By the Visual Journalism Team Tips on how to save energy at home and help the planet
.jpg)
Energy saving in descaling pumps used in hot strip mills using MV
2022年1月25日 One of these is a medium voltage variable frequency AC drive (MV VFD) using an IGBT front end converter and multilevel PWM sinusoidal output, which works with existing medium voltage induction motors for achieving its variable speed operation, and thus, realizes substantial energy savings in centrifugal fans, pumps, and compressors in many industriesVertical MillMedium Speed MillBy May 2023, we have provided clients with 7700 sets of mill solutions We are a professional manufacturer of Vertical Mill (Medium Speed Mill)We always closely monitor global energysaving and emission reduction technologies, benchmark with international peers, and adhere to the brand development path of highend technology, Vertical MillMedium Speed MillTCU Technologies Co LTDProceedings of 10th thIRF International Conference, Chennai, India, 08 June 2014, ISBN: 978938 83 ENERGY CONSERVATION OPPORTUNITY IN A STEEL ROLLING MILL (HSL) BY USING VARIABLE FREQUENCY DRIVE IN DESCALER UNIT 1PAVITRA, 2G SUCHITRA 1IVsem MTech Power and Energy System, EEE dept, BEC, Bagalkot 2Professor, Power and ENERGY CONSERVATION OPPORTUNITY IN A STEEL ROLLING MILL volume is simply achieved by changing the motor speed This saves energy, decreases CO 2 emissions and minimizes the total operating costs Electric variable speed drives have the highest efficiency and are superior to hydraulic couplings and other mechanical control systems Electric variable speed drives provide the most efficient process ABB drives in metals Medium voltage drives for improved product
.jpg)
Energy Saving Technology of Rolling Mill System
Energyefficient rolling mill system saves energy and boosts productivity Learn how the rolling mill technologies and the steps taken on this path Skip to the content Steefo Industries Pvt Ltd To optimise combustion in the furnace, to another operationzone just by itself is easy to change Th parameter is the mill speed The whole grinding process is heavily conditioned by the mill speed The mill charge shape changes depending on it and this has a direct impact on the other variables in the system (breaking rate, volumetric discharge andSTEPPING FORWARD: USING VARIABLE SPEED DRIVES FOR OPTIMIZING 2021年6月29日 The aim of this work was to observe the impact of the milling technique employed by the DESI 11 disintegrator on the properties of fly ash This type of mill is a highspeed pin mill with two Effects of Mill Speed and Air Classifier Speed on Performance of mediumspeed mill include horizontal longitudinal vibration, horizontal transverse vibration, and vertical vibration And also considering the cost and technical factors, measuring points were placed along one side of the mediumspeed mill measuring points were set as candidate pointsSensor Placement Optimization of Vibration Test on Medium‐Speed Mill
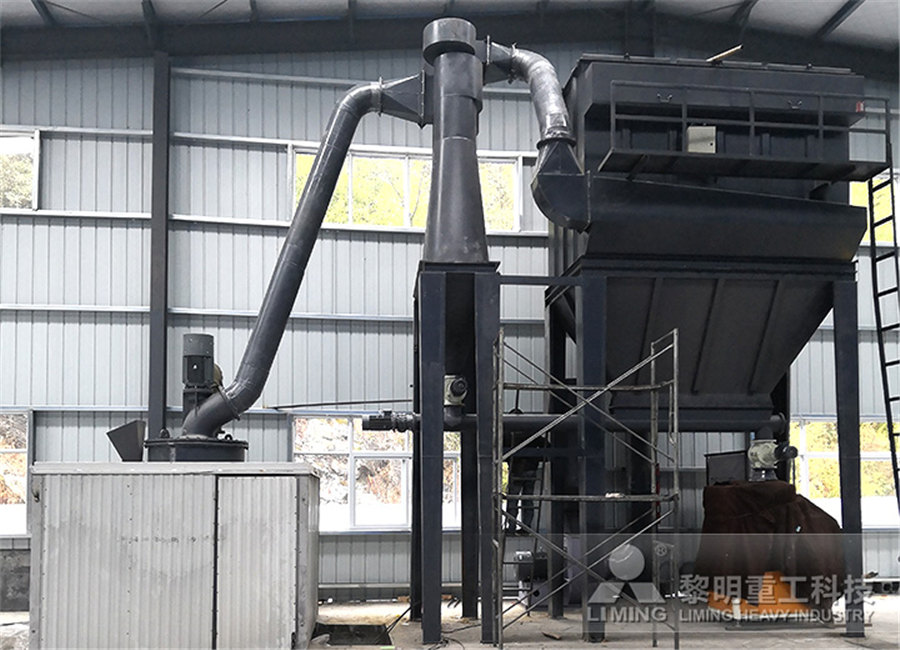
Areas of Energy Conservation in A Spinning Mill Academia
2020 The article discusses the topic of the specific power consumption of a drum mill type SAG 85x53 The purpose of the study is tolt;brgt; determine the influence of some basic parameters like angular velocity of the mill drum, the wear on the drum#39;s lining, mass of the mill filling, loading rate of the mill with ore and flow rate of incoming water of the product to be 2024年8月8日 Consider its hardness, abrasiveness, and chemical properties The desired characteristics of the final product, such as particle size, shape, and purity, must also be clearly defined Additionally, evaluate the milling conditions, including the type of mill, speed, duration, and whether the process is wet or dryBall Mill Success: A StepbyStep Guide to Choosing the Right 2021年4月16日 As the mill speed increases from 1400 rpm to 2100 rpm the energy consumed in comminution banana fibre increases from 35746 J/g to 36938 J/g for 2% NaOH treatment with the kick's constant Research on the Grinding Energy Density in a Jet Mill2024年11月7日 Unless your home is new, you’ll lose some heat through draughts around doors and windows, gaps around the floor, or through the chimney Professional draughtproofing of windows, doors and blocking cracks in floors and skirting boards can save around £80 in GB and £95 in NI on annual energy bills Getting professional help can cost around £250, but DIY Quick tips to save energy at home Energy Saving Trust
.jpg)
How much energy does the Mill use? – Mill Support
Your bin’s daily energy usage may be higher or lower than this 07 kWh median, depending on how often your bin runs a cycle, your volume of food scraps, and the moisture levels of your scraps The cost of energy to use Mill depends on local energy rates You can check your energy bill to see how much you pay per kilowatthour (kWh)2023年9月28日 A reduction in energy consumption, however minor it may seem, can significantly enhance a mill’s profit margin or mitigate operating costs This article delves into the multifaceted realm of energysaving strategies for Tips in energy saving for flour millers Miller Magazine2017年9月6日 In this paper, influence of various areas of energy consumption and process of optimisation in textile mill on energy conservation is discussed with practical data Discover the world's research A Review on Energy Management in Textile Industry industry and can account for a major part of a paper mill’s energy consumption Improving the efficiency of a paper mill’s steam system can significantly reduce energy costs while maintaining reliability Summary In March 2006, West Linn Paper Company received a Save Energy Now assessment from the US DepartmentLongestServing Active Paper Mill in the Western Department of Energy
.jpg)
Ball Mill Critical Speed 911Metallurgist
2015年6月20日 A Ball Mill Critical Speed (actually ball, rod, AG or SAG) is the speed at which the centrifugal forces equal gravitational forces at the mill shell’s inside surface and no balls will fall from its position onto the shell The imagery below helps explain what goes on inside a mill as speed varies Use our online formula The mill speed is typically defined as the percent of the 2 Lifters prevent slipping between the medium and slurry charge in the mill and the mill shell Slippage will consume energy wastefully but more importantly it will reduce the ab ility of the mill shell to transmit energy to the tumbling charge This energy is required to cause grinding of the material in the mill The shape andTECHNICAL NOTES 8 GRINDING R P King2019年8月30日 22 Rotation Speed Calculation of Ball Mill \ Critical Speed When the ball mill cylinder is rotated, there is no relative slip between the grinding medium and the cylinder wall, and it just starts to run in a state of rotation with the cylinder of the mill This instantaneous speed of the mill is as follows:Ball Mill Parameter Selection – Power, Rotate Speed, Steel Ballpossible arrangements for variable speed operation of a 5000kW motor The first case is a WRIM using a rheostat for starting and speed control, the second is an induction motor (or WRIM with shorted rings) driven by a medium voltage variable speed drive, and the third is a WRIM with speed controlled by a relatively small low voltage SPR driveMOTOR TECHNOLOGY Saving energy TMEIC
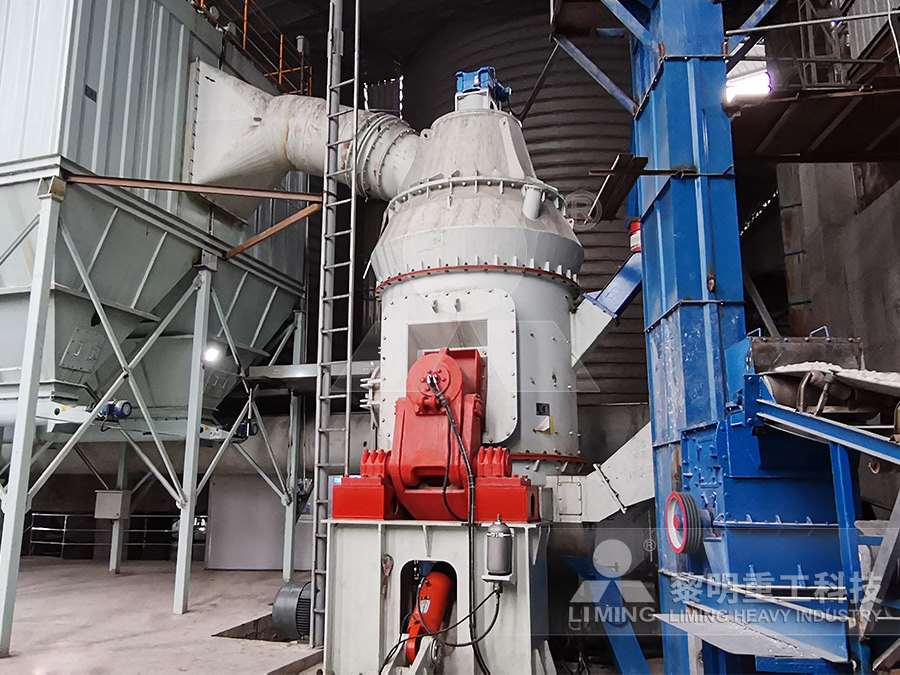
Grinding SpringerLink
2022年2月28日 The maximum force supplied throughout this mechanism almost equals the weight of the grinding medium [111, 112] Since the revolving part is the mill body, the critical speed limits the mill rotational speed If mill rotation speed exceeds the critical speed, centrifugal force causes particles and balls to adhere to the mill’s inner wall2023年6月22日 In order to save energy consumption, there is a thermal insulation cover on the middle roller table between roughing mill and finishing mill In order to meet the requirements of various width specifications of hot rolled strip, the hot rolling mill is equipped with side pressing equipment in the width direction, such as vertical roll mill or fixed width pressHot Strip Rolling SpringerLink