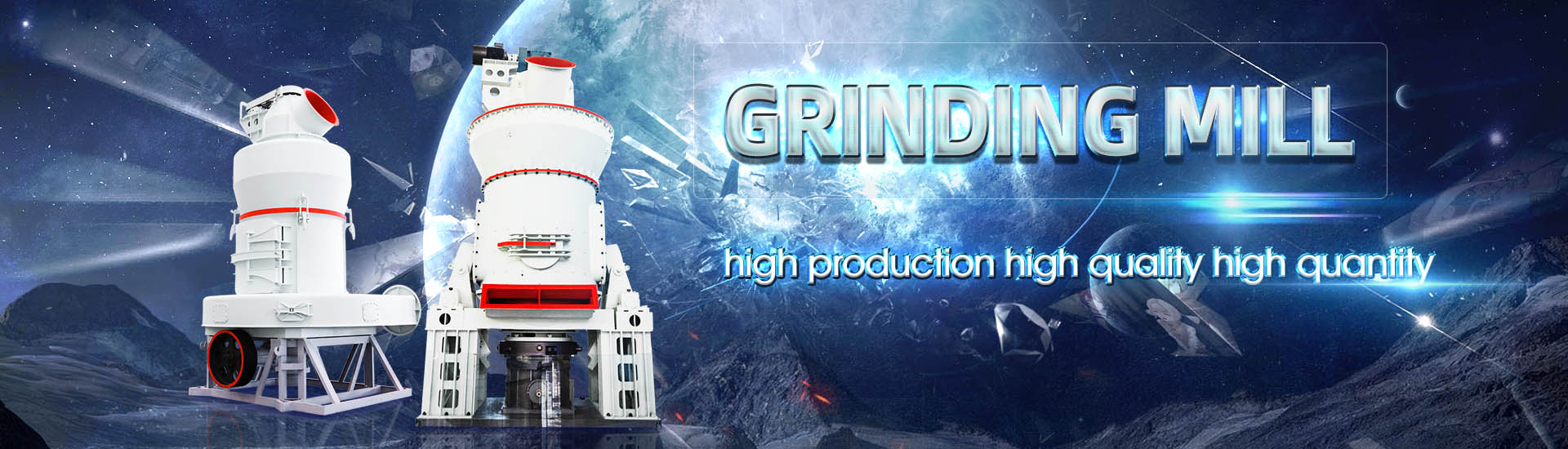
Operating procedures of 200 mesh coal powder mill
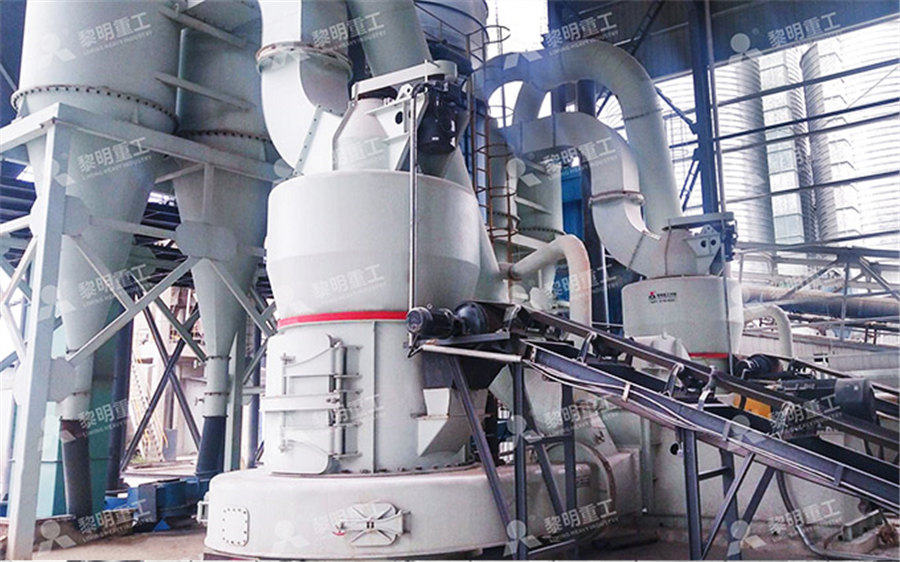
Coal mill pulverizer in thermal power plants PPT
2012年11月17日 The document discusses coal mill/pulverizers used in thermal power plants It describes how pulverized coal is dried, ground, circulated, and classified within the mill to produce a fine powder that is then transported to Advantages: The production of clean pulverized coal for boiler combustion, heating and power supply improves the operation efficiency of small and mediumsized coalfired boilers to 80% Pulverized Coal Processing,Guidance,Technological A 200 mesh coal powder mill, also known as a coal powder preparation production line, is an industrial system that grinds coal into fine powder with a particle size of 200 mesh or smaller 200 mesh coal powder mill/coal powder preparation production lineThis document provides specifications and operating procedures for coal mill pulverizers (A through F) at a power plant It describes the functions of the pulverizers to grind coal into a fine powder to facilitate complete combustionSop Coal Mill PDF Scribd
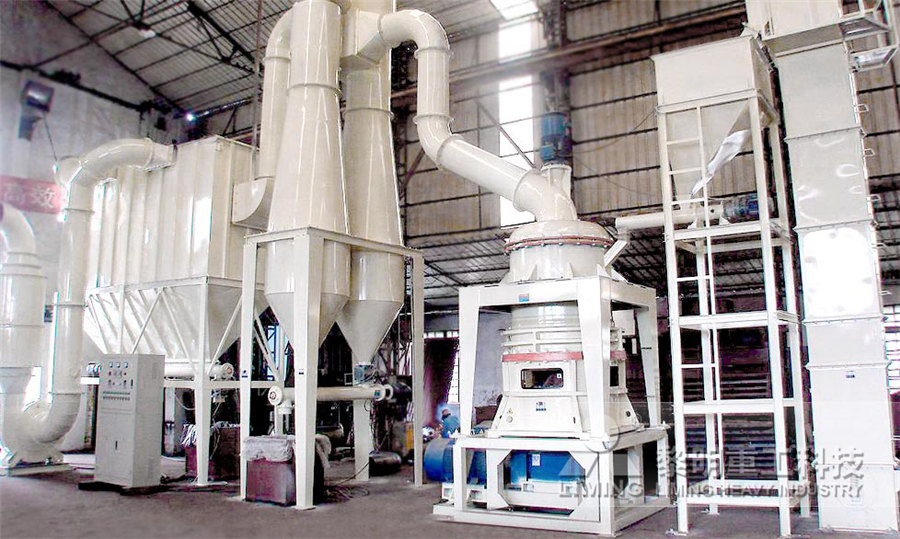
Raymond Bowl Mill designed and built for flexibility Qlar
The Raymond Bowl Mill is considered the finest vertical roller mill available for pulverizing coal The typical Raymond bowl mill system is designed to simultaneously dry, pulverize, and grinding rolls which process four inch coal into a fine powder The bowl (roller) mill is an example of recognized reliability These mills are specifically designed for grinding coal of most grades A Publication of the Lubrication Engineers Technical DepartmentTypically a mill will be controlled so that 70% of the coal powder it produces will pass through a 200 mesh, indicating a particle size of less than 75 microns Operation of coal mills is affected Coal Mill an overview ScienceDirect TopicsCoal and preheated primary air enter one or both ends of the mill from a crusher/dryer or feeder As the mill rotates, the balls cascade and pulverize the coal by impact and attrition The A Comparison of Three Types of Coal Pulverizers Babcock Power
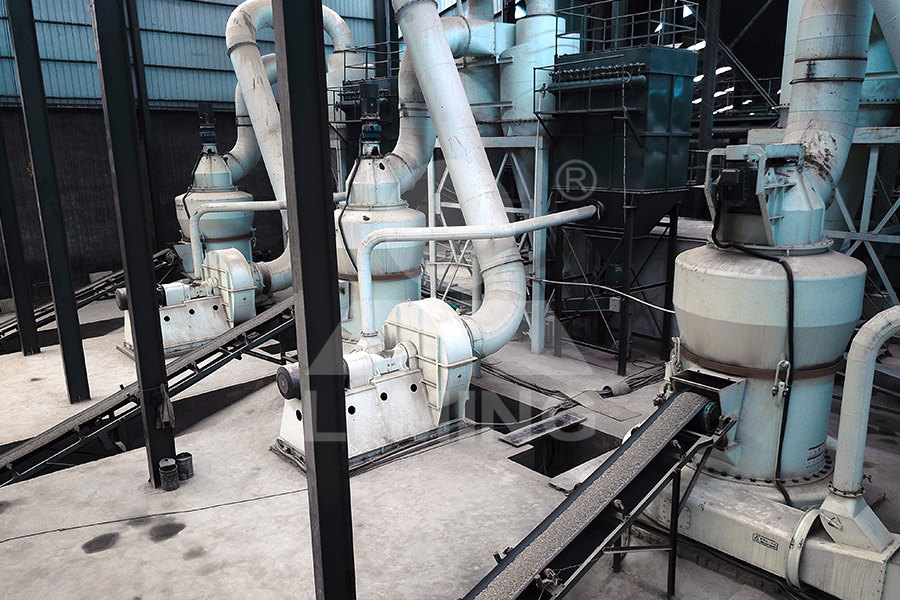
Vertical Grinding Mill (Coal Pulverizer) Explained saVRee
Grinding is achieved using the impact, crush or attrition methods (see below) Grinding increases the cross sectional area of the coal and allows it to dry quicker whilst also making it easier to ignite Grinding is often referred to as ' size The curve is the final part of a feeding duct that carries the coal powder from mill to the Signal acquisitions have been carried out in several ducts and different operating conditions, acquiring 200 consecutive For Plant B, instead the (PDF) Power plant condition monitoring by means of A 200 mesh coal powder mill, also known as a coal powder preparation production line, is an industrial system that grinds coal into fine powder with a particle size of 200 mesh or smaller This powder is then used for various applications, such as combustion in power plants, steelmaking in blast furnaces, or as a component in cement and other industrial processes200 mesh coal powder mill/coal powder preparation production Introduction This article concerns itself with vertical grinding mills used for coal pulverization only (coal pulverizers), although vertical grinding mills can and are used for other purposes The 3D model in the saVRee database represents a vertical grinding bowl millOther grinding mill types include the ball tube mill, hammer mill, ball and race mill, and , roll and ring millVertical Grinding Mill (Coal Pulverizer) Explained saVRee
.jpg)
Boiler Performance and Mill Outlet Temperature Bright Hub
While all these are regarding the mill performance, the coal fineness and mill out let temperature also affect the boiler performance The coal fineness has an effect on the combustion performance like the bottom ash percentage combustibles when the plus 50 mesh percentage goes up It has been very well established that in the case of tangential firing system, the Mill Training Manual Alstom Free download as PDF File (pdf), Text File (txt) or read online for freeMill Training Manual Alstom PDF Coal Mill (Grinding)nominal 600 megawatt (MW) coal fired unit that burns subbituminous Powder River Basin (PRB) coal from Wyoming This paper will cover the experience and results of PGE’s Boardman plant operating on 100% torrefied wood (TW) pellets at 255 MW consuming almost 5000 tons of pellets100% TEST BURN OF TORREFIED WOOD PELLETS AT A FULL Coal 2020年8月12日 Vertical Coal Mill (VCM) is equipment for grinding and pulverizing coal into micron size Rotary kilns then use the powders as fuel burners The VCM has a housing section equipped with a lining An investigation of performance characteristics and energetic
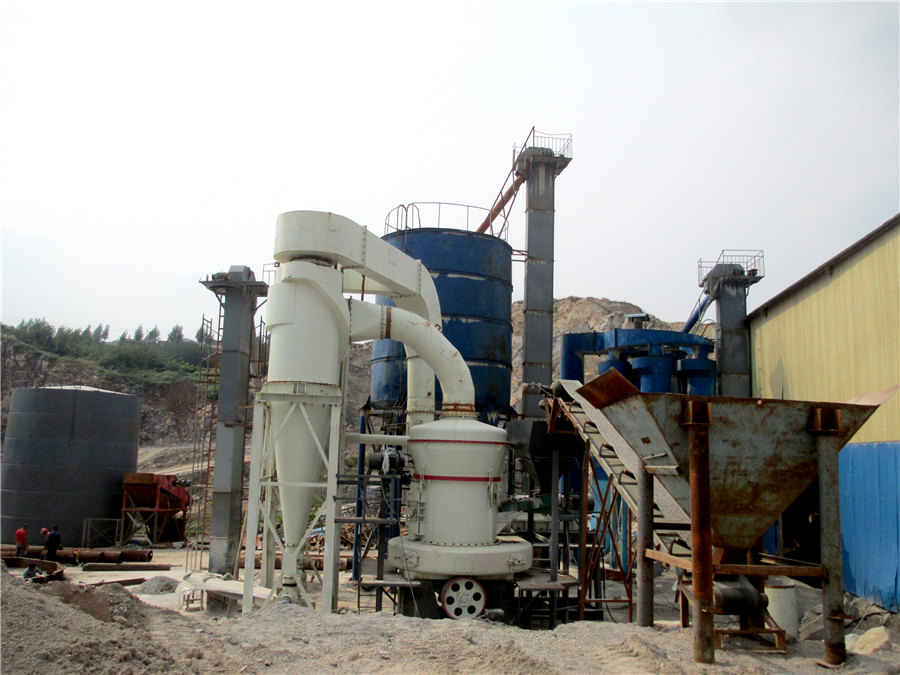
Coal IJSER
By knowing charateristics of the coal mill operating parameters and the probability of the root cause of failure, signal of the outlet coal powder flow of the coal mill was constructed as a new output control target of the pulverizing system [1] Finest coal : 200 mesh Diameter bowl : 96” Quantity of grinding roll : 2015年11月1日 The coal mill grinds the raw coal into fine powder and hot air entering the mill dries and carries the pulverized coal to the burners of the furnace 75% of the pulverized coal passing a 200 mesh screen is optimal for the mill and combustion It can be used for evaluating and validating new controls and operating proceduresA unified thermomechanical model for coal mill operation2017年12月8日 Among them, simplicity, efficiency and low cost have all made sieving analysis the most widely used qualitycontrol procedure in any powder process control industry In order to conduct accurate sieving analysis, Principles and Procedures of Sieving Analysis AggNetPowder Technology, 59 (1989) 255 260 Effect of Operating Parameters in Stirred Ball Mill Grinding of Coal M J MANKOSA, G T ADEL and R H YOON 255 Department of Mining and Minerals Engineering, Virginia Polytechnic Institute and State University, Blacksburg, VA 24061 (USA) (Received January 9, 1989) SUMMARY For any physical separation process to work Effect of operating parameters in stirred ball mill grinding of coal
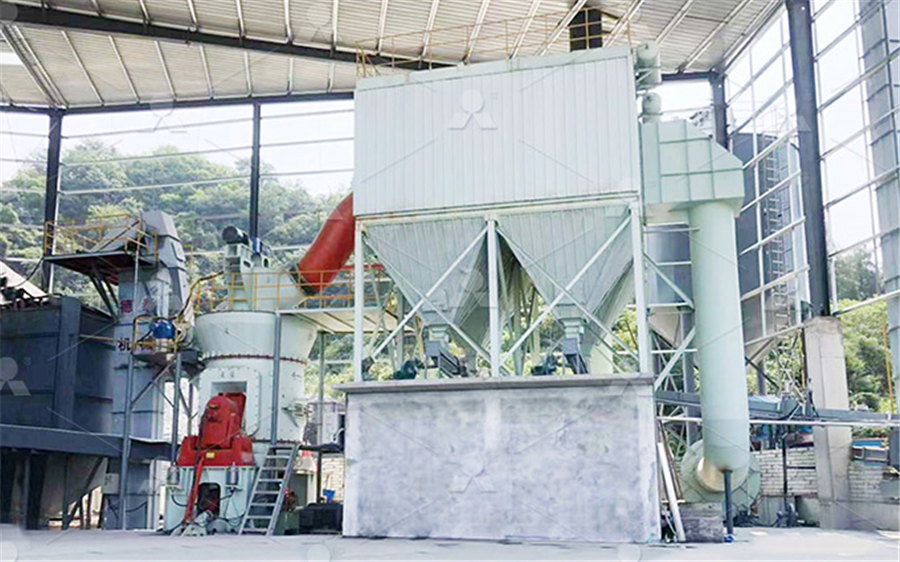
General Commissioning and Operating Procedure of Ball Tube Mill
General Commissioning and Operating Procedure of Ball Tube Mill BBD 4772 Free download as PDF File (pdf), Text File (txt) or read online for free General Commissioning and Operating Procedure of Ball Tube Mill BBD 4772 Capacity Design coal845 tons per hour Ball load 81 tons2021年11月4日 The operating costs of breaking coal particles into fine powder, to achieve optimum combustion for the boilers in a power plant, are made up of power input to carry on an energy intensive Technique to Investigate Pulverizing and Abrasive Performance of Coals DOI: 101016/00325910(89)800841 Corpus ID: ; Effect of operating parameters in stirred ball mill grinding of coal @article{Mankosa1989EffectOO, title={Effect of operating parameters in stirred ball mill grinding of coal}, author={Michael James Mankosa and Gregory T Adel and RoeHoan Yoon}, journal={Powder Technology}, year={1989}, volume={59}, Effect of operating parameters in stirred ball mill grinding of coalPhrase one: raw material crushing Coal blocks will be crushed to 15mm50mm fineness by crusher Phrase two: drying and grinding 1Coal material with low moisture will be sent to the storage hopper by the elevator, and than the feeder will send the material to the main mill for grinding The hot air in the mill will dry the coal This will reduce drying cost 2For high Coal Mill Manufacturers Powder Making Machine Price
.jpg)
Standard Operating Procedure (SOP) For Effective Coal Scribd
Sop Free download as PDF File (pdf), Text File (txt) or read online for free This document outlines the Standard Operating Procedure (SOP) for effective coal administration in Chhattisgarh as established by the Directorate of Geology Mining The SOP details procedures for (1) categorizing coal grades annually based on quality parameters like heat content and ash This document provides standard operating procedures for coal mill and coal feeder operations at a 1x525 MW thermal power plant in Tuticorin, Tamil Nadu, India It outlines responsibilities for personnel, safety and environmental procedures, work instructions, and references The purpose is to safely start and stop the coal mill and feeder while minimizing environmental impacts Key 15sop For Coal Mill and Feeder PDF Scribd2015年4月24日 6 During grinding, balls themselves wear and are continuosly replaced by new ones so that mill contain balls of various ages and thus of various ages and thus of various sizes Ball mill produces 1 to 50 tonn/hr of Ball mill PPT Free Download SlideShare2020年8月19日 Attach clean bag, bottle or bucket (depending on the mill), for every sample d Prior to grinding in the Hammer mill, the large samples must be reduced to small to fit into the milling chamber If a large mill such as a Wiley Mill is available, coarsely grind the entire sample of about 200 g, then subsample to 5 to 10 g for fine grinding in theSTANDARD OPERATING PROCEDURES Center for International
.jpg)
HighEfficiency Vertical Coal Mill Enhancing Coal
Application field: Coal vertical mills are widely used in cement production, calcium carbonate crushing processing, coal powder preparation stations, gypsum powder and reduce the operating power consumption of the coal mill Fineness of ASME Coal Fineness Sampling Test Procedure Rev 3/2010 Page 1 2367 LAKESIDE DRIVE, SUITE A1 BIRMINGHAM, AL 35244 PHONE (205) 4530236 FACSIMILE (205) 4530239 innovativecombustion The design of the ASME Fineness Sampler has been adapted from our longstanding Isokinetic CoalMicrosoft Word ASME Coal Sampling Test ProcedureRaymond Mill for Coal Powder Making The Raymond mill is widely used for grinding coal into fine powder, [] 2024 1115 HGM Ring Roller Mill: Equipment: HGM Series Ultrafine Grinding Mill; Feeding size: 200325 Mesh, D97; Output size: 800 mesh, D90; Capacity: 4000 kg/hourSBM Ultrafine Powder Technology Industrial Grinding Mill, i ABSTRACT Coal pulverisers’ performance optimisation is an important process in power generation plants Pulveriser operation is costly; reliability and availability is key to power generation andPerformance optimisation of vertical spindle coal pulverisers
.jpg)
Pulverizer Plant OM Aspects
Maximum mill capacity vs HGI at coal moisture of 12 % 3000 3200 3400 3600 3800 4000 4200 60 70 80 HGI 90 100 110 120) Output at coal fineness of 70 % passing through 200 Mesh Output at coal fineness of 75 % passing through 200 mesh 年5月31日 Mineral crushing is the main source of energy consumption in mineral processing According to statistics, this consumption accounts for about 35–50% of the total cost of the mine (Curry et al, 2014), or even higherIt may also account for 18% of the global electrical energy consumption (NapierMunn, 2015)More efficient crushing equipment needs to be Analysis of vertical roller mill performance with changes in Fuel preparation for a pc boiler occurs in a mill, where coal is typically reduced to 70% through a 200mesh (74μm) screen Figure 2 shows a particlesize distribution from a bowlmill grinder typically used in power plants A typical utility specification for particle size distribution of the coal is that 70% of the mass should pass through a 200mesh screen, which is equivalent to 70% Pulverized Coal Boiler an overview ScienceDirect Topics2019年1月15日 Different feed coals (CoalA and CoalB) grinded in ball mill with and without balls referred as type I and type II respectively in the present study Crushed samples were subjected to size analysis Each coal sample with different size fraction was studied under oil immersion reflected light microscope (Leica DM6000M) for its liberation characteristics under Generation of low ash fine clean coal powder by autogenous
.jpg)
Coal Mill Safety: A Critical Aspect of Power Plant Operations Coal
Coal mills, also known as pulverizers, play a critical role in power plants by grinding coal into fine powder, which is then used in various pyroprocesses These mills pose significant safety risks Ensuring the safe operation of coal mills is crucial for preventing accidents, maintaining plant efficiency, and safeguarding the health of workerscinnamon (ground) 70 to 200 clay 01 to 2 coal dust 1 to 100 coffee (ground) 5 to 400 concrete dust 3 to 100 dust (household) 005 to 100 dust mites 100 to 300 eye of a needle 1230 flour (wheat milled) 25 to 212 gelatin powder 5 to 90 giardia cysts 8 to 14 ginger (ground) 25 to 40 200 No 200 200 Mesh 00500 00020 0 MESH and MICRON SIZES Industrial Spec2014年3月1日 The object of the study reported here is the grinding process in a tumbling mill where the mechanism of destruction by crushing is implemented, which is caused by the mechanism of compression loading(PDF) Analysis of ball mill grinding operation using mill power The Mixer Mill MM 400 is a true multipurpose mill designed for dry, wet and cryogenic grinding of small volumes up to 2 x 20 ml It mixes and homogenizes powders and suspensions with a frequency of 30 Hz within seconds – unbeatably fast and easy to operateLaboratory Mixer Mill MM 400 RETSCH

Multi mill operation and cleaning procedure
Multi mill , The purpose of this SOP is to describe the Operation and cleaning procedure of Multi Mill (Model: GMP) in order to comply with cGMP standard Multi mill , Scope : The scope of the procedure is applicable to the Multi Mill (Model: GMP) at the Product Development area of XX Pharmaceuticals Pvt Limited Definitions / Abbreviation Vertical Coal Mill (VCM) is equipment for grinding and pulverizing coal into micron size Rotary kilns then use the powders as fuel burners The VCM has a housing section equipped with a lining The layout of the coal mill with a rotary classifierHLMX 2500 Mesh Superfine Powder Grinding Mill; HLM Vertical Roller Mill; RSeries Raymond for decades, with good product quality, excellent service and an experienced team For more information on the safety operating procedures of Raymond mill, please feel free to consult, address:hcmkt@ Coal Grind, Petroleum Coke Vertical What are the safe operating procedures for Raymond mills?Powder Technology 192 (2009) 260–267 Contents lists available at ScienceDirect Powder Technology j o u r n a l h o m e p a g e : w w w e l s ev i e r c o m / l o c a t e / p ow t e c Steady state inferential modeling of temperature and pressure in an airswept coal pulverizing ball mill Augustine B Makokha a,⁎, Michael H Moys a, Costa Couvas a, Alex M Muumbo b a b (PDF) Steady state inferential modeling of temperature and
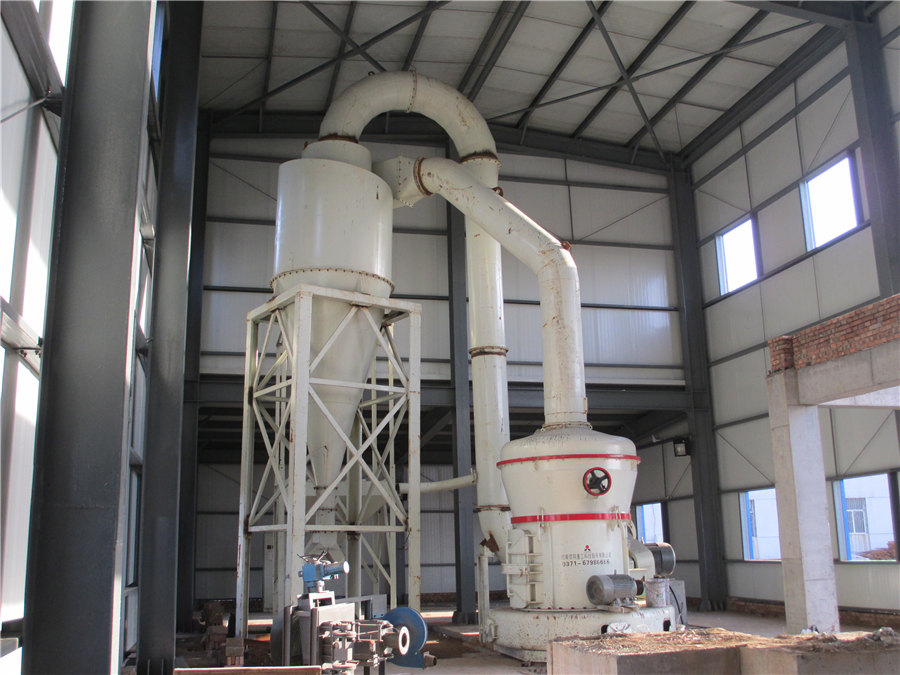
(PDF) Modeling and Control of Coal Mill Academia
Modeling and Control of Coal Mill × Close Log In Log in with Facebook Log in under the following operating conditions: Mass flow rate of raw coal 30 tons/hr; Mill differential pressure 160; Outlet 200 mm wc; Primary air temperature 250280 Motor 350 Mass of coal (kg) 300 mc mpc mcair 250 200 150 100 50 0 500 1000 1500 2000 Time