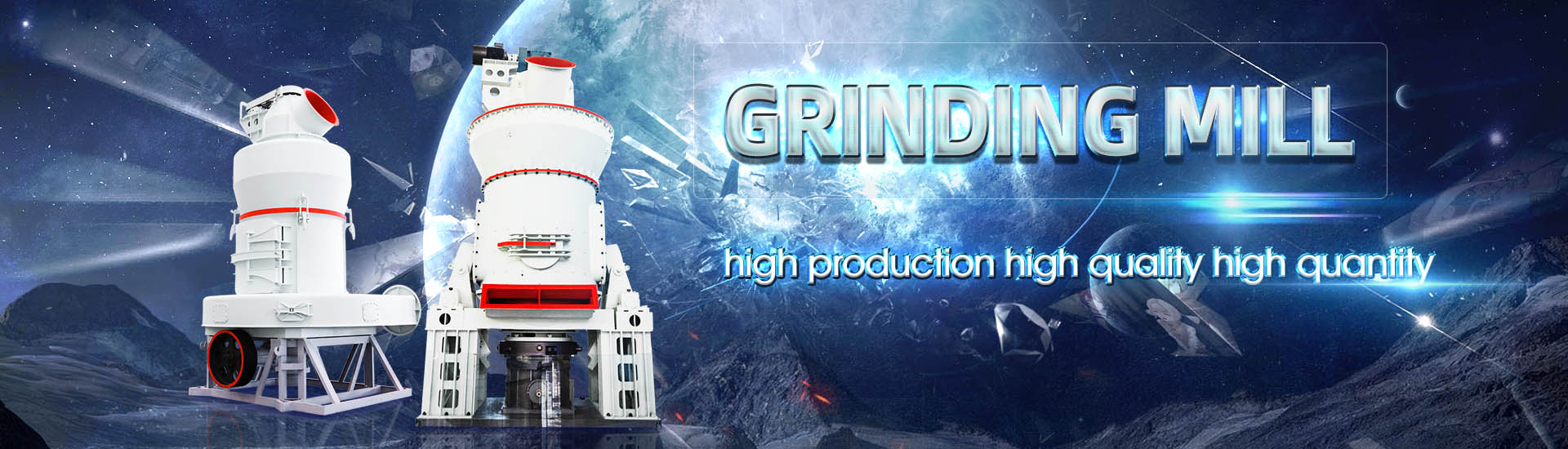
Specific content of cement two grinding and one burning
.jpg)
WS Zhang, JY Ye, HX Wang, Y Wang
In this paper, the easily grinding Portland cement clinker has been prepared by increasing the content of C3S in the clinker and adding the mineralizer to the raw mix The composition, There are four stages in the manufacture of portland cement: (1) crushing and grinding the raw materials, (2) blending the materials in the correct proportions, (3) burning the prepared mix in Study and Review of Ordinary Portland Cement1983年1月1日 C2S decreases and C3S increases Higher mechanical strength at later ages and lower at early ages Heat of hydration at early ages decreases Unburnt clinker can produce Burnability and Clinkerization of Cement Raw Mixes2024年11月23日 There are four stages in the manufacture of portland cement: (1) crushing and grinding the raw materials, (2) blending the materials in the correct proportions, (3) burning the prepared mix in a kiln, and (4) grinding the Cement Extraction, Processing, Manufacturing
.jpg)
Cement SpringerLink
2021年3月3日 CO 2 is generated at two points during cement production: as a byproduct of burning of fossil fuels, which indirectly results in CO 2 emissions, and from the thermal 2019年3月6日 The process of manufacture of cement consists essentially of grinding and mixing the raw materials in certain proportions and burning in a huge cylindrical steel rotary kilns lined Constituent Materials SpringerLink224 The final grinding in the cement mill The clinker temperature must be maintained from 100 to 125 °C in this stage to prevent dry or wet clogging of the cement plant equipment This can Impacts of Cement Production on the Environment with Practical 2021年4月19日 The compressive strength of cement pastes at 1, 3, 7 and 28 days was evaluated to verify that the blends with low resistance to grinding complied with compressive Resistance to Grinding and Cement Paste Performance of Blends
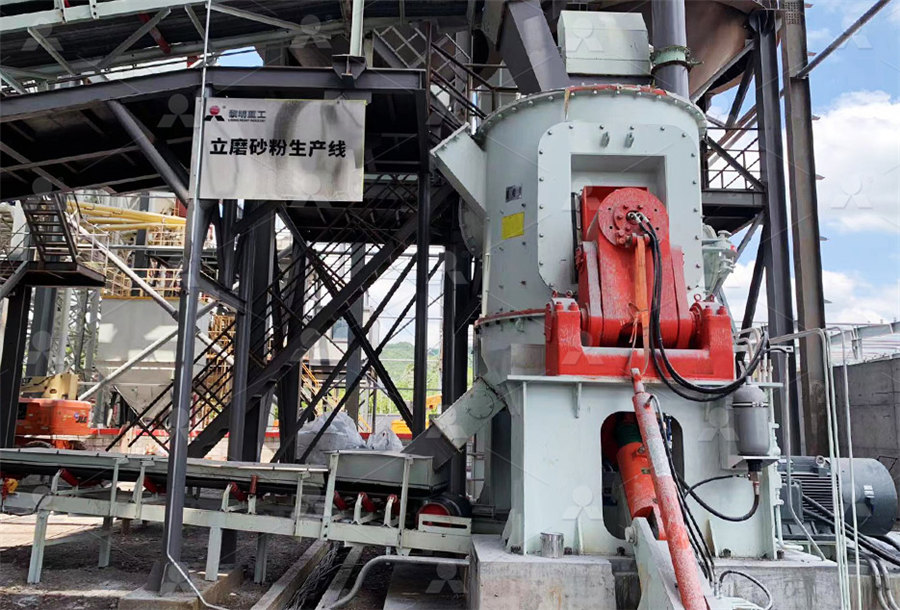
A «carbon footprint» of low water demand cements and cement
2022年4月23日 about 330 kg CO2 are emitted from the combustion of fossil fuel for burning 1 ton of clinker In total, 835 kg CO 2 are produced per 1 ton of clinker The CO 2 emission 2021年4月19日 In Portland cement, oxides’ composition defines final product quality and performance Variations in chemical composition of the oxides are evidenced throughout the cement manufacture process at its different stages, such as mining of raw materials at different quarries, differences in the kiln burning conditions, or the addition of aggregates during the Resistance to Grinding and Cement Paste Performance of Blends 2022年8月10日 It also contains several retarders to meet the requirement of reducing tricalcium aluminate (C3A) and the coarser grinding content of cement clinker However, the slurries of such oilwell cement remain pumpable even 18 Types of Cement and Its Uses Civil TrekCondition in one of the grinding chambers of the mill Results of Optimization The graphical analysis presented in Figure 2 represents progress of grinding along the length of the mill after optimizing the grinding process rogress of grinding is clearly visible in Desired p the graphs Figure 2: Analysis of longitudinal samplesOPTIMIZATION OF CEMENT GRINDING OPERATION IN BALL MILLS
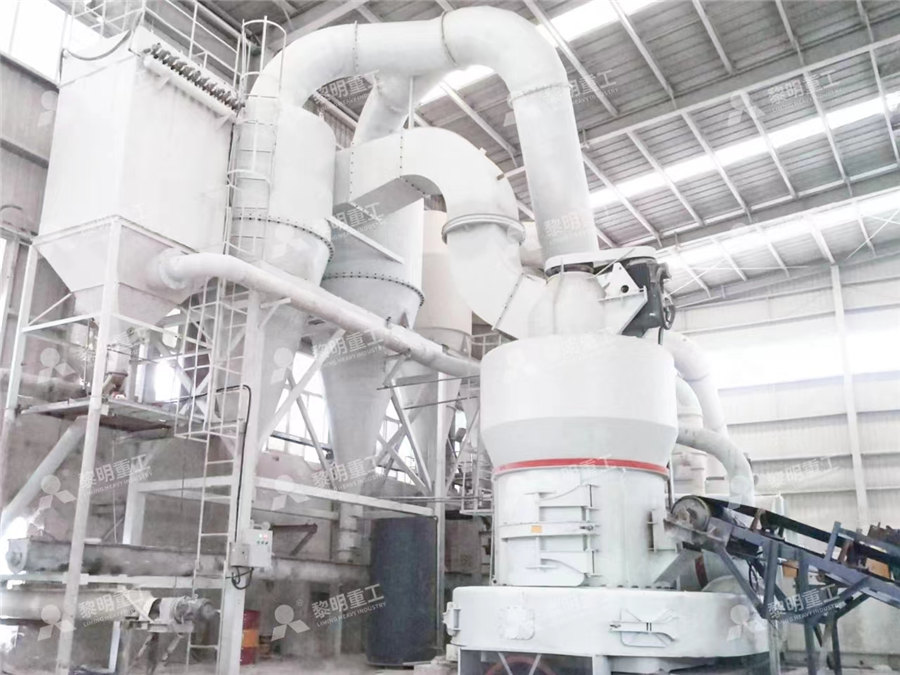
(PDF) Rice Husk Ash in Concrete ResearchGate
2022年12月22日 SEM images of RHA grounded for varying lengths of time, adapted from [28] (a) Grinding time: 10 min; (b) Grinding time: 30 min; (c) Grinding time: 120 minLSF of clinker lies in the range of 9298 Higher LSF at controlled free lime content translates to better quality of clinker (high C3S), difficult clinkerization, high heat consumption Silica Modulus (SM) is the ratio of content of oxides of silica to the oxides of alumina and iron SM signifies the ratio of solid content to the melt contentClinkerization Cement Plant OptimizationAn industrial comparative study of cement clinker grinding systems regarding the specific energy consumption and The splitter bin separates the classifier coarse product into two streams One stream feeds the ball mill circuit at a controlled rate matching of 45μm residue than the cements produced in the other two grinding (PDF) An industrial comparative study of cement clinker grinding 2021年8月26日 This research aimed to investigate the environmental, economic, and functional performances of ordinary portland cement (OPC) In short, we discussed the definition, the chemical composition and Study and Review of Ordinary Portland Cement ResearchGate
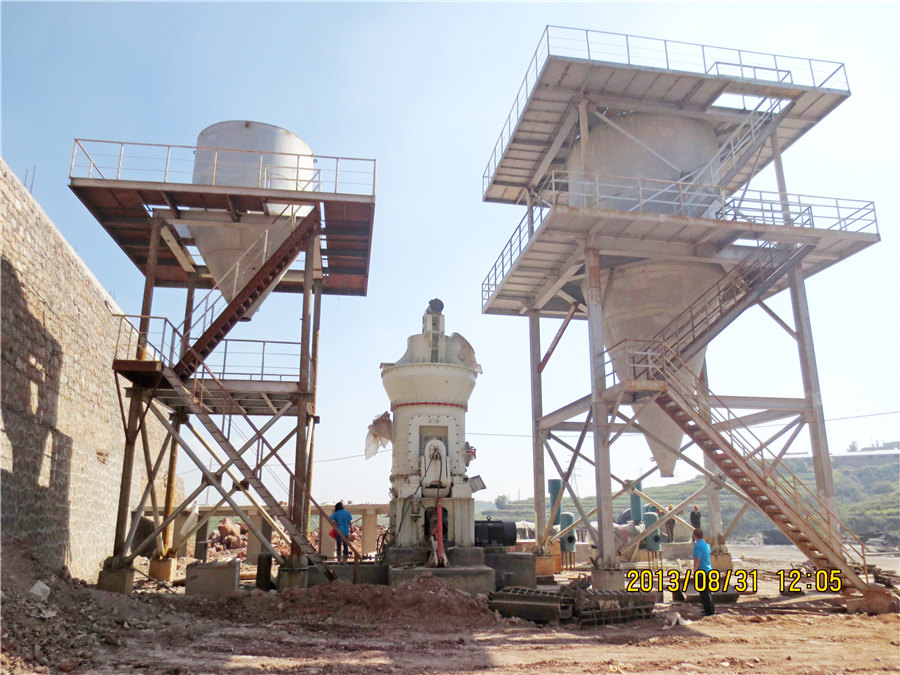
Study and Review of Ordinary Portland Cement
As per Indian standard, IS 2692015, 33 Grade of cement means a compressive strength of cement after 28 days is 33N/mm2 This grade of cement is outdated and no one is using it in recent times 33 grade of cement is not suitable for making more than M20 grade of concrete2013年11月1日 Materials characterization showed that the grinding quality of the seven cements was very different This parameter was defined by the ratio of specific surface (Blaine) and residue at 40 lmThe Effects of grinding on the properties of Portlandlimestone cement2022年12月23日 This review provides an indepth analysis of the complex chemistry of cement, offering valuable insights for researchers(PDF) An Insight into the Chemistry of Cement—A Review2024年11月23日 Cement Composition, Properties, Major Cements: Portland cement is made up of four main compounds: tricalcium silicate (3CaO SiO2), dicalcium silicate (2CaO SiO2), tricalcium aluminate (3CaO Al2O3), and a Cement Composition, Properties, Major Cements
.jpg)
Resistance to Grinding and Cement Paste Performance of Blends
Resistance to Grinding and Cement Paste Performance of Blends of Clinker, Limestone and Gypsum Sofı´a HenaoDuque 1 • Diego A Acosta1 • Jua´n A Tobo´n2 • Santiago Builes Received: 16 October 2020/Accepted: 29 March 2021/Published online: 19 April 2021 The Institution of Engineers (India) 2021 Abstract Grinding of finished cement is In this article we will discuss about: 1 Characteristics of Cement 2 Properties of Cement 3 Composition 4 Functions of Ingredients 5 Harmful Constituents 6 Setting Action 7 Site for Factory 8 Packing 9 Ball Mills and Tube Mills 10 Field Tests 11 Storage 12 Uses Characteristics of Cement: Following are the characteristics of cement: (i) The colour of Cement: Characteristics, Properties, Composition, Harmful Constituents 2024年11月23日 Cement Extraction, Processing, Manufacturing: Raw materials employed in the manufacture of cement are extracted by quarrying in the case of hard rocks such as limestones, slates, and some shales, with the aid of blasting when necessary Some deposits are mined by underground methods Softer rocks such as chalk and clay can be dug directly by Cement Extraction, Processing, Manufacturing Britannicaclinker are processed in the mill, divided into two stages: the grinding stage in chamber I and the milling stage in chamber II In the final stage, the cement is transferred to the separation stage, where the raw material is returned to the mill while the fine cement is stored in the storage silo [38, 40] 23 Cement Packaging and DispatchImpacts of Cement Production on the Environment with Practical
.jpg)
The influence of surfactants upon grinding and hardening of cement
2013年6月15日 The additive was dosed in three different ratios (0,03%, 005% and 01%), reported at the weight of cement subject to grinding Grinding fineness of the cements, expressed through Blaine specific 2023年3月18日 1 Introduction The cement industry is one of the leading contributors to the carbon footprint, and the production of Portland cement (PC) accounts for 10–23% of total anthropogenic CO 2 emissions [1,2], resulting from (1) carbonate decomposition and (2) the oxidation of fossil fuelsThe minimum theoretical energy required for calcination is estimated to Effects of Grinding Methods and WatertoBinder Ratio on the Indeed, the given curves do not relate to cement or cement raw mix, but represent results of practical grinding of iron ore with different mosture contents in a onecompartment tube mill (size 425 x 117 m, open circuit, 4400 HP drive)Finish grinding INFINITY FOR CEMENT EQUIPMENTClinker grinding can be influenced by adding metal oxides or calcium sulfate of metal oxides or calcium sulfate to raw mix [13,14] They control the oven's melt content and the clinker's porosity Regarding the final grinding of the cement, all the grinding steps areGRINDING ABILITY OF UNPROCESSED AND PROCESSED CLINKER FROM CEMENT

Influence Grinding Procedure, Limestone Content and PSD of
2017年10月28日 Concrete is the most widely used material on earth; It is strong, durable and relatively inexpensive The cement industry is responsible for about 5–8% of the global manmade CO 2 emissions On average 08–09 tons CO 2 is emitted for the production of 1 ton of cement During the production of cement clinker, calcium carbonate from limestone decomposes to 2018年11月8日 Overview of the Influence of Burning Temperature and Grinding Time two important facts on cement as a is one kind of new generation gap graded hot mix asphalt with higher content of Overview of the Influence of Burning Temperature and Grinding Keywords: Cement grinding aid, Fineness, Compressive strength, Size distribution Abstract In this paper, By choosing four kinds of grinding aids better onecomponent, The grinding aid of cement grinding aids is determined by orthogonal optimization By adding different inorganic reinforcing components, Developed a cement grindingThe Effect on the Performance of Cement Grinding Aid Components2015年1月31日 One of such materials is the rice husk which under controlled burning, and if sufficiently ground, the ash that is produced can be used as a cement replacement material in concreteStudies on effects of burning conditions and rice
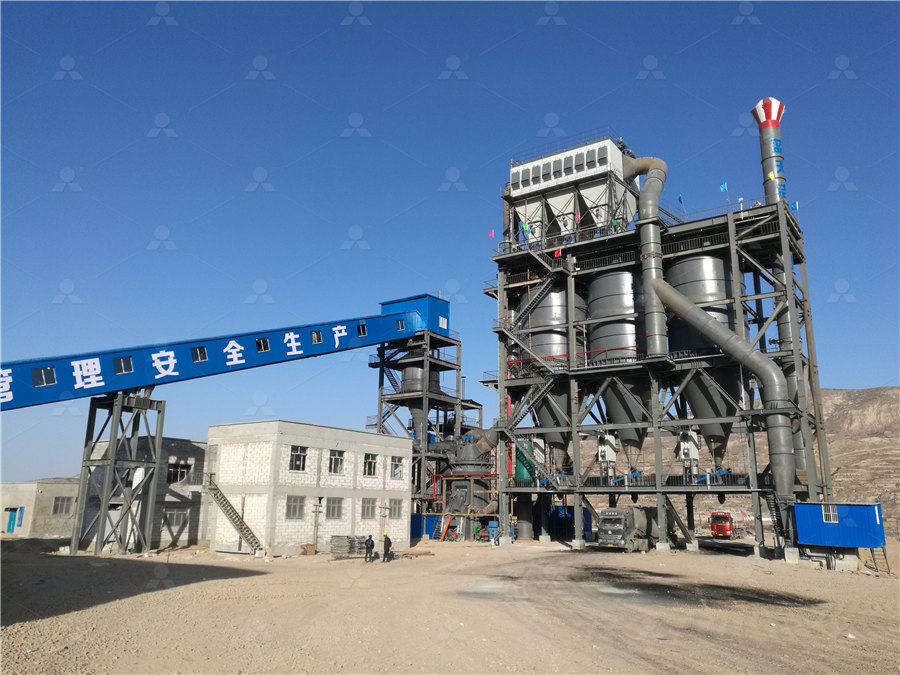
Overview of cement grinding: fundamentals, additives, technologies
2017年5月19日 Cement industry is characterized by sizeable energy demand which accounts for about 110kWh (375 thm) per ton of cement in modern plants Industry impacts heavily also on CO2 emissionsdeterioration Increase in fineness of cement is also found to increase the drying shrinkage of concrete Fineness of cement is tested in two ways: a) By sieving b) By determination of specific surface (total surface area of all the particles in one gram of cement) by air –permeability apparatus (generally Blaine air –permeability apparatus)1 Manufacturing Process of Cement Indus University2012年5月1日 Possible alternatives are the presented maize ashes, the K 2 CO 3 /Ca(OH) 2 mixture from Esaifan et al [15], or the sodium aluminate from Gluth et al [16] and van Riessen et al [17]An industrial comparative study of cement clinker grinding DOI: 101016/00088846(93)900163 Corpus ID: ; The effect of intergrinding and separate grinding of cement raw mix on the burning process @article{Kakali1993TheEO, title={The effect of intergrinding and separate grinding of cement raw mix on the burning process}, author={Glykeria Kakali and Sotiris Tsivilis}, journal={Cement and Concrete Research}, The effect of intergrinding and separate grinding of cement raw
.jpg)
The effect of intergrinding and separate grinding of cement raw
1993年5月1日 The effect of intergrinding and separate grinding of cement raw mix on the burning process Experimental Limestone and clay of industrial origin were used in order to prepare two groups of samples The first one is consisted of No 3 INTERGRINDING, SEPARATE GRINDING, CEMENT RAW MIX 655 TABLE 4 fCaO Content of Interground content of the easily Portland grinding cement clinker is up to 738wt% based on the whole mineral composition On the same test condition, it takes for 45 min when the specific surface area of the easily grinding Portland cement clinker attains to 320 m2/kg and the ordinary Portland cement clinker needs to be ground for 8 minWS Zhang, JY Ye, HX Wang, Y Wangstrength and water content A low amount of grinding causes the production of coarsergrained cement than the desired one, and as a result of the cement hydration, the setting time and final concrete strength will be affected On the other hand, overgrinding will yield finegrained cement, which will lead to a very rapid settingEffects of various grinding aids dosage on comminution Srce2023年1月15日 Cement is stored and transported in bags The amount of cement in a bag varies from one country to another, depending upon their local practices Weight of 1 bag of cement =50 kg; Volume of 1 bag of cement = Portland Cement: Raw Materials, Manufacturing, Types
.jpg)
(PDF) Energy and Economic Comparison of Different Fuels in Cement
2021年5月3日 This study aims to assess the impact of using different fuels in Egyptian Titan Alexandria Portland Cement Company on emissions and concentrations of pollutants (Total suspended particles (TSP It is mainly the content of alumina and ferric oxide that governs the combination of calcium and silica at lower sintering temperatures At this poin it is appropriate to define the terms “easy burning” and “hard burning” In this text, an easy EVERYTHING YOU NEED TO KNOW ABOUT THE 2023年10月19日 Variability in Clinker Properties: Clinker properties can vary from one batch to another, leading to inconsistencies in the grinding process and the quality of the final cement product Solutions: Quality Control: Rigorous quality control measures can help identify and address variations in clinker propertiesClinker Grinding Techniques in Cement Manufacturing JM 2019年8月14日 The cements were prepared from two limestone types and two clinker types with a graded limestone content of up to 30 wt % The limestones had a different CaCO 3 contentPreparation and properties of Portland limestone cements
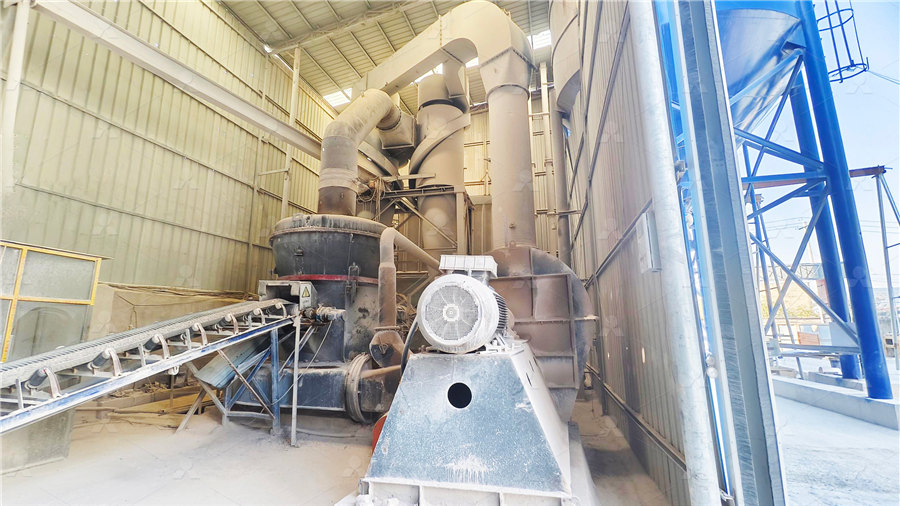
The effects of grinding media shapes on the grinding kinetics of cement
2013年2月1日 The effects of balls and cylinders on the clinker's specific rate of breakage were investigated The results showed that the specific rate of breakage provided by cylinders is higher than that of balls − 200 + 170 mm is an optimum feed size for 20 mm diameter balls and 20 × 20 mm diameter cylindersAt that feed size, the value of Si is maximized2020年10月15日 This research focused the role to study the effects and ways to control the chemical composition of clinker for better cement production Cement is a substance produced by grinding a mixture of a Effects and Control of Chemical Composition of Clinker for Cement 2020年7月24日 This paper presents results regarding the grinding behaviour of two batches of material (clinker) in a ball mill with its own twostep grinding process: the first one with a ball load, the second Determination of granulometrical composition of the clinker by grinding 2015年10月23日 In this chapter an introduction of widely applied energyefficient grinding technologies in cement grinding and description of the operating principles of the related equipments and comparisons over each other in terms of grinding efficiency, specific energy consumption, production capacity and cement quality are given A case study performed on a EnergyEfficient Technologies in Cement Grinding IntechOpen
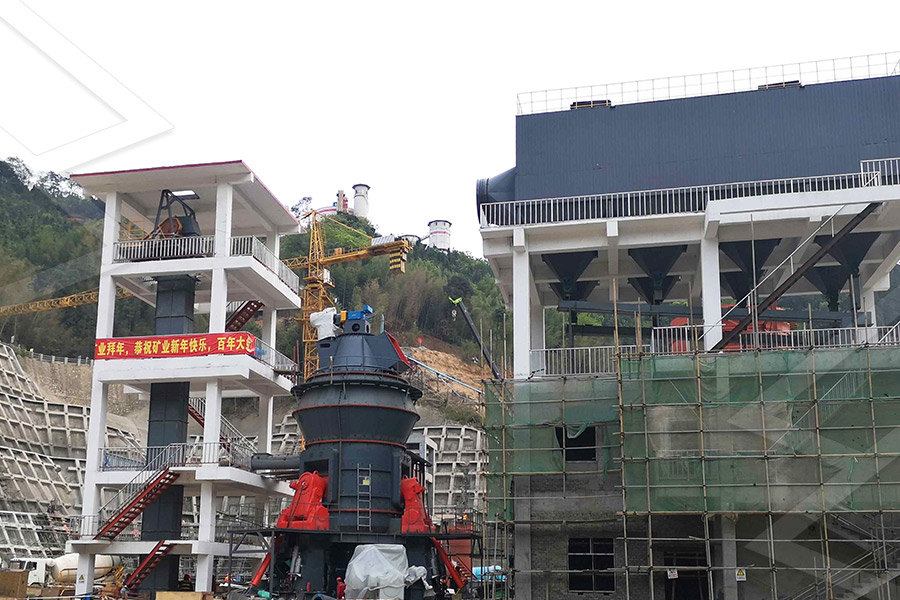
Performance of glassblended cement produced by intergrinding
2021年4月1日 This study aims to investigate the grindability and performance of glassblended cements depending on the grinding method and glass type Two grinding methods, intergrinding and separate grinding