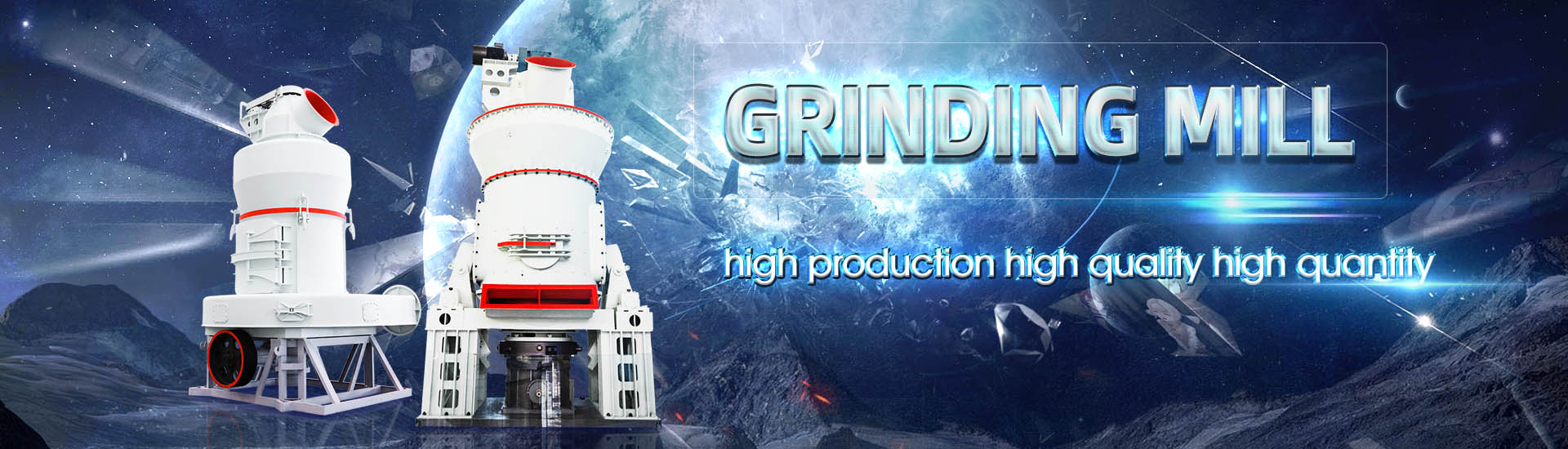
Roller Mill Operation ProcessRoller Mill Operation ProcessRoller Mill Operation Process
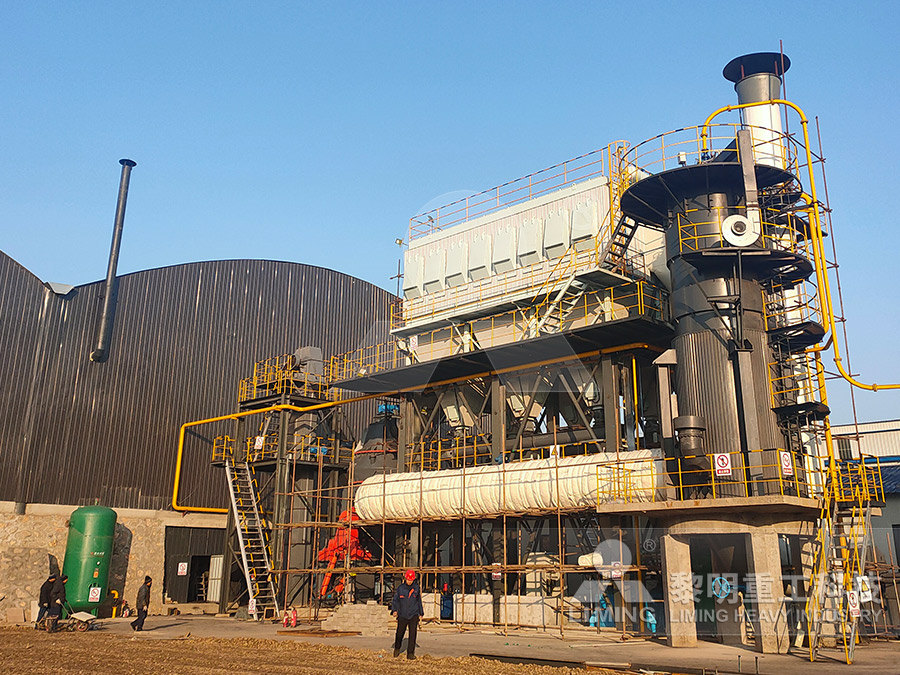
Roller mills: Precisely reducing particle size with greater efficiency
roller mill operator can control the particle size by widening or narrowing the roll gap For most roller mills, the roll gap is automatically adjusted through a PLC that’s programmed to change Rolling is the most important metal forming process More than 95% of ferrous and nonferrous metals and alloys are processed to their usable shapes by rolling Usable shapes of rolled Introduction to Rolling Process Cambridge University Press2020年6月17日 The present article aimed to access rolling techniques in metal forming operation, or as part of the industrial manufacturing process Comparison in performance of Rolling operation in metal forming: Process and principlesIt begins with comprehensive coverage of rolling processes and the mechanics of rolling, which is the theoretical content of the subject This is followed by a chapter on ‘rolling practices’ that Principles and Applications of Metal Rolling
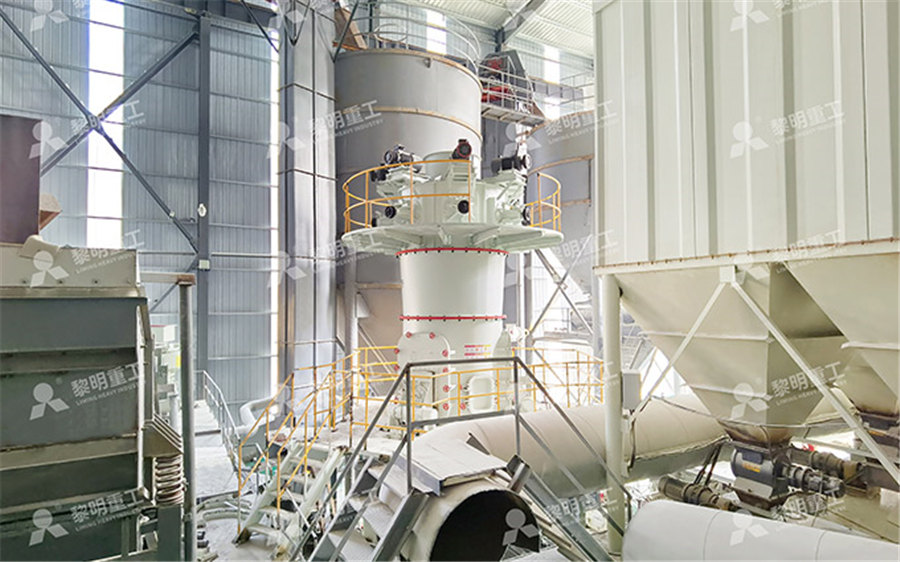
Roller mill Wikipedia
Roller mills are mills that use cylindrical rollers, either in opposing pairs or against flat plates, to crush or grind various materials, such as grain, ore, gravel, plastic, and others Roller grain 2007年1月1日 Breakage of wheat kernels during roller milling has been modelled in terms of the distribution of kernel characteristics (hardness, size, moisture) and roller mill operation (roll Chapter 7 Roller Milling of Wheat ScienceDirectRoller mill is a type of grinding equipment for crushing materials by pressure between two or more rolling surfaces or between rolling grinding bodies (balls, rollers) and a track (plane, ring, and Roller Mill Springer2016年6月5日 Definition of Rolling Process Rolling is the most important metal forming process More than 95% of ferrous and nonferrous metals and alloys are processed to their usable Introduction to Rolling Process (Chapter 1) Principles and
.jpg)
Operational parameters affecting the vertical roller mill
2017年4月1日 In this study, pilot scale tests were performed with a mobile verticalrollermill grinding plant to investigate the relationships between operational parameters The grindability affects the capacity of grinding, type of mill and roller pressure The capacity of the mill is calculated Using G K * D 251 Where, G is capacity of the mill, K1 is roller mill coefficient and D is table diameter 2 PROCESS CONTROL OF VRM The conventional control system of VRM composed of field staff to adjust the few processPROCESS CONTROL FOR CEMENT GRINDING IN VERTICAL ROLLER MILL containing materials are dried in the process of contacting with hot airflow By adjusting the hot air temperature, Roller Mill, Fig 1 Structure diagram of vertical roller mill 2 Roller Mill the hydraulic system After completing a grinding operation in the extrusion area, the material rotates with the cylinder and falls onto the feeding Roller Mill Springer2017年9月11日 PDF In this study, an extensive sampling study was carried out at vertical roller mill of ESCH Cement Plant in Luxemburg Samples were collected from Find, read and cite all the research (PDF) Performance Evaluation of Vertical Roller Mill
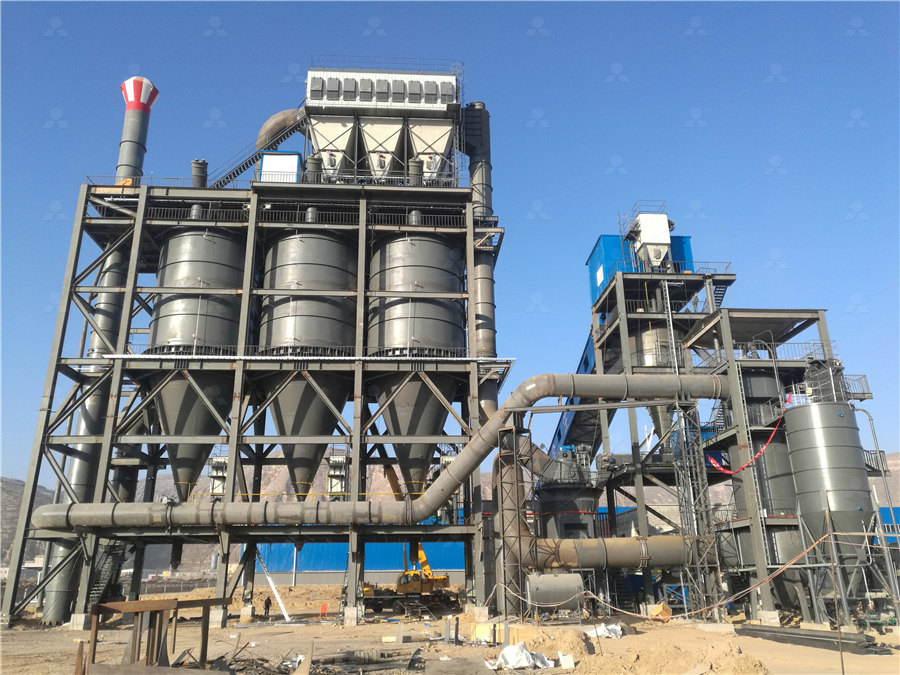
Operational parameters affecting the vertical roller mill
Request PDF On Sep 1, 2016, Deniz Altun and others published Operational parameters affecting the vertical roller mill performance Find, read and cite all the research you need on ResearchGate15 roller mill 32 41 47 52 55 18 roller mill 32 40 47 53 50 60 • Wt of bagasse after each mill w = TCHxfbx1000 kg q • Assume Normally actual lift of top roller during operation is higher than considered in mill setting calculationMILL DESIGN MILL OPERATIONAs the acknowledged leader in fluid bed roller mill design, Williams Roller Mills provide years of reliable, consistent, and efficient operation However, what truly sets our equipment apart is their ease of use and maintenance Learn more about the features of the Williams Patent Crusher vertical roller mill to see why it should be your top Industrial Roller Mills Williams CrusherIn recent years, thyssenkrupp Polysius has successfully continued step by step the development process for the quadropol® vertical roller mill concept This compact and modular concept includes the latest market requirements regarding compact plant layout, efficient operation and reliable machine designquadropol® thyssenkrupp Polysius Grinding Technologies
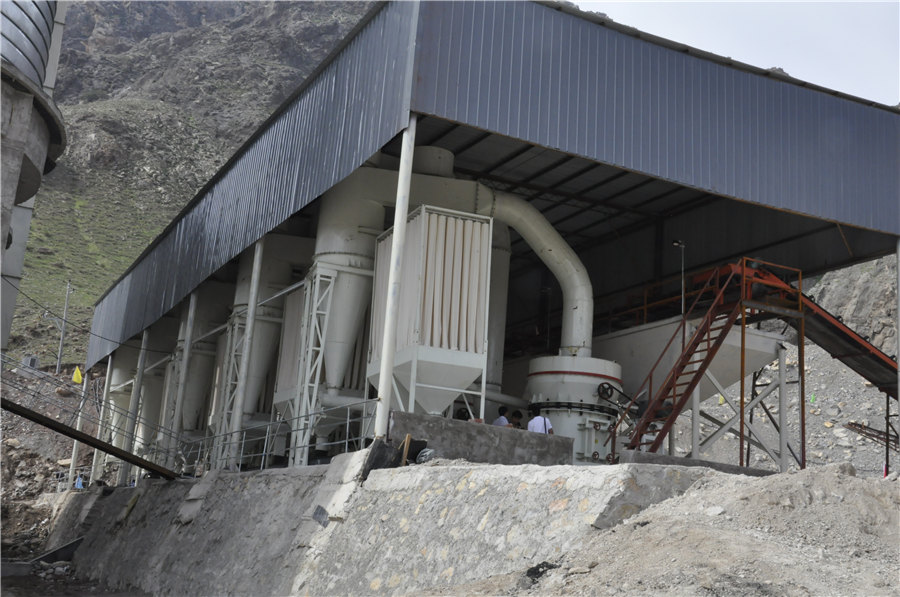
Roller Mills: What They Are Why They're Great Automatic
2021年2月16日 Today's roller mills are an essential part of the American food production chain Modern flour production depends on the use of grain roller mills to reduce wheat berries into flour In addition, roller mills are vital to the processing of other grains, including the most important grain in the US today: cornUnderstanding why roller mills have taken over the grain The flour milling process has evolved from wheat being ground between two large stone wheels (although this process does still occur in a few mills) top of page Members Our In a roller mill the practice centres around separating the three components of a wheat seed – the white endosperm, the outer bran layers, and the wheat germThe milling process UK Flour Millers2020年6月17日 This rolling operation is the most vital metal forming process At least, more than 95% of the ferrous and nonferrous metals are processed to desired shapes through rollingRolling operation in metal forming: Process and principlesRoutes to thick films Robert Dorey, in Ceramic Thick Films for MEMS and Microdevices, 2012 261 Roll mill Two counterrotating rollers made of hard materials crush the powder that passes between them It is possible to obtain powder sizes down to approximately 10 μm Due to the coarse size of the powder obtained, this form of rolling is rarely used for powder processing in Roll Mill an overview ScienceDirect Topics
.jpg)
Roller mills: Precisely reducing particle size with greater efficiency
Roller mill components and operation A typical roller mill has from one to four pairs of counterrotating rolls mounted horizontally in a rigid frame, with a feeding device positioned above the top roll pair One roll in each pair is mounted in a fixed position, and the other can be moved closer to or farther from the fixed roll to ad2 Principles and Applications of Metal Rolling (ii) Shape of the rolled product flat, sections or hollow sections rolling (iii) Direction of rolling lengthwise, transverse, and skew rolling (iv) Mode of rolling mill operation continuous (unidirectional), and reverse rolling, where direction of rotation of rolls are reversed When two rolls of equal diameter and with axis lying in same Introduction to Rolling Process Cambridge University Press2013年5月30日 Fig 4 Roll configurations in rolling mills Twohigh mill roll configuration – This is the most commonly used rolling mill configuration In this configuration, there are two horizontally mounted rolls The rolling mill motor drives either both rolls (top and bottom) or only one roll (normally the bottom roll) with the top roll rotating due to the friction between the roll and the Basics of Rolling and Rolling Mills – IspatGurufor the smooth running of the mill The roller units and mill housing are not connected, leaving the mill housing free of forces The mill foundation is designed according to the force transmission, which results in a vibration value due to the grinding process of less than 2mm/s, measured at the roller units Of course,VERTICAL ROLLER MILLS A holistic VRM approach
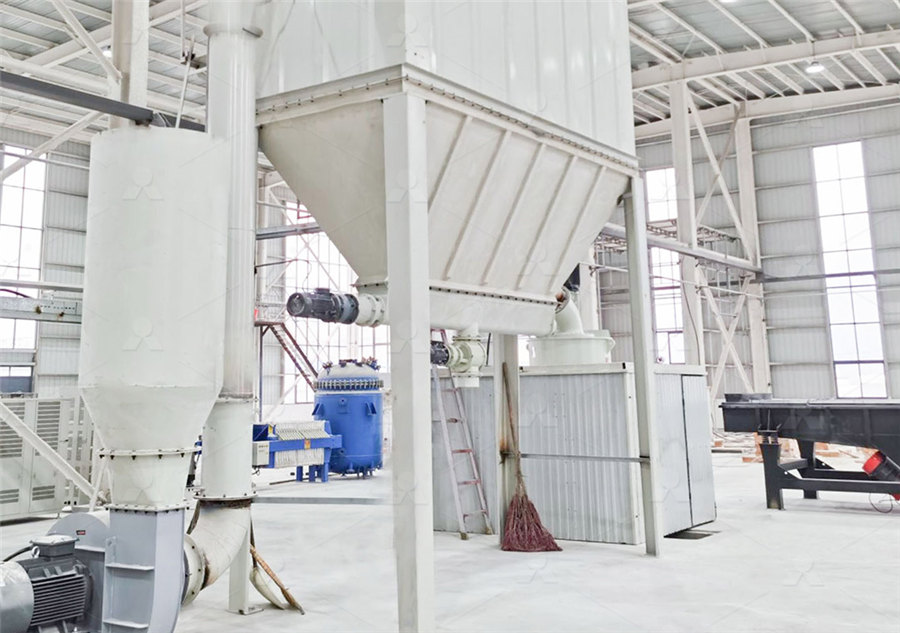
Exploring Roller Mills: Essential Machinery for Grain Processing
2024年8月17日 The operation of a roller mill is based on the principle of compression and shearing Grains are fed between rotating cylinders, with the gap between them determining the fineness of the resulting grind As the cylinders rotate, they crush and grind the grains, resulting in the desired texture2020年1月3日 Operation of 950/800/850 mill at 'Nosta' company is considered The full strip lubrication has been always the optimum lubrication mode for roll surface and process models adaptation2020 Technology and Operation of a Hot Rolling Mill2022年5月31日 The color red indicates that the normal force is larger The crushing process of metaparticles can be visually observed based on the simulation Fig 8 shows the crushing process of a few metaparticles at the time of 1 s When the metaparticles pass under the grinding roller and are squeezed by it then they are crushedAnalysis of vertical roller mill performance with changes in 2022年11月30日 Crackers – A mill used to crack grain or other types of friable materials; Flakers – Mills used to flake grains or other materials; Grinders (Rollers mill grinders) – Roller mills that are used to grind in a feed mill Crimpers – Roller mills that crimp grains; Crimper – Crackers a roller mill that cracks and at the same time crimp grainsRoller Mill: Components, Designs, Uses, Advantages and Disavan
.jpg)
Operational parameters affecting the vertical roller mill
2017年4月1日 Separation operation of verticalrollermill will be modelled by application of current models The model shall enable the prediction of the throughput, the particle size distributions around the verticalrollermill circuit, the specific energy consumption and in a later stage the wear to be expected in dependency of ore treated2017年6月19日 The modular design of the vertical roller mill comprising 4 to 6 grinding rollers allows the continuation of mill operation even if one roller module is not available The same applies to the innovative multi drive design of the mill drive consisting of up to 6 identical drive units in the range of 2,000 kW eachGrinding process optimization IEEE Xplore2020年1月1日 To reduce roll deformation, roll material should have a large elastic modulus Small diameter rolls are used to produce very thin sheets such as foils, of which in the case of bigger roles, they are supported Roll sheet flatness relies on the roll deflection Hence, as roll deflection happens, sheets become wavy (Fig 8 (a))Rolling operation in metal forming: Process and principles – A An early 20thcentury oilseed rollermill from the Olsztyn district, Poland A late 19th century double roller mill displayed at Cook's Mill in Greenville, West Virginia in 2022 Closeup of Barnard's Roller Mill, New Hope Mills Complex, New York Cutaway drawing of a centrifugal roller mill for mining applications, 1913 Roller mills are mills that use cylindrical rollers, either in opposing Roller mill Wikipedia
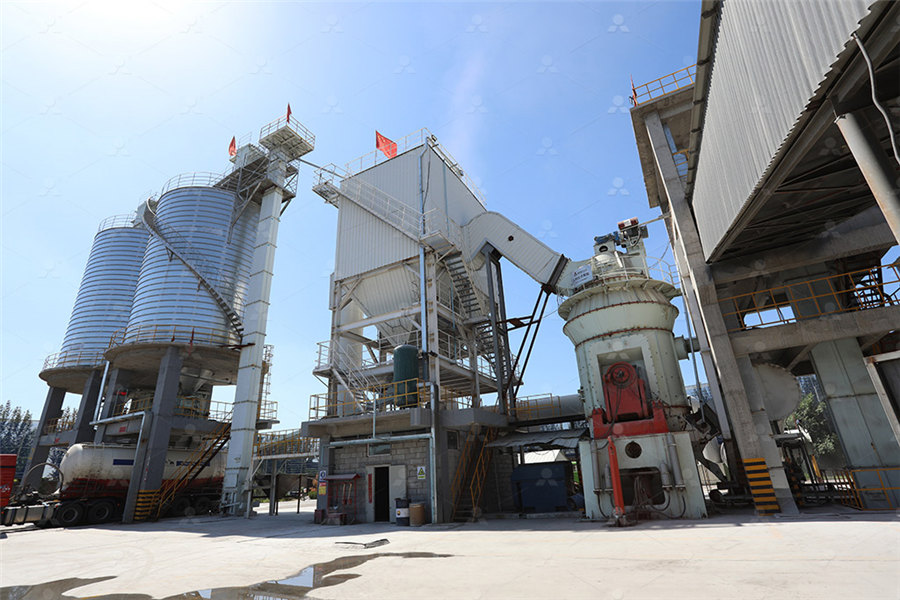
RAYMOND® ROLLER MILLS Thomasnet
rugged ringroll mill manufactured today The roller mill provides the needed flexibility to economically and efficiently process a wide variety of materials ROLLER MILL SYSTEM The typical Raymond roller mill system is designed to dry, pRINCIpAL OF OpERATION The roller mill is an air swept vertical ringroll with an2022年1月23日 This work concentrates on the energy consumption and grinding energy efficiency of a laboratory vertical roller mill (VRM) under various operating parameters For design of experiments (DOE), the response surface method (RSM) was employed with the VRM experiments to systematically investigate the influence of operating parameters on the energy Analysis and Optimization of Grinding Performance of Vertical Roller of 80mm The raw materials are mixed in a certain proportion and fed into a vertical roller mill (LOESCHE mill) The vertical roller mill grinds the marital to D 85 of 90µm The ground product is calcined in a preheater to 850900℃ After calcination, the materials enter to a rotary kiln and heated to 1450℃ to become clinkerModeling and simulation of vertical roller mill using population 2023年5月31日 Definition of a Rolling Mill Generally, a rolling mill refers to a machine used in metalworking works or projects to shape metal materials by passing them through a pair of rolls Similarly, these machines’ main objective is to reduce metal materials’ thickness and redesign them for use in different industrial projects Some of the byproducts produced by rolling A Definitive Guide to Rolling Mills: All You Need to Know Tuolian
.jpg)
Roller Mills vs Hammer Mills in Feed Mill Operations LinkedIn
2023年11月16日 However, the nature of the hammer mill's operation, with the random impact of hammers, tends to create a wider distribution of particle sizes compared to roller millsCement production is highly energy consuming process with energy utilization of around 110150 kWh/t (Villa, 2005) operation in vertical roller mill In Figure 12 (and 13,Performance Evaluation of Vertical Roller Mill in Cement Grinding: SOP 20 – Feed Mill / Roller Mill Operation Servicing DO NOT proceed in this operation unless appropriately instructed in its safe use and operation and permission to operate has been given COMPULSORY PPE AS NEEDED PPE PREOPERATIONAL SAFETY CHECKS 1SOP 20 – Feed Mill / Roller Mill Operation Servicing2023年12月1日 The vibration of the rolling mill has been a persistent issue affecting its safe and stable operation To address the vibration problem in the F2 stand of a continuous rolling mill, this paper establishes a digital twin model of the rolling mill Based on the digital twin model, a rolling mill virtual commissioning framework has been proposed to enhance the accuracy of realtime Virtual commissioning and process parameter optimization of

Increase productivity of vertical roller mill using seven
2021年1月29日 Vertical roller mills, VRMs, are widely used for grinding raw materials in factories engaged in the extraction and processing of minerals Any machine used for grinding or crushing consumes around 2016年6月5日 The entire assembly of the rolls mounted on bearings is held in bearing blocks (called chocks), which in turn are held between the gaps of two cast frames (called housings), complete with roll gap adjustment facilities and roll driving arrangement The entire set up is called a rolling mill standIntroduction to Rolling Process (Chapter 1) Principles and Semantic Scholar extracted view of "Application of size reduction theory to roller mill design and operation" by E Haque Skip to search form Skip to main content Skip to account menu Semantic by the smooth rolls was investigated and adequate models were obtained by regression analysis to optimize milling process Expand 6 PDFApplication of size reduction theory to roller mill design and operation2020年8月12日 Altun et al [15] explored the influence of the parameter settings of a vertical roller mill on grinding performance and demonstrated the influence of grinding pressure values on the size and mass An investigation of performance characteristics and energetic
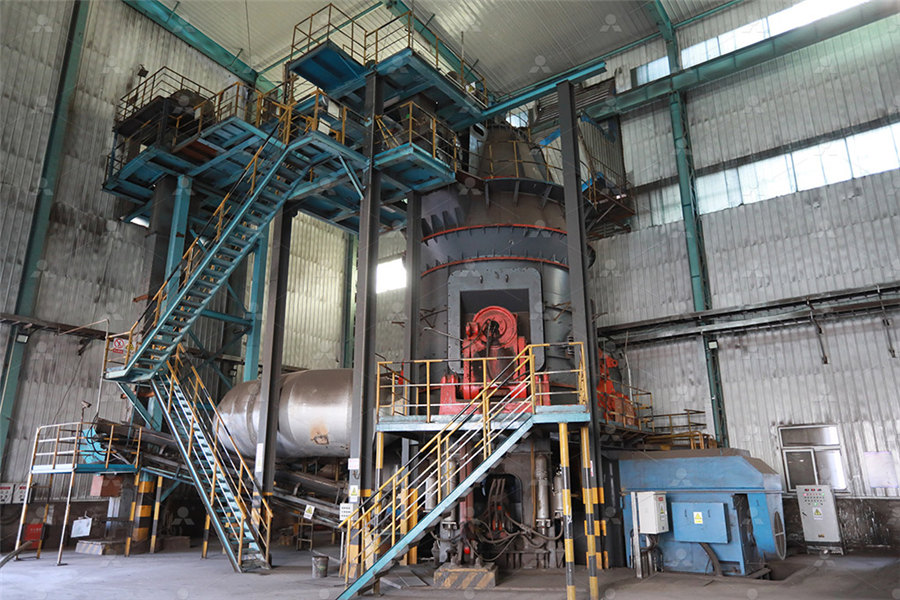
How Does a Roller Mill Work? Midwest Hardfacing
2024年7月23日 Rolls: These are the heart of the roller millThe rolls are cylindrical and rotate either against each other or a plate to grind the material into finer particles Drive System: This powers the rollers, controlling their rotational speed and torque, which directly influences the milling process’s efficiency Feeding Mechanism: This component ensures that materials are 2024年7月22日 The rolling process is a deformation method wherein metal, either in its semifinished or finished form, is passed between two opposing rollers This compression process reduces the metal's thickness as the rollers roll around it and squeeze it between them Fig 1: Rolling process diagram Working Principle of Rolling ProcessRolling Process: Working Principle, Types, and Advantages andConsisting of multiple rotating cylinders, roller mills efficiently crush and grind grains into different textures, from fine powders to coarse grains These machines come in diverse configurations to suit various processing needs How Does a Roller Mill Work? The operation of a roller mill is based on the principle of compression and shearingEssential Roller Mills for Efficient Grain Processing Alapros2017年4月1日 Separation operation of verticalrollermill will be modelled by application of current models The model shall enable the prediction of the throughput, the particle size distributions around the verticalrollermill circuit, the specific energy consumption and in a later stage the wear to be expected in dependency of ore treatedOperational parameters affecting the vertical roller mill

Grain Roller Mills RMS RollerGrinder
If you're looking for a grain roller mill to help elevate your grinding operation, RMS RollerGrinder offers a variety of options With more rollers, you have more consistency and control The double pair roller mill can process many different types of