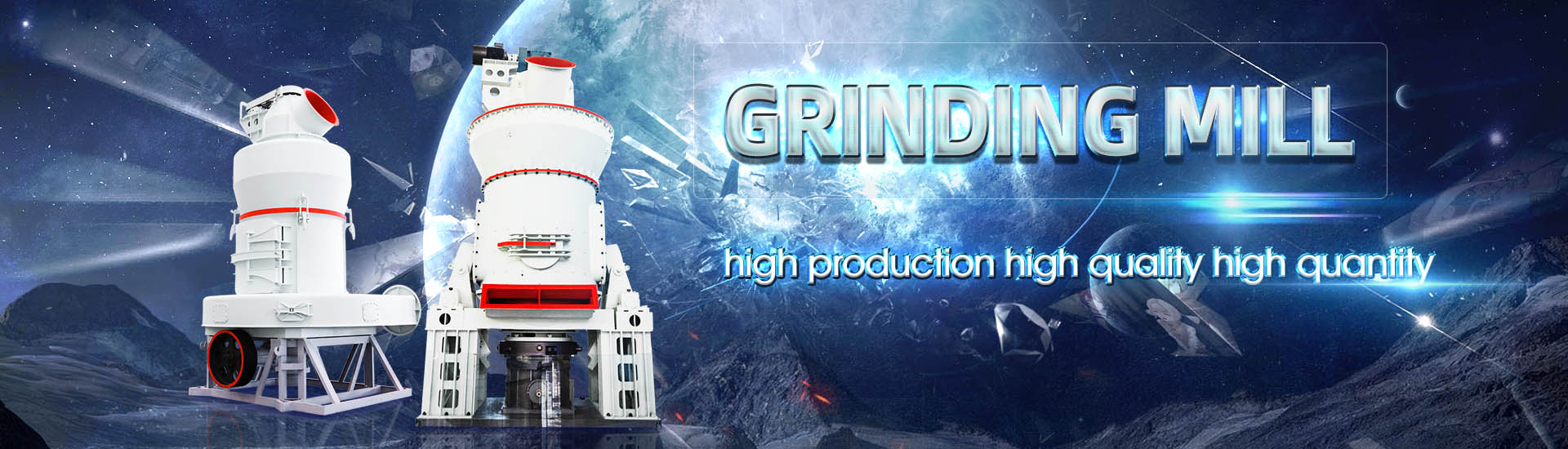
What is the safe distance of mine blasting
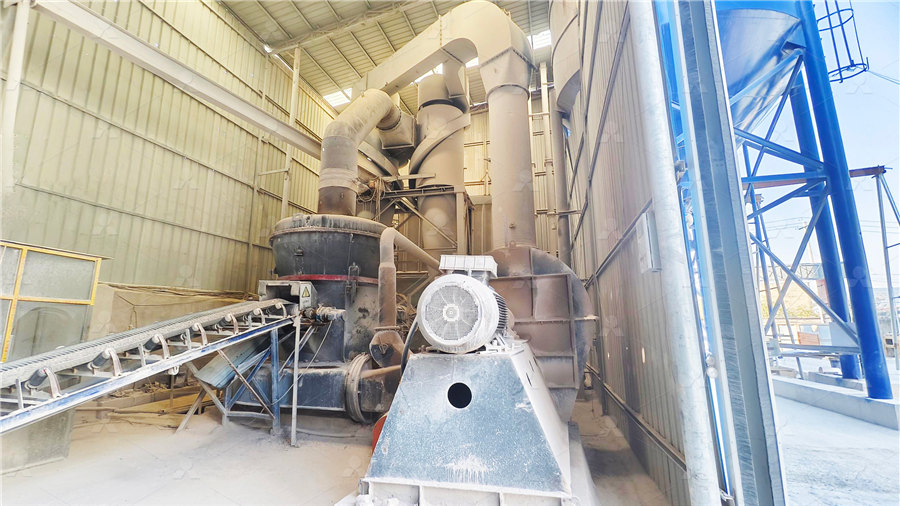
Breaking down the legalities of blasting within 500 m
2020年12月1日 Strict regulations and principles apply when mine blasting is to be conducted within half a kilometre of buildings or areas with any significant The safety distance for blast hazards should be calculated to reduce risk of temporary hearing loss A simple estimated calculation of a blast hazard danger area can be taken from the Estimation of explosion danger areas Mine Action StandardsBlast Exclusion Zone – The area that is determined by the risk assessment process, to ensure that all the potential/foreseen hazards and effects of the blast, are controlled within the Code of Practice BLAST GUARDING IN AN OPEN CUT MININGBlast Area – The area where blastholes are to be charged and fired, and within which access will be restricted to authorised persons, authorised vehicles, or personnel/vehicles under the ONBENCH PRACTICES FOR OPEN CUT MINES AND QUARRIES
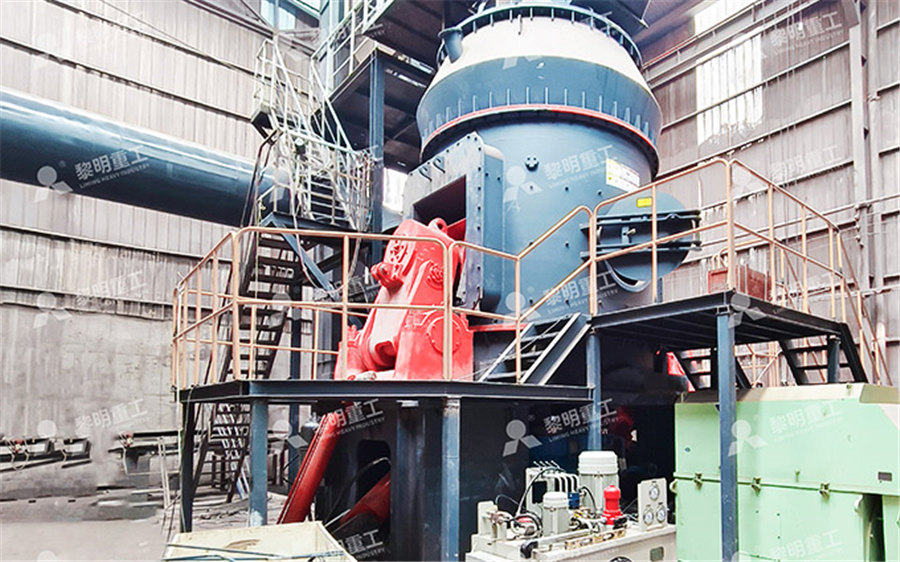
Safe Distance for Blasting Uttam Blastach
Hence, though Indian Regulations Prescribe 500 Meters as the safety distance for Blasting, Regulation 164 of Metaliferrous Mines Regulations of Government of India, allows blasting with certain conditions within the safety distance Rule Guard or barricade all access routes to the blast area to prevent people and vehicles from entering Before firing a blast, give ample warning to allow all persons to be evacuated from MNM Safety Alert Explosive and Blasting Safety Mine Safety 2023年10月26日 The controlled blast design patterns have been developed for the three mines viz Pachhwara (North) Coal Mines, Talabira II III OCP and Chatti Bariatu Coal Mine Project Controlled Blasting Within Danger Zone of 500 M From Dwelling It is the distance by which the face of tunnel is progressed and may be described as distance per blast or distance per unit time (shift, day, week, or month) Pressure pulses in air (often not Blasting Principles
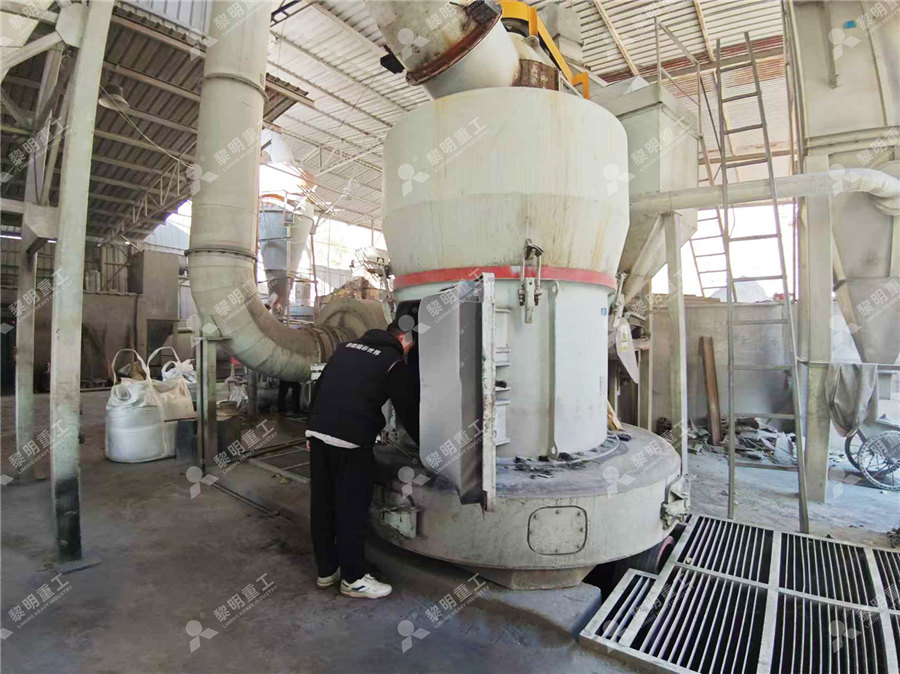
Blasting Safety for Surface Blasting SpringerLink
2016年11月23日 How to estimate the distance that the flyrock may propel is an important issue, as it is the base for determining the safe distance of blasting within which all people should be 2023年4月13日 The potential hazards of blasting include air overpressure, ground vibration, fly rock, noise, dust, and toxic fumes Who is responsible for ensuring blasting safety? Blasting safety is the responsibility of the blasting Blasting Safety in Daily Mining Operations IDENTEC 2022年1月4日 Blasting is accompanied by a number of side effects that have a negative impact on the environment, such as ground vibration, flyrock, AOp, and backbreaks [33, 42]These effects are more severe if they are carried out in close proximity to residential buildings, factories, offices or if they are improperly designed []Proper designing of a blasting operation plays a An Overview of Blasting Operations and Possible Techniques to 2020年12月2日 Strict regulations and principles apply when mine blasting is to be conducted within half a 2018 Regulation 416(2) are clear and should provide a minimum baseline for procedures to ensure safe blasting “This Legal blasting within 500 m of structures Crown
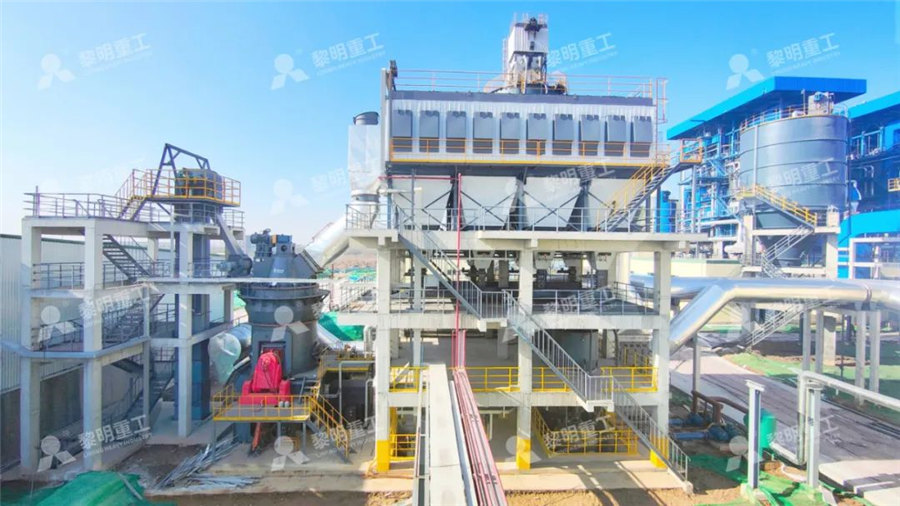
Predicting the peak particle velocity from rock blasting operations
2022年2月3日 Measuring the blastinduced ground vibration at blasting sites is very important, to plan and avoid adverse effects of blasting in terms of the peak particle velocity (PPV) However, the measurement of PPV often requires time, cost, and logistic commitment, which may not be economical for smallscale mining operations This has prompted the development of 2023年2月16日 40 The entire operations of conduct of safe deephole drilling and blasting operations in the mine including transport of the explosive to the site of its use, shall be placed under the overall charge of a competent person holding First class manager’s certificate, hereinafter referred to as “Blasting Officer”, duly appointed in writing by the manager for the Conditions For DeepHole Blasting In Opencast Coal Mine2024年3月27日 Safe Distance: All personnel must evacuate to a minimum distance of 200 meters from the detonation site Whistle Warning: A shrill whistle is blown before initiating the blast using a fuse Skilled Professionals: Only skilled and experienced professionals should conduct blasting operationsThe Ultimate Guide to Drilling and Blasting JOUAV2010年6月9日 1 Introduction In mining engineering, interest is given to the determination of peak particle velocity (PPV) from the amount of explosivecharge (mass) used in blasting (Bollinger 1971, Siskind et al 1980, 1989, Anderson et al 1982, Dowding 1985, Anderson 1993, Persson et al 1994, Muller 1997, Muller and Hohlfeld 1997, Hoshino et al 2000, Siskind 2000, Explosive charge mass and peak particle velocity (PPV)frequency
.jpg)
Determination of Safe Distance While Blasting at Open Pit Mine
Determination of Safe Distance While Blasting at Open Pit Mine Zabrdica, Valjevo Conference paper; pp 749–758; Cite this conference paper; Download book PDF Mine Planning and Equipment Selection Determination of Safe Distance While Blasting at 1999年6月20日 The results also concluded that it is safe to use the proposed modeled blasting designs (1) (2)(3)(4) at the pyrophyllite mine, as the value of PPV is less than 2 mm/s, which cannot affect the ENVIRONMENTAL IMPACT OF MINE BLASTING ResearchGate2023年10月7日 The Different Types of Blasting Blasting methods in rock quarrying include several distinct approaches, each selected based on the specific geological conditions of the site and the desired outcomes of the quarry operation Surface Blasting: This method is employed in openpit quarries and involves detonating explosives at the surface levelWhat is the Role of Blasting in Mining and Quarrying?Contents Related Guidelines + Add to My Handbook; 211 Definitions DIVISION 1 — GENERAL REQUIREMENTS 212 Employer's responsibility 2121 Planning and conducting blasting operations 213 Dangerous incident reports 214 Blasting log 215 Authority to blast 216 Other legislation [Repealed] 2161 General explosives and blasting accessories 2162 Technical DIVISION 1 — GENERAL REQUIREMENTS WorkSafeBC
.jpg)
Practical prediction of blast fume clearance and workplace reentry
11 Mine Development Blasting Blasting with explosives is an essential activity for developing tunnels in most underground hard rock mines, however the process introduces a number of MX6 units) were left at a safe distance of 50m – 100m from the face, and collected after the blast2019年2月19日 Locations of the blasting monitoring points (a) Monitoring points in the À707 m level and (b) Monitoring points in the À647 m level Optimization of blasting parameters for an 2016年6月1日 The minimum safe distance of throw of fragments caused by blast is specified by various codes (2006) based on measurement of vibration caused by bench blasting in an openpit mine in Turkey Nicholson (2005) compared Office of Surface Mines (OSM) Determination of blastinduced ground vibration equations for be expected to increase as the distance to the blast becomes smaller When the distance between the recording point and the blast becomes large enough, there is little the blaster can do to alter the frequency of the vibration The greater the distance from the blast, waves that have traveled different paths arrive at different times and overlapUnderstanding Blast Vibration and Airblast, their Causes, and their

TRANSPORTATION, USE, AND STORAGE OF EXPLOSIVES Mine
blasting site 7 A) Failure to properly tie series B) Lost caps and explosives 8 A) Inadequate wire B) Initiate from testing device 6 RECOMMENDED SAFE JOB PROCEDURES 5 A) Put blasting cap through primer and out other side, and bring the cap in again from the other side Make sure cap is enclosed in primer and cannot be pulled out B) Put 2017年4月15日 The mine blasting expenditure should also Through a properly designed blasting pattern and safe execution, in a mine, The distance from the back row to the line d rill is normally 50 to 75 (PDF) ROCK BLASTING FOR MINING ResearchGate2018年9月26日 R=Distance between vibration monitoring the safe level of vibration has been taken as 10 mm/s for the safety of houses/structures in close proximity of the Jayant Structure response and damage produced by airblast from surface mine blasting US Bureau of Mines, RI 8485, 111 [3] Singh, PK, Vogt, W, Singh, RB, Singh, D Applicability of Controlled Blasting in Large Opencast Mine at The National Green Tribunal in OA No 304/2019, in order dated February 28, 2020 noted that "a report has been filed by the Kerala State PCB on 17122019 reitreating the distance criteria of 50 mtrs, and mentioning that no study is available with the CPCB", and the NGT expressed that "we are of the view, as earlier observed that the distance CPCB report on distance criteria for stone quarrying, 09/07/2020

IS 4081 (1986): Safety code for blasting and related drilling
1986年11月20日 02 Blasting and drilling is a specialized job involving a lot of hazards which often lead to accidents It is necessary, lherefore, that certain safety precautions are laid down for various operations involved in the process of blasting Again, all but the first two factors can be adjusted or designed for by a Blasting Contractor to reduce the amount of flyrock What ODOT and the Blasting Contractor can do to keep ground vibration, airblast, and flyrock at acceptable and safe levels: • Require an approved Blasting Consultant to design/approve the blasting plansROCK BLASTING and the COMMUNITY Oregongov2017年5月8日 the effect of back rows delay timing and size of blast on fragmentation and muckpile shape parameter(PDF) THE EFFECT OF BACK ROWS DELAY TIMING AND 2022年1月19日 PDF Rock damage and vibration attenuation are the basis of blasting design, R is the distance—usually radial—from the measurement point to the blast face (m), (PDF) The Effect of BlastHole Arrangement, Delay
.jpg)
Storage, transportation and handling of explosives in mine action
2024年7月3日 Introduction Managing risk is fundamental to every aspect of mine action The aim of risk management is to identify, assess, control and review risk wherever it may arise, so that mine action programmes, projects and activities are safe, efficient and effective in achieving their objectivesThis guide and its associated templates will assist the mining industry and other blasting operations to prepare a blast plan and records about the blast that address the key requirements of regulations 129, 130 In mining applications, the manager of the mine would have control and management of the miningBlast plan preparation, including mining operations guide(vii) critical charging distance: refers to the distance between adjacent charges that minimises the likelihood of explosive desensitisation or charge interaction This is illustrated later in the text (viii) standoff or offset distance: refers to the distance between a blasthole or toe of a blasthole and an excavation boundary (eg stope or Design methodology for underground ring blasting2003年1月1日 His study aimed at maintaining high wall stability and integrity at the mine On the other hand, Tealeb et al [9][10] [11] carried out an intensive monitoring of blasting ground vibrations and Determination of Safe Distance between Quarry Blasting and
.jpg)
Blasting and Explosives Quick Reference Guide 2010 Minnesota
Presplit blasting Spacing = Hole diameter x 12 Burden = 05 x production blast burden (B) Uncharged length at top = 10 x D Powder factor = 05kg per square metre of face Do not stem holes Fire all holes on the same delay, or in groups of ≥ 5 holes Smooth Blasting Spacing = 15 x Hole diameter (hard rock) 20 x Hole diameter (soft rock)2005年8月1日 This PPV represents the maximum particle velocity recorded throughout the entire time duration of the event (Edwards 1960) (Gad et al 2005) These vibrations possess the potential to induce Effects of Mine Blasting on Residential Structures ResearchGateDOI: 101016/jgsme202408006 Corpus ID: ; Machine learning based prediction of flyrock distance in rock blasting: A safe and sustainable mining approach @article{Taiwo2024MachineLB, title={Machine learning based prediction of flyrock distance in rock blasting: A safe and sustainable mining approach}, author={Blessing Olamide Taiwo and Machine learning based prediction of flyrock distance in rock blasting working bench where blasting is to be carried out unless: i the drilling of shot holes have been completed; ii the shot holes are ready to be charged with explosives; iii the quantity of explosives does not exceed the estimated required quantity to be used for the blast; and iv a safe distance, to which explosives may be brought toEXPLOSIVES REGULATIONS Booklet MHSC
.jpg)
Safe Distance for Blasting Uttam Blastach
Rule #1: There are no Rules! The Rule of Safe Blasting Distance is there are no Rules There are instances where Blasting was done to chisel a sculpture out of a mountain There are also instances of blasting Damage witnessed more than 2021年11月15日 If ΔCp is less than or equal to 10%, it is judged that the blasting is safe and the rock mass is not damaged In our study, blasting tests were carried out on holes 1#, 2# and 3# respectively, and the wave velocity Study on Blasting Technology for OpenPit Layering of Download scientific diagram The safe level blasting criteria from the USBM RI 8507 (Siskind et al, 1980) from publication: Effect of a presplit plane on the frequencies of blast induced The safe level blasting criteria from the USBM RI 年4月12日 Blasting is an economical technique for rock breaking in hard rock excavation One of its complex undesired environmental effects is flyrock, which may result in human injuries, fatalities and property damage Because previously developed techniques for predicting flyrock are having less accuracy, this paper develops a new hybrid intelligent system of extreme A Novel Intelligent ELMBBO Technique for Predicting Distance of Mine

CMR2017 NOTES ON EXPLOSIVE AND SHOTFIRING CHAPTER Mine
2021年8月17日 Comprehensive notes on Chapter 14(Explosives and Shotfiring) of CMR 2017Chapter 14 of Coal Mines Regulations, 2017 deals with provisions regarding Drilling and Blasting In this blog, notes are made by compiling the respective DGMS Circulars for better understanding and quick revision for important exams An attempt is made to make the Determination of Safe Distance While Blasting at Open Pit Mine Zabrdica, Valjevo Slobodan Trajković, Suzana Lutovac, and Marina Ravilić Faculty of Mining and Geology, Belgrade, Serbia Rudarskogeološki Fakultet, Beograd Abstract This paper deals with problems related to the determination of safe distance with special reference to adverse Determination of Safe Distance While Blasting at Open Pit Mine 2022年3月17日 To address the problem of damage to adjacent buildings (structures) caused by bench blasting construction, blasting in a sand and gravel mine in Guizhou Province was used as the background(PDF) Effect Of OpenPit Blasting Vibrations on a ResearchGate2021年12月1日 Based on a review of the previous works for the prediction of flyrock distance using artificial intelligence (AI) techniques (as summarized in Table 1), it has been identified that researchers used the controllable parameters of blasting and several uncertainty parameters of rock mass to predict flyrock distanceMost researchers used a single uncertain parameter for Prediction of flyrock distance induced by mine blasting using a
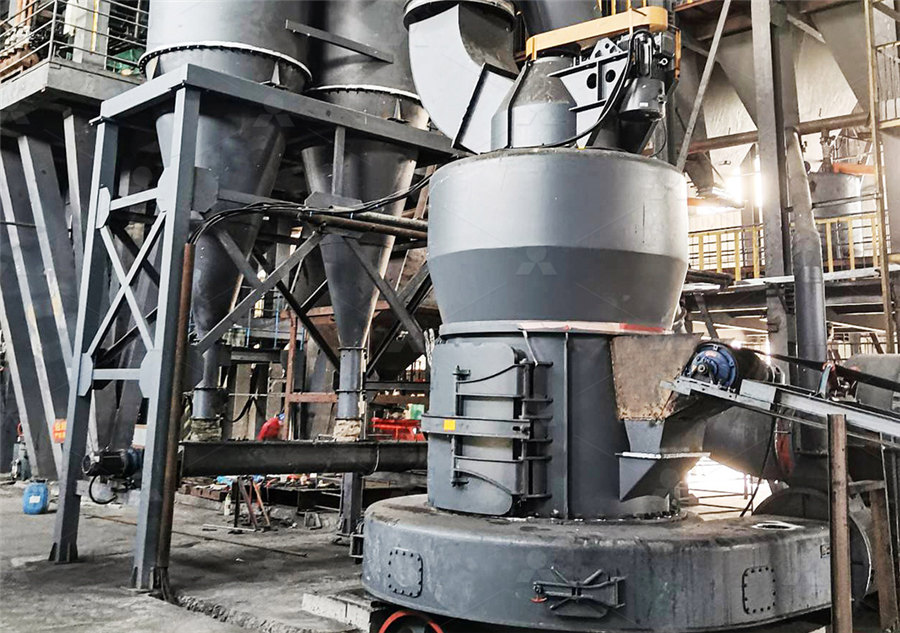
ONBENCH PRACTICES FOR OPEN CUT MINES AND QUARRIES
12 This code does not cover the detailed requirements for the safe and secure storage and transport of explosives and security sensitive materials, as would be described of any scheduled blasting on a mine/quarry site Blast Area – The area where blastholes are to be charged and fired, and within which