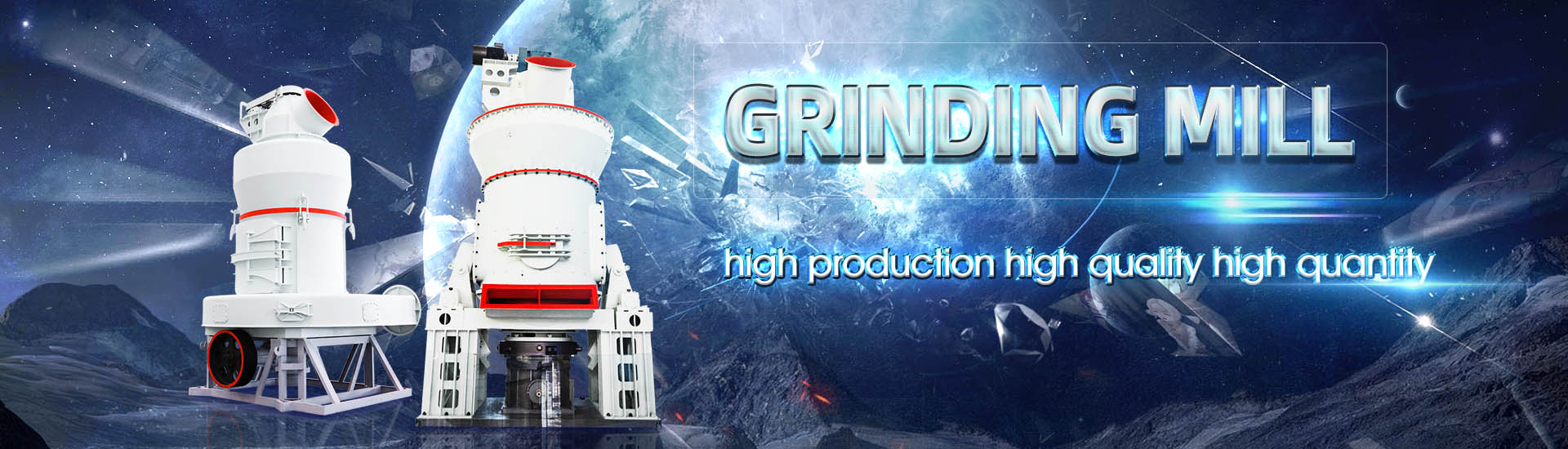
Ore mill manufacturing process
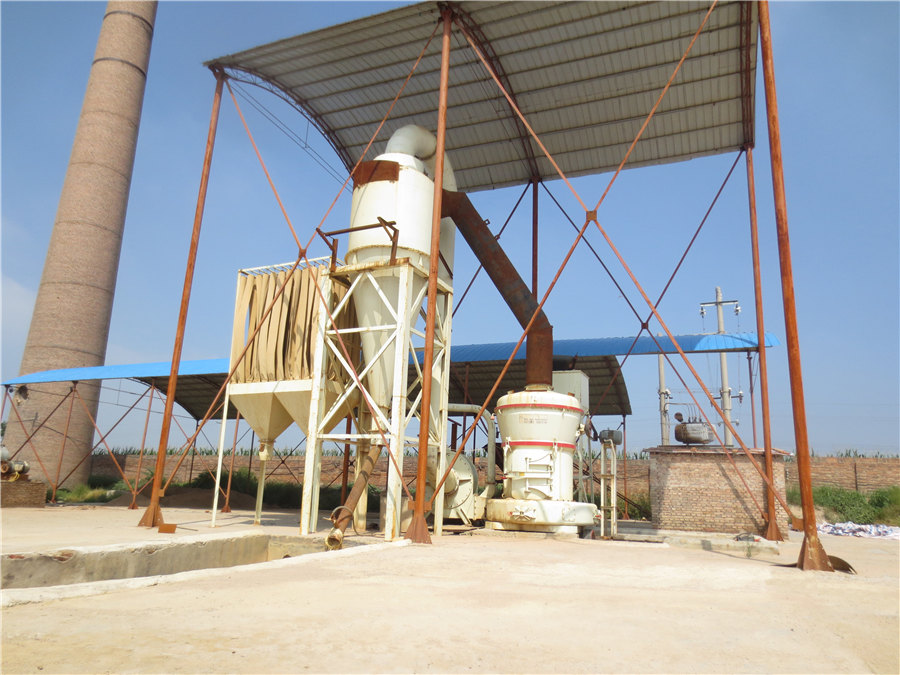
Understanding the Steel Making Process: A Flow
2024年3月20日 The steel making process involves several key stages: preparation of raw materials such as iron ore, coke, and limestone; smelting and reduction to produce molten iron; primary steelmaking which converts molten 2024年4月26日 Iron ore processing is a complex and vital process that transforms raw iron ore into usable steel From exploration and extraction to grinding, beneficiation, and ironmaking, each stage plays a crucial role in Iron Ore Processing: From Extraction to ManufacturingSteel is primarily produced using one of two methods: Blast Furnace or Electric Arc Furnace The blast furnace is the first step in producing steel from iron oxides The first blast furnaces appeared in the 14th century and produced one ton Steel Production American Iron and Steel Institute2017年7月20日 Steel production consists of three major steps: Ironmaking—From Ore to Iron The iron ore to steel process flowline can follow several different paths Steelmaking begins by the processing of iron ore The Technology and Processes Behind Steel Production
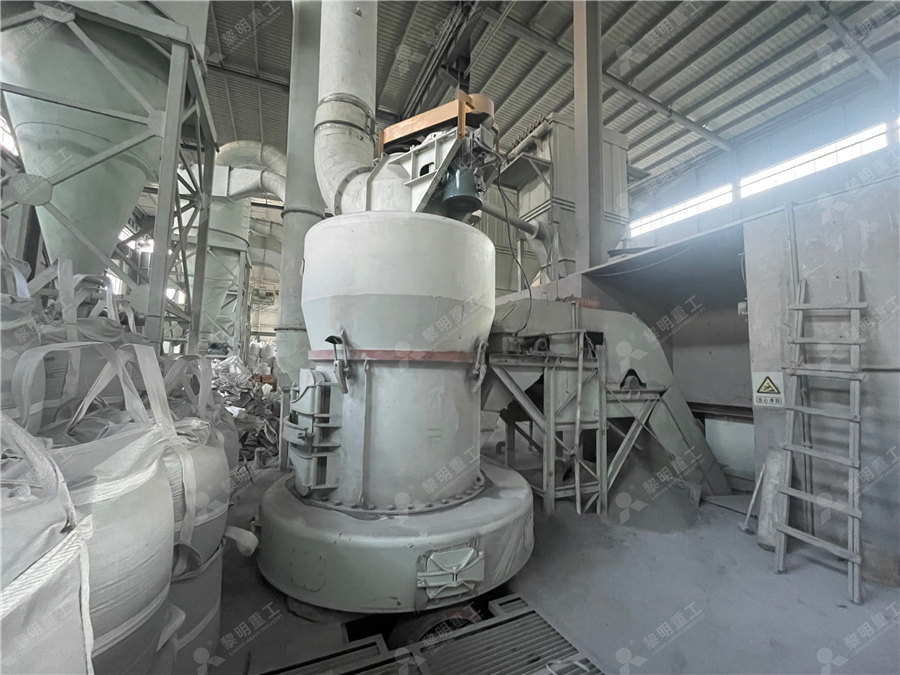
Steel Manufacturing: Process, Types, and Standards
2024年5月13日 The steel production process is a multifaceted journey that begins with extracting and processing iron ore, a primary raw material essential to steel making Iron ore undergoes a series of refining steps to extract the iron The smelting and refining process for iron and steel in the BFBOF process involves the carbon reduction of iron ore (Fe 2 O 3) in the BF to make molten iron, and decarburization of molten 1A Manufacturing Process for Iron and SteelSteel is manufactured by the chemical reduction of iron ore, using an integrated steel manufac turing process or a direct reduction process In the conventional integrated steel manufacturing Iron and Steel Manufacturing International Finance Corporation2017年10月17日 Ironmaking is a critical step in producing high performance steel because highquality raw materials reduce the time and energy to purify the iron to steel On the other hand, newer smelting and direct iron reduction From Ore to Iron with Smelting and Direct Iron
.jpg)
(PDF) ironsteel making From start to finish
PDF On Dec 27, 2019, Mr Bhavesh R Rana published ironsteel making From start to finish Find, read and cite all the research you need on ResearchGate2024年9月10日 Learn about the Cement Manufacturing Process including dry and wet processes and know the manufacturing process involves the extraction and preparation of raw materials, such as Limestone, clay, shale, iron ore, and Cement Manufacturing Process: Know Extraction, Stage of Cement Manufacture There are six main stages of the cement manufacturing process Stage 1: Raw Material Extraction/Quarry The raw cement ingredients needed for cement production are limestone (calcium), sand and clay (silicon, aluminum, iron), shale, fly ash, mill scale, and bauxite The ore rocks are quarried and crushed into smaller pieces of about 6 inchesHow Cement is Made Cement Manufacturing ProcessQuality rolling mill that gives the uniform and proper shape for all rebars; Quality system for quenching and tempering; Iron Ore to Steel Raw material for manufacturing the TMT Bar are iron ore, coal, dolomite In this process raw materials are piled, recovered and mixed in Manufacturing Process of TMT Bar Shyam Steel
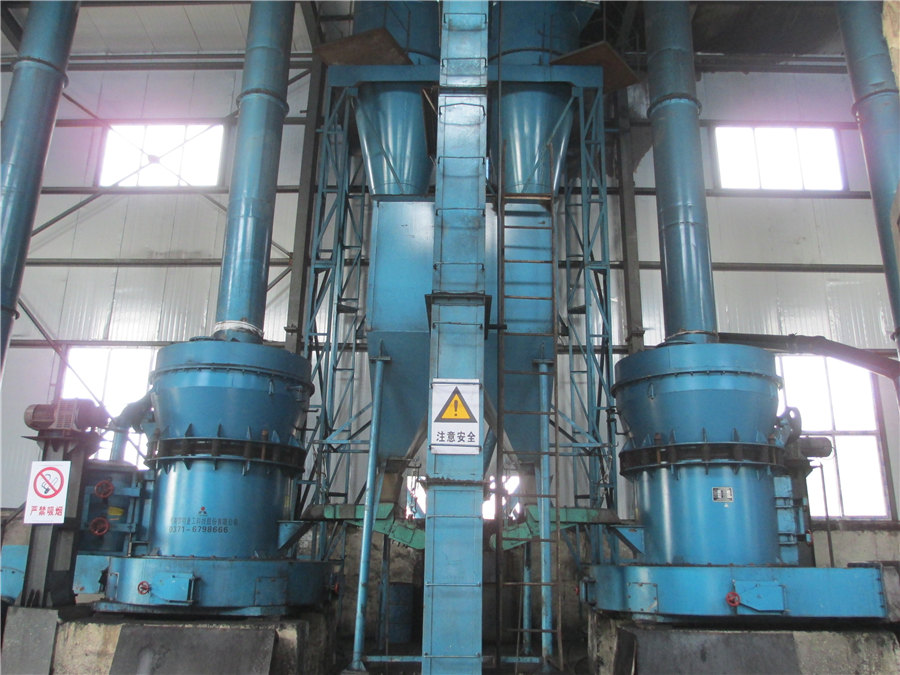
Introduction to Mineral Processing or Beneficiation
Within an ore body, valuable minerals are surrounded by gangue and it is the primary function of mineral processing, to liberate and concentrate those valuable minerals 13 RunOfMine Material and Minerals Generally, mineral processing begins when an ore is delivered from a mine, to a processing facility2023年7月10日 Cement manufacturing is a significant industrial activity that plays a vital role in the construction sector However, the process of cement production is associated with various environmental Cement Manufacturing Process and Its Environmental ImpactIron ore has a sandlike structure that can put out the fire in the furnace Because of that, you can't put it in the furnace just like that The ore is first baked to make it into porous chunks, or sinters This is done in the Sintering Plant In the Pelletising Plant, we turn the fine ore into small balls in large drumsProcess of steelmaking Tata SteelSteel mill with two arc furnaces Steelmaking is the process of producing steel from iron ore and/or scrapIn steelmaking, impurities such as nitrogen, silicon, phosphorus, sulfur, and excess carbon (the most important impurity) are removed from the sourced iron, and alloying elements such as manganese, nickel, chromium, carbon, and vanadium are added to produce different Steelmaking Wikipedia
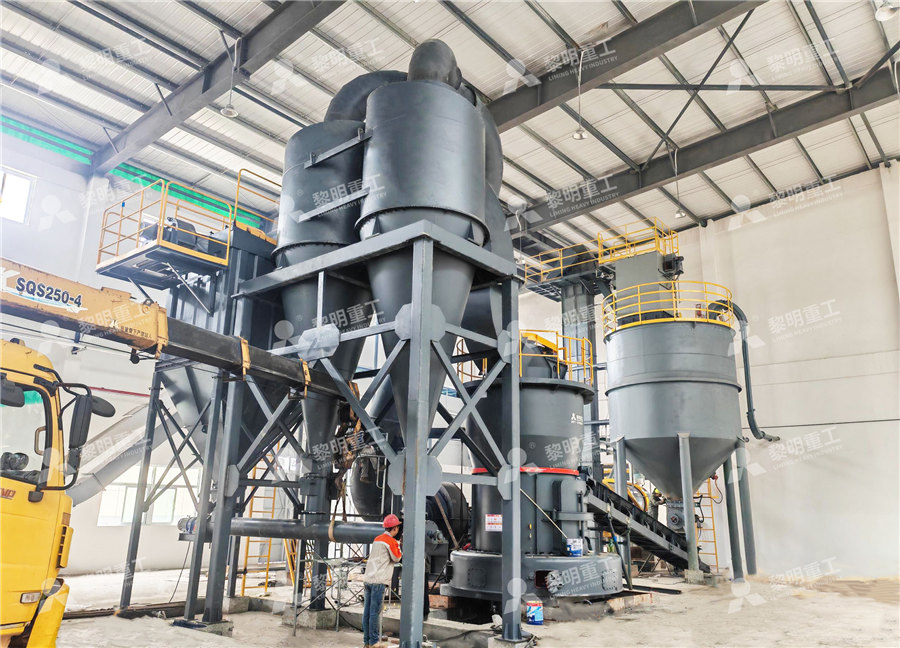
Mineral processing Wikipedia
Crushing, a form of comminution, one of the unit operations of mineral processing Mineral processing is the process of separating commercially valuable minerals from their ores in the field of extractive metallurgy [1] Depending on the processes used in each instance, it is often referred to as ore dressing or ore milling Beneficiation is any process that improves (benefits) the The rod mill is another type of grinding mill used in the copper ore mining process This machine uses steel rods as the grinding media instead of balls, which are commonly used in ball mills The rods grind the ore by tumbling within the mill, similar to the action of a rotating drumUnderstanding the SAG Mill in Copper Ore Mining Process2016年3月30日 In book: Encyclopedia of Iron, Steel, and Their Alloys (pppp 10821108) Chapter: i) Direct Reduced Iron: Production; Publisher: CRC Press, Taylor and Francis Group, New York(PDF) i) Direct Reduced Iron: Production2014年6月10日 Cement manufacturing process Download as a PDF or view online for free Submit Cement manufacturing process – Sand (SiO2) – Shale, Clay (SiO2, Al2O3, Fe2O3) – Iron Ore/Mill Scale (Fe2O3) 10 Portland Cement manufacturing process PPT Free Download
.jpg)
Zeolite Manufacturing The manufacturing Process
Learn about the Manufacturing Process of Zeolite Zeolite Manufacturing by IdaOre Bulk Zeolite mining and supplier Call at 2085156966MillOre Industries is an engineering based manufacturing company We manufacture and remanufacture mineral processing systems to suit specific design Our niche business is combining new, used and reconditioned equipment into our plant design which reduces our clients' capital investmentMillOre Products Inc Mining Life Online2019年6月11日 World resources are estimated to be greater than 800 billion tons of crude ore containing more than 230 billion tons of iron The only source of primary iron is iron ore, but before all that iron ore can be turned into steel, it must go through the sintering process Sinter is the primary feed material for making iron and steel in a blast furnaceSintering: A Step Between Mining Iron Ore and Steelmaking2019年7月1日 Simulation of casting process: case study on the gating and feeding design for outlet diaphragms of iron ore ball mill July 2019 Heat and Mass Transfer 55(7):1959–1967(PDF) Simulation of casting process: case study on the gating
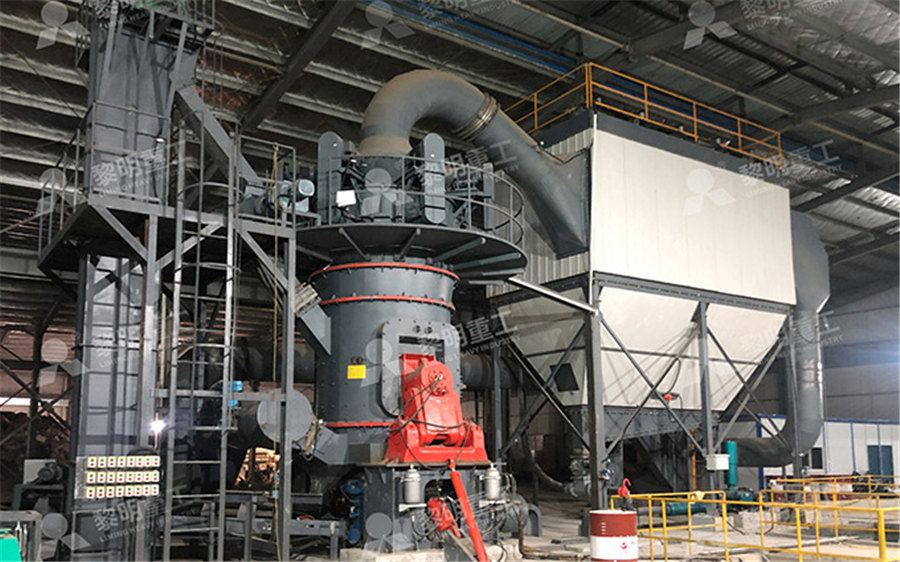
How is Steel Made? Steel Production Process – What Is Piping
There are two processes by which steel is produced in a blast furnace The Bessemer Process for Steel production and; The Open Hearth Process of Steelmaking; Steel manufacturing Principle of the Bessemer Process The main raw materials for Steel production in a blast furnace are Iron ore, limestone, coke, and some scrap steel2024年1月4日 Steel manufacturing is a complex process that transforms iron ore into steel, involving precise heating and mixing to create different grades for various applications The journey includes primary methods like Basic Oxygen Steelmaking BOS and Electric Arc Furnace EAF, followed by secondary refining to meet specific quality standardsExploring Steel Manufacturing: A StepbyStep Insider GuideThe ingredients – iron ore, coke and limestone fines – are carefully stacked and blended, then passed under an ignition hood at the sinter plant This heating process is carefully controlled to make sure the resulting sinter has the right composition and optimum sizes for the next stage of the process at the blast furnacesHow we make steelManufacturing process flow 1 Quarrying and Crushing The quarry (where the mining activity is performed) is located 07 km away from the plant and has the main raw materials such as Limestone and shale that is estimated to last for 100 years, the other raw materials (Iron ore, silica sand, gypsum and Pozzolana (pumice) ) are brought from nearbyManufacturing process flow 1 Quarrying and Crushing
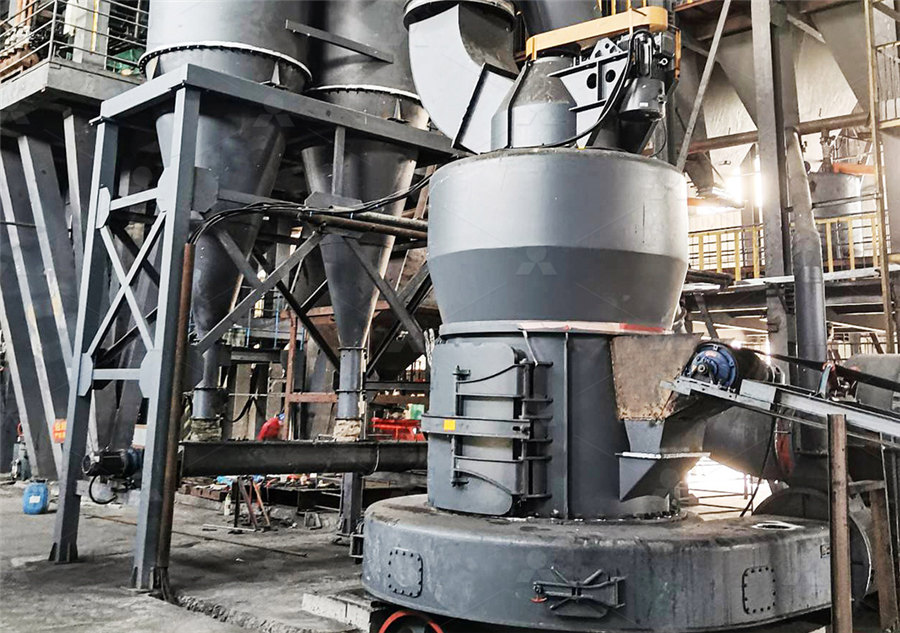
Understanding the Manufacturing Process of TMT Bars
2023年5月3日 As the proverb goes, knowledge is power And TMT bars reflect the same The knowledge of its manufacturing process helps you in a way that is of paramount importance TMT bars have become the goto solution or the Steelmaking process can generally be classified into four main different routes including blast furnace/basic oxygen furnace (BFBOF), direct reduction/electric arc furnace (DRIEAF), smelting reduction/basic oxygen furnace (SRBOF) and melting of scarp in electric arc furnace (EAF) Fig 1 shows the various steel production routes from the raw materials to the crude steel Steelmaking Process an overview ScienceDirect Topics2023年7月6日 Alluvial tin ore is separated by the gravity separation method For alluvial tin ore with a high degree of monomer dissociation, the final concentrate is obtained by the 6S shaker tables at one timeThe concentrate grade is above 60% For alluvial tin ore with a low monomer dissociation degree, use a jig machine for primary selection, then concentrate enters 6s TIN ORE PROCESSING PLANT Pineer Mining Machinery2021年11月5日 Today, Metso Outotec can offer processes and equipment that cover the full gold value stream from ore to dore This includes all three main oxidative processes for the treatment of refractory gold concentrates – BIOX, pressure oxidation, and roasting – as well as the equipment for ultrafine grinding as a fourth, nonoxidative treatment optionFrom ore to dore: Four main processes in gold production
.jpg)
What is Mill Liner Manufacturing? Beyond The Net
2024年7月10日 The manufacturing process of mill liners involves several key steps Initially, the design phase is critical, as it determines the liner’s shape, size, and material composition, tailored to specific milling conditions and ore types2024年7月8日 In the ball mill, the ore is crushed into fine particles to a size that will The future trends in oxidized gold ore processing will no doubt present new opportunities and challenges for the Established in 1985, JXSC has more than 30 years’ experience in mining equipment manufacturing, offering stone crushers, gravity Mastering Oxidized Gold Ore Processing Techniques JXSCMultotec South Africa helps mineral processing plants maximise efficiency to optimise their cost per ton targets agile manufacturing, distribution and turnkey plant services In addition to manufacturing facilities in Kempton Park unbiased mineral samples of ore with our wet, primary and secondary dry sampling solutions Read moreMultotec South AfricaFrom the time that the ore hoisted from underground and enters the processing plant, it takes up to five days before the process of smelting into gold bars can commence South Deep’s gold plant has the capacity to process around 330,000 tonnes of ore per month and the capability to treat more underground ore than most other plants in the Far West Rand Region of South AfricaGold Fields South Deep Gold Mine How we process
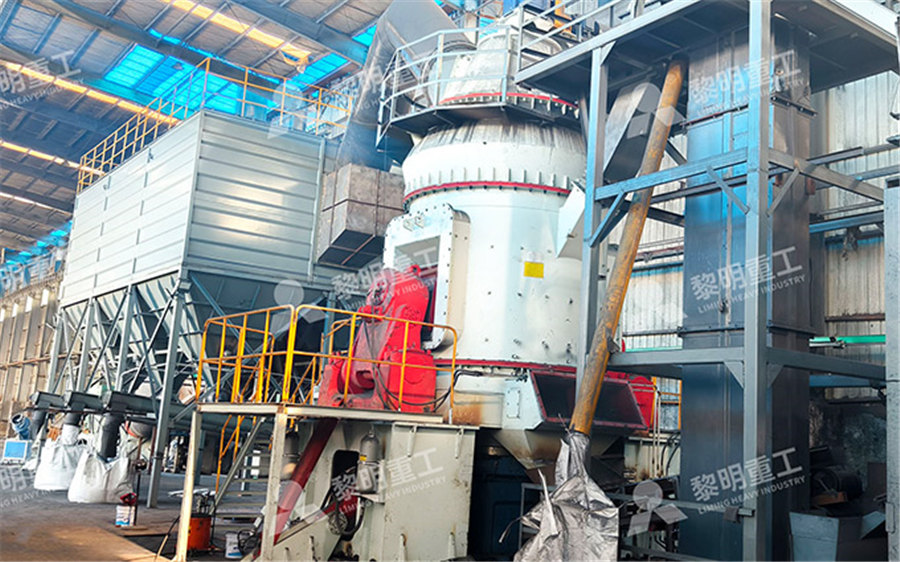
Copper Production: How Is Copper Made? ThoughtCo
2019年9月26日 Here's information about the modern manufacturing process of copper and how much is generally produced The first step in this process is crushing and powdering ore in a ball or rod mill Sulfide Copper Ores Virtually all sulfide Guide to Modern Smelting Processes – T09002 7 Use of Retorts in Ancient Smelting Processes Figure 2 Ancient Retort An ancient retort (see image above), used in ancient smelting processes, served several important purposes: 1 Ore Concentration: Retorts were used to concentrateGuide to Modern Smelting Processes CED EngineeringThe blast furnace turns the iron ore into pig iron, the chief ingredient used to make the steel Rolling is the process by which billets are converted into sheets with thicknesses ranging from less than 1 mm to 400 mm JFE's rolling Production Process and Products JFE Steel 2023年4月16日 Steel manufacturing is a complex process that involves numerous stages, from mining and refining iron ore to creating finished products Each step requires precision, expertise, and stateoftheart technology to The Fascinating Journey of Steel Manufacturing
.jpg)
Australian Steel Institute Steel Manufacturing in Australia
Steelmaking begins when iron ore is smelted to produce metallic iron, which is then converted to steel by removing excess carbon and adding various alloys in a Basic Oxygen Furnace It is then continuously cast and rolled into a variety of shapes and sizes Hot rolled steel is produced for various uses; eg welded beams, reinforcing bar and floor plate2023年9月1日 The Effects of Chemical Elements on Steel Properties 1 Carbon (C): As the carbon content in steel increases, the yield point and tensile strength rise, but plasticity and impact resistance decrease When the carbon content exceeds 023%, the weldability of the steel deteriorates Therefore, for lowalloy structural steel used for welding, the carbon content Steel Production Process: The Comprehensive GuideInteractive Steel Manufacturing Process AIST’s Making, Shaping and Treating of Steel ® Wheel AIST has collaborated with Purdue University Northwest’s Center for Innovation Through Visualization and Simulation to create a unique, interactive experience of the steel manufacturing process This oneofakind experience allows you to click on each phase of steelmaking and Steel Manufacturing Process Association for Iron Steel Mine to Mill, which links aspects of mining and mineral processing in order to optimise the combined mining and processing stages, has been under development and use for the last 20 years Implemented effectively, numerous operations have experienced productivity gains from Mine to Mill in the range of 1020%UNDErsTaNDINg MINE TO MILL 911 Metallurgist
.jpg)
How to Process Talc (the Softest Mineral)? FTM Machinery
2023年2月15日 Talc chemical formula: Mg 3 Si 4 O 10 (OH) 2 Talc hardness: 1 on Mohs scale Color of talc: Talc minerals are colorless, white, green, brown or gray Talc powders are white or gray Transparency: Translucent Talc luster: Vitreous and pearly Morphology: Euhedral crystals are extremely rare, usually found in platy, foliated to finegrained compact masses, sometimes Find your ore mill easily amongst the 42 products from the leading brands (Fritsch GmbH, Retsch, Eriez By the late 1990s the HPGR became standard equipment for processing iron ores Successful hard rock mining installations followed about a decade later and HPGR applications Compare this product Remove from comparison tool See the Ore mill, Ore grinding mill All industrial manufacturers2023年3月13日 The process of extracting iron ore involves mining, where largescale excavation is carried out to access the ore deposits deep within the earth Once the iron ore is extracted, it undergoes a series of processing steps to remove impurities and prepare it for further useManufacturing Process From Ore To Stainless Steel: A Stepby