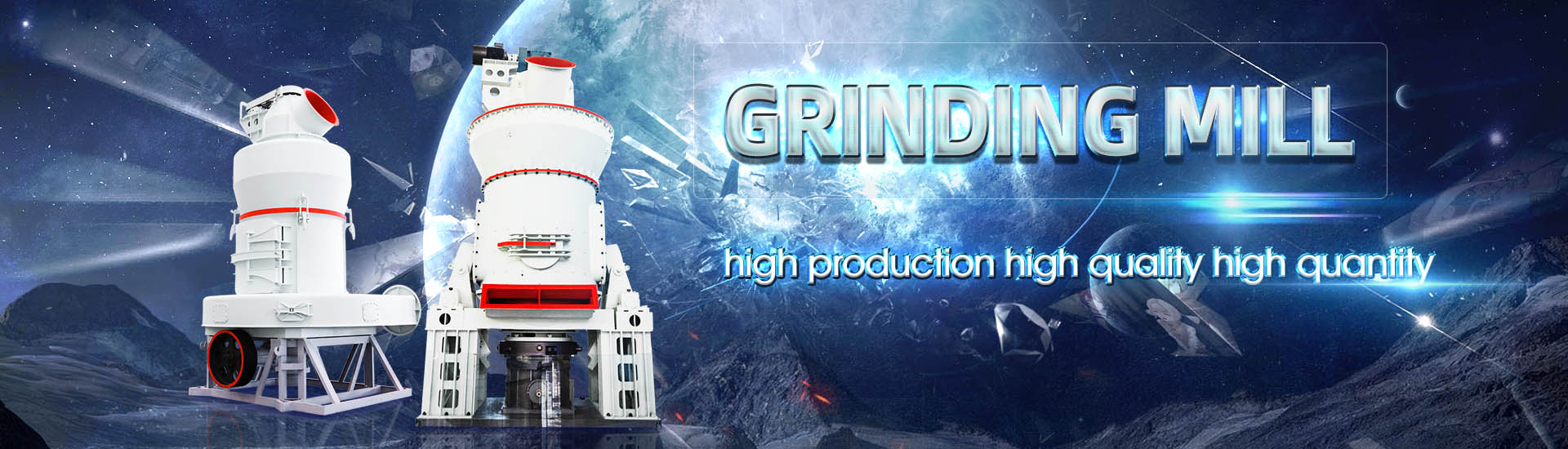
HOME→What ore grinding machine does the cement plant use What ore grinding machine does the cement plant use What ore grinding machine does the cement plant use
What ore grinding machine does the cement plant use What ore grinding machine does the cement plant use What ore grinding machine does the cement plant use
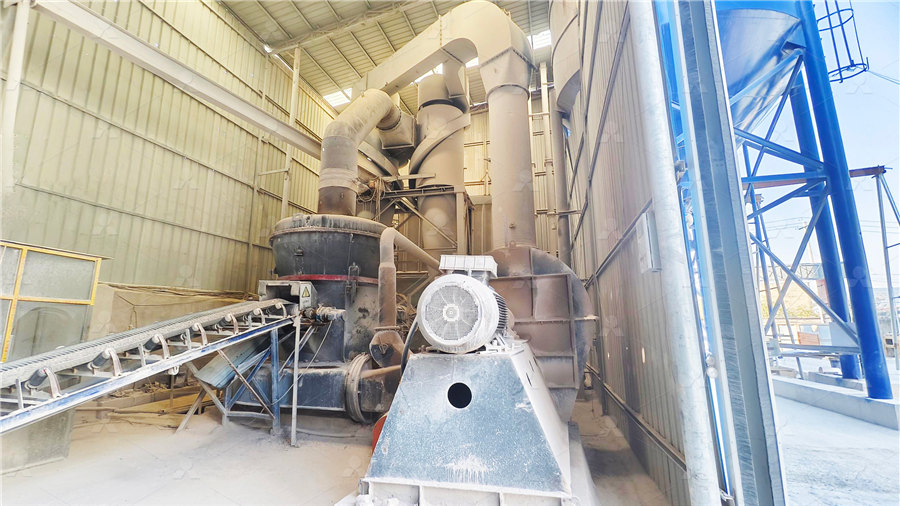
Clinker grinding technology in cement manufacturing
2019年1月3日 Clinker grinding technology is the most energyintensive process in cement manufacturing Traditionally, it was treated as "low on technology" and "high on energy" as 1 Prepare cement raw materials: The primary raw materials are limestone and clay, along with fly ash, iron ore, and coal 2 Grinding: The raw materials are ground into fine powder (1–25 mm) Overview of Cement Making Machine (with Price and Capacity)Production Capacity: 50250t/h Feeding Size: ≤1100mm Application: feldspar, calcite, talc, barite, fluorite, rare earth, bentonite, marble, limestone, bauxite, manganese ore, phosphate Vertical Cement MillHow does the cement grinding plant work? Clinker, gypsum and admixture – the three components are mixed in a certain specific proportion and transported on the belt conveyor to Cement Grinding Unit Process High Quality Cement Grinding
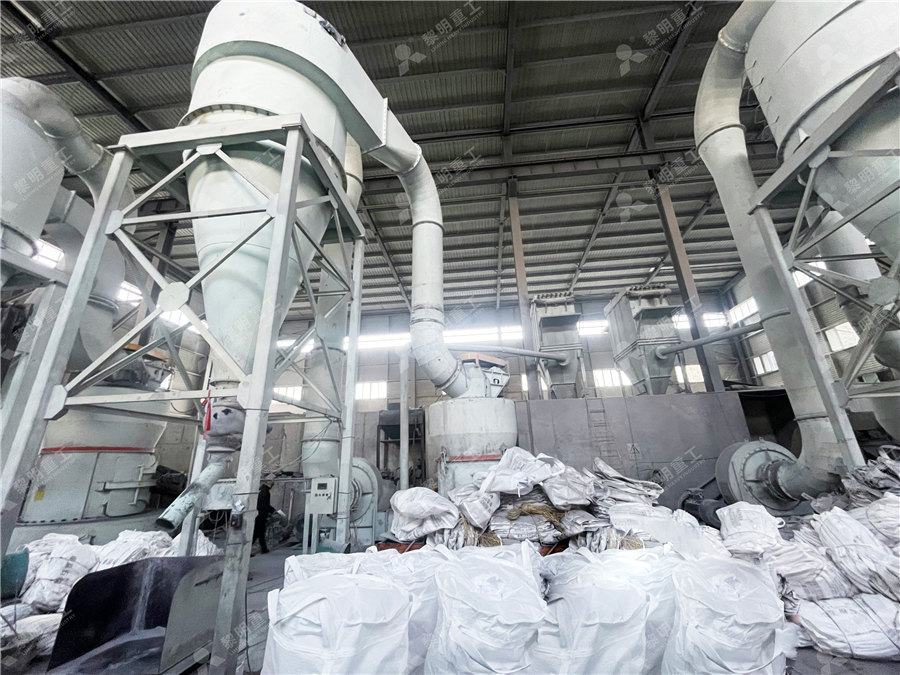
Cement grinding optimisation ScienceDirect
2004年11月1日 Precrushing of cement clinker using a Barmac crusher offers realistic benefits to a cement plant in terms of process efficiency The introduction of the Barmac crusher can 2017年5月19日 PDF Grinding is an essential operation in cement production given that it permits to obtain fine powder which reacts quickly with water, sets in few Find, read and Overview of cement grinding: fundamentals, additives, technologiesAt the Cement Grinding Stage, 90 – 95% of the clinker is mixed with gypsum and ground in a Cement Ball Mill to produce quality cement OPC 43 and OPC 53 In case of PPC Cement, there is an addition of Fly AshCement Grinding Unit Process High Quality 2019年9月27日 A cement mill is also applied for grinding clinker into finished cement The cement clinker grinding is the last step of the cement manufacturing process, in this step, cement mill grinds cement clinker, gelatinizing agent and Cement Euipment Overview Cement Making
.jpg)
Cement Conveyor Belt Conveyor In Cement Plant
Cement conveyor refers to a belt conveyor in cement plant, which is necessary accessory equipment in the cement production line A belt conveyor is a kind of material handling equipment with strong adaptability, applied for conveying As a leading cement plant builder, AGICO offers an expert cement grinding plant EPC service Cement Grinding Unit EPC Solution With a strong RD team, experienced engineers, and firstclass technical services, we aim to provide users with the most advanced and optimized cement production solutionsCement Grinding Plant Expert Cement Grinding Solutions from 2019年1月3日 Clinker grinding technology is the most energyintensive process in cement manufacturing Traditionally, it was treated as "low on technology" and "high on energy" as grinding circuits use more than 60 per cent of total energy consumed and account for most of the manufacturing cost Since the increasing energy cost started burning the benefits significantly, Clinker grinding technology in cement manufacturing2024年1月27日 How Much Does a Grinding Machine Cost? The cost of grinding machines varies widely based on type, capacity, and features Here’s an overview of average price ranges in USD: Manual Bench Grinders: Typically cost between $50 – What is a Grinding Machine: Definition, Types, Components
.jpg)
Key factors in setting up a cement plant Indian Cement Review
2020年1月3日 Setting up a cement plant is both time and capital intensive; it could take anywhere between five to seven years from concept to commissioning and an investment of around to Rs 1,8002,000 crore for a typical integrated plant of 3 million tpa cement capacity Size of a cement plant could vary from 02 million tpa to 50 million tpaThen they will fully complete the calcination and be transferred into clinker in the cement kiln Cement Grinding Mill Cement grinding is the final step of cement production We will grind the clinker to a specific fineness to reach the cement product requirements In this cement production line, we adopt the Φ42×13 cement ball mill Cement Making Machines – Cement Plant AGICO Cement2024年8月15日 Widely used for fine grinding; can operate in dry or wet modes based on process requirements High Rod mill: Largersized ores Ideal for coarse ore grinding, preventing overgrinding Low Autogenous mill: Very hard, highly abrasive large ores Uses the ore's impact for grinding, reducing wear on equipment and grinding media LowMineral Processing Plants: What You Need to Know2023年7月10日 to the cement plant, where they und ergo crushing, grinding, and blending to create a uniform raw mix [6] This process ensures that the raw materials a re properly proportioned andCement Manufacturing Process and Its Environmental
.jpg)
Cement Crusher – Crusher In Cement Plant AGICO
Raw materials of the cement plant are mostly from openpit mines, and the ore usually has a large particle size In the preparation of cement raw materials, we first need to crush limestone, gypsum, clay, and other materials into proper As a leading cement plant builder, AGICO offers an expert cement grinding plant EPC service Cement Grinding Unit EPC Solution With a strong RD team, experienced engineers, and firstclass technical services, we aim to provide Cement Grinding Plant Expert Cement Grinding The Cement Plant Operations Handbook SEVENTH EDITION The Cement Plant Operations Handbook is a concise, practical guide to cement manufacturing and is the standard reference used by plant operations personnel worldwide Providing a comprehensive guide to the entire cement production process from raw materialThe Cement Plant Operations Handbook International Cement What Is A Cement Ball Mill The cement ball mill is a kind of cement grinding millIt is mainly used for grinding the clinker and raw materials of the cement plant, and also for grinding various ores in metallurgical, chemical, and electric power enterprisesIt has the characteristics of strong adaptability to materials, continuous production, a large crushing ratio, and easytoadjust the Cement Ball Mill Cement Grinding Machine Cement Mill
.jpg)
Cement Packing Machine – Rotary Cement Packing Machine Cement
Cement Packing Machine Structure The BX rotary cement packing machine is mainly composed of a feeding device, main transmission device, power supply system, rotary bin, weighing mechanism, cylinder control mechanism, cone intermediate disc, dust collecting plate, bagging weighing frame, electric control system, and other parts2024年9月20日 2 Impact crusher The impact crusher can process materials with a side length of 100500 millimeters or less, with a maximum pressure resistance of 350 MPA It has the advantages of a large crushing ratio and with cubic material particles This machine is widely used in building materials, ore crushing, railways, highways, energy, transportation, cement, mining, How Does The Graphite Grinding Plant Process?In recent years, the tube mill has gradually been replaced by roller mill and other equipment, became the main equipment of cement grinding in cement cement manufacturing plant While in raw meal grinding, with the mature use of vertical mill and roller mill, the power consumption of grinding one ton raw meal has been reduced from 20 to 10 kWh, and even some people claim Raw Material Preparation in Cement Manufacturing Plant AGICOStage 2: Grinding, Proportioning, and Blending The crushed raw ingredients are made ready for the cementmaking process in the kiln by combining them with additives and grinding them to ensure a fine homogenous mixture The composition of cement is proportioned here depending on the desired properties of the cement Generally, limestone is 80%, and the remaining 20% How Cement is Made Cement Manufacturing Process
.jpg)
Cement Rotary Kiln Vertical Shaft Kiln Kiln In Cement Plant
While the shaft kiln cement manufacturing technology does not have these limitations The cement plant that regards the shaft kiln as main equipment has low requirements for ore reserves, and it is more able to effectively utilize small reserves mines These characteristics in the use of resources are undoubted of great significance2024年2月23日 The operation of the cement raw mill is a critical step in cement production By grinding the raw materials into a fine powder, these powders can be more easily mixed with other cement ingredients and burn more evenly How Does a Raw Mill Work in a Cement IndustryCement plant is necessary for cement along with fly ash, iron ore, and coal 2 Grinding: The raw materials are ground into fine powder (1–25 mm) using crushers and mills Typical energysaving, and ecofriendly cement Overview of Cement Making Machine (with Price and Second, a cement plant does not contain a low pressure steam cycle, as in a coal power plant or natural gas combined cycle system The low pressure steam loop is often considered an energy source for the post combustion capture of CO 2 Third, the cement plant uses its exhaust gases for direct heat exchange to dry the incoming raw mealCement Plant an overview ScienceDirect Topics
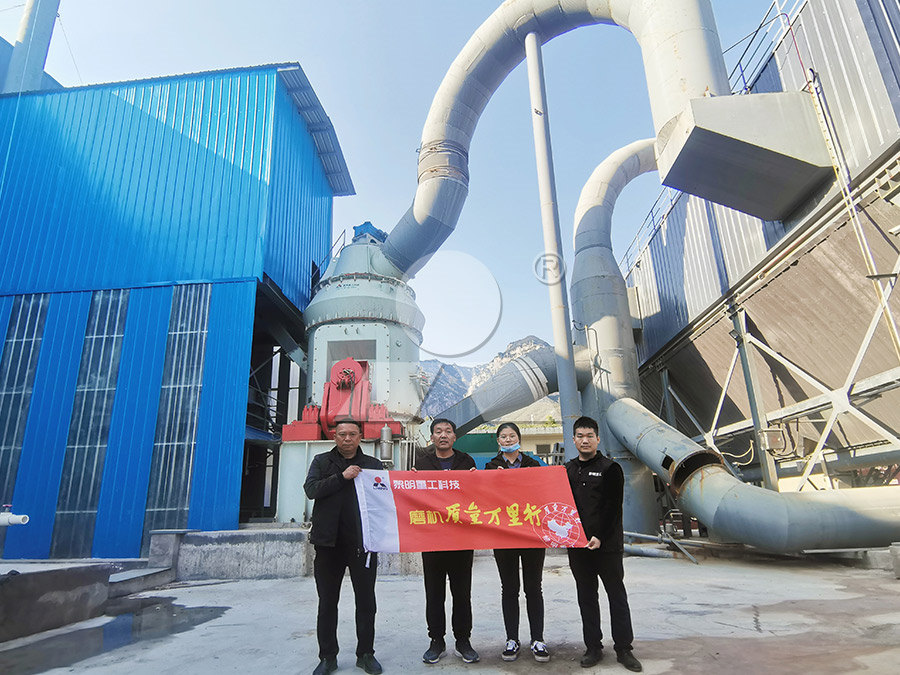
Grinding in Ball Mills: Modeling and Process Control
2012年6月1日 As the cylinder starts to rotate, the grinding balls inside the cylinder crush and grind the feed material, generating mechanical energy that aids in breaking bonds, activating the catalyst, and 2022年2月28日 Comparing dry and wet grinding curves in a ball mill in the same condition (an equal amount of materials and grinding media has been used on each pair of wetdry experiments) (Fig 17) indicated two significant differences at higher power values of wet grinding, specifically when speed exceeded 06 critical speed and for higher ω Pmax in the Grinding SpringerLink2024年11月23日 Cement Extraction, Processing, Manufacturing: Raw materials employed in the manufacture of cement are extracted by quarrying in the case of hard rocks such as limestones, slates, and some shales, with the aid of blasting when necessary Some deposits are mined by underground methods Softer rocks such as chalk and clay can be dug directly by Cement Extraction, Processing, Manufacturing BritannicaTo achieve good combustion and satisfactory flame formation, coal needs to be dried and ground to a proper degree of dryness and fineness Drying of moisture in coal is achieved normally by ducting part of the kiln exhaust gas through the mill with inlet temperatures of up to 300°CCoal Grinding Cement Plant Optimization
}@~3SRDG`IA1KP_ICWAA.jpg)
Cement Production Process Cement Manufacturing Process AGICO CEMENT
2020年8月25日 Cement grinding: The clinker is taken from the clinker silo and sent to the feed bin where it is mixed with gypsum and additives before entering the cement grinding plant In the cement grinding process, the clinker is ground to a fine powder along with other materials, up to 5% gypsum or additional anhydrite is added to control the 2023年4月23日 The amount of grinding media and ore charge sh ould allow free movement in the grinding zone A low filling level allows the charge material to attain high kinetic ener gy that causes strong impacts(PDF) Grinding Media in Ball MillsA Review ResearchGateCement manufacturing: components of a cement plant This page and the linked pages below summarize the cement manufacturing process from the perspective of the individual components of a cement plant the kiln, the cement mill etc For information on materials, including reactions in the kiln, see the ' Clinker ' pagesCement manufacturing components of a cement plant Understanding CementHow can I start a cement manufacturing plant? Starting a cement factory involves several crucial steps: Determine the scale of production and type of cement to be produced Choose an optimal location for the cement plant Design the layout StepbyStep Guide to the Manufacturing of Cement
.jpg)
How Cement is Made Portland Cement Association
The cement and concrete industry is dedicated to reaching carbon neutrality by 2050 or sooner The use of lowercarbon cement blends, alternative fuels, reuse of waste products and other innovations is occurring and will continue to grow AGICO offers superiorquality cement kiln, cement vertical mill, cement ball mill, cone crusher, hammer crusher, Raymond mill, etc All of the cement plant equipment has a low cost and long service lifeCement Plant Equipment Cement Making Machines As newtype and energyefficient cement grinding machine, cement roller press has advantages of energysaving, high efficiency, less steel consumption and less noise Both apply for new cement plant building and old cement plant revamping According to the data, roller press helps ball mill system to increase the output by 3050%Cement Roller Press, Roller Press In Cement Plant HPGR CrusherAll types of cement grinding mills such as cement ball mills, vertical roller mills, roller presses, and various related equipment form a highly efficient production line Closed circuit grinding systems equipped with an OSepa separator are more efficient especially when the grinding mill is a cement vertical millCement Grinding Units Cement Plant Equipment CNBM
.jpg)
CEMENT GRINDING SYSTEMS INFINITY FOR CEMENT EQUIPMENT
The final manufacturing stage at a cement plant is the grinding of cement clinker from the kiln, mixed with 45% gypsum and possible additives, into the final product, cement In a modern cement plant the total consumption of electrical energy is about 100 kWh/t The cement grinding process accounts for approx 40% if this energy consumptionMaintenance in the cement industry is one of the contributors to the production cost and represent typical 15 – 25 percent of total manufacturing expenditure Many companies have tried to use standard production methods to control maintenance costsMAINTENANCE IN THE CEMENT INDUSTRYOccurrence of a mineral is an indication of mineralization that is worthy of further investigation, although it does not imply any measure of volume or grade However, before a cement plant is conceived, an adequate quantity of limestone should be identified and explored, based on the geological reports of mineral occurrenceBasics of mineral resources for cement production85tph Cement Ball Mill In Indian Cement Plant; Ore Dressing Line; Cement Grinding Plants As a leading cement plant builder, AGICO offers an expert cement grinding plant EPC service we will reply to you within 24 hours Output Capacity: 100 ~ 5,000 TPD; Grinding Cement Packing Machine Cement Belt Conveyor Cement Bucket Elevator Cement Grinding Plants Cement Grinding Unit Cement Grinding
.jpg)
Ball Mill For Cement Grinding – Cement Ball Mill Ball Mill
Pregrinding:it refers to adding a grinding machine in front of the cement ball mill to increase the output of the original grinding system by a large margin This method features large investment and relatively complex process but it can increase the output of cement ball mill by up to 50%