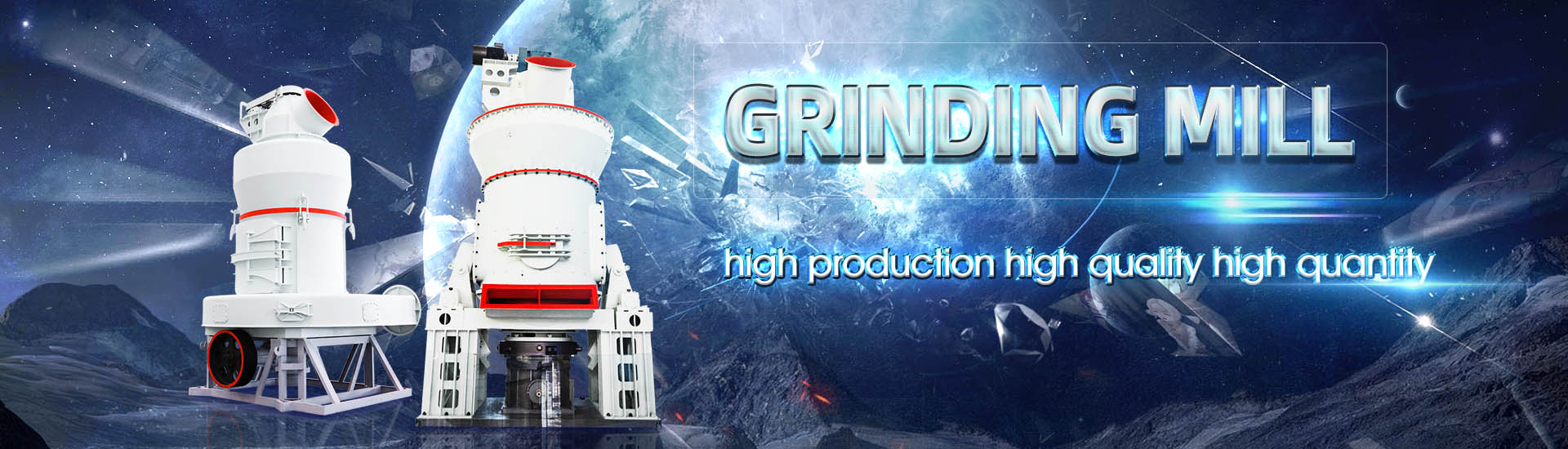
Desulfurization liquidgas ratio
.jpg)
Influence of liquid to gas ratio on the desulfurization process in
2007年6月1日 The desulphurization efficiency increases with increasing pH value and the ratio of liquor and gas, while decreases with increasing solution density and flue gas velocity2020年2月1日 With the decline of the liquid/gas ratio and flue gas temperature, the removal efficiency of ammonia sulfate aerosols increased, and the NH 4 + emitted from entrainment Transformation and removal of ammonium sulfate aerosols and 2020年11月13日 Seawater flue gas desulfurization (SWFGD) is considered to be a viable solution for coastal and naval applications; however, this process has several drawbacks, including its corrosive(PDF) Advanced and Intensified Seawater Flue Gas 2020年2月7日 The results show that the desulfurization efficiency increased by increasing the liquid–gas ratio and pH of the absorbed liquid, and decreased by increasing the inlet Prediction of SO2 removal efficiency for ammoniabased wet flue
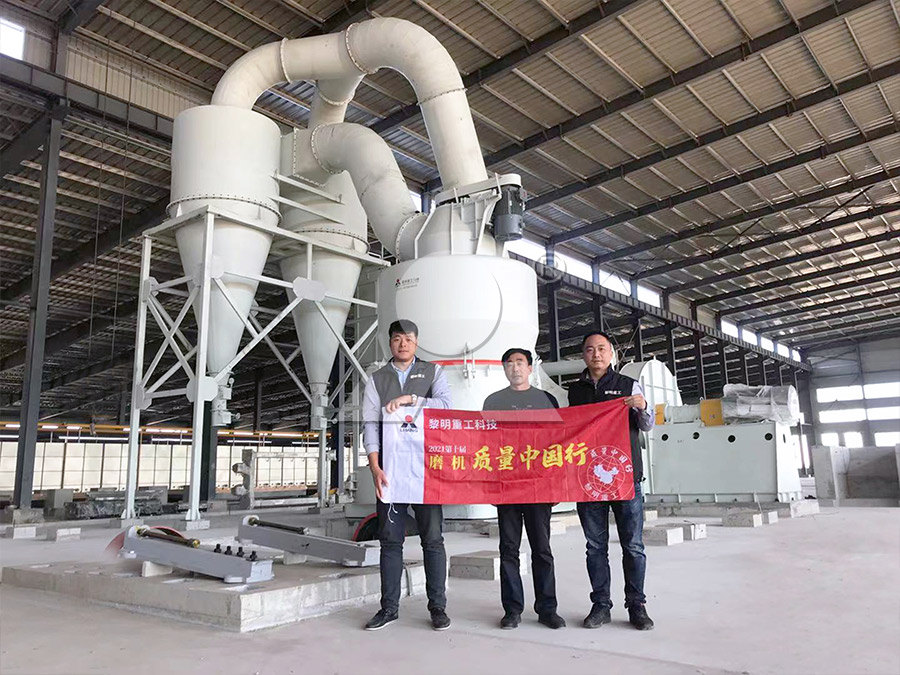
Efficient and promising oxidative desulfurization of fuel using
2024年6月1日 Oxidative desulfurization (ODS) has emerged as a prominent technique for the removal of sulfur compounds from fuels, aiming to comply with stringent environmental 2021年1月7日 Accordingly, three typical desulfurization share setups of 80%, 85%, and 90% were compared under various operational conditions by varying the fuelsulfur content, ASPEN PLUS desulfurization simulations for the scrubber of a large 2010年5月1日 On the basis of experimental data, the correlations of the desulfurization efficiency with flue gas flow rate, slurry flow rate, pH value of slurry and liquid–gas ratio were Experimental study on desulfurization efficiency and gas–liquid Liquid–gas ratio (L/G) is an influencing factor that can decide the size of the absorption equipment and influence the operating cost With a larger L/G ratio, the driving force of absorption enhances, which is in favor of absorption Modeling and simulation of an improved ammonia
.jpg)
Prediction of SO2 removal efficiency for ammoniabased wet flue gas
2020年2月7日 42 The effect of liquid–gas ratio The liquid–gas ratio is vital in the absorption process When the gas flow was 1 m 3 /h, SO 2 concentration in the flue gas was 2500 mg/m 3 The pH of the absorption solution was 8 The relationship between the liquid–gas ratio and desulfurization efficiency is shown in Fig 52021年12月30日 To reduce operating costs on the basis of ensuring the desulfurization efficiency in a wet flue gas desulfurization system, a theoretical model was put forward, and a calculation method was set up Correlations CoalFired Boiler Flue Gas Desulfurization System 2020年11月13日 Effect of liquidtogas ratio on desulfurization When the L/G increases at a fixed volume of gas, the volume of the liquid rises in the column, leading to a higher contact gas–liquid area [6,11] As a result, higher SO 2 Advanced and Intensified Seawater Flue Gas Overall, removal efficiencies of 989% and 559% for SO2 and NOx abatement were obtained in two inseries scrubbers operated under a gas contact time of 1 and 100 s, and a liquidtogas ratio of 7 Influence of liquidtogas ratio (L/G) on ( ) sulfurremoval
.jpg)
An evaluation of desulfurization technologies for
Abstract Sulfur compounds represent one of the most common impurities present in the crude oil Sulfur in liquid fuel oil leads directly to the emission of SO 2 and sulfate particulate matter that endangers public health and community property; and reduces the life of the engine due to corrosionFurthermore, the sulfur compounds in the exhaust gases of diesel engines can 2021年6月1日 The influences of liquidtogas ratio, SO 2 concentration of inlet flue gas, and combination mode of different spray levels to the desulfurization efficiency were analyzed Gutiérrez Ortiz ( Gutiérrez Ortiz, 2010 ) used the number of transfer units (NTU) and height of transfer unit (HTU) to develop a model of WFGD system in fullscale coalfired power plantsSimulation of SO2 absorption and performance enhancement of wet flue 2021年1月7日 Finally, the comparison of total liquid/gas ratio requirements listed in Tables 1 and 2 suggest that (i) under the conditions with the fuelsulfur not exceeding 35%, the total liquid/gas ratio requirements of the case settings labeled as the main section’s desulfurization share of 80% and 85% are almost at the same levels but clearly lower ASPEN PLUS desulfurization simulations for the scrubber of a 2011年9月1日 The aerosol particles removal efficiencies by the condenser increase with the liquid–gas ratio When ammonia solution is used as scrubbing the liquid, the influence of the liquid–gas ratio is more pronounced, and the removal efficiency increases from 45% to about 75% with increase in the liquid–gas ratio from 1 to 4 L m −3 (STP)The formation and removal characteristics of aerosols in
.jpg)
(PDF) Modeling of ammoniabased wet flue gas desulfurization
2011年4月1日 PDF A mathematical model of ammoniabased wet flue gas desulfurization process was developed based on the double film theory liquid/gas ratio and SO2 concentration2021年4月1日 Perea et al [71] reported the influence of the Si/Al ratio on the adsorption efficiency of Ni incorporated MCM41 (Ni/MCM41) for denitrogenation and desulfurization of a mixture of quinoline and DBT The material with the higher Si/Al ratio possesses a relatively higher surface area and favored denitrogenationReview on recent advances in adsorptive desulfurization2021年5月15日 The aminebased flue gas desulfurization (FGD) method is a competitive and promising technique to realize SO 2 removal and sulfur recycling from flue gas To study the steady and transient state behaviors of continuous SO 2 absorption and desorption processes with ethylenediaminephosphoric acid solution, a ratebased system model including main Continuous SO2 absorption and desorption in regenerable flue gas 2002年4月1日 The influences of liquidtogas ratio, SO2 concentration of inlet flue gas, and combination mode of different spray levels to the desulfurization efficiency were analyzedOptimum Values of Process Parameters of the “Wet Limestone Flue Gas
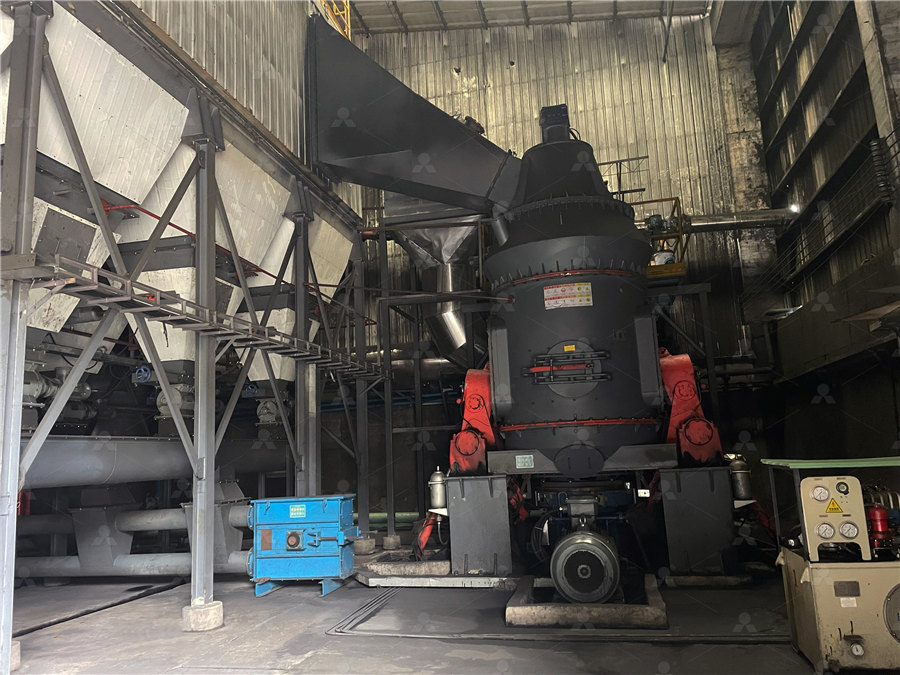
(PDF) Desulfurization of Offshore Natural Gas by ResearchGate
2019年6月19日 Desulfurization of Offshore Natural Gas by Chelated Iron Solution in a HiGee Reactor: The gasliquid ratio and packing height significantly improve H2S removal efficiency, Fluegas desulfurization (FGD) is a set of technologies used to remove sulfur dioxide (SO 2) The chief drawback of spray towers is that they require a higher liquidtogas ratio requirement for equivalent SO 2 removal than other absorber designsFluegas desulfurization Wikipedia2014年7月3日 Furthermore, many studies showed that the oxygen would be absorbed from gas into steel when liquid steel contacted with oxidizing gases at high temperature, and some elements in liquid steel would be oxidized[28–31] In slag eyes where the liquid steel is directly exposed to the ambient environment, these effects on the desulfurization behavior were still Numerical Simulation of Desulfurization Behavior in GasStirred Two setups approaching the former two liquid–gas ratio assembles (ie, a total liquid–gas ratio of 4 L/Nm3 gaining a high alkali‐utilization efficiency above 98%) thus confirmed that this Desulfurization performance comparison of a 162‐kW marine
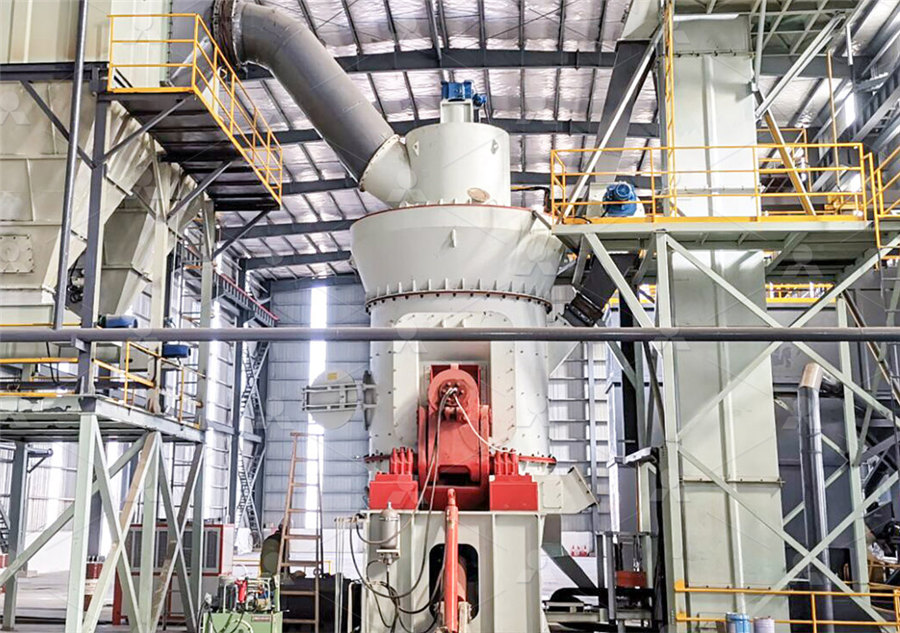
A Venturitype slurry jet nozzle for efficient flue gas desulfurization
2023年8月3日 The slurry jet technique is widely used for flue gas desulfurization, whereas the increase in its absorption efficiency is required to meet the increasingly strict exhaust emission standards In this work, we developed a Venturitype slurry jet nozzle to improve the efficiency of flue gas desulfurization As anticipated, the absorption efficiency of SO2 can be enhanced by 2020年8月1日 Numerous mitigation techniques have been incorporated to capture or remove SO2 with flue gas desulfurization molar ratio of HBA:HB D and liquidgas ratio Amino ac id shows better SO 2Sulfur dioxide removal: An overview of regenerative flue gas 2009年10月1日 It is showed that the ratios of the gas side resistance to the overall gas side resistance were in the range of 043–052 for droplet sizes of 500–2000 μm, indicating that both liquid and gas side resistances were important, with the absorption rate likely to be controlled by a combination of both gasfilm and liquidfilm diffusion controlsPrediction of SO2 removal efficiency for wet Flue Gas DesulfurizationAnalytical Investigation and Design of Flue Gas Desulfurization System Madhur Dhoot*, Vishal Shevale, Mayur Tambe, Swikruti Shelorkar, Nikhil Chougule, Krunal Meshram and z = Multiplication factor for gasliquid ratio required for equilibrium reaction c = Conversion factor But actual liquid required = 15to 30 times LAnalytical Investigation and Design of Flue Gas Desulfurization
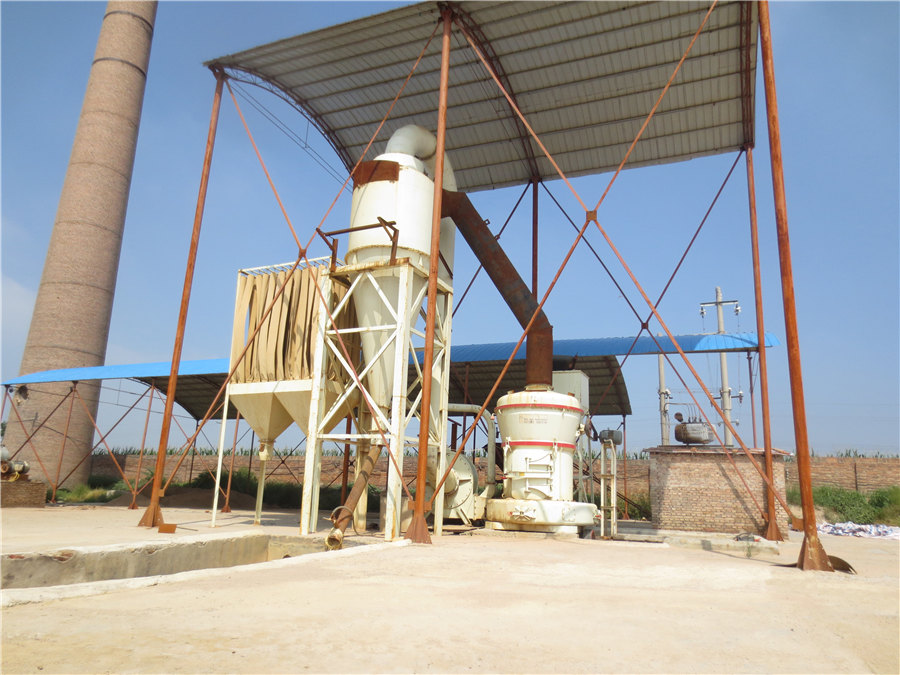
A concise algorithm for calculating absorption height in spray
2015年1月1日 The absorption of SO 2 in wet desulfurization units is realized in absorption towers There are several types of towers, such as spray towers, packed towers, jet bubbling reactors, venture scrubbers and double loop towers [13]The most commonly used and best studied wet scrubber is the countercurrent spray tower employing liquid distribution at different 2013年3月1日 Fig 4 a shows that the desulfurization efficiency raised with an increase of the liquid–gas ratio R LG The liquid–gas ratio is one of the most important parameters in desulfurization process The increase of the liquid–gas ratio will directly raise the gas–liquid contacting area, greatly accelerate the mass transfer, and improve the Studies on magnesiumbased wet flue gas desulfurization 2021年5月1日 Wet Flue Gas Desulfurization (WFGD) is a flue gas purification technology widely used in coalfired power plants, steel sintering machines, marine exhaust gas washing (Caiazzo et al, 2013), etc Desulfurization efficiency is the core of SO 2 removal In principle, the absorption process can be regarded as a gasliquid mass transferProcess optimization of S (IV) oxidation in flue gas desulfurization 2020年8月1日 For the primary desulfurization tower, the desulfurization liquid temperature and liquidtogas ratio were maintained at 50 °C and 10 LNm −3, respectively The humiture of the flue gas at the heat exchanger inlet was 60 °C and 95%, and the flue gas temperaturedrop in heat exchanger was set at 5 °CPromoting fine particle removal in doubletower cascade wet flue gas
.jpg)
A twostage desalination process for zero liquid discharge of flue gas
Pr These results indicated that effluent of the twostage process had considerable desulfurization capacity and can be recycled for the preparation of CaCO3 slurry or as na l the makeup water of desulfurization tower 100 60 40 Jo 20 ur SO2 removal (%) 80 Absorption liquid A Absorption liquid B Absorption liquid C Absorption liquid D 0 0 20 40 60 80 100 120 140 Absorption time 2015年3月15日 The mol ratio of liquid/gas (L/G) has been found to be one of the most important criterions for reporting the reactor performance from an United States Environmental Protection Agency (US EPA) Flue gas desulfurization system capabilities for coalfired steam generators Vol II Technical Report EPA600/778032b; March 1978 Status of Flue Gas Desulphurisation (FGD) systems from coal 2023年10月1日 The extractive desulfurization has been found to be one of the most effective way for desulfurization of the liquid fuels The major aspects which affects the desulfurization are the temperature, oilIL/DES mass ratio, extraction time, initial S Content, mutual solubilities, multiple cycles and regeneration of the used solvents in the EDS processA comparative review of extractive desulfurization using designer Energy Fundamentals Zhihua Wang, in Comprehensive Energy Systems, 2018 12333152 Liquid–gas ratio The liquid–gas (L/G) ratio, which is defined as the ratio of slurry flow to flue gas flow, is expressed in units of L/m 3Normally, L/G values are 40–67 L/m 3 in lime WFGD and 80–134 L/m 3 in limestone WFGD [48], respectivelyA lower L/G ratio is required in lime Gas Liquid Ratio an overview ScienceDirect Topics
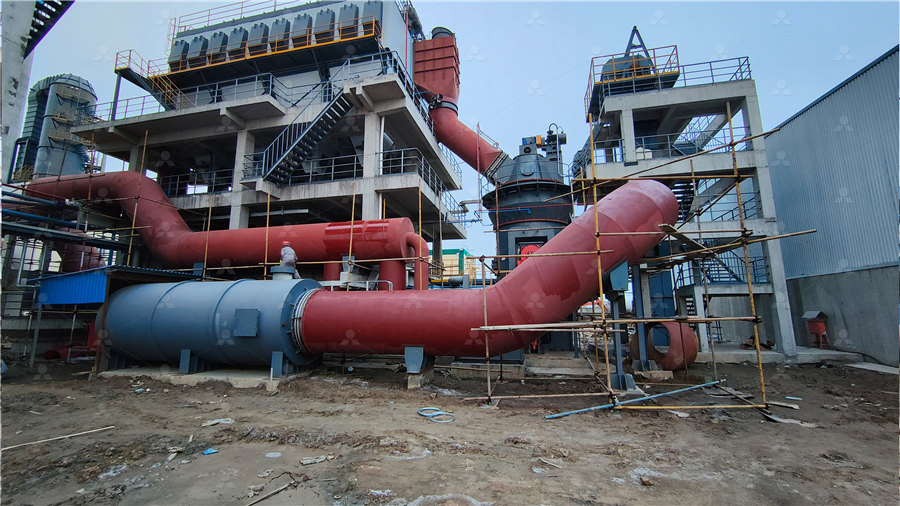
Ionic liquid screening for desulfurization of coke oven gas based
2021年12月1日 The effect of four key parameters including the number of equilibrium stagesN stage, the liquid–gas ratio − L/V, the temperature of the inlet ILs (T in), and the operating pressure (p) of the absorption column on the toxic gas removal ratios and selectivity of different sulfides over methane were separately investigated by the sensitivity PDF On Oct 15, 2018, Cara Niu published Comparison of flue Gas Desulfurization Technologies spray amount of absorbent liquid and increasing the ratio of liquid to gas parison of flue Gas Desulfurization Technologies2020年10月5日 Hypersaline wastewater generated from industries, including coal chemical industry, oil and gas industry, inland desalination, flue gas desulfurization (FGD) and vanadium extraction, is of growing environmental concern (Boo et al, 2019; Tong and Elimelech, 2016; Wang et al, 2015; Zhang et al, 2020)In recent years, desalination for water reuse in plants A twostage desalination process for zero liquid discharge of flue gas 2014年10月15日 Reutilization of lowgrade magnesium oxides for flue gas desulfurization during calcination of natural magnesite: A closedloop process Author links open overlay panel R del ValleZermeño a, J Formosa b, [23]: liquidtogas ratio (L/G, liter of slurry per m 3 of gas), time (t), gas flow, pH, water (W) and solid (S)Reutilization of lowgrade magnesium oxides for flue gas
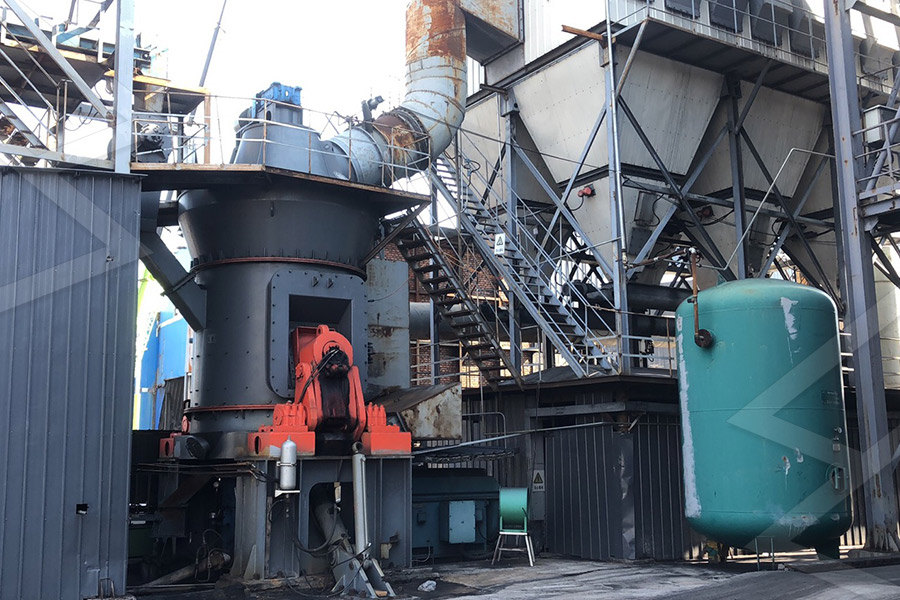
Flue Gas Desulfurization Gypsum ScienceDirect Topics
Cheng et al determined that a proper reduction in the liquid gas ratio, concentration of the slurry and inlet flue gas temperature could help reduce the emission of NH 3 /NH 4 + in an ammonia desulfurization system [181]desulfurization share setups of 80%, 85%, and 90% were compared under various operational conditions by varying the fuelsulfur content, liquid/gas ratio, and seawater alkalinity In complying with the desulfurization requirements of emission control areas, 85% was obtained as the optimal desulfurization share among the three setupsASPEN PLUS desulfurization simulations for the scrubber of a 2017年11月30日 The desulfurization efficiency of MSEGCS is affected by many factors, including the gas flow rate, initial concentration of SO 2, liquid–gas ratio (%v/v), Mg–S ratio (mol/mol), pH and flow field 9,10 In our previous work, the effects of gas flow rate, liquid–gas ratio, Mg–S ratio and pH on the efficiency of the desulfurization tower in MSEGCS were Modeling and prediction of desulfurization efficiency for 2019年3月30日 The influences of liquidtogas ratio, SO2 concentration of inlet flue gas, and combination mode of different spray levels to the desulfurization efficiency were analyzedProgress of Desulfurization and Denitration Technology of Flue Gas
.jpg)
Efficient desulfurization of gasoline fuel using ionic liquid
2015年3月28日 The extractive desulfurization of a model gasoline containing several alkyl thiols and aromatic thiophenic compounds was investigated using two imidazoliumbased ionic liquids (ILs), 1butyl3methylimidazolium tetrachloroaluminate, and 1octyl3methylimidazolium tetrafluoroborate, as extractants A fractional factorial design of experiments was employed to 2010年1月1日 In the WFGD process the liquidtogas ratio is an important operational parameter that can influence SO 2 removal and gas–liquid mass and energy transfer characteristics The number removal efficiencies of fine particles for steam addition in the gas inlet and above the scrubbing liquid inlet are shown in Fig 8 (a and b) as a function of liquidtogas ratioRemoval of fine particles in wet flue gas desulfurization system 2010年5月1日 This paper presents a new liquidscreen gas–liquid twophase flow pattern with discarded carbide slag as the liquid sorbent of sulfur dioxide (SO 2) in a wet flue gas desulfurization (WFGD) systemOn the basis of experimental data, the correlations of the desulfurization efficiency with flue gas flow rate, slurry flow rate, pH value of slurry and Experimental study on desulfurization efficiency and gas–liquid 2015年2月15日 A similar influence to the masstransfer process can be deduced from the liquidtogas (L/G) ratio, which is considered one of the most important parameters for describing the desulfurization process as the dissolution process of the solids and thus the absorption of SO 2 is controlled by mass transfer [5], [11], [17], [18], [21], [22]Synergistic effect of the parameters affecting wet flue gas