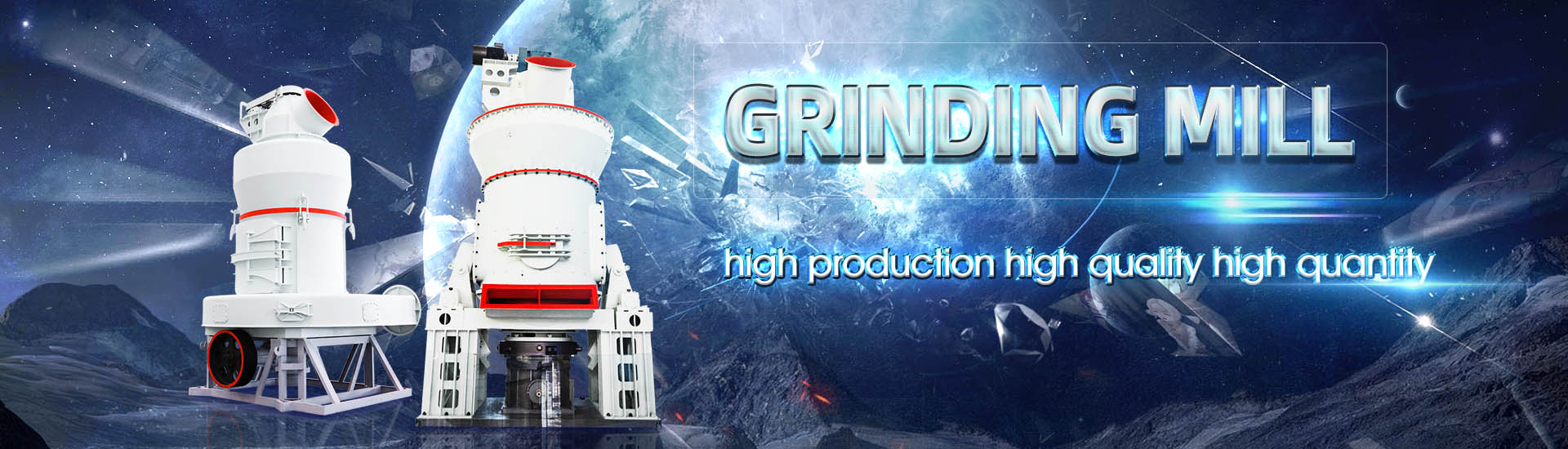
Steel Slag Production Zinc Oxide Process
.jpg)
HighPerformance Method of Recovery of Metals from EAF Dust
Granulated steelmaking dust with reducer (coal dust) was the input material The products of the process are zinc oxide, iron alloy and slag, with properties meeting high ecological 2024年4月1日 Recovery of zinc from slag is typically carried out via a slag zinc fuming operation, where a reductant is used to reduce zinc oxide and volatilize zinc metal In most cases,Technology Selection for Slag Zinc Fuming Process ResearchGatelize the slag produced, it is necessary to process it to the grain size specified by the customer Therefore, the slag Processing and Reusing Technologies for Steelmaking Slag2019年6月18日 Gravimetric, magnetic, floatation, pyrometallurgical and hydrometallurgical treatments are discussed for processing of charge chrome, steel, copper smelter, brass smelter, tin, incineration,(PDF) Metallurgical Processing Strategies for Metals
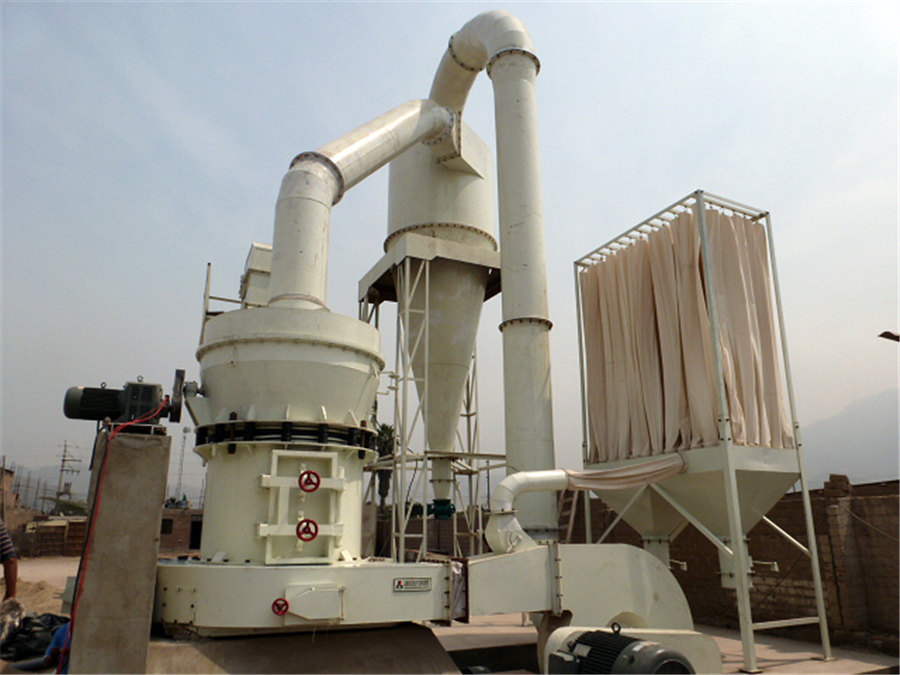
Basic Oxygen Steelmaking Slag: Formation, Reaction,
Basic oxygen steelmaking (BOS) slag, a product of hot metal element (eg, Si, Mn, Fe, P) oxidation and flux (eg lime, dolomite) dissolution, plays a critical role in the production of highquality crude steel, although its behavior inside the 2007年3月1日 Steel plant slags mainly include blast furnace slag and steel melting slag (open hearth or LD process slag) Various efforts have been made on the utilization of blast furnace An overview of utilization of slag and sludge from steel industries1 天前 Zincextraction kiln slag is generated from metallurgical dust in the steel industry after zinc extraction (Song et al 2019) According to the “2021 annual report on prevention and Characterization and solidification of heavy metals in sintered solid Three types of slag, namely electric arc furnace (EAF), basic oxygen furnace (BOF), and LinzDonawitz processed slag (LDslag) are the steel industry byproducts That slag comprises precious elements including zinc (Zn), An Overview of Precious Metal Recovery from Steel
.jpg)
Zinc recovery from metallurgical slag and dust by
1 Introduction Currently, the main source of zinc metal is the traditional zinc resource—zinc sulfide ores However, as the zinc consumption increases and the zinc sulfide ore grades deteriorate, the gap between supply and demand has Flow sheet for recovery of chromium from stainlesssteel slag by alkali onestep electrodialysis process produces a ZnSO 4 solution with a lowenough chloride concentration for an electrolytic zinc production process from leaching solutions of disclose the AAC leaching process for EAF dust, Waelz oxide, and CZO Hydrometallurgical Processes for the Recovery of Metals from Steel 2019年5月23日 Steel slag is the waste generated in the steelmaking process and includes ferric oxide and the impurities of some infusible matters It is the byproduct when slagforming constituents (such as fluorite, lime, and deoxidant) are added for deoxidization, desulfurization, and dephosphorization in prehensive Utilization Technology of Steel SlagThe products of the process are zinc oxide, iron alloy and slag, with properties meeting high ecological requirements The technology does not generate solid waste Zinc recovery is over 99% and iron recovery over 98% The content of heavy metals (Zn + Pb + Cu) As per [2,3] average annual steel production is 1600 million tons, HighPerformance Method of Recovery of Metals from EAF Dust
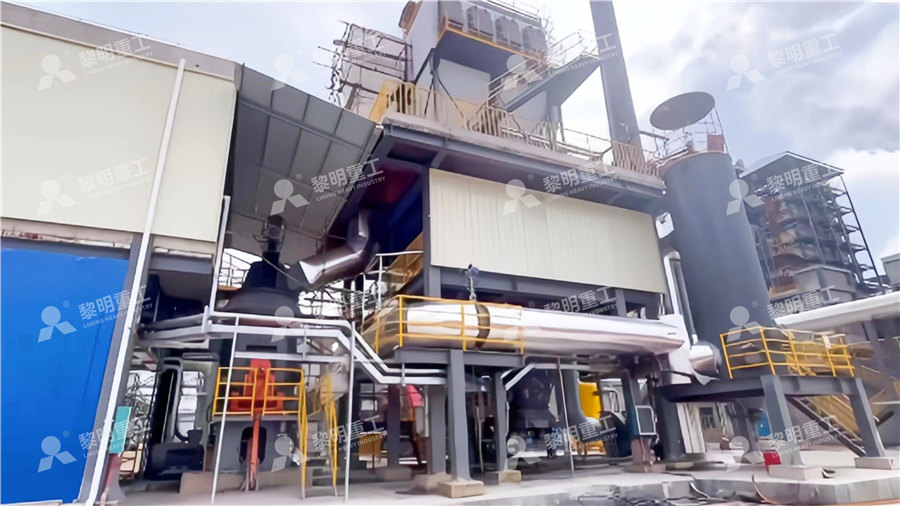
Preparation of active zinc oxide from zinccontaining dust and
Steel metallurgical dust The dried zinc carbonate was calcined in a muffle furnace at 400 ℃ for 2 h, and the active zinc oxide product was obtained after (8695 %) and Cd (9228 %), while Pb, Sn, Bi and In were enriched in the neutral leaching slag Neutral leaching slag in the high acid leaching process realizes the 2000年1月1日 Download Citation Recovery of Zinc Oxide from Secondary Raw Materials: New Developments of the Waelz Process Because of the increasing use of zinc as an active and passive anticorrosion agent Recovery of Zinc Oxide from Secondary Raw Materials: New2016年8月31日 Process of slag Generation (epagov) During the process of reducing iron ore through coke in a blast furnace, blast furnace slag is generated while steel making slag is generated in the process of Steel Slag Utilization — Overview in Indian PerspectiveMild steel: Mild steel is iron containing up to about 025% of carbon The presence of the carbon makes the steel stronger and harder than pure iron The higher the percentage of carbon, the harder the steel becomes Mild steel is used for lots of things nails, wire, car bodies, ship building, girders and bridges amongst others233: Metallurgy of Iron and Steel Chemistry LibreTexts
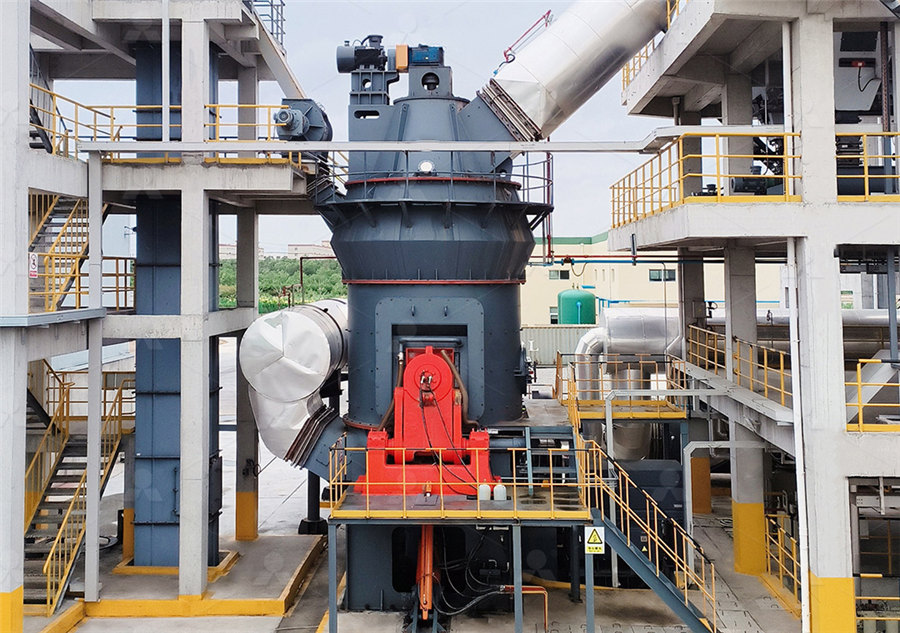
Residual Processing in the European Steel Industry: A
2019年4月3日 In the SDHL Waelz process, steel mill dusts, various zinccontaining residuals, For the use of the Waelz oxide product in the zinc industry, eg, in steel production as an iron carrier Table 6 shows the composition of the final Waelz process products (Waelz oxide and slag) Table 6 Compositions of Waelz oxide and slag 1 Introduction The basic oxygen steelmaking (BOS) process produced over 70% of the global crude steel in 2018, [] generating 100 to 150 kg of slag (“BOS slag”) for every tonne of crude steel produced BOS slag, a product of hot metal element (eg, Si, Mn, Fe, P) oxidation and flux (eg, lime, dolomite) dissolution, plays a critical role in the production of highquality crude steelBasic Oxygen Steelmaking Slag: Formation, Reaction, and Energy 2007年3月1日 Integrated steel plants utilize mostly five materials such as raw materials, air, water, fuel and power to produce steel During the production of steel, 2–4 t of wastes are being generated per tonne of steel producedThe various solid wastes in the form of slags and sludges that are emerged from steel plants are blast furnace slag, blast furnace flue dust and sludge, An overview of utilization of slag and sludge from steel industries2022年1月14日 24 Pig Iron and Zinc Oxide (PIZO) Process PIZO process uses electrical energy to produce three products in a single reactor, which are crude zinc oxide, hot metal of BF quality and slag The PIZO process uses a continuous channel induction furnace as the primary processing unit for the recycling of steelmaking dust A Review on Processing of Electric Arc Furnace Dust (EAFD) by
.jpg)
Steel slag in China: Treatment, recycling, and management
2018年8月1日 The China Association of Metal Scrap Utilization first announced the production and utilization of steel slag in 2005 (2005); between 2005 and 2013, China’s steel slag production rose sharply along with an increase in its crude steel production The amount of steel slag reached 1013 million tons in 20132023年10月27日 This article presents the mineralogical and chemical characteristics of zinc and lead smelting slags, with particular reference to the slags formed during the simultaneous production of Zn and Pb by the Imperial Smelting Process These slags, because of the presence of many metals in their composition, mainly in the form of crystalline phases, are a valuable Zinc and Lead Metallurgical Slags as a Potential Source of Metal2011年10月26日 The slag generated from a steelmaking cycle is later processed, and the final product after processing is referred to as basicoxygenfurnace slag (BOF slag) The chemical reactions occurring during the removal of impurities determine the chemical composition of the basicoxygenfurnace slag [ 1 , 3 , 5 ]Chemical, Mineralogical, and Morphological Properties of Steel Slag 2004年5月14日 Steel slag is a byproduct from either the conversion of iron to steel in a basic oxygen furnace, or the melting of scrap to make steel in an electric arc furnace This paper reviews the production, processing, and characteristics of steel slag, and its Steel Slag—Its Production, Processing, Characteristics, and
.jpg)
SLAG IRON AND STEEL IBM
SLAG IRON AND STEEL 16 Slag Iron and Steel S lag is a byproduct generated during manufacturing of pig iron and steel It is produced by action of various fluxes upon gangue materials within the iron ore during the process of pig iron making in blast furnace and steel manufacturing in steel melting shop Primarily, slag consists of calcium The main challenge of the steel industry for the next decade is the steel production transformation process, starting in Europe The CO 2 intensive blast furnace/basic oxygen furnace (BOF) route will be substituted by a combination of Direct Reduced Iron (DRI), based on natural gas, later on “green” hydrogen, with an Electric Arc Furnace (EAF) or a Submerged Arc Furnace (SAF), The steel production transformation process in Europe: New slag 2021年8月10日 1 Introduction The basic oxygen steelmaking (BOS) process produced over 70% of the global crude steel in 2018, [] generating 100 to 150 kg of slag (“BOS slag”) for every tonne of crude steel produced BOS slag, a product of hot metal element (eg, Si, Mn, Fe, P) oxidation and flux (eg, lime, dolomite) dissolution, plays a critical role in the production of high Basic Oxygen Steelmaking Slag: Formation, Reaction, and Alternative production and experimental scale zinc recovery processes include the rotary hearth treatment of pelletised zinc containing dust (Kimitsu works, Nippon Steel); [9] [10] the SDHL (Saage, Dittrich, Hasche, Langbein) process, an efficiency modification of the Waelz process; [3] the "DK process" a modified blast furnace process producing pig iron and zinc (oxide) dust Waelz process Wikipedia
.jpg)
Production, characterisation, utilisation, and beneficial soil
2021年10月5日 The ironmaking and steelmaking industries produce four types of slags, named after the processes from which they are produced (Fig 2): Blast Furnace Slag (BFS), BasicOxygen Furnace Slag (BOFS), ElectricArc Furnace Slag (EAFS), and Ladle Furnace Slag (LFS), and the type of slag produced is dependent on the desired steel endpoint (Ilyushechkin et al, 2024年3月17日 Steel making is a sophisticated process that turns iron ore into steel, involving methods like the Blast Furnace and Electric Arc Furnace to produce various grades of steel The industry emphasizes sustainability by A Visual Guide: Steel Making Process Chart Cabaro Chemical Principles of Zinc Oxide Reduction 169 Reduction From Molten Slags 173 Process Description 201 Slag Composition 204 Impurities and Zinc Metal Quality 205 General and Comparative Aspects of Major Zinc Production Processes 253 Chapter 19 – Treatment of Oxide and Secondary Materials 255 Scope 255The Extractive Metallurgy of Zinc AusIMM2023年2月3日 This article presents the history of zinc, its production and demand The quantity of zinc production, both primary zinc from ores and concentrates, and secondary zinc from scrap and zincrich waste, was discussed A comprehensive economic analysis covers zinc prices in the years 1960–2021 The basic methods of obtaining zinc from ores, including pyrometallurgical Evaluation and Current State of Primary and Secondary Zinc Production

Galvanizing process
The fluxing operation removes the last traces of oxide from the surface and allows the molten zinc to wet the steel The galvanizing process When the clean iron or steel component is dipped into the molten zinc (which is commonly at around 450°C) a series of zinciron alloy layers are formed by a metallurgical reaction between the iron and zincAlmost 2957–3846 million tons of zincbearing dust were produced in Chinese iron and steel enterprises annually The recovery of Zn and other metals in zincbearing dust from ironmaking and steelmaking could improve economic efficiency However, zincbearing dust was classified as hazardous waste, and the volatile metals (like Zn, Na, Pb, etc) in zincbearing dust limited the Research status and development of extraction process of zinc 2024年1月12日 Steel slag is a byproduct of the steel production process, accounting for approximately 15% of the whole crude steel output [1]The accumulation of untreated steel slag not only occupies a significant amount of land but also leads to the leaching of heavy metal ions (such as vanadium, chromium, arsenic, lead, cadmium), polluting surrounding water sources Review Accelerated carbonation of steel slag: A review of Zinc Oxide Production: Zinc ash is used to extract zinc oxide, which is a crucial component used in the manufacturing process of rubber, ceramics, glass, paints, pigments, and even various cosmetics Pharmaceuticals: Zinc oxide is often used in a variety of pharmaceutical products, such as ointments, sunscreens, and dietary supplements, owing to its antibacterial and UV A Buyer’s Guide to Zinc Products: Dross, Ash, Dust IBMD
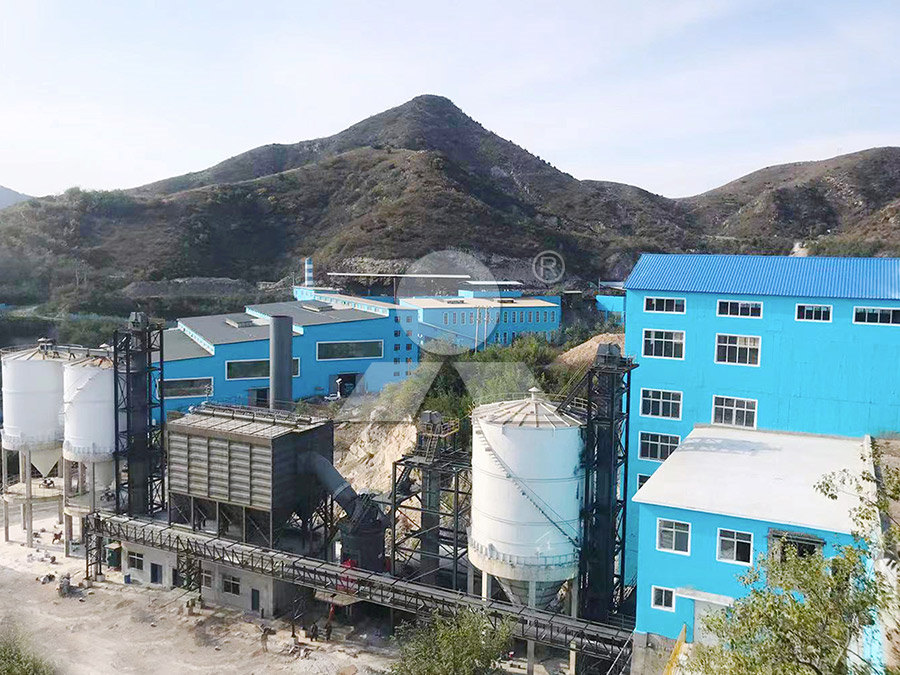
Iron and SteelMaking Process SpringerLink
2020年6月10日 The foremost requirement of RH process is the production of steel grades with very low hydrogen and carbonlevel steel The process involves vacuum decarburization, degassing of other gases including hydrogen and subsequent alloying The heats for ULC grades are tapped at LD converter with dissolved oxygen level of 500–700 ppmLinzDonawitz (LD) slag, a byproduct of steel manufacturing process, is rich in iron oxide, calcium oxide, silica, various macro, and micronutrients as well as varying degrees of heavy metals Flowchart of slag production in a modern steel plantSteelmaking slag, or steel slag, is a byproduct from the production of steel during the conversion of hot metal to crude steel in a basic oxygen furnace, or during the melting of scrap in an EAFThe slag is generated as a melt and is a complex solution of silicates and oxides that solidify upon cooling 11 Depending on the specific steel production process, three different types of steel Steelmaking Slag an overview ScienceDirect Topics2005年5月31日 Request PDF Steel Slag — Its Production, Processing, Generally, these materials are characterized by a high calcium oxide content being in the range of 3060% [73,78,79,83, 84] Steel Slag — Its Production, Processing, Characteristics, and
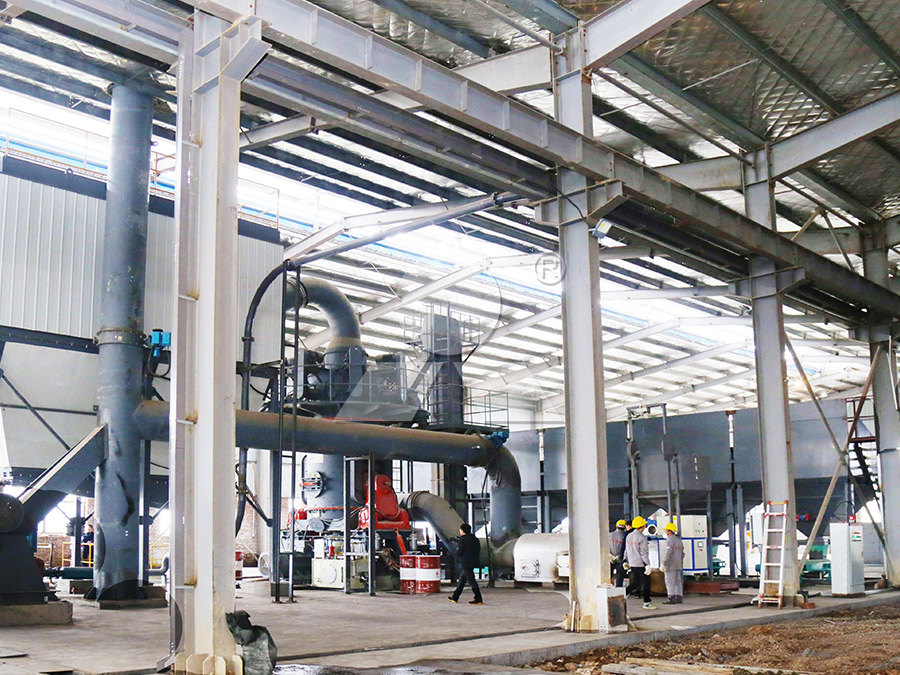
Characteristics and environmental aspects of slag: A review
2015年6月1日 After final processing, the steel slag generated is approximately 10–15% of crude steel output Based on Fe and steel production data, approximately 260–330 Mt of blast furnace Fe slag and approximately 150–220 Mt of steel slag were produced worldwide in 2017年3月22日 The other main steelmaking process, the electric arc furnace (EAF) process (used for 30% of the world’s steel production), is not discussed in this paper In the EAF, the scrap types used control the sulphur concentration of the liquid steel The SM ladle treatment processes are comparable for both BFBOF and EAF steelmakingSulphur removal in ironmaking and oxygen steelmakingproduction and slag composition of highzinc EAFdust Za+ co, zoo +co 1200 ~ ~f'! ~ ~ 1000 f" 800 10 100 CO/CO2, volume ratio Figure 5Temperature of the backreaction of zinc with CO2at different CO/CO2 ratios and zinc partial pressures in the offgas When a typical alloysteel dust is smelted at l500°C, aThe Enviroplas process for the treatment of steelplant dustsAn example of slag chemistries during stainless steel production from Holappa et al (2021) is given in Table 23 where significant quantities of chromium oxide are found in the EAF slag; however, due to the high reactivity of chromium with FeO and the addition of slag reducing agents such as silicon and aluminum in the EAF, there are low levels of FeO and MnO in the EAF 2 Electric Arc Furnace Steelmaking and Slag Formation,
.jpg)
Production process of zinc oxide – TYSONZINC
2018年11月6日 In fact, many indirect zinc oxide products on the market today use zinc slag as raw material, rather than pure zinc ingots Therefore, the heavy metal content in products is often relatively high The production process of indirect zinc oxide is simple and its price is mainly determined by the price of its raw materialzinc oxide reduction was between 25 and 50 pct of the overall reaction mechanism The mass transfer coefficient of the zinc oxide reduction quadrupled from 1400 C to 1500 C The zinc recovery rate Carbothermic Reduction of Zinc Containing Industrial2019年11月5日 GA Yurko, “ Slag Fuming Process at the Cominco Smelter ”, in Extractive metallurgy of lead and zinc, CH Catterill (ed), Vol2, AIME, New York, 1970,p 330347 * Calculated value(PDF) Slag Fuming Process – A Review ResearchGate2020年4月30日 Characterization of steel slag for the production of chemically bonded phosphate ceramics through calcination of the zinc oxide and the use of zinc hydroxide and aluminum to neutralize the phosphoric acid specifically using steel slag, a Characterization of steel slag for the production of chemically