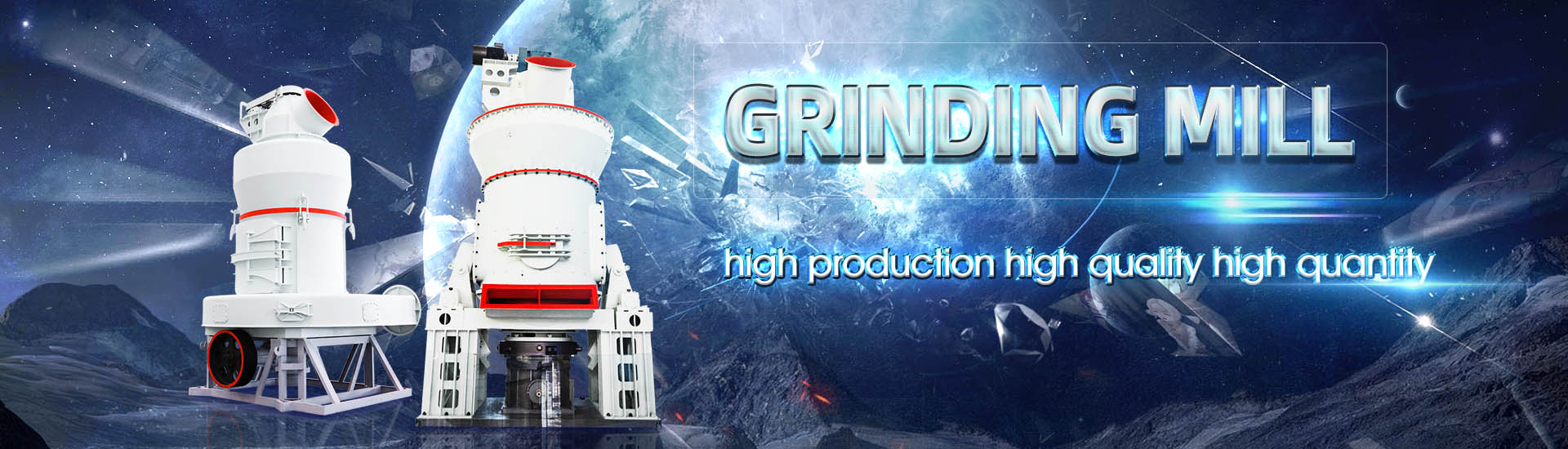
Tieling water coal slurry ball mill
.jpg)
Coal Water Slurry Ball Mill
Coal water slurry ball mill is grinding equipment specially used for coal water slurry production Its specifications, structure and working conditions must meet the requirements of coal water The raw material of coal powder is coal with various hardness, and it drying in the Coal Ball MillCoalwater slurries (CWS) (also referred to as coalwater fuels (CWF), or as coalwater mixtures (CWM)) are highly loaded suspensions of fine coal in water Since these are mixtures of coal CoalWaterSlurries an overview ScienceDirect Topicsfine grinding for coal water slurry fuels is by ball mills; for example, ball mills are commonly used in China where over 30Mt of slurry fuel is currently produced annually with ash levels below Premium coal fuels with advanced coal beneficiation Glencore
R)8OC`6F[ZIB.jpg)
CoalWaterSlurries an overview ScienceDirect Topics
Coal water slurry gasification is an entrained flow gasification process for generating syngas under high temperature and high pressure with coal water slurry as raw material and oxygen or air as gasification agent Both one and twostep grinding techniques in ball mills have been used to produce the required particle size distribution2019年10月1日 Hence, the pulp density of coalwaterslurry was optimized with the addition of extra water, which resulted in 151%–173% ash clean coal at an average yield of 54–58% from coal tailings Wet and dry grinding of coal in a laboratoryscale ball mill: Particle 2015年10月15日 A) Total Apparent Volumetric Charge Filling – including balls and excess slurry on top of the ball charge, plus the interstitial voids in between the balls – expressed as a percentage of the net internal mill volume (inside Calculate Ball Mill Grinding Capacity 911Metallurgist2012年12月1日 Optimization of inmill ball loading and slurry solids concentration in grinding of UG2 ores: A statistical experimental design approach December 2012; Minerals Engineering 39:149155;(PDF) Optimization of inmill ball loading and slurry solids
.jpg)
Grinding in Ball Mills: Modeling and Process Control
2012年6月1日 As the cylinder starts to rotate, the grinding balls inside the cylinder crush and grind the feed material, generating mechanical energy that aids in breaking bonds, activating the catalyst, and 2008年8月1日 Residence time distributions (RTDs) were estimated by water tracing in a number of wet overflow ball mills (diameters 038 to 465 m) producing dense, coalwater slurries In opencircuit mills of 038 m diameter and various lengthdiameter (L/D) ratios, the mean residence times of solid were also determined from measured mill holdups Holdup increased with increased Experimental study of residence time distributions of ballmill 2017年2月13日 The apparent difference in capacities between grinding mills (listed as being the same size) is due to the fact that there is no uniform method of designating the size of a mill, for example: a 5′ x 5′ Ball Mill has a working diameter of 5′ inside the liners and has 20 per cent more capacity than all other ball mills designated as 5′ x 5′ where the shell is 5′ inside diameter and Ball Mills 911Metallurgist2012年4月17日 Effect of Slurry Density on Load Dynamic and Milling Performances in an Iron Ore Ball Mill Online Estimation of Inmill Slurry Density April 2012 DOI: 1013140/2146258561Effect of Slurry Density on Load Dynamic and Milling Performances in

Ball Mill an overview ScienceDirect Topics
The characteristic tumbling motion of these mills has given them the name ‘tumbling mills’, which include the ball mill, tube mill and rod mill Ball mills are horizontal rotating cylindrical or conical steel chambers, approximately one third to half full of steel, alloy steel or iron balls, like that shown in Fig 410 A–C , or flint stones2023年10月27日 The impact of cavitationactivated water on combustion dynamics and environmental characteristics of coalwater slurry fuel IOP conference series, [online] 537, pp doi:https://doi (PDF) An Overview of CoalWater Slurry Fuels ResearchGateEspecially for seeding as a preliminary stage of product crystallization proper, the use of a slurry suspension is now state of the art BMA's supply line of crystallization equipment also includes a slurry mill operating by the ball mill Slurry mill BMA's supply line of crystallization 2016年6月3日 The Tower mill can be installed for a fraction of the cost of an equivalent kilowatt (horsepower) ball mill The Tower mill develops very little dynamic forces Therefore, its foundation can be a concrete floor slab Tower Mill Operating Work Index 911Metallurgist
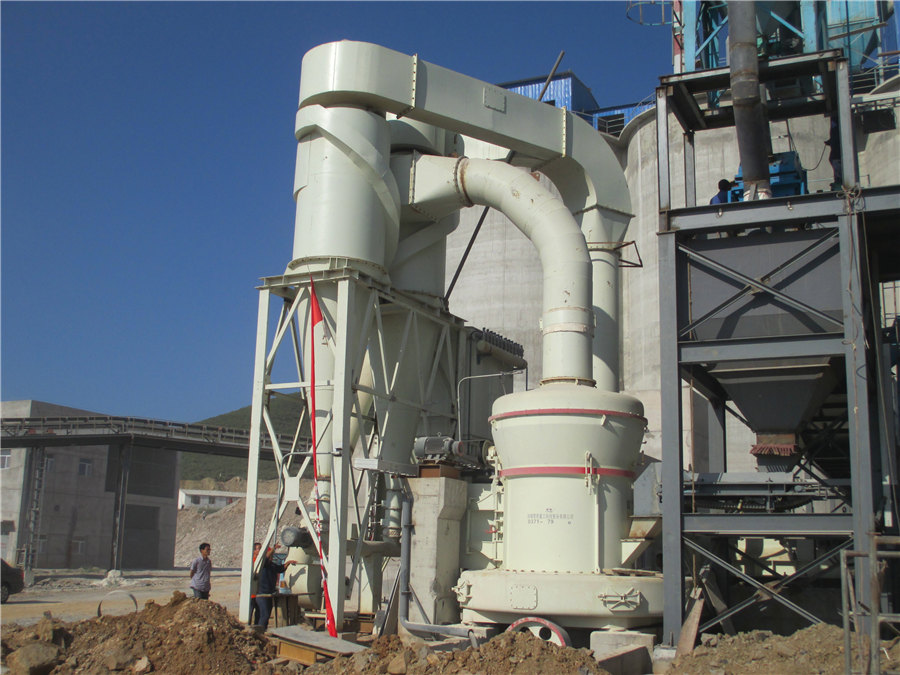
Coal Water Slurry Mixing Mill, Barite Reverse Milling
Coal Water Slurry Mixing Mill, Barite Reverse Milling Machine, To through the rotational energy of the stirring wheel to drive the medium ball and slurry to generate turbulence then interactional colliding, shearing, and squeezing to 2017年10月30日 The pilot mill used was 44 cm id and 60 cm il with a volume of 91,250 cm and was fitted with six onehalf inch lifter bars The ball charge was made up of 2,200 oneinch balls for a bulk volume of 36,500 cm³ (40% loading and a Grinding Coal Water Slurry 911MetallurgistChina Slurry Ball Mill wholesale Select 2024 high quality Slurry Ball Mill products in best price from certified Chinese Rice Mill manufacturers, Coal Water Slurry Making Machine Ball Mill US$ / Set 1 Set (MOQ) Zhengzhou Zhongjia Heavy Industry Co, LtdSlurry Ball Mill MadeinChina2015年8月6日 Soon there will only be the large and intermediate size of feed left in the mill Mill slurry characteristics affect grinding efficiency because of their influence on slurry rheology Slurry characteristics can be manipulated and tested to determine their effect on grinding efficiency There are three mill slurry characteristics which you Ball Rod Mill Density – How Water Impacts Grinding
.jpg)
Coal micronization studies in vibrating mill in terms of Coal Water
2017年3月1日 The paper presents the results of coal milling tests in the aspect of slurry fuel preparation The tests were carried out with the use of vibrating mill with a working chamber of 475 dm32023年12月28日 3 The ball mill is of good quality The better the quality of the ball mill, the more stable the performance of the ball mill will be during operation In addition, as for the lining plate of the ball mill’s wearing parts, the quality of the lining plate affects the overall production efficiency of the ball mill As we all know, the lining Factors Affect The Output and Quality of Ball Mills And How to 2013年7月15日 PDF The ball mill in closed circuit with hydrocyclones is an industry standard, and well known methodologies exist for equipment sizing, selection and Find, read and cite all the research (PDF) Energy Efficient Ball Mill Circuit – Equipment Sizing 2019年10月19日 Ball mills are extensively used in the size reduction process of different ores and minerals The fill level inside a ball mill is a crucial parameter which needs to be monitored regularly for optimal operation of the ball mill In this paper, a vibration monitoringbased method is proposed and tested for estimating the fill level inside a laboratoryscale ball mill A vibration Monitoring the fill level of a ball mill using vibration sensing and
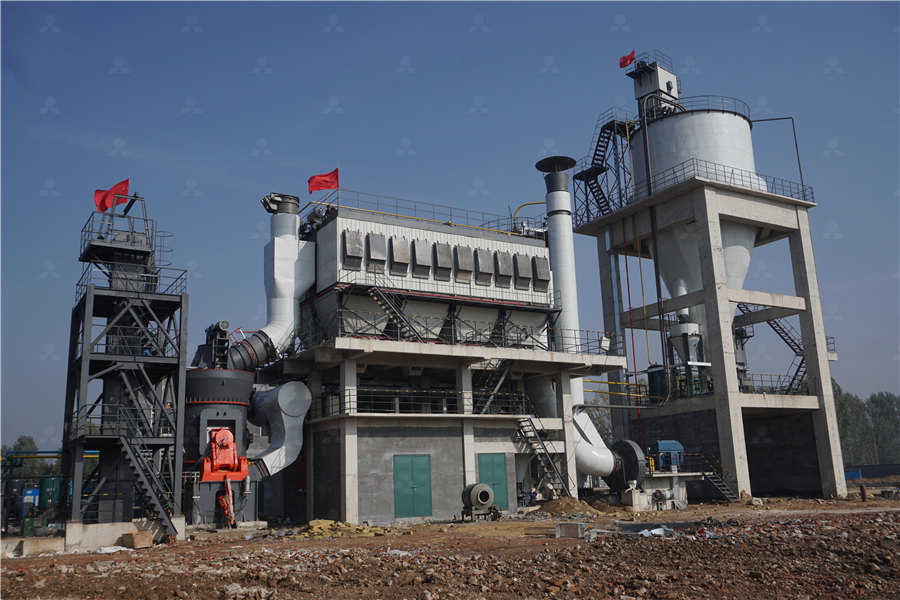
Ball Mill Circulating Load Formula 911Metallurgist
2015年10月9日 Calculating a grinding circuit’s circulating loads based on Screen Analysis of its slurries Compared to %Solids or Density based Circulating load equations, a more precise method of determining grinding 2002年11月1日 The effect of ball load composition, by varying the grinding media size distribution (eg alternatively by mixing four groups of 195, 38 mm; 195, 50 mm; 38, 50 mm and 195, 38, 50 mm), on the The energy efficiency of ball milling in comminution2017年10月26日 The following are factors that have been investigated and applied in conventional ball milling in order to maximize grinding efficiency: a) Mill Geometry and Speed – Bond (1954) observed grinding efficiency to be a Factors Affecting Ball Mill Grinding Efficiency2023年10月27日 The ball mill is a rotating cylindrical vessel with grinding media inside, which is responsible for breaking the ore particles Grinding media play an important role in the comminution of mineral ores in these mills This work reviews the application of balls in mineral processing as a function of the materials used to manufacture them and the mass loss, as A Review of the Grinding Media in Ball Mills for Mineral
.jpg)
(PDF) Highconcentration coal–water slurry from Indian coals
One of the exciting areas in Coal Water Slurry (CWS) is coal–wateralcohol slurry in which different alcohol compound can act as a dispersant for the stabilisation of coal–water slurry Objective: The objective of this paper is to prepare a high concentration coal–wateralcohol slurry using glycerol, glycol and ethanol as an additive, and different particle size distribution of coal2023年4月23日 One of the most used tumbling mills is the ball mill This paper reviews different types of grinding media that have been developed and improved over the years and their properties(PDF) Grinding Media in Ball MillsA Review ResearchGateRequest PDF On May 1, 2014, MM Bwalya and others published Exploring ball size distribution in coal grinding mills Find, read and cite all the research you need on ResearchGateExploring ball size distribution in coal grinding millsReason: This is a common problem mining ball mills face, resulting in low productivity and low ore processing efficiency One reason may be the improper design of the grinding chamber, which affects the flow of materials and reduces grinding efficiency Additionally, worn or damaged liners can hinder the grinding process by reducing the effective impact between the ball and the Inventory Of Common Faults And Solutions Of Mining Ball Mill
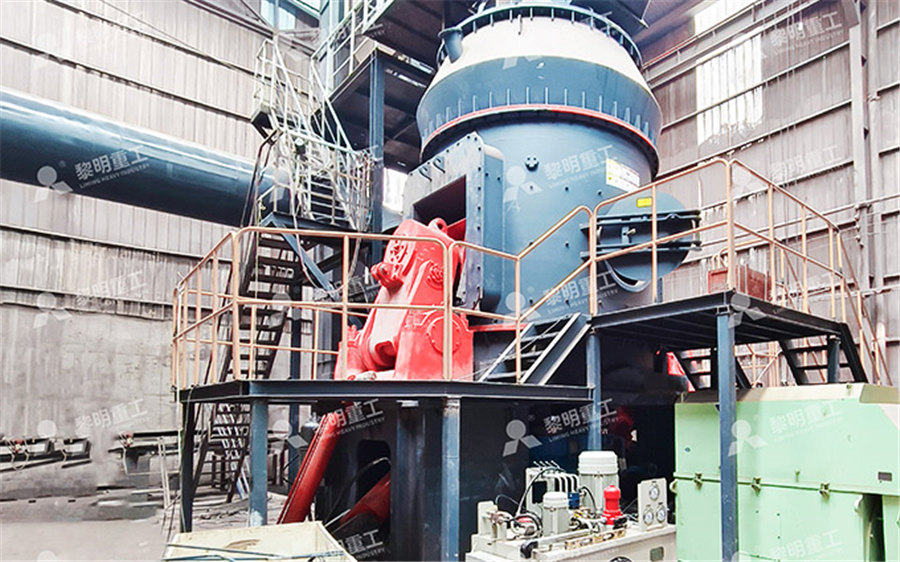
Ball Mill an overview ScienceDirect Topics
The ball mill is a tumbling mill that uses steel balls as the grinding media The length of the cylindrical shell is usually 1–15 times the shell diameter (Figure 811)The feed can be dry, with less than 3% moisture to minimize ball coating, or slurry containing 20–40% water by weightBall Mill, Wet Ball Mill Lubrication system, Mill circuit tank with an agitator, Mill circuit Pump, Mill Hydro cyclone, 3way distributor and accessories The Wet Ball Mill is the wet horizontal type The Process water is supplied to Wet Ball Mill and Wet Mill circuit Tank Slurry from the Wet Ball Mill flows by gravity to the Wet Mill Receiver TECHNICAL SPECIFICATION OF WET BALL MILL EQUIPMENT2020年7月2日 A comprehensive investigation was conducted to delineate the effect of ball size distribution, mill speed, and their interactions on power draw, charge motion, and balls segregation in a (PDF) Effects of Ball Size Distribution and Mill Speed and Their 2019年8月1日 Hence, the pulp density of coalwaterslurry was optimized with the addition of extra water, which resulted in 151%–173% ash clean coal at an average yield of 54–58% from coal tailings Differences in dry and wet grinding with a high solid
.jpg)
(PDF) Rheological properties of coal water slurries
2018年1月1日 The integral ignition characteristics of a single droplet (initial radius 03–10 mm) of various organic coal–water fuels (prepared by means of a homogenizer or a ball mill) in an oxidant flux 2020年1月1日 However, further reduction in clean coal ash by maintaining the yield was limited due to the hindrance in the movement of the highash coal particle caused by particleparticle interactions in a thick slurry Hence, the pulp density of coalwaterslurry was optimized with the addition of extra water, which resulted in 151%–173% ash clean Wet and dry grinding of coal in a laboratoryscale ball mill: Particle 2015年11月30日 In this paper the effects of flow rate, slurry solid content and feed size distribution on the rod mill efficiency have been investigated It is difficult to achieve highest grinding efficiency (PDF) Effects of Flow Rate, Slurry Solid Content and Feed Size 2008年8月1日 Residence time distributions (RTDs) were estimated by water tracing in a number of wet overflow ball mills (diameters 038 to 465 m) producing dense, coalwater slurriesExperimental study of residence time distributions of ballmill
.jpg)
Ball Mill Online Estimation of Inmill Slurry Density Bernard de
Effect of Slurry Density on Load Dynamic and Milling Performances in an Iron Ore Ball Mill Online Estimation of Inmill Slurry Density Comminution Conference 2012 – Cape Town 2/9Coalwater slurry fuel was made in a ball mill which pulverised the coal or coal sludge This was done near a coal mine in Belovo , Siberia The coalwater slurry fuel was transported through a pipeline to Novosibirskaya TEC5, Novosibirsk , a distance of 262 km (163 mi)Coalwater slurry fuel Wikipedia2002年9月1日 The coal samples were ground with a laboratory size ball mill and classi®ed into 2 210 1 106, 2 106 1 74, grinding aids in ball mills Coal water slurry The effect of coal properties on the viscosity of coalwater slurry2018年6月4日 In this study, superfine fly ash slurry [WGFA] was prepared by wet grinding from the coal fly ash Cementfly ash binder with 30%, 50%, and 70% dosage of fly ash was designed, with a water/binder (PDF) Influences of Ultrafine Slag Slurry Prepared by Wet Ball