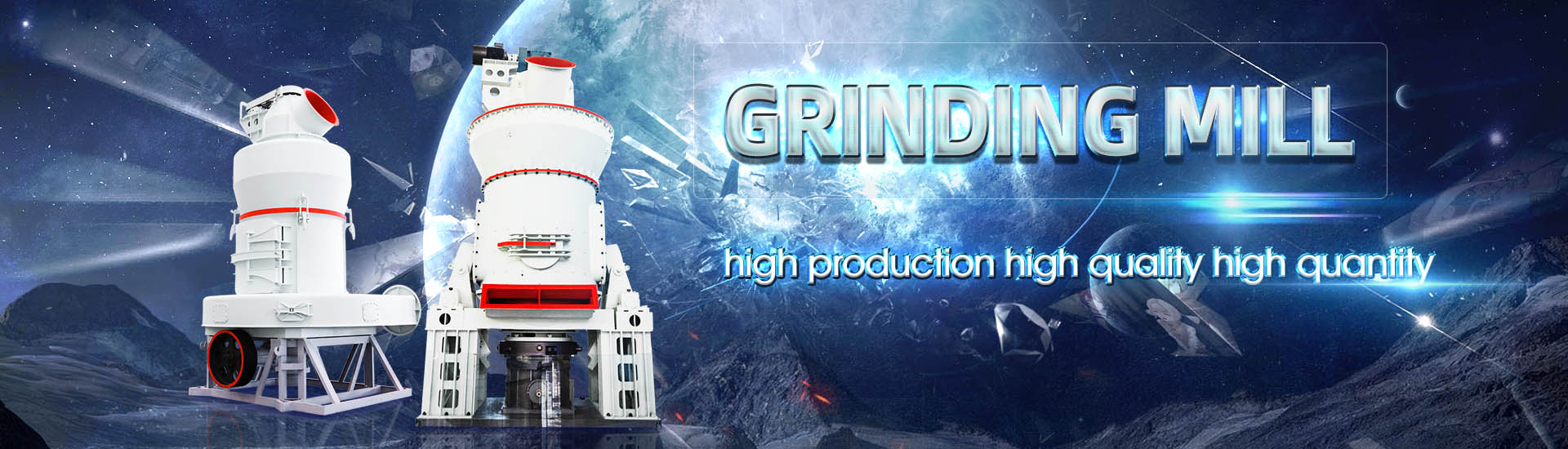
How big is the vertical mill gastomaterial ratio
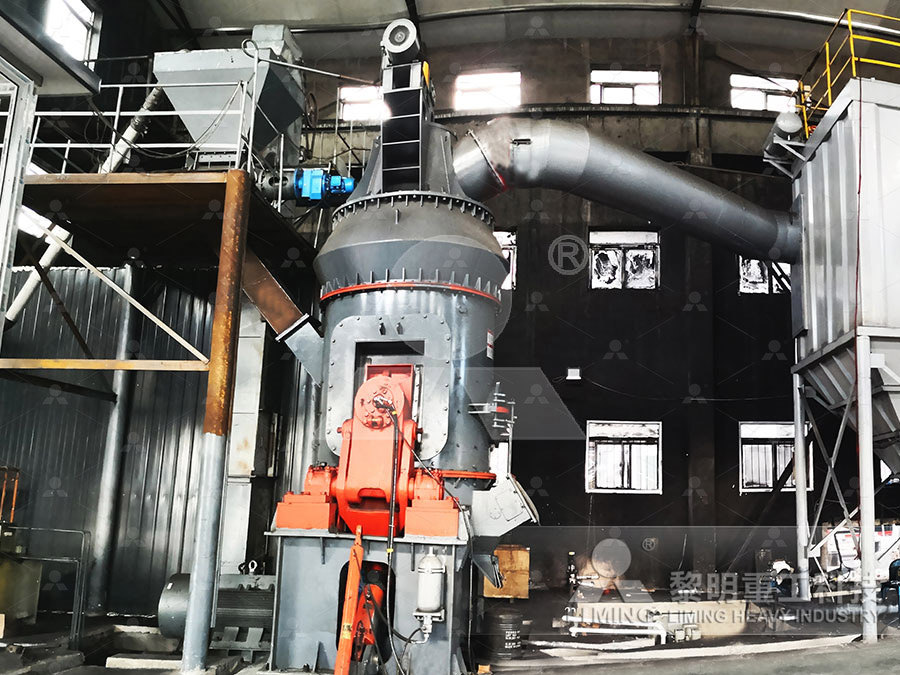
Vertical roller mill for raw Application p rocess materials
Vertical roller mills are adopted in 20 cement plants (44 mills) in Japan In the vertical roller mill which is widely used in the raw material grinding process, raw materials input grinding table are crushed and pulverized on it and transported to separator by kiln exit gas introduced into the 2022年5月31日 The metaparticle size ratio (representing feed size) has a significant effect on the performance of the VRM By increasing the metaparticle size ratio, the crushing rate firstly Analysis of vertical roller mill performance with changes in material 2017年4月1日 Vertical roller mills (VRM) have found applications mostly in cement grinding operations where they were used in raw meal and finish grinding stages and in power plants Operational parameters affecting the vertical roller mill 2021年1月1日 Big feed size The vertical roller mill can grind the material of particle size of 5% of the grinding roller diameter The feed size is generally 40 to 100 mm and can reach 120 mm Review on vertical roller mill in cement industry its performance
.jpg)
VERTICAL ROLLER MILL TECHNICAL DETAILS
The suitable grinding concentration of Tongkeng ore and Gaofeng ore is 70% and 75%, respectively The effect of mill filling ratio on Gaofeng ore is not obviousslag in roller grinding mills (vertical airswept grinding mills) is a technology introduced by Loesche The first use of a Loesche mill, with a grinding track diameter of only 11 metres, was used as 2 µm 5 µm LoescheThe core elements of these plants are the Loesche vertical mills for drygrinding the abovementioned grinding stock Loesche has developed and built the largest and most efficient PROCESS OPTIMISATION FOR LOESCHE GRINDING PLANTSVertical Roller Mills (VRM) have a clearly higher energy eficiency than ball mills, even if the ball mill is combined with a roller press This and further arguments led to the increased share of SikaGrind® for vertical roller mills
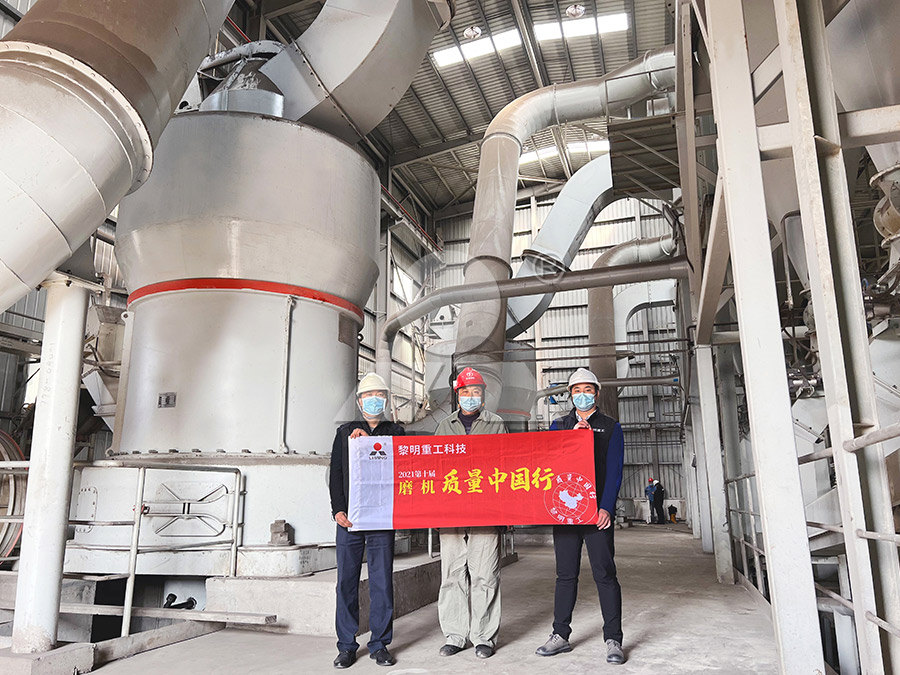
Parámetros para el Proceso de Molienda en Molinos Verticales
Los molinos verticales de rodillos (VRM), son máquinas muy utilizadas para moler materia prima en fábricas dedicadas a la extracción y procesamiento de minerales Cualquier máquina The quadropol® vertical roller mill by thyssenkrupp Industrial Solutions takes a holistic approach to modern grinding systems in terms of its simple and compatible design Describing the key VERTICAL ROLLER MILLS A holistic VRM approachThe clinkers and gypsum with a ratio of 97 to 3% are interred to a vertical roller mill (LOESCHE mill) The feed rate of the clinker VRM is 160t/h The VRM has four rollers including two big rollers (master rollers) and two small rollers (slave roller), which respectively perform grinding and make material layering on the grinding tableModeling and simulation of vertical roller mill using population 2016年9月1日 At similar millclassifier conditions, characteristic particle sizes of 050 mm for comminuted I1 pellets (compared to 083 mm for material within I1 pellets) and of 056 mm for comminuted I2 Operational parameters affecting the vertical roller mill
.jpg)
Numerical Investigation of Vertical Roller Mill Operation Using
2023年12月4日 The fine material leaves the mill, and coarser material is diverted to the grinding table by the separator This process is carried out until the required product size is achieved The VRM investigated in this study has a roller diameter of 3000 mm and a width of 1000 mm2016年1月6日 Milling involves removing material from the allows you to control the size of the chamber so you can get the volume needed to achieve a desired compression ratio daily driver, don’t want hot rod it I’ve heard old steal shems 025 thick and new are 050 So I’d need too mill 025 for compensation of old gasket Head Milling 101: The Basics of Head Milling to Gain Grinding is the preparation of material particle size, and its product's particle size composition will significantly affect the efficiency of subsequent separation operations and the economic and VERTICAL ROLLER MILL TECHNICAL DETAILS ResearchGate2015年3月15日 Vertical Agitated Media Mill modeling has become subject of a research project due to its potential application as a secondary grinding mill as well as regrind and pellet feed preparation projectsVertical Agitated Media Mill scaleup and simulation
.jpg)
(PDF) The latest innovative technology for vertical roller mills
2014年4月1日 The newly developed modular roller mill for grinding cement raw material, cement clinker, and additives with an installed power of up to 12,000 kW was specifically designed to meet those needs2021年1月1日 India is the world's second largest producer of cement and produces more than 8 per cent of global capacity Due to the rapidly growing demand in various sectors such as defense, housing, commercial and industrial construction, government initiative such as smart cities PMAY, cement production in India is expected to touch 550–600 million tones per Review on vertical roller mill in cement industry its 2021年1月6日 Download Citation Review on vertical roller mill in cement industry its performance parameters India is the world's second largest producer of cement and produces more than 8 per cent of Review on vertical roller mill in cement industry its in combination with a ball mill for cement grinding applications and as finished product grinding units, as well as raw ingredient grinding equipment in mineral applications This paper will focus on the ball mill grinding process, its tools and optimisation possibilities (see Figure 1) The ball mill comminution process has a high electricalBALL MILLS Ball mill optimisation Holzinger Consulting
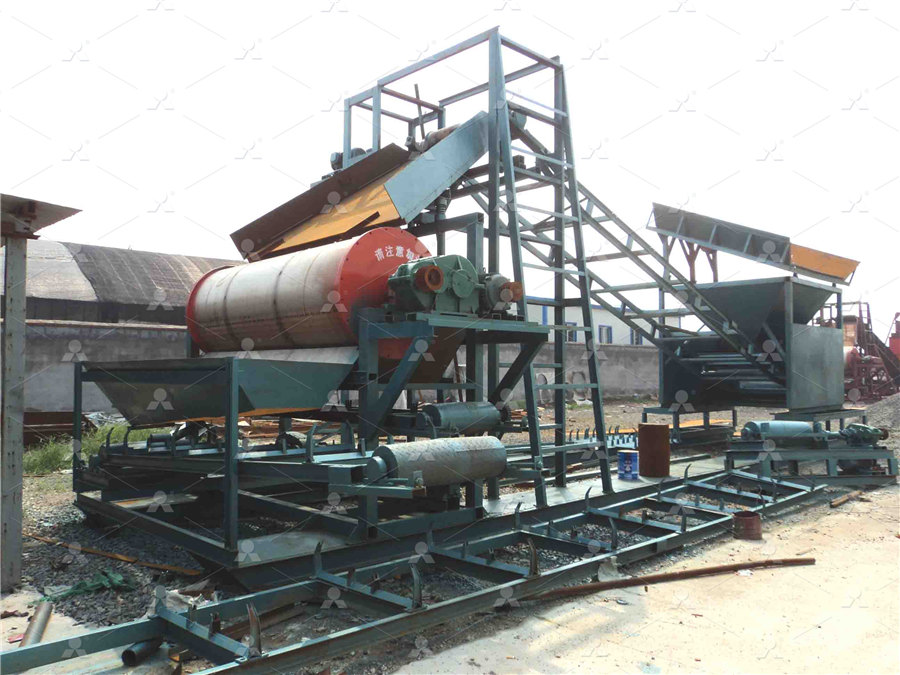
Common Basic Formulas for Mineral Processing
2016年3月21日 In calculating the Ratio of Concentration (R) of the mineral operations, the following formula has been found very useful Assays of heads, concentrate, and tailing are required Mill Water to Ore Ratio Requirements 2017年1月1日 7 CEM 6000 kW drive for a raw material mill FLSmidth Maag Gear 8 lists of the leading vendors in vertical mill sector VAriance) and the S/N (Signal to Noise) ratio(PDF) Drives for large vertical roller mills ResearchGatePDF On May 1, 2017, Caroline Woywadt published Grinding process optimization — Featuring case studies and operating results of the modular vertical roller mill Find, read and cite all the (PDF) Grinding process optimization — Featuring case 2013年3月1日 This is referred to as the classifier cut size Generally, the plant operator can control the classifier cut size, and thus the comminuted product fineness by adjusting the classifier rotor speed Cements ground in the vertical roller mill fulfil the quality
.jpg)
Effect of mill outlet temperature on the coal volatile matter
Download scientific diagram Effect of mill outlet temperature on the coal volatile matter from publication: An investigation of performance characteristics and energetic efficiency of vertical 2021年1月22日 In the whole process of cement production, the electricity consumption of a raw material mill accounts for about 24% of the total Based on the statistics of the electricity consumption of the raw A Survey and Analysis on Electricity Consumption of Raw Material Mill The vertical roller mill (VRM) is a type of grinding machine for raw material processing and cement grinding in the cement manufacturing processIn recent years, the VRM cement mill has been equipped in more and more cement plants around the world because of its features like high energy efficiency, low pollutant generation, small floor area, etc The VRM cement mill has a Vertical Roller Mill Operation in Cement Plant2019年6月22日 Ratio of actual to predicted kwh/tonne are as under for Vertical Roller Mill 05 Good performance 055 Typical performance 06 Safe design value 075 poor performance with lots of scope to improveOptimizing Raw Mills Performance ; the Materials WAY
.jpg)
Cement grinding Vertical roller mills versus ball mills
grinding of raw materials The grinding efficiency of the vertical roller mill combined with an ability to dry, grind and classify within a single unit gives the vertical roller mill a decided advantage over a ball mill system However, despite these benefits, applications of the vertical roller mill for cement grinding are less prevalent2023年4月23日 ciency include mill design, liner design, mill speed, charge ratio, and grinding media properties The authors also indi cated that circuit efficiency is determined by how well the power applied (PDF) Grinding Media in Ball MillsA Review ResearchGateRawmixes are formulated to contain a correctly balanced chemistry for the production of calcium silicates (alite and belite) and fluxes (aluminate and ferrite) in the kilnChemical analysis data in cement manufacture are expressed in terms of oxides, and the most important of these in rawmix design are SiO 2, Al 2 O 3, Fe 2 O 3 and CaO In principle, any material that can contribute Rawmill Wikipedia2016年1月20日 A mixed material, having a humidity rate of 282%, moves from the material silos into the raw mill The kiln exit gases are conditioned in the gas conditioning tower to leave at 52815 K, for preheating and drying the feed to the raw mill In the mill, the mixed and dried materials exit as raw meal with a humidity rate of 048%, after grindingAnalysis of material flow and consumption in cement
7TOCS.jpg)
Reprint from ZKG 3 Gebr Pfeiffer
In most areas of industrial grinding of bulk solids material, vertical roller mills (VRM) have prevailed Compared with ball mills, the ratio is about 90 to 10 This relationship also exists in coal grinding applications in the cement industry, where normally a twomillsystem is used 1 Introduction Two mill systems are employed for most coal2023年1月31日 The mill also has vertical arrangement VXP Mill is a product of FLSmidth company and is vertically oriented stirred media mill The mill is often used in flotation concentrate regrind and precious metals tailings retreatment where the feed size is typically 200 µm [11,12] HIG Mill is a recently developed technology by MetsoOutotech companyPerformance Comparison of the Vertical and Horizontal Oriented 2019年1月9日 Power coefficient with fixed and variable pitch for a range of tipspeed ratios and blade solidity for a twobladed verticalaxis wind turbine (VAWT) using the N crit = 001 polars of the optimised DU17VAWT200(A,B), DU17VAWT250 (C,D), and DU17VAWT300 airfoil (E,F) [Colour figure can be viewed at wileyonlinelibrary]Airfoil optimisation for vertical‐axis wind turbines with variable 2017年4月1日 Grinding test results for zinc ore showed that it is possible to decrease the total grinding energy consumption from 2011 to 1140 kW h/t by using vertical roller mill instead of AG/SAGball mill circuit (van Drunick et al, 2010)Operational parameters affecting the vertical roller mill
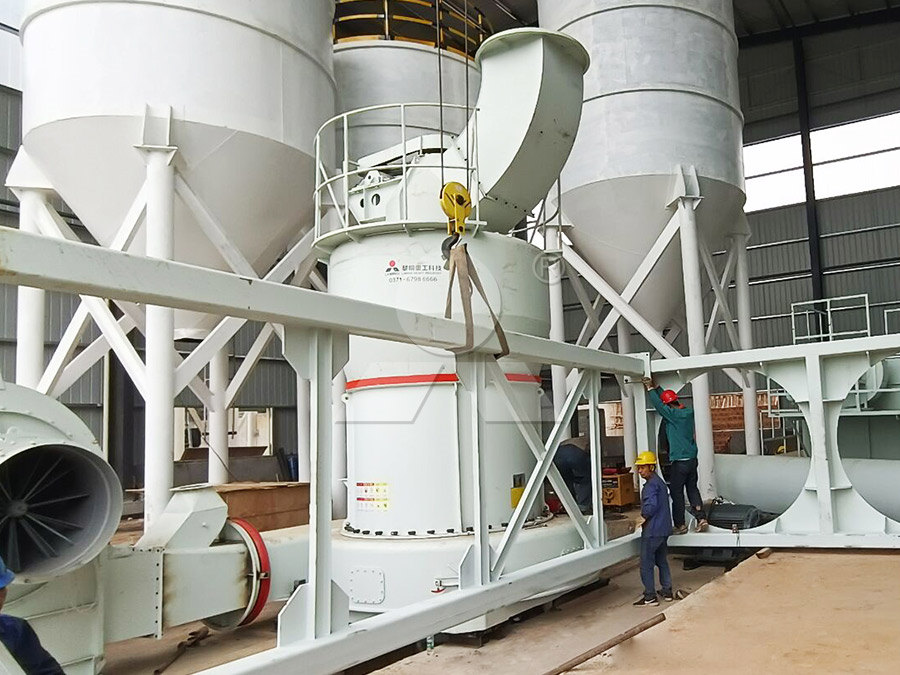
Operating experience with a vertical roller mill for grinding
2012年3月1日 the distributions of the ball mill and the vertical roller mill Fig 6a shows an example of the circularity of a ground granulated blastfurnace slag, produced with the LM 352+22021年6月8日 Working principle of a roller mill Loesche has been manufacturing industrial mills for grinding mineral raw materials such as coal and cement for almost 100 years Socalled vertical roller mills are shown here in more detail (Figure 1) The raw material falls over the chute (2) onto the center of the grinding table (3)Strength Assessment of Heavy Load Cast Iron Machine PartSpace needed for vertical mill is much less than a closed circuit ball mill of same capacity As separator is integral part of the mill itself, the number of auxiliary equipments are less Total power consumption for grinding circuit as a whole is also less by about 30% compared to closed circuit ball mill in spite of higher fan powerRaw Material DryingGrinding Cement Plant OptimizationLow energy, the powder consumption of vertical mill is 20%30% less than that of ball mill With the incensement of moisture of the raw material, the powder consumption will decrease obviously The vertical mill saves 30%40% of energy consumption compared to the ball mill Vertical mill has less noise than ball mill, about 2025dBVertical Cement Mill
.jpg)
Google Traductor
El servicio de Google, que se ofrece sin costo, traduce al instante palabras, frases y páginas web del inglés a más de 100 idiomas2014年1月1日 Two mill systems are employed for most coal grinding applications in the cement industry These are, on the one hand, vertical roller mills (VRM) that have achieved a share of almost 90% and, on (PDF) MPS mills for coal grinding ResearchGateDIFFERENT MILLS REQUIRE DIFFERENT AMOUNTS OF MEDIA •BASED UPON WORKING VOLUME OR TOTAL VOLUME •Mills such as the Immersion Mill have a fixed amount determined by size of the basket •Steel Ball Mill 333% •Open Head Sand Mill 3545% •Ceramic Pebble Ball Mill 50% •Dry Grind Batch Attritor 4560% •Wet Grind Batch Attritor 3845% •Continuous How to Choose the Correct GRINDING MEDIA PCI MagVertical roller mill specific grinding energies were lower than those for a ball mill at all product sizes, and when estimates of classification energy and scaleup of the VRM are included, the specific energy for the vertical roller mill is up to 35% lower than for a ball mill in closed circuitPerformance of the vertical roller mill in a mineral processing
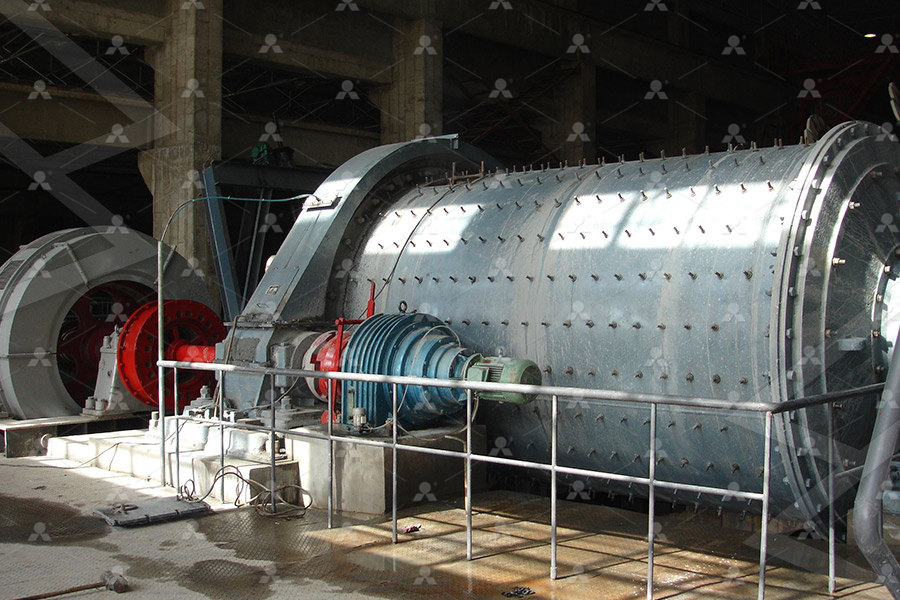
Vertical Mill Calculations PDF Mill (Grinding) Nozzle
The document discusses the layout, calculations, components, and heat balance of a vertical roller mill (VRM) There are two basic layouts product collection in cyclones or a filter Key calculations include power consumption, grinding pressure, and heat balance Important internals are the nozzle ring, which controls material fall through its area and velocity, and the dam ring, Another type of ball mill is used to an increasing extent, where the mill is vibrated instead of being rotated, and the rate of passage of material is controlled by the slope of the mill The ball mill is used for the grinding of a wide range of materials, including coal, pigments, and felspar for pottery, and it copes with feed up to about 50 mm in sizeBall Mill an overview ScienceDirect TopicsThe cement raw material mixtures are ground, dried, and classified in the Pfeiffer vertical roller mill For drying the material, hot gases are directed into the mill Product fineness can be adjusted within a wide range (0063 to 02 mm)Raw mills for all requirements Gebr PfeifferCement production globally is estimated at 42 billion tons in 2019, and cement grinding consuming approximately 20 percent of the total available electrical energy (Ghalandari, Majd, Golestanian, 2019; A I Okoji, Anozie, Omoleye, Taiwo, Osuolale, 2022b)Consequently, cement plants consume an average of 100 kWh per ton of cement produced, with twothirds of Assessment of the thermodynamics efficiency of a cement vertical
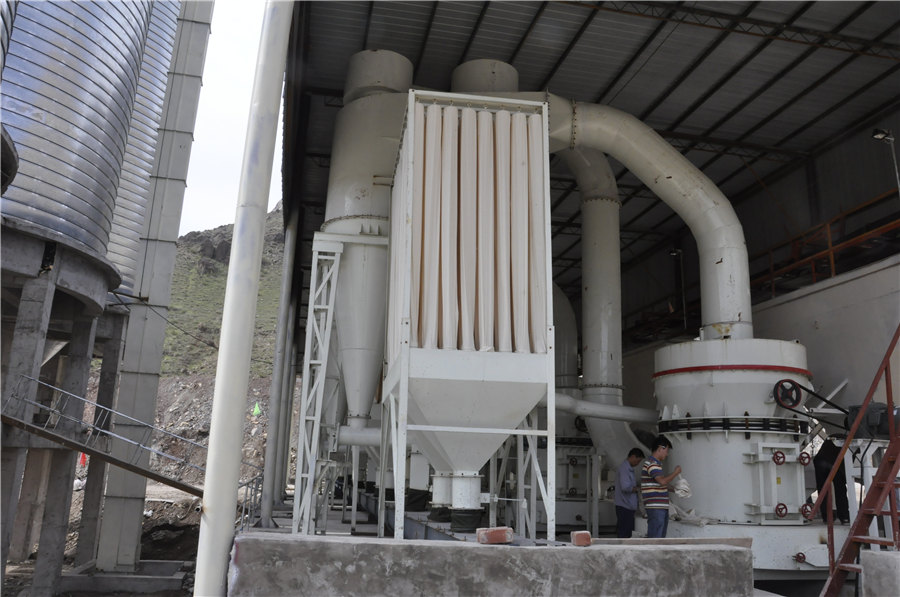
ANALISA KINERJA ALAT VERTICAL RAW MILL PABRIK II PT
Vertical Raw Mill has a heat efficiency of 90,09% with a heat loss 9,91% which indicates that this equipment is stillefeective to use because its is witin the tolerance limit of heat loss, which 2022年11月1日 Vertical Coal Mill The specific material resilient to abrasion is required to extend operating services C ratio of about 10 and up to 10 wt% MoWEAR ANALYSIS OF VERTICAL COAL MILL PLATE ResearchGate