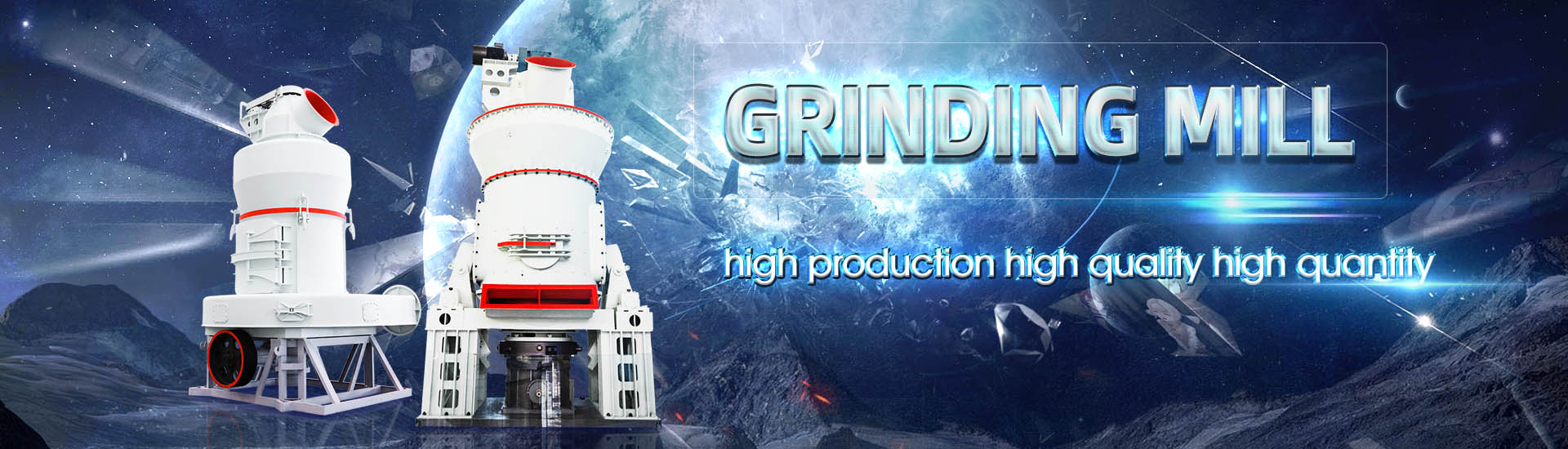
Ore powder plant process and investment
.jpg)
Mineral Processing Plant Design University of Technology, Iraq
Ore characteristics are a critical element in both crusher selection and plant design Dry ores require greater provisions for dust suppression and collection, including dust enclosures around screens, sealing on conveyor skirts, and vacuum and washdown systemsGuidelines for mineral process plant development studies P R Whincup* This paper presents guidelines for studies required for the development of mineral processing facilities from initial Guidelines for mineral process plant development studies AusIMM2014年6月1日 Ore characterizationrelated losses continue to represent a major cost factor for mining, routing, processing and tailings handling Debottlenecking of existing or recent design Ore characterization, process mineralogy and lab automation a 2019年8月16日 It is now possible to design (offline) extremely flexible and robust mineral processing and metal extraction plants using IT platforms (for example, TCS PREMAP) which Future of Mining, Mineral Processing and Metal Extraction Industry
.jpg)
Iron ore pelletization ScienceDirect
2022年1月1日 A brief introduction to recent developments in iron ore pelletizing is provided in this chapter, including the world output of fired pellets, pellet production processes, 2021年9月6日 We describe a micronsized ore powder production by propulsion and rapid unloading of highpressure gas The research consists of three parts Firstly, we obtain the Micronsized ore powder production by propulsion and rapid The iron ore pelletizing process consists of three main steps: 1 Pelletizing feed preparation and mixing: the raw material (iron ore concentrate, additives anthracite, dolomite and binders are Iron Ore Pelletizing Process: An Overview IntechOpen2024年8月15日 A mineral processing plant is a place dedicated to processing ores, converting raw ores extracted from mines into highgrade mineral products or metals through a series of Mineral Processing Plants: What You Need to Know
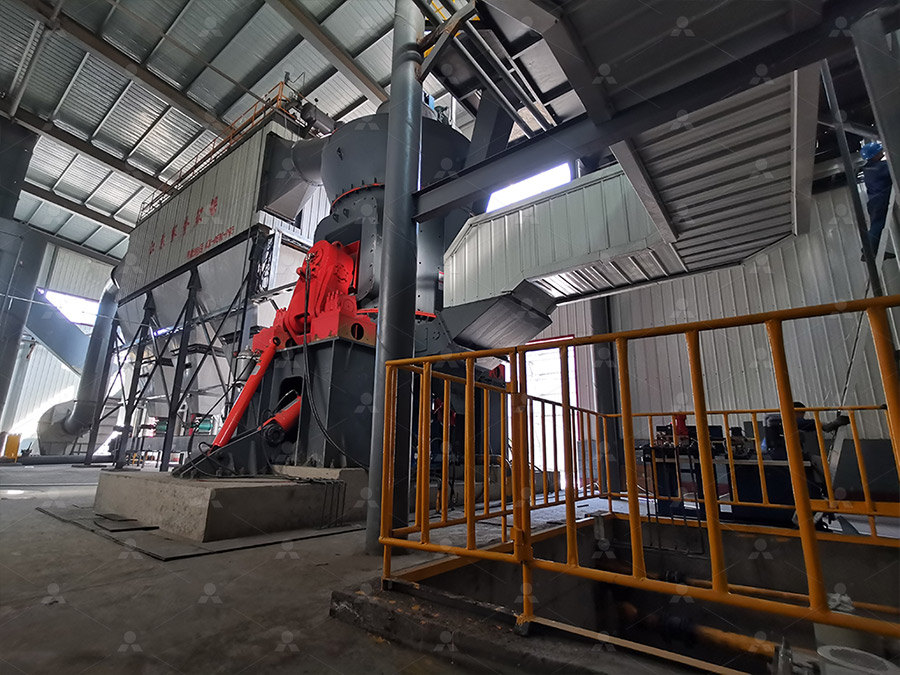
Copper Introduction And Ore Crushing JXSC Mineral
2024年6月13日 The third stage: ore dressing – mixed flotation process The copper ore powder that meets the requirements is fed into the flotation machine for mixed flotation The copper ore powder after flotation is fed into the dryer 2013年3月16日 The first plant of Midrex process came into operation in May 17, 1969 at Oregon Steel mills in Portland, Oregon The coal based rotary kiln process combines the Republic SteelNational Lead (RN) process developed Direct Reduced Iron and its Production Processes – 2023年5月6日 In the flotation process of copper ore processing, the collector adsorbed on the surface of the target mineral, which increases the hydrophobicity difference between valuable and gangue mineralsThen the mineral particles Copper Ore Production Process JXSC MineralIron Ore Mining (EOU) Manufacturing Plant, Detailed Project Report, Profile, Business Plan, Industry Trends, Market Research, Survey, Manufacturing Process, Machinery, Raw Materials, Feasibility Study, Investment Opportunities, Cost of TechnoEconomic Feasibility Report, Identification and Selection of Plant, Process NIIR Project Consultancy Services:Iron Ore Mining (EOU
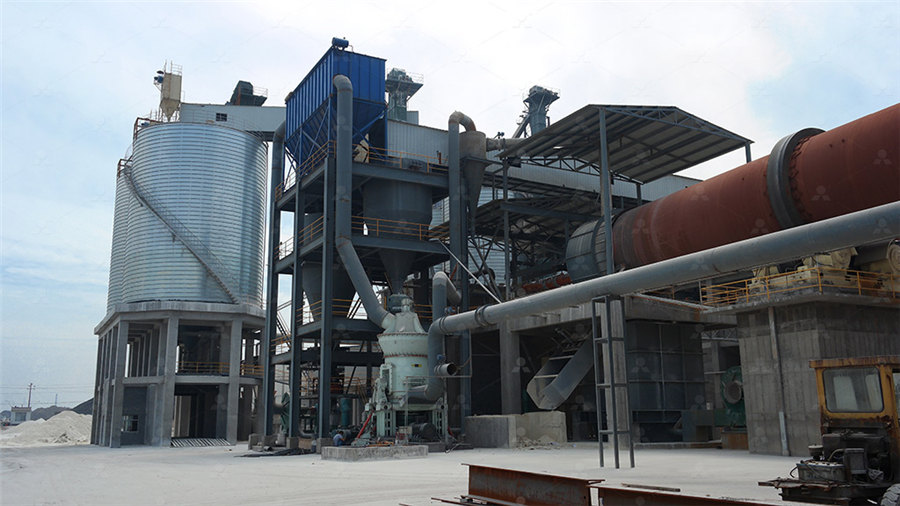
Vale and Jinnan Steel Iron Group annouce investment in iron ore
2024年10月28日 The Sohar Concentration Plant, scheduled to commence operations by mid2027, will process 18 million tons of lowgrade iron ore annually, producing 126 million tons of highgrade concentrate Vale will invest US$ 227 million to connect the plant to its agglomerate facilities in the regionManganese (Mn) is the twelfth most abundant element in the Earth’s crust Amongst some 300 minerals containing manganese, only about a dozen are of economic significance Manganese is a silverygray metal that resembles ironIt is hard and very brittle, difficult to Manganese Ore Process Plant JXSC MineralReasonable and efficient process flow: The production line usually adopts the process flow of “crushinggrindingore dressingsmelting”, and each link is carefully designed to ensure that the ore can be fully processed and extracted Economical investment and large production capacity: The overall investment of the gold ore dressing production line is economical, with a small Gold Ore Processing Production Line TAYMACHINERYIn general, the process of construction and commissioning of a mining and processing plant often requires an initial investment in excess of 250300% of the annual production volume Of course, specific numbers vary widely and are largely determined by the type of deposit and the method of production, as well as the specific need for equipment for processing mineral raw materialsProject finance for mining and processing plant: investment loan
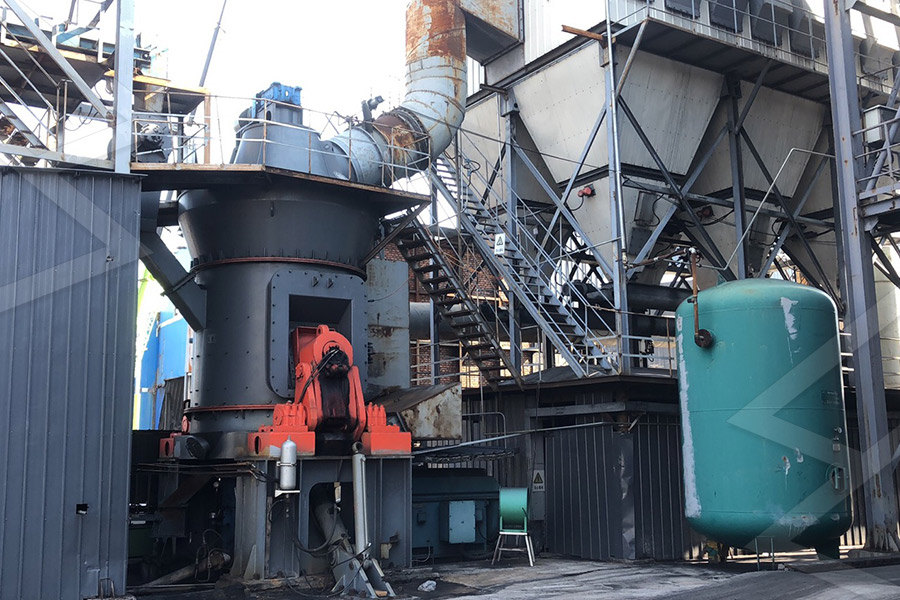
Iron Ore Beneficiation Plant, Iron Ore Magnetic Separation Process
Iron ore beneficiation process including ilmenite, magnetite, limonite etc ore processing plants and equipment as per customer's needs Skip to content JXSC Machinery Us +86 Home No work/ Not buy or sell minerals/ No investment, cooperation) Your Name Your Phone or WhatsApp Processing 21 Midrex Process Midrex is the most successful gasbased DR process; it is a continuous process It is basically a countercurrent process where a hot and highly reducing gas (95vol% of this gas mixture being hydrogen and carbon monoxide with a ratio of H 2:CO varying from 15 to 16) reduces lump iron ore or pellets to metallic iron as the metallic charge descends through Direct Reduction Process an overview ScienceDirect Topics2023年3月13日 The bulk ores are crushed to about 12cm by a jaw crusher or a cone crusher Then the crushed materials are sent to the grinding equipment, and the final particle size of the copper ore is reduced to 01502mm Copper ore How to Process Copper Ore: Beneficiation Methods THE ORE ROUTE Viewing the process from the ore route, a pneumatic conveying system transports the iron ore fines to the fluidizedbed reactor tower The fine iron ore is then charged to a 3stage fluidizedbed reactor series A reduction gas generated in the meltergasifier flows through each of the fluidizedbed reactors in counter flowTHE FINEX® PROCESS ECONOMICAL AND ENVIRONMENTALLY
.jpg)
Iron Ore Pelletizing Process: An Overview
Therefore, the reasons why new investments in pelletizing capacity are likely to occur are the following [29]: • the pelletizing process is currently the most widely used option for producing suitable agglomerates for ironmaking applications Sized iron ore for DRI plant 176 tons ROM ore for washing 125 tons Noncoking coal for SI plant 1006 tons 63378 Dolomite for SI plant 0075 tons 4725 Fuel oil for SI plant 05 litres 33 Sized iron ore will be used for the production of RANJITPURA INFRASTRUCURE PRIVATE LIMITED (RIPL) IRON ORE 2016年3月30日 In book: Encyclopedia of Iron, Steel, and Their Alloys (pppp 10821108) Chapter: i) Direct Reduced Iron: Production; Publisher: CRC Press, Taylor and Francis Group, New York(PDF) i) Direct Reduced Iron: Production ResearchGate12TPH Lead Zinc Copper Ore Process Plant in Morocco and the classifier can classify and screen the copper ore to release the required ore powder 3 Gravity separation: shaking tables Notes: in order to reduce the investment in the early stage of equipment, 12TPH Lead Zinc Copper Ore Process Plant in Morocco
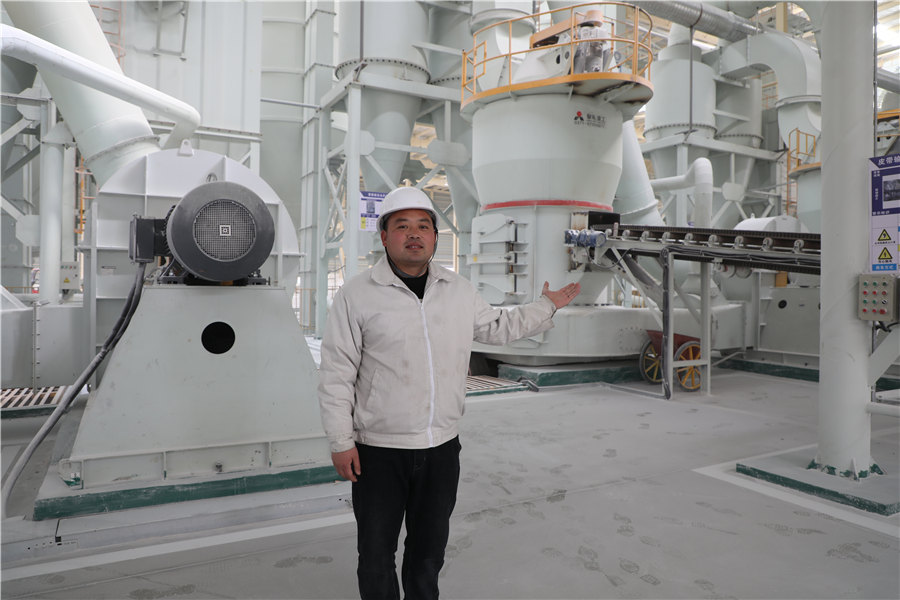
ENERGYEFFICIENT TECHNOLOGY OPTIONS FOR DIRECT REDUCTION OF IRON PROCESS
30 Energyefficient Technologies in Direct Reduction of Iron Process 17 31 Waste Heat Recovery for Power Generation 18 32 Iron Ore Preheating Rotary Kiln Using Waste Heat Recovery System 20 33 Coal Gasification for Partial Substitution in Rotary Kiln 22 34 Waste Heat Recoverybased Absorption Chiller 23Detailed Project Reports Profiles on Powder Coating Paints Manufacturing Plant, Detailed Project Report, Profile, Business Plan, Industry Trends, Market Research, Survey, Manufacturing Process, Machinery, Raw Materials, Feasibility Study, Investment Opportunities, Cost Powder Coating Paints Manufacturing Plant, Detailed Project 2023年12月15日 Introduction Ore extraction and processing remain highly relevant today, pivotal in the global economy and technological advancement As the backbone of the manufacturing and construction industries, titanium mining techniques and subsequent processing are crucial for producing a wide array of essential materials, from steel and aluminum to rare Titanium Ore Plant: Efficient Mining and Processing MethodsTin From Tin Ore Manufacturing Plant, Detailed Project Report, Profile, Business Plan, Industry Trends, Market Research, We also offer selfcontained PreInvestment and PreFeasibility Studies, Study, Market Research Study, Preparation of TechnoEconomic Feasibility Report, Identification and Selection of Plant, Process, Equipment, NIIR Project Consultancy Services:Tin From Tin Ore
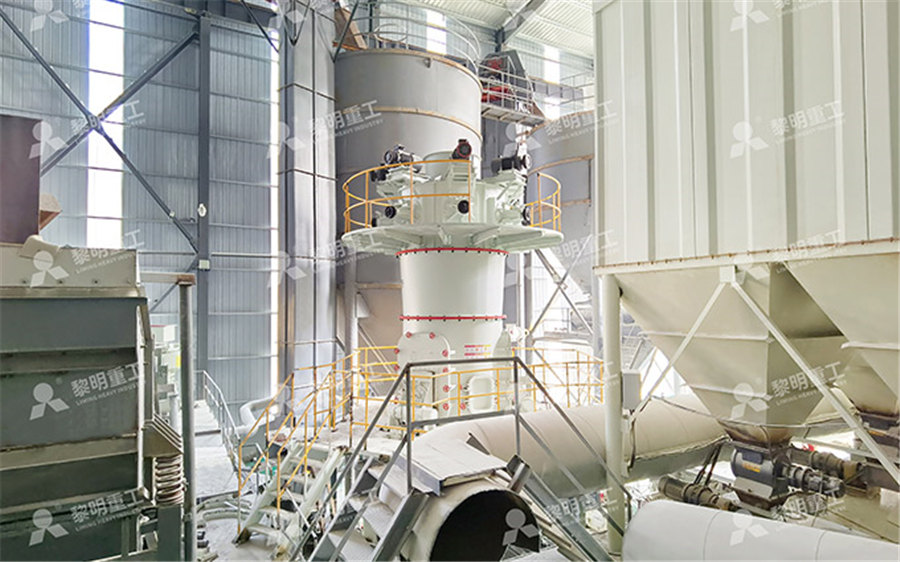
How to Process Titanium Ore (A Stepbystep Guide)
2023年10月27日 From the blog Titanium: Metal of 21st Century, we learned that titanium has always been an essential metal due to its wide range of applications in different industriesThe rising market demand for titanium products such as 2016年2月29日 Some of the metallurgical relationships that must be considered from the testwork program as follows: ore grade relationship to gold recovery, crushing and grinding parameters and their relationship to the ore variability in Gold Extraction Recovery ProcessesTechnological processes of ore dressing at mining and processing plants Natural raw materials of mineral origin usually do not have properties that allow direct commercial use For example, most nonferrous metals are currently obtained Mining and processing plant design ESFC 2023年10月27日 Ilmenite is the most important titanium ore It is often used for the production of the metal titanium and titanium dioxide (FeTiO 3) accessory products, such as paint, paper, titanium white (white pigment), plastics, fabrics, etc This blog will introduce the ilmenite beneficiation process and processing plantIlmenite: An Ore of Titanium Beneficiation and Plant
.jpg)
Recovery and separation of iron from iron ore using innovative
2017年1月1日 Therefore, the generated waste iron ore beneficiation plant tailings (IOBPT) containing 5696% Fe(T), 407% Al2O3, 723% SiO2 and 438% of LOI (contributed mainly from clay and goethite) can be The customer requires that the impurities on the surface of the ore be washed first to remove iron impurities, and the final concentrate recovery rate must reach 95% JXSC has developed a complete set of tin ore process plant equipment lines based on customer needs The following is the specific process flow: 1 Washing stage: trommel scrubber20TPH Alluvial Rock Tin Ore Process Plant In ZimbabweEngineering design of processing plants ESFC Investment Group cooperates with leading European contractors, equipment manufacturers and technology suppliers for the mining industry We have sufficient experience in in financing plants for processing of polymetallic ores, uranium ores, phosphate ores, etc Professional engineering services include:Mining and processing plant construction ESFC Investment 2024年3月16日 The sintering process is an intricate system with a protracted process flow The steps in the manufacturing line are primarily composed of the ingredients and mixing process, the sintering operation process, and the treatment of the sintered ore [39, 40]22 Important parameters and characteristics of sintering process As shown in Fig 2, all variables affecting Application of deep learning in iron ore sintering process: a review
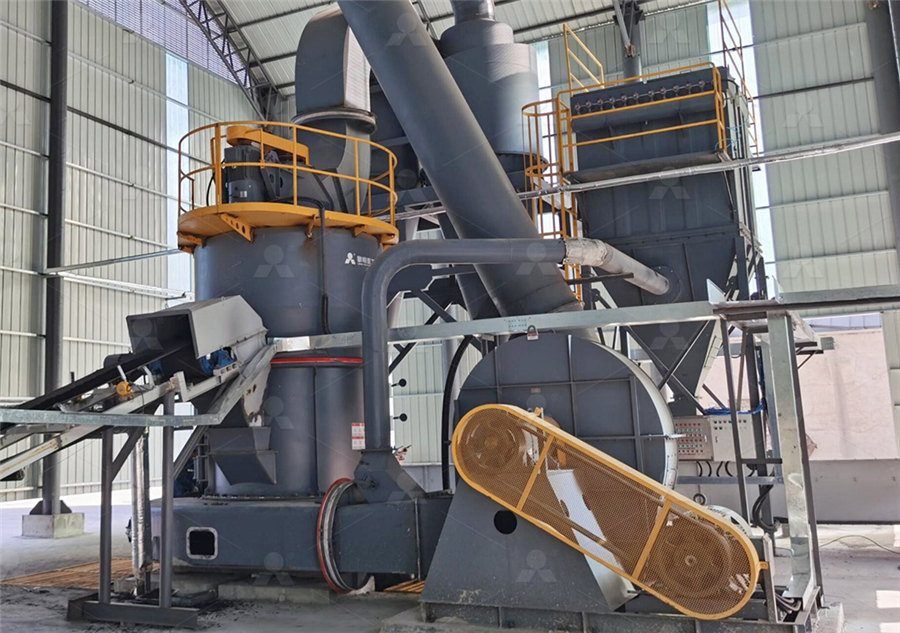
Mastering Oxidized Gold Ore Processing Techniques JXSC
2024年7月8日 The processing of oxidized gold ore is a challenging and complex process that needs a lot of expertise in the physical and chemical characteristics of the ore and the available technology As technology improves the techniques used in the extraction and beneficiation of gold ores have improved to become more efficient and less damaging to the environment2014年11月26日 Iron Ore Pellets and Pelletization Process satyendra; November 26, 2014; 0 Comments ; bentonite, binder, Grate kiln, induration, Pelletization Pellets, straight grate,; Iron Ore Pellets and Pelletization Process Pelletizing of iron ore was started in the 1950s to facilitate the utilization of finely ground iron ore concentrates in steel productionIron Ore Pellets and Pelletization Process IspatGuru2023年7月5日 To assist producers in getting their operations up and running, as well as optimizing their output, FEECO offers process training to pelletizing plants The training process While FEECO provides training for a range of Process training for pelletizing plants Processing 2012年10月19日 Technoeconomic Evaluation of Iron Ore Pellet Manufacturing Processes in India and Justification for new units in Odisha(PDF) Technoeconomic Evaluation of Iron Ore Pellet
.jpg)
Iron Ore Sintering SpringerLink
2023年6月8日 Iron ore sintering is the iron ore powder agglomeration process that changes fine iron ore powder into the lumpy ironbearing raw material used for blast furnace ironmaking Hightemperature process and addition of alkaline flux will improve metallurgical performance of ironbearing raw materialIn conclusion, grinding gold ore into powder is a critical step in the gold extraction process that requires careful consideration of equipment and techniques By understanding the importance of efficient grinding and utilizing the right tools, miners can significantly enhance their gold recovery rates and reduce operational costsWant To Grind Gold Ore Into Powder? Here’S How! Stone 2021年1月1日 Currently, approximately 14 billion tons per year of iron ore tailing wastes (IOT) are generated, mainly in Australia, Brazil, and China This work describes the characterization and application Iron Ore Tailings: Characterization and Applications2021年4月9日 It can process fluorite ore with a particle size of 050mm Related auxiliary equipments are crushers, vibrating screens, etc If you are interested in a fluorite ore gravity separation plant, please contact us Here we introduce you to the gravity separation process of fluorite ore Fluorite ore gravity separation process flow chartFluorite Ore Processing Flowsheet and Washing Plant
.jpg)
Gold Refinery Process: From Raw Material to Pure Gold
In the gold refinery process, after the gold ore is extracted from the ground, it undergoes crushing and grinding stages to prepare it for further processing These steps are crucial in breaking down the ore into smaller fragments and reducing it to a fine powder, making it easier to extract the valuable gold particlesThe possibility of directly using powder, granular ore, and coal was confirmed, and necessary equipment specifications were Investment cost reduced by 35% 2 Molten iron production cost decreased by 19% 3 Fig 1 Process flowchart for DIOS pilot plant (per 1,000kg of molten iron) Coal 952kg Flux 80kg Iron ore 1450kg Preheating furnace3A3 Direct Iron Ore Smelting Reduction Process (DIOS)This setup is a 510tph vein gold ore crushing plant, main equipment and flow details as follows: 1 The trough feeder it can feed evenly to the crusher 2 The jaw crusher preliminary crushing of large rocks can also be made mobile type as requested 3 The hammer crusher output size is adjustable like 10mm,5mm, etc For this project it’s grind materials to 02mm, it also can be Hard Rock Gold Processing Plant JXSC Machinery2022年2月10日 With the Circored process, Metso Outotec provides an alternative process route for the reduction of iron ores, using hydrogen as the sole reductant and fine ore instead of pellets as feed material Circored is currently the only process for iron ore direct reduction based on pure hydrogen and has proven its functionality and performance in an industrialscale Circored Fine Ore Direct Reduction Plus DRI Smelting: Proven