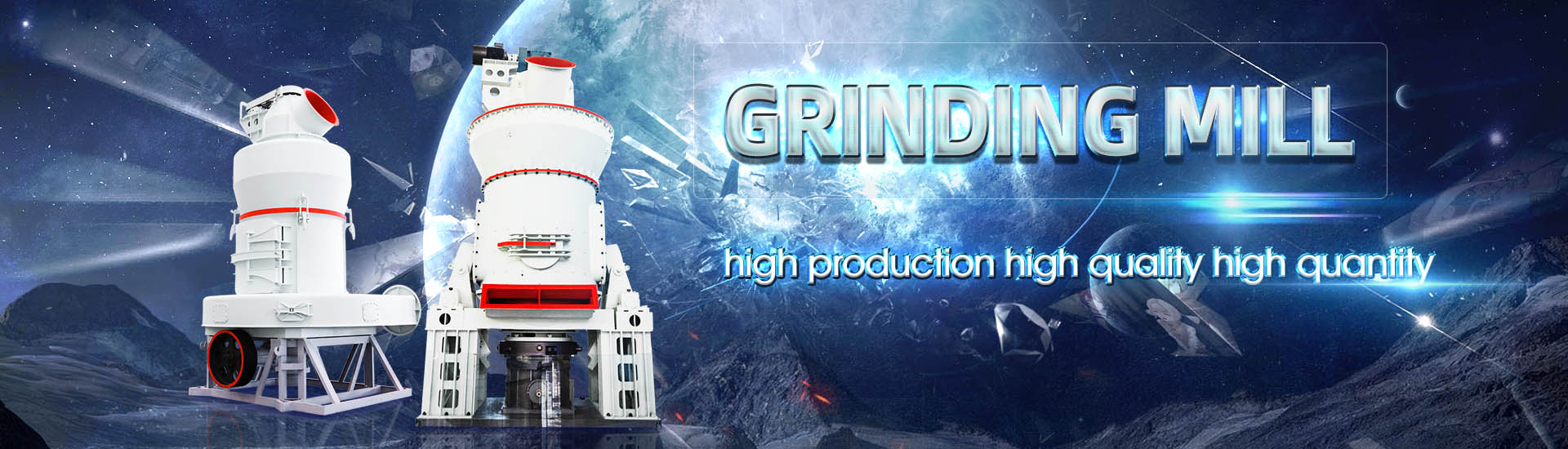
Limestone gypsum desulfurization equipment manufacturer
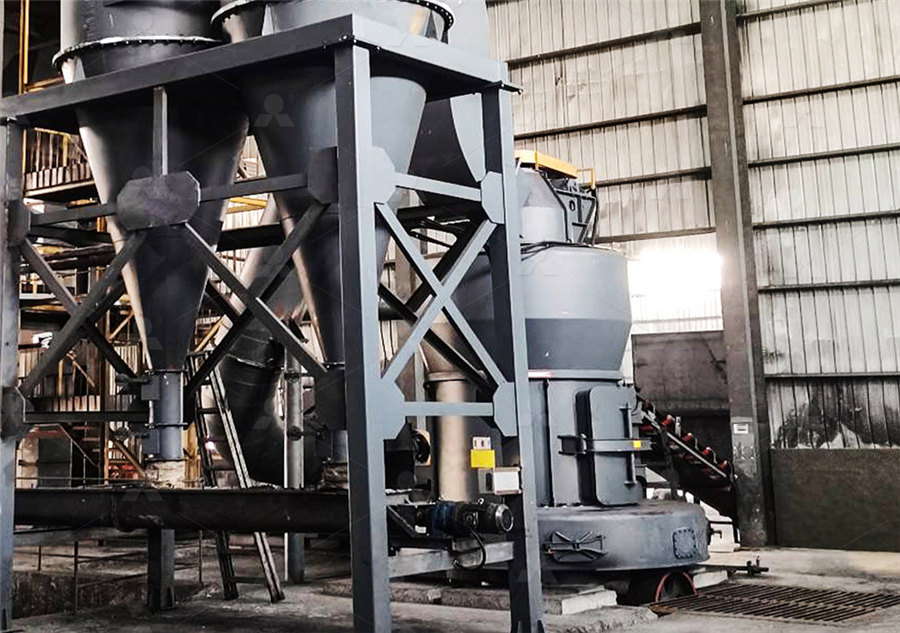
Flue Gas Desulfurization (FGD) Plants Mitsubishi Power
The flue gas desulfurization (FGD) plant removes sulfur dioxides (SO 2) from flue gas produced by boilers, furnaces, and other sources Mitsubishi Power effectively contributes to the Useful Byproducts: Our lime/limestonebased system produces useful byproducts like gypsum, promoting circular economy principles Specially Designed Spray Tower: Our spray towers minimize material buildup, ensuring low downtime Best Flue Gas de Sulphurization System SolutionANDRITZ provides you with a full range of efficient wet flue gas desulphurization (FGD) technologies to reduce your sulphur oxides (SOx) emissions Depending on the process, industry and level of SOx outlet emissions to be met, Desulphurization (DeSOx) AndritzSteuler flue gas desulfurization units based on the limestone/gypsum process are typically used in the following industries: Coal and fueloil fired industrial cogeneration (CHP) plants; Small to mediumsized power stations; General DeSO x plants/ flue gas desulfurization plants Steuler
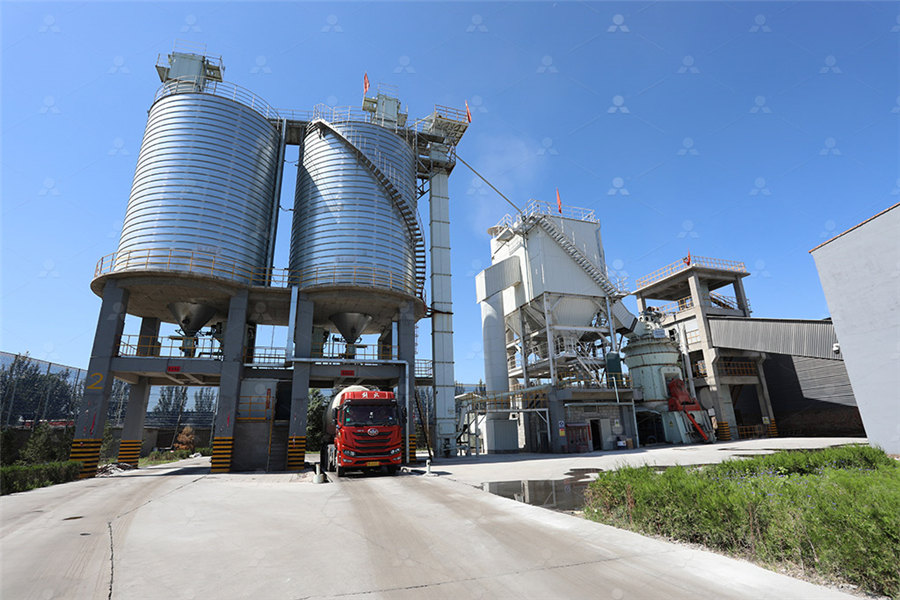
Wet flue gas cleaning, limestone FGD Andritz
Limestone flue gas desulphurization (FGD) units are wellproven and costeffective ANDRITZ provides novel scrubber system (FGDplus) that maximizes SO2 and dust removal while 2021年11月1日 Flue gas desulfurized gypsum mainly comes from thermal power plants, smelters, and largeenterprise boilers, and contains industrial byproducts produced through a wet desulfurization combustion process, where SO 2 gas and lime slurry react under strong oxidation conditions The main component of this gypsum is calcium sulfate dihydrate, which also Production and resource utilization of flue gas desulfurized gypsum 2017年7月1日 Among the reasons for the success of the wet FGD system, there is the possibility of recovering a new product to be allocated on the market namely gypsum (He and Lee, 2014)In fact, the synthetic gypsum suitable for several applications such as wallboard manufacturing is the byproduct of the SO 2 scrubbing process for scrubbers using lime or Enhancing the recovery of gypsum in limestonebased wet flue 2023年3月15日 The equipment consisted of a bubbling reactor, gas supplier, and analytical apparatus New limestonegypsum flue gas desulfurization technology International Conference on Energy and Environment Technology, 2009 (2009), pp 7881, 101109/ICEET2009485Desulfurization characteristics of limestone slurry with added
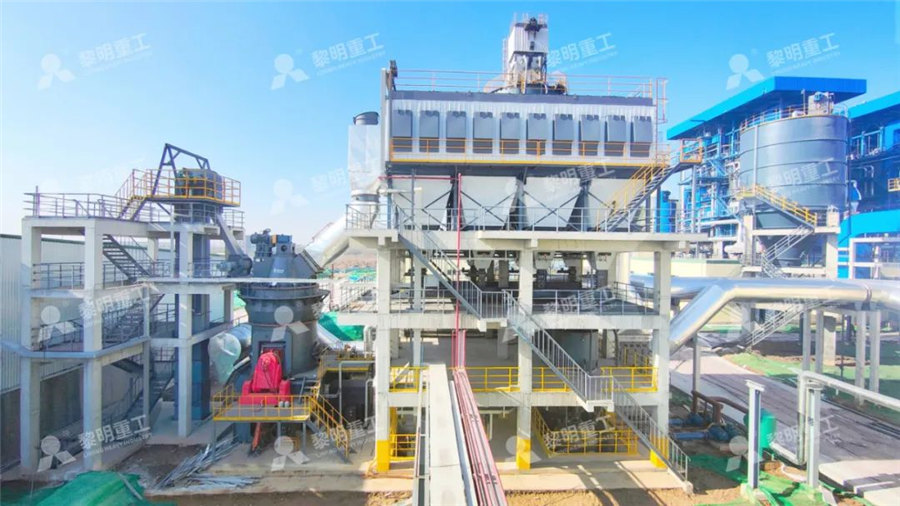
Review of Design, Operating, and Financial Considerations in
2015年7月27日 3 Flue Gas Desulfurization Technologies Flue gas desulfurization is an efficient method for the reduction of the sulfur dioxide emissions Citation 2 Many processes are available in the market, such as (a) wet scrubbers, (b) spray dry scrubbers, (c) sorbent injection, (d) regenerable processes, and (e) combined SO 2 /NO X removal processes The different flue 2019年6月1日 Applying the advanced technology of CPS to the (WFGD) system can improve the whole system operation efficiency and reduce energy waste, and has good utilization value for promoting the intelligent upgrade of the factory The limestonegypsum wet flue gas desulfurization system has been widely used due to its remarkable desulfurization effect, but Limestonegypsum wet flue gas desulfurization based on Cyber 2024年8月13日 This blog post is the third in a threepart series that discusses flue gas desulfurization (FGD) The first post provides overviews of sulfur dioxide (SO 2) and emissions regulations, the FGD industry, and global FGD market trendsThe second post provides highlevel overviews of wet, semidry, and dry FGD technologies with respect to SO 2 capture Flue Gas Desulfurization: Detailed Process Overview2018年12月1日 This wet FGD unit was designed by IHI Corporation (Japan) with desulfurization efficiency over 96% for two pulverized coal boilers in that petrochemical company, and it mainly consisted of five systems including limestone preparation system, boiler air and gas system, absorption system, gypsum dewatering system, and waste water treatment systemCorrosion evaluation of one wet desulfurization equipment –
.jpg)
LimestoneGypsum Wet Flue Gas Desulfurization Wastewater
2021年2月1日 LimestoneGypsum Wet Flue Gas Desulfurization Wastewater Treatment Tingting Ni 1,2, Yunzhong Wang 2, Chenghui Huang 2, Dongsheng Jiang 1 and Qingyu Liu 1 Published under licence by IOP Publishing Ltd IOP Conference Series: Earth and Environmental Science, Volume 651, 3rd International Conference on Green Energy and Sustainable 2) and limestone (CaCO 3) Rosemount Analytical pH equipment is used to control the feed rate of these chemicals PROCESS After fly ash removal, the flue gas (seen in Figure 1) is bubbled through the scrubber, and the slurry is added from aboveThe lime or limestone reacts with the SO 2 in the flue gas to create insoluble calcium sulfite (CaSO Lime / Limestone Wet Scrubbing System for Flue Gas Desulfurization2024年3月20日 Desulfurization wastewater is industrial wastewater with a high salt content, high metal ions, and high hardness produced by flue gas desulfurization of the limestonegypsum method in coalfired power plants This paper summarizes the source of desulfurization wastewater, water quality characteristics, water quality impacts, and other factors, combined Current Status of Zero Liquid Discharge Technology for Desulfurization To reduce waste and improve the overall efficiency of FGD scrubber systems, the collection and processing of byproducts are often employed For example, when lime is used as the neutralizing agent, gypsum (CaSO₄) is produced, which can be utilized in construction, such as in the manufacturing of drywallFlue Gas Desulfurization (FGD) Scrubber Systems
.jpg)
Advancement of Environmental Sustainability: A Comparative
2024年3月18日 Plant in Chongqing introduced two sets of limestone (lime) – gypsum flue gas desulfurization equipment from Mitsubishi Heavy Industries in Japan, equipped with two 360MW generator sets, achieving a desulfurization efficiency of 95% and producing about 400,000 tons of gypsum byproducts annuallyFlue gas desulfurization plants, wet systems, gypsum dewatering, gypsum recovery, vacuum belt filters, environmental, coalfired power plant equipment, new technology for coalfired power plants ABSTRACT Recovering gypsum from flue gas desulfurization (FGD) plants is becoming more important as theCOMPARISON OF GYPSUM DEWATERING TECHNOLOGIES AT FLUE 2021年11月22日 Limestonegypsum Wet Desulfurization Wastewater Shanshan Zhang, WU Qiaoling, JIN Yinjia et alDesign of Air Floating EGR Water Treatment Device Fangyong Wang and Zhanguang WangStudy on the composition of resistant organics in winery wastewater and their degradation technique J C Li, Z X Chen, W X Xia et alVLVRI7REDFFR:DVWHZDWHU Limestonegypsum Wet Desulfurization Cement manufacturing utilizes a variety of naturally occurring raw materials such as limestone, clay, shale, sand, iron ore, and gypsum as the main ingredients In addition, because of chemical compatibility, today as in the past, alternative materials such as industrial wastes, byproducts, and other marginal materials can be easily and economically utilized as raw material in cement Use of Alternative Materials in Cement Manufacturing
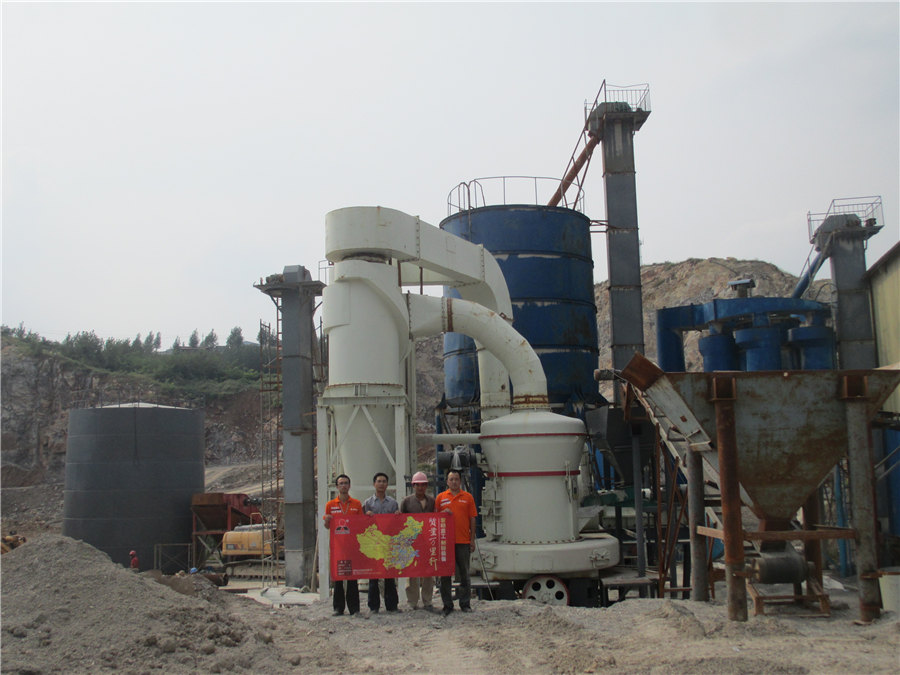
Modeling of the wet flue gas desulfurization system to utilize low
2020年11月11日 Wet flue gas desulfurization was simulated to improve gypsum production using lowgrade limestone Highgrade limestone with 94 wt% CaCO3 content is used for producing gypsum with 93 wt% purity, but owing to the resource depletion of highgrade limestone, lowgrade limestone should be replaced as an alternative However, lowgrade This article takes a 5000t/d clinker cement production line as an example to introduce the design scheme of limestonegypsum desulfurization and return to the absorption tower during operation of the equipment flushing water, CLIRIK has a firstclass manufacturing base with standardized and intelligent production lines CLIRIK's Limestonegypsum Desulfurization Process in Cement Plant2002年4月1日 In this study, cement, made of flue gas desulfurization (FGD) gypsum obtained in a desulfurization process using limestone sludge, was manufactured then, experiments were conducted to identify the Optimum Values of Process Parameters of the “Wet Limestone 2019年3月13日 Introduction Sulfur dioxide (SO 2) is one of the major pollutants contributing to frequent hazy weather in ChinaA large amount of SO 2 in the atmosphere comes from coal combustion As the amount of coal for power generation accounts for 45% of the total coal consumption in 2015 (National Bureau of Statistics [NBS] Citation 2017), the Chinese Full article: Modeling and optimization of wet flue gas desulfurization
]@S0{UDKK%G24F3JGHC.jpg)
Study on Biological Treatment of Limestonegypsum Wet Desulfurization
2019年8月9日 Physico chemical Pilot Study Of Wet Limestonegypsum Method For Flue Gas Desulfurization Wastewater Environmental Pollution and Public Health(EPPH) Special Track within iCBBE2012Advances in Engineering Research, volume 112 4th International Conference on Renewable Energy and Environmental Technology (ICREET 2016) Optimization of Limestonegypsum Wet Flue Gas Desulfurization System Jing Han, (PDF) Optimization of Limestonegypsum Wet Flue Limestone Flue Gas Desulfurization Pilot Plant 《Industrial Engineering Chemistry Research》, 2008, 47(21):82638272 14 GMD Celso,D Karatza,A Lancia,D Musmarra,M Prisciandaro LimestoneGypsum Flue Gas Desulfurization Process: Modeling of Catalyzed Bisulfite Oxidation International Conference on Chemical Process , 2013, 32: Optimization of Limestonegypsum Wet Flue Gas Desulfurization2023年8月22日 Flue gas desulfurization (FGD) gypsum is a byproduct of the combustion of coal, used for electricity generation This material is generated during the process of scrubbing flue gases from power plants to remove sulfur dioxide emissions, which contribute to acid rain and other environmental problemsA comprehensive review of flue gas desulphurized gypsum:
.jpg)
Comprehensive evaluation of flue gas desulfurization and
2020年8月15日 Postcombustion flue gas desulfurization and denitrification technologies are essential in achieving the full compliance of fine particulate matter (PM25, aerodynamic diameter less than 25 μm) air quality standards by 2030 in China as sulfur dioxide (SO2) and nitrogen oxides (NOX) are the main precursors of PM25 Some studies have addressed the The final FGD waste is wallboardgrade gypsum Limestone Forced Oxidation FlueGas Desulfurization Process Note: FGD = fluegas desulfurization By controlling the gypsum quality in the dewatering step, a wallboardgrade gypsum can be produced The majority of scrubber installations in Europe and Japan generate gypsum for reuseWet Flue Gas Desulfurization (FGD) ARCOR EpoxyPDF On Oct 1, 2009, Shengyu Liu and others published New LimestoneGypsum Flue Gas Desulfuization Technology Find, read and cite all the research you need on ResearchGateNew LimestoneGypsum Flue Gas Desulfuization Technologyequipment, which concentrates the waste From the wastehandling equipment, the concentrated waste is sent for disposal (ponding or stacking) or, alternatively, processed to produce a salable gypsum (calcium sulfate dihydrate) byproduct The practical wet FGD processes are described in the following sections Limestone Forced OxidationFlue Gas Desulfurization: The State of the Art Taylor Francis
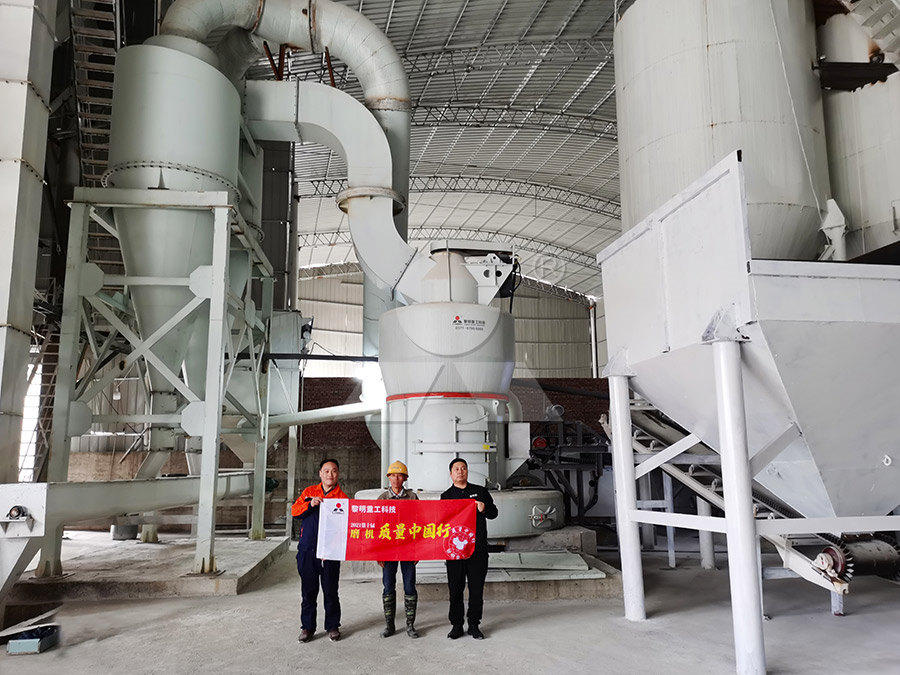
New Wet FGD Process Using Granular Limestone ResearchGate
2002年6月1日 A new wet limestone−gypsum process for flue gas desulfurization (FGD) has been developed The main difference compared to a conventional wet FGD process is the ability of the new process to matched desulfurization equipment, and in the production of generator sets retrofitted limestonegypsum desulfurization unit more than 75% of total installed capacity below 5% In the 1990s, FGD gypsum began to be widely used throughout the gypsum manufacturing, and large quantities of replacing natural gypsum FGD gypsum production in Advances in Utilization of Flue Gas Desulfurization Gypsumfired power plant combustion system, limestone gypsum flue gas desulfurization, equipment, process in this part and know the entire equipment name and their respective roles then make "static cognition system" This part mainly use thermal interaction icon, drags a group icon and display icon into flow line, the name, equipmentInvestigation of courseware design of flue gas desulfurization of 2024年4月19日 Limestone gypsum wet flue gas desulfurization process 2 Magnesium oxide desulfurization process The basic principle of magnesium oxide desulfurization is similar to that of limestone (lime) method, that is, the SO2 in 4 Flue Gas Desulfurization Process You Should Never
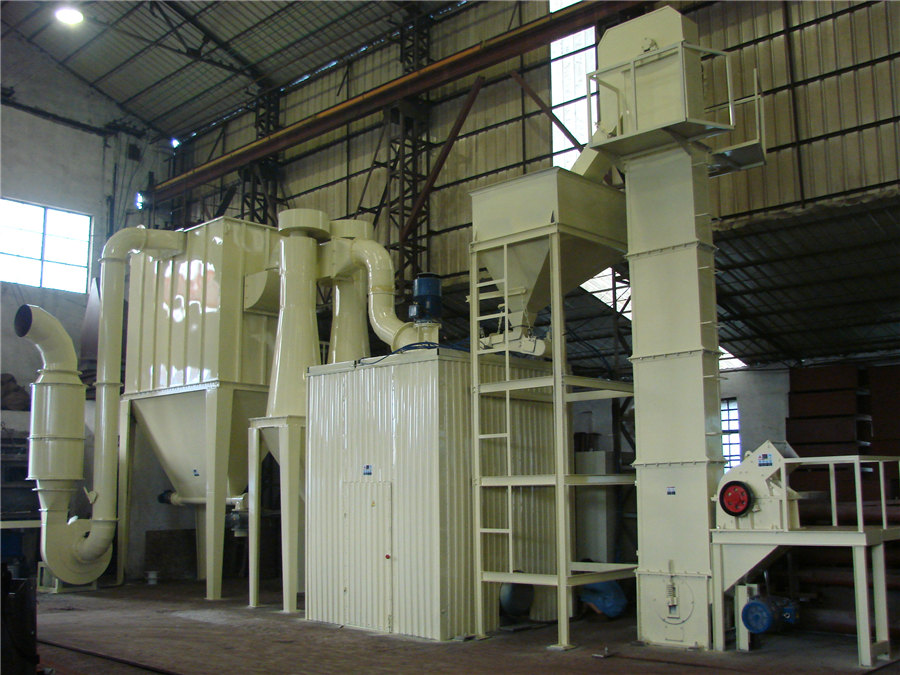
Application and Development Trend of Flue Gas Desulfurization
Rehan Jamil, Li Ming, Irfan Jamil, and Rizwan Jamil ISSN : 20289324 Vol 4 No 2, Oct 2013 289 Fig 3 3rd Generation of wetProcess Limestone/LimeGypsum Flue Gas Desulfurization System SchematicThere are many material handling equipment required for processing Limestone and Gypsum in this plant for which Zeus Engitech Private Limited got the order from Thermax Ltd in June, 2020 Zeus Engitech has supplied Flue Gas Flue Gas Desulfurization System Manufacturer Zeus 2021年12月31日 Limestonegypsum Wet Desulfurization Wastewater Shanshan Zhang, WU Qiaoling, JIN Yinjia et al Table 2 Main reagents and equipment Device name Model Manufacturer Major reagents Major reagents Mute adjustable oxygen pump SB948 Zhongshan City Song Bao ElectricQFKURQRXVXOWLYDWLRQDQG'RPHVWLFDWLRQRI Limestonegypsum Gypsum Powder Plant: Gypsum Grinding Mill Machine,Gypsum Mining Grinder Plant Equipment Home; Product; Application; Case; Service; About us; Contact; Currently the world's most technologically sophisticated desulfurization process is limestone Gypsum Powder Making Production Line Manufacturer
.jpg)
Easy Installation Steel Structure Silica Sand Limestone Desulfurization
Easy Installation Steel Structure Silica Sand Limestone Desulfurization Gypsum Rotary Dryer Machine, Find Details and Price about Rotary Dryer Machine Rotary Dryer Machine Dryer Equipment for Sale from Easy continuously enhancing product competitiveness to strive to become a leading enterprise in the machinery manufacturing industry 2023年7月4日 Gypsum briquetting machine mainly presses gypsum powder and desulfurized gypsum materials Desulfurization gypsum, also known as flue gas desulfurization gypsum, sulfur gypsum, or FGD gypsum, is an industrial byproduct obtained by desulfurization of flue gas generated after the combustion of sulfurcontaining fuel (coal, oil, etc)5 Types of Briquette Machines (With Budget Analysis)2019年5月23日 The desulfurization equipment for limestone (lime)–gypsum method mainly includes flue gas system (flue damper, fume reheater, and pressure increasing blower), absorption system (absorption tower, circular pump, oxidation air blower, and demister), serosity preparation system (serosity pump, limestone grinding machine, serosity pool and stirrer), Comprehensive Utilization of Carbide Slag SpringerLink2022年7月9日 Limestonegypsum Wet Desulfurization Wastewater Shanshan Zhang, WU Qiaoling, JIN Yinjia et alImprovement of SalineAlkaline Soil via Flue Gas Desulfurization Gypsum and Safety Analysis of the Associated Heavy Metals Yanrong Fu, Kun He, Chunliang Zhou et alStudy on the Thermal Expansion Performance of Gypsum in the Application of SVXPXVHGDVFHPHQW Limestonegypsum Wet Desulfurization
.jpg)
The Degree of Desulphurization of a Limestone/Gypsum Wet
2007年4月1日 The wet type dominates an estimated 84% of the market share and therefore deserve a special analysis (Frandsen, Kiil, Johnsson, 2001;Kaminski, 2003)