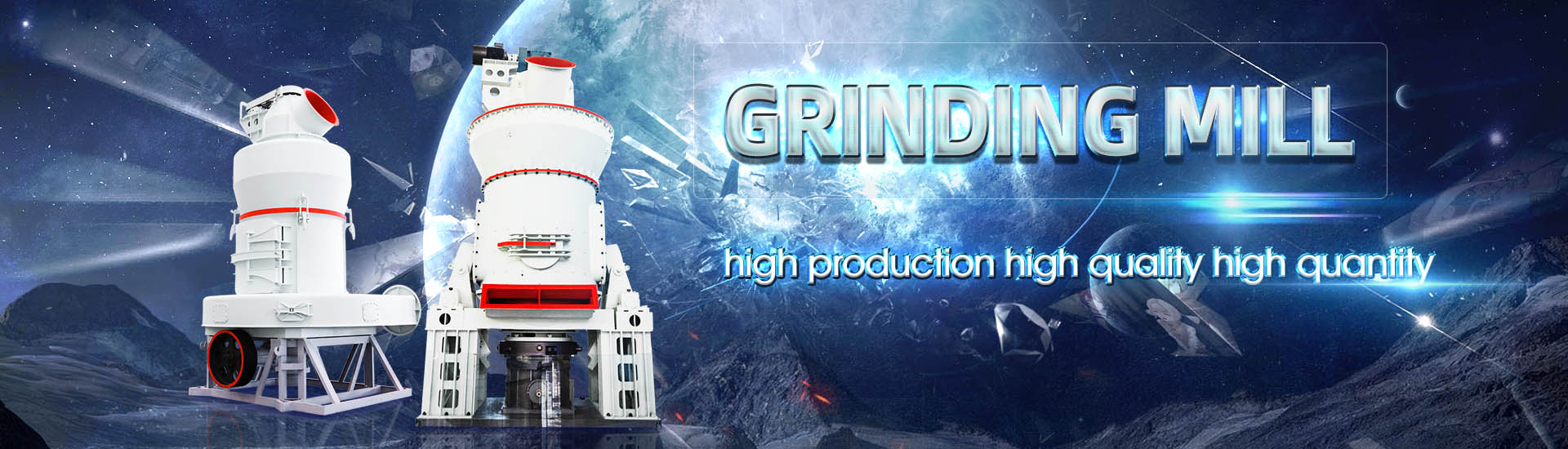
Internal structure diagram of cement plant vertical mill
.jpg)
Vertical roller mill for raw Application p rocess materials
Vertical roller mills are adopted in 20 cement plants (44 mills) in Japan In the vertical roller mill which is widely used in the raw material grinding process, raw materials input grinding table Roller mills are constructed of major mechanical components that can be easily damaged by high mill vibrations It is very important that a mill is operated in a stable manner and that corrective FOR VERTICAL ROLLER MILLS LoescheThe core elements of these plants are the Loesche vertical mills for drygrinding the abovementioned grinding stock Loesche has developed and built the largest and most efficient PROCESS OPTIMISATION FOR LOESCHE GRINDING PLANTSThrough the analysis of the main structure of the vertical mill, we use the assembly function of the solid edge threedimensional solid software to implement the assembly link of the main Solid Edge’s Application in Vertical Mill Design Springer
7TOCS.jpg)
Cement Vertical Mill Vertical Grinding Mill
What Is Cement Vertical Mill The cement vertical mill is a type of grinding equipment that merges fine crushing, drying, grinding, and powder separating into a single, which simplifies the production process and has many irreplaceable 2017年9月11日 PDF In this study, an extensive sampling study was carried out at vertical roller mill of ESCH Cement Plant in Luxemburg Samples were collected from Find, read and cite all the research (PDF) Performance Evaluation of Vertical Roller Mill Vertical raw mill is one kind of raw mill, generally used to grind bulk, granular, and powder raw materials into required cement raw meal in the cement manufacturing plantVertical raw mill is an ideal grinding mill that crushing, drying, grinding, Vertical raw mill Cement PlantThe annual production capacity reaches 150,000 tons of equipment and structure parts and 20,000 tons of casting parts EPC project: the first vertical raw mill in cement plant is designed in German It is widely used in cement, electric power, Raw mill Cement Plant
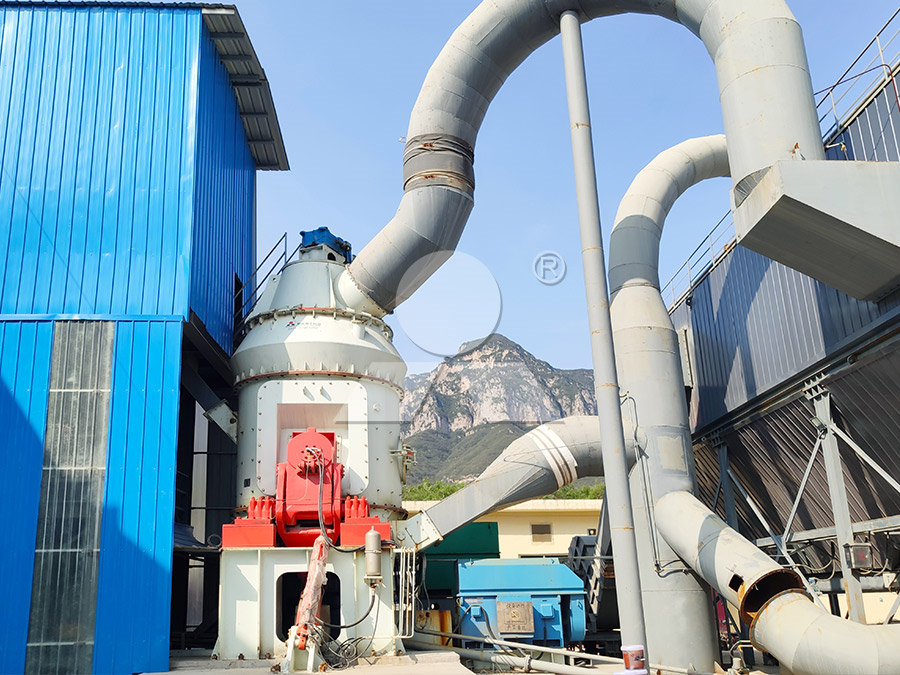
EVERY COMPONENT OF BALL MILL DETAILED EXPLAINED INFINITY FOR CEMENT
EVERY COMPONENT OF BALL MILL DETAILED EXPLAINED To Download this post + all manuals and books and Excel sheets and all notes I collected over my 23 years of experiance in Cement industry click here now Elements of Ball Mill – Overview (Internals) Overview Internal Elements Liners for Coarse Grinding Lifting Height Requirements 2021年1月1日 Cement Grinding: Grinding Mill Vertical Roller Mill or Ball High system pressure loss due to high internal recirculating load, Rashmi cement limited environmental pre feasibility report for Expansion of existing cement grinding plant from 096 MTPA to 111 MTPA by enhancing capacity of 2000 TPD VRM base grinding units to Review on vertical roller mill in cement industry its The Cement Plant Operations Handbook is a concise, Finish mill – 12 Cement – 13 Quality control – 14 Packing and distribution – 15 Emission abatement (dust, NO x, SO 2, etc) – 16 mentioned in Chapter 3 for dry raw milling – ball mills, vertical roller mills, roll presses, Horomill The Cement Plant Operations Handbook International Cement 2022年5月9日 Cement production is one of the most energyintensive manufacturing industries, and the milling circuit of cement plants consumes around 4% of a year's global electrical energy productionModeling of energy consumption factors for an industrial cement
.jpg)
Cement manufacturing components of a cement plant Understanding Cement
After cooling, the clinker may be stored temporarily in a clinker store, or it may pass directly to the cement mill The cement mill grinds the clinker to a fine powder A small amount of gypsum a form of calcium sulfate is normally ground up with the clinker The gypsum controls the setting properties of the cement when water is added• Mill motor speed • Mill air flow/mill differential pressure • Temperature after the mill • Pressure before the mill • Grinding stock feed • Classifier speed • Mill fan speed • Water spraying • Hot gas • Fresh air Manipulated variables Disturbance variable Process measured value RelauchLMmaster 6 250814 11:47PROCESS OPTIMISATION FOR LOESCHE GRINDING PLANTSDownload scientific diagram The layout of the coal mill with a rotary classifier from publication: An investigation of performance characteristics and energetic efficiency of vertical roller The layout of the coal mill with a rotary classifier2020年8月12日 This study shows the performance of a currently running vertical roller coal mill (VRM) in an existing coalfired power plant In a power plant, the coal mill is the critical equipment, whose An investigation of performance characteristics and
.jpg)
Vertical Shaft Kilns Why They Are Diminishing
Vertical Kilns Vertical Shaft Kiln Structures Working Principles In cement plants using vertical kilns, the grinded raw materials are first made into wet pellets by adding 1214% water to the pelletizing pan of the disc pelletizerThen the wet Airswept coal mill is the main equipment of cement plant, also called coal mill in cement plant, used for grinding and drying various hardness of coal, crushing the coal briquette into pulverized coalIt is the important auxiliary equipment of pulverized coal furnace The airswept coal mill runs reliably, can work continuously, also has a large production capacity and less energy Coal Mill In Cement Plant, Airswept Coal Mill Coal MillDownload scientific diagram Schematic of raw vertical roller mill circuit in the Ilam cement plant from publication: Modeling of energy consumption factors for an industrial cement vertical Schematic of raw vertical roller mill circuit in the Ilam cement plant When the mill is too full the mill main drive can be overloaded and it will be necessary to remove some material from the mill Preparations for mill start up The grinding plant is started in a special sequence which is fixed in the interlocking – see interlocking diagram PROCESS TRAINING for operators of Vertical RAW Mills
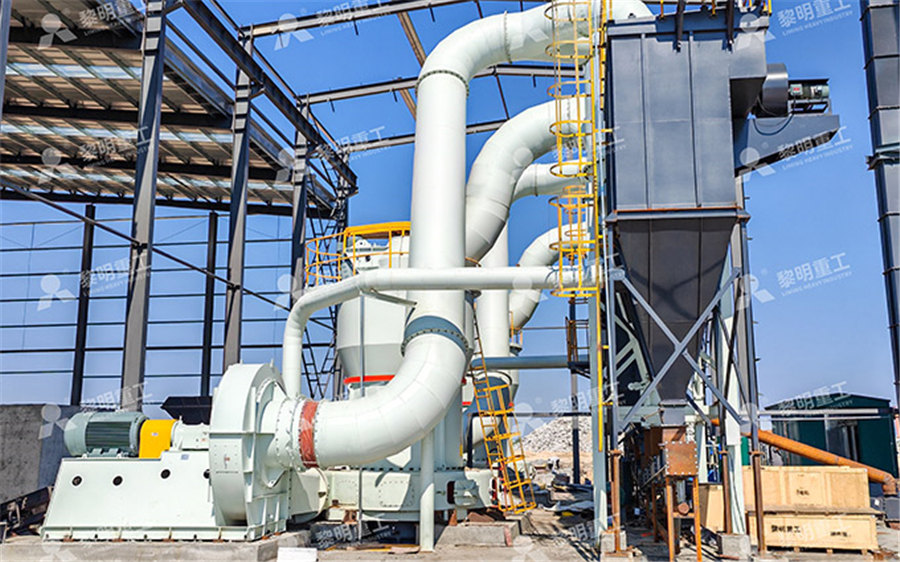
Cement Plant Cement Manufacturing Plant EPC Project
AGICO Cement is a cement plant manufacturer supplies cement manufacturing plants, EPC project for cement plant, onestop service and factory direct Solution3:vertical cement mill; Cement type: PO425: PO425: PO425: Cement ratio (%) Clinker: 90: 90: Limestone: 5: 5: Gypsum: 5: 5: Specific surface of cement: 3500:2016年9月1日 Cement production is one of the most energyintensive manufacturing industries, and the milling circuit of cement plants consumes around 4% of a year's global electrical energy productionOperational parameters affecting the vertical roller mill Vertical cement mill has high grinding efficiency and low power consumption (20% – 30% less than ball mill) The granularity of the feeding material is larger(VRM cement mill is 80mm120mm, cement ball mill is less than or equal to 30mm)Vertical Cement Mill Cement Clinker Grinding Equipment in Cement PlantDownload scientific diagram Technical specifications of vertical roller coal mill from publication: An investigation of performance characteristics and energetic efficiency of vertical roller Technical specifications of vertical roller coal mill
.jpg)
Modeling of energy consumption factors for an industrial cement
the vertical roller raw mill circuits (line 2) in the Ilam cement plant e critical operating parameters gathered during the standard operation are summarized in Table 1 Variables were monitored This study was performed in Ilam cement plant Ilam cement plant is located in Ilam province, west Iran The plant has two cement production lines and totally produces 5300 t/day cement In this study, the second production line was surveyed The cement raw materials (lime, silica and iron ore) enter the circuit through two apron feedersModeling and simulation of vertical roller mill using population Ball mill is the cement crushing equipment in the cement plant high output, low cement temperature, and good comprehensive benefit It is the best choice for a cement plant Skip to content Blog Contact About Cases Factory Ball Mill In Cement Plant Cement Ball Mill AGICO CEMENT PRODUCTION AND QUALITY CONTROL A Cement manufacturing Process Source:civilengineeringforumme The whole process of cement manufacturing in Messebo Cement plant which consists of two separate Cement Production lines can be summarized into the following processes ;as can be seen in the process and Quality flow diagram below; 1CEMENT PRODUCTION AND QUALITY CONTROL
.jpg)
PERFORMING A CEMENT PLANT OPERATIONS AUDIT
An operations audit should be carried out whenever important changes of a general nature are considered Some important changes may include: a plantwide cost reduction effort, the installation of a productivity program, thermal energy efficiency program, electrical energy efficiency program, chemistry and operations strategy, the introduction of new products, AGICO vertical roller mills can be used as cement mills, raw mills, and slag mills AGICO also supplies vertical roller mill components and parts, we can customize machines according to customers’ needs Vertical roller mills (VRM) are a type of mainstream clinker grinding equipment in the cement manufacturing process Vertical roller mills are still newish []Vertical Roller Mill for Sale AGICO Cement PlantMini Cement Plant Hot Sale; Cement Plant 700 ~ 2000tpd; Cement Plant 2500~7000tpd; Optimizing their structure minimizes internal wear of the mill, extending equipment lifespan Cement Ball Mill; Vertical Roller Mill; Cement Mill Separator; Cement Mill; Others Menu ToggleUpgrade and Retrofit of Cement PlantDownload scientific diagram Schematic of ball mill circuit in the Ilam cement plant from publication: Ventilation Prediction for an Industrial Cement Raw Ball Mill by BNN—A “Conscious Lab Schematic of ball mill circuit in the Ilam cement plant
.jpg)
FOR VERTICAL ROLLER MILLS Loesche
cement plant, hence mills are generally operated below optimum capacity to Figure 2: control structure diagram Figure 3: Loesche is launching its new LMMaster for advanced vertical roller mill (VRM) control This automation solution stabilises the VRM to allowand cement Roller presses are used mainly in combination with a ball mill for cement grinding applications and as finished product grinding units, as well as raw ingredient grinding equipment in mineral applications This paper will focus on the ball mill grinding process, its tools and optimisation possibilities (see Figure 1) The ball millBALL MILLS Ball mill optimisation Holzinger ConsultingVertical coal grinding mill integrates crushing, drying, grinding, powder selection and conveying; It has simple system and compact structure Vertical coal mill covers an floor area about 50% of the coal ball mill with the same Vertical Coal Mill for Coal Grinding in Cement PlantAGICO Cement Vertical Mill AGICO Cement Ball Mill Cement Vertical Mill Grinding System Cement vertical mill, also called roller mill, is another raw mill commonly used in cement pared with the cement ball mill, it has a Raw Mill – Raw Mill In Cement Plant AGICO Cement

VRM In Cement Plant Maximize Energy Saving CNBMSINOMA
Vertical roller mill manufacturers Vertical roller mill or VRM is a largescale grinding equipment designed for pulverizing cement raw meal, cement clinker, slag, coal, fly ash, limestone, and other hard grinding materialIt integrates grinding, drying, separation, and conveying in one machine The equipment is widely used in many industries such as cement, electric power, metallurgy Download scientific diagram Schematic layout of a typical cement plant from publication: Energetic assessment of a precalcining rotary kiln in a cement plant using process simulator and neural Schematic layout of a typical cement plant ResearchGate2021年1月29日 Vertical roller mills, VRMs, are widely used for grinding raw materials in factories engaged in the extraction and processing of minerals Any machine used for grinding or crushing consumes around Increase productivity of vertical roller mill using seven QC toolsWhat Is A Cement Ball Mill The cement ball mill is a kind of cement grinding millIt is mainly used for grinding the clinker and raw materials of the cement plant, and also for grinding various ores in metallurgical, chemical, and electric power enterprisesIt has the characteristics of strong adaptability to materials, continuous production, a large crushing ratio, and easytoadjust the Cement Ball Mill Cement Grinding Machine Cement Mill
.jpg)
Analysis of vertical roller mill performance with changes in
2022年5月31日 Mineral crushing is the main source of energy consumption in mineral processing According to statistics, this consumption accounts for about 35–50% of the total cost of the mine (Curry et al, 2014), or even higherIt may also account for 18% of the global electrical energy consumption (NapierMunn, 2015)More efficient crushing equipment needs to be Mini Cement Plant Hot Sale; Cement Plant 700 ~ 2000tpd; Cement Plant 2500~7000tpd; Cement Types Menu Toggle OPC Manufacturing Plant; Application of Vertical Roller Mill in Cement Industry Vertical roller mill (VRM) technology has become Application of Vertical Roller Mill in Cement ProductionOur bestinclass OK™ Mill is a globally successful vertical roller mill solution for grinding raw material, cement and slag Its cuttingedge design features consistently deliver the highest quality products with the greatest efficiency It is affordable to install and cost effective to operate over your cement plant’s lifetimeOK™ Raw and Cement Mill2 VERTICAL ROLLER MILLS INTERNATIONAL CEMENT REVIEW SEPTEMBER 2021 played by the mill foundation, which has been optimised to reduce vibrations2 Built to last The mill foundation, ie, the basic block with its four concrete pylons, is responsible for the smooth running of the mill The roller units and mill housing are notVERTICAL ROLLER MILLS A holistic VRM approach