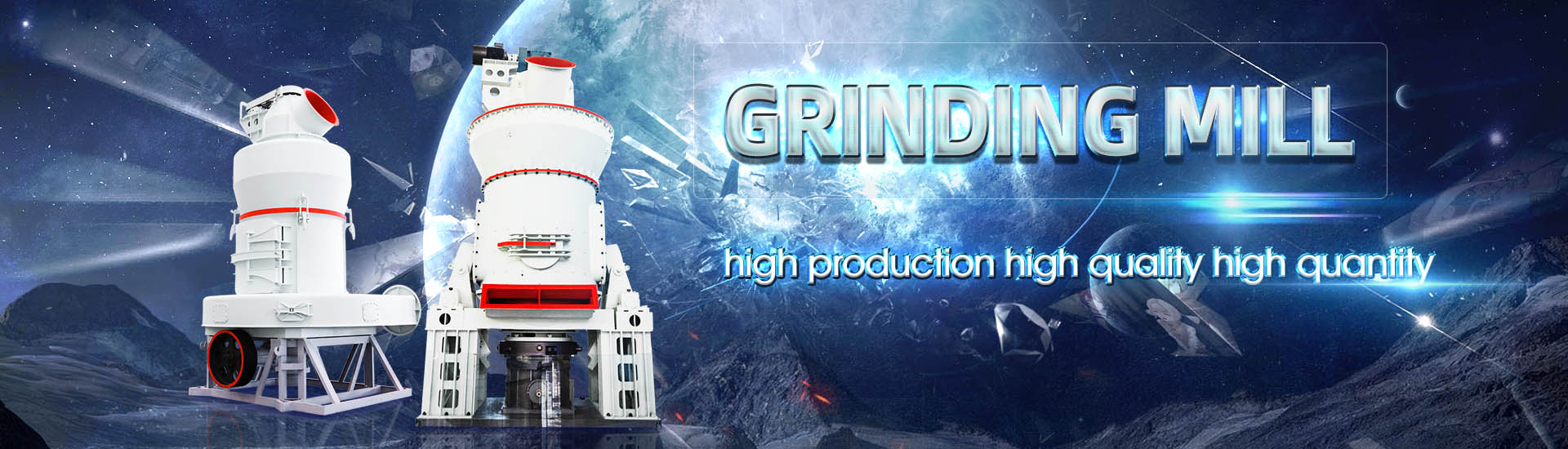
The discharge port of the ore bin and the width of the magnesite grinding mill
.jpg)
Study on the influence of the discharge end cover structure of
2024年11月1日 Three characteristic position angle parameters of the slurry lifter in the discharge process are defined to help describe the discharge state: the discharge start angle, which is the angle at which the ore particles start to leave the slurry lifter along the partition; the discharge There are three main steps in designing a good crushing plant: process design, equipment selection, and layout The paper analyses all of these steps Gold mining is the process of Design of a crushing system that improves the crushing efficiency ore discharge port size is measured by two small pinions, which are close to the switch measurement drive ring When the pinions rotate, the switch counts the number of teeth and converts it MeasurementControl for Crushing and Screening Process2020年1月1日 Lifters with primary, secondary and tertiary plates were used at discharge end Discharge of desired particle size is directly related to critical speed of the mill Mill with lifters A comparative study on a newly designed ball mill and the
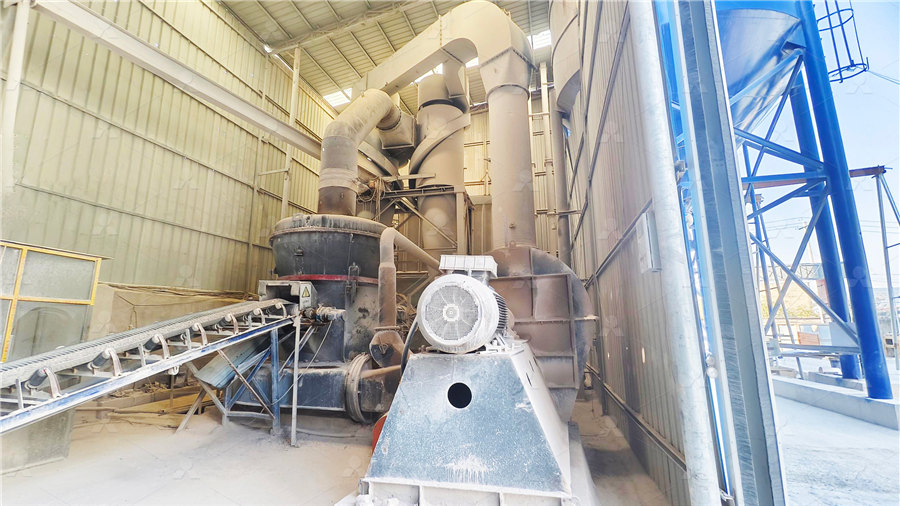
Crushing Plant Design and Layout Considerations 911 Metallurgist
There are three main steps in designing a good crushing plant: process design, equipment selection, and layout The first two are dictated by production requirements and design The scope of this thesis is to examine the dynamic relations between the SAG mill and the pebble crusher in a closed circuit and thus to optimize the circuit efficiency by controlling the pebble Dynamic Modeling and Simulation of SAG Mill Circuits with2016年6月6日 In cases such as autogenous mills at the Empire Mine, all the pulp discharges through ports, approximately 3″ square, with no slots in the “grates” It is important that SAG Mill Liner Design 911Metallurgist2023年6月3日 The ore discharge port size is measured by two small pinions, which are close to the switch measurement drive ring When the pinions rotate, the switch counts the number of MeasurementControl for Crushing and Screening Process
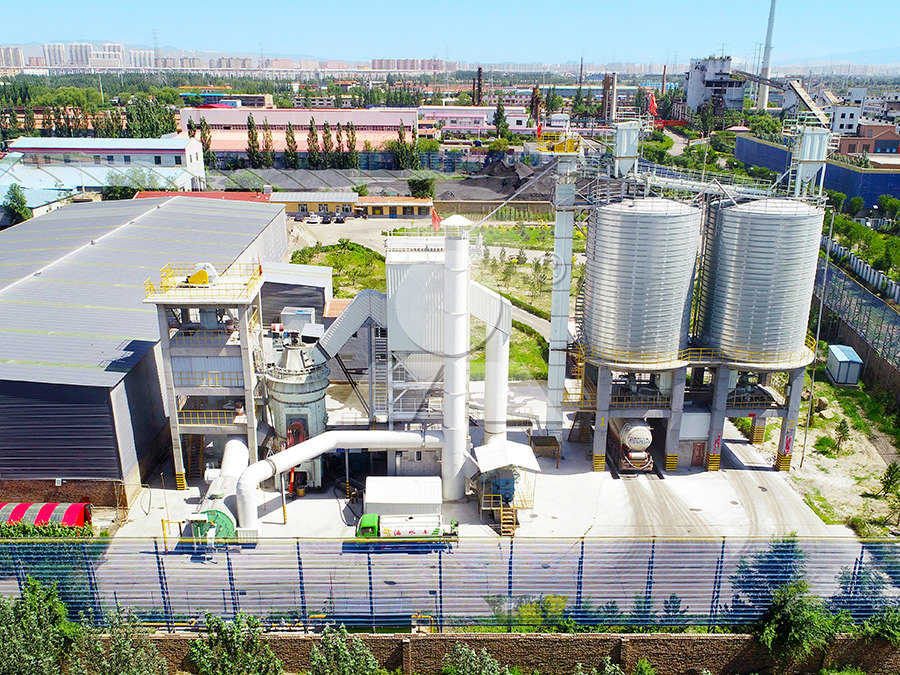
Operation Analysis of a SAG Mill under Different Conditions Based
2020年10月9日 In order to obtain the optimal operation parameters of a SAG mill, in this paper, the discrete element method (DEM) is used to simulate the breakage process of the particles 2012年6月1日 The paper presents an overview of the current methodology and practice in modeling and control of the grinding process in industrial ball mills Basic kinetic and energy Grinding in Ball Mills: Modeling and Process Control ResearchGate2022年7月29日 The established experimental platform for ore discharge through the pass is shown in Fig 7 The dust concentration variation monitoring points are located at the mouth of each midsection ore pass After the experimental ore discharge meets the similarity criteria, the single ore discharge is 128 kg and the discharge flow is 064 kg/sDust catching mechanism of foam in ore bin2024年10月10日 The grinding process is a key link in mineral processing production and a typical complex, controlled process The steadystate model is limited by its model structure and thus difficult to applyied in a control system A hybrid modeling method driven by multisource compensation is proposed in this paper based on the mechanism model using key equipment Hybrid Modeling and Simulation of the Grinding and
.jpg)
Crushing Plant Flowsheet DesignLayout
2016年3月11日 The screen bypasses any material fine enough to enter the grinding section and delivers the oversize to a cone crusher, the discharge of which joins the undersize of the screen and is taken by a belt conveyor to the 2016年6月6日 Grinding Mill Shell Design Lift width is up to two times that on the shell and/or greater height See Figure 5 Because of wider chordal spacing than on the shell cylinder, Type of Mill Discharge; Ore Type; Ore Hardness; Feed Size; Product Size; Media Size; Wet or SAG Mill Liner Design 911MetallurgistThe mass of dry ore fed to flotation is 100 t/h The feed from ore bin contains 6% moisture The cyclone feed, underflow and overflow contain 30%, 75%, 15% solids respectively Calculate 1) Circulating load on the circuit in dry t/hour 2) Amount of The flowsheet shown below is a conventional closed CheggBall Mill Introduction There are three main stages to mineral processing in the mining industryThese are: Comminution (crushing and grinding); Beneficiation (separation and concentration); Smelting and refining; Ball mills are employed in the comminution stage as grinding machines (size reduction)The purpose of grinders in the mining industry is to reduce Ball Mill (Ball Mills Explained) saVRee saVRee
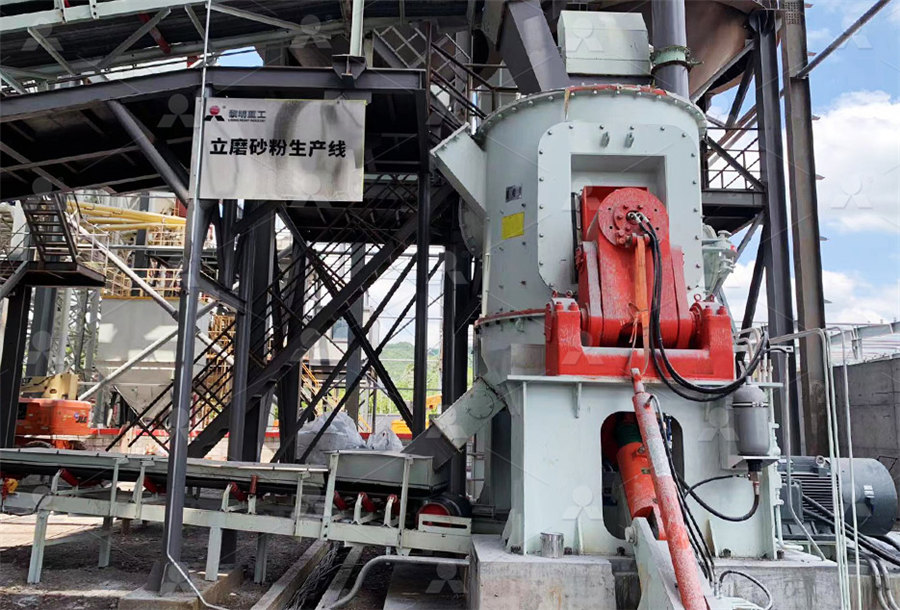
Design of a crushing system that improves the crushing efficiency
pivoted at the bottom end The size of a jaw crusher is measured by its gape and width, expressed as gape x width The gape is the size of the feed opening The opening at the discharge end of the jaws is known as the set For example, 400 by 600mm, indicates a distance of 400mm from fixed jaw plate to moving jaw plate where the feed enters, and2018年12月4日 Geometric comparison of dynamic modeling and DEM, showing the change in the center of mass due to the load, with (1) upper screen deck, (2) rigidbody model, (3) lower screen deck, and (4) feed chute(PDF) Dynamic Modeling of a Vibrating Screen Considering the Ore 2016年3月14日 Without any reference to dry grinding, the first successful ballmill for wet crushing, which is still in operation, was built 10 years ago This mill, designed by Erminio Ferraris for crushing Sardinian ores for concentration, is of more than passing interestPeripheral Discharge Ball Mills Theory and Practice2007年7月1日 Silica and Fe presence, however, are almost universal and, together with oxygen, are usually the most abundant elements, with Al, Ca, K, Mg, Mn, Na, P, Ti and S also major components (Table 1)Methods for the disposal and storage of mine tailings
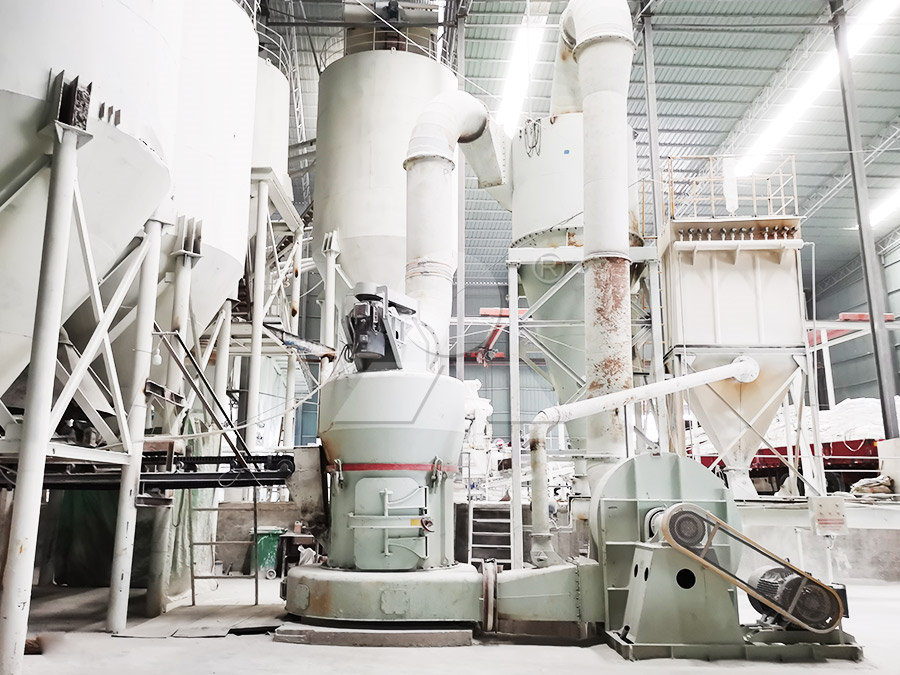
DESIGN OF BINS AND HOPPERS FOR THE STORAGE OF
the wall in the bin discharge zone (8) and bin geometry The value of the material's effective angle of internal friction (0) and the angle of friction betweenthe material and the bin surface ($) are determined by the shear experiments set outin points 333 and 3342016年3月21日 Concentration and Recovery Formulas These are used to compute the production of concentrate in a mill or in a particular circuit The formulas are based on assays of samples, and the results of the calculations Common Basic Formulas for Mineral Processing 2020年6月23日 Converting a mill from an overflow to a grate discharge arrangement leads to an increased power draw This happens because the installation of the grate discharge arrangement enables the mill to run with a Converting a ball mill from overflow to grate 2015年7月27日 Let’s begin with fine ore storage bin or stockpile, get it out of the way and then proceed to grinding You would think that there isn't that much to learn 911 Metallurgist is a trusted resource for practical insights, solutions, and support in mineral processing engineering, helping industry professionals succeed with proven expertise Fine Ore Storage Bin and Fine Ore Storage Bin and Stock Pile 911Metallurgist
.jpg)
Rod Mill SpringerLink
2023年5月3日 Center Periphery Discharging Rod Mill The center periphery discharging rod mill feeds the material through the journals at both ends of the mill, and discharges the grinding products through the circular orifice in the middle of the cylinder (Fig 3)Ore pulp is characterized by short stroke, steep slope, and it can be coarsely ground with fewer fine particles and low The purpose of the primary crusher is to reduce the ROM ore to a size amenable for feeding the secondary crusher or the SAG mill grinding circuit The ratio of reduction through a primary crusher can be up to about 8:1 Feed: ROM up to 15 m; Product: 300mm (for transport) to 200mm (for SAG mill) Feed Rate: 160 to 13,000 tphAMIT 135: Lesson 5 Crushing – Mining Mill Operator Trainingefficiency of grinding equipment can be as low as 1% Therefore, efforts have been devoted during the past decades to increase the grinding process efficiency The word ‘autogenous’ in AG mills indicates the grinding media is formed exclusively by ore particles In a SAG mill, external grinding balls are added in the chamber to aid in theDynamic Modeling and Simulation of SAG Mill Circuits with2018年3月1日 An inclined mediumthick ore body refers to a type of ore body with an ore width ranging from 4 to 15 m, where its dip ranges from 30° to 55° 1 Such deposits account for approximately 23% of nonferrous metal ores in underground mines in China 2 With the increase in mining depth, the ground pressure correspondingly increases, as do the numbers of low Laboratory study of the influence of dip and ore width on gravity
.jpg)
Chute Design Essentials – How to Design and Implement Chutes in
speed, as indicated earlier Where the chute feeds into skirts, the chute width must not be greater than the width of the skirts Any necking or reduction in width of the chute body must comply with the chute wall slope and valley angle requirements2021年6月10日 Oregon Geology (formerly The OreBin) contains timely information about DOGAMI and about new and interesting developments in mining, metallurgy, and geology and is designed to reach a wide spectrum of readers in the geoscience community who are interested in all aspects of the geology of Oregon and its applications DOGAMI is not currently accepting Oregon Geology and The Ore Bin2024年1月1日 Center Periphery Discharging Rod Mill The center periphery discharging rod mill feeds the material through the journals at both ends of the mill, and discharges the grinding products through the circular orifice in the middle of the cylinder (Fig 3)Ore pulp is characterized by short stroke, steep slope, and it can be coarsely ground with fewer fine particles and low Rod Mill SpringerLink2022年8月2日 PDF In order to research the variation law of the longitudinal resistance coefficient of the ore bin in the marine mining system under different (length × width × dep th), and the (PDF) Experimental research and analysis on the resistance
.jpg)
A Review of the Grinding Media in Ball Mills for Mineral
2023年10月27日 The ball mill is a rotating cylindrical vessel with grinding media inside, which is responsible for breaking the ore particles Grinding media play an important role in the comminution of mineral ores in these mills This work reviews the application of balls in mineral processing as a function of the materials used to manufacture them and the mass loss, as content and the amount of fine particles in the ore Fig 6 Repose and drawdown angles of a bulk material Fig 7 Drawdown angle of a crushed copper ore tested at 1% and 5% moisture in a slice 2D model of a flat bottom bin 45 Wall friction and chute angle Wall friction tests should be performed on differentEffect of moisture content on the flowability of crushed ores2016年3月30日 In book: Encyclopedia of Iron, Steel, and Their Alloys (pppp 10821108) Chapter: i) Direct Reduced Iron: Production; Publisher: CRC Press, Taylor and Francis Group, New York(PDF) i) Direct Reduced Iron: Production ResearchGate2012年6月1日 overflow discharge mill, diaphragm or grate discharge mill and centreperiphery discharge mill, eg see [23] In industrial applications, the inner surface of the millGrinding in Ball Mills: Modeling and Process Control
.jpg)
Influence of oredrawing port position on orerock flow
2024年9月11日 Position and eccentricity of oredrawing port While ore drawing at the bottom of the ore pass, the orerock bulk temporarily stored in the ore storage section (ie, the ore bin) continuously 2022年1月23日 Preparing the RunofMine (ROM) bauxite for the grinding mill circuit must be completed in order to efficiently size the grinding mill circuit The focus of the Sect 412 discussion is about choosing the correct crusher for the bauxite application Including the considerations for using a drum scrubber or not Bauxite mines are in many placesPhysical Bauxite Processing: Crushing and Grinding of Bauxite2021年1月1日 Mill filling has a dominant effect on grinding mill performance (Apelt, Asprey and Thornhill, 2001), and therefore, its accurate measurement is vital for modelling grinding mill performanceMeasuring filling is also necessary to estimate the composition of the load for mill modelling: rock and slurry for AG mills; rock, balls and slurry for SAG mills; or balls and slurry An improved method for grinding mill filling measurement and 2021年9月15日 Ore Particle Size Composition When the content of coarse particles (larger than the size of the discharge port) in the crushed ore is high and the ratio of the largest ore block to the width of the feed port is large, the crusher needs to achieve a large crushing ratio, so the productivity is reduced8 Factors That Affect Production Efficiency of Crushers
.jpg)
Factors affecting the performance of crushing plant
2014年1月1日 Conference: Proceedings of the 23rd International Mining Congress and Exhibition of Turkey IMCET 2013; At: Kemer, Antalya, Turkey, April 1619, 2013, pp 2933012020年10月9日 the qualified particle size at the discharge port of the semi autogenous mill, and the qualified particle size is defined as no more than 25 mm The simulation process is shown in Figure 5 Operation Analysis of a SAG Mill under Different 2015年6月25日 The above tables list some of the most common Grate Discharge Ball Mill sizes Capacities are based on medium hard ore with mill operating in closed circuit under wet grinding conditions at speeds indicated Overflow VS Grate Discharge Ball or Mill – Why 2017年2月13日 Center peripheral discharge Rod Mill for minimal slimes in final product CERAMIC LINED BALL MILL Ball Mills can be supplied with either ceramic or rubber linings for wet or dry grinding, for continuous or batch type operation, in sizes from 15″ x 21″ to 8′ x 12′Ball Mills 911Metallurgist
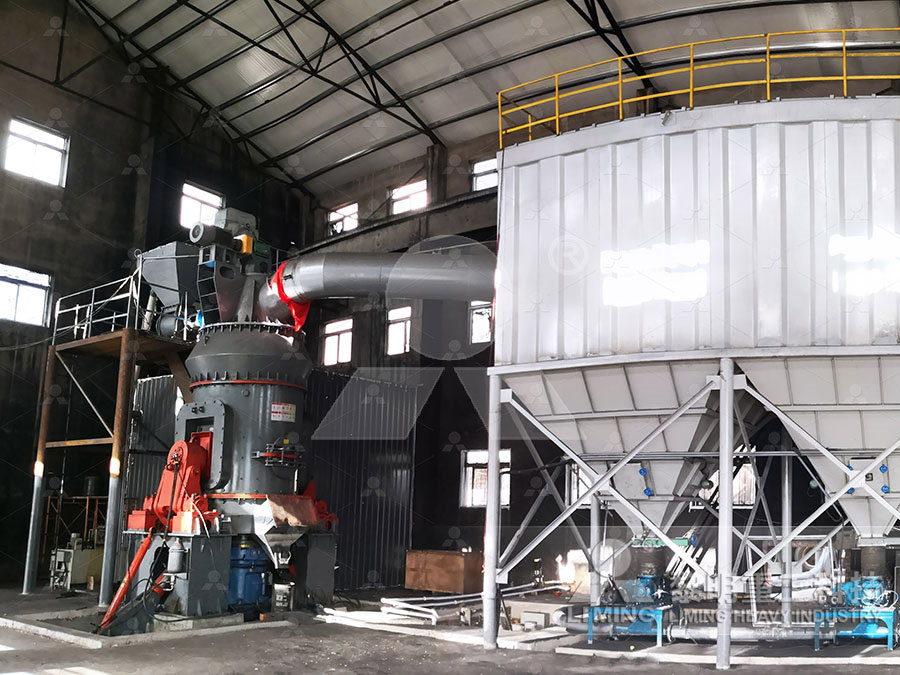
Operating and Troubleshooting a Grinding Circuit
2015年8月7日 A ball mill operates more with the grinding surface action of the balls than the impact form of grinding that the rod mill uses Taking this into account you can see that if the rod mill doesn’t reduce the ore to a size that the ball mill can reduce quickly, the circuit load will climb until its volume is greater than can be handled2023年2月15日 1 Difference in (ball mill) structure Dry grinding A dry ball mill is equipped with a cylindrical rotating device and two bins, which can rotate by gears The discharge port is straight There are also air intake devices, dust exhaust pipes, and dust collectors Wet grinding The structure of wet ball mill is simple The discharge port is What Are the Differences between Dry and Wet Type Ball Mill?2020年7月2日 ore discharge via trench bottom in blind ore bodies to the height o f no more than 2 levels initially The width of rib pillars is limited to 10–12 and 15–20 m in medium and heavily jointed Extraction of ore reserves from pillars in roomandpillar miningWhen the bin discharge rate is greater than the charge rate, the level of solids within the channel drops, causing layers to slough off the top of the stagnant mass and fall into the channel This spasmodic behaviour is detrimental with cohesive solids since the falling bulk material packs on impact, thereby increasing the possibility of archingBulk Materials Storage Design: Considerations for the Design of
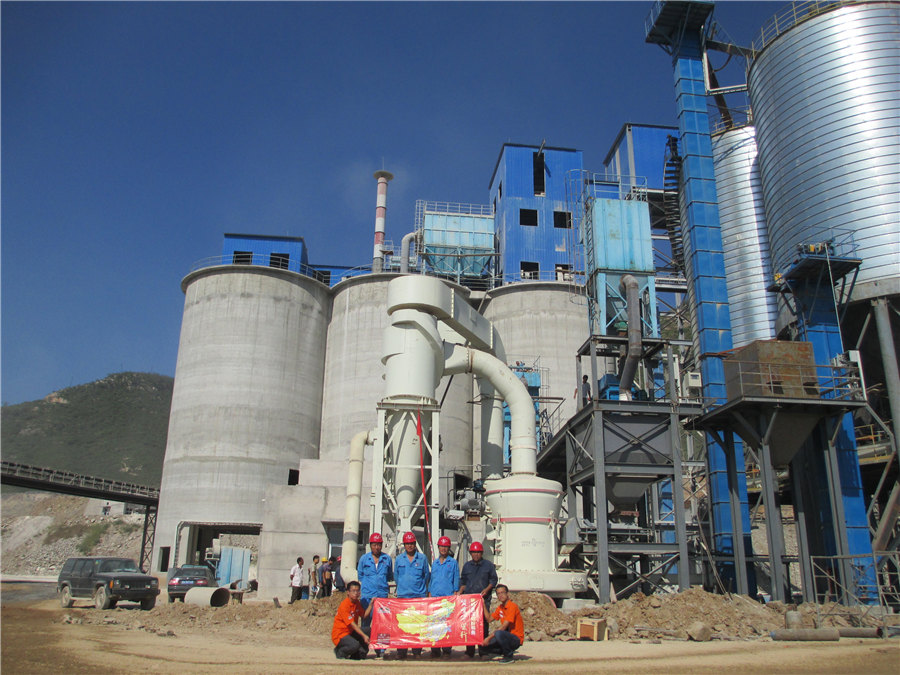
THE MODELLING OF SCRUBBERS AND AG MILLS, WHEN TO USE
MILL POWER DRAW Charge Motion Modelling of the charge motion is based on the approach adopted by Morrell (1996a and 1996b) for predicting the power draw of wet tumbling mills2016年5月10日 In the handling of wet, sticky ores such as encountered in tropical areas having distinct dry and rainy seasons, the crushing plant is a section of the mill which must be planned very carefully Unless this is done, crushing becomes a constant source of trouble resulting in lost production and high milling cost In some areas rainfall is high for prolonged periodsCrushing and Grinding Wet Sticky Ore 911Metallurgist