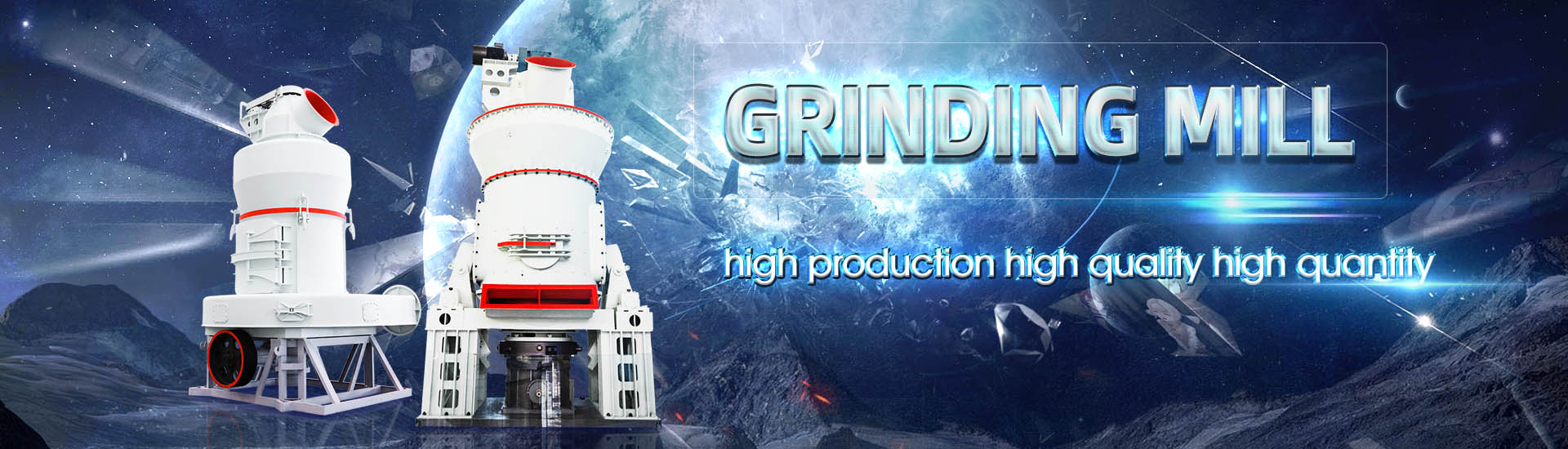
What substances do iron plant desulfurization slag contain
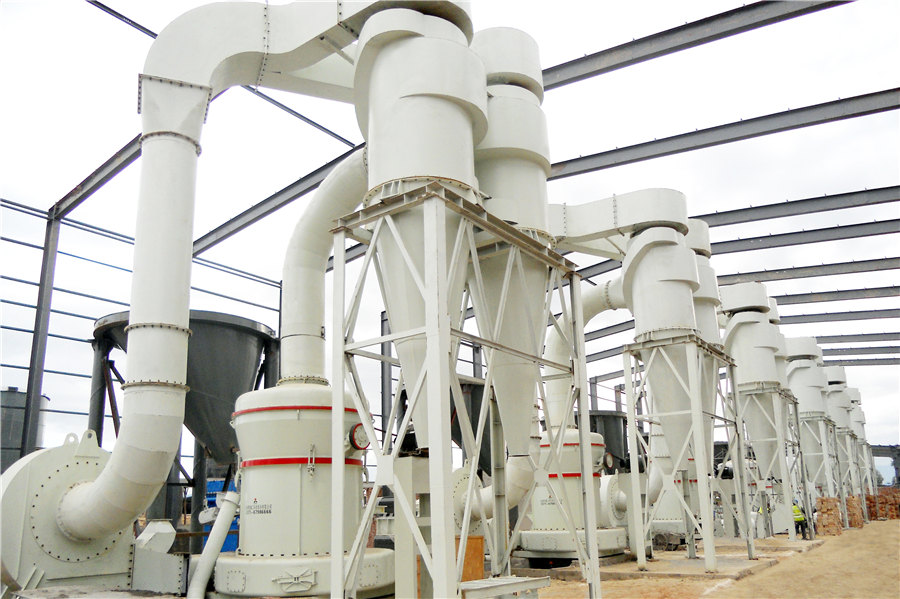
Application of molten iron desulfurization slag to replace steel
2022年12月1日 Molten iron desulfurization slag (DS) is the tail slag produced in the predesulfurization process of molten iron Molten iron desulfurization produces approximately 7–9 kg/t of DS (Zhang and AnJun 2009) The main components of DS are Ca(OH) 2, CaSO 4, 2021年2月21日 In hot metal desulphurisation (HMD) the slag will hold the removed sulphur However, the iron that is lost when the slag is skimmed off, accounts for the highest costs of Optimal hot metal desulphurisation slag considering iron loss and 2002年7月1日 Blast furnace slags typically contain 01–15% iron (NSA, 2000) and are commonly used for applications such as industrial aggregates, cement admixtures, and Pelletizing steel mill desulfurization slag ScienceDirect2017年3月5日 The physicochemical properties of four different types of iron and steel slags, including blast furnace slag, basic oxygen furnace slag, electric arc furnace slag, and ladle (PDF) Iron and Steel Slags ResearchGate
.jpg)
Optimal hot metal desulphurisation slag considering iron loss and
In hot metal desulphurisation (HMD) the slag will hold the removed sulphur However, the iron that is lost when the slag is skimmed off, accounts for the highest costs of the HMD process Steelmaking desulfurization slag samples were characterized using chemical, Xray diffraction (XRD), scanning electron microscopy (SEM) and energy dispersive spectrometry (EDS) Characterization of Steelmaking Desulfurization Slag2018年5月24日 In this research, an effort is made to separately introduce the various processes, industrial practices, and fundamental research activities to remove sulfur from iron ores, Desulfurization of Iron Ores: Processes and Challenges2021年11月8日 Production statistic shows that the VO x (5–10 wt%), TiO 2 (5–10 wt%) and FeO (10–16 wt%) contents are high in the semisteel desulfurization slag, which is much Influence of desulfurization slag containing oxides of vanadium
.jpg)
Full article: Lowering iron losses during slag removal in hot metal
2020年4月9日 To lower the iron losses of the hot metal desulphurisation (HMD) process, slag modifiers can be added to the slag Slag modifiers decrease the apparent viscosity of the HMD 2005年2月1日 Steelmaking slag has been considered a potential P source due to its huge production and the increasing P content in slag with the utilization of lowgrade iron ores(PDF) Industrial uses of slag The use and reuse of iron and 2014年5月12日 In the study of Zhibo Tong et al [1], a novel valorization process of KR desulfurization waste slag into ironcontaining substances and desulfurization agent for hot metal pretreatment was Potential Reuse of Slag from the Kambara Reactor Desulfurization 2022年9月11日 Desulfurization slag (DS) is the solid waste discharged from the bottom of the circulating fluidized bed (CFB) boiler It has good pozzolanic activity, selfhardening property and large expansibility In this paper, ground Axial Compressive Properties of SelfCompacting
.jpg)
The potential utilization of slag generated from iron
2019年10月29日 Along with iron and steel production, large amount of slag is generated Proper management on the iron and steelmaking slag is highly demanded due to the high cost of direct disposal of the slag to landfill, which Iron ore contains typically 001% sulphur and is only a minor source of sulphur in the steelmaking process [2,8] In the BFBOF process there are four process steps where sulphur can be removed: BF; iron to the slag, after which the slag layer is separated from the metalSulphur removal in ironmaking and oxygen steelmaking2009年10月1日 About 7 to 9kg waste slag is produced per ton hot metal treated in the Kanbara Reactor (KR) desulfurization process, and the waste slag contains approximately 40–60 % CaO and large amounts of Development of Slag Recycling Process in Hot Metal Desulfurization 2017年3月9日 With regard to slagphase masstransfer control, Yan et al investigated the desulfurization of stainless steel via CaOAl 2 O 3 –based slag and concluded that the mass transfer of sulfur in the slag phase determined the desulfurization rate and derived the slagphase masstransfer coefficient to be 08 to 12 × 10 −6 m/s based on several previous references Effect of Slag Chemistry on the Desulfurization Kinetics in Secondary
.jpg)
Formation of optimal slag composition in ladle furnace for
2024年11月8日 The refining properties of slags are contingent upon the presence of free oxygen anions (O 2−)In the slag formed in LFU, several oxides serve as sources of O 2− (CaO and MgO), while other oxides uptake them (SiO 2) through the formation of \({\mathrm{SiO}}{4}^{4}\)Furthermore, the slag contains the amphoteric oxide Al 2 O 3, which exhibits both basic and tion slag and melt emission control residuals Calcium Carbide Desulfurization Slag Process Description In the production of ductile iron, it is often necessary to add a desulfurizing agent in the melt because the charge materials contain excessive amounts of sulfur One desulfurization agent commonly used is solid calcium carbide (CaC2)Waste in the Foundry Industry Taylor Francis Online2016年5月16日 In this study, aqueous mineral carbonation of Linz–Donawitz (LD) slag waste from Rourkela, Bokaro, and Tata steel industries was undertaken at a room temperature of 30°C and elevated CO2 (PDF) Sustainable Approaches for LD Slag Waste ResearchGateSteelmaking desulfurization slag samples were characterized using chemical, Xray diffraction (XRD), scanning electron microscopy (SEM) Dippenaar, R, “Industrial uses of slag (the use and reuse of iron and steelmaking slags),” Ironmaking steelmaking, 32(1), 35–46, 2005Characterization of Steelmaking Desulfurization Slag
.jpg)
Treatment of Hot Metal Desulfurization Slag With CO
2023年11月21日 From Figure 1, one can also see that in the temperature range 873 K (600 °C) to 1473 K (1200 °C), O 2 could oxidize not only CaS, MgS and FeS, but also iron and iron oxides By using pure oxygen as an oxidation reagent, under standard conditions, treated hot metal desulfurization slag might no longer be separated by regular magnetic separation since iron The kinetics of carbide slag desulfurization process conforms to pseudorstorder kinetics, and the sulfur content of calcium carbide slag reaches to 1000 mgSO 2 g−1 A project demonstration was carried out in the gold smelting Tielu Plant of Zhenyuan Huashuo Precious Metals Development Co, Ltd, in YunnanDesulphurization mechanism and engineering practice of carbide slag2002年7月1日 Hot metal desulfurization slag is a highmetallic iron content slag produced at a typical steelmaking facility and is currently considered waste Each year, 50,000 tons of this slag is produced at Pelletizing steel mill desulfurization slag Request PDFThe primary components of iron and steel slag are limestone (CaO) and silica (SiO 2)Other components of blast furnace slag include alumina (Alsub>2 O 3) and magnesium oxide (MgO), as well as a small amount of sulfur (S), while steelmaking slag contains iron oxide (FeO) and magnesium oxide (MgO)In the case of steelmaking slag, the slag contains metal elements Chemical composition of iron and steel slag
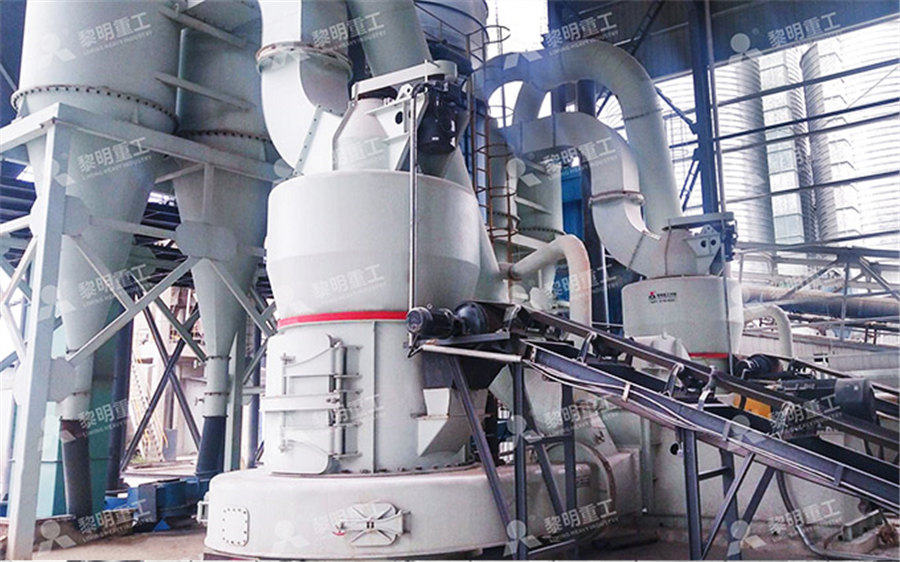
Pelletizing steel mill desulfurization slag ScienceDirect
2002年7月1日 The iron in steelmaking slag has the advantage of either being partially reduced to iron oxides such as magnetite (Fe 3 O 4) or wustite (FeO) or being completely reduced to metallic iron The steelmaking slag is currently sold as aggregate, stockpiled, inventoried, or in the worst case, it is landfilled at costs of US$5–100 per ton2019年5月23日 Dong Y, Zhou QL, Hui SE et al (2006) Dissolution characteristics of carbide slag during wet flue gas desulfurization J Power Eng 26(6): 884–887 Google Scholar Lv HJ (2011) Application analysis of flue gas desulfurization with carbide slaggypsum Power Syst Eng 27(1): 41–42 CAS Google ScholarComprehensive Utilization of Carbide Slag SpringerLink2013年4月1日 The deoxidation and the desulfurization limits of liquid iron by calcium are calculated to be 16 mass ppm O (at 15 mass ppm Ca) and 35 mass ppm S (at 40 mass ppm Ca) under the condition of aCaO Desulfurization strategies in oxygen steelmaking ResearchGate2021年2月21日 In hot metal desulphurisation (HMD) the slag will hold the removed sulphur However, the iron that is lost when the slag is skimmed off, accounts for the highest costs of the HMD processOptimal hot metal desulphurisation slag considering iron loss
.jpg)
Desulfurization of CopperIron Reduced from Copper Slag
2018年1月10日 But copperiron reduced from copper slag contains a large number of copper matte, making sulfur content high In (2018) Desulfurization of CopperIron Reduced from Copper Slag In: Lambotte, G, Lee, J, Allanore, A, Wagstaff, S (eds) Materials Processing Fundamentals 2018 TMS 2018 The Minerals, Metals Materials 2016年5月16日 The average rate of generation of LD slag is approximately 150–180 kg per ton of crude steel in India []Researchers also found that this rate of production of LD slag somtimes reaches a high of 200 kg per ton of crude steel []In India, over 1215–1458 metric tons of steelmelting slag has been generated in the financial year 2013, and this rate is still increasing Sustainable Approaches for LD Slag Waste Management in Steel 2022年5月1日 Steel slag is a byproduct produced by the conversion of carbonrich molten iron into steel in basic oxygen furnaces (BOFs) and electric arc furnaces (EAFs) during the steelmaking process, accounting for about 15 to 20 wt% of the crude steel production [1]The global steelmaking industry produced 18 billion tons of crude steel in 2019, and China alone Resource utilization of slag from desulphurization and slag 2020年8月1日 Sulfur dioxide removal: An overview of regenerative flue gas desulfurization and factors affecting desulfurization capacity and sorbent regenerationSulfur dioxide removal: An overview of regenerative
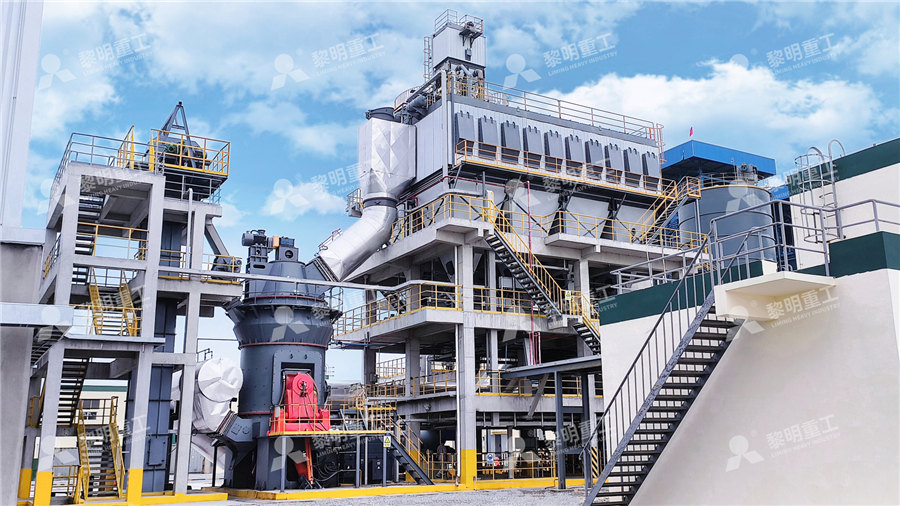
Desulfurization of Iron Ores: Processes and
2018年5月24日 Various studies have been increasingly performed on the reduction of sulfur content of iron ores and concentrates The presence of sulfur in Finally, the techniques are compared from technical, economic and SLAG IRON AND STEEL 16 Slag Iron and Steel S lag is a byproduct generated during manufacturing of pig iron and steel It is produced by action of various fluxes upon gangue materials within the iron ore during the process of pig iron making in blast furnace and steel manufacturing in steel melting shopSLAG IRON AND STEEL2019年5月23日 Steel slag is the waste generated in the steelmaking process and includes ferric oxide and the impurities of some infusible matters It is the byproduct when slagforming constituents (such as fluorite, lime, and deoxidant) are added for deoxidization, desulfurization, and dephosphorization in prehensive Utilization Technology of Steel Slag2020年5月16日 Numerous mitigation techniques have been incorporated to capture or remove SO2 with flue gas desulfurization (FGD) being the most common method Regenerative FGD method is advantageous over other methods due to high desulfurization efficiency, sorbent regenerability, and reduction in waste handling The capital costs of regenerative methods are Sulfur dioxide removal: An overview of regenerative flue gas

Recycling of desulfurization slag for the production of autoclaved
2018年1月15日 Although DeS slag normally contains considerable amount of iron and iron oxides, it is not often recycled in steel manufacturing because of the high sulfur content, so reusing DS in cement raw materials, agricultural applications, or wastewater treatments [2], [5], [6] is a much more feasible and common approach2001年1月1日 Desulfurization kinetics of molten pig iron were studied using CaOSiO2Al2O3Na2O quaternary slag systems at 1 350 degreesC The concentration of Na2O in slag decreases with lime due to evaporationReaction Kinetics of Desulfurization of Molten Pig Iron Using integrated iron and steel plant oil contain 13–20% This adds up to a sum of 95% Desulfurization with liquid slag would be possible as well, Desulfurization Strategies in Oxygen Steelmaking ResearchGatestability tests showed that they are nontoxic and do not contain dioxin A3 Desulfurization slags Molten iron created from smelting in a BF contains sulfur content The molten iron is subsequently transferred to the torpedo to be desulfurized by desulfurization agents Once discharged from the torpedo, the slags undergoStrategies for Promoting Steelmaking Slag Resourcezation in Taiwan
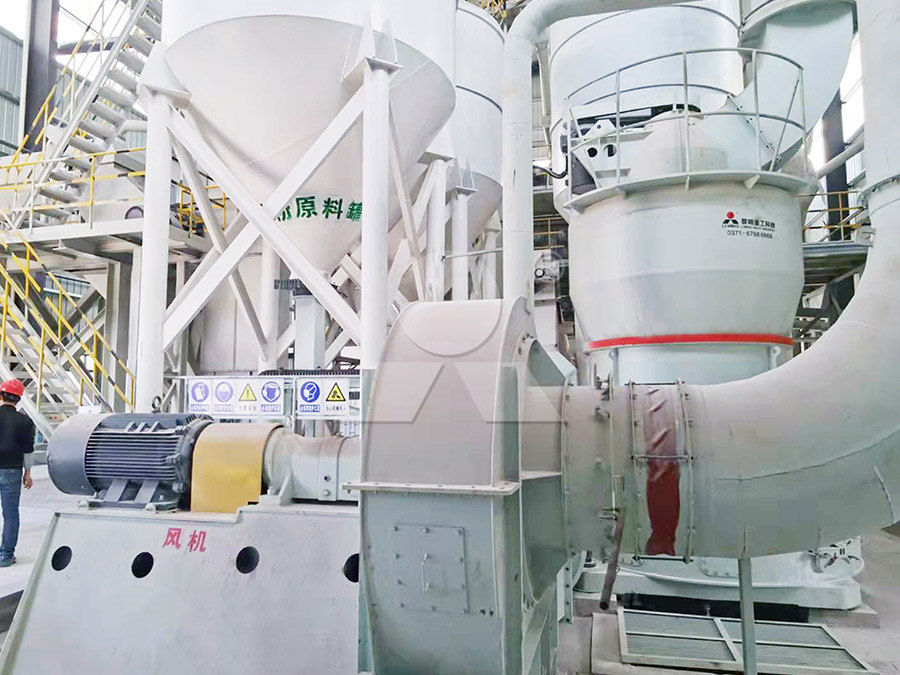
Strategies for Promoting Steelmaking Slag
2018年1月1日 Hot metal desulfurization slag is a highmetallic iron content slag produced at a typical steelmaking facility and is currently considered waste Each year, 50,000 tons of this slag is produced at 2013年10月16日 When the slag is skimmed, the trapped iron is lost with it It is called emulsion loss In general, around 50 % of the slag is iron in emulsion This means that emulsion loss can be minimized by reducing the total amount of Desulphurization of Hot Metal IspatGuruThe BOS slag was considered a waste in old times but now as a secondary resource because it contains a large amount of thermal energy (temperature up to 1700 °C), chemical energy (metallic and lowvalence metallic oxides), and Basic Oxygen Steelmaking Slag: Formation, Reaction, 2020年11月24日 Brief process flow of sintering flue gas deep desulfurization system in iron and steel plant Effect of pH value of absorption solution on desulfurization and denitrification of sintering flue gas(PDF) Deep desulfurization of sintering flue gas in iron and steel
.jpg)
Carbon mineralization of steel and ironmaking slag: Paving the
2024年4月1日 Steel and ironmaking slag contain 30–60 wt% of calcium oxide (CaO) and 3–15 wt% of magnesium oxide (MgO), suggesting high CO 2 storage capacities [19] It has been reported that the potential CO 2 sequestration capacity if using alkaline industrial waste is 310 Mt CO 2 , and steel and ironmaking slag sources can contribute to a 435% reduction in CO 2 [20] 2015年9月9日 The desulfurization waste slag from hot metal pretreatment process is a typical solid waste generated in the integrated steel company About 7 to 9kg waste slag is produced per ton hot metal treated in the Kanbara Reactor (KR) desulfurization process, and the waste slag contains approximately 40–60 % CaO and large amounts of iron Therefore, effectively Characterization and Valorization of Kanbara Reactor Desulfurization 2023年6月10日 In the process of blast furnace ironmaking, Slagforming in blast furnace ironmaking is the solvent that interacts with the gangue in the ore and the ash of coke to dissolve, collect, and melt the substances that do not enter pig iron and gas, so that the liquid slag is formed In the blast furnace, slag and pig iron are formed at the same timeSlagForming in Blast Furnace Ironmaking SpringerLinkMetallurgical slag, as a byproduct of the metallurgical industry, has an increasing stockpile worldwide, which not only occupies land but also causes serious damage to the environmentIn particular, heavy metal elements in metallurgical slag will infiltrate into groundwater with accumulation time and rain erosion, which seriously threatens the safety of human lifeMetallurgical Slag an overview ScienceDirect Topics
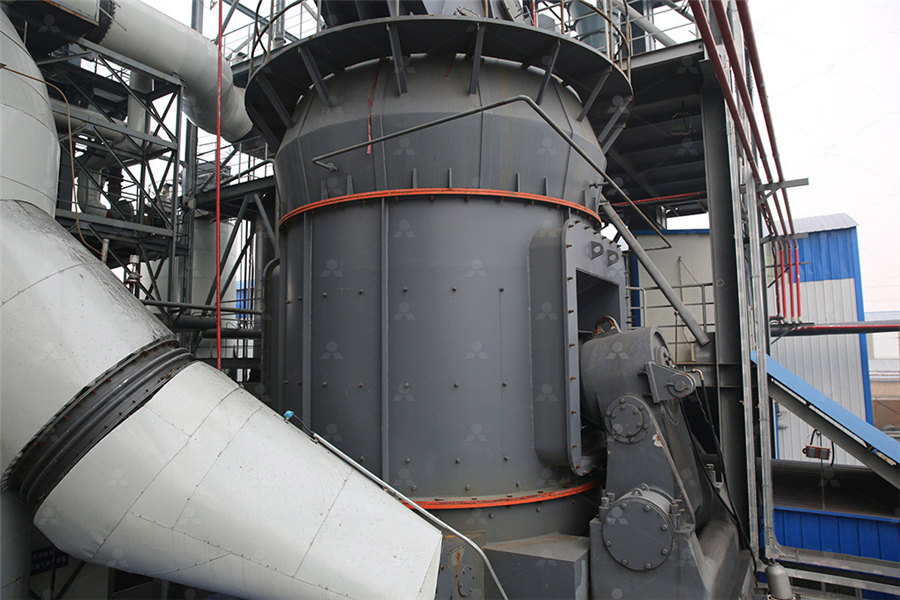
Dephosphorization and Desulfurization Pretreatment of Molten Iron
1998年1月1日 Dephosphorization and Desulfurization Pretreatment of Molten Iron with CaOSiO2CaF2FeONa2O SlagsDesulfurization in Steelmaking Steelmaking basically involves two consequential processes: an oxidation process performed in the furnace, followed by a reduction (refinement) process performed in the ladle Ladle metallurgy objectives including homogenization, vacuum degassing, deoxidation, temperature adjustment, alloying and refining (including desulfurization) are Desulfurization in Steelmaking AF Chemicals