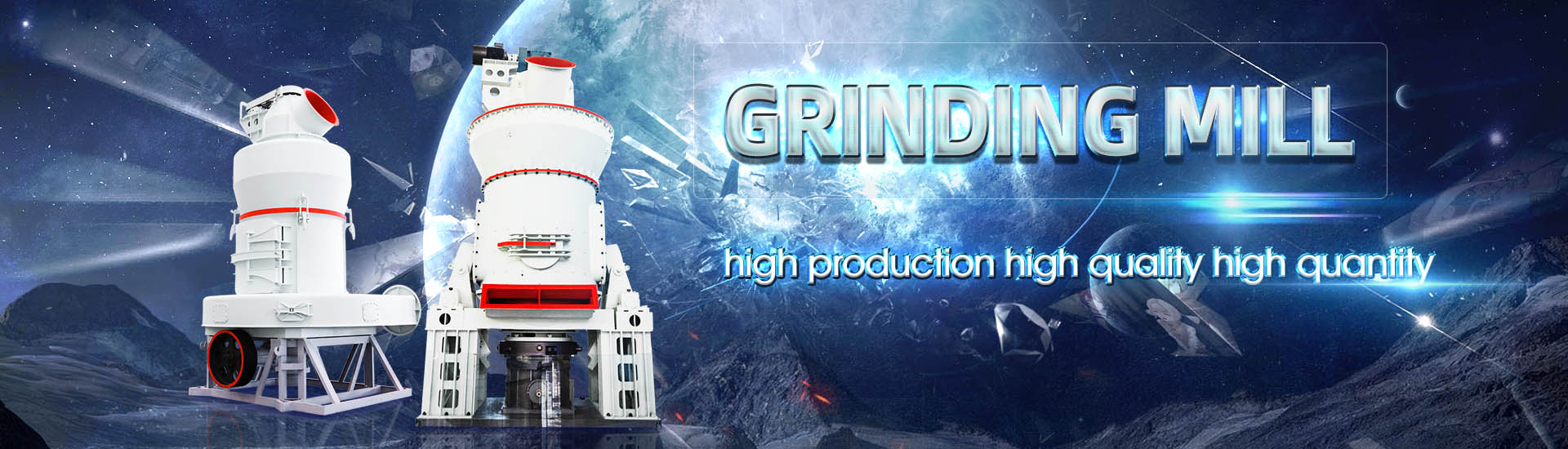
Acceptance of fixed hydraulic ore grinding mill
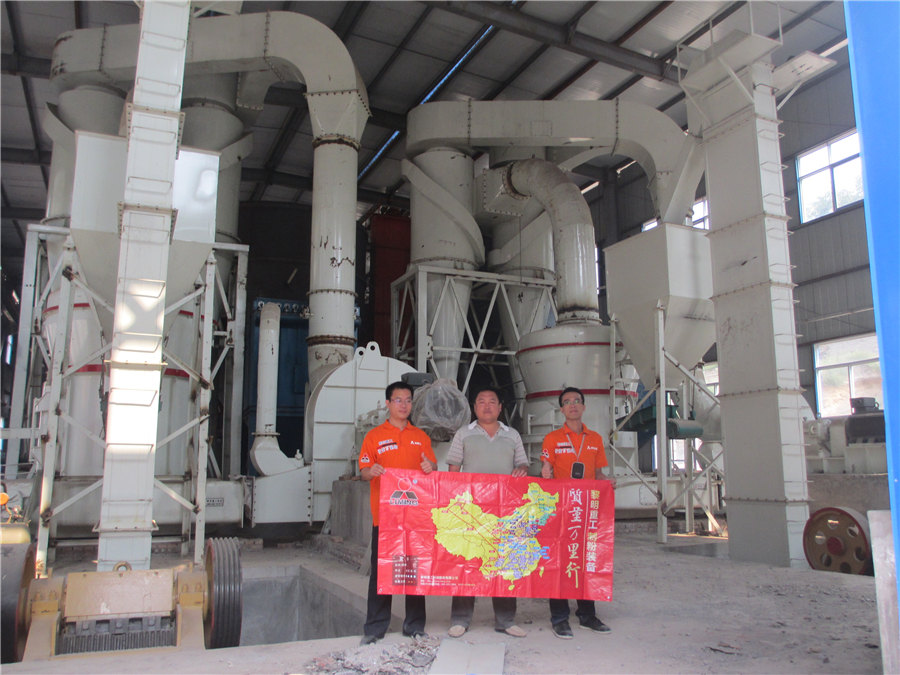
Quantification of HPGR energy efficiency effects on downstream
HPGRs (high pressure grinding rolls) have been developed within the last decades for energy efficient processing of a wide variety of ores Special interest has been raised by projects ore grinding is divided into dry grinding, wet grinding, and moist grinding Dry grinding relies on pneumatic conveying, in which the classification system and gas supply system of grinding Ore Grinding Methods and Process of Ore Grindingthe amount of ball milling power required downstream With a reduced load for the ball mills, you get a substantial reduction in required motor power, lowered steel ball consumption and HPGR / HPGR Pro The next level in grinding FLSmidth2019年2月5日 This study evaluates the effect of using high pressure grinding rolls (HPGR) in new comminution circuit designs in comparison to conventional comminution devices such as HPGR Grinding Technology and its Application to the Bauxite
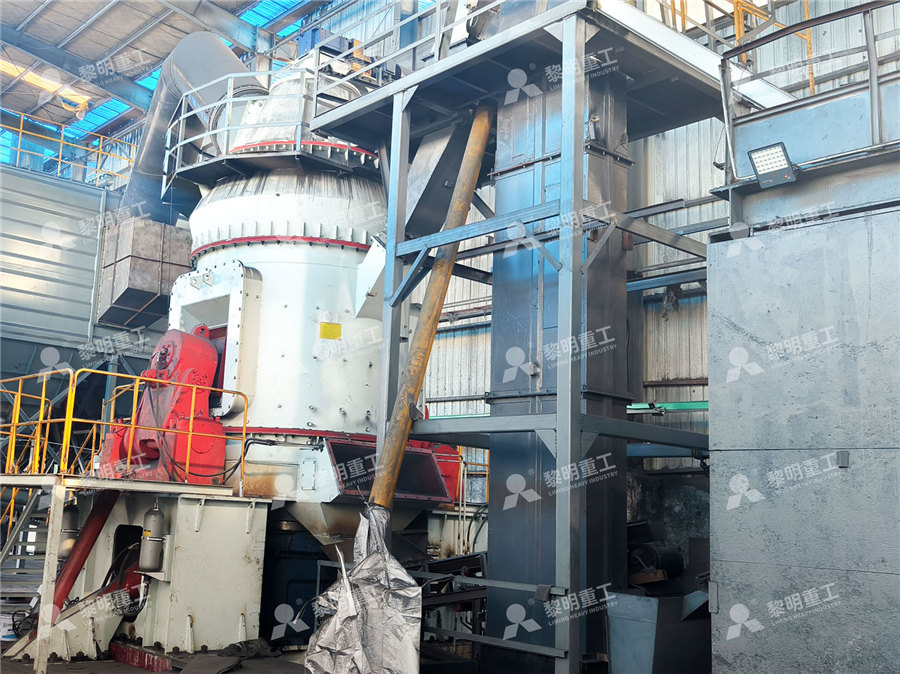
Ore Grinding SpringerLink
2023年7月20日 Moist grinding, a special grinding method, is used to prepare pellets for smelting According to the grinding medium features, ore grinding is mainly classified into ball grinding In Comparison to SAG Milling Technology Presented by: Hassan Ghaffari, PEng Major Parts: •Counterrotating Rolls •One fixed roll, one moving roll Hydraulic Pistons Feed Floating High Pressure Grinding Rolls (HPGR) 911 Metallurgist2019年2月5日 High Pressure Grinding Roll ("HPGR") technology is very rapidly gaining a wide acceptance within the mineral processing industry Benefits from energy efficiency and a low HIGH PRESSURE GRINDING; HOW HIGH CAN YOU GO?2019年2月5日 Circuits closed with air classification have enabled the use of HPGR in the cement industry for reliable premill grind or final product grind, reducing power and steel Case Study of Dry HPGR Grinding and Classification in Ore
.jpg)
Potential of HighPressure Grinding Roll (HPGR) for Size Reduction
2022年3月16日 HPGR has been found to be efficient size reduction equipment compared to conventional size reduction equipments due to its potential processing benefits in terms of 2017年4月1日 Pilot plant test results with various ores showed that low energy consumption feature of vertical roller mills is applicable to the ore industry Grinding test results for zinc ore Operational parameters affecting the vertical roller mill 2017年10月3日 Share with Facebook; Share with Twitter; Share with Google+; Share with LinkedIn; Posted: October 3, 2017 Grinding Mills Types, Working Principle Applications The purpose of this article is to explain the usage of Grinding Mill Types, Working Principle 2019年8月14日 Ball mill is a common grinding equipment in concentrator Common Types of Ball mill back to top The common industrial ball mills mainly include cement ball mill, tubular ball mill, ultrafine laminating mill, cone ball mill, ceramic ball mill, intermittent ball mill, overflow ball mill, grid ball mill, wind discharge ball mill, double bin ball mill, energy saving ball millThe Ultimate Guide to Ball Mills Miningpedia

Hydraulic Cone Crusher Stone Crusher Grinding Mill
Application range: river pebble, granite, basalt, iron ore, limestone, quartzite, diabase, etc Materials: sand and gravel yard, mining, coal mining, concrete mixing station, dry mortar, power plant desulfurization, quartz sand, etc Feed 2015年3月15日 For the grinding tests, a Loesche mill LM45 (table diameter 045 m) is used (Fig 2a) This pilot scale mill is a special development for ore grinding, which is reflected by several features The mill has four rollers, which are able to stress the particle bed with grinding pressures of up to 5000 kN/m 2Research of iron ore grinding in a verticalrollermill» small and 100 % active high pressure grinding zone Different ores Feed material and HPGR product after sizing Primary and secondary crushing Screening at 20–50 mm Screening at 4–12 mm Water Classi˜cation and ball mill Hydrocyclone HPGR Water Ore storage Downstream process Ore Grinding using an HPGR – Example Rule of thumb forHighPressure Grinding Roller Presses for Minerals Processingores with varying grinding properties This leads to significant optimization potential for the plant design as well as for its operation Furthermore, energy and cost savings due to optimized operation, high system efficiency and high system availability are shown Introduction In the past, for grinding applications often fixed speed drives haveTECHNICAL AND COMMERCIAL BENEFITS OF GEARLESS MILL DRIVES FOR GRINDING
.jpg)
Roller Mill SpringerLink
2023年7月4日 Roller mill is a type of grinding equipment for widely applied in cement, steel and power industry, the preparation of nonmetallic ore ultrafine powder, manganese ore fine grinding blast furnace slag, and coal The highpressure roller mill mainly consists of the feeding system, working rollers (a fixed roller 2020年8月12日 As one of the three major forces of coal mills, the grinding force exerts a significant impact on the working process of coal mills and parameters like mill current and outlet temperatureAn investigation of performance characteristics and energetic 2017年3月20日 An effect of a grinding method, that is ball mill and high pressure grinding rolls (HPGR), on the particle size, specific surface area and particle shape of an iron ore concentrate was studiedPhysicochemical Problems of Mineral Processing Investigation 即时翻译文本完整的文档文件。为个人和团队提供准确的翻译。每天有数百万人使用DeepL进行翻译。DeepL翻译:全世界最准确的翻译 DeepL Translate
.jpg)
(PDF) Grinding process optimization — Featuring case
PDF On May 1, 2017, Caroline Woywadt published Grinding process optimization — Featuring case studies and operating results of the modular vertical roller mill Find, read and cite all the Ore grinding machines can be divided into many types according to different classification methods, each with significant characteristics The following is a general introduction to the types of oregrinding machines and their Ore Grinding Machines: Ball Mill, Rod Mil Grinding 6 天之前 Fixed roll 2 Feeding chute 3 Floating roll 4 Lubrication oil station 5 Motor 6 Reducer 7 Coupling 8 Hydraulic station Rolls Roll can be the type of builtup it is arranged in front of the ball mill as a pregrinding equipment or High pressure grinding rolls HPGR for iron ore, The 012mm copper powder sieved by the vibrating screen is evenly sent to the ball mill for grinding, and sieved by the screw classifier, and those that do not meet the requirements are sent to the ball mill to continue grinding Ball mill is a more commonly used and efficient grinding equipment It is suitable for grinding ore such as iron ore Copper ore crushing equipment and beneficiation process
.jpg)
Grinding Mill an overview ScienceDirect Topics
A crushing plant delivered ore to a wet grinding mill for further size reduction The size of crushed ore (F 80) was 40 mm and the SG 28 t/m 3 The work index of the ore was determined as 122 kWh/t A wet ball mill 1 m × 1 m was chosen to grind the ore down to 200 micronsIn the mill, the mixture of medium, ore, and water, known as the mill charge, is intimately mixed, the medium comminuting the particles by any of the above methods Apart from laboratory testing, grinding in mineral processing is a continuous process, material being fed at a controlled rate into one end of the mill and discharging at the other end after a suitable dwell (residence) timeGrinding Mill an overview ScienceDirect TopicsThe mill shell with the fixed magnets is the rotor The large numbers of magnets produce a multipole machine that by itself reduces the rotational speed of the rotor Cycloconverters, which are high power rectifier inverters, convert the incoming three phase 50 Hz power supply to a lower frequency power supplyAdvantages of Gearless Motor Drives in Large Ore Grinding Mills2024年5月17日 A SAG (SemiAutogenous Grinding) mill is a giant rotating cylinder filled with grinding media and the ore being reduced As the mill rotates, the grinding media lifts and the impact crushes the feed material SAG mill control refers to the practice of managing the mill load, which is the amount of material inside the mill at any given timeA guide to SAG Mill management
.jpg)
Quantification of HPGR energy efficiency effects on downstream grinding
An increase of the hydraulic pressure in the HPGR leads to an increased power draw of the HPGR roll drives as well (see Figure 4) Figure 4 – Correlation of specific hydraulic pressure and specific energy demand from a test series with iron ore Moreover, the high pressure grinding regime leads to microfractures within the product asFTM Raymond mill, as a kind of grinding mill which is widely used in the field of ore grinding can help users to grind the limestone, marble, calcite, feldspar, and other solid materials into the requested particle size within the range 80325 meshRaymond Mill FTM Mining Machine2019年2月5日 High Pressure Grinding Roll ("HPGR") technology is very rapidly gaining a wide acceptance within the mineral processing industry Benefits from energy efficiency and a low overall operating cost High Pressure Grinding Rolls for Bauxite Size Grinding of ore is one of the most important and power intensive operation in The grinding circuit includes a variablespeed SAG mill of 12 MW with two fixedspeed ball mills with synchronous motors of 55 HIGHPOWER GRINDING Technical evaluation and practical experience of high

Roller Mill SpringerLink
2024年1月1日 Roller mill is a type of grinding equipment for widely applied in cement, steel and power industry, the preparation of nonmetallic ore ultrafine powder, manganese ore fine grinding blast furnace slag, and coal The highpressure roller mill mainly consists of the feeding system, working rollers (a fixed roller 2016年7月14日 HPGR test results published by Grier (1992) on gold ores from the Mt Todd project showed significant energy savings for a HPGR/Ball Mill circuit as compared to a SAG/Ball Mill plant By adding a Polycom highpressure grinding roll, the throughput of existing plants can be increased by as much as 150% while simultaneously reducing the power consumption by HPGR 911Metallurgist2013年4月16日 ABSTRACT In this study, ultrafine grinding of a refractory silver ore tailings was studied A laboratory scale pintype vertical stirred mill and ceramic beads were employed for the grinding testsInvestigation of some parameters affecting the Ultrafine grinding 2016年6月6日 Aside from parameters fixed at design (mill dimensions, installed power, and circuit type), the major variables affecting AG/SAG mill circuit performance (throughput and grind attained) include: Feed characteristics in terms of ore SAG Mill Grinding Circuit Design 911Metallurgist
.jpg)
(PDF) Optimization of inmill ball loading and slurry solids
2012年12月1日 Optimization of inmill ball loading and slurry solids concentration in grinding of UG2 ores: A statistical experimental design approach December 2012 Minerals Engineering 39:149155The weight of mill and charge (ore and grinding media) is 3,452 tons The substructure method is used for dynamic analysis of the ball mill foundation, that is, the structure and soil are DYNAMIC DESIGN FOR GRINDING MILL FOUNDATIONS2023年4月23日 grinding media in a grinding mill with about 2630 wt% chrome by Chen et al [37] using a phosphate ore in a modified ball laboratory ball mill whose electrochemical potential could be controlled(PDF) Grinding Media in Ball MillsA Review ResearchGateDepending on the application, ore grinding can take place in a ball mill, SAG or AG mill, towe r mill, rod mill or HPGR Empowering the future of mining FLS is a leading, full flowsheet minerals processing supplier to the global mining industryFlexible, efficient grinding systems – FLS
.jpg)
Grinding Mill Liners 911Metallurgist
2015年8月6日 Rubber liners absorb the impact of the larger grinding media and thus protecting – the mill structure and prolonging it’s life Weight: Rubber weighs about 15% of an equivalent volume of steel This means that a rubber liner CLUM series of ultrafine gypsum powder vertical grinding mills are a new type of ultrafine industrial ore grinding equipment that integrates grinding, grading, powder collection and conveying +17CLUM Ultrafine Vertical Grinding Mill1 Population balance model approach to ball mill optimization in iron ore grinding Patricia M C Faria1,2, Luís Marcelo Tavares2 and Raj K Rajamani3 1 Vale SA, Brazil 2 Department of Population balance model approach to ball mill optimization in iron ore LUMSeries Ultra fine vertical grinding mill is an advanced mill which combining our company’ several years of millproducing experiences, It is designed and researched based on vertical mill technology, absorbing the worldwide ultrafine grinding theories This series is a professional equipment including ultra fine grinding,LUM SERIES ULTRAFINE GRINDING MILL
.jpg)
Analyzing the influence of lifter design and ball mill speed on
2023年10月30日 Ball mills are the foremost equipment used for grinding in the mineral processing sector Lifters are placed on the internal walls of the mill and are designed to lift the grinding media (balls The mill is driven by an electric motor via a flexible coupling and the mill gearbox via a vertical output flange A segmental thrust bearing at the top of the gearbox absorbs the grinding forces Before the mill motor is started, the grinding rollers are Loesche Mills for industrial minerals2021年1月18日 Grinding mills were designed for each project, so every project in a sense, was a trial of how well the testing/calculation method suited the ore The results showed that in all cases there were no problems in sizing the grinding mills, even for the hardest ores There are three key elements in a successful SAG mill grinding circuit designImpact on Grinding Mill Design of Recent New Discoveries2017年11月1日 An iron ore mill relies on the grinding and impact of grinding balls to complete iron ore crushing The operating process of an iron ore mill is as follows: first, the ores are poured into the mill, and both the ores and the grinding balls are lifted by the lifting bar arranged on the wall of the cylinder body to a certain height, after which they fall onto the bottom of the mill to Friction and wear of liner and grinding ball in iron ore ball mill
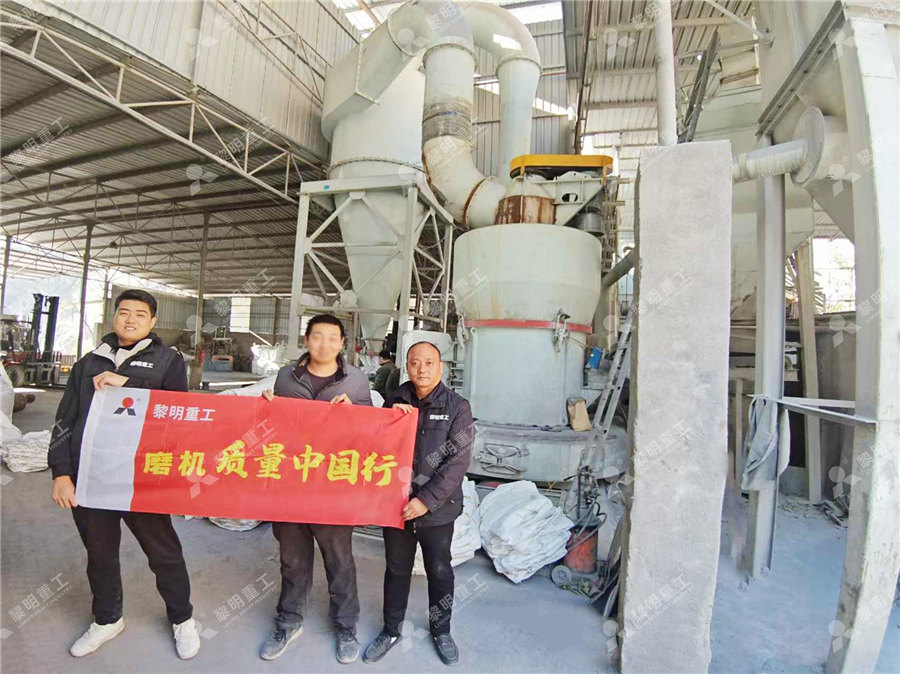
The layout of the coal mill with a rotary classifier
Vertical Coal Mill (VCM) is equipment for grinding and pulverizing coal into micron size Rotary kilns then use the powders as fuel burners The VCM has a housing section equipped with a lining Typically the relining of a mill represents between 2 – 5% of lost annual mill availability for grinding plants With declining ore grades creating additional production pressure, it is highly beneficial to reduce the duration of relining to achieve a higher mill availability While grinding mill maintenance often dictates the length of plant DESIGNING GRINDING PLANTS FOR MILL RELINING TO MAXIMISE MILL