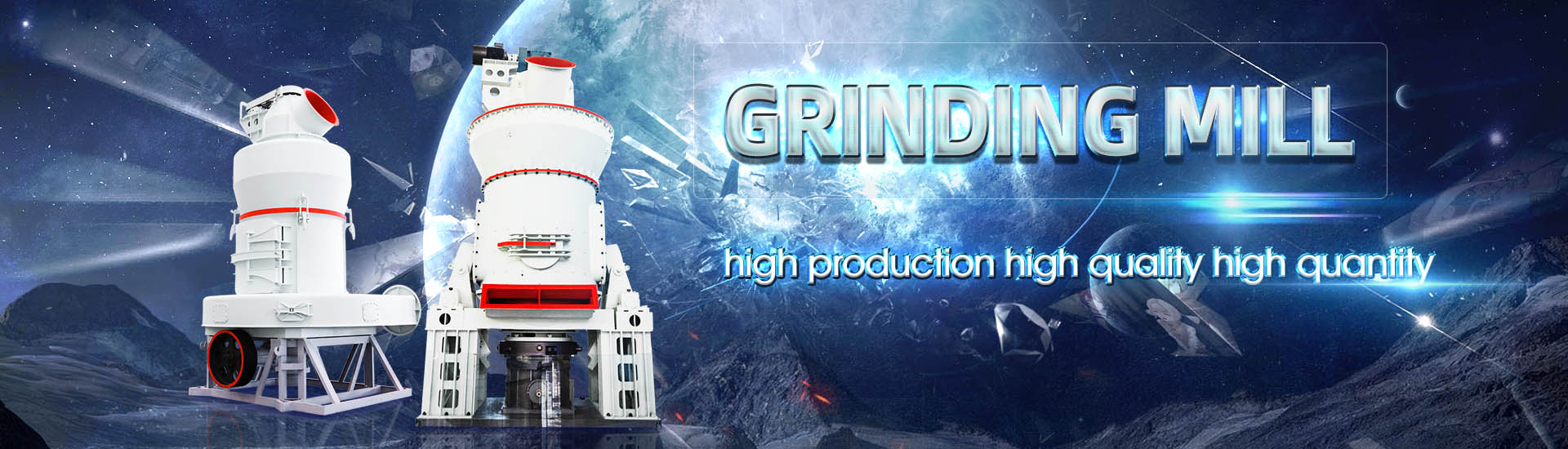
Grinding mill assembly inspection procedures
.jpg)
Avoid catastrophic failures by Metso
grinding mills required an assessment to determine their actual condition Metso was mandated to conduct a visual and nondestructive inspection of the mill Results: Through the inspections, This document outlines inspection procedures for the ball mill at Arish Cement Company's production department It details checking various parts of the mill like the inlet, feeders, liners, ball charge, and diaphragms Measurements are Ball Mill Inspection Procedure PDF PDF Mill This document provides guidance on inspecting ball mills used in cement production It outlines key steps and measurements to take when inspecting the interior of a twocompartment mill Key areas to examine include the ball Ball Mill Inspection Procedure PDF Mill (Grinding)Nowadays, conducting grindability tests requiring only a few kilos of material on several samples, is a more typical approach to grinding mill design This paper summarises the requirements SAG Mill Testing Test Procedures to Characterize Ore Grindability
CFB石灰石脱硫剂制备64.jpg)
CNC Machining Quality Testing and Inspection:
2024年1月27日 Quality testing and inspection in CNC machining are processes dedicated to verifying that the output meets specific standards of accuracy and integrity These procedures encompass a range of activities, from dimensional 2024年3月18日 The following procedures are conducted annually or as dictated by meter readings: 1 Cylinder regrinding: Remove and have cylinder grinding surfaces reground or Guide to Raymond Mill Maintenance: Schedule and Best Practicesgrinding mills required an assessment to determine their actual condition Metso Outotec was mandated to conduct a visual and nondestructive inspection of the millby finding problems early Metso2023年7月18日 Regular maintenance also requires inspection of various parts of the ball mill to find problems and deal with them promptly When inspecting, pay attention to the following Ball Mill Maintenance Process and Methods Miningpedia
.jpg)
CLASSIFIER MILL INSTALLATION, OPERATION, AND
When your shipment arrives, thoroughly inspect the Classifier Mill and all related equipment In the event of shipping damage, note the problem on the bill of lading or freight bill and make 2Measure height, h, in three different points along axis for each grinding compartment For Best results the measurements takes place in an empty mill (mill feed stopped for approx 10 min) Mill material level: Inspection only at BALL MILL INSPECTION PROCEDURES INFINITY 2024年1月27日 One key aspect of quality control in machining is maintaining an optimal environment for machining processes This includes: Temperature and Humidity Sensors: These sensors are crucial in ensuring the machining CNC Machining Quality Testing and Inspection: 2017年2月20日 All Grinding Mill Ball Mill Manufacturers understand the object of the grinding process is a mechanical reduction in size of crushable material They are always split in 2 or 4 pieces in order to facilitate the assembly Competent supervision encourages close inspection of each mill both as to quality and proper fabricationGrinding Mill Design Ball Mill Manufacturer 911Metallurgist
.jpg)
SAG Mill Liner Design 911Metallurgist
2016年6月6日 Grinding Mill Shell Design The shell liner assembly is particularly subject to damage during ballonliner contact as experienced during grind outs the following procedures for shutdowns for inspection and maintenance are EATON VC IOM OF AIRFLEX MODEL VC GRINDING MILL CLUTCHES ECLCLTH001E1 December 2017 eaton 5 Airflex VC Grinding mill clutches Figure 1 Component parts for Airflex type VC element Dual mounted Airflex model VC Grinding mill clutches Item Descriptions 1 Rim 2 Tube (w/valve stem snap rings where req’d) 3 Elbow assemblyVC 5001 Installation, operation and maintenance of Airflex model 2024年3月18日 The following procedures are conducted annually or as dictated by meter readings: 1 Cylinder regrinding: Remove and have cylinder grinding surfaces reground or replaced every other year as per wear specifications to restore concentricity 2 Chassis works: Loosen base assembly bolts, remove accumulated rust deposits through wire brushingGuide to Raymond Mill Maintenance: Schedule and Best PracticesSince the Eddy Current sensor is integrated in the roll measuring system, all measurements are carried out during grinding and therefore without delay Manufacturing defects within the roll as well as fatigue from operation in the mill are detected during a Roll Inspection Control Measuring Technology HCC/KPM
.jpg)
Operation and Maint A4P 20 en PDF Mill (Grinding
OPERATION AND MAINTA4P20EN Free download as PDF File (pdf), Text File (txt) or read online for free This document is an instruction manual for operating and maintaining an Atox mill for raw meal It provides general information about the construction and operation of the mill, including the drive station and grinding machineryGrinding mill gear inspection Recommendations revealed in inspections help mills make the right changes to maximize their production and savings Description Through this service, we conduct a basic grinding mill gear inspection of central grease, open gears and key lubrication points to seek early identification of abnormal conditionsGrinding mill gear inspection2023年11月14日 Follow this procedure for the regular inspection of your ball mill machine and all its components to make sure if its proper working condition and prolong its life span Health and Safety Procedure when accessing a CNC and assembly technology machines machines ABIC 08/08/2023 Tennant 7400 1 Month Maintenance TMCO, Inc 02/23 Ball Mill Preventive MaintenanceMill visuals and vitals: Aimed at improving mill reliability, this inspection focuses on catching cracks, oil contamination, and slurry leaks with minimal downtime Mill mechanical verification: Aimed at improving mill integrity, this inspection Grinding mill services Metso
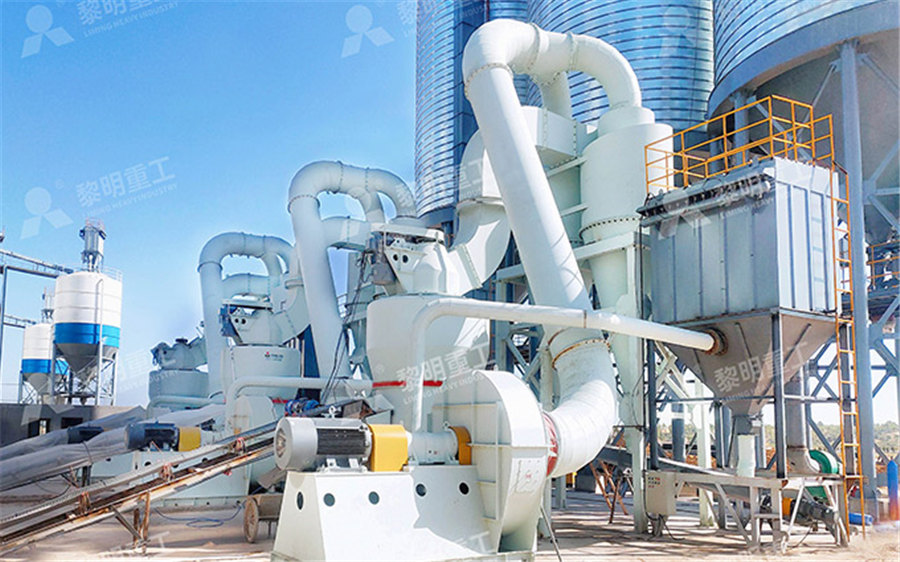
Ball Mill Installation Essential Work and Precautions
Inspection of the ball mill After installing a ball mill, it is important to conduct a thorough inspection of the equipment to ensure everything is in order The inspection should include a check of all bolts, nuts, and other fasteners to ensure they are tight and secure2020年3月17日 With grinding equipment operating around the clock, any revenues lost due to a mechanical failure are lost forever and can severely impact a mine’s bottom line Every grinding mill part has a role Large grinding The magic of bolting for a grinding mill assemblyThis document provides guidelines for grinding weld toes to improve fatigue life It outlines that a high speed grinder with a burr diameter over 10mm should be used to grind at least 05mm but not more than 15mm from the weld toe at an angle of 15 to 45 degrees Only trained operators should perform the grinding, and safety gear is required The ground weld should then be Weld Toe Burr Grinding Procedurethe need to change inspection sensors 4 Roll Wastage Mill rolls are a direct expense to the mill The grinding process is a costly procedure considering that every pass reduces the life of the roll The cost of a new or refurbished roll can run from $100K to $500K per roll Caster roll shells with less than 4” of usable life are equally Improved Technologies for Mill Roll Inspection
.jpg)
Mill Training Manual Alstom PDF Coal Mill (Grinding)
Mill Training Manual Alstom Free download as PDF File (pdf), Text File (txt) or read online for freecoal mill Free download as Powerpoint Presentation (ppt), PDF File (pdf), Text File (txt) or view presentation slides online This document discusses maintenance of coal mills and coal feeders Key points include: Maintenance is important to improve reliability, efficiency and reduce downtime Wear parts include grinding rolls, bull ring segments, and separator body linersCoal Mill PDF Mill (Grinding) TroubleshootingA guide to grinding mill installation: Ensuring efficient and troublefree operation Grinding mills are critical components in many industrial processes, responsible for reducing the size of materials and achieving desired particle sizes The successful installation of a grinding mill is essential for ensuring efficient and troublefree A guide to grinding mill installation: Ensuring efficient and 2021年5月5日 A grinding machine is a production machine tool used in the manufacturing industry in which the grinding wheel is attached in the tool post and the workpiece is fixed to the work table and when the operation starts it removes the unwanted material to get the desired surface finish, correct size, and accurate shape of the workpieceGrinding Machine: Definition, Parts, Working Principle, Operation
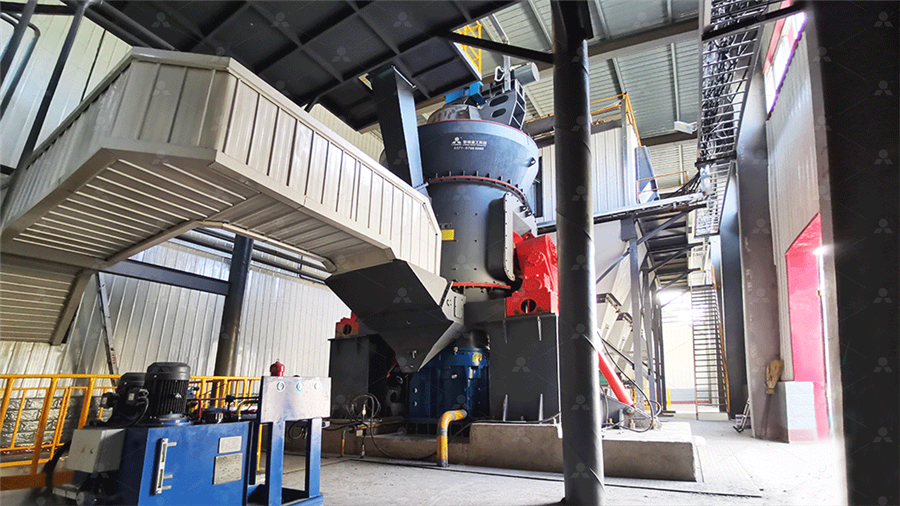
Ball Mill Grinding Machines: Working Principle, Types,
Ball mill grinding machines are valuable tools in various industries, offering efficient and reliable grinding and mixing capabilities Understanding their working principle, different types, parts, applications, advantages, and recent in variable speed mills, this may be achieved by reducing mill speed; and in both cases this may be achieved by design by increasing the lifter face angle Traditionally, the number of shell lifters used in a SAG mill is equal to twice the number of the feet in the mill shell diameter (eg, a 34ftdiameter mill shell would have 68 shell lifters)Semiautogenous grinding (SAG) mill liner design and developmentVisual inspection after cleaning uncovered a crack on a gear tooth A full inspection using MPI detected a deeper crack Once detected, cracks are assesed and treated immediately by OEM experts Scoping process • Metso Outotec will identify necessary inspection points, putting together a full inspection planGears and pinions MetsoIncorporation of these relationships into eq 1, with the recognition that for a batch mill drawing constant power, the quantity Pt/H is exactly equal to the specific energy input to the mill, E, yields the normalized batch grinding model for i = 1, 2 , , n: i1 dmi(E) =kEmi (~) + ~l bijkEmi(E) dE, j=l (11) This "detailed energysize reduction relationship" predicts that for a (PDF) Scaleup procedure for continuous grinding mill design using
.jpg)
B Ball Mill Inspection PDF Bearing (Mechanical) Mill (Grinding)
B Ball Mill Inspection Free download as Powerpoint Presentation (ppt), PDF File (pdf), Text File (txt) or view presentation slides online This document provides guidance on inspecting, servicing, and troubleshooting a ball mill It outlines inspection procedures that should be performed daily, weekly, monthly, and annually Specific components that require inspection User manual: ABC Hansen Hippo Mill, Model BABY, 1, 1½, 47, 57, 69, L 63, Mammoth Page 3 44 INDEX: 1 Safety Declaration of Conformity 2 Installation Procedure 21 Roof clearing 22 Mill dimensions 23 Moving assembly and installing the Hippo Hammer Mils ABC Hansen AfricaAdvanced mill liner wear measurement and prediction services 3 FARO laser scanner Recording liner profiles as 3D cloud point data inside the mill chamber Our advanced liner profiling and scanning services use cuttingedge technology to give you the most accurate and actionable information about the condition of your mill linersFLS Advanced mill liner wear measurement and prediction servicesSAG MILL TESTING AN OVERVIEW OF THE TEST PROCEDURES AVAILABLE TO CHARACTERIZE ORE GRINDABILITY AUTHOR: FO VERRET, G CHIASSON AND A MCKEN SGS KEYWORDS Comminution, grindability, grinding, SAG mill, AG mill, milling, HPGR, work index, pilot plant INTRODUCTION The resistance of ore samples to breakage (or hardness) is SAG Mill Testing Test Procedures to Characterize Ore
.jpg)
A Comprehensive Guide to Ball Mill Manual
Each type of ball mill has its own unique advantages and disadvantages For example, grate discharge ball mills are efficient for coarse grinding, but not suitable for fine grinding Overflow ball mills, on the other hand, are suitable for both coarse and fine grinding but require a higher level of maintenance Safety Procedures and PrecautionsProject Mill size DXL (ft) Drive system Capital cost Horsepower Production rate A Ptimary SAG, 26x11 Vatiable speed ac synchronized motor mill, $13 million 4025 11,000 coupled to a gear dfive motor, $13 million Secondary ball mill, 18x27 ac synchronized motor coupled to a gear mill, $16 million dtive with an air clutch motor, $602,000 6050Mill drive selection for semiautogenous grinding mills 911 13 Grinding, smoothing, lapping, polishing surfaces This procedure is for surface refinement, which is based on the classic procedure These processes are normally performed in machines or systems designed especially for this Deburring – Procedure and methods GravostarThe document discusses parameters for quality finish milling including cement strength, Blaine surface area, and residue percentages It also covers inspection of ball mills including measuring filling degrees, conducting longitudinal testing Ball Mill Operation, Inspection Optimization PDF
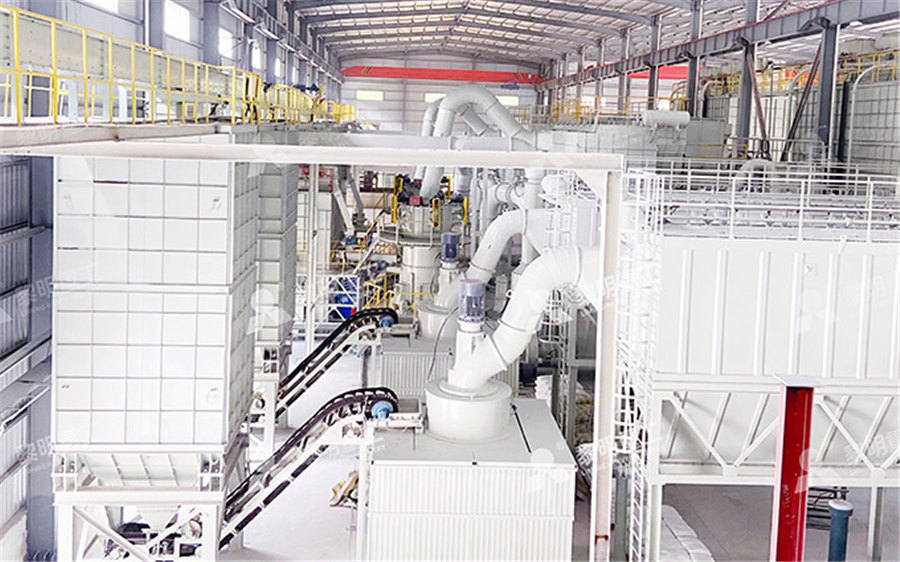
SAG Mill Testing Test Procedures to Characterize Ore
SAG MILL TESTING AN OVERVIEW OF THE TEST PROCEDURES AVAILABLE TO CHARACTERIZE ORE GRINDABILITY AUTHOR: FO VERRET, G CHIASSON AND A MCKEN SGS KEYWORDS Comminution, grindability, grinding, SAG mill, AG mill, milling, HPGR, work index, pilot plant INTRODUCTION The resistance of ore samples to breakage (or hardness) is Ball mills are used primary for single stage fine grinding, regrinding, and as the second stage in two stage grinding circuits According to the need of customers, ball mill can be either wet or dry designs Ball mills have been designed in standard sizes of the final products between 0074 mm and 04 mm in diameter Applicationpresentation of ball mill inspection Grinding Mill ChinaJune 2022; ARCHIVE Proceedings of the Institution of Mechanical Engineers Part C Journal of Mechanical Engineering Science 19891996 (vols 203210) 236(2):1107(PDF) A comprehensive review on the grinding process: BALL MILL INSPECTION PROCEDURE The Cement Grinding Read more about material, balls, mill, ball, visual and diaphragmBALL MILL INSPECTION PROCEDURE The Cement Grinding
.jpg)
Grinding and Polishing Guide Buehler Metallography
2021年11月15日 Grinding in one direction is usually better for maintaining flatness than grinding in both directions This procedure can be done dry for certain delicate materials, most applications for electrolytic polishing in metallography have been in process inspection of materials that are difficult to polish and etch with chemical 2020年1月1日 During grinding some detrimental microestructural changes can appear in the workpiece if the temperature reaches the tempering point in the contact zone(PDF) Experimental approach for a grinding burn inprocess inspection an explosion Scrap metal in a coal mill is particularly dangerous during mill shut down or start up Coal Mill Operation Fires or explosions most likely occur during startup and shutdown of a coal mill system If a small amount of coal remains in the COAL GRINDING SYSTEMS SAFETY CONSIDERATIONS PEC 2023年7月18日 Regular maintenance also requires inspection of various parts of the ball mill to find problems and deal with them promptly When inspecting, pay attention to the following aspects: 1 Check the grinding media The grinding media is an important part of the ball mill for grinding ore and needs to be checked for wearBall Mill Maintenance Process and Methods Miningpedia