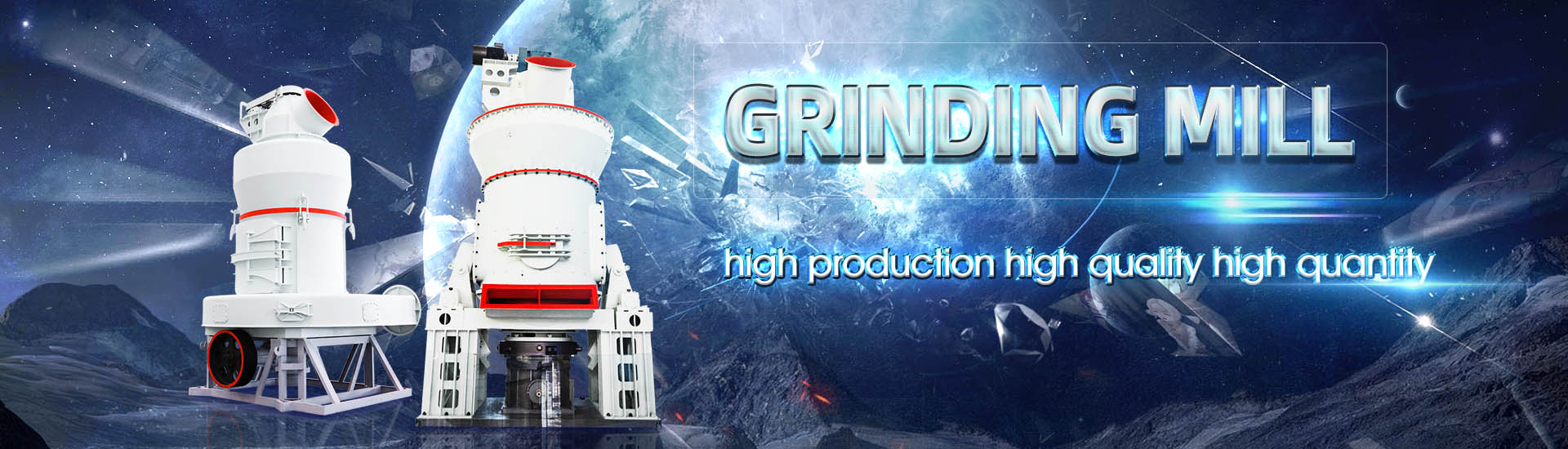
Limestone plant process flow
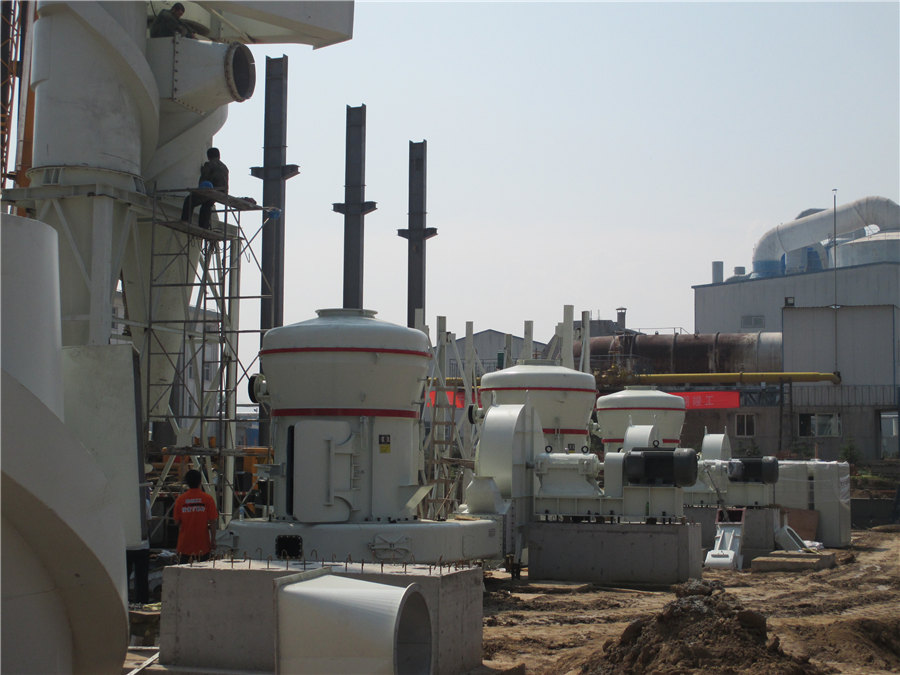
Limestone Quarrying and Processing: A LifeCycle Inventory
Process flow diagram for limestone processing operations Processing commences with transportation of the (raw) stone from the quarry to the processing facility, as depicted by Figure 2In some lime plants, the resulting lime is reacted (slaked) with water to form hydrated lime The basic processes in the production of lime are: (1) quarrying raw limestone; (2) preparing 1117 Lime Manufacturing US EPAThe analysis was performed through process modelling of the CaL plant using 4 different supplementary fuels in the calciner, namely, biomass charcoal (BC), solid recovered fuel (SRF), coal, andFlow diagram and system boundaries of limestoneProcess flow diagram for limestone processing operations Processing commences with transportation of the (raw) stone from the quarry to the processing facility, as depicted by A LifeCycle Inventory of Limestone Dimension Stone Quarrying
.jpg)
PROCESS FLOW DIAGRAM FOR LIMESTONE
Download scientific diagram PROCESS FLOW DIAGRAM FOR LIMESTONE QUARRYING OPERATIONS (NATURAL STONE COUNCIL, 2008) from publication: Metallic Commodities – Carbonate Ores Carbonates The flue gas desulfurization process using scrubbers or sorbent is the most preferred treatment method in industrial applications due to high process maturity and high removal efficiencyFlow diagram of the limestone scrubbing methodSection 2 provides a detailed description of the production process for lime, with discussions of individual lime products, limestone inputs, and costs of production Section 3 describes the Lime Production: Industry ProfileAbstract—A long term production planning of limestone quarry is presented to supply consistent quantity and quality of limestone to a cement plant A case study from Indian cement industry Limestone Quarry Production Planning for Consistent Supply of
.jpg)
Production European Lime Association
Heat transfer for lime burning can be divided into three main stages: ‘Preheating zone’ – limestone is heated to approximately 800°C by direct contact with gases leaving the calcining Typical limestone crushing plant feature successive size reduction stages and intermediate screening to classify material A standard flow involves primary, secondary, and tertiary (or fines) crushing Primary crushing, the initial size Limestone Crusher for Efficient Limestone Crushing Plant2012年8月30日 Cement Manufacturing Process Phase II: Proportioning, Blending Grinding The raw materials from quarry are now routed in plant laboratory where, they are analyzed and proper proportioning of limestone Cement Manufacturing Process Engineering IntroLimestone preparation system in flue gas desulfurization (FGD) consists of following subsystems: 1 Limestone Handling System Limestone will be delivered to the limestone storage shed by truck Limestone will be delivered Flue Gas Desulfurization (FGD) Working Thermal
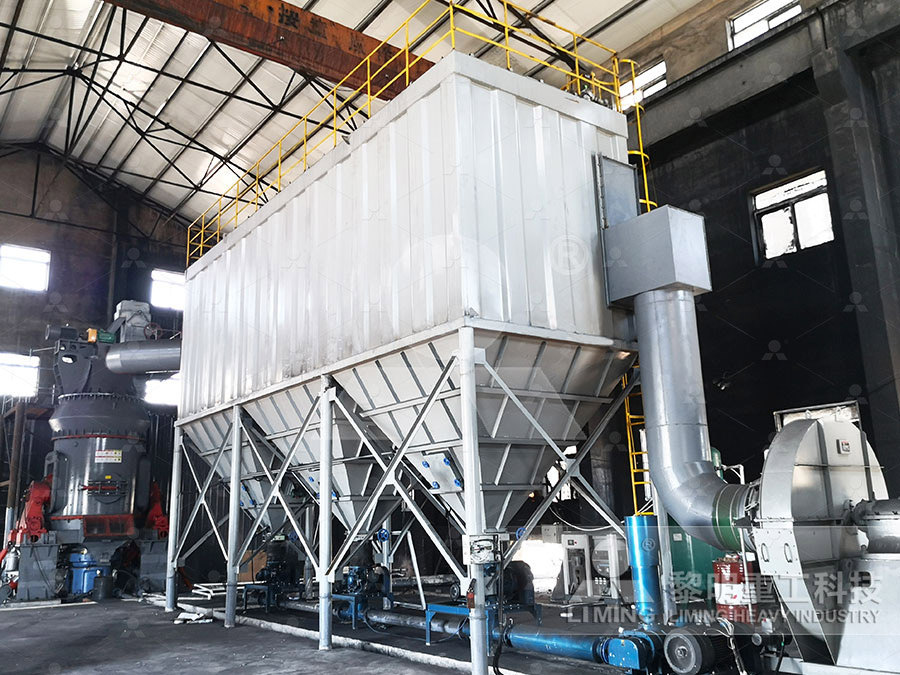
Soda ash manufacturing and process flow diagram
2017年11月19日 It then provides the overall reaction and a process flow diagram depicting the major steps These steps include: 1) ammonia absorption into salt water, 2) production of carbon dioxide from limestone, 3) carbonation The crushed limestone and aggregates such as sand, clay and ironstone are blended together in a raw mill to a particle size of 90 micrometres, producing “kiln feed” Cement Plant: The Manufacturing Process worldcementassociation 1 Limestone (CaCO3) is taken from a quarry 2 4 3 The limestone is fed into a crusher and then stored until neededCement Plant: The Manufacturing Process 4 5 World Cement Download scientific diagram Flow diagram of the limestone scrubbing method from publication: Review of Design, Operating, and Financial Considerations in Flue Gas Desulfurization Systems In Flow diagram of the limestone scrubbing method1977年5月3日 11171 Process Description15 Lime is the hightemperature product of the calcination of limestone Although limestone deposits are found in every state, only a small portion is pure enough for industrial lime manufacturing To be classified as limestone, the rock must contain at least 50 percent calcium carbonate1117 Lime Manufacturing US EPA
.jpg)
Simulation and Optimization of an Integrated Process Flow Sheet
2021年3月9日 In this study the process flow diagram for the cement production was simulated using Aspen HYSYS 88 software to achieve high energy optimization and optimum cement flow rate by varying the flow rate of calcium oxide and silica in the clinker feed Central composite Design (CCD) of Response Surface Methodology was used to design the ten experiments for 2016年1月20日 All cement types contain approximately 4–5% gypsum to control the setting time of the product Other mineral components such as slag, power plant fly ash, limestone, and other materials are used to replace clinker to produce blended cement The process of cement grinding is shown in supplementary materialAnalysis of material flow and consumption in cement production process The process flow of the limestone grinding production line mainly includes the following steps: Crushing: The initial step is to run large chunks of limestone through a crusher, A Limestone Grinding Mill Plant is a facility designed to process limestone into fine Limestone Grinding Mill Plant TAYMACHINERY2018年8月28日 The raw materials from quarry are now routed in plant laboratory where, they are analyzed and proper proportioning of limestone and clay are making possible before the beginning of grinding Generally, limestone is 80% and remaining 20% is the clay Proportioning of raw material at cement plant laboratoryCement Manufacturing Process The Engineering Community
.jpg)
Configuration and Process Flow of Limestone Milling
2017年11月28日 Although the configuration scheme and process flow of limestone processing plant are not complicated, only the reasonable equipment configuration and scientific limestone plant design can improve the economic The process flow of the limestone grinding production line mainly includes the following steps: Crushing: The initial step is to run large chunks of limestone through a crusher, A Limestone Grinding Mill Plant is a facility designed to process limestone into fine Limestone Grinding Mill Plant TAYMACHINERYLimestone Crushing Plant Processing Flow Typical limestone crushing plant feature successive size reduction stages and intermediate screening to classify material The limestone crushing process is a complex operation that Limestone Crusher for Efficient Limestone Crushing 2015年3月15日 Understanding Sinter and Sinter Plant Operations satyendra; March 15, 2015; 8 Comments ; fluxes, Iron ore fines, SCFA, sinter, sinter plant basic sinter, sintering machine,; Understanding Sinter and Sinter Plant Operations Sintering is a process of agglomeration of fine mineral particles into a porous and lumpy mass by incipient fusion caused by heat produced Understanding Sinter and Sinter Plant Operations IspatGuru
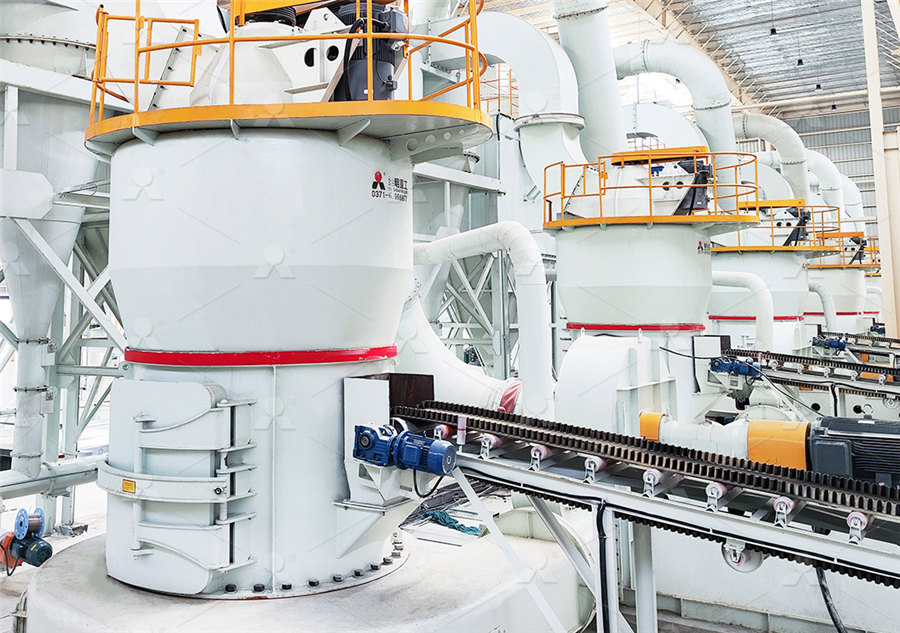
How Is Cement Produced in Cement Plants Cement Making Process
The cyclone preheating system Phase IV: Calcination The calcination is the core phase of the cement making dry process The calcination of the preheated raw meal takes place in the rotary kiln of the cement plant The rotary kiln is a huge rotating furnace in which the raw meal is heated up to 1450 ⁰C and turned to clinkerManufacturing process flow 1 Quarrying and Crushing The quarry (where the mining activity is performed) is located 07 km away from the plant and has the main raw materials such as Limestone and shale that is estimated to last for 100 years, the other raw materials (Iron ore, silica sand, gypsum and Pozzolana (pumice) ) are brought from nearbyManufacturing process flow 1 Quarrying and Crushing Messebo Download scientific diagram Typical cement manufacturing process flow diagram [4] from publication: Model Development for CO2 Capture in the Cement Industry Climate change has become a Typical cement manufacturing process flow diagram [4]The process simulation software „NIAflow ® “ developed by HB provides a robust process flow design and fast scenario analysis It gives all tools that you need to develop, characterise and optimise a mineral processing plant in a single software packageSimulation software for mineral processing plants NIAflow
.jpg)
Configuration and design of 1000tph limestone aggregate production plant
Process flow of the production plant The process flow includes the following units: (1) Aggregate primary crushing and transportation; (2) Aggregate soil removal, screening and transportation; (3) Aggregate secondary crushing and transportation; (4) Aggregate primary screening and transportation; (5) Aggregate secondary screening and conveying;examined is a typical process In this process, limestone is calcinated to lime, which reacts with coke in an electric arc furnace, producing calcium carbide The report examines onetime costs associated with the construction of a plant and the continuing costs associated with the daily operation of such a plantCalcium Carbide from Limestone (Electrothermic Process) IntratecStage 2: Grinding, Proportioning, and Blending The crushed raw ingredients are made ready for the cementmaking process in the kiln by combining them with additives and grinding them to ensure a fine homogenous mixture The composition of cement is proportioned here depending on the desired properties of the cement Generally, limestone is 80%, and the remaining 20% How Cement is Made Cement Manufacturing Process2022年1月15日 The absorption reaction kinetics in the spray drying process have been studied in the pilot plant of spray drying scrubbing flue gas desulfurization Fig 5 shows the process flow chart of limestone wet desulfurization technology [93] Summary of research progress on industrial flue gas desulfurization
.jpg)
Beneficiation of limestone plant rejects for value addition
2013年11月15日 In the present study, attempts are made to upgrade these fines by froth flotation techniques This paper deals with: (i) the results of beneficiation studies of the rejects, (ii) mineralogical characteristics of feed and flotation products and (iii) process flow sheet development to treat the limestone plant rejects for upgradation 2 ExperimentalProcess flow diagram for limestone quarrying operations 3 As shown in Figure 1, have been cut into slabs before reaching the main fabrication plant These are most commonly sliced to a thickness of 3/4 in (2 cm), 11/4 in (3 cm), or more in lengths of approximately 1012 ftLimestone Quarrying and Processing: A LifeCycle InventoryLime is made from indigenous limestone or chalk rock, one of the most abundant materials in the Earth’s crust Limestone and chalk are both sedimentary rocks and are chemically known as calcium carbonate When crushed or ground, they are widely used as aggregates and building products As a raw material, calcium carbonate can also be processed []Production European Lime Association2021年10月22日 Equipment selection of limestone crushing sand making plant There are mainly three types of commonly used crushers suitable for limestone: Process flow of the production plant The process flow includes the following units: (1) Aggregate primary crushing and transportation; (2) Aggregate soil removal, Configuration and design of 1000tph limestone aggregate production plant
.jpg)
FACT SHEET: MEADOWBROOKLIMESTONE WASTEWATER TREATMENT PLANT
FACT SHEET: MEADOWBROOKLIMESTONE WWTP SPDES Permit No NY – Treatment Plant Specifications Performance Data (2016) SPDES Permit compliance history can be found at: https://echoepagov/ Treatment Process Flow Diagram Rotary Drum Decant Tank Thickener Hauled for further Processing at the Metro WWTP WAS2024年6月9日 The article explains the importance of understanding a steelmaking flow chart, which outlines each step from raw material preparation to final products, aiding in efficiency and productivity It details key components like raw materials iron ore, limestone, coal, primary steps raw material prep, ironmaking, steelmaking, and methods such as Basic Oxygen Furnace BOF The Steelmaking Flow Chart: A Roadmap to Efficient ProductionDownload scientific diagram General flow chart belonging to the Bornova stone aggregate crushing facility from publication: Development of a model estimating energy consumption values of primary General flow chart belonging to the Bornova stone aggregate Schematic process flow of FGD plant; 5000 MW FGD Plant (includes a detailed process flow diagram) Alstom presentation to UNECE on air pollution control (includes process flow diagram for dry, wet and seawater FGD) Flue Gas Treatment article including the removal of hydrogen chloride, sulfur trioxide, and other heavy metal particles such as Fluegas desulfurization Wikipedia
.jpg)
Calcium Carbide from Limestone (OxyThermal Process) Intratec
The third part, Process Overview, presents basic aspects of the process studied: products generated, process inputs, and physicochemistry highlights The fourth part, Industrial Site, describes an industrial plant based on the process under analysis, in terms of the process unit and infrastructure requiredReport Overview: IMARC Group’s report, titled “Limestone Manufacturing Plant Project Report 2024: Industry Trends, Plant Setup, Machinery, Raw Materials, Investment Opportunities, Cost and Revenue” provides a complete roadmap for setting up a limestone manufacturing plant It covers a comprehensive market overview to microlevel information such as unit operations Limestone Manufacturing Plant Report 2024: Setup and Cost1971年8月17日 The paragraphs below briefly describe the process, starting with the wet process and then noting differences in the other processes In the wet process and long dry process, all of the pyroprocessing activity occurs in the rotary kiln Depending on the process type, kilns have lengthtodiameter ratios in the range of 15:1 to 40:1116 Portland Cement Manufacturing US EPAConsequently, this study intends to predict the process performances for a fullscale coal fired power plant (1 GW e ), in particular in terms of separation efficiencies, gypsum quality, limestone Simplified flow scheme of the wet FGD process adapted for
.jpg)
Manufacture of Cement Materials and Manufacturing Process of
Each process is explained chemical reactions for manufacture of Portland Cement Cement is a greenish grey colored powder, made of calcined mixtures of clay and limestone The powdered limestone and water washed clay are sent to flow in the channels and transfer to grinding mills where they are completely mixed and the paste is Process Flow Diagram Process Flow Diagram (PFD) is a drawing which describesthe process flow for a processing plant PFD is used to capture the main process equipment and main process streams in a single drawing losses to atmosphere Waste Water Power 9,700 kg/h Limestone 700,000 kg/h 533,370 kg/h ~300 MW Sorbent 13,000 kg/h 1,800 kg/hK22: Full Chain Process Flow Diagrams GOVUKUptodate report, based on Q2 2024 data, examining Calcium Carbide production costs from Limestone, including Calcium Carbide plant capital cost and operating costs See free preview Solutions Primary Commodity Prices process consumption figures and comprehensive process flow diagrams (PFD)Calcium Carbide from Limestone (Electrothermic Process)2022年7月20日 Process flow of limestone sand production line 1 Process flow of limestone manufactured sand Sand making: Through the crushed limestone, part of it is directly sent to the stockpile as a finished product, and the other part is crushed and made sand by the sand making machine Screening: The vibrating screen is also responsible for distinguishing the finished Limestone crushing, sand making and grinding process
.jpg)
Stages in cement production flow chart [43] ResearchGate
Download scientific diagram Stages in cement production flow chart [43] from publication: A review on kiln system modeling The purpose of this study is to evaluate performance cement of 2015年3月15日 The evaluation of desulphurisation efficiency and abatement capacity of inorganic trace pollutants during two consecutive campaigns at a cocombustion power plant equipped with a wet limestone FGD [42], revealed a relatively low retention for SO 2 (82–88%), in comparison with that of other FGD system (94%) of similar capacity [27], as a consequence of Status of Flue Gas Desulphurisation (FGD) systems from coal