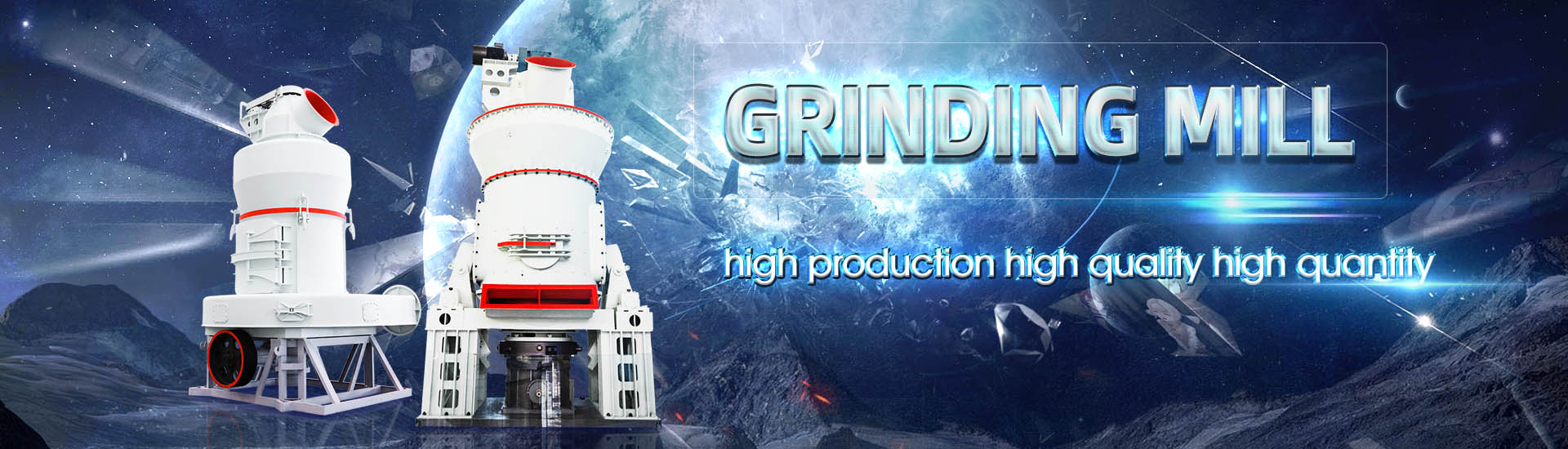
Dry grinding ball mill system power consumption
.jpg)
Ball Mill Design/Power Calculation 911Metallurgist
2015年6月19日 The ball mill motor power requirement calculated above as 1400 HP is the power that must be applied at the mill drive in order to grind the This paper will focus on the ball mill grinding process, its tools and optimisation possibilities (see Figure 1) The ball mill comminution process has a high electrical energy consumption, BALL MILLS Ball mill optimisation Holzinger Consulting2020年10月1日 In this paper, we present a detailed investigation of the dry grinding of silica sand in an oscillatory ball mill We are interested in the evolution of specific surface area Evolution of grinding energy and particle size during dry ball 2001年8月1日 Discrete element method (DEM) modelling has been used to systematically study the effects of changes in mill operating parameters and particle properties on the charge Charge behaviour and power consumption in ball mills: sensitivity
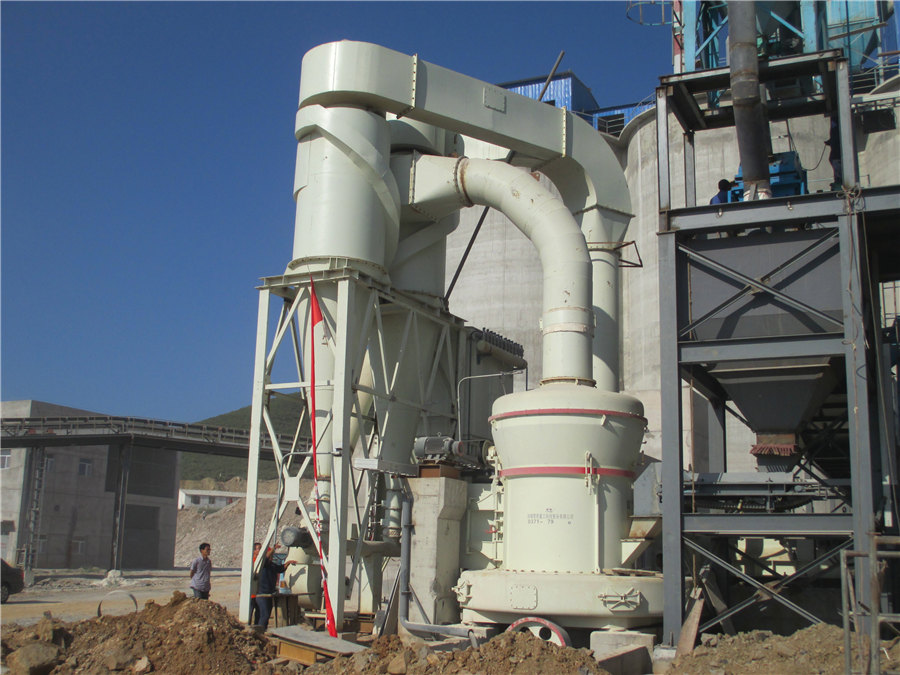
Breaking down energy consumption in industrial
2017年1月17日 It is generally accepted that the energy required to produce new mineral surfaces is less than 1% of the electricity consumed to operate ball mills The remaining 99% is assumed to beTypical power consumption for a 5m diameter by 7mlong ball mill is between 25 and 35 MW The actual proportion of this energy usefully used in size reduction is thought to be very low, Charge behaviour and power consumption in ball mills: sensitivity 2001年8月1日 The results show that the charging of particles in the PHSP grinding system is blocked to a certain extent by polyhedral particles, both the power consumption and energy Charge behaviour and power consumption in ball mills: Sensitivity 2020年5月1日 Measurement results of two ball mills in a real ceramic manufacturing plant showed that the proposed calculation models could achieve an accuracy of more than 96% for predicting the ball mill energy consumption Calculation method and its application for energy
.jpg)
AMIT 135: Lesson 7 Ball Mills Circuits – Mining Mill
Mill Power Consumption Example Ball mill = 35 m x 35 m; Rubber lining = 75 mm % Mill volume charge = 40%; Grinding balls diameter = 70 mm; Mill operational speed = 176; Calculate the optimum power consumption to 2017年2月13日 grinding ball consumption Table 13 is a rough guide to the wear that may be expected from the three classes of balls Their average relative grinding ball consumption is approximately as follows: Chrome: highcarbon: Ball Mills 911Metallurgist2015年4月9日 Ball mill is a versatile grinding mill and has a wide range of applications This type of mill is used for dry grinding only and accepts only relatively soft materials Maximum capacity is of the order of 10 tons per Grinding Mills and Their Types IspatGuruNETZSCH Dry Fine Grinding: From A (activated carbon) to Z (zinc) There are numerous application areas which demand a high fineness at high throughput capacities with a low energy consumption, especially in the area of dry Dry Grinding NETZSCH Grinding Dispersing
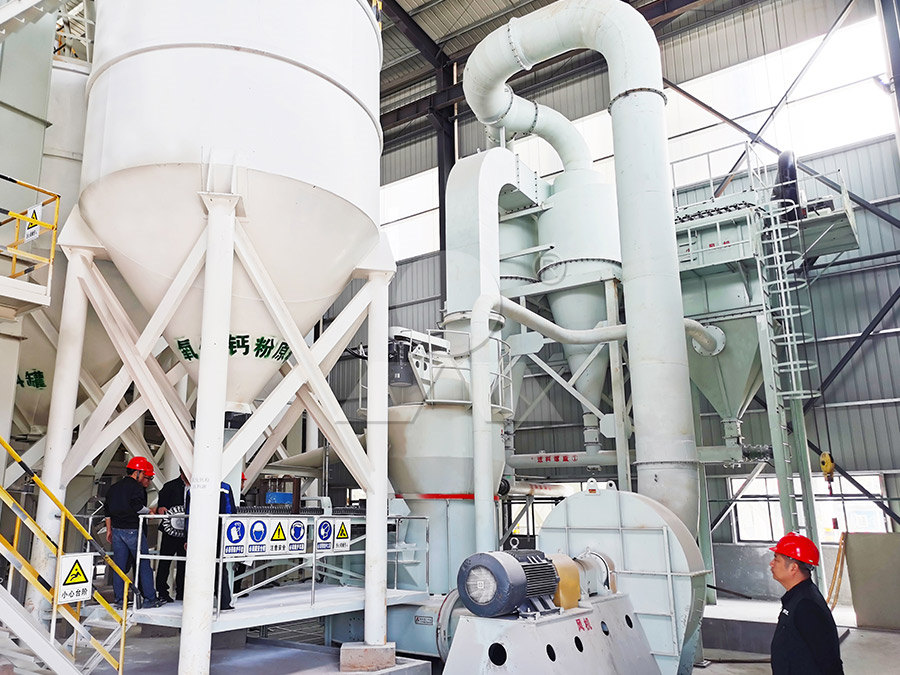
AMIT 135: Lesson 7 Ball Mills Circuits – Mining Mill Operator
Dry and wet grinding common Ball mill photographed by Ron Frisard and shared on Flickr, CC Cyclones are typically installed above the mill and thus the cyclone underflow is fed to the mill by gravity Discharge System One exit unit; Mill Power Consumption Example Ball mill = 35 m x 35 m; Rubber lining = 75 mm2022年2月28日 Comparing dry and wet grinding curves in a ball mill in the same condition (an equal amount of materials and grinding media has been used on each pair of wetdry experiments) (Fig 17) indicated two significant differences at higher power values of wet grinding, specifically when speed exceeded 06 critical speed and for higher ω Pmax in the Grinding SpringerLinkInt J Miner Process 63 Ž2001 79–114 elsevierrlocaterijminpro Charge behaviour and power consumption in ball mills: sensitivity to mill operating conditions, liner geometry and charge composition Paul W Cleary ) CSIRO DiÕision of Mathematical and Information Sciences, PriÕate Bag 10, Clayton South MDC, Clayton, Victoria, 3169, Australia Received 21 January 2000; Charge behaviour and power consumption in ball mills: 2017年5月25日 It appears, however, that the rate of ball and liner wear is greater in wet milling so the decision between wet and dry operation is, in cases where the choice is permitted, a matter of balancing the economic gain arising from reduced power demand and increased throughput against the increased cost of replacement of the ball charge and the mill liners and the loss of Dry Grinding VS Wet Grinding 911Metallurgist
.jpg)
EnergyEfficient Advanced Ultrafine Grinding of Particles Using
2023年7月10日 The present literature review explores the energyefficient ultrafine grinding of particles using stirred mills The review provides an overview of the different techniques for size reduction and the impact of energy requirements on the choice of stirred mills It also discusses the factors, including the design, operating parameters, and feed material properties, 2012年6月1日 PDF The paper presents an overview of the current methodology and practice in modeling and control of the grinding process in industrial ball mills Find, read and cite all the research you Grinding in Ball Mills: Modeling and Process Control2023年9月15日 To get a better idea of dry ball mill grinding and wet ball mill grinding, let’s first look at the differences between the two associated machines Dry grinding machine : A dry grinding machine uses no liquid element and Dry Ball Mill Grinding Vs Wet Ball Mill GrindingTotal power consumption for grinding circuit as a whole is also less by about 30% compared to closed circuit ball mill in spite of higher fan power Feed size can be as large as 75 to 100 mm Feed size can be as large as 5% of roller diameterRaw Material DryingGrinding Cement Plant Optimization
.jpg)
(PDF) Analysis of ball mill grinding operation using mill power
2014年3月1日 An analysis of the kinetics of dolomite grinding in a dry ball mill reveals that the following approximations apply for the parameters of the batch grinding model: the size discretized selection To determine the power that a dry grinding needs, full grate discharge mill Equation 1 is multiplied by the factor of 108 A multicompartment ball mill consists of two or more grate discharge ball mills in series The same equation is used to calculate the power that each ball mill compartment should draw The total power isCALCULATION OF THE POWER DRAW OF DRY MULTI–COMPARTMENT BALL The attritor ball mill, also known as stirred ball mill, is a kind of vertical ball mill It can be divided into dry type and wet type, suitable for grinding a variety of materials, such as industrial ceramics, fireproof materials, silicate materials, metal powder, ores, etc It is equipped with an agitation system inside the grinding cylinderAttritor Ball Mill Wet Dry Grinding Stirred Ball Mill AGICO Ball Mill2022年5月9日 Modeling of energy consumption factors for an industrial cement vertical roller mill by SHAPXGBoost: a "conscious lab" approachModeling of energy consumption factors for an industrial cement
.jpg)
Dry milling mill, Dry milling grinding mill All DirectIndustry
Find your dry milling mill easily amongst the 105 products from the leading brands (Fritsch GmbH, Retsch, Brabender, • Its 230V motor has an average power consumption of 1,500W DESIGN • This flour mill ball grinding mill MaxxMill series Output: 190, 800 t/h 2023年12月28日 3 Moisture content of grinding materials Ball mill grinding can be divided into two methods: dry grinding and wet grinding For the dry grinding method, the grinding materials’ moisture content greatly influences the mill’s production and quality The higher the moisture content of the grinding materials, the easier it is to cause saturationFactors Affect The Output and Quality of Ball Mills And How to 2020年7月2日 Keywords: ball mill, mill power, charge shape, mill speed, ball size distribution, DEM 1 Introduction The grinding process within the ball mill includes crushing and grinding, which are mainly (PDF) Effects of Ball Size Distribution and Mill Speed and Their 2017年2月20日 This should be compared with 4045% in wet grinding The expression used for this phenomenon is that the charge in a dry grinding mill is swollen Big dry grinding ball mills are often twocompartment mills, with big balls in the first compartment and small balls or cylpebs in the second one An extra grate wall is used to separate the two chargesGrinding Mill Design Ball Mill Manufacturer 911Metallurgist
.jpg)
Open and closed circuit dry grinding of cement mill rejects in a
below 600 Am with a median and 80% passing sizes of 75 and 150 Am, respectively This size is more convenient to stirred mill grinding rather than ball mill grinding [5]2001年8月1日 Request PDF Charge behaviour and power consumption in ball mills: Sensitivity to mill operating conditions, liner geometry and charge composition Discrete element method (DEM) modelling has Charge behaviour and power consumption in ball mills: the grinding process intensification Specific energy consumption for the grinding dropped down to 30% Current methods of power consumption calculation of a mill drive do not allow determining the power consumption for ball drum mills with a crosslongitudinal motion of the grinding media A new calculationThe Power Consumption Calculation of a Ball Drum MillPrediction and optimization of tower mill grinding power consumption based on GABP neural network Ziyang Wang 1, Ying Hou 1, equivalent ball mill The grinding kinetics of a pilot scale unit were investigated, grinding systems, it can be fitted with a simple firstorder breakage model (Austin and Schneider, 2022) de Bakker, 2013 #1 Prediction and optimization of tower mill grinding power consumption
.jpg)
Dry Grinding an overview ScienceDirect Topics
Fine grinding of wood – Overview from wood breakage to applications Pasi Karinkanta, Jouko Niinimäki, in Biomass and Bioenergy, 2018 52 Wet grinding In general, wet grinding in a liquid medium like water is more energy efficient than dry grinding in a gaseous medium, typically air [124]Wet grinding of wood in an aqueous medium is scarcely reported in the literature if 2017年10月26日 Dry grinding may require ten to fifty percent more power than wet, although this is offset by greatly diminshed media and liner consumption The introduction of several percent moisture without heated gas sweeping can virtually halt grinding of fine material, until increased water addition carries the material through the sticky stage into the normal wet grinding range Factors Affecting Ball Mill Grinding EfficiencyEnergy efficiency of cement finish grinding in a dry batch ball mill C Frances Cement and DEM method DEM is a simulation method that models particulate systems whose motions are Min Eng 14, 1295–1319 Cleary, PW, 2001b Charge behaviour and power consumption in ball mills: Sensitivity to mill operating conditions, liner Ball motion, axial segregation and power consumption in a full 2017年5月8日 Grinding Mill Power ScaleUp Probably one of the most comprehensive experimental investigations of the power demands of the ball or tube mill is that carried out by one of the present authors, with a worker, Rose and Evans by use of smallscale models; the test apparatus being that shown in Fig 31Grinding Mill Power 911Metallurgist
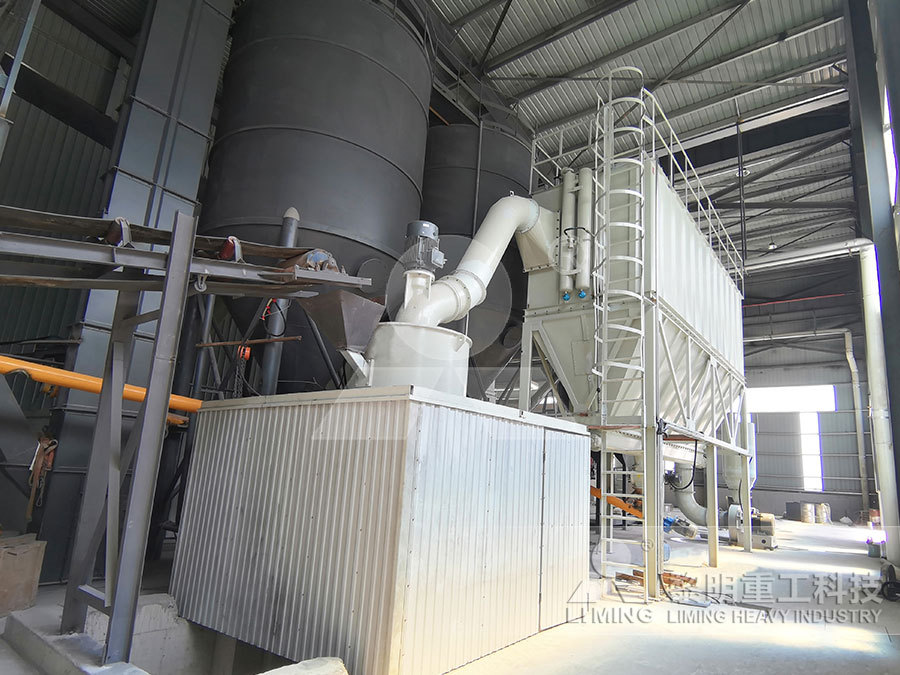
Energy conservation and consumption reduction in grinding
2023年11月1日 As shown in Fig 15, the grinding unit consumption of the ceramic medium stirring mill was 317(kWh/t), When the content of −0043 mm accounted for 80% Therefore, the cost of grinding power consumption is significantly reduced by about 5016% by using the new ceramic ball stirring mill system to substitute the original twostage ball mill2018年3月27日 Dry grinding and classification circuit: (a) Idea of the circuit: 1feed stream, 2mill working chamber, 3working area with ferromagnetic rods, 4main transport air stream, 5mills output stream Comparison of Wet and Dry Grinding in 2001年8月1日 (a) Dependence of the specific power consumption vs mill speed curve on the lifter shape for face angles between 85° and 225° The fill level here is 40% (b) Change in specific power consumption with face lifter angle throughout the lifter life cycle for the rotation rates N=70%, 80%, 90% and 100%Charge behaviour and power consumption in ball mills: mill speed (% of Nc), ball filling ratio (J), ball size distribution (%), powder filling ratio (fc), grinding aid dosage (g/Mg) and grinding time (min) on the dry fine grinding of calcite using a laboratory batch scale conventional ball mill The evaluation of the results of grinding tests was performed based on the product particle size (d 50 Influences of operating parameters on dry ball mill performance
CFB石灰石脱硫剂制备——磨机公众号12.8 推送案例(8)53.jpg)
Ball Mill Design Power PDF Mill (Grinding) Iron Ore
Ball Mill Design Power Free download as PDF File (pdf), Text File (txt) or read online for free This document provides information about grinding mills, including standard sizes and dimensions of mills, descriptions of mill types and components, and methods for estimating mill power requirements The key details are mill dimensions and specifications for different standard 2020年2月26日 Owing to the lack of effective energy consumption models of ball mills in the ceramic industry, a calculation model to forecast energy consumption of ceramic ball mills during the grinding process Calculation method and its application for energy consumption of ball 2019年6月20日 Design Considerations for Selecting a Grinding System Most dry iron ore grinding installations utilizing the standard type rod or ball mill are grinding highgrade natural ores that do not require beneficiation generally the power consumption in the actual grinding process is 2530% higher with dry grindingFine Dry Grinding of Iron Ore for Pelletizing 911MetallurgistNETZSCH Taurus Ball Mill, the pinnacle of fine and ultrafine grinding technology Achieve precise particle sizes with durable, lowmaintenance equipmentTaurus Ball Mill NETZSCH Grinding Dispersing
.jpg)
Ball Mill Grinding Machines: Working Principle, Types, Parts
Advantages of Ball Mill Ball mill grinding machine offer several advantages, including: Versatility: Ball mills can perform various types of grinding, such as dry grinding ball mill or wet grid ball mill, batch or continuous grinding, and fine or ultrafine grinding, making them 2023年4月23日 In ball mill operations, it is always helpful to op timise the grinding media system to min imize the costs of the operation In a research done by Yu et al [16] to o ptimize grinding media (PDF) Grinding Media in Ball MillsA Review ResearchGate